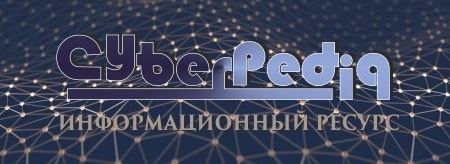
Общие условия выбора системы дренажа: Система дренажа выбирается в зависимости от характера защищаемого...
Особенности сооружения опор в сложных условиях: Сооружение ВЛ в районах с суровыми климатическими и тяжелыми геологическими условиями...
Топ:
История развития методов оптимизации: теорема Куна-Таккера, метод Лагранжа, роль выпуклости в оптимизации...
Комплексной системы оценки состояния охраны труда на производственном объекте (КСОТ-П): Цели и задачи Комплексной системы оценки состояния охраны труда и определению факторов рисков по охране труда...
Интересное:
Искусственное повышение поверхности территории: Варианты искусственного повышения поверхности территории необходимо выбирать на основе анализа следующих характеристик защищаемой территории...
Наиболее распространенные виды рака: Раковая опухоль — это самостоятельное новообразование, которое может возникнуть и от повышенного давления...
Влияние предпринимательской среды на эффективное функционирование предприятия: Предпринимательская среда – это совокупность внешних и внутренних факторов, оказывающих влияние на функционирование фирмы...
Дисциплины:
![]() |
![]() |
5.00
из
|
Заказать работу |
|
|
Содержание
Введение | |
1 Общая часть | 5 |
1.1 Организация технического контроля в машиностроительном производстве | |
1.2 Виды технического контроля | 7 |
1.3 Анализ причин возникновения брака при реализации технологического процесса изготовления детали | 10 |
2 Проектная часть | 12 |
2.1 Оценка соответствия режущего инструмента операциям механической обработки технологического процесса изготовления детали | |
2.2 Составление технологического маршрута процесса контроля. Выбор видов и средств технического контроля, с учетом характеристик технологического процесса изготовления детали | 22 |
2.3 Описание и расчет измерительного инструмента | 35 |
Заключение | 39 |
Список использованных источников | 40 |
Приложение А Комплект документации процесса технического контроля детали «Кронштейн» | 41 |
Введение
Детали создают основную массу объектов производства на любом машиностроительном предприятии. Этап изготовления деталей является наиболее многономенклатурным в любом производственном цикле. Трудоемкость и сложность подготовки и организации изготовления деталей усугубляется тем, что изделия выпускаются с низким качеством.
Полный цикл изготовления детали включает в себя важный этап – технический контроль. На стадии разработки продукции технический контроль заключается в проверке соответствия опытного образца техническому заданию, технической документации, правилам оформления, изложенным в ЕСКД (Единая система конструкторской документации). На стадии изготовления он охватывает качество, комплектность, упаковку, маркировку, количество предъявляемой продукции, ход производственных процессов; на стадии эксплуатации состоит в проверке соблюдения требований эксплуатационной и ремонтной документации.
|
Основной задачей курсового проекта является разработка контрольных операций для технологического процесса изготовления детали «Кронштейн».
Целью данного курсового проектирования является:
¾ выбор средств измерений при изготовлении детали;
¾ развитие и закрепление навыков ведения самостоятельной работы;
¾ анализ причин возникновения брака при реализации технологического процесса изготовления детали;
¾ оценка соответствия режущего инструмента операциям механической обработки технологического процесса изготовления детали;
¾ описание и расчет измерительного инструмента;
¾ обучение студента краткому изложению сущности проделанной работы, аргументированному объяснению принятого решения при ответах на вопросы.
Общая часть
Виды технического контроля
Технический контроль включает три основных этапа:
Получение первичной информации о фактическом состоянии объекта контроля, его контролируемых признаках и показателях.
Получение вторичной информации - отклонений от заданных параметров путем сопоставления первичной информации с запланированными критериями, нормами и требованиями.
Подготовка информации для выработки соответствующих управляющих воздействий на объект, подвергавшийся контролю.
Испытаниям подлежат опытные образцы (партии) и продукция серийного, массового и единичного производства. Опытный образец или опытную партию подвергают предварительным и приемочным испытаниям (проверкам) по специально разработанным программам.
