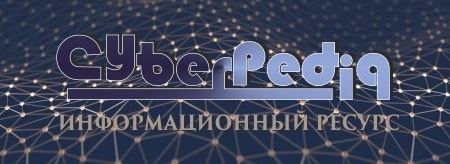
Папиллярные узоры пальцев рук - маркер спортивных способностей: дерматоглифические признаки формируются на 3-5 месяце беременности, не изменяются в течение жизни...
Особенности сооружения опор в сложных условиях: Сооружение ВЛ в районах с суровыми климатическими и тяжелыми геологическими условиями...
Топ:
Теоретическая значимость работы: Описание теоретической значимости (ценности) результатов исследования должно присутствовать во введении...
Выпускная квалификационная работа: Основная часть ВКР, как правило, состоит из двух-трех глав, каждая из которых, в свою очередь...
Проблема типологии научных революций: Глобальные научные революции и типы научной рациональности...
Интересное:
Принципы управления денежными потоками: одним из методов контроля за состоянием денежной наличности является...
Распространение рака на другие отдаленные от желудка органы: Характерных симптомов рака желудка не существует. Выраженные симптомы появляются, когда опухоль...
Подходы к решению темы фильма: Существует три основных типа исторического фильма, имеющих между собой много общего...
Дисциплины:
![]() |
![]() |
5.00
из
|
Заказать работу |
|
|
ОСНОВНЫЕ ПОЛОЖЕНИЯ
1.1 Основными условиями осуществления
нормального процесса непрерывной разливки стали на МНЛЗ являются:
1.1.1 Подготовка металла к разливке в соответствии с действующими технологическими инструкциями и указаниями по выплавке и внепечной обработке на конкретную марку стали.
1.1.2 Подготовка и проверка всех узлов и
механизмов МНЛЗ, КИП и систем автоматического управления процессом разливки, а также выполнение текущих и плановых ремонтов в соответствии с действующими производственно техническими инструкциями.
1.1.3 Тщательная подготовка сталеразливочных, промежуточных ковшей в соответствии с
действующими технологическими, производственно-техническими инструкциями и технологическими указаниями.
1.1.4 Использование при разливке в кристаллизаторе шлакообразующей смеси, обеспечивающей нормальную разливку стали в диапазоне скоростей от 0,2 до 1,0 м/мин.
1.1.5 Выполнение технологических операций, предусмотренных настоящей инструкцией, технологическими указаниями, производственно-техническими и инструкциями по технике безопасности.
1.1.6 Своевременная подача на МНЛЗ для
разливки ковшей с подготовленным металлом.
1.1.7 Использование при разливке стали
огнеупорных защитных труб, стопоров и погружных стаканов, соответствующих требованиям стандартов и технических условий.
1.2 Подготовка МНЛЗ к работе и разливке стали осуществляется под руководством сменного мастера производственного участка машины непрерывного литья заготовок.
1.3 Основным режимом разливки стали является разливка стали под управлением УРОВНЯ 2 автоматизации:
-управление вторичным охлаждением;
-порезка на мерные заготовки;
|
-маркировка заготовок;
-работа с системой слежения за качеством продукта CAQC;
-оптимизация закрытия ручьев;
-формирование достоверного общего паспорта плавки.
Данный режим обеспечивает наиболее качественную разливку металла.
Для рядовых марок стали разрешается разливка в режиме ручного управления.
1.4 Режим разливки в автоматическом режиме под управлением базисной автоматики
(УРОВЕНЬ 1)и режим ручного управления используется при невозможности применения режима управления разливкой под управлением УРОВНЯ 2 (аварийные ситуации, выходы из строя датчиков, оборудования и т.д.).
1.5 Разливка стали на МНЛЗ марок с повышенными требованиями по качеству (трубный, качественный для холодной штамповки и т.д.) без использования УРОВНЯ 2 автоматизации, считается как разливка с нарушением технологии.
1.6 Краткая техническая характеристика МНЛЗ:
1.6.1 Тип машины - криволинейная с вертикальным кристаллизатором с загибом и разгибом слитка.
1.6.2 Количество ручьев - комбин. 2/4
1.6.3 Размеры отливаемых заготовок:
слябы, мм 240х1250 до 1515
длиной от 3700-9000,
сортовые заготовки, мм 240 х (310-575)
длиной 3700-11400.
