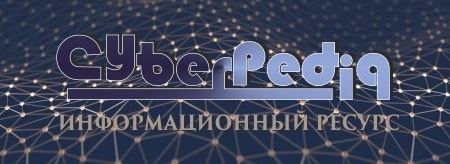
История создания датчика движения: Первый прибор для обнаружения движения был изобретен немецким физиком Генрихом Герцем...
Индивидуальные очистные сооружения: К классу индивидуальных очистных сооружений относят сооружения, пропускная способность которых...
Топ:
Организация стока поверхностных вод: Наибольшее количество влаги на земном шаре испаряется с поверхности морей и океанов...
Генеалогическое древо Султанов Османской империи: Османские правители, вначале, будучи еще бейлербеями Анатолии, женились на дочерях византийских императоров...
Интересное:
Уполаживание и террасирование склонов: Если глубина оврага более 5 м необходимо устройство берм. Варианты использования оврагов для градостроительных целей...
Влияние предпринимательской среды на эффективное функционирование предприятия: Предпринимательская среда – это совокупность внешних и внутренних факторов, оказывающих влияние на функционирование фирмы...
Что нужно делать при лейкемии: Прежде всего, необходимо выяснить, не страдаете ли вы каким-либо душевным недугом...
Дисциплины:
![]() |
![]() |
5.00
из
|
Заказать работу |
|
|
Браком на производстве считается продукция, по своим техническим или качественным характеристикам не соответствующая стандарту данного вида продукции и не способная выполнять функции, предусмотренные для данного изделия. Бракованной может быть признана продукция на любой стадии производства.
Анализ брака проводят по следующим направлениям:
1) по способу использования - на брак исправимый и неисправимый. Если изделие после доработки можно использовать в том качестве, для которого оно и предназначалось первоначально, брак считается исправимым. В противном случае возможны несколько путей его использования: как заготовка для других изделий в том же производстве; как материал для основного производства; для реализации на сторону;
2) по цехам и операциям по отдельности - обнаружившие брак и виновные за его производство. По виновникам различают брак, допущенный по вине рабочего-оператора; рабочего - наладчика оборудования; отделов главного технолога, главного конструктора, главного механика; инструментального цеха; отдела технического контроля качества;
3) по причинам происхождения брака. Причин может быть множество, например, некачественное сырье и материалы; неверно выполненные чертежи и иная техническая документация; несоответствующее оборудование и инструмент; неэффективная организация производства и управления; отсутствие должного контроля на предыдущих стадиях производства;
4) по бракующим признакам (в чем состоит брак);
5) по месту обнаружения брак делится на: внутренний (выявленный на предприятии до отправки продукции потребителям) и внешний (выявленный у покупателей в процессе сборки, монтажа или эксплуатации изделия). Внешний брак свидетельствует как о плохом качестве продукции, так и о неудовлетворительной работе контрольных служб предприятия и называется рекламацией. Появление рекламаций наносит производителю не только материальный, но и моральный ущерб, сказываясь на его репутации.
|
Анализ брака на предприятии преследует две основные цели: первая из них заключается в выявлении причин брака и их дальнейшем устранении.
Второй важной целью проведения такого анализа является выявление виновных в том, что часть продукции предприятия оказалась не соответствующей нормативам. С этой точки зрения, анализ брака является частью контроля эффективности деятельности всех работников предприятия.
Каждая партия продукции предъявляется на контроль с сопроводительной документацией, в которой контролер отмечает результаты проверки качества. При обнаружении в предъявленной продукции неисправимого брака контролер обязан оформить его актом. Исправимый брак возвращается на доработку. Акт является основным и единым первичным документом для учета и анализа брака. Он должен содержать только необходимые сведения: наименование изделия, а также операции, на которой образовался брак, характеристику брака с указанием шифра его вида, причины брака и его виновника (согласно классификатору), сумму потерь, подлежащую взысканию с виновника.
Весь выявленный брак помечается клеймом, немедленно изымается и направляется на склад-изолятор (используются на крупных предприятиях), откуда передается на склад утиля.
Если брак продукции обнаруживается у потребителя, на предприятие поступает рекламация (претензия покупателя или заказчика, предъявляемая продавцу или поставщику по поводу ненадлежащего качества или количества поставляемого товара, требование об устранении недостатков, снижении цены, возмещении убытков). В ней указываются причины, вследствие которых продукция не удовлетворяет требованиям заказчика. Предприятие проверяет обоснованность рекламации и бракованную продукцию заменяют годной, возмещая потребителю убытки. Возврат дефектной или бракованной продукции по каждому производственному звену учитывается при оценке эффективности его работы, подведении итогов деятельности всего предприятия.
|
Чтобы сократить потери от брака, необходимо:
1. Наладить тщательный контроль за качеством продукции в процессе ее изготовления и соблюдением технологического режима на отдельных стадиях производства.
2. Организовать точный и своевременный учет брака (окончательного и исправимого) — документооборот во всех цехах и на всех переделах, операциях, а также причин и конкретных виновников брака.
3. Организовать учет затрат по центрам ответственности (по цехам, производственным участкам).
4. Выявить полную сумму потерь от брака во всех цехах предприятия и принять меры к возмещению причиненного предприятию ущерба.
5. Строго соблюдать установленный порядок учета потерь от брака.
Первый документ, в котором фиксируется брак, — это сменное задание, наряд, рапорт или маршрутная карта. Главная задача этих документов — зафиксировать трудозатраты и выполненный объем работ.
Проектная часть
2.1 Оценка соответствия режущего инструмента операциям механической обработки технологического процесса изготовления детали
Технологический процесс - это часть производственного процесса, содержащая целенаправленные действия по изменению и (или) определению состояния предмета труда. К предметам труда относят заготовки и изделия.
Технологическая операция - это часть технологического процесса, выполняемая непрерывно на одном рабочем месте, над одним или несколькими одновременно обрабатываемыми или собираемыми изделиями, одним или несколькими рабочими.
Разработка технологического процесса изготовления детали «Кронштейн» начинается с выбора конкретных моделей станков, станочных приспособлений, режущих и мерительных инструментов. Для изготовления детали «Кронштейн» применятся стандартные и специальные режущие инструменты, которые приведены в таблице 1.
Таблица 1 – Оценка совместимости режущего инструмента
№ | Наименование операции | Обрабатываемые поверхности | Режущий инструмент |
1 | 2 | 3 | 4 |
020 | 1)Фрезеровать плоскости 1и 2 с переустановкой выдерживая размер 1 и ось симметрии детали. Данный эскиз показан на рисунке 1, в приложении А | 1)Фреза концевая Ø30 ГОСТ 53002 | |
1 | 2 | 3 | 4 |
025 | Фрезерная 1) Фрезеровать поверхность 1, выдерживая размер 1.Даный эскиз показан на рисунке2, в приложении А. | 1)Фреза Ø50 ГОСТ53002 |
Продолжение таблицы№1
|
1 | 2 | 3 | 4 |
030 | 1)Фрезеровать поверхность 3и2, выдерживая размер 2, с переустановкой. 2)Фрезеровать поверхности 1и2,выдержиая размер 1, с переустановкой. Данный эскиз показан на рисунке 3, в приложении А | 1)Фреза концевая Ø50 ГОСТ53002 | |
040 | Шлифовальная 1)Шлифовать поверхности 1и2 с переустановкой, выдерживая размер 1 Данный эскиз показан на рисунке 4, в приложении А. | 1)Шлифовальный круг 1-450х63х203 ГОСТ 6507 | |
045 | Шлифовальная 1)Шлифовать поверхность 1, выдерживая размер1 Данный эскиз показан на рисунке 5, в приложении А. | 1)Шлифовальный круг 1-450х63х203 ГОСТ 6507 |
Продолжение таблицы№1
1 | 2 | 3 | 4 |
050 | Расточная 1)Зацентровать отверстие выдерживая размеры 2и3. Данный эскиз представлен на рисунке 6,в приложении А. | 1) Сверло центровочное Ø4 ГОСТ 14032 2)Сверло Ø13 ГОСТ10903 | |
055 | Расточная 1)Зацентровать 2 отверстия выдерживая размеры 1,2,3 2)Сверлить 2 отверстия Ø 4, выдерживая размеры 1,2,3. Данный эскиз представлен на рисунке 7, в приложении А. | 1) Сверло центровочное Ø4 ГОСТ 14032 2)Сверло Ø9,5 ГОСТ 10903 | |
060 | Фрезерная 1)Фрезеровать занижения с 2-х сторон, выдерживая размеры 1,2,3,4. | 1)Фреза концевая Ø12 R4 ГОСТ 20534 | |
065 | Фрезерная ЧПУ 1)Фрезеровать контур детали | 1)Фреза концевая Ø24 ГОСТ 23248 | |
1 | 2 | 3 | 4 |
075 | Фрезерная 1)Фрезеровать две фаски | 1)Фреза концевая Ø20 ГОСТ 23248 |
Подробно рассмотрим характеристики режущих инструментов, которые используются при изготовлении детали «Кронштейн».
1. Фреза – это многолезвийный режущий инструмент, который представляет собой тело вращения с режущими зубьями на периферии или торце.
Виды фрез:
1) по расположению зубьев на исходном цилиндре – торцовые, цилиндрические, трехсторонние;
насадные концевые;
2) по виду обрабатываемой поверхности – угловые, шпоночные, фасонные, для Т – образных пазов, пазовые, отрезные, резьбовые, зуборезные и т.п.;
|
3) по расположению зуба на фрезе – прямозубые, с винтовым зубом и разнонаправленным зубом;
4) по виду задней поверхности – плоскозаточенные и затылованные;
5) по материалу, из которого изготовлена режущая часть фрезы – из быстрорежущей стали, из твердого сплава, из керамики, из эльбора;
6) по способу крепления режущих элементов – цельные с направленными пластинами, с рефлеными вставными ножами, с механическим креплением и т. д.;
7) по виду хвостовика для крепления фрезы в шпинделе – с цилиндрическим и коническим хвостовиком;
8) по размеру зубьев – с мелкими и крупными зубьями.
2. Спиральные сверлапредназначены для получения отверстий в сплошном материале. Различают:
1) твердосплавные сверлаприменяют для сверления заготовок из чугуна, цветных металлов, пластмассы, мрамора, гранита и других неметаллических материалов.
Сверла диаметром от 5 до 30 мм оснащают пластинами или коронками из твердого сплава. У сверл диаметром от 3 до 12 мм рабочую часть делают из твердого сплава и впаивают стальной хвостовик, так же эти сверла могут изготавливаться целиком из твердого сплава;
2) сверла для сверления глубоких отверстий. Под глубоким сверлением понимается сверление отверстий на глубину, превышающую диаметр сверла в 5 – 10 раз и более. Для сплошного сверления применяют сверла диаметром ≤ 80мм, а для кольцевого сверления – диаметром> 80мм;
3) спиральные сверла с отверстиями для подвода смазочно-охлаждающей жидкости (СОЖ);
4) шнековые – для сверления отверстий глубиной свыше 10 диаметров. Увеличенный угол наклона винтовой канавки (ω = 60°) позволяет сверлить без вывода сверла из отверстия для очистки от стружки;
5) четырехленточные спиральные сверла отличаются утолщенной сердцевиной и наличием на каждом зубе двух ленточек, образующих дополнительные канавки для подачи СОЖ.
3. Центровочные сверла используются для получения предварительного отверстия небольшого диаметра.
4. Резец – это режущий инструмент, предназначен для обработки деталей различных размеров, форм, точности и материалов. Является основным инструментом, применяемым при токарных, строгальных и долбёжных работах
Расточные резцы используют для растачивания отверстий, предварительно просверленных или полученных штамповкой или литьем. Существует два типа расточных резцов: проходные – для сквозного растачивания; упорные – для глухого растачивания.
5. Зенковки применяются для обработки входной и выходной части отверстия, а также для получения углублений под головки болтов, винтов, заклёпок.
6. Развертки применяются для окончательной обработки отверстий. Виды разверток:
|
1. По форме обрабатываемого отверстия – цилиндрические и конические;
2. По способу крепления – хвостовые и насадные;
3. По конструкции – цельные и сборные;
4. По способу применения – ручные и машинные.
Конические развертки предназначены для превращения цилиндрического отверстия в коническое или для калибрования (то есть уменьшения шероховатости) конического отверстия, предварительно обработанного другим инструментом.
2.2 Составление технологического маршрута процесса контроля. Выбор видов и средств технического контроля, с учетом характеристик технологического процесса изготовления детали
При выборе средств измерений должны учитываться:
1) допустимые значения погрешности для данного измерения;
2) допустимые отклонения;
3) методы проведения измерений и способы контроля.
Главным критерием выбора средств измерения является соответствие средств измерения требованиям достоверности измерений величин, получение настоящих значений с заданной точностью при минимальных временных и материальных затратах.
Для контроля детали «Кронштейн» применяют следующие средства контроля: штангенциркули, штангенрейсмас, угломер, калибры, шаблоны и специальные контрольные приспособления. По технологическому процессу выбираем следующие универсальные средства измерений:
1. Штангенинструменты – это средства измерений линейных размеров, основными частями которых являются штанга со шкалой и нониус (вспомогательная шкала для уточнения отсчета показаний).
Штангенинструменты делятся на:
- штенгенциркуль;
- штангенглубиномер;
- штангенрейсмас.
Штангенциркуль с отсчетом по нониусу типа ШЦ – I ГОСТ 166 с двухсторонним расположением губок предназначен для измерения наружных и внутренних поверхностей, а также для измерения глубины отверстий и уступов. Диапазон измерений ШЦ – I от 0 до 125 мм. На рисунке 1 приведен эскиз штангенциркуля типа ШЦ – I.
Рисунок 1 – Эскиз штангенциркуля ШЦ – I ГОСТ 166
Штангенциркуль ШЦ – I состоит из: 1 – штанги; 2 – внутренних губок; 3 – стопорного винта; 4 – рамки; 5 – линейкинониус: 6 – глубиномера; 7 – внешних губок.
Штангенциркуль типа ШЦ – I (150 – 0,05) ГОСТ 166 с двухсторонним расположением губок, оснащенных твердым сплавом, предназначен для наружных и внутренних измерений, может применяться для разметочных работ. Имеет устройство тонкой подачи. Имеет двойную шкалу: в миллиметрах и дюймах. Имеет губки с плоскими и цилиндрическими измерительными поверхностями для измерения наружных и внутренних размеров соответственно, а также губки с кромочными измерительными поверхностями для измерения наружных размеров. Длина основных губок может быть разная в зависимости от модификации. На рисунке 2 приведен эскиз штангенциркуля типа ШЦ – II.
Рисунок 2 – Эскиз штангенциркуля ШЦ – II ГОСТ 166
Штангенциркуль ШЦ – II состоит из: 1 – внутреннихгубкок; 2 – рамки; 3 – зажима для рамки; 4 – штанги; 5 – шкалы штанги; 6 – шкалы нониуса; 7 – наружных губок.
Штангенрейсмасы ГОСТ 164применяются для пространственной разметки и прямых измерений на точной плите расстояний от базовых поверхностей деталей до выемок, выступов и осей отверстий. Оснащен устройством точной подачи. Диапазон измерений 0 – 250 мм. Цена деления 0,05 мм. Твердосплавный наконечник измерительной лапки. На рисунке 3 приведен эскиз штангенрейсмаса.
Рисунок 3 – Эскиз штангенрейсмаса
Штангенрейсмас состоит из: 1 – основания; 2 – разметочной ножки; 3 – рамки; 4 –шкалы нониуса; 5 – винта и гайки микрометрической подачи; 6 – штанги; 7 – микрометрической подачи; 8, 9 – стопорных винтов.
Калибры – это жесткие средства контроля, применяемые для определения годности размеров элементов деталей машин.
В зависимости от формы контролируемой поверхности калибры разделяют на: гладкие – для контроля деталей гладких цилиндрических соединений, резьбовые – для контроля деталей резьбовых соединений, шлицевые – для контроля деталей шлицевых соединений, конусные гладкие – для контроля деталей конусных гладких соединений и специальные – для контроля деталей нестандартных соединений и контроля отдельных деталей специальной формы.
Предельные гладкие калибры. Предельными эти калибры называют потому, что ими контролируют годность наибольшего и наименьшего предельных размеров элемента детали. Такие калибры разделяют на проходной ПР и непроходной НЕ. Калибры для контроля отверстий называют пробками. Проходным калибром-пробкой ПР контролируют в отверстии годность наименьшего предельного размера Dmin. Этот размер годен, если пробка ПР проходит сквозь него. Непроходным калибром-пробкой НЕ контролируют в отверстии годность наибольшего предельного размера Dmax. Этот размер годен, если пробка НЕ не проходит в отверстие. Если пробка ПР прошла, а пробка НЕ не вошла в отверстие, то принято считать, что действительный размер отверстия находится в пределах поля допуска TD и это отверстие годно.
Когда калибры ПР не проходят, а калибры НЕ проходят через детали, принято считать, что действительные размеры этих деталей находятся за пределами поля допуска, и эти детали признаются браком.
При контроле калибрами не определяют числовые величины контролируемых размеров, а только устанавливают годность или негодность элемента детали. Когда требуется определить числовую величину действительного размера забракованной детали, то его измеряют универсальными средствами измерения. Так поступают для того, чтобы найти причину брака, а также для того, чтобы решить, можно ли исправить забракованную деталь. Это делают всегда, когда калибр ПР не проходит, т. е. вал велик или отверстие мало и брак исправимый.
Пробка гладкая ГСОТ 14810 – пробка гладкая используется для контроля внутренних диаметров цилиндрических отверстий детали. На рисунке 4 приведен эскиз калибра-пробки гладкой Ø13Н12мм.
Калибр пробка состоит из 1. Проходная часть, 2. Непроходная часть, 3. Ручка
Рисунок 4 – Эскиз калибра-пробки гладкой
2. Шаблоны предназначены для проверки деталей сложного профиля.
Профиль шаблона представляет собой ту идеальную форму, которую следует придать детали. Проверка шаблоном заключается в прикладывании его к изделию и оценке величины световой щели между проверяемым профилем и измерительной кромкой шаблона.
Радиусомер №1 ТУ 2.034 – 228 – шаблоны радиусные предназначены для оценки радиусов выпуклых и вогнутых поверхностей.
Изготовляются три набора радиусных шаблонов:
Шаблон радиусный №1 R = 1.0 - 6.0 мм;
Шаблон радиусный №2 R = 8.0 - 25.0 мм;
Шаблон радиусный №3 R = 7.0 - 25.0мм.
Каждый набор укомплектован шаблонами для контроля как внутреннего, так и наружного радиусов.
Конструкция обоймы набора обеспечивает возможность свободной замены шаблона, а также регулирования плавности вращения их на оси.
На рисунке 5 приведен эскиз шаблона радиусного.
Рисунок 5 – Эскиз шаблона радиусного
По технологическому процессу изготовления детали «Кронштейн», поверхности контролируются с помощью различных средств контроля, которые приведены ниже в таблице 1.
Таблица 2 – Оценка совместимости мерительного инструмента
№ | Наименование операции | Контролируемые поверхности | Мерительный инструмент |
1 | 2 | 3 | 4 |
020 | Фрезерная | 1. Шт.циркуль ЩЦ2-160-0,05 ГОСТ 166 | |
025 | Фрезерная | 1. Микрометр МК50 ГОСТ 6507 |
Продолжение таблицы№2
1 | 2 | 3 | 4 |
030 | Фрезерная | 1. Шт.цируль ШЦ2-160-0,05 ГОСТ 166 | |
040 | Шлифовальная | 1. Микрометр МК 50-1 ГОСТ 6507 | |
045 | Шлифовальная | 1. Микрометр МК 50-1 ГОСТ 6507 |
Продолжение таблицы№2
1 | 2 | 3 | 4 |
050 | Расточная | 1. Шт.циркуль ШЦ1-150-0,02 ГОСТ 166 2.Штырь технологический Ø4 6900-2026 3.Колибр-пробка Ø13Н12 ГОСТ 14810 4.Штырь технологический Ø13 ГОСТ6900-2026 5.Штангенрейсмасс ШР-250-0,05 ГОСТ 164 | |
055 | Расточная | 1. 1) Шт.циркуль ШЦ1-150-0,02 ГОСТ 166 2.Штырь технологический Ø4 6900-2026 3.Штангенрейсмасс ШР-250-0,05 ГОСТ 164 4.Колибр-пробка Ø9,5Н12 ГОСТ14810 5.Штыри технологические Ø9,5 ГОСТ 6900-2026 6.Микрометр МР50 ГОСТ4381 | |
060 | Фрезерная | 1. Штангенциркуль ШЦ2-160-0,05 ГОСТ 166 2.Микрометр МК25 ГОСТ 2507 3.Набор шаблонов радиусных№1 8450-8287 4.Штангенрейсмасс ШР-250-0,05 ГОСТ164 5.Штырь технологический Ø13 6900 | |
1 | 2 | 3 | 4 |
065 | Фрезерная ЧПУ | 1)Штангенциркуль ШЦ2-160-0,05 ГОСТ 166 2)Радиусный шаблон 3)Угломер | |
075 | Фрезерная | 1)Набор шаблонов для замера фасок 8450-6144 |
2.3 Описание и расчет измерительного инструмента
Описание и расчет измерительного инструмента на операцию 050 расточную
Калибры – бесшкальные измерительные инструменты, предназначенные для контроля размеров, формы и взаимного расположения поверхностей.
Для контроля размеров гладких цилиндрических изделий применяются предельные калибры, имеющие два размера: проходной (ПР) и непроходной (НЕ), ограничивающие наибольший и наименьший предельные размеры изделий.
При контроле калибрами не определяется истинная величина размера. Контроль устанавливает, находится ли действительный размер изделия в пределах допуска или вне их. Если проходной калибр (при контроле изделий средних размеров) проходит под действием собственного веса, а непроходной не проходит, то изделие считается годным.
Калибры для гладких цилиндрических изделий подразделяются на калибры для проверки отверстий–пробки и калибры, для проверки валов–скобы (или кольца).
Благодаря простоте и удобству измерения, незначительному времени на контроль, калибры нашли широкое применение в серийном и массовом производстве, в машиностроении и приборостроении.
По назначению гладкие калибры подразделяются на рабочие и контрольные (контркалибры), которые обозначаются:
ПР – рабочий проходной калибр;
НЕ – рабочий непроходной калибр;
К-ПР – контркалибр для проверки новых рабочих проходных скоб;
К-НЕ – контркалибр для проверки новых рабочих непроходных скоб;
К-И – контркалибр для контроля износа рабочих проходных скоб.
Контркалибры к калибрам для отверстий не предусматриваются, так как пробки (наружный размер) легко проверить универсальными измерительными средствами.
Контркалибры для проверки скоб представляют собой, пробки или мерные шайбы. Они применяются для проверки скоб в процессе их эксплуатации. Контрольные калибры К-ПР и К-НЕ должны проходить в новые контролируемые скобы. При этом устанавливается, что размер скобы не уменьшается в результате повреждения во время эксплуатации или естественного старения.
Контрольный калибр К-И не должен проходить в контролируемую скобу. Если он проходит, то это означает, что проходная скоба должна быть изъята из эксплуатации вследствие износа.
Для контроля внутренней цилиндрической поверхности 13Н12, необходимо произвести расчеты исполнительных размеров калибра-пробки.
Определяем исполнительные размеры калибра–пробки для отверстия Ø13Н12, обрабатываемого на операции 050 расточная.
1. Находим основное (нижнее) отклонение по таблице «Значения основных отклонений отверстий» (таблица 8 СТ СЭВ 145 – 75 [3]) –EI = 0.
2. По таблице «Значения допусков» (таблица 6 СТ СЭВ 145 – 75 [3]) находим, что допуск 12 квалитета для интервалов размеров свыше 1 до 3 мм, равен 25 мкм. Тогда второе верхнее отклонение для 5Н13 будет равняться:
ES = EI + IT7 = 0 + 25 мкм
где ES – верхнее отклонение отверстия;
EI – нижнее отклонение отверстия;
IT – допуск размера.
3. Находим предельные размеры изделия, которые соответственно являются номинальными размерами калибра:
Dmin = 5 + 0 = 5 мм;
Dmax = 5 + 0,25 = 5,25 мм;
где Dmin – наименьший предельный размер изделия;
Dmax – наибольший предельный размер изделия.
4. По табличным значениям (таблица 2 СТ СЭВ 157 – 75 [4]) находим:
Z= 6 мкм
H= 2,5 мкм
Y= 0 мкм
где Z – отклонение середины поля допуска на изготовление проходного калибра для отверстия относительно наименьшего предельного размера изделия;
H – допуск на изготовление калибров (за исключением калибров со сферическими измерительными поверхностями) для отверстия;
Y – допустимый выход размера изношенного проходного калибра для отверстия за границу поля допуска изделия.
5. Наибольший размер проходной стороны новой пробки определяем по формуле:
Прmax = Dmin + Z + H / 2, (мм) (1)
где ПРmax – наибольший размер проходной стороны новой пробки;
Dmin – наименьший предельный размер изделия;
Z – отклонение середины поля допуска на изготовление проходного калибра для отверстия относительно наименьшего предельного размера изделия;
H – допуск на изготовление калибров (за исключением калибров со сферическими измерительными поверхностями) для отверстия;
Определяем наибольший размер проходной стороны новой пробки по формуле (1):
ПРmax =13 + 0,006 + 0,0025 / 2 = 13,0072 (мм)
Исполнительный размер проходной стороны:
ПР = 13,0072-0,0025.
(За исполнительный размер пробки принимается наибольший предельный размер пробки, и допуск располагается «в тело»).
6. Наименьший размер изношенной проходной стороны определяем по формуле:
Призн = Dmin – Y, (мм), (2)
где Dmin – наименьший предельный размер изделия;
Y – допустимый выход размера изношенного проходного калибра для отверстия за границу поля допуска изделия.
Определяем наименьший размер изношенной проходной стороны по формуле (2):
ПРизн = 13 – 0 = 13 (мм).
(При достижении, в результате износа этого размера, пробка ПР должна быть изъята из эксплуатации).
7. Наибольший размер непроходной стороны пробки определяется по формуле:
НЕmax = Dmax + H / 2 , (мм), (3)
где НЕmax – наибольший размер непроходной стороны пробки;
Dmax – наибольший предельный размер изделия;
H – допуск на изготовление калибров (за исключением калибров со сферическими измерительными поверхностями) для отверстия.
Определяем наибольший размер непроходной стороны пробки по формуле (3):
НЕmax = 13,025 + 0,0025 / 2 = 13,025125 (мм)
Исполнительный размер непроходной стороны:
НЕ = 13,025125-0,0025
На основании данных расчета строим схему расположения полей допусков для отверстия Ø13Н12, которая представлена на рисунке 6.
Рисунок 6 – Схема расположения полей допусков отверстия Ø13Н12
Заключение
Технический контроль является важным этапом при изготовлении деталей. На стадии разработки продукции технический контроль заключается в проверке соответствия опытного образца техническому заданию, технической документации, правилам оформления, изложенным в ЕСКД (Единая система конструкторской документации). На стадии изготовления он охватывает качество, комплектность, упаковку, маркировку, количество предъявляемой продукции, ход производственных процессов; на стадии эксплуатации состоит в проверке соблюдения требований эксплуатационной и ремонтной документации.
При разработке курсового проекта были достигнуты следующие цели:
¾ выбор средств измерений при изготовлении детали;
¾ развитие и закрепление навыков ведения самостоятельной работы;
¾ анализ причин возникновения брака при реализации технологического процесса изготовления детали;
¾ оценка соответствия режущего инструмента операциям механической обработки технологического процесса изготовления детали;
¾ описание и расчет измерительного инструмента;
¾ обучение студента краткому изложению сущности проделанной работы, аргументированному объяснению принятого решения при ответах на вопросы.
В ходе проектирования данного курсового проекта были разработаны контрольные операции для технологического процесса изготовления детали «Шток». Дана характеристика организации технического контроля в машиностроительном производстве; видов технического контроля. Проанализированы причины возникновения брака при реализации технологического процесса изготовления детали. Дана оценка соответствия режущего инструмента операциям механической обработки технологического процесса изготовления детали «Кронштейн». Составлен технологический маршрут процесса контроля. Произведен расчет специального измерительного инструмента.
|
|
Типы оградительных сооружений в морском порту: По расположению оградительных сооружений в плане различают волноломы, обе оконечности...
Адаптации растений и животных к жизни в горах: Большое значение для жизни организмов в горах имеют степень расчленения, крутизна и экспозиционные различия склонов...
Типы сооружений для обработки осадков: Септиками называются сооружения, в которых одновременно происходят осветление сточной жидкости...
Механическое удерживание земляных масс: Механическое удерживание земляных масс на склоне обеспечивают контрфорсными сооружениями различных конструкций...
© cyberpedia.su 2017-2024 - Не является автором материалов. Исключительное право сохранено за автором текста.
Если вы не хотите, чтобы данный материал был у нас на сайте, перейдите по ссылке: Нарушение авторских прав. Мы поможем в написании вашей работы!