Предварительные испытания проводят для определения соответствия продукции техническому заданию, требованиям стандартов, технической документации и для решения вопроса о возможности представления ее на приемочные испытания.
|
Приемочные испытания проводят с целью: определения соответствия продукции техническому заданию, требованиям стандартов и технической документации, оценке технического уровня; определения возможности постановки продукции на производство; выработки рекомендаций по установлению категории качества.
Этап производственного контроля включает в себя:
Входной контроль заключается в проверке качества сырья, материалов. Полуфабрикатов до начала их обработки с целью предотвращения поступления в производство бракованных предметов труда.
Промежуточный (текущий) контроль осуществляется в процессе изготовления продукции по отдельным операциям.
Окончательный (приёмочный) контроль предусматривает проверку годности продукции после её полной обработки для выявления некачественной.
Применяют следующие методы определения показателей качества продукции:
1) измерительные (методы метрологии). Осуществляется с помощью технических средств (метра, термометра и т.п.). Измеряются геометрические размеры, масса, содержание компонентов, твёрдость, электропроводность и т.д.;
2) регистрационный – осуществляется на основе наблюдений и подсчёта;
3) расчётный использует теоретические или эмпирические данные и зависимости;
4) органолептический. Например, внешний осмотр. Осуществляется на основе восприятия органов чувств (зрения, слуха, обоняния, вкуса, осязания);
5) экспертный – на основе решения, принимаемого группой специалистов – экспертов;
6) социологический – на основе мнений потребителей (опрос, анкетирование).
Сплошной контроль применяется в тех случаях, когда технологический процесс не обеспечивает достаточной стабильности заданных размеров и других параметров качества продукции; при неоднородности качества материалов или комплектующих изделий; после технологических операций, от которых в значительной мере зависят точность или другие качественные показатели изделия, а также при проверке сложной или точной готовой продукции.
При выборочном контроле качество контролируется только у некоторых деталей из партии и по их качеству судят обо всей партии. Для предъявления на контроль детали могут выбираться случайным образом. Выборочный контроль применяется гораздо чаще сплошного, поскольку полностью проконтролировать качество бывает сложно из–за больших объёмов выпускаемой продукции и высокой стоимости сплошного контроля.
|
Непрерывный контроль состоит в непрерывной проверке соответствия контролируемых размеров (или значений) нормам в течение всего процесса изготовления или определенной стадии жизненного цикла.
При периодическом контроле измерительную информацию получают периодически через установленные интервалы времени.
Большинство видов контроля проводится непосредственно на рабочих местах: у станка, на производственных участках, в цехах и т.п., такой контроль называют скользящим. Однако, осуществить такой контроль не всегда возможно, т.к. возникает необходимость применения специальных средств контроля, требующих отдельно расположенных контрольных участков, стендов, лабораторий, а иногда отдельно стоящих сооружений, как например радиационный контроль, такой контроль называют стационарным.
Активный контроль объекта осуществляется непосредственно в ходе технологического процесса формирования изделия, например, обработки детали на станке. Текущие результаты активного контроля дают информацию о необходимости изменения режимов обработки или корректировке параметров технологического оборудования, например, необходимость изменения положения между режущим инструментом и деталью.
Пассивный контроль осуществляется после завершения отдельной технологической операции или всего технологического цикла изготовления объекта (детали или изделия).
Летучий контроль — это контроль качества продукции или процессов, не предусмотренный в планах проведения технического контроля качества. Проводится в произвольные моменты времени.
Наиболее совершенные и рациональные способы организации контроля качества продукции в процессе производства основаны на использовании статистических методов. Суть статистических методов контроля состоит в том, что заключение о качестве изготовленной продукции и технологического процесса делают по результатам выборочного контроля параметров производимой продукции. Для того чтобы вовремя выявить нарушения в ходе процесса, необходимо периодически брать пробы (выборки), осуществлять измерение их параметров и в зависимости от результатов измерений либо продолжать процесс (если отклонений не выявлено), либо (если выявлены отклонения) остановить его и осуществить под наладку.
|
Текущий предупредительный контроль применяется на всех этапах производства, а также для периодической межоперационной проверки. К предупредительному контролю относятся: предварительный контроль материалов, заготовок и полуфабрикатов перед обработкой, обязательная проверка изделий в начале смены и после переналадки станка или смены инструмента, промежуточный (пооперационный или групповой контроль), контроль средств измерения, инструментов, оснастки, оборудования, а также контроль соблюдения технологической дисциплины.
Деталь «Кронштейн» изготавливается в условиях единичного производства.
Для контроля детали «Кронштейн» применяется выборочный операционный контроль, сплошной операционный контроль для высокоточных деталей и профилактический контроль первой детали.
Применяют универсальные средства контроля: калибры, шаблоны и специальные контрольные приспособления.
На отдельных операциях применяют механизированные и автоматические средства контроля.
Для контроля детали «Кронштейн» выбираем выборочный операционный контроль и окончательный приемочный контроль.
Входной контроль операции 005 проверяют наличие, комплектность и правильность сопроводительной документации, наличие клейм термообработки.
Операционный контроль – проводится проверка размеров после механических операций тех. процесса изготовление детали «Кронштейн» на рабочем месте самим рабочим.
Промежуточный контроль – производится проверка детали внешним осмотром, и проверка размеров – ШЦ – I – 150 – 0,05 ГОСТ 166, контролируют радиус поверхности – набором шаблонов радиусных №2 ТУ – 234 – 228, шероховатости поверхностей – образцами шероховатости 6,3 ФЦ ГОСТ 9378.
Окончательный контроль операции 0100 – производится проверка детали внешним осмотром. Проверка наличия и комплектности сопроводительной документации. Проверка закрытия всех операций по технологическому процессу. Клеймить окончательно. Сделать отметку в сопроводительной документации о закрытии контрольной операции.
Проектная часть
2.1 Оценка соответствия режущего инструмента операциям механической обработки технологического процесса изготовления детали
Технологический процесс - это часть производственного процесса, содержащая целенаправленные действия по изменению и (или) определению состояния предмета труда. К предметам труда относят заготовки и изделия.
|
Технологическая операция - это часть технологического процесса, выполняемая непрерывно на одном рабочем месте, над одним или несколькими одновременно обрабатываемыми или собираемыми изделиями, одним или несколькими рабочими.
Разработка технологического процесса изготовления детали «Кронштейн» начинается с выбора конкретных моделей станков, станочных приспособлений, режущих и мерительных инструментов. Для изготовления детали «Кронштейн» применятся стандартные и специальные режущие инструменты, которые приведены в таблице 1.
Таблица 1 – Оценка совместимости режущего инструмента
№ | Наименование операции | Обрабатываемые поверхности | Режущий инструмент |
1 | 2 | 3 | 4 |
020 | 1)Фрезеровать плоскости 1и 2 с переустановкой выдерживая размер 1 и ось симметрии детали. Данный эскиз показан на рисунке 1, в приложении А | 1)Фреза концевая Ø30 ГОСТ 53002 | |
1 | 2 | 3 | 4 |
025 | Фрезерная 1) Фрезеровать поверхность 1, выдерживая размер 1.Даный эскиз показан на рисунке2, в приложении А. | 1)Фреза Ø50 ГОСТ53002 |
Продолжение таблицы№1
1 | 2 | 3 | 4 |
030 | 1)Фрезеровать поверхность 3и2, выдерживая размер 2, с переустановкой. 2)Фрезеровать поверхности 1и2,выдержиая размер 1, с переустановкой. Данный эскиз показан на рисунке 3, в приложении А | 1)Фреза концевая Ø50 ГОСТ53002 | |
040 | Шлифовальная 1)Шлифовать поверхности 1и2 с переустановкой, выдерживая размер 1 Данный эскиз показан на рисунке 4, в приложении А. | 1)Шлифовальный круг 1-450х63х203 ГОСТ 6507 | |
045 | Шлифовальная 1)Шлифовать поверхность 1, выдерживая размер1 Данный эскиз показан на рисунке 5, в приложении А. | 1)Шлифовальный круг 1-450х63х203 ГОСТ 6507 |
Продолжение таблицы№1
1 | 2 | 3 | 4 |
050 | Расточная 1)Зацентровать отверстие выдерживая размеры 2и3. Данный эскиз представлен на рисунке 6,в приложении А. | 1) Сверло центровочное Ø4 ГОСТ 14032 2)Сверло Ø13 ГОСТ10903 | |
055 | Расточная 1)Зацентровать 2 отверстия выдерживая размеры 1,2,3 2)Сверлить 2 отверстия Ø 4, выдерживая размеры 1,2,3. Данный эскиз представлен на рисунке 7, в приложении А. | 1) Сверло центровочное Ø4 ГОСТ 14032 2)Сверло Ø9,5 ГОСТ 10903 | |
060 | Фрезерная 1)Фрезеровать занижения с 2-х сторон, выдерживая размеры 1,2,3,4. | 1)Фреза концевая Ø12 R4 ГОСТ 20534 | |
065 | Фрезерная ЧПУ 1)Фрезеровать контур детали | 1)Фреза концевая Ø24 ГОСТ 23248 | |
1 | 2 | 3 | 4 |
075 | Фрезерная 1)Фрезеровать две фаски | 1)Фреза концевая Ø20 ГОСТ 23248 |
Подробно рассмотрим характеристики режущих инструментов, которые используются при изготовлении детали «Кронштейн».
1. Фреза – это многолезвийный режущий инструмент, который представляет собой тело вращения с режущими зубьями на периферии или торце.
Виды фрез:
1) по расположению зубьев на исходном цилиндре – торцовые, цилиндрические, трехсторонние;
насадные концевые;
2) по виду обрабатываемой поверхности – угловые, шпоночные, фасонные, для Т – образных пазов, пазовые, отрезные, резьбовые, зуборезные и т.п.;
3) по расположению зуба на фрезе – прямозубые, с винтовым зубом и разнонаправленным зубом;
4) по виду задней поверхности – плоскозаточенные и затылованные;
5) по материалу, из которого изготовлена режущая часть фрезы – из быстрорежущей стали, из твердого сплава, из керамики, из эльбора;
6) по способу крепления режущих элементов – цельные с направленными пластинами, с рефлеными вставными ножами, с механическим креплением и т. д.;
7) по виду хвостовика для крепления фрезы в шпинделе – с цилиндрическим и коническим хвостовиком;
8) по размеру зубьев – с мелкими и крупными зубьями.
2. Спиральные сверлапредназначены для получения отверстий в сплошном материале. Различают:
1) твердосплавные сверлаприменяют для сверления заготовок из чугуна, цветных металлов, пластмассы, мрамора, гранита и других неметаллических материалов.
Сверла диаметром от 5 до 30 мм оснащают пластинами или коронками из твердого сплава. У сверл диаметром от 3 до 12 мм рабочую часть делают из твердого сплава и впаивают стальной хвостовик, так же эти сверла могут изготавливаться целиком из твердого сплава;
2) сверла для сверления глубоких отверстий. Под глубоким сверлением понимается сверление отверстий на глубину, превышающую диаметр сверла в 5 – 10 раз и более. Для сплошного сверления применяют сверла диаметром ≤ 80мм, а для кольцевого сверления – диаметром> 80мм;
3) спиральные сверла с отверстиями для подвода смазочно-охлаждающей жидкости (СОЖ);
4) шнековые – для сверления отверстий глубиной свыше 10 диаметров. Увеличенный угол наклона винтовой канавки (ω = 60°) позволяет сверлить без вывода сверла из отверстия для очистки от стружки;
5) четырехленточные спиральные сверла отличаются утолщенной сердцевиной и наличием на каждом зубе двух ленточек, образующих дополнительные канавки для подачи СОЖ.
3. Центровочные сверла используются для получения предварительного отверстия небольшого диаметра.
4. Резец – это режущий инструмент, предназначен для обработки деталей различных размеров, форм, точности и материалов. Является основным инструментом, применяемым при токарных, строгальных и долбёжных работах
Расточные резцы используют для растачивания отверстий, предварительно просверленных или полученных штамповкой или литьем. Существует два типа расточных резцов: проходные – для сквозного растачивания; упорные – для глухого растачивания.
5. Зенковки применяются для обработки входной и выходной части отверстия, а также для получения углублений под головки болтов, винтов, заклёпок.
6. Развертки применяются для окончательной обработки отверстий. Виды разверток:
1. По форме обрабатываемого отверстия – цилиндрические и конические;
2. По способу крепления – хвостовые и насадные;
3. По конструкции – цельные и сборные;
4. По способу применения – ручные и машинные.
Конические развертки предназначены для превращения цилиндрического отверстия в коническое или для калибрования (то есть уменьшения шероховатости) конического отверстия, предварительно обработанного другим инструментом.
2.2 Составление технологического маршрута процесса контроля. Выбор видов и средств технического контроля, с учетом характеристик технологического процесса изготовления детали
При выборе средств измерений должны учитываться:
1) допустимые значения погрешности для данного измерения;
2) допустимые отклонения;
3) методы проведения измерений и способы контроля.
