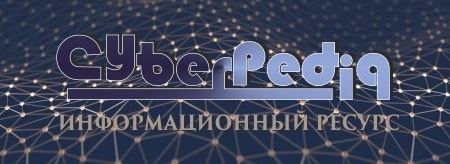
История создания датчика движения: Первый прибор для обнаружения движения был изобретен немецким физиком Генрихом Герцем...
Таксономические единицы (категории) растений: Каждая система классификации состоит из определённых соподчиненных друг другу...
Топ:
Выпускная квалификационная работа: Основная часть ВКР, как правило, состоит из двух-трех глав, каждая из которых, в свою очередь...
Методика измерений сопротивления растеканию тока анодного заземления: Анодный заземлитель (анод) – проводник, погруженный в электролитическую среду (грунт, раствор электролита) и подключенный к положительному...
Характеристика АТП и сварочно-жестяницкого участка: Транспорт в настоящее время является одной из важнейших отраслей народного хозяйства...
Интересное:
Наиболее распространенные виды рака: Раковая опухоль — это самостоятельное новообразование, которое может возникнуть и от повышенного давления...
Инженерная защита территорий, зданий и сооружений от опасных геологических процессов: Изучение оползневых явлений, оценка устойчивости склонов и проектирование противооползневых сооружений — актуальнейшие задачи, стоящие перед отечественными...
Берегоукрепление оползневых склонов: На прибрежных склонах основной причиной развития оползневых процессов является подмыв водами рек естественных склонов...
Дисциплины:
![]() |
![]() |
5.00
из
|
Заказать работу |
|
|
Технологические свойства характеризуют способность смеси обеспечивать получение высококачественных форм при различных технологических процессах их изготовления. К наиболее важным технологическим свойствам относятся влажность, текучесть, уплотняемость, формуемость, насыпная плотность, прочность, ударная вязкость, при-липаемость, кажущаяся плотность.
Влажность определяется непосредственно после приготовления смеси (не позднее чем через 10 мин) по ГОСТ 23409-78. Влажность оказывает влияние практически на все технологические и рабочие свойства смесей. Важным технологическим фактором пластические свойства смеси. Они характеризует способность смеси к необратимым деформациям при приложении определенных внешних нагрузок. При уплотнении смеси ее пластичность определяется перемещением частиц относительно друг друга и деформацией пленок, покрывающих зерна наполнителя. Способность к пластической деформации смеси определяется влажностью, типом связующего и его вязкостью. Для оценки пластичности смеси различают следующие характеристики: уплотняемость, текучесть, сыпучесть, формуемость, заполняемость Уплотняемость характеризует способность смеси уменьшать свой объем (в замкнутом пространстве) под действием собственного веса или внешней нагрузки. Она определяется по относительному снижению высоты стандартного образца Смеси после уплотнения тремя ударами копра (ГОСТ 23409. 13-78). Уплотняемостъ увеличивается с ростом влажности смеси до момента покрытия поверхности зерен влажной пленкой. По мере заполнения водой пор смеси повышение влажности уменьшает уплотняемость. Уплотняемостъ уменьшается с увеличением вязкости связующего. От уплотняемости смеси зависит качество и чистота поверхности отливок.
|
Понятие текучести смеси строго определяется понятием пластичности, т. е: характеризует способность смеси получать пластические деформаций без нарушения сплошности под действием внешнего давления. Чем большую деформацию при данной нагрузке получает смесь, тем выше ее текучесть. Текучесть можно охарактеризовать как способность смеси к перемещению в направлении, перпендикулярном к уплотняющей силе. Высокая текучесть обеспечивает равномерную степень уплотнения форм. Текучесть характеризуется сопротивлением смеси сдвигу ее слоев.
