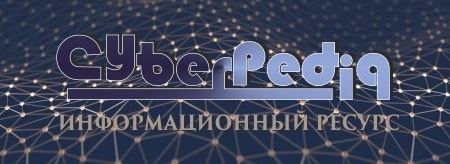
Архитектура электронного правительства: Единая архитектура – это методологический подход при создании системы управления государства, который строится...
Папиллярные узоры пальцев рук - маркер спортивных способностей: дерматоглифические признаки формируются на 3-5 месяце беременности, не изменяются в течение жизни...
Топ:
Организация стока поверхностных вод: Наибольшее количество влаги на земном шаре испаряется с поверхности морей и океанов...
Теоретическая значимость работы: Описание теоретической значимости (ценности) результатов исследования должно присутствовать во введении...
Выпускная квалификационная работа: Основная часть ВКР, как правило, состоит из двух-трех глав, каждая из которых, в свою очередь...
Интересное:
Искусственное повышение поверхности территории: Варианты искусственного повышения поверхности территории необходимо выбирать на основе анализа следующих характеристик защищаемой территории...
Что нужно делать при лейкемии: Прежде всего, необходимо выяснить, не страдаете ли вы каким-либо душевным недугом...
Мероприятия для защиты от морозного пучения грунтов: Инженерная защита от морозного (криогенного) пучения грунтов необходима для легких малоэтажных зданий и других сооружений...
Дисциплины:
![]() |
![]() |
5.00
из
|
Заказать работу |
|
|
Кафедра конструирования и стандартизации машиностроения
Допускаю к защите
Руководитель Тумаш Александр
Михайлович
Проектирование привода ленточного питателя
Пояснительная записка
к курсовому проекту по дисциплине
Детали машин
1.024.00.00.ПЗ
Выполнил студент группы ХТТ – 04 – 1
Алексеев Николай Александрович
Нормоконтролёр
Тумаш Александр Михайлович
Курсовой проект защищён
Иркутск 2005 г.
Задание на проектирование
Исходные данные
Тяговое усиление ленты Fл = 2,7 кН
Скорость ленты vл = 1,2 м/с
Диаметр барабана DБ = 300 мм
Допускаемое отклонение скорости ленты d = 4 %
Срок службы привода LГ = 6 лет
1) Двигатель
2) Муфта
3) Редуктор
4) Цепная передача
5) Лента конвейера
Выбор электродвигателя и кинематический расчет
Определим КПД привода
Общий КПД привода равен:
h = h1 * h2 * h32 * h42 * h5 (1.1)
где h1 – КПД закрытой зубчатой передачи; h1 = 0,98;
h2 – КПД открытой цепной передачи, h2 = 0,92;
h3 – КПД муфты; h3 = 0,98;
h4 – коэффициент, учитывающий потери пары подшипников качения,
h4 = 0,99;
h5 – коэффициент, учитывающий потери в опорах приводного барабана,
h5 = 0,99
Значения КПД принимаем по таб. 1.1 [1, стр.5]
h = 0,98 * 0,92 * 0,982 * 0,992 * 0,99 = 0,84
1.2. Определим мощность на валу барабана:
Рб = Fл * vл (1.2)
где Fл – тяговая сила ленты;
vл – скорость ленты
Рб = 2,7 * 1,2 = 3,24 кВт
1.3. Требуемая мощность электродвигателя:
Ртр = Рб / h (1.3)
Ртр = 3,24 / 0,84 = 3,8 кВт
1.4. Угловая скорость барабана:
wб = 2 * vл / Dб (1.4)
wб = 2 * 1,2 / 0,3 = 8 рад/с
1.5. Частота вращения барабана:
nб = 30 * wб / p (1.5)
nб = 30 * 8 / 3,14 = 76,4 об/мин
Выбираем электродвигатель
