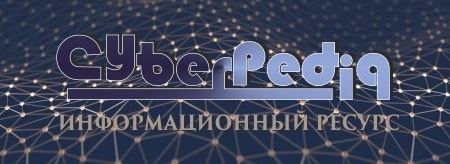
Индивидуальные и групповые автопоилки: для животных. Схемы и конструкции...
Папиллярные узоры пальцев рук - маркер спортивных способностей: дерматоглифические признаки формируются на 3-5 месяце беременности, не изменяются в течение жизни...
Топ:
Марксистская теория происхождения государства: По мнению Маркса и Энгельса, в основе развития общества, происходящих в нем изменений лежит...
Отражение на счетах бухгалтерского учета процесса приобретения: Процесс заготовления представляет систему экономических событий, включающих приобретение организацией у поставщиков сырья...
Процедура выполнения команд. Рабочий цикл процессора: Функционирование процессора в основном состоит из повторяющихся рабочих циклов, каждый из которых соответствует...
Интересное:
Как мы говорим и как мы слушаем: общение можно сравнить с огромным зонтиком, под которым скрыто все...
Подходы к решению темы фильма: Существует три основных типа исторического фильма, имеющих между собой много общего...
Что нужно делать при лейкемии: Прежде всего, необходимо выяснить, не страдаете ли вы каким-либо душевным недугом...
Дисциплины:
![]() |
![]() |
5.00
из
|
Заказать работу |
Предварительное раскисление металла производят в ковше, непосредственно при выпуске, присадкой алюминия для снятия переокисленности металла и производят науглероживание вдуванием коксовой мелочи под струю. Выпуск металла производится при достижении температуры не ниже 1630ºС. При выпуске металла из печи производится отсечка шлака с помощью скриммерного желоба.
Присадка ферросплавов в ковш во время продувки позволяет достичь большей их экономии за счет более высокой степени усвоения легирующих элементов, достигающей для большинства элементов по многочисленным литературным данным величины более 90%.
При выпуске металла из печи содержание углерода в стали равно 0,04. По содержанию углерода по эмпирической формуле легко найти массовую долю растворенного кислорода в стали [О].
аО = \0,00252 + 0,0032/[С] (23)
где [С] - содержание углерода в металле перед выпуском из печи,
массов. доли, %
аО = [О] (24)
[О] = 0,00252 + 0,0032/0,4 = 0,011%
Раскисление стали алюминием проходит по реакции:
2[Al] + 3[O] = (Al2O3) (25)
K = a2Al · a3 o/aA1203 (26)
a2Al · a3o = K · aA1203 ≈ K’
где aAl и ao – активности алюминия и кислорода в металле;
К – константа равновесия реакции;
aA1203 – активность глинозема в шлаковой фазе.
При преобразовании чистого Al2O3 можно принять aA1203 = 1
Для связывания 0,011% кислорода потребуется алюминия 0,012%.
В процессе выпуска металла основная задача сводится к тому, чтобы раскислить сталь. Поэтому на выпуске вводим чушкового алюминия, с учетом угара 30% в количестве 0,017 кг/100 кг стали или 42,5 кг/плавку.
Для науглероживания будем применять коксик следующего состава:
S – 0,05%, C – 82%
Коксик = 1000 · (0,36 – 0,04)/82 · 0,5 = 7,8 кг/т.
На всю выплавку необходимо 1950 кг. Внесет S = 0,00039%
В процессе внепечной обработки легируем ферромарганцем ФМи75, ферросилицием ФС85, феррохром ФХ800 (химический состав ферросалавов приведен в таблице 15). Ферросилиций, феррохром и ферромарганец присаживаются в ковш во время продувки.
Таблица 15 – Химический состав ферросплавов
Ферросплав | Массовая доля элементов, % | |||||||
С | Mn | Si | Cr | S | P | H | N | |
1 | 2 | 3 | 4 | 5 | 6 | 7 | 8 | 9 |
ФC 75 | 0,1 | - | 65,0 | - | 0,03 | 0,05 | 0,0008 | 0,001 |
ФМн 75 | 7,0 | 76,0 | 2,0 | - | 0,03 | 0,45 | 0,0020 | 0,020 |
ФХ 800 | 0,5 | 2,0 | 2,0 | 65 | 0,05 | 0,08 | 0,0005 | 0,004 |
Содержание остаточной массовой доли легирующих и примесей в стали перед легированием составляет марганца – 0,088%, кремния – следы, углерода – 0,36%, серы – 0,012%, фосфора – 0,011%, хрома – 0,3%.
