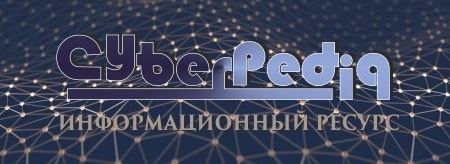
Своеобразие русской архитектуры: Основной материал – дерево – быстрота постройки, но недолговечность и необходимость деления...
Наброски и зарисовки растений, плодов, цветов: Освоить конструктивное построение структуры дерева через зарисовки отдельных деревьев, группы деревьев...
Топ:
Характеристика АТП и сварочно-жестяницкого участка: Транспорт в настоящее время является одной из важнейших отраслей народного хозяйства...
Методика измерений сопротивления растеканию тока анодного заземления: Анодный заземлитель (анод) – проводник, погруженный в электролитическую среду (грунт, раствор электролита) и подключенный к положительному...
Марксистская теория происхождения государства: По мнению Маркса и Энгельса, в основе развития общества, происходящих в нем изменений лежит...
Интересное:
Финансовый рынок и его значение в управлении денежными потоками на современном этапе: любому предприятию для расширения производства и увеличения прибыли нужны...
Принципы управления денежными потоками: одним из методов контроля за состоянием денежной наличности является...
Берегоукрепление оползневых склонов: На прибрежных склонах основной причиной развития оползневых процессов является подмыв водами рек естественных склонов...
Дисциплины:
![]() |
![]() |
5.00
из
|
Заказать работу |
|
|
Введение
В дипломном проекте предполагается совершенствование технологии сборки и сварки цистерны из коррозионностойкой стали изготавливаемой на ООО «Озерский завод нестандартного оборудования». Цистерна из коррозионностойкой стали применяется в химической промышленности для транспортировки и хранения химически активных веществ, в том числе и кислот.
Существующая технология сборки и сварки цистерны была основана на применении ручного труда сборщиков и использовании механизированной сварки с более низким уровнем механизации, нежели автоматическая сварка. Такая технология является устаревшей и малоэффективной при современном уровне развития сварочного производства.
В данной работе разработано специализированное оборудование для сборки цистерны, позволяющее механизировать процесс сборки, что позволило существенно снизить долю ручного труда. Разработана также установка для автоматической сварки цистерны на основе поворотной колонны, роликового стенда и подвесных сварочных автоматов для сварки под флюсом.
Таким образом достигается улучшения условий труда сборщиков, увеличение производительности труда при сборке. Разработанная технология автоматической сварки позволила избежать необходимости привлечения для выполнения работ высококвалифицированных сварщиков для выполнения полуавтоматической сварки, повысить производительность труда, снизить потери на угар и разбрызгивание при сварке, улучшить внешний вид и качество сварных швов.
Технологический раздел
Анализ сварного узла
Конструкция цистерны
Цистерна состоит из обечайки, и двух штампованных днищ, изготавливаемых из листовой стали 12Х18Н9Т толщиной 12 мм. Для заливки продукта в цистерну предусмотрена горловина, которая герметизируется крышкой, закрепляемой к горловине при помощи фланца. Для слива продукта из цистерны предусмотрен патрубок. Конструкция изделия показана на рисунке 1.
|
Материал изделия, его свойства
Для изготовления цистерны применяется коррозионностойкая листовая сталь 12Х18Н9Т, которая содержит 0,12% углерода, 18% хрома, 9% никеля и 1% титана. Данная сталь имеет аустенитную структуру.
Способность к пассивации обеспечивает хромоникелевым аустенитным сталям достаточно высокую стойкость в азотной кислоте. Аустенитные хромоникелевые стали имеют также высокую стойкость в растворах органических кислот — уксусной, лимонной и муравьиной, а также в щелочах КОН и NaOH.
Данные стали нашли широкое применение в химической промышленности.
Рисунок 1.1 – Цистерна: 1 днище, 2 обечайка, 3 горловина, 4 фланец, 5 кольцо подкладочное кольцевое, 6 подкладка обечайки.
Выводы
Технология, реализуемая в базовом варианте является низко производительной и устаревшей, основана на применении большой доли ручного труда, условия труда сварщиков требуют улучшения. Требуется применение более производительных способов сварки и применения специализированного сборочного и сварочного оборудования для механизации процесса.