|
По требуемой мощности Ртр = 3,8 кВт выбираем электродвигатель трехфазный асинхронный короткозамкнутый общего назначения в закрытом обдуваемом исполнении серии 4А с синхронной частотой вращения 1500 об/мин 4А100L4 с параметрами Рдв = 4,0 кВт и скольжением 4,7 %, см. таб. П1 [1, стр. 390]
Обозначение: Двигатель 4А 112МВ6 ГОСТ 19523 – 81
Номинальная частота вращения вала двигателя:
nдв = 1500 * (1 – 0,047) = 1429,5 об/ мин
Угловая скорость вала двигателя:
wдв = p · nдв / 30 (1.6)
wдв = 3,14 · 1429,5 / 30 = 149,6 рад/с
1.7. Определяем передаточное отношение привода:
i = wдв / wб (1.7)
i = 149,6 / 8 = 18,7 = u
Намечаем для редуктора uР = 5, тогда для цепной передачи:
i ц = u / u Р (1.8)
i ц = 18,7 / 5 = 3,74
Вычисляем вращающий момент на валу шестерни:
Т1 = Ртр * h3 * h4 / w1 (1.9)
Т1 = 3,7 * 103 * 0,98 * 0,99 / 149,6 = 24 Нм = 24*103 Нмм
1.8. Вычисляем вращающие моменты на валу колеса:
Т2 = Т1* Uр * h1 * h4 (1.10)
Т2 = 24 * 103 * 5 * 0,98 * 0,99 = 116,4 * 103 Нмм
Частоты вращения и угловые скорости валов
Таблица 1 – Частоты вращения и угловые скорости валов
Частота вращения | Угловая скорость | |
Вал В | n1 = nдв = 1429,5 об/ мин | w1 = wдв = 149,6 рад/с |
Вал С | n2 = n1 / Uр = 285,9 об/мин | w2 = w1 / Uр = 30 рад/с |
Вал А | nБ = 76,4 об/мин | wБ = 8 рад/с |
Расчет зубчатых колес редуктора
Определим суммарное число зубьев
Из рекомендованных значений b = 8…20° предварительно назначим угол наклона зубьев b = 10°
(2.8)
Принимаем z1 = 16, тогда z2 = z1 · u = 16 · 5 = 80
Фактическое передаточное число:
u = z2 / z1= 80 / 16 = 5
2.9. Уточняем значение угла наклона зубьев:
(2.9)
Угол наклона зубьев b = 16,260 = 160 15’
Основные размеры шестерни и колеса
делительные диаметры:
d1 = mn · z1 / cos b d1 = 2 · 16 / 0,96 = 33,3 мм
d2 = mn · z2 / cos b d2 = 2 · 80 / 0,96 = 166,7 мм
диаметры вершин зубьев:
dа1 = d1 + 2 mn dа1 = 33,3 + 2 · 2 = 37,3 мм
dа2 = d2 + 2 mn dа2 = 166,7 + 2 · 2 = 170,7 мм
диаметры впадин зубьев:
df1 = d1 – 2,5 · mn df1 = 33,3 – 2,5 · 2 = 28,3 мм
|
df2 = d2 – 2,5 · mn df2 = 166,7 – 2,5 · 2 = 161,7 мм
Проверка: аw = d1 + d2 / 2 = 33,3 + 166,7 / 2 = 100 мм
2.11. Ширина колеса и шестерни:
b2 = yba · аw (2.10)
b2 = 0,5 · 100 = 50 мм
b1 = b2 + 5 мм (2.11)
b1 = 50 + 5 мм = 55 мм
2.12. Коэффициент ширины шестерни по диаметру:
ybd = b1 / d1 (2.12)
ybd = 55 / 33,3 = 1,65
Окружная скорость колес
v = w1 · d1 / 2 (2.13)
v = 149,6 · 33,3 / 2 · 103 = 2,49 м/с
Степень точности передачи для косозубых колес при скорости до 10 м/с 8-ая
2.14. Коэффициент нагрузки:
KH = KHb · KHa · KHv (2.14)
KHb = 1,04 таб. 3.5 [1, стр. 39] при твердости НВ < 350, ybd = 1,65 и симметричном расположении колес
KHa = 1,073 таб. 3.4 [1, стр. 39] при v = 2,49 м/с и 8-й степени точности
KHv = 1,0 таб. 3.6 [1, стр. 40] при скорости менее 5 м/с
KH = 1,04 · 1,073 · 1,0 = 1,116
2.15. Проверяем контактные напряжения по формуле:
(2,15)
что менее [sH] = 410 МПа. Условие прочности выполняется.
2.16. Силы, действующие в зацеплении:
Окружная сила:
Ft = 2 · Т2 / d2 (2.16)
Ft = 2 · 116,4 · 103 / 166,7 = 1396,5 Н
Осевая сила:
Fа = Ft · tg b (2.17)
Fа = 1396,5 · tg 160 15’ = 407,3 Н
Радиальная сила:
Fr = Ft · tg a / cos b (2.18)
Fr = 1396,5 · tg 200 / 0,96 = 529,5 Н
2.17. Проверим зубья на выносливость по напряжениям изгиба:
(2.19)
KFb = 1,1 таб. 3.7 [1, стр. 43] при твердости НВ < 350, ybd = 1,65 и симметричном расположении колес
KFv = 1,26 таб. 3.8 [1, стр. 43] при скорости менее 3 м/с и 8-й степени точности
Тогда: KF = KFb · KFv = 1,1 · 1,26 = 1,386
Коэффициент, учитывающий форму зуба, YF зависит от эквивалентного числа зубьев zv:
для шестерни zv1 = z1 / cos3 b = 16 / 0,963» 18
для колеса zv2 = z2 / cos3 b = 80 / 0,963» 90
Коэффициенты YF1 = 4,2 и YF2 = 3,60 см. [1, стр. 42]
Допускаемое напряжение:
По таблице 3.9 для стали 45 улучшенной при твердости НВ≤350
1.8НВ.
Для шестерни 1,8 * 230 = 415 МПа;
для колеса 1,8 * 200 =360 МПа.
- коэффициент безопасности, где
= 1,75,
= 1. Следовательно,
= 1,75
Допускаемые напряжения:
для шестерни [σF1] = 415 / 1,75 = 237 МПа
для колеса [σF2] = 360 / 1,75 = 206 МПа
Находим отношения :
для шестерни: 237 / 4,2 = 56,4 МПа
для колеса: 206 / 3,60 = 57,2 МПа
Определяем коэффициенты Yb и KFa:
где n = 8 – степень точности;
ea = 1,5 – средние значения коэффициента торцового перекрытия
Проверку на изгиб проводим для шестерни, т.к. она менее прочная
Условие прочности выполняется.
Таблица 3 – Параметры зубчатой цилиндрической передачи
Параметр, обозначение | Величина |
Межосевое расстояние aw | 100 мм |
Нормальный модуль mn | 2 мм |
Делительный диаметр шестерни d1 колеса d2 | 33 мм 167 мм |
Число зубьев шестерни z1 колеса z2 | 16 80 |
Передаточное отношение u | 5 |
Ширина зубчатого венца шестерни b1 колеса b2 | 55 мм 50 мм |
Диаметр окружности вершин шестерни dа1 колеса dа2 | 37 мм 171 мм |
Параметр, обозначение | Величина |
Диаметр окружности впадин шестерни df1 колеса df2 | 28 мм 162 мм |
Угол наклона зубьев b | 16015’ |
|
Предварительный расчет валов редуктора
Предварительный расчет проведем на кручение по пониженным допускаемым напряжениям.