Требуемое количество массовых долей элементов в готовой стали: марганца -0,6%, кремния – 0,28%, углерода – 0,36%, серы – 0,015%, фосфора – 0,015%, хром – 0,9%.
Необходимое количество ферросплавов для легирования стали определяем по формуле:
ФСпл = М · ∆ [Эл] / η · с (27)
где ФСпл – количество вводимого ферросплава, кг/т стали;
М – масса металла, кг;
∆ [Эл] - массовая доля элемента, которую необходимо внести, %;
η – степень усвоения ферросплава;
с – содержание элемента в ферросплаве, масс. доли, %
Требуется внести с ферромарганцем 0,592% марганца. Степень усвоения ферромарганца в ковше составляет 95%. Необходимое количество ферромарганца
ФМн 75 = 1000 · 0,592/0,95 · 76 = 8,0 кг/т стали;
ФМн 75 = 8,0 кг/т жидкой стали или 2000 кг. на плавку.
Требуется внести с ферросилицием 0,28% кремния. Степень усвоения ферросилиция в ковше при пульсирующей продувке составляет 92%. Необходимое количество ферросилиция
ФС75 = 1000 · 0,28/0,92 · 80 = 3,9 кг/т стали;
ФС75 = 4,05 кг/т жидкой стали или 1012,5 кг. на плавку.
Требуется внести с феррохромом 0,6% хрома. Степень усвоения феррохрома в ковше при продувке составляет 98%. Необходимое количество феррохрома
ФХ800 = 1000 · 0,6/0,98 · 65 = 9,41 кг/т стали
ФХ800 = 9,41 кг/т жидкой стали или 2352 кг. на плавку.
Количество внесенных элементов с ферросплавами показаны в таблице 16.
Таблица 16 – Количество внесенных элементов с ферросплавами
Ферросплав | Содержание вносимых элементов, массов. доля, % | |||||
С | Сr | Мn | Si | S | P | |
1 | 2 | 3 | 4 | 5 | 6 | 7 |
ФМн75 | 0,0570 | - | 0,59200 | 0,016 | 0,00020 | 0,0036 |
ФХ800 | 0,0090 | 0,6 | - | 0,019 | 0,00050 | 0,0003 |
ФС75 | 0,0008 | - | 0,0016 | 0,280 | 0,00008 | 0,0002 |
После легирования сталь будет иметь химический состав, который показан в таблице 17.
Таблица 17 – Химический состав стали после легирования и науглероживания
С | Mn | Si | P | S | Cr |
0,42 | 0,68 | 0,315 | 0,015 | 0,0127 | 0,9 |
2.2.8 Изменение температуры в процессе внепечной обработки металла
В процессе производства стали без дополнительного подогрева на технологических стадиях между выпуском металла и разливки на МНЛЗ, температура металла все время уменьшается.
Температуру металла в печи перед выпуском можно найти из соотношения
Твып = ∆Т1 + ∆Т2 + ∆Т3 + ∆Т4 + ∆Т5 (28)
где ∆Т1 – падение температуры стали при выпуске из печи, ºС;
∆Т2 - падение температуры стали при транспортировке стальковша до стенда
продувки, ºС;
∆Т3 - падение температуры стали при продувке в ковше, ºС;
∆Т4 - падение температуры стали при транспортировке стальковша от стенда до
МНЛЗ, ºС;
∆Т5 - заданная температура в промковше, ºС.
Падение температуры при выпуске стали из печи за счет излучения струи металла в атмосферу цеха и нагрев футеровки ковша и ввода ТШС составляет 60ºС.
Падение температуры стали при транспортировке стальковша до стенда и от стенда до МНЛЗ можно принять равным 20ºС.
При продувке и с учетом ввода ферросплавов температура металла падает на 20ºС.