1.6.4 Скорость разливки, м/мин 0,2-1,4
1.6.5 Металлургическая длина МНЛЗ, м 31,3
1.6.6 Высота кристаллизатора, мм 1000
1.6.7 Длина вертикального
участка зоны вторичного охлаждения, мм 1580
1.6.8 Длина участка загиба ЗВО, мм 1920
1.6.9 Длина радиального участка
ЗВО, мм 8080
1.6.10 Длина криволинейного участка
ЗВО, мм 6630
1.6.11 Длина горизонтального участка
ЗВО, мм 12090
1.6.12 Базовый радиус радиального участка ЗВО, мм 8000
1.6.13 Расстояние между ручьями, м 5
1.6.14 Емкость сталеразливочного
ковша, т 160
|
1.6.15 Емкость промежуточного
ковша, т 35
1.6.16 Рабочий уровень металла в промежуточном ковше, мм 1100
1.6.17 Высота подъема сталеразливочного ковша, мм 850
1.6.18 Высота подъема промежуточного ковша, мм 550
1.6.19 Отметка разливочной площадки, мм
+ 12600
1.6.20 Отметка верха бочки роликов рольганга, мм + 1050
1.6.21 Частота качания кристаллизатора, подъемов в мин. 20-180
1.6.22 Амплитуда качания, мм 4
1.6.23 Минимальная длина заготовок с МНЛЗ, мм 3700
1.6.24 Максимальная длина заготовок МНЛЗ, мм 11400
1.6.25 Ход МГР по эстакаде, м
рабочий 5,8
максимальный 6,0
1.6.26 Скорость перемещения МГР по эстакаде, м/мин: при резке 0,2-1,4
при возврате 30
1.6.27 Ход резака максимальный, мм:
при резке сортовых заготовок 815
при резке слябов 1005
1.6.28Скорость перемещения резака, мм/мин
при резке 30-600
при возврате 3900
1.6.29 Участок обрезки головных и донных концов и заготовок для темплетов длина обрезамых концов слябов:
головных, мм 500
донных, мм 800
длина обрезаемых концов сортовых заготовок:
головных, мм 500
донных, мм 2000
толщина заготовок темплетов, мм 35-40
усилие сталкивателя, кг, не менее 2000
скорость перемещения МГР:
по эстакаде, м/мин 3
рабочий ход МГР, мм 250
полный ход МГР, мм 1600
скорость перемещения резака, м/мин:
при врезании 60
при резке 60-320
при возврате в исходное положение 1600
1.6.30 Скорость разливки, м/мин:
сечение, мм максимальная рабочая
|
240х310 (4р.) 1,40 1,0-1,2
240х360 (4р.) 1,27 0,8-1,0
240х400 (4р.) 1,15 0,7-1,1
240х440 (4р.) 1,10 0,6-1,1
240х485 (4р.) 1,10 0,6-1,1
240х575 (4р.) 0,90 0,6-0,9
240х1250 (2р.) 1,00 0,6-1,0
240х1500 (2р.) 0,90 0,6-0,9
240х1515(2р) 0,90 0,6-0,9
ПОДГОТОВКА МЕТАЛЛА К
НЕПРЕРЫВНОЙ РАЗЛИВКЕ
2.1 Для разливки на МНЛЗ №2 подается металл после корректировки его химического состава и температуры на установке "печь-ковш" или вакууматоре. Допускается корректировка по температуре (при работе без установки "печь-ковш") слябой с обязательной продувкой аргоном и замером температуры.
Содержания серы и фосфора в стали должна соответствовать требованиям, указанным в таблице1.
Таблица 1 - Содержания серы и фосфора в стали
для разливке на МНЛЗ
Углеродистая сталь | Конструкционная, низколегированная и легированная сталь | ||
сера | фосфор | сера | фосфор |
не более | не более | ||
% | % | % | % |
0,015 | 0,015 | 0,010 | 0,015 |
0,020 | 0,020 | 0,015 | 0,020 |
0,020 | 0,025 | 0,020 | 0,025 |
2.2 Температура стали, подаваемой на разливку, не должна отклоняться от номинальной более, чем на 5 ºС. Точная необходимая температура стали в сталеразливочном ковше определяется мастером разливки и согласуется с персоналом на "печи-ковше" (необходимо учесть состояние сталеразливочного ковша, температуру футеровки перед выпуском металла, качество продувки аргоном на "печи-ковше" и данную температуру стали в промковше).
2.3 Температура металла при передаче на МНЛЗ в сталеразливочном ковше и во время разливки в промежуточном ковше при производстве заготовки сечением 240х440 мм, 240х1500 мм и 240х1250мм, должна соответствовать требованиям, указанным в таблице 2.