3.1. Определим диаметр выходного конца ведущего вала:
(3.1)
где [tк] = 25 МПа допускаемое напряжение на кручение
Т1 = Т2 / u = 116,4 / 5 = 23,28 Н·м
Так как вал редуктора соединён муфтой с валом электродвигателя, то у подобранного электродвигателя [1. табл. П2] диаметр вала 18 мм. Выбираем МУПВ по ГОСТ 21424-75 с расточками полумуфт под dДВ = 18 мм и dВ1 = 16 мм
Длина посадочного места под полумуфту:
lМ1 = (1,0…1,5) · dВ1 (3.2)
lМ1 = (1,0…1,5) · 16 = 16…24 мм
Принимаем значение lМ1 = 18 мм
Диаметр вала под уплотнение крышки и подшипник:
dП1 = dВ1 + 2 · t (3.3)
где t = 2,0 мм - таб. 7.1 [2, стр. 109]
dП1 = 16 + 2 · 2,0 = 20 мм
Принимаем стандартное значение [1, стр. 161] dП1 = 20 мм
Посадочное место под первый подшипник:
lП1= 1,5 · dп1 (3.4)
lП1 = 1,5 · 20 = 30 мм
Принимаем стандартное значение lП1 = 30 мм
Диаметр вала под шестерню:
dШ1 = dП1 + 3,2 · r (3.5)
где r = 1,6 мм - таб. 7.1 [2, стр. 109]
dШ1 = 20 + 3,2 · 1,6 = 25,12 мм
Принимаем стандартное значение dШ1 = 25 мм
Посадочное место под шестерню не определяется, так как её рекомендуется изготавливать заодно с валом
Посадочное место под второй подшипник:
lП2 = В или lП2 = Т
где В и Т – ширина подшипника в зависимости от типа
3.2. Определим диаметр выходного конца ведомого вала:
(3.6)
где [tк] = 25 МПа допускаемое напряжение на кручение
Так как ведомый вал редуктора соединён муфтой валом цепной передачи, то у редуктора диаметр вала 28 мм. Выбираем с расточками полумуфт под dВ2 = 28 мм и dЦ = 25 мм
Длина посадочного места под полумуфту:
|
lМ2 = (1,0…1,5) · dВ2 (3.7)
lМ2 = (1,0…1,5) · 28 = 28…42 мм
Принимаем значение lМ2 = 26 мм
Диаметр вала под уплотнение крышки и подшипник:
dП2 = dВ2 + 2 · t (3.8)
где t = 2,2 мм - таб. 7.1 [2, стр. 109]
dП2 = 28 + 2 · 2,2 = 32,4 мм
Принимаем стандартное значение [1, стр. 161] dП2 = 35 мм
Посадочное место под первый подшипник:
lП2 = 1,5 · dП2 (3.9)
lП2 = 1,5 · 35 = 52,5 мм
Принимаем стандартное значение lП2 = 50 мм
Диаметр вала под колесо:
dК2 = dП2 + 3,2 · r (3.10)
где r = 2,5 мм - таб. 7.1 [7, стр. 109]
dК2 = 35 + 3,2 · 2,5 = 43,0 мм
Принимаем стандартное значение dК2 = 42 мм
Посадочное место под второй подшипник:
lП3 = В или lП3 = Т
где В и Т – ширина подшипника в зависимости от типа
Диаметры остальных участков валов назначают исходя из конструктивных соображений при компоновке редуктора.
Выбираем подшипники
Принимаем радиальные шариковые однорядные подшипники лёгкой серии по ГОСТ 8338 – 75, размеры подшипников выбираем по диаметру вала в месте посадки: ведущий вал dП1 = 20 мм и ведомый вал dП2 = 35 мм.
По таб. П3 [1, стр. 392] имеем:
Таблица 4 – Подшипники (предварительный выбор)
Условное обозначение подшипника | d | D | B | R | Грузоподъемность, кН | |
Размеры, мм | С | С0 | ||||
204 | 20 | 47 | 14 | 1,5 | 12,7 | 6,2 |
207 | 35 | 72 | 17 | 2,0 | 25,5 | 13,7 |
Расчет цепной передачи
Ведущий вал.
Из предыдущих расчетов имеем Ft = 1396,5 Н, Fа = 407,3 Н, Fr = 529,5 Н; Из первого этапа компоновки l1 = l2 = 46,5 мм.
Реакции опор:
в плоскости xz
Rx1 = Rx2 = Ft / 2 = 1396,5 / 2 = 698,25 H
в плоскости yz
Ry1 + Ry2 - Fr = 337 + 162,5 - 529,5 = 0
Суммарные реакции
Подбираем подшипники по более нагруженной опоре 1.
Суммарные реакции
Подбираем подшипники по более нагруженной опоре 1.
Расчет шпоночных соединений
Уточненный расчет валов.
Быстроходный вал
10.1. Так как быстроходный вал изготовляют вместе с шестерней, то его материал известен – сталь 45, термообработка – улучшение.
По таб. 3.3 [1, стр. 34] при диаметре заготовки до 90 мм (в нашем случае dа1 = 37 мм) среднее значение sв = 780 МПа
Предел выносливости при симметричном цикле изгиба:
s-1» 0,43 · sв (10.1)
s-1 = 0,43 · 780 = 335 МПа
Предел выносливости при симметричном цикле касательных напряжений:
t-1» 0,58 · s-1 (10.2)
t-1 = 0,58 · 335 = 193 МПа
Сечение А – А.
Это сечение при передаче вращающего момента от электродвигателя через муфту рассчитываем на кручение. Концентрацию напряжений вызывает наличие шпоночной канавки.
Коэффициент запаса прочности по касательным напряжениям:
(10.3)
где амплитуда и среднее напряжение отнулевого цикла
(10.4)
При d = 16 мм, b = 5 мм, t1 = 3 мм по таб. 8.9 [1, стр. 169]
Принимаем: kt = 1,68 по таб. 8.5 [1, стр. 165], et = 0,83 по таб. 8.8 [1, стр. 166], yt = 0,1 см [1, стр. 164 и 166].
|
Сечение А – А.
Диаметр вала в этом сечении 20 мм. Концентрация напряжений обусловлена посадкой подшипника с гарантированным натягом: ks/es = 3,0, kt/et = 2,2 по таб. 8.7 [1, стр. 166]. Коэффициенты ys = 0,2; yt = 0,1 см.
Изгибающий момент МИ = 172,1 Н·м. Крутящий момент Т1 = 75,3 Н·м.
Осевой момент сопротивления:
(10.6)
мм3
Амплитуда нормальных напряжений:
(10.7)
Полярный момент сопротивления:
WP = 2 · W = 2 · 4,2 · 103 = 8,4 · 103 мм3
Амплитуда и среднее напряжение цикла касательных напряжений:
(10.8)
Коэффициент запаса прочности по нормальным напряжениям:
(10.9)
Коэффициент запаса прочности по касательным напряжениям:
(10.5)
Результирующий коэффициент запаса прочности на участке А – А:
(10.10)
Прочность на данном участке обеспечена.
Так как на участке А – А действует наибольший изгибающий и крутящий моменты при диаметре 35 мм и прочность обеспечивается, то проверка прочности других участков с большим диаметром и меньшими действующими изгибающими моментами не требуется.
Тихоходный вал
Сечение Д – Д.
Диаметр вала в этом сечении 40 мм. Концентрация напряжений обусловлена наличием шпоночной канавки: ks = 1,6, kt = 1,5 по таб. 8.5 [6, стр. 165]. Масштабные факторы: es = 0,78; et = 0,66 по таб. 8.8 [6, стр. 166]. Коэффициенты ys = 0,15; yt = 0,1 см [6, стр. 163 и 166].
Изгибающий момент МИ = 0 Крутящий момент Т1 = 301,2 Н·м.
Момент сопротивления кручению:
(10.3)
где d = 40 мм, b = 12 мм, t1 = 5 мм размеры шпонки по таб. 8.9 [6, стр 169]
Амплитуда и среднее напряжение цикла касательных напряжений:
Коэффициент запаса прочности по касательным напряжениям:
Прочность на данном участке обеспечена.
Сечение С – С.
Диаметр вала в этом сечении 55 мм. Концентрация напряжений обусловлена посадкой ступицы зубчатого колеса: ks/es = 3,3, kt/et = 2,38 по таб. 8.7 [6, стр. 166]. Коэффициенты ys = 0,15; yt = 0,1 см.