Главным критерием выбора средств измерения является соответствие средств измерения требованиям достоверности измерений величин, получение настоящих значений с заданной точностью при минимальных временных и материальных затратах.
Для контроля детали «Кронштейн» применяют следующие средства контроля: штангенциркули, штангенрейсмас, угломер, калибры, шаблоны и специальные контрольные приспособления. По технологическому процессу выбираем следующие универсальные средства измерений:
1. Штангенинструменты – это средства измерений линейных размеров, основными частями которых являются штанга со шкалой и нониус (вспомогательная шкала для уточнения отсчета показаний).
Штангенинструменты делятся на:
- штенгенциркуль;
- штангенглубиномер;
- штангенрейсмас.
Штангенциркуль с отсчетом по нониусу типа ШЦ – I ГОСТ 166 с двухсторонним расположением губок предназначен для измерения наружных и внутренних поверхностей, а также для измерения глубины отверстий и уступов. Диапазон измерений ШЦ – I от 0 до 125 мм. На рисунке 1 приведен эскиз штангенциркуля типа ШЦ – I.
Рисунок 1 – Эскиз штангенциркуля ШЦ – I ГОСТ 166
Штангенциркуль ШЦ – I состоит из: 1 – штанги; 2 – внутренних губок; 3 – стопорного винта; 4 – рамки; 5 – линейкинониус: 6 – глубиномера; 7 – внешних губок.
Штангенциркуль типа ШЦ – I (150 – 0,05) ГОСТ 166 с двухсторонним расположением губок, оснащенных твердым сплавом, предназначен для наружных и внутренних измерений, может применяться для разметочных работ. Имеет устройство тонкой подачи. Имеет двойную шкалу: в миллиметрах и дюймах. Имеет губки с плоскими и цилиндрическими измерительными поверхностями для измерения наружных и внутренних размеров соответственно, а также губки с кромочными измерительными поверхностями для измерения наружных размеров. Длина основных губок может быть разная в зависимости от модификации. На рисунке 2 приведен эскиз штангенциркуля типа ШЦ – II.
Рисунок 2 – Эскиз штангенциркуля ШЦ – II ГОСТ 166
Штангенциркуль ШЦ – II состоит из: 1 – внутреннихгубкок; 2 – рамки; 3 – зажима для рамки; 4 – штанги; 5 – шкалы штанги; 6 – шкалы нониуса; 7 – наружных губок.
Штангенрейсмасы ГОСТ 164применяются для пространственной разметки и прямых измерений на точной плите расстояний от базовых поверхностей деталей до выемок, выступов и осей отверстий. Оснащен устройством точной подачи. Диапазон измерений 0 – 250 мм. Цена деления 0,05 мм. Твердосплавный наконечник измерительной лапки. На рисунке 3 приведен эскиз штангенрейсмаса.
Рисунок 3 – Эскиз штангенрейсмаса
Штангенрейсмас состоит из: 1 – основания; 2 – разметочной ножки; 3 – рамки; 4 –шкалы нониуса; 5 – винта и гайки микрометрической подачи; 6 – штанги; 7 – микрометрической подачи; 8, 9 – стопорных винтов.
Калибры – это жесткие средства контроля, применяемые для определения годности размеров элементов деталей машин.
В зависимости от формы контролируемой поверхности калибры разделяют на: гладкие – для контроля деталей гладких цилиндрических соединений, резьбовые – для контроля деталей резьбовых соединений, шлицевые – для контроля деталей шлицевых соединений, конусные гладкие – для контроля деталей конусных гладких соединений и специальные – для контроля деталей нестандартных соединений и контроля отдельных деталей специальной формы.
Предельные гладкие калибры. Предельными эти калибры называют потому, что ими контролируют годность наибольшего и наименьшего предельных размеров элемента детали. Такие калибры разделяют на проходной ПР и непроходной НЕ. Калибры для контроля отверстий называют пробками. Проходным калибром-пробкой ПР контролируют в отверстии годность наименьшего предельного размера Dmin. Этот размер годен, если пробка ПР проходит сквозь него. Непроходным калибром-пробкой НЕ контролируют в отверстии годность наибольшего предельного размера Dmax. Этот размер годен, если пробка НЕ не проходит в отверстие. Если пробка ПР прошла, а пробка НЕ не вошла в отверстие, то принято считать, что действительный размер отверстия находится в пределах поля допуска TD и это отверстие годно.
Когда калибры ПР не проходят, а калибры НЕ проходят через детали, принято считать, что действительные размеры этих деталей находятся за пределами поля допуска, и эти детали признаются браком.
При контроле калибрами не определяют числовые величины контролируемых размеров, а только устанавливают годность или негодность элемента детали. Когда требуется определить числовую величину действительного размера забракованной детали, то его измеряют универсальными средствами измерения. Так поступают для того, чтобы найти причину брака, а также для того, чтобы решить, можно ли исправить забракованную деталь. Это делают всегда, когда калибр ПР не проходит, т. е. вал велик или отверстие мало и брак исправимый.
Пробка гладкая ГСОТ 14810 – пробка гладкая используется для контроля внутренних диаметров цилиндрических отверстий детали. На рисунке 4 приведен эскиз калибра-пробки гладкой Ø13Н12мм.
Калибр пробка состоит из 1. Проходная часть, 2. Непроходная часть, 3. Ручка
Рисунок 4 – Эскиз калибра-пробки гладкой
2. Шаблоны предназначены для проверки деталей сложного профиля.
Профиль шаблона представляет собой ту идеальную форму, которую следует придать детали. Проверка шаблоном заключается в прикладывании его к изделию и оценке величины световой щели между проверяемым профилем и измерительной кромкой шаблона.
Радиусомер №1 ТУ 2.034 – 228 – шаблоны радиусные предназначены для оценки радиусов выпуклых и вогнутых поверхностей.
Изготовляются три набора радиусных шаблонов:
Шаблон радиусный №1 R = 1.0 - 6.0 мм;
Шаблон радиусный №2 R = 8.0 - 25.0 мм;
Шаблон радиусный №3 R = 7.0 - 25.0мм.
Каждый набор укомплектован шаблонами для контроля как внутреннего, так и наружного радиусов.
Конструкция обоймы набора обеспечивает возможность свободной замены шаблона, а также регулирования плавности вращения их на оси.
На рисунке 5 приведен эскиз шаблона радиусного.
Рисунок 5 – Эскиз шаблона радиусного
По технологическому процессу изготовления детали «Кронштейн», поверхности контролируются с помощью различных средств контроля, которые приведены ниже в таблице 1.
Таблица 2 – Оценка совместимости мерительного инструмента
№ | Наименование операции | Контролируемые поверхности | Мерительный инструмент |
1 | 2 | 3 | 4 |
020 | Фрезерная | 1. Шт.циркуль ЩЦ2-160-0,05 ГОСТ 166 | |
025 | Фрезерная | 1. Микрометр МК50 ГОСТ 6507 |
Продолжение таблицы№2
1 | 2 | 3 | 4 |
030 | Фрезерная | 1. Шт.цируль ШЦ2-160-0,05 ГОСТ 166 | |
040 | Шлифовальная | 1. Микрометр МК 50-1 ГОСТ 6507 | |
045 | Шлифовальная | 1. Микрометр МК 50-1 ГОСТ 6507 |
Продолжение таблицы№2
1 | 2 | 3 | 4 |
050 | Расточная | 1. Шт.циркуль ШЦ1-150-0,02 ГОСТ 166 2.Штырь технологический Ø4 6900-2026 3.Колибр-пробка Ø13Н12 ГОСТ 14810 4.Штырь технологический Ø13 ГОСТ6900-2026 5.Штангенрейсмасс ШР-250-0,05 ГОСТ 164 | |
055 | Расточная | 1. 1) Шт.циркуль ШЦ1-150-0,02 ГОСТ 166 2.Штырь технологический Ø4 6900-2026 3.Штангенрейсмасс ШР-250-0,05 ГОСТ 164 4.Колибр-пробка Ø9,5Н12 ГОСТ14810 5.Штыри технологические Ø9,5 ГОСТ 6900-2026 6.Микрометр МР50 ГОСТ4381 | |
060 | Фрезерная | 1. Штангенциркуль ШЦ2-160-0,05 ГОСТ 166 2.Микрометр МК25 ГОСТ 2507 3.Набор шаблонов радиусных№1 8450-8287 4.Штангенрейсмасс ШР-250-0,05 ГОСТ164 5.Штырь технологический Ø13 6900 | |
1 | 2 | 3 | 4 |
065 | Фрезерная ЧПУ | 1)Штангенциркуль ШЦ2-160-0,05 ГОСТ 166 2)Радиусный шаблон 3)Угломер | |
075 | Фрезерная | 1)Набор шаблонов для замера фасок 8450-6144 |
2.3 Описание и расчет измерительного инструмента
Описание и расчет измерительного инструмента на операцию 050 расточную
Калибры – бесшкальные измерительные инструменты, предназначенные для контроля размеров, формы и взаимного расположения поверхностей.
Для контроля размеров гладких цилиндрических изделий применяются предельные калибры, имеющие два размера: проходной (ПР) и непроходной (НЕ), ограничивающие наибольший и наименьший предельные размеры изделий.
При контроле калибрами не определяется истинная величина размера. Контроль устанавливает, находится ли действительный размер изделия в пределах допуска или вне их. Если проходной калибр (при контроле изделий средних размеров) проходит под действием собственного веса, а непроходной не проходит, то изделие считается годным.
Калибры для гладких цилиндрических изделий подразделяются на калибры для проверки отверстий–пробки и калибры, для проверки валов–скобы (или кольца).
Благодаря простоте и удобству измерения, незначительному времени на контроль, калибры нашли широкое применение в серийном и массовом производстве, в машиностроении и приборостроении.
По назначению гладкие калибры подразделяются на рабочие и контрольные (контркалибры), которые обозначаются:
ПР – рабочий проходной калибр;
НЕ – рабочий непроходной калибр;
К-ПР – контркалибр для проверки новых рабочих проходных скоб;
К-НЕ – контркалибр для проверки новых рабочих непроходных скоб;
К-И – контркалибр для контроля износа рабочих проходных скоб.
Контркалибры к калибрам для отверстий не предусматриваются, так как пробки (наружный размер) легко проверить универсальными измерительными средствами.
Контркалибры для проверки скоб представляют собой, пробки или мерные шайбы. Они применяются для проверки скоб в процессе их эксплуатации. Контрольные калибры К-ПР и К-НЕ должны проходить в новые контролируемые скобы. При этом устанавливается, что размер скобы не уменьшается в результате повреждения во время эксплуатации или естественного старения.
Контрольный калибр К-И не должен проходить в контролируемую скобу. Если он проходит, то это означает, что проходная скоба должна быть изъята из эксплуатации вследствие износа.
Для контроля внутренней цилиндрической поверхности 13Н12, необходимо произвести расчеты исполнительных размеров калибра-пробки.
Определяем исполнительные размеры калибра–пробки для отверстия Ø13Н12, обрабатываемого на операции 050 расточная.
1. Находим основное (нижнее) отклонение по таблице «Значения основных отклонений отверстий» (таблица 8 СТ СЭВ 145 – 75 [3]) –EI = 0.
2. По таблице «Значения допусков» (таблица 6 СТ СЭВ 145 – 75 [3]) находим, что допуск 12 квалитета для интервалов размеров свыше 1 до 3 мм, равен 25 мкм. Тогда второе верхнее отклонение для 5Н13 будет равняться:
ES = EI + IT7 = 0 + 25 мкм
где ES – верхнее отклонение отверстия;
EI – нижнее отклонение отверстия;
IT – допуск размера.
3. Находим предельные размеры изделия, которые соответственно являются номинальными размерами калибра:
Dmin = 5 + 0 = 5 мм;
Dmax = 5 + 0,25 = 5,25 мм;
где Dmin – наименьший предельный размер изделия;
Dmax – наибольший предельный размер изделия.
4. По табличным значениям (таблица 2 СТ СЭВ 157 – 75 [4]) находим:
Z= 6 мкм
H= 2,5 мкм
Y= 0 мкм
где Z – отклонение середины поля допуска на изготовление проходного калибра для отверстия относительно наименьшего предельного размера изделия;
H – допуск на изготовление калибров (за исключением калибров со сферическими измерительными поверхностями) для отверстия;
Y – допустимый выход размера изношенного проходного калибра для отверстия за границу поля допуска изделия.
5. Наибольший размер проходной стороны новой пробки определяем по формуле:
Прmax = Dmin + Z + H / 2, (мм) (1)
где ПРmax – наибольший размер проходной стороны новой пробки;
Dmin – наименьший предельный размер изделия;
Z – отклонение середины поля допуска на изготовление проходного калибра для отверстия относительно наименьшего предельного размера изделия;
H – допуск на изготовление калибров (за исключением калибров со сферическими измерительными поверхностями) для отверстия;
Определяем наибольший размер проходной стороны новой пробки по формуле (1):
ПРmax =13 + 0,006 + 0,0025 / 2 = 13,0072 (мм)
Исполнительный размер проходной стороны:
ПР = 13,0072-0,0025.
(За исполнительный размер пробки принимается наибольший предельный размер пробки, и допуск располагается «в тело»).
6. Наименьший размер изношенной проходной стороны определяем по формуле:
Призн = Dmin – Y, (мм), (2)
где Dmin – наименьший предельный размер изделия;
Y – допустимый выход размера изношенного проходного калибра для отверстия за границу поля допуска изделия.
Определяем наименьший размер изношенной проходной стороны по формуле (2):
ПРизн = 13 – 0 = 13 (мм).
(При достижении, в результате износа этого размера, пробка ПР должна быть изъята из эксплуатации).
7. Наибольший размер непроходной стороны пробки определяется по формуле:
НЕmax = Dmax + H / 2 , (мм), (3)
где НЕmax – наибольший размер непроходной стороны пробки;
Dmax – наибольший предельный размер изделия;
H – допуск на изготовление калибров (за исключением калибров со сферическими измерительными поверхностями) для отверстия.
Определяем наибольший размер непроходной стороны пробки по формуле (3):
НЕmax = 13,025 + 0,0025 / 2 = 13,025125 (мм)
Исполнительный размер непроходной стороны:
НЕ = 13,025125-0,0025
На основании данных расчета строим схему расположения полей допусков для отверстия Ø13Н12, которая представлена на рисунке 6.
Рисунок 6 – Схема расположения полей допусков отверстия Ø13Н12
Заключение
Технический контроль является важным этапом при изготовлении деталей. На стадии разработки продукции технический контроль заключается в проверке соответствия опытного образца техническому заданию, технической документации, правилам оформления, изложенным в ЕСКД (Единая система конструкторской документации). На стадии изготовления он охватывает качество, комплектность, упаковку, маркировку, количество предъявляемой продукции, ход производственных процессов; на стадии эксплуатации состоит в проверке соблюдения требований эксплуатационной и ремонтной документации.
При разработке курсового проекта были достигнуты следующие цели:
¾ выбор средств измерений при изготовлении детали;
¾ развитие и закрепление навыков ведения самостоятельной работы;
¾ анализ причин возникновения брака при реализации технологического процесса изготовления детали;
¾ оценка соответствия режущего инструмента операциям механической обработки технологического процесса изготовления детали;
¾ описание и расчет измерительного инструмента;
¾ обучение студента краткому изложению сущности проделанной работы, аргументированному объяснению принятого решения при ответах на вопросы.
В ходе проектирования данного курсового проекта были разработаны контрольные операции для технологического процесса изготовления детали «Шток». Дана характеристика организации технического контроля в машиностроительном производстве; видов технического контроля. Проанализированы причины возникновения брака при реализации технологического процесса изготовления детали. Дана оценка соответствия режущего инструмента операциям механической обработки технологического процесса изготовления детали «Кронштейн». Составлен технологический маршрут процесса контроля. Произведен расчет специального измерительного инструмента.
Дополнительные источники
1. Ермолаев В.В. Технологическая оснастка. Практикум. – М: Академия, 2012. – 36 с.
2. Карпицкий В.Р. Общий курс слесарного дела: учебное пособие - 2-е изд. - М: ИНФРА-М, 2012. - 400 с.: ил.
3. Курсовое проектирование деталей машин. - 3-е изд., перер. и доп. - М: ИНФРА-М, 2014. - 414 с.: ил.
4. Новиков В.Ю., Ильянков А.И. Технология машино
|
|
Таксономические единицы (категории) растений: Каждая система классификации состоит из определённых соподчиненных друг другу...
История развития хранилищ для нефти: Первые склады нефти появились в XVII веке. Они представляли собой землянные ямы-амбара глубиной 4…5 м...
Архитектура электронного правительства: Единая архитектура – это методологический подход при создании системы управления государства, который строится...
Кормораздатчик мобильный электрифицированный: схема и процесс работы устройства...
© cyberpedia.su 2017-2024 - Не является автором материалов. Исключительное право сохранено за автором текста.
Если вы не хотите, чтобы данный материал был у нас на сайте, перейдите по ссылке: Нарушение авторских прав. Мы поможем в написании вашей работы!