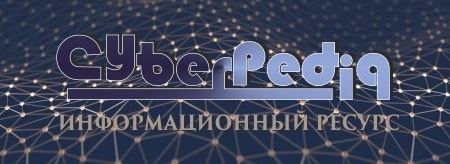
Индивидуальные очистные сооружения: К классу индивидуальных очистных сооружений относят сооружения, пропускная способность которых...
Таксономические единицы (категории) растений: Каждая система классификации состоит из определённых соподчиненных друг другу...
Топ:
Характеристика АТП и сварочно-жестяницкого участка: Транспорт в настоящее время является одной из важнейших отраслей народного хозяйства...
Когда производится ограждение поезда, остановившегося на перегоне: Во всех случаях немедленно должно быть ограждено место препятствия для движения поездов на смежном пути двухпутного...
Интересное:
Мероприятия для защиты от морозного пучения грунтов: Инженерная защита от морозного (криогенного) пучения грунтов необходима для легких малоэтажных зданий и других сооружений...
Что нужно делать при лейкемии: Прежде всего, необходимо выяснить, не страдаете ли вы каким-либо душевным недугом...
Наиболее распространенные виды рака: Раковая опухоль — это самостоятельное новообразование, которое может возникнуть и от повышенного давления...
Дисциплины:
![]() |
![]() |
5.00
из
|
Заказать работу |
|
|
КОМИТЕТ ОБРАЗОВАНИЯ, НАУКИ И МОЛОДЕЖНОЙ ПОЛИТИКИ ВОЛГОГРАДСКОЙ ОБЛАСТИ
государственное бюджетное профессиональное образовательное учреждение
«волгоградский колледж управления и новых технологий
Имени Юрия Гагарина»
(ГБПОУ «ВКУиНТ им. Ю. Гагарина»)
Методические рекомендации для выполнения практических работ
по МДК. 06. 01.02. Подготовка и ведение технологического процесса производства угольных электродов для алюминиевых электролизеров для специальности
Металлургия цветных металлов
Волгоград 2019 г.
Рассмотрено и одобрено цикловой комиссией №10профессионального цикла специальностей технологии материалов Протокол № ____ от «___»_______20__г. Председатель ЦПК _________________А.Н.Ананьева | Составлено в соответствии с ФГОС СПО и рабочей программой ПМ.06 «Подготовка и ведение технологических процессов в производстве алюминия и сплавов» по специальности 22.02.02 Металлургия цветных металлов Утверждаю Зам. директора по УиМР _____________ Т.Е. Солодова «____» _________201_ г. |
Разработчик: ______________ Чайко А.С.
Рецензент:________________ Сагатдинов М.О
Содержание
Введение | 4 |
ПРАКТИЧЕСКАЯ РАБОТА № 1 Аппаратурно - технологическая схема подготовки пека | 5 |
ПРАКТИЧЕСКАЯ РАБОТА №2 Аппаратурно-технологическая схема подготовки и прокаливание сырого нефтяного кокса. | 13 |
ПРАКТИЧЕСКАЯ РАБОТА №3 Расчет основных характеристик прокалочной печи | 23 |
ПРАКТИЧЕСКАЯ РАБОТА №4 Аппаратурно-технологическая схема очистки отходящих газов прокалочной печи и пыли холодильника | 25 |
ПРАКТИЧЕСКАЯ РАБОТА №5 Аппаратурно-технологической схемы производства коксовой шихты. | 33 |
ПРАКТИЧЕСКАЯ РАБОТА №6 Аппаратурно - технологическая схема приготовления анодной массы | 46 |
ПРАКТИЧЕСКАЯ РАБОТА №7 Аппаратурно-технологическая схема виброформования «зеленых» анодов | 56 |
ПРАКТИЧЕСКАЯ РАБОТА №8 Печи обжига «зеленых» анодов, технология обжига. | 67 |
ПРАКТИЧЕСКАЯ РАБОТА №9 Монтаж новых и демонтаж отработанных анодов. | 76 |
ПРИЛОЖЕНИЕ А | 85 |
ПРИЛОЖЕНИЕ Б | 86 |
|
Введение
Методические рекомендации для выполнения практических работ по МДК.06.01.02 «Подготовка и ведение технологического процесса производства угольных электродов для алюминиевых электролизеров» содержат необходимые теоретические сведения и практические задания, предназначенные для студентов специальности 22.02.02 «Металлургия цветных металлов».