Необходимая температура металла в стальковше перед разливкой
Тс.к = Тлик + Тп.к. + Ткр + 20 (29)
где Тлик – температура ликвидус стали, ºС;
Тп.к – температура стали в промковше, ºС;
Ткр – температура в кристаллизаторе, ºС.
Тлик = 1539 - 79[С] - 12[Si] - 5[Mn] - 25[S] - 30[P] + 2,7[Al] (30)
Тлик = 1539 – 79,0 · 0,17 – 12 · 0,5 – 5 · 1,38 – 25 · 0,04 – 30 · 0,035 + 2,7 · 0,03 =
= 1501ºС
Тс.к = 1501 + 10 + 20 + 20 = 1551ºС
Теперь легко подсчитать, что без принятия мер по дополнительному подогреву, температура стали на выпуске из ДПСА должна составлять
Твып = 60 + 20 + 20 + 1551 = 1650ºС
При необходимости сталь подогревают перед разливкой на МНРС химическим подогревом. Химический нагрев – это нагрев металла тепловым эффектом экзотермических реакций окисления элементов, растворенных в расплаве. Основными такими элементами являются алюминий и кремний. При окислении алюминия температура расплава может повышаться с максимальной скоростью 2-4ºС мин. Недостатками этого метода является значительное загрязнение стали неметаллическими включениями и невысоким коэффициентом полезного действия.
2.2.9 Разработка МНЛЗ
Выбор типа МНЛЗ
Для выпуска тонкого листа выбирается заготовка сечением 50 х 1200 мм. Принимается время разливки равное 90 мин., т.к. оптимальный вариант, когда время разливки равно времени плавки в ДПСА.
Найдем скорость разливки. Она определяется по формуле:
(31)
где ω – скорость разливки, м/мин;
М – масса металла в ковше, кг;
N – количество ручьем;
τ – допустимое время разливки, мин;
ρ – плотность стали, кг/м3;
φ – коэффициент, учитывающий потери времени при разливке.
ω = 210 ·/(1 · 0,05 · 1,2 · 7,65 · 90) = 5,1 м/мин.
Металлургическая длина машины определяется по формуле:
L = 300 · a2 · ω (32)
L = 1,1 · 0,052 · 5,1/(22 · 0,0252) = 5,61 м
Исходя из этого выбираем вертикальную машину с загибом. Управление для оценки допустимого базового радиуса технологической оси МНЛЗ записывается /9/.
(33)
Производительность МНЛЗ.
Производительность МНЛЗ рассчитывается по формуле:
(34)
где Р1 – пропускная способность при отливке заготовки определенного сечения,
т/год;
n – количество плавок в серии при разливке методом плавка на плавку
(принимаем n = 15 плавок);
М – масса металла, т;
Ф – фонд времени работы МНЛЗ, сут;
τ1 – время разливки стали из сталеразливочного ковша, мин;
τ2 – время подготовки машины к приему плавки без изменения размеров слитка,
мин.
Принимаем τ1 = 90 мин, τ2 = 40 мин.
Ф = 365 – (Тк + Тпп + Тт), (35)
где Тк – продолжительность капитального ремонта установки, 10 сут.;
Тпп – продолжительность планово-предупредительных ремонтов, 17 сут.;
Тт – продолжительность текущих ремонтов, 30 сут.
Тогда
Ф = 365 – (10 + 17 + 30) = 308 сут.
Производительность МНЛЗ равна:
Специальная часть
Индивидуальные очистные сооружения: К классу индивидуальных очистных сооружений относят сооружения, пропускная способность которых...
Типы сооружений для обработки осадков: Септиками называются сооружения, в которых одновременно происходят осветление сточной жидкости...
Таксономические единицы (категории) растений: Каждая система классификации состоит из определённых соподчиненных друг другу...
Историки об Елизавете Петровне: Елизавета попала между двумя встречными культурными течениями, воспитывалась среди новых европейских веяний и преданий...
© cyberpedia.su 2017-2024 - Не является автором материалов. Исключительное право сохранено за автором текста.
Если вы не хотите, чтобы данный материал был у нас на сайте, перейдите по ссылке: Нарушение авторских прав. Мы поможем в написании вашей работы!