Конструкторский раздел
2.1 Изменения технологии изготовления цистерны при
реализации проектного варианта
2.1.1 Модернизация технологии получения карт из листовой стали
для изготовления обечайки и днищ
Таблица 2.1. Проектный вариант технологии изготовления цистерны
Операция | Оборудование, инструмент | Материалы |
1 | 2 | 3 |
Обезжиривание исходного листового материала | Реагентные ванны | - Едкий натр 5–10; - углекислый натрий 20–40; - тринатрнйфосфат 20–40 |
Разделка кромок на исходном листовом материале | Станок кромкострогальный 7814 (рис. 1.4) | |
Сварка карт из исходного листового материала (рисунок 2.1; 2.2) | MZ-ZK: 1 (рис. 2.4) | - Проволока сварочная Св 04Х19Н9 ГОСТ 18143-72, Æ3 мм Флюс сварочный 48ОФ10 |
Резка заготовок из листа | Портальная установка для плазменной резки Шквал 2П (рисунок 1.6) | - Аргон чистый марки В ГОСТ 10157-62 - Сжатыйвоздух |
Разделка кромок | Станок кромкострогальный 7814 (рис. 1.7) | |
Гибка обечайки | Машина листогибочная Sahinler 4R-HS (рис. 1.8) | |
Штамповка днищ | Пресс гидравлический К04.К3533 (рис. 1.9) | |
Сборка обечайки | - Специализированный сборочный стенд (рисунок 2.2); - выпрямитель сварочный Неон ВД 315 | Электроды покрытые ЦЛ-11, Æ4 мм |
Таблица 2.1 продолжение
|
1 | 2 | 3 |
Приварка остающихся подкладок | Выпрямитель сварочный Неон ВД 315 | Электроды покрытые ЦЛ-11, Æ4 мм |
Сборка обечайки и днищ | - Специализированный сборочный стенд (рис. 2.3) - выпрямитель сварочный Неон ВД 315 | Электроды покрытые ЦЛ-11, Æ4 мм |
Сварка обечайки и днищ | Специализированная сварочная установка (рис 2.4) | - Проволока сварочная Св 04Х19Н9 ГОСТ 18143-72, Æ3 мм - флюс сварочный 48ОФ10 |
Сборка и сварка горловины и фланца | - Полуавтомат сварочный ПДГ 315; - стол сварочный | - Проволока сварочная Св 04Х19Н9 ГОСТ 18143-72, Æ2 мм - Аргон чистый марки В ГОСТ 10157-62 - Кислород сорт 1 ГОСТ 5583-78 |
Сборка и сварка корпуса цистерны с горловиной | - Полуавтомат сварочный ПДГ 315; - балкон для установки и перемещения сварщика | - Проволока сварочная Св 04Х19Н9 ГОСТ 18143-72, Æ2 мм - Аргон чистый марки В ГОСТ 10157-62 - Кислород сорт 1 ГОСТ 5583-78 |
Приварка сливного патрубка | Выпрямитель сварочный Неон ВД 315 | Электроды покрытые ЦЛ-11, Æ4 мм |
Вакуумный контроль швов корпуса цистерны | Камера вакуумная | Мыльный раствор |
Контроль швов горловины и сливного патрубка керосином | Пульверизатор | - Керосин технический ГОСТ 18499-76; - водно-меловой состав |
Для получения карты из стального листа размерами 1500х3000 мм толщиной 12 мм из стали марки 12Х18Н9Т, в проектном варианте предложено применение автоматической сварки под флюсом. Оборудование – сварочный трактор MZ-ZK. Изготовитель: «SHENZHEN RILAND INDUSTRY CO., LTD», Китай.
Сварка под флюсом является одним из основных процессов сварки высоколегированных сталей толщиной 3 – 50 мм при производстве химической и нефтехимической аппаратуры. Основным преимуществом этого способа является стабильность состава и свойств металла по всей длине шва при сварке как с разделкой, так и без разделки кромок. Это обеспечивается возможностью получения шва любой длины без кратеров, равномерностью плавления электродной проволоки и основного металла по длине шва и более надежной защитой зоны сварки от окисления легирующих компонентов кислородом воздуха. Хорошее формирование поверхности швов с мелкой чешуйчатостью и плавным переходом к основному металлу, отсутствие брызг на поверхности изделия заметно повышают коррозионную стойкость сварных соединений. Уменьшается трудоемкость подготовительных работ, так как разделку кромок производят на металле толщиной свыше 12 мм.