МДК 06.01.02 «Подготовка и ведение технологического процесса производства угольных электродов для алюминиевых электролизеров» является частью ПМ.06 «Подготовка и ведение технологических процессов в производстве алюминия и сплавов» и изучается в течение одного семестра. В ходе изучения МДК. 06.01.02 рассматриваются следующие вопросы: физико-химические свойства углеродистых материаллов, теоретические и практические основы производства анодной массы и обожженных анодов, сырье и материалы используемые в процессе производства и требования к ним, конструкции основного оборудования, технико- экономические показатели процесса, экологические требования к процессу, способы утилизации отходов производства.
На изучение МДК 06.01.02 отводится 208 часов, из них 88 часов на лекции,80 часов на практические работы, и 40 часов на курсовой проект.
Пособие включает методические указания для выполнения 9-ти практических работ. Каждая практическая работа содержит, теоретическую часть, контрольные вопросы и практические задания.
|
Цель методических рекомендаций – предоставление необходимой информации для выполнения практических работ по МДК 06.01.02, в ходе которых происходит закрепление полученных знаний и получение умений:
У1-выбирать сырьевые материалы для производства на основе их свойств;
У2-выбирать способы подготовки сырья;
У3-выполнять расчет сырьевых материалов;
У4-отслеживать показания КИП, анализировать их, вносить коррективы в процесс;
У6-рассчитывать материальные потоки;
У7-определять основные параметры технологического режима;
У8-регистрировать и обрабатывать данные технологических процессов;
Приобретенные знания и умения помогут студентам в дальнейшем для формирования и развитияпрофессиональных компетенций:
ПК6.1. Осуществлять подготовку исходного сырья к переработке;
ПК6.2 Вести технологический процесс по результатам анализов, показаниям контрольно-измерительных приборов (КИП);
ПК6.3 Контролировать и регулировать технологический процесс;
ПК6.4 Использовать автоматизированные системы управления технологическими процессами (АСУТП) в производстве электродной продукции, алюминия и сплавов;
ПК6.5 Выполнять необходимые типовые расчеты;
По каждой практической работе оформляется отчет в письменном виде на формате А4 (210х297), на одной стороне листа. Интервал межстрочный – одинарный. Цвет шрифта – чёрный. Страницы должны быть пронумерованы с учётом титульного листа, который не обозначается цифрой.
Отчет состоит:
- титульный лист Приложение 1
- содержание Приложение 2
- текстовая часть практической работы
Практическая работа № 1
Тема: Аппаратурно - технологическая схемы подготовки пека
Цель: разработка аппаратурно-технологической схемы подготовки пека. Подбор оборудования и технологических параметров пекоподготовки.
Теоретические сведения
Введение
Каменноугольный пек является одним из сырьевых материалов, используемых в качестве связующего при производстве электродной массы. Качественные характеристики пеков оказывают влияние на технологию производства массы и показатели работы в электролизере. Вариативность свойств пеков в значительной степени влияет на пластические свойства анодной массы. Стабильность данного показателя, в определенной степени достигается в процессе пекоподготовки.
|
Транспортировка пека
Связующее поступает в цех, как правило, в жидком (в термоцистернах) или в гранулированном виде (в биг-бегах), а иногда в виде монолита. В последнем случае разгрузка его весьма затруднена, особенно в летнее время, когда пек теряет способность дробиться. Поэтому поступление пека в виде монолита считается нарушением условий поставки заводом-изготовитёлем. В последнее время на заводах внедряется перевозка пека в жидком состоянии в стальных термоцистернах (железнодорожных). Такая транспортировка позволяет избавиться от двух операций: грануляции и охлаждения пека с помощью воды на коксохимических заводах, обезвоживания и расплавления в цехах анодной массы. Для предотвращения потерь тепла и охлаждения пека при транспортировании цистерны снабжены слоем тепловой изоляции, которая выкладывается отдельными матами между наружными кожухами и электронагревательными элементами.
Во время транспортировки пек в термоцистернах остывает. Подогрев пека в цистерне осуществляется трубчатыми электронагревателями, установленными между котлом и слоем изоляции. Электронагреватели питаются переменным током от сети через разъемно-штепсельные соединения, расположенные в арматурном ящике, прикрепленном к раме цистерны, для предотвращения местных перегревов при включении системы в электросхему включены термореле.
Среднесуточное снижение температуры в термоцистерне составляет 5-6оС (при отсутствии нагрева), что позволяет сохранить пек в жидком виде 5—7 суток. При включении электронагрева пек разогревается в районе сливного устройства и стенок котла, т.е. где он наиболее охлажден. В том случае, если при транспортировании на большие расстояния пек остынет с 200 до 15О0С, необходимое время разогрева не превысит 8—10 ч. Разогретый до 170-180 0С пек выливается из цистерны в течение 45-60мин.
Рациональнее перевозить пек в железнодорожных термоцистернах, чем в автоцистернах, объем которых мал, а это приводит к относительному увеличению площадей охлаждающих поверхностей и чрезмерным потерям тепла. Кроме того, необходимо содержание большого автопарка с обслуживающим персоналом.
|
Поступающий на производство пек по составу и свойствам еще не отвечает всем требованиям технологии. В нем содержатся влага и легко - летучие вещества, которые вызывают его вспучивание, низка его истинная плотность и т.д. для устранения указанных недостатков пек подвергают термостатированию (выдержке) при I5О-I8ОоС в течение 3—4 суток.
Подготовка пека к переработке, склады открытого типа
Переработка поступающего на предприятие пека осуществляется в следующей последовательности:
1. прием и расплавление пека в пекоприемнике;
2. перекачка жидкого пека в пекоплавители;
3. длительная выдержка в пекоплавителе;
4. подача пека в производство.
Рис.1 Схема узла подготовки пека
Схема узла подготовки пека по традиционной схеме в заглубленных ёмкостях представлена на рис. 1. Пек разгружается в пекоприемник 1, где он расплавляется и доводится до 120 —140°С. Из пекоприёмника жидкий пек перекачивается шестеренчатым насосом 2 для окончательной доводки в пекоплавитель З.
Пекоприемник представляет собой резервуар, обогреваемый паром. Регистры 4 служат нагревательными элементами; через них от магистрального паропровода 5 проходит перегретый до 2000С пар под давлением 4,50—5,0 атм. Регистры установлены по боковым стенкам и на днище пекоприёмника: всего в одном пекоприёмнике имеется 40—50 регистров с 8—12 трубами в каждом. Проходя через трубы регистров, пар отдает тепло, охлаждается и конденсируется. Пар подается в верхнюю часть системы регистров, а из нижней части сливается конденсат в специальную конденсатную линию 6 (условно показана сверху) и возвращается на ТЭЦ.
Полезный объем пекоприёмника 500—600 м3 днище его имеет уклон для лучшего слива пека. В месте наибольшей глубины установлен выходной патрубок, через который пек поступает в шестеренчатый насос. В цехе анодной массы современных заводов имеется не менее трех пекоприемников.
Конструкция пекоплавителя аналогична конструкции пекоприёмника, однако емкость его значительно меньше и рассчитана на 150—180 т пека. Обогрев пекоплавителя происходит также с помощью парообогреваемых регистров. Готовый пек из пекоплавителя подается через магистральный пекопривод 7 в цех на узел смешения, как правило, двумя шестеренчатыми насосами (один работает, один в резерве). Перекачка пека осуществляется по парообогреваемым трубам, работающим по принципу “труба в трубе”; на наружной трубе имеется слой теплоизоляции. Коммуникации в узле пекоподводки устроены таким образом, что пек может перекачиваться из любого пекоприемника в любой пекоплавитель.
|
Готовность пека определяют по результатам анализов и по внешнему виду. Готовый пек имеет ровную зеркальную поверхность, без следов пены или вспучивания. Продолжительность выдержки пека зависит от содержания в нем влаги, летучих, способа транспортировки и других факторов. Однако склады такого типа имеют ряд недостатков:
- трудность герметизации емкостей, и большие выбросы в атмосферу возгонов, в виде смол и газов;
- трудность поддержания их в работоспособном состоянии, чистки от осадков и ремонта.
Склады закрытого типа
В последние годы на вновь строящихся заводах устанавливают склады пека закрытого типа с напольным расположением баков-резервуаров (рис. 2), что дает полную герметизацию и обеспечивает экологическую безопасность. Пек поступает только в жидком виде в термоцистернах-пековозах 1. Пек сливается в парообогреваемый приемник 2, откуда перекачивается через фильтр 3 шестеренчатым насосом 4 в резервуар 5 с секционным обогревателем, далее пек поступает в трубчатую электропечь 6, где температура его поднимается до необходимой. Из печи пек перекачивается в отстойный бак и далее на дозирующее устройство. В случае остановки смесительных машин циркуляция пека в системе резервуар 5 — отстойник 7 продолжается через обводящую линию 8; тем самым исключается застой и перегрев пека. Достоинствами складов закрытого типа являются удобство их обслуживания и хорошие санитарные условия труда.
Рис.2 Склад пека закрытого типа
Подготовка каменноугольного пека на ВгАЗе.
Технологический режим пекоподготовки и вовлечения технологического пека в производство осуществляется в соответствие со следующими требованиями (табл.1).
Таблица 1 Режим подготовки пека
Вид и состояние пека | Режимы подготовки пека | |
Термостатирование после окончания загрузки в резервуар, сутки | Температура термостатирования, °С | |
Гранулированный | Не менее 4 | 190-205 |
Жидкий из термоцистерн | Не менее 2 | 190-205 |
Смесь | Не менее 4 | 190-205 |
Рис.3 Схема склада пека ВгАЗ
Поступающий на завод пек по составу и свойствам еще не отвечает всем требованиям технологии. В нем содержатся влага и легкокипящие вещества, которые вызывают его вспучивание, а также нестабильны многие характеристики. Для устранения указанных недостатков пек подвергают термостатированию (выдержке) при температурах 190-205ºС.
В гранулированном пеке влага присутствует в виде капель на гранулах и в распыленном виде. В пеке, поступающем в жидком виде в термоцистернах, влага практически отсутствует или ее доля очень мала. Избыточная влага в пеке вызывает его вспенивание. Распыленная вода отделяется только в результате выдержки пека при температурах выше 130ºС. Наибольшее удаление влаги после расплавления гранулированного пека происходит за первые сутки выдержки. Практически полное обезвоживание гранулированного пека достигается на 3-4 сутки выдержки, поверхность пека становится «зеркальной».
В ходе термостатирования пека происходит дистилляция наиболее легкокипящих (летучих) фракций (смол, масел, простейших углеводородов), а так же частичное удаление водорода за счет реакций окисления и поликонденсации углеводородов. Удаление летучих веществ необходимо с точки зрения снижения пористости анода и уплотнения его структуры. Использование пека с повышенной вспучиваемостью недопустимо, так как приводит к вспениванию массы при ее использовании в аноде. Полученный из такой массы анод обладает повышенной пористостью, низкой механической прочностью, легко окисляется и осыпается при электролизе.
Температура размягчения определяет такой показатель, как вязкость поступающего в производство пека, от которой, в свою очередь, зависит выбор температурного режима процесса смешения анодной массы и ее пластические свойства. В ходе термостатирования на складах пек претерпевает воздействие температуры и кислорода воздуха в реакциях окисления. В процессе термостатирования, при температурах 190-2000С, значение температуры размягчения повышается в среднем на 1-1,50С в течение 4-5 суток. Повышение температуры размягчения пека в процессе термостатирования не должно приводить к чрезмерному увеличению вязкости пека. Поэтому в зависимости от исходного значения этого показателя время хранения пека на пекоскладе необходимо ограничивать. Если есть необходимость длительного хранения пека в жидком виде, то температуру следует понизить на 50-60ºС. В таком виде пек может храниться до 4 месяцев. Кроме этого установлено, что гранулированный пек, хранившийся на открытой площадке более 6 месяцев, под действием осадков и солнечного облучения становится непригодным для производства. Окисляемость и осыпаемость анодной массы из такого пека возрастают.
Целью технологического процесса подготовки пека для производства электродной массы является:
- удаление влаги и легколетучих веществ;
- стабилизация физико-химических свойств пека;
- обеспечение температурного режима технологического пека, подаваемого на смешение.
Согласно схемы склада пека (рис.3):
Гранулированный пек перерабатывается в жидкое состояние на автоматизированном участке по приёму и переработке гранулированного пека «Оникс». Загрузка гранулированного пека производится из «биг-бегов» в дозирующий бункер, затем с помощью шнекового транспортёра в накопительный бункер и, путём открывания шибера, в пекоплавитель;
Расплавленный пек, поступающий на завод в термоцистернах, во время транспортировки, как правило, охлаждается до температуры, при которой невозможен его слив, поэтому термоцистерны направляют на посты разогрева. Пек, разогретый до температуры 190-200°С, перекачивается из термоцистерн в резервуары «Оникс». Слив пека из термоцистерн производят на одном из двух устройств слива, работающих по принципу передавливания рабочей среды избыточным давлением не более 0,6 атм из цистерн в резервуары;
Из термоцистерн и участка по переработке гранулированного пека жидкий пек перекачивается шестеренчатыми насосами в резервуары электрообогреваемого склада пека «Оникс». В зависимости от поставок пека на завод, технических возможностей емкостей склада и натурных остатков, выбирается один из способов загрузки пека в емкости: слив только предварительно расплавленного гранулированного пека; слив только жидкого пека из термоцистерн до заполнения резервуара; разгрузка пеков в смеси, по следующей схеме - предварительно расплавленный гранулированный пек разгружается в накопительный резервуар и туда же производится слив жидкого пека из термоцистерн. Технологический режим пекоподготовки и порядок вовлечения технологического пека в производство определяются требованиями;
Готовый пек насосными станциями подается в расходные баки стабилизации пека, которые служат для стабилизации температурного режима, а также уровня пека перед дозированием. Необходимая температура пека в баках стабилизации перед вовлечением в производство поддерживается через линию подачи высокоорганическим теплоносителем. Из баков стабилизации пек распределяется через дозаторы на смесители.
Режимы работы (температурные уставки нагревателей резервуаров, секций обогрева пекопроводов, электрообогреваемых кранов пека, насосов пека, обогреваемых органическим теплоносителем баков стабилизации) устанавливаются с целью обеспечения температуры технологического пека для вовлечения в производство, в соответствии с регламентируемыми требованиями
Порядок выполнения работы
1. Ознакомьтесь с текстом данной работы.
2. Изучите существующие способы подготовки пека, используемое оборудование, достоинства и недостатки существующих способов подготовки.
3. Дайте письменные ответы на предложенные контрольные вопросы.
4. Разработайте аппаратурно – технологическую схему подготовки пека с подбором оборудования и технологических параметров согласно заданного варианта.
5. Доложите преподавателю о проделанной работе.
Контрольные вопросы
1. Способы транспортировки пека.
2. Разновидности складов пеков.
3. Оборудование используемое на складах открытого типа.
4. Время и температура термостатирования на складах открытого типа.
5. Принципиальная схема склада закрытого типа, используемое оборудование
6. Температурный режим термостатирования на складах закрытого типа.
Варианты заданий
Разработать аппаратурно – технологическую схему подготовки пека, подобрать технологические параметры и оборудование.
№ вар. | Вид и состояние поступающего пека |
1 | Гранулированный пек |
2. | Жидкий из термоцистерн |
3 | Смесь пеков |
Литература:
1. Янко, Э. Я. Аноды алюминиевых электролизеров / Э. Я. Янко. - М.: Руды и металлы, 2001.-670с.
2. Технология производства электродных масс для алюминиевых электролизеров: учеб. пособие для вузов / Г. В. Галевский [и др.]. – Новосибирск: Наука, Сибирская издательская фирма РАН, 1999. – 295 с.
3. Москвитин, В. И. Металлургия легких металлов: учебник для вузов / В. И. Москвитин, И. В. Николаев, Б. А. Фоминых. - М.: Интермет Инжиниринг, 2005. - 416с.
Практическая работа №2
Тема: Аппаратурно-технологическая схема подготовки и прокаливание сырого нефтяного кокса
Цель: разработка принципиальной аппаратурно-технологической схемы подготовки и прокаливания сырого нефтяного кокса, выбор основного оборудования и параметров процесса.
Теоретические сведения
Введение
В зависимости от существующей технологии предприятия перерабатывают:
- привозные прокаленные коксы
- сырые (зеленые) коксы
- сырые коксы с частичной поставкой предварительно прокаленных коксов.
Прокаленные коксы подвергаются сушке, сырые коксы - прокалке. В зависимости от содержания влаги, если содержание влаги более 0,3—0,5% кокс направляется на сушку. Под сушкой прокалённого кокса понимают процесс удаления влаги посредством высоких температур в течение определенного времени. Сушку осуществляют, как правило, в сушильных барабанных печах.
Под прокаливанием коксов и других углеродистых материалов понимают процесс обработки кокса в течение определенного времени при высоких температурах с возможно минимальным доступом воздуха. Прокаливание кокса относится к одному из основных процессов в производстве электродной массы, поскольку основные физико-химические и эксплуатационные свойства электродной массы во многом зависят от качества прокаливания.
Процессы, происходящие при прокаливании коксов, довольно сложны. Прокаливание производят при 1200—1350 0С; при этом практически полностью удаляется влага, происходят процессы разложения сложных углеводородов с удалением летучих веществ и прежде всего — водорода, а также уплотняется структура кокса, формируется его кристаллическая решетка и осуществляется частичная графитация материала.
1. Аппаратурно-технологическая схема подготовки электродных коксов
При поступлении сырого «зеленого» кокса он подвергается прокаливанию.
Рис.1 Аппаратурно-технологическая схема прокалочного отделения
На рис. 1приведена аппаратурно-технологическая схема прокалочного отделения. Коксы поступают на завод в открытых железнодорожных вагонах и разгружаются на складе 1 в специальные приемники — траншеи. Емкость склада зависит от местоположения поставщиков. Чем дальше поставщик, тем больше должен быть склад. При большом отдалении заводов-поставщиков от завода-потребителя емкость склада рассчитана обычно на 20—30-суточную потребность завода в коксе.
Для перемещения кокса внутри склада, а также для загрузки в приемные бункера на складе установлены грейферные краны 2. Из приемного бункера З кокс лотковым питателем 4 подается на валковую зубчатую дробилку 5 для предварительного дробления, где куски кокса уменьшаются от 250—350 до 60—70 мм. Элеваторами дробленый кокс подается в расходные бункера 7, откуда ленточными питателями 8 через загрузочную течку 9 в “холодный” конец вращающейся прокалочной печи 10. Пековый и нефтяной коксы загружаются в разные бункера. Прокалённый кокс через перегрузочную водоохлаждаемую течку поступает в холодильник барабанного типа 11, из которого охлажденный кокс через ленточный дозатор, транспортерами и элеваторами подается в бункер размольного отделения или силос запаса.
Образующиеся в печи газы с мелкими частицами кокса, запылённый воздух из холодильника очищаются аспирационными системами, удаляются через “холодную” головку и дымовую трубу, которая находится под разрежением, а при наличия пылеулавливающих устройств (циклона, электрофильтра) газы отсасываются дымососами. Запылённый воздух отсасывается из холодильника и очищается в электрофильтре или рукавном фильтре. Уловленная пыль с помощью пневмотранспорта возвращается в производство.
2. Конструкция печи
Прокалочная печь (рис.2) состоит из следующих основных узлов: цилиндрического стального барабана 3, футерованного изнутри огнеупорным кирпичом, опорных устройств, привода10, венцовая шестерня 5, головок — топочной (горячей 1) и газоотводящей (холодной 6), перегрузочного устройства, фундамента 9, бандажа 4, упорно – опорные ролики для бандажа 4, опор станция на фундаменте 9, загрузочная течка 7.
Рис.2 Конструкция прокалочной печи.
Барабан печи сварен из отдельных стальных царг. Барабан печи посредством бандажей опирается на опорные ролики. Число опор зависит от длины барабана; максимальное расстояние между опорами не более 20 м, при длине барабана 40 — 45 м оно не превышает трех. Ролики устанавливаются на массивные стальные плиты, а последняя на железобетонный фундамент, так чтобы печь имела уклон в сторону горячего обреза. Бандажи изготовлены в виде колец из специальной твердой литой стали. Для усиления корпуса под бандажами устанавливаются кольцевые или пластинчатые накладки, которые привариваются к корпусу. Насадку бандажа проводят непосредственно на корпус с таким расчетом, чтобы при рабочих температурах между бандажами и корпусом не было зазоров. Ролики (рис.3) опорные изготовляют из менее твердой стали, чем бандаж.
Рис.4 Схема установки опорных роликов:1- бандаж печи;2-опорный ролик; 3- регулировочный болт;4- упорный ролик
Каждая из опор состоит из двух опорных роликов, которые при регулировке перемещаются по опорной плите.
Для предотвращения осевых перемещений барабана и нарушения зацепления зубчатого венца с подвенцовой шестерней у наиболее близкого к приводу бандажа размещяют упорно-опорную станцию. Помимо опорных роликов станция оснащена упорными роликами они упираясь в боковую поверхность бандажа фиксируют положение печи вдоль ее оси.
Привод печи состоит из следующих основных узлов: основного электродвигателя привода, редуктора основного привода, венцовой и подвенцовой шестерен, электромагнитной муфты. Вспомогательный привод состоит из редуктора и электродвигателя (для аварийных ситуаций и запуска печи.)
Для привода печи на ее корпусе устанавливают стальную венцовую шестерню (рис.3, поз.7), снизу зацепляется подвенцовую шестерню (рис.3, поз.8). Нижняя часть венцовой шестерни погружается в масленую ванну. При вращении происходит смазывание всей венцовой и подвенцовой шестерни. Для настройки зацепления подвенцовую шестерню перемещяют по плите упорными болтами. Венцовая шестерня закрыта стальным кожухом, предохраняющим ее от попадания посторонних предметов и грязи.
Холодная головка печи (рис.2, поз.6) служит для отвода отходящих из барабана прокалочной печи газов в газоход; в нижней части она переходит в осадительную камеру первой ступени очистки отходящих газов от твердых частиц кокса. Для сбора просыпавшейся через колосники части кокса под холодной головкой находится сборный бункер.
Холодная головка футерована огнеупорным кирпичом; для герметизации она оснащена специальным, например ленточным уплотнением. Уплотнение осуществляется следующим образом.
К обечайке барабана печи плотно прилегает уплотнитель, сделанный из транспортерной ленты, который крепится с помощью шпильки и пластины к кожуху холодной головки.
Горячая топочная головка (рис.2, поз.1) печи имеет более мощную огнеупорную и теплоизоляционную футеровку, чем холодная. В торцовой стенке печи имеется фурменное устройство для форсунки, смотровые окна и специальная дверь. На случай ремонта футеровки барабана печи обе головки оснащены устройствами для откатывания.
Для предотвращения окисления и сгорания кокса при перегрузке его из печи в холодильник, а также для предотвращения подсосов воздуха горячая головка оснащена перегрузочным устройством в виде футерованного или водоохлаждаемого перегрузочного канала
Для обогрева печей используют горелочные устройства для газообразного и жидкого топлива. Горелочные устройства расположены в торцевой части горячей головки. При сжигании газообразного топлива газ и первичный воздух смешиваются в горелке до момента возгорания, газовоздушная смесь поступает в фурменное устройство где смешивается с вторичным воздухом (поступает из холодильника) для сгорания.
При прокаливания кокса выделяется большое количество летучих веществ, которые сгорают и выделяют тепло. Для более эффективного сгорания в зону выделения этих веществ подается третичный воздух. Воздух подается вентилятором низкого давления в нескольких точках зоны горения возгонов.
Существуют горелки диффузионного типа, В этих горелках происходит раздельная подача в фурменное устройство струи газа и воздуха, образуя возгорание.
Конструкция холодильника
Барабанный холодильник (рис.3, поз.16) по конструкции в принципе не отличается от вращающейся печи. Величина диаметра холодильника иногда совпадает с величиной диаметра печи, но обычно на 1/3 меньше, угол наклона и число оборотов больше чем у печи. Наклон и вращение барабана холодильника противоположны наклону и направлению вращения печи обеспечивает нормальное продвижение материала. Прокаленный кокс по перегрузочной охлаждаемой водой течке поступает в верхнюю головку барабана холодильника. Конструкция головки аналогична конструкции головки печи.
Раньше горячая часть холодильника футировалась,сейчас от этого отказались. Барабан снаружи охлаждается водой. Внутри барабана приварены перегребные полки, для перемешивания материала.
В разгрузочном конце барабана для предотвращения подсоса воздуха установлена штора, изготовленная из транспортерных лент. Через штору и верхнюю часть разгрузочной головки холодильника проходит патрубок для отсоса воздуха из барабана холодильника в аспирационную систему. В качестве дополнительного уплотнения в разгрузочной течке установлен шлюзовой затвор или мигалка.
На ряде зарубежных заводах в холодильник впрыскивается вода, это резко снижает температуру и пыление. При этом снижается угар кокса из-за быстрого гашения кокса и создания нейтральной атмосферы.
Техническая характеристика холодильника: длина 30 м, диаметр 2,5—3,0 м, угол наклона 2,5―3,5 0, число оборотов в минуту 2,5—4,0.
Параметры процесса
В заводской практике для характеристики температурного режима работы вращающейся печи принято условно делить ее длину на следующие зоны (начиная с холодного конца печи):
1) зона подсушки и нагрева;
2) зона прокалки;
3) зона охлаждения.
Зона подсушки и нагрева Кокс, поступающий в холодный конец печи, содержит от 3 до 15 % влаги и от 1 до 10% летучих веществ. В результате непрерывного перемешивания и контакта с отходящими газами, нагретыми до 400 — 500 оС, влага и летучие вещества интенсивно удаляются. По мере продвижения кокса в зону более высоких температур газовыделение становится более интенсивным. На расстоянии 10 — 15 м от холодного конца печи летучие загораются; температура кокса в районе конца факела форсунки повышается до 1200 0С. Здесь условно кончается зона подсушки и подогрева материала и начинается зона прокалки. Длина зоны подсушки и подогрева 25 — 30 м.
Зона прокалки; область самых высоких температур, температура газового потока достигает 1400 0С, а материал прогревается до 1200-13000С. Длина зоны зависит от длины факела и обычно составляет 5 — 6 м. При увеличении содержания летучих достигает 12-15м, сдвиг в сторону холодной насадки. Газовыделение и горение летучих в этой зоне практически прекращается, в коксе заканчиваются все основные физико-химические превращения и объемная усадка, раскаленный кокс приобретает ослепительно белый цвет.
Зона охлаждения находится между факелом и горячим концом печи, длина зоны охлаждения определяется конструкцией фурменного устройства и составляет 1,5—2,0 м. Из-за отсутствия подогрева и в результате подсосов воздуха из холодильника температура здесь снижается до 1100— I000 оС. Цвет кокса в этой зоне становится более темным, с вишнёвым оттенком.
Наиболее ответственная зона это зона прокаливания, от длины и расположения которой зависит качество прокаленного кокса и потери его от угара. При удалении зоны от горячей головки печи и увеличение ее длины, увеличивается угар за счет окисления воздухом, предназначенным для сжигания летучих веществ. Из-за этого может образоваться нехватка кислорода, летучие могут сгорать в конце печи или за ее пределами, резко повышая температуру отходящих газов. Удлинение зоны прокаливания является также положительным фактором, создается условие для более полного прокаливания кокса, в результате чего может быть увеличена производительность печи.
Для более надежного управления процессом прокаливания число регулируемых параметров сводится к минимуму. Загрузку печи и число оборотов барабана стремятся поддерживать постоянными и в качестве регулирующих параметров не использовать, так как колебания загрузки вредно отражаются как на качестве прокаленного кокса, так и на стойкости футеровки.
Регулирование процесса прокалки сводится к поддержанию заданной температуры, оптимальной длины зоны прокалки и ее положения в печи путем изменения количества топлива, кислорода воздуха и разрежения в печи. При изменении одного из регулируемых параметров необходимо принять меры к соответствующим изменениям и других параметров.
Таким образом, в результате физико-химических процессов при 1200— 1350°С в прокаливаемых углеродистых материалах возрастает относительное содержание углерода (в основном за счет снижения содержания водорода и в незначительной мере других элементов), полностью удаляется влага и основная масса летучих, происходит объемная усадка, увеличивается истинная плотность, повышаются злектропроводность и механическая прочность, резко снижается окисляемость (реакционная способность). Все эти превращения необходимы для получения анодной массы высокого качества.
Для производства анодной массы коксы должны иметь следующие характеристики:
— для пековых удельное электросопротивление не должно превышать 650 мкОм∙м, истинная плотность 1,99-2,01 г/см3
— для нефтяных. удельное электросопротивление не должно превышать 600 мкОм∙м, истинная плотность 2,02-2,04 г/см3
Для производства обожженных анодов нефтяные коксы должны иметь;
— удельное электросопротивление не должно превышат
|
|
Наброски и зарисовки растений, плодов, цветов: Освоить конструктивное построение структуры дерева через зарисовки отдельных деревьев, группы деревьев...
Историки об Елизавете Петровне: Елизавета попала между двумя встречными культурными течениями, воспитывалась среди новых европейских веяний и преданий...
Типы оградительных сооружений в морском порту: По расположению оградительных сооружений в плане различают волноломы, обе оконечности...
Индивидуальные очистные сооружения: К классу индивидуальных очистных сооружений относят сооружения, пропускная способность которых...
© cyberpedia.su 2017-2024 - Не является автором материалов. Исключительное право сохранено за автором текста.
Если вы не хотите, чтобы данный материал был у нас на сайте, перейдите по ссылке: Нарушение авторских прав. Мы поможем в написании вашей работы!