Степень связности песчано-глннистых смесей оценивается по их формуемости. Согласно ГОСТ 2340915-78 формуемость определяют по методу Диггерта путем просеивания пробы смеси за определенное время через вращающийся сетчатый барабан. Ее оценивают как выраженное в процентах отношение массы смесн, прошедшей через ячейки сетки, к исходной массе смеси. Под формуемостью можно понимать способность смеси сжиматься и изменять свой объем под действием сжимающей силы, которая увеличивается от начального значения до предельной величины. Выше этой величины смесь практически не уплотняется.
Важной характеристикой жидкоподвижных смесей (ЖСС) является подвижностъ, текучесть, характеризующая способность смеси заполнять полости стержневых ящиков или модельно-опочной оснастки под действием собственного веса. По ГОСТ 23409.25-78 подвижность ЖСС может определяться по сопротивлению сдвигу или диаметру расплывания определенного объема смеси.
Прочностные характеристики смесей определяются на стандартных образцах В соответствии с ГОСТ 23409.7-78 проводятся испытания влажных, сухих и отвержденных образцов при сжатии, растяжении, изгибе и срезе. Прочностные характеристики определяют на образцах смеси, полученных при стандартном уплотнении. При обычных испытаниях формовочных смесей определяют общую прочность, т.е. среднюю величину по всему сечению образца. В объеме смеси каждое зерно равномерно со всех сторон связано с окружающими подобными же частицами пленкой связующего. Поверхностная прочность определяет сопротивляемость формы механическому и термическому воздействию струи металла при заливке формы и поэтому существенно влияет на качество поверхности отливок. Поверхностную прочность смесей характеризуют величиной осыпаемости. Определение осыпаемости по ГОСТ 234099-78 основано на измерении потери массы стандартного образца смеси в сыром и высушенном состояниях при его трении в течение 1 мин о стенки сетчатого барабана диаметром 110 мм и с размерами ячеек сита 2,5 мм, вращающегося с частотой 1с-1.
|
Важным технологическим свойством смесей является их живучесть, характеризующая время, в течение которого смесь сохраняет свойства, необходимые для принятой технологии изготовления форм стержней. Живучесть выражают отношением значений прочности смеси, подученных после ее выдержки через определенные промежутки времени и сразу после приготовления.
Твердость - величина, характеризующая сопротивление поверхности проникновению в нее постороннего тела. Твердость форм и стержней косвенно характеризует такие свойства, как прочность и плотность смеси. Простота определения твердости без разрушения формы обеспечила широкое распространение определения твердости как показателя качества формы или стержня.
Прилипаемостъ - характеризующее способность сырой смеси прилипать к ленте транспортера, стенкам бункеров, поверхностям моделей и стержневых ящиков. Прилипаемость - нежелательное свойство смесей. Прилипание смеси к твердым поверхностям возникает, если силы адгезии (сцепления) смеси с этими поверхностями больше сил когезии, характеризующих сцепление между отдельными частицами смеси. Для уменьшения сил адгезии необходимо снижать смачиваемость поверхностей водой или жидким связующим, а также влажность смеси и содержание в ней связующего. С уменьшением поверхностного натяжения связующего сила адгезии и,следовательно, прилипаемость уменьшаются.
Очень важное значение имеет гигроскопичность смесей, т. е. их способность поглощать влагу при хранении стержней и выдержке форм перед заливкой. Гигроскопичность смесей зависит от рода применяемых связующих. Наибольшей гигроскопичностью обладают смеси на лигно-сульфонатах и жидком стекле (равновесная влажность 4,2 %), а наименьшей - смеси на маслах и смолах (равновесная влажность менее 1 %).
|
По ГОСТ 23409.10-78 гигроскопичность смесей определяют по нарастанию массы образца, выдержанного в течение 2 ч в эксикаторе на фильтровальной бумаге, помещенной на влажном песке.
Теплофизические свойства материалов формы. Теплофизические свойства смесей определяют тепловые процессы в отливке и в форме. Изменяя теплофизические свойства материала формы, можно в десятки раз изменять скорость затвердевания отливки. К основным теплофизическим свойствам относят удельную теплоемкость, теплопроводность, плотность, коэффициент температуропроводности и коэффициент аккумуляции тепла. Удельная теплоемкость С - свойство, определяющее количество тепла, необходимое для изменения температуры единицы массы вещества на один градус. Удельная теплоемкость смесей зависит от состава, влажности, уплотнения и температуры. С увеличением влажности удельная теплоемкость возрастает. С повышением температуры увеличение удельной теплоемкости происходит по линейному закону. Размерность удельной теплоемкости - Дж/(кгК). Теплопроводность смеси определяется удельным тепловым потоком, передаваемым смесью по нормали к изотермической поверхности при градиенте температуры (dT/dn) равном единице. Размерность теплопроводности в СИ - Вт/(мК). На основании закона. Теплопроводность смеси определяется как эффективная, учитывающая все указанные процессы. Она увеличивается с ростом температуры, влажности и уплотнения, а также с повышением содержания связующего. Теплопроводность смеси зависит от теплопроводности наполнителя.
Коэффициент температуропроводность, м2/с (распределение температур в стенке формы):
Теплоаккумулирующая способность формы b является основной физической константой, определяющей интенсивность охлаждения отливки. Величина b связана с основными теплофизическими свойствами выражением
Коэффициент аккумуляции тепла смесью зависит от состава смеси, наполнителя, уплотнения, влажности и температуры. С ростом температуры b увеличивается. Изменяя состав смеси и степень уплотнения, можно изменять b в пределах от 1000 до 4000 Вт-с1У2/(м2-К). Как следует из вышеприведенной формулы, скорость затвердевания отливок при изменении b в указанном диапазоне может быть увеличена в 16 раз.
|
Так как теплофизические свойства смеси существенно зависят от температуры, то их реальные значения в зависимости от степени прогрева в разных точках по толщине стенки формы различны. Поэтому применяемые в расчетах значения теплофизических свойств, представляющие собой некоторые усредненные, эффективные значения, являются характеристикой не только смеси, но и конкретных технологических условий (вида сплава, толщины стенки отливки, степени уплотнения и т.п.).
31. Физико-химические процессы на границе «металл-форма» и образование дефектов: пригара; ужимин; наростов.
После заливки металла в форму и охлаждения отливки можно наблюдать в слое песка, прилегающем к поверхности отливки, полное изменение его свойств. Образовавшаяся сплошная масса имеет типичный серый цвет и блестящую поверхность. В некоторых случаях этот слой прочно связан с отливкой.
Пока температура поверхности отливки выше температуры солидуса, проникновение металла в форму может произойти. Поэтому, если па поверхности формы присутствует науглероживающее вещество (например, для стали), то также может произойти местное расширение интервала затвердевания и повышение проникновения металла в форму.
Кроме того, между основой формы и металлом может произойти химическая реакция с образованием, например, фаялита.
Проникновение расплава можно ограничить снижением температуры заливаемого металла и тщательным его раскислением. Полностью предупредить протекание химических процессов можно лишь изменением вида формовочного материала.
Пригар. Известно, что элементы, вызывающие повышение текучести расплава, одновременно облегчает его проникновение в форму, при чем при более низкой температуре. Например, добавки фосфора в сталь (до 0,9 % Р) вызывают значительное повышение ее текучести, что приводит к глубокому проникновению металла в форму. Титан, наоборот, известен как элемент, снижающий текучесть стали. При его добавлении в сталь проникновение металла в форму происходят лишь при повышенных температурах.
Пока температура поверхности отливки выше температуры солидуса, что наблюдается в сталях с повышенным содержанием углерода, проникновение металла в форму может произойти, поэтому если па поверхности формы присутствует науглероживающее вещество, то также может произойти местное расширение и затвердевания и повышение проникновения металла в форму.
|
После заливки металла в форму и охлаждения отливки можно наблюдать в слое песка, прилегающем к поверхности отливки полное изменение его свойств. Образовавшаяся сплошная масса имеет типичный серый цвет и блестящую поверхность. В некоторых случаях этот слой4трочно связан с отливкой.
На разрезе этого слоя песка можно видеть исходные кварцевые зерна, которые частично окружены темным шлаковидным веществом.
Микрорентгеновский анализ показал в этом слое наличие фаялита (2FeO . SiO2), который образуется при достаточно высокой температуре металла и достаточном времени реакции FeO (из расплава) с SiO2 (наполнителя).
В присутствии оксида алюминия образуется муллит (3Al2O3 . 2SiO2).
Из приведенного анализа следует, что спекание кварцевых зерен песка может продолжаться до относительно низких температур.
На процесс проникновения расплава оказывает влияние также содержание марганца в заливаемом металле. Например, если сталь содержит примерно 0,6 % Mn, то оксид марганца, обнаруженный в слое песка, образующий пригар, составляет примерно 3 % от общего содержания марганца. При повышенном содержании марганца, например при заливке аустенитной марганцевой стали, основной оксид марганца MnO активно реагирует с кварцевыми зернами (SiO2), которые имеют кислородный характер: SiO2 + MnO → MnO . SiO2.
Образовавшееся соединение силиката марганца отличается низкой температурой плавления.
В обоих случаях проникновение расплава, вызванное химическими процессами, можно значительно ограничить снижением температуры заливаемого металла и тщательным его раскисления.
Полностью предупредить протекание химических процессов можно лишь изменением вида формовочного материала. Например, протекание приведенных химических реакций можно предотвратить применением магнезита или хромомагнезита, которые не имеют кислотного характера.
Ужимины. Неравномерное расширение слоев смеси под поверхностью формы вызывает в ней напряжение, которое может привести к повреждению формы. В зоне, где наблюдается наибольшее расширение песка (рис.2), т.е. на поверхности формы, расширяющийся формовочный мате риал тормозится соседними, слабоподвергшимися действию тепла, слоями. В нем возникает напряжение сжатия, которое при соответствующей конфигурации отливки переходит в напряжение, перпендикулярное к поверхности формы. Если это напряжение превысит жесткость напряженного слоя, го при определенных условиях (низкая прочность формовочного материала, влажность и газы) он может вспучиться и отслоиться. Этот механизм образования ужимин.
1 – давление газов; 2 – сжимающее напряжение, обусловленное расширением зерен песка; 3 – растягивающее напряжение смеси; 4 – конденсационная зона; 5 – результирующая сила, вызывающая отслоение поверхностной корки смеси; 6 – направление
Рис.2. Факторы, влияющие на образование ужимин
Предупреждение. Подобрать состав с большей огнеупорностью, прочностью и меньшей деформацией при нагреве.
Нарост. Причины появления: Неравномерное уплотнение смеси при формовке, неправильная литниковая система.
Предупреждение. Более тщательное уплотнение смеси при формовке и более равномерное увлажнение, изменить подвод металла к отливке.
32. Физико-химические процессы на границе «металл-форма» и образование дефектов ситовидной пористости; засоров и неметаллических включений.
Ситовидная пористость – сплошная зона удлиненных пузырьков, вытянутых перпендикулярно к поверхности отливки.
1 – оксиды железа; 2 – расплав; 3 – форма; 4 – ситовидная пористость
Рис.3. Форма пузырьков ситовидной пористости и характер их роста
Причины:
1. Водород или азот, растворяющиеся в расплаве при его контакте с формой, или их сочетание. В процессе затвердевания растворимость этих газов в металле быстро снижается, образуя ситовидную пористость: 2Н → Н2 (ситовидная пористость), 2N → N2 (ситовидная пористость). Водородная теория была применена для сплавов Mg, Al, Cu, Fe, а азотная – только для сплавов Fe;
2. Образование СО (только в сплавах железа). В расплаве присутствует кислород в форме оксидов. Содержание кислорода возрастает при контакте металла с формой, поскольку на поверхности отливки образуются оксиды FeO. При определенном содержании кислорода в металле происходит восстановление оксидов углеродом расплава по реакции: МеО + С (в металле) → Ме + СО (ситовидная пористость). Образовавшиеся пузырьки СО могут увеличиваться за счет диффузии водорода, иногда других газов, которые в них ассоциируются в молекулы. СО, как причина ситовидной пористости, указывается для отливок из стали, высокопрочного и серого чугуна. В работах Гака приводится теория возникновения ситовидной пористости в сером чугуне при наличии корольков внутри газовых пор вследствие протекания следующих реакций: Fe2O3 + 3C (в металле) → 2Fe + 3CO (ситовидная пористость) или 2Fe2O3 + 3C (в металле) → 4Fe + 3CO (ситовидная пористость). Присутствующие С или СО2 образуют в пузырьках пленку графита.
3. Образование водяного пара. Эта гипотеза была предложена, в частности, для сплавов Cu, но была применена и для сплавов железа (для отливок из стали). Водяной пар образуется при повышенной температуре в сырой форе по уравнению: MeO + 2H → Me + H2O (ситовидная пористость).
4. Образование сероводорода. Эта теория применяется специально для высокопрочного чугуна. При обработке чугуна магнием образуется MgS, который частично остается в расплаве. При заливке в сырые формы происходит реакция MgS + H2O → MgO + H2S (ситовидная пористость).
Таким образом, пористость в отливках из сплавов железа появляется главным образом при их изготовлении в сырой форме. Для стали наиболее важной причиной ситовидной форме. Для стали наиболее важной причиной ситовидной пористости считают СО, в то время как в сером чугуне и, в особенности высокопрочном, – водород. Однако механизм образования ситовидной пористости не является простым, на его возникновение оказывают влияние одновременно и другие газы: азот, водяной пар, углекислый газ и т.п.
Для предупреждения ситовидной пористости производится тщательное раскисление металла и обеспечивается полная защита стали от воздействия влаги и водяного пара. Для этого необходимо хорошо просушивать футеровку печи и приспособления, которые входят в контакт с жидким металлом.
Неметаллические включения, засоры. Правильно соблюдать технологический процесс приготовления формы и формовочной смеси. Неметаллические включения в отливках представляют собой твердые частицы соединений компонентов сплавов с неметаллическими примесями. Их размеры колеблются от долей микрона до десятков микрон. Основная масса неметаллических включений в литейных сплавах делится по составу на окислы и сульфиды. По видам источников неметаллические включения: на попадающие в сплав вместе с шихтой, продукты взаимодействия компонентов сплава с примесями или добавками, продукты взаимодействия компонентов сплава с атмосферой. По формам неметаллические включения делятся на круглые, кристаллические, дендритные и пленочные. Причины: 1.Неправильный расчет и конструкции элементов литниковой системы; 2.Некачественная сборка формы. 3.Низкая формовочной или стержневой смеси. 4.Слабое уплотнение формы или стержня.
|
|
Типы сооружений для обработки осадков: Септиками называются сооружения, в которых одновременно происходят осветление сточной жидкости...
Типы оградительных сооружений в морском порту: По расположению оградительных сооружений в плане различают волноломы, обе оконечности...
Двойное оплодотворение у цветковых растений: Оплодотворение - это процесс слияния мужской и женской половых клеток с образованием зиготы...
Механическое удерживание земляных масс: Механическое удерживание земляных масс на склоне обеспечивают контрфорсными сооружениями различных конструкций...
© cyberpedia.su 2017-2024 - Не является автором материалов. Исключительное право сохранено за автором текста.
Если вы не хотите, чтобы данный материал был у нас на сайте, перейдите по ссылке: Нарушение авторских прав. Мы поможем в написании вашей работы!