Таблица 2
Марка стали | Температура стали, ºС | |
в сталеразливочном ковше перед подачей на МНЛЗ | в промежуточном ковше | |
1 | 2 | 3 |
Ст 1сп, Ст 2сп, 10, 10тр 08Ю, 08К, 10Ю, 12Ю, 15Ю | 1570-1580 | 1535-1550 |
Ст 3сп, 20, 20тр, 3Гсп, 14Г2, 09Г2С, 09Г2, 10Г2Ф, 13Г1Ф1, 17Г2С, 17Г1Ф1, 15Г1С | 1570-1580 | 1535-1545 |
Ст 4сп, 25,20Г2Ф, 20Г, 20Г1Ф | 1565-1575 | 1530-1540 |
Продолжение таблицы 2
1 | 2 | 3 |
Ст 5сп, 25Г, 30, 28Га, 28Гб, 27Г1 | 1560-1570 | 1525-1535 |
35, 35Г, 35Г2а, 25Г2С, 35Г2б, 35Гг | 1555-1565 | 1520-1530 |
40, 45, 45тр, 40Х, "Д", 35Г2 | 1550-1560 | 1515-1525 |
50, 50Г | 1540-1550 | 1505-1515 |
60, 60Г | 1530-1540 | 1495-1505 |
65, 65Г | 1525-1535 | 1490-1500 |
70, 70Г | 1520-1530 | 1485-1495 |
|
Примечание - Температура металла в сталеразливочном ковше при производстве заготовки сечением 240х440 мм, должна быть на 10 ºС выше указанных в таблице 2.
Температура металла в сталеразливочном ковше первой плавки в серии, при замене промковша, при разливке через 3 ручья и подаче металла на установку "печь-ковш" ковша с новой футеровкой, должна быть на 10ºС выше указанной в таблице 2.
2.4 При подготовке МНЛЗ к разливке обратить особое внимание на ввод начальной информации в АСУТП "Разливка" согласно инструкции
по эксплуатации систем автоматики.
ПОДГОТОВКА МНЛЗ К РАЗЛИВКЕ
3.1 Подготовка МНЛЗ к разливке производится под руководством сменного мастера производственного участка разливки МНЛЗ.
3.2 Перед разливкой проверяется состояние кристаллизаторов.
3.2.1 Очищаются кристаллизаторы от металла и шлака при включенной подаче воды на кристаллизатор, затем поверхность рабочих стенок обмывается водой и обдувается сжатым воздухом.
3.2.2 При рабочем расходе воды проверяется герметичность кристаллизаторов. Течь воды в рабочую полость кристаллизатора не допускается.
3.2.3 Проверяется положение кристаллизаторов на раме механизма качания. Положение
рабочей поверхности базовой стенки относительно роликов секции №1 проверяется устройством для выверки кристаллизатора, которое
прикладывается к базовой стенке кристаллизатора в двух местах на расстоянии 50-75мм от каждой узкой стенки. Допустимое отклонение должно быть не более 0,2мм.
3.2.4 Проверяется измерителем конусности уклон (конусность) и износ узких стенок кристаллизаторов. При износе низа узких стенок более 0,5мм уклон их увеличивается до получения указанного в таблице 3 размера. Расстояние между узкими стенками вверху кристаллизатора не изменяется. Разница между конусностями противолежащих узких стенок после настройки не должно превышать 0,5мм на длине стенки.
Настройка узких стенок кристаллизатора, ширины головок затравок в зависимости от ширины отливаемых заготовок указанна в таблице 3
Таблица 3
Ширина заготовок, мм | Размер кристаллизатора, мм | Ширина головки затравки, мм | |
верх | низ | ||
1 | 2 | 3 | 4 |
340 360 400 440 485 575 1250 1260 1500 1515 | 317,75 369,00 410,00 451,00 497,10 589,40 1271,0 1281,0 1522,0 1537,5 | 314,65 365,40 406,00 446,00 492,30 583,60 1256,0 1266,0 1508,0 1522,5 | 340 356 396 436 480 570 1254 1254 1496 1510 |
При износе узких стенок более чем 3мм на
сторону, кристаллизатор должен быть заменен.
3.2.5 Кристаллизатор подлежит замене если
- на рабочих стенках имеются выбоины, задиры, царапины глубиной 1,5мм;
|
- выработка широких стенок в нижней части более 0,5мм на сторону;
- зазоры в стыках рабочих стенок
более 0,1мм;
- обнаружена течь в рабочую полость.
3.3 Проверяется работа механизмов качания кристаллизатора. Механизм качания кристаллизатора должен работать плавно, без толчков и стука.
3.4 Проверяется работа устройства для установки защитной трубы.
3.5 Осматривается состояние роликов и их подшипников в зоне вторичного охлаждения.
Удаляются из зоны скрапины и окалина.
3.6 Осматривается и проверяется система охлаждения оборудования, протекания воды через все ролики и траверсы, а также через корпуса средних подшипников. Утечка воды не допускается.
3.7 Проверяется работа форсунок в каждой зоне при заданных максимальных расходах охладителя. Засоренные и дефектные форсунки заменяются новыми исправными. Проверяется попадает ли факел охладителя между роликами. После
проверки подача охладителя прекращается.
Коллектора с форсунками должны быть настроены в соответствии с шириной отливаемой
заготовки.
3.8 Проверяется состояние и чистота поддонов под кристаллизатором и секцией №1.
3.9 Осматривается и проверяется работа механического и электрического оборудования, систем смазки, гидравлики и пневматики в соответствии с инструкцией по их эксплуатации.
3.10 Проверяется исправность систем автоматики и связи, производится подготовка их к работе.
3.11 Проверяется работа машин газовой резки (МГР) и наличие воды в баках грануляции шлака.
3.12 Проверяется работа устройства для передачи заготовок (УПЗ) с приемного рольганга за МНЛЗ на рольганг транспортно отделочной линии (ТОЛ).
3.13 Проверяется работа поворотного рольганга, сталкивателя и машины газовой обрезки головных и донных заготовок.
3.14 Производится подготовка затравки:
- проверяется состояние замка, надежность крепления головки к корпусу затравки, герметичность надувных элементов, наличие и состояние прокладок;
- очищается головка затравки от остатков металла, заусениц;
- надувные элементы затравки проверяются на герметичность при давлении воздуха не менее 0,60-0,75 МПа или 6-7 кгс/см2.
Показание манометра при отсоединении воздухопровода не должны изменяться более чем
на 0,02 МПа (0,2кгс/см2) в течение 30 минут
после прекращения подачи воздуха.
3.15 Перед разливкой заготовок в 4 ручья устанавливаются на устройствах для заведения затравок подвески и клещи.
3.16 Подготовленные затравки навешиваются на устройства для заведения затравок.
3.17 Перед заведением затравок в кристаллизаторы проверяется работа всех механизмов, устанавливаются в кристаллизаторы приспособления для защиты стенок (защитные шторки).
3.18 Проверенная затравка подается устройством для заведения к кристаллизатору и заводится в него с таким расчетом, чтобы остался незаведенным конец ее длиной 150-200мм от кромки кристаллизатора. После этого рукава затравки надуваются сжатым воздухом давлением
0,60-0,75 МПа (6,0-7,5 кг/см2). После надувки рукавов затравки показание манометра при отсоединении сжатого воздуха не должны изменяться более чем на 0,02 МПа (0,2 кг/см2) в течение
30 мин после прекращения подачи воздуха.
3.19 После надува рукавов отсоединяются захваты от головки затравки и устройство для ввода затравки возвращается в положение приема затравки.
3.20 Дальнейшее заведение затравки в кристаллизаторе осуществляется с помощью приводных роликов машины со скоростью
не более 0,5м/мин.
3.21 После установки затравки в рабочее положение производятся следующие операции:
- убираются защитные шторки из кристаллизатора;
- полость кристаллизатора обдувается сжатым воздухом;
- зазоры между головкой затравки и стенками кристаллизатора заделываются асбестовым шнуром (на уровне головки или выше на 1-3мм);
- заделка асбестовым шнуром зазоров производится специальной забивалкой, на конце которой находится медная лопатка;
- на головку затравки укладываются "холодильники" - пластины, прутки толщиной 10-15мм, масса которых должна быть - для блюма 8-10кг, для сляба 15-18кг.
- поверхность стенок и углы кристаллизаторов смазываются тонким слоем густой смазки (например - смесь солидола и графита).
Категорически запрещается заводить затравку в кристаллизатор принудительными способами. Если затравка не заходит, необходимо выяснить причины и устранить выявленные
неисправности машины.
3.22 Для аварийного слива металла подготавливаются емкости и желоба. Наличие влаги,
шлака, металла в них не допускается.
3.23 На рабочей площадке перед разливкой проверяется наличие рабочего инструмента и защитной шлакообразующей смеси (ШОС) необходимого типа соответствующей требованиям стандарта предприятия СТП 102-3-99 (приложение А).
Срок хранения шлакообразующей смеси в герметичной упаковке, в железных контейнерах - не более 5суток.
При задержке в использовании ШОС
более 5 суток она должна апробироваться на содержание влаги
3.24 Подготовляются к разливке промежуточный ковш и погружные стаканы.
3.24.1 Подготовленный к плавке заторкретированный, накрытый крышками промежуточный ковш с установленными в него стопорами с участка подготовки промковшей передается в разливочное отделение.
3.24.2 Ковш устанавливается на тележку, путем повторного открывания и закрывания проверяется посадка стопора в стакан-дозатор. Стопор должен входить в лунку стакана со стороны стопорного механизма. При необходимости посадка стопора регулируется в вилке с помощью крепежных контргаек, перемещая его в вилке так, чтобы он занял необходимое положение у стакана.
3.24.3 После проверки промежуточного ковша в него опускаются горелки и производится разогрев футеровки промковша.
3.24.4 Перед включением горелок стопора устанавливаются в позицию разливки (поднимаются в верхнее положение и фиксируются). При разогреве промковша стаканы – дозаторы снизу подогреваются с помощью эжекторов, которые устанавливаются в начале разогрева промковша.
3.24.5 Разогрев футеровки промковша ведется в соответствии с требованиями технологической инструкции ТИ 102-КК-319-2000 до температуры 1100-1200ºС. Общее время нагрева должно быть не менее 3-х и не более 6 часов, при равномерном подъеме температуры.
3.24.6 При разогреве не допускается прямое попадание факела на стопор.
3.24.7 При длительности разогрева более 6 часов промковш на разливку не подается и заменяется на другой.
3.24.8 После разогрева осуществляется опробование работы стопоров.
3.24.9 Контроль за режимом разогрева и подготовкой промковша к плавке осуществляется сменным производственным мастером МНЛЗ №2.
3.24.10 Погружные корундографитовые стаканы перед разливкой разогреваются в течение
1 часа до температуры 700-900ºС. Перед разогревом визуально проверяется их целостность и геометрия.
Кварцевые стаканы используются для разливки без предварительного прогрева, но должны
иметь плюсовую температуру.
3.25 В период внепечной обработки плавки на установке "печь-ковш" или на вакууматоре сменный производственный мастер МНЛЗ проверяет окончательно готовность МНЛЗ к приему плавки, проверяет отсутствие людей в опасных зонах и сообщает на пульты управления машин
газовой резки и ТОО (транспортно-отделочного оборудования) марку стали и заданные мерные
длины заготовок.
3.26 До начала подачи сталеразливочного ковша на МНЛЗ оператор пульта №1 проверяет наличие обслуживающего персонала на рабочих
местах как на МНЛЗ, так и на ТОО и производит:
- проверку систем подачи воды, сжатого воздуха, кислорода, аргона, природного газа;
- включение вентиляторов пароотсоса из бункера вторичного охлаждения;
- установку механизмов в исходное положение;
-проверку охлаждения оборудования и при необходимости подачу воды на отдельные элементы.
Оператор ПУ-2 проверяет работу машины клеймения заготовок.
3.27 Оператор после проверки отсутствия
людей в опасных зонах закрывает входы в бункер вторичного охлаждения.
3.28 После установки сталеразливочного ковша на разливочный стенд гидроцилиндр шибера соединяется с шиберным затвором и разворотом траверсы стенда сталеразливочный ковш устанавливается в рабочую позицию с поднятием его в крайнее верхнее положение.
3.29 После установки сталеразливочного ковша в рабочую позицию промежуточный ковш с разогретой футеровкой переводится в рабочую
позицию.
Затем производится проверка центровки погружных стаканов в кристаллизаторы, стопора
расфиксируются.
Погружные стаканы устанавливаются строго вертикально. Отклонение оси стаканов от оси кристаллизаторов не должно превышать по толщине - 5мм, по ширине – 15мм.
РАЗЛИВКА СТАЛИ
4.1 Сталеразливочный ковш опускается в крайнее нижнее положение и производится открытие шиберного затвора сталеразливочного ковша и заполнение промковша металлом. Открытие шиберного затвора должно производится по команде сменного мастера производственного участка МНЛЗ или старшего разливщика.
Если после открытия шиберного затвора
металл из сталеразливочного ковша не пошел, канал сталевыпускного отверстия прожигается кислородом до появления металла. При стабилизации струи металла и наполнении промковша до 15-20 т шиберный затвор закрывается и защитная труба манипулятором устанавливается в рабочее положение, в отверстие трубы подается аргон и вновь открывается шиберный затвор. В место подвода металла присаживается 4-6 мешков перлитографитовой или другой утепляющей смеси.
4.2 При наполнении промежуточного ковша до 15т начинается наполнение кристаллизаторов. В течение 5-7 с. наполнение ведется полной струей. При этом следить, чтобы не были залиты узкие стенки кристаллизатора. Затем стопора прирабатываются.
4.3 При отливке заготовок в 4 ручья заполнение кристаллизаторов должно производится под руководством старшего разливщика стали.
Заполнение металлом обеих полостей кристаллизатора должно производиться синхронно. Разница уровней металла в обеих полостях кристаллизатора не должна быть более 50мм (определяется визуально).
Если синхронно обе полости кристаллизатора заполнить не удается, прикрывается стопор
той полости кристаллизатора, которая заполняется первой.
4.4 После того, как боковые отверстия погружного стакана при отливке слябов закроются металлом, а при отливке сортовых заготовок уровень металла в кристаллизаторе будет находиться выше низа погружного стакана на 70-120мм,в кристаллизаторы подается шлакообразующая смесь. Толщина шлакового покрытия должна составлять от 40-50 мм (определяется визуально).
При достижении уровня металла в кристаллизаторе 100-150мм от верха кромки медных плит включается привод механизма качания кристаллизаторов и вытягивания слитка на скорости 0,20 м/мин. При отливке заготовок в 4 ручья заполнение кристаллизаторов металлом производится двумя-тремя порциями. После пуска машины плавно подается аргон в стопор - моноблок.
Время от начала наполнения кристаллизатора металлом при отливке слябов до пуска машины должно составлять не менее 2 минут, при отливке заготовок в 4 ручья от 40 до 50с.
Промковш опускается в рабочее положение. Уровень металла в кристаллизаторе в процессе разливки должен составлять от 100 до 150мм от верхней кромки медных плит. Колебания уровня в процессе разливки не должно превышать 10мм.
Расстояние от мениска металла до верха сталевыпускного отверстия погружного стакана должно быть 130 мм 20 мм (определяется визуально).
4.5 При ручном управлении скорость разливки плавно за 5-6 мин доводится до 0,6м/мин.
Набор скоростей после пуска должен производится по следующему режиму, приведенному в
таблице 4.
Таблица 4
Длина отлитой заготовки, м | Скорость разливки, м/мин |
0,0-0,5 0,5-1,0 1,0-1,5 1,5-2,5 2,5-10,0 | 0,2 0,3 0,4 0,5 0,6 |
После первого замера температуры металла в промковше скорость разливки увеличивается до рабочей и осуществляется перевод на автоматический режим разливки.
Рабочие скорости разливки в зависимости от марки разливаемой стали, температуры металла в промковше должны быть в пределах 0,6-1,20 м/мин.
4.6 При разливке число качаний кристаллизатора при полном его ходе 8мм должно соответствовать приведенному в таблице 5.
Таблица 5
Скорость разливки, м/мин | 0,2-0,6 | 0,7-1,0 | более 1,1 |
число качаний в мин | 60 | 80-120 | 150 |
4.7 Вода на форсуночное охлаждение слитка в 1 и 2 зонах и на охлаждение узких граней подается после наполнения кристаллизатора металлом. До начала наполнения кристаллизатора металлом подача воды в эти зоны во избежание выброса металла запрещается.
4.8 При автоматическом управлении форсуночным охлаждением включение зон охлаждения по мере прохождения зоны вторичного охлаждения (ЗВО) и соответствие расходов охладителя скорости разливки отрабатывается без участия оператора.
При ручном управлении эти операции осуществляются с ПУ-1.
Расход воды на кристаллизатор должен соответствовать данным таблице 6.
Таблица 6
Наименование | Расход охлаждающей воды, л/мин при скорости протекания 6 м/с |
Кристаллизатор сдвоенный на широкие стенки на узкие стенки | 3833 2266 |
Кристаллизатор для слябовых заготовок на широкие стенки на узкие стенки | 4500 1133 |
Расход воды на вторичное охлаждение устанавливается в зависимости от скорости разливки и марки стали и должен соответствовать приложениям Б,В,Г.
4.9 В процессе разливки шлакообразующая смесь в кристаллизаторы подается небольшими порциями равномерно по всей площади.
Поверхность смеси в кристаллизаторе должна быть темной. Яркого свечения смеси и оголения мениска металла не допускается. Шлак на поверхности металла должен быть жидкоподвижным, гарнисаж эластичным. Не допускается при разливке образования мостов между корочкой слитка и погружным стаканом.
4.10 При смене сталеразливочного ковша, остановке ручьев и продолжительной разливке со скоростью 0,3 м/мин и менее, толщина шлакообразующей смеси в кристаллизаторе увеличивается до 40-50мм.
4.11 При выборе скоростей разливки по ручьям рекомендуется обеспечить неодновременное отделение затравок от слитков.
4.12 В процессе разливки уровень металла в промежуточном ковше должен поддерживаться на уровне 1100мм (100мм от нижнего среза аварийного носка). При замене сталеразливочного ковша допускается снижение уровня металла от номинального на 200мм (т.е. 900мм). Если в промковше после опорожнения сталеразливочного ковша окажется 15-17т металла, скорость разливки плавно снижается до 0,4 м/мин.
4.13 Замер температуры металла в промковше производится между стопорами после отливки 5м, второй в середине разливки и третий примерно за 10 минут перед окончанием разливки плавки из сталеразливочного ковша.
4.14 Если температура жидкого металла в промежуточном ковше в начале разливки окажется на верхнем пределе, то разливка должна производиться на нижнем пределе скорости для соответствующего сечения заготовки.
4.15 В середине разливки каждой плавки из промежуточного ковша отбираются две пробы на химический анализ. Каждая проба клеймится номером плавки и номером пробы. Пробы отправляются в экспресс-лабораторию НТУ.
4.16 Ответственность за соблюдением установленных настоящей инструкцией температурно-скоростных режимов разливки, поддерживания уровня металла в кристаллизаторах несут сменный производственный мастер МНЛЗ и старший разливщик. О всех изменениях скоростей разливки оператору ПУ-1 сообщает по внутренней связи старший разливщик.
4.17 После выхода головки затравки из последних роликов горизонтального участка ЗВО и отделения ее от слитка, она с помощью устройства для подъема и заведения затравки поднимается в верхнее положение и подвешивается на штыри.
Если головка затравки не отделилась от заготовки, головной конец обрезается на машине газовой резки (МГР), затем транспортируется в зону работы устройства для передачи заготовок (УПЗ) и передается на стеллаж, где головка отделяется от заготовки. Затем заготовка передается в пролет цеха в осях "ЛМ".
4.18 При выходе из строя погружного стакана под руководством старшего разливщика производится его замена. Замену рекомендуется производить на мерной длине заготовки.
4.19 На ручье, где производится замена погружного стакана, в кристаллизатор дополнительно засыпается смесь для изоляции зеркала металла во время процесса замены.
Стакан-дозатор перекрывается стопором, скорость вытягивания слитка снижается до
0,2 м/мин. Уровень жидкого металла при смене стакана в кристаллизаторе не должен опускаться ниже середины высоты кристаллизатора.
4.20 После замены предварительно нагретого стакана двух-трехкратным открыванием и закрыванием стопора кристаллизатор заполняется до нижнего уровня погружного стакана, на зеркало металла присаживается шлакообразующая смесь, затем кристаллизатор заполняется металлом до рабочего уровня. Разливка стали в ручье на скорости 0,2м/мин производится в течение 3х минут, затем в течение 3х минут производится разгон до рабочей скорости.
4.21 Если в процессе вытягивания слитка уровень металла в кристаллизаторе опустился ниже середины высоты кристаллизатора, то вытягивание слитка прекращается, а механизм качания кристаллизатора продолжает оставаться включенным. Затем двух - трехкратным открыванием и закрыванием стопора кристаллизатор заполняется до уровня погружного стакана, на зеркало металла присаживается шлакообразующая смесь и после 20-секундной выдержки включается механизм вытягивания слитка со скоростью 0,2м/мин. В этот момент необходимо следить, чтобы не было подвисания оболочки слитка. Открытием стопора кристаллизатор заполняется до рабочего уровня и промежуточный ковш опускается в нижнее положение. Разливка на скорости 0,2м/мин и разгон до рабочей скорости осуществляется так же, как указано в 4.16.
4.22 При замене погружного стакана дефектный участок заготовки длиной по 500мм выше и ниже пояса вырезается.
4.23 В случае, если при замене погружного стакана подача металла в кристаллизатор не производилась более 2 минут, разливка на ручье прекращается и горячий слиток выводится из машины.
4.24 По окончании разливки плавки из сталеразливочного ковша закрывается шиберный
затвор, прекращается подача аргона в защитную трубу. Сталеразливочный ковш поднимается в верхнее положение, отсоединяется защитная труба, ковш устанавливается в среднее положение, разворачивается в резервную позицию, отсоединяется гидроцилиндр, снимается с ковша крышка и разливочным краном сливается из ковша шлак, затем промывается кислородом шиберный затвор и аргонные узлы и ковш устанавливается на сталевоз передаточной эстакады.
4.25 При снижении уровня металла в промковше плавно скорость разливки снижается до 0,4м/мин и определяется масса и толщина оставшего металла и шлака. Минимальный уровень жидкого металла в промежуточном ковше в момент последнего закрытия стопора должен составлять 300-350мм. Замер производится кислородной трубкой в районе бойного места. Высота металла должна составлять 50-100мм.
4.26 Распределение оставшегося металла из промежуточного ковша по ручьям производится из расчета получения мерных длин заготовок путем закрытия стопоров сначала на одном, затем на другом кристаллизаторе в автоматическом или ручном режимах.
4.27 При прекращении подачи металла в кристаллизатор с мениска металла убирается шлак, захолаживается конец слитка и слитки выводятся из МНЛЗ на минимальной скорости, а после полного затвердения корочки – на повышенной. При разливке в четырех ручьевом варианте кристаллизатор, при выводе из него слитка, закрывается крышкой для исключения выделения пара.
4.28 Запрещается выводить за пределы кристаллизатора хвостовую часть слитка, если она не затвердела по всей поверхности. При плохом затвердевании хвостовой части слитка скорость снижается до 0,2м/мин. Возможная остановка машины с затвердевшей хвостовой частью не должна превышать 1 минуту.
Для ускорения затвердевания хвостовой части слитка допускается охлаждение ее водой.
При выполнении этой операции в районе кристаллизатора нахождение людей и обслуживающего персонала не допускается.
4.29 По мере выведения хвостовой части слитка из машины отключаются соответствующие зоны вторичного охлаждения.
4.30 После отделения затравки и подходе заготовки под машину газовой резки, производится подрезка головной части слитка. Головная обрезь устанавливается на всех типах заготовок 500мм, на донной слябовой заготовке 800мм, на стали марок "Ю" 1000 мм, а на донной сортовой заготовке 2000мм. При подрезании головных и хвостовых за готовок недорезанный перешеек должен быть не менее 150мм.
4.31 Головные заготовки с недорезанными концами передаются без маркировки по рольгангам ТОО на участок обрезки головных и донных концов заготовок, где машиной газовой резки отрезаются концы, заготовки вручную клеймятся и укладываются на стеллажи.
4.32 После порезки непрерывнолитых заготовок на мерные длины они с МГР подаются к упорам.
После остановки их на торец с помощью клеймовочной машины наносится маркировка. Каждая заготовка клеймится номером плавки (без номера года изготовления), номером ручья и порядковым номером заготовки в ручье по ходу разливки. Свободные в наборе знаки резервируются для условной марки стали. Допускается производить маркировку заготовок в горячем виде резиной на узкой грани заготовки:
- при производстве слябов, каждая заготовка маркируется номером плавки (без номера года изготовления), номером ручья и порядковым номером заготовки в ручье по ходу разливки;
- при производстве остальных видов продукции заготовка маркируется номером плавки (без номера года изготовления).
4.33 После маркировки мерные заготовки передаются в зону работы устройства передачи заготовок (УПЗ). В зоне работы УПЗ заготовки передаются на рольганг, находящийся перед поворотным рольгангом. Группа заготовок и одиночные заготовки поворотным рольгангом поворачиваются на 90º и транспортируются на рольганги склада заготовок в зону работы двух сталкивателей. Сталкивателями заготовки сталкиваются на стеллажи. Со сталкивателей заготовки снимаются мостовым краном и укладываются на вагоны.
При отливке слябов производятся те же операции, но при этом на рольгангах УПЗ слябы останавливаются по одной и все остальные операции производятся как с одиночными заготовками.
4.34 При необходимости отрезания головных и донных концов сортовых заготовок или слябов или вырезки от них темплетов,слябы и заготовки транспортируются в зону работы машины газовой резки к ПУ №5.
РАЗЛИВКА ПЛАВОК СЕРИЯМИ
5.1 Методом "плавка на плавку" разливаются только стали одной марки. При этом необходимо, чтобы в смежных плавках химический состав стали был в пределах, оговоренных соответствующими стандартами, техническими условиями или международным стандартами на производство данной марки стали.
5.2 Количество плавок в серии (от запуска МНЛЗ до ее остановки) определяется заказами ПРУ и должно быть не более 110-и плавок.
Разделение смежных плавок производится на мерные длины ориентируясь на массу металла в сталеразливочном ковше.
Разливка разных марок стали через один промежуточный ковш – не допускается.
При расхождении химического состава смежных плавок, разливаемых через один промежуточный ковш, в зависимости от мерной длины заготовок необходимо осуществить отсортировку от основных пл
|
|
Археология об основании Рима: Новые раскопки проясняют и такой острый дискуссионный вопрос, как дата самого возникновения Рима...
Эмиссия газов от очистных сооружений канализации: В последние годы внимание мирового сообщества сосредоточено на экологических проблемах...
Наброски и зарисовки растений, плодов, цветов: Освоить конструктивное построение структуры дерева через зарисовки отдельных деревьев, группы деревьев...
Типы оградительных сооружений в морском порту: По расположению оградительных сооружений в плане различают волноломы, обе оконечности...
© cyberpedia.su 2017-2024 - Не является автором материалов. Исключительное право сохранено за автором текста.
Если вы не хотите, чтобы данный материал был у нас на сайте, перейдите по ссылке: Нарушение авторских прав. Мы поможем в написании вашей работы!