Изгибающий момент МИ = 98 Н·м. Крутящий момент Т1 = 301,2 Н·м.
Осевой момент сопротивления:
мм3
Амплитуда нормальных напряжений:
Полярный момент сопротивления:
WP = 2 · W = 2 · 16,3 · 103 = 32,6 · 103 мм3
Амплитуда и среднее напряжение цикла касательных напряжений:
Коэффициент запаса прочности по нормальным напряжениям:
Коэффициент запаса прочности по касательным напряжениям:
Результирующий коэффициент запаса прочности на участке А – А:
Прочность на данном участке обеспечена.
Так как на участке С – С действует наибольший изгибающий и крутящий моменты и прочность участка обеспечивается, то проверка прочности других участков с меньшими действующими изгибающими моментами не требуется.
Выбор масла
Смазывание зубчатого зацепления производится окунанием шестерни в масло, заливаемое внутрь корпуса до уровня обеспечивающего погружение шестерни примерно на 12 мм. Объем масляной ванны V определим из расчета 0,25 дм3 масла на 1 кВт передаваемой мощности:
V = 0,25 · 3,24 = 0,81 дм3
По таб. 10.8 [1, стр. 253] устанавливаем вязкость масла. При контактных напряжениях sН = 410 МПа и скорости 2,49 м/с рекомендуемая вязкость масла должна быть примерно равна 28 · 10-6 м2/с. По таблице 10.10 [1, стр. 253] принимаем масло индустриальное И – 30 А по ГОСТ 20799 – 75.
Камеры подшипников заполняем пластичным смазочным материалом УТ – 1 (см. таб. 9.14), периодически пополняем его шприцем через пресс-масленки.
Сборка редуктора
Литература
1. Курсовое проектирование деталей машин: Учеб. пособие для учащихся машиностроительных специальностей техникумов / С.А. Чернавский, К.Н. Боков, И.М. Чернин и др. - М.: Машиностроение, 1988. – 416 с., ил.
2. Шейнблит А.Е. Курсовое проектирование деталей машин: Учеб. пособие для техникумов. – М.: Высш. шк., 1991. – 432 с., ил.
3. Дунаев П.Ф., Леликов О.П. Детали машин. Курсовое проектирование. Учеб. пособие для техникумов. – М.: Высш. шк., 1990.
4. Дунаев П.Ф., Леликов О.П. Конструирование узлов и деталей машин: Учеб. пособие для техн. спец. вузов. – М.: Высш. шк., 1998. – 447 с., ил.
5. Иванов М.Н. Детали машин: Учебник для студентов машиностроительных специальностей вузов. – М.: Высш. шк., 1998.
6. Кудрявцев В.Н. Детали машин: Учебник для студентов машиностроительных специальностей вузов. – Л.: Машиностроение, 1980. – 464 с., ил.
7. Детали машин: Атлас конструкций / Под ред. Д.Н. Решетова. В двух частях. – М.: Машиностроение, 1992.
Кафедра конструирования и стандартизации машиностроения
Допускаю к защите
Руководитель Тумаш Александр
Михайлович
|
|
Папиллярные узоры пальцев рук - маркер спортивных способностей: дерматоглифические признаки формируются на 3-5 месяце беременности, не изменяются в течение жизни...
Индивидуальные очистные сооружения: К классу индивидуальных очистных сооружений относят сооружения, пропускная способность которых...
Наброски и зарисовки растений, плодов, цветов: Освоить конструктивное построение структуры дерева через зарисовки отдельных деревьев, группы деревьев...
Биохимия спиртового брожения: Основу технологии получения пива составляет спиртовое брожение, - при котором сахар превращается...
© cyberpedia.su 2017-2024 - Не является автором материалов. Исключительное право сохранено за автором текста.
Если вы не хотите, чтобы данный материал был у нас на сайте, перейдите по ссылке: Нарушение авторских прав. Мы поможем в написании вашей работы!