|
Размеры карт для изготовления деталей обечайки и днища:
Рисунок 2.2 – карта для сварки обечайки
Рисунок 2.3 – карта для штамповки днища
Рисунок 2.4 – Основные компоненты сварочного трактора MZ-ZK: 1 блок управления, 2 катушка с проволокой, 3 горизонтальная штанга, 4 рукоятка регулировки поперечного положения сварочной головки, 5 вертикальная колонна, 6 винт M8, 7 ролики поддержки сварочной проволоки, 8 колесо ручной регулировки высоты сварочной головки, 9 двигатель подачи сварочной проволоки, 10 опорный суппорт механизма подачи сварочной проволоки, 11 флюсовый бункер, 12 сетка флюсового бункера, 13 винт M8, 14 рукоятка регулировки положения сварочной головки, 15 рукоятка регулировки подачи флюса, 16 рукоятка регулировки высоты вертикальной колонны, 17 ролики правки сварочной проволоки, 18 шиберная задвижка флюсового бункера, 19 каретка, 20 регулятор усилия прижима сварочной проволоки, 21 рукоятка сцепления, 22 штанга сварочной головки, 23 трубка подачи флюса, 24 токопроводящая пластина, 25 головка подачи флюса, 26 механизм подачи сварочной проволоки, 27 индикатор направления, 28 сопло подачи флюса, 29 колесо каретки, 30 рукоятка регулировки положения горизонтальной штанги, 31 каркас для катушки с проволокой, 32 рым – болт.
Таблица 2.2 Технические характеристики сварочного трактора MZ-ZK
Рисунок 2.2 – Стенд для сборки обечайки: 1 – портал, 2 – роликовый стенд, 3 – струбцина, 4 – передвижные каретки, 5 – цепная винтовая стяжка.
Рисунок 2.3 – Сборочный стенд для сборки днищ с обечайкой: 1 – вакуумный захват, 2 – консольно-поворотный кран, 3 – рама, 4 – роликовый стенд, 5 - электроталь, 6 – блок пневмоцилиндров.
|
Рисунок 2.4 – Установка сварочная: 1 – колонна поворотная ПК 4, 2 – сварочный автомат А 184, 3 – роликовый стенд, 4 – рама.
2.1.2 Расчет режимов сварки [4], конструкция сварных швов:
2.1.2.1 Расчет режимов и параметров стыковых швов обечайки и днищ
Сварка автоматическая под флюсом
Таблица 2.3 Параметры швов емкости цистерны (обечайки и днищ)
Условное обозначение по ГОСТ 8713-79 | Конструктивные элементы | Способ сварки | S=S1 | b | δ не менее | е | g | |
подготовленных кромок | шва сварного соединения | |||||||
С 19 | ![]() | ![]() | Автоматическая под флюсом | 12 | 1,5±1,0 | 4 | 23±3 | 1,5±1 |
Сварочный ток, А:
(2.1)
где dэ – диаметр электрода
iсв – плотность тока в сварочной проволоке
При сварке под флюсом высоколегированных коррозионностойких сталей, рекомендуется использовать значения плотности тока в электродной проволоке iсв =30 - 50 А/мм2
Зависимость напряжения дуги от силы сварочного тока (флюс 48-ОФ-10) принимаем согласно [1]:
Напряжение на дуге 35 В
Скорость подачи проволоки, м/час:
(2.2)
где dпр – диаметр проволоки, мм;
ρ – плотность металла электродной проволоки, г/см3(для стали ρ =7,8 г/см3).
Коэффициент расплавления проволоки сплошного сечения при сварке под флюсом для постоянного тока обратной полярности:
αР= 10 - 12 г/А·ч
Требуемое число проходов:
![]() | (2.3) |
где F1 = (6 – 8) dэ = 7∙3 = 21 мм2 – площадь наплавленного металла корневого прохода [5]
FП.П = (8 – 12) dэ = 10∙3 = 30 мм2 – площадь наплавленного металла последующих проходов
Fоб = F1 + FП.П =21 + 30 = 51 мм2 – общая площадь наплавленного металла
Скорость сварки, м/час:
(2.4)
где αн - коэффициент наплавки, г/А∙час
Fв - площадь поперечного сечения валика, см2, определяем средствами программы «Компас»
Принимаем:
Для корневого прохода
Fв = 0,43 см2
Для второго прохода
Fв = 0,71 см2
Площадь наплавленного металла (определяем средствами программы «Компас»:
Fн = 0,74 см2
Длина сварного шва:
(2.5)
Объем наплавленного металла:
Vн = Fн lш = 0,74∙1 525,22 = 1 143,22 см3 (2.6)
Масса наплавленного металла:
Gн = Vнρ = 1 143,22∙7,8 = 8 917 г (2.7)
Расход сварочной проволоки:
Gпр = Gн(1+ψ) = 8 917∙(1+0,25) = 11 143 г (2.8)
|
где ψ = 0,20 – 0,30 – коэффициент потерь на угар и разбрызгивание [4]
Расход флюса:
(2.9)
Время горения дуги:
(2.10)
Полное время сварки:
(2.11)
где kп = 0,6 – 0,7 - коэффициент использования сварочного поста
Расход электроэнергии, кВт∙час:
(2.12)
где η = 0,6 – 0,7 - КПД источника питания при постоянном токе
Wо = 2,0 – 3,0 кВт - мощность источника питания, работающего на холостом ходу при постоянном токе
2.1.2.2 Расчет режимов и параметров швов горловины и фланца
Сварка полуавтоматическая в смеси газов аргона + 5% кислорода
Таблица 2.4 Сварные швы горловины и фланца
Условное обозначение по ГОСТ 14771-76 | Конструктивные элементы | Способ сварки | S | b | с | е | α, град ±2° | |
подготовленных кромок | шва сварного соединения | |||||||
Т 6 | ![]() | ![]() | Полуавтоматическая в смеси газов Ar+5% O2 | 12 | 0±2 | 2+1-2 | 16±3 | 45 |
Диаметр электродной проволоки [19]: dэ = 2 мм, число проходов n = 2.
Сила сварочного тока [19]:
Напряжение на дуге [19]: Uд = 32 В
Скорость сварки:
Расход защитного газа Qг = 18 – 20 л/мин
Расход сварочной проволоки
Gпр = Gн(1+ψ) = 3 834∙(1+0,25) = 479 г
Время горения дуги
Полное время сварки
Расход электроэнергии, кВт∙час
2.1.2.3 Расчет режимов и параметров швов сливного пат рубка
Сварка ручная дуговая
Таблица 2.5 Сварной шов патрубка
Условное обозначение по ГОСТ 14534-75 | Конструктивные элементы | Способ сварки | S | e | α | b | g | |
подготовленных кромок | шва сварного соединения | |||||||
Т 3 | ![]() | ![]() | Ручная дуговая | 12 | 14+6 | 45° | 2+1-2 | 4±3 |
Диаметр электрода при сварке коррозионностойкой аустенитной стали в полупотолочном положении принимаем dэ = 3 мм
Сила сварочного тока Iсв = 30 – 40 dэ = 35∙3 = 105 А
Напряжение холостого хода источника питания при сварке на постоянном токе обратной полярности: UХХ = 90 В
Напряжение на дуге: Uд = 24 В
Расход электродов
GЭ = GнКЭ= 42,5∙1,8 = 76,5 г
где КЭ – коэффициент расхода электродов [7]
Время горения дуги
Полное время сварки
Расход электроэнергии, кВт∙час
2.1.2.4 Расчет режимов и параметров швов остающихся подкладок
Сварка ручная дуговая
Таблица 2.6 Сварные швы подкладок
Условное обозначение по ГОСТ 5264-80 | Конструктивные элементы | Способ сварки | S | В | в | |
подготовленных кромок | шва сварного соединения | |||||
Т 3 | ![]() | ![]() | Ручная дуговая | 4 | 20 | 0±2 |
Диаметр электрода при сварке коррозионностойкой аустенитной стали в горизонтальном положении и кольцевых швов в вертикальном положении стыка принимаем dэ = 3 мм
Сила сварочного тока Iсв = 30 – 40 dэ = 35*3 = 105 А
Напряжение холостого хода источника питания при сварке на постоянном токе обратной полярности: UХХ = 90 В
Напряжение на дуге: Uд = 24 В
Расход электродов
GЭ = GнКЭ= 1 052∙1,8 = 1 894 г
где КЭ – коэффициент расхода электродов [7]
Время горения дуги
Полное время сварки
Расход электроэнергии, кВт∙час
Выводы
Предложенная технология сборки и сварки позволила существенно повысить производительность труда, улучшить условия труда сварщиков и сборщиков, улучшить качество сварных соединений.
Маркетинговые исследования
Маркетинговый анализ
Ремонтный механический завод распложен на территории промышленной площадки «ФГУП ПО «Маяк». Завод выполняет как ремонтные работы, так и работы по изготовлению сварных конструкций для нужд «Маяка».
Рассматриваемая в проекте цистерна используется для краткосрочного хранения и транспортировки радиоактивных изотопов.
В настоящее время завод оснащён несовременным оборудованием. При этом вся выпускаемая продукция соответствует отраслевым требованиям и требованиям заказчиков, в том числе и иностранных.
Изготовляемые цистерны имеют высокую степень защиты и надёжности от механических повреждений и от утечки хранимого в них продукта. Высокое качество своей продукции завод ежегодно подтверждает сертификатом системы менеджмента на соответствие стандарта РД 95.10541-98, который распространяется на все этапы производства. Продукция завода подлежит 100% стилоскопированию, а также 100% визуальному контролю и контролю на герметичность.
Маркетинговые исследования
На сегодняшний день при изготовлении цистерн производительность отличается большой трудоемкостью, малой точностью изготовления и большим количеством работ.
В дипломном проекте разрабатывается технология сборки-сварки для производства цистерн, а также применение автоматического способа сварки под флюсом. Применение роликового стенда и поворотной колонны для установки сварочного автомата, специализированного оборудования для сборки. Что позволит значительно повысить уровень производства.
Сбыт и конкуренция
Основным потребителем и заказчиком продукции является ПО «Маяк». От потребности «Маяка», зависит и объём выпускаемой продукции. Средняя потребность цистерн рассматриваемого типа составляет 1000 шт. год. Конкуренции по выпускаемой продукции у РМЗ нет.
Техническое нормирование
Расчет норм резки
1. Подготовка к резке, разметка листа - 10 мин на каждую заготовку.
2. Резка в размер - 5 мин.
Контроль качества
Расчет штучного времени на контроле качества производится по следующей формуле:
,
где to – непосредственно время испытания;
tвсп – время на подготовку оборудования и детали;
k – время на обслуживание рабочего места, отдых и личные надобности (k=1.19).
, (4.6)
где, LШ –длина сварных швов,
VК – скорость контроля.
,
Организация производства
Расчет потребности оборудования и его загрузки
Потребность в сварочном оборудовании на проектируемом участке определяется расчетом и зависит от трудоемкости изготовляемой продукции и действительного фонда времени работы оборудования.
Ср = (4.7)
Принимаем заданное число установок – 1 шт на одну линию производства.
Таким образом, вместо единиц оборудования рассчитывается количество линий.
где Тшт - штучное время на данной операции для одного изделия, мин;
N - годовая программа выпуска изделия (N = 1000 шт)
Fд - действительный фонд времени оборудования (Fд = 1916 час.)
Кв = 1.1 - коэффициент выполнения норм выработки;
n = 1 - количество смен.
Полученное значение Ср округляем до ближайшего целого числа Спр, которое является принятым количеством оборудования.
Коэффициент загрузки оборудования:
Кз = С р /С пр,
Где Ср - расчетное количество оборудования;
Спр - принятое количество оборудования.
Расчет количества применяемого оборудования приведен в таблице 4.2
Для увеличения выпуска продукции берем оборудования в два раза больше.
Таблица 4.2 - Количество применяемого оборудования
Наименование операции | Т шт, мин | Топ, мин | Сp | Сnp | Кз |
Резка, правка, разделка | 15 | 15 | 0,12 | 2 | 0,12 |
Полуавтоматическая сварка | 44 | 79,7 | 0,35 | 2 | 0,35 |
Контроль ОТК | 28,9 | 14,3 | 0,23 | 1 | 0,23 |
Расчет капитальных вложений
При расчете капитальных вложений учитывается единовременные затраты во все виды основных производственных фондов.
Капитальными вложения в здания и сооружения Кз определяется по удельным нормам:
Кз= V∙ C, (4.14)
где V - объём здания или сооружения;
С - стоимость кубического метра здания или сооружения.
Капитальные вложения в рабочие машины и оборудование Крм рассчитываются по их потребному количеству и оптовой цене с учетом затрат на транспортировку и монтаж:
Крм= , (4.15)
где n -принятое количество оборудования;
См - оптовая цена оборудования;
Рт - процент затрат на транспортировку оборудования (Рт=3..5%);
Рм - процент затрат на монтаж оборудования (Рм=2..7%).
Исходные данные и результаты расчетов занесены в таблице 4.7:
Таблица 4.7 – Расчет основных средств и амортизации
№ | Наименование основных средств | Количество | Цена, тыс. руб. | Амортизация | |
Норма,% | Сумма, тыс.руб. | ||||
1 | Здания и сооружения | 1 | 3920 | 3 | 477,6 |
2 | Основное оборудование | 10 | 3610 | 12 | 541,2 |
3 | Приспособления и инструмент | __ | 10 | 16 | 1,6 |
4 | Производственный и хозяйственный инвентарь | __ | 10 | 16 | 1,6 |
Итого по участку: | 7550 | 1022 |
Таблица 4.8 – Калькуляция себестоимости изделия
Наименование статей затрат | Сумма затрат | Удельный вес затрат | |
Изделие, руб | Годовой выпуск, тыс.руб | ||
1.Основные материалы | 1311,9 | 1311,9 | |
2.Вспомогательные (сварочные) материалы | 30.08 | 30,08 | |
3.Энергия, топливо для технических целей | 2,84 | 2,84 | |
4.Транспортно-заготовительные затраты (10% от стоимости основных затрат) | 131,19 | 131,19 | |
4.Основная зарплата производ. рабочих | 123,98 | 123,98 | |
5.Дополнительная зарплата произв. рабочих (за неотработанное время 10% от основной) | 12,4 | 12,4 | |
6. Отчисления на социальное страхование (39% от суммы основной и допол. з/п) | 53,2 | 53,2 | |
7.Расходы по содерж. и экспл. Оборудования (210% от основной з/п) | 260,4 | 260,4 | |
8.Амортизация оборудования | 1022 | 1022 | |
9.Общецеховые расходы (90% от основ. з/п) | 111,6 | 111,6 | |
10.Итоговая цеховая себестоимость | 3059,6 | 3059,6 | 100 |
Вывод
ЧДД=144,07>0, следовательно, реализация проекта эффективна;
ИД=1,02>1, следовательно проект считается эффективным и это соответствует значению ЧДД>0;
Евн=0,265 –внутренняя норма доходности показывает норму срок окупаемости 4,8 года – минимальный интервал времени, за пределами которого интегральный эффект становится неотрицательным.
Из полученных результатов видно, что проект является рентабельным и экономический эффект достигнут.
Список использованной литературы
1. Сварка в машиностроении: Справочник. В 4-х т /Ред-С24 кол.: Г. А. Николаев (пред.) и др. — М.: Машиностроение, /Под ред. А. И. Акулова. 2010. 462с, ил
2. Сорокин, В.Г. Стали и сплавы. Марочник: справочное издание / В.Г. Сорокин. – М.: «Интермет Инжиниринг», 2012. – 608 с.
3. Учебное пособие для выполнения курсового проекта по дисциплине «Производство сварных конструкций» / М.В. Шахматов. – Челябинск: ЮУрГУ, 2006. – 22 с.
4. Производство сварных конструкций: методическое пособие по курсовому проектированию / М.В. Шахматов, Д.М. Шахматов. – Челябинск: ЮУрГУ, 2010. – 118 с.
5. Выбор параметров режима и расчет размеров сварных швов: методическое пособие / Н.Л. Зайцев. - Челябинск: ЮУрГУ, 2014. – 42 с.
6. Акулов, А.И. Технология и оборудование сварки плавлением: учебник / А.И. Акулов, Г.А. Бельчук. – М.: Машиностроение, 2012. – 432 с.
7. Сварка в машиностроении: справочник / под. ред. А.И. Акулова. – М.: Машиностроение, 1972 – 462 с.
8. Сварка в машиностроении: справочник: в 4 т. / под. ред. В.А. Винокурова. – М.: Машиностроение, 1979. – Т.3. – 468 с.
9. Сварка и свариваемые материалы: справочник: в 3 т. / под. ред. В.Н. Волченко. – М.: Изд-во МГТУ, 1998. – Т.2. – 574 с.
10. Гитлевич, А.Д. Альбом механического оборудования сварочного производства / А.Д. Гитлевич, Л.А. Животинский, А.И. Клейнер. – М.: Высшая школа, 1974. – 159с.
11. Гитлевич, А.Д. Механизация и автоматизация сварочного производства: учебник / А.Д. Гитлевич, Л.А. Этингоф. – М.: Машистроение, 1979. – 280 с.
12. Голиков, В.Н. Производственный менеджмент: учебное пособие / В.Н. Голиков. – Челябинск: Изд-во ЮУрГУ, 2003. – 32 с.
13. Кульневич, Т.В. Техническое нормирование сварочных процессов: учебное пособие для выполнения курсовых и дипломных проектов / Т.В. Кульневич, А.А. Колпаков, В.Н. Голиков. – Челябинск: ЧПИ, 1984. – 33 с.
14. Красовский, А.И. Основы проектирования сварочных цехов: учебник / А.И. Красовский. – М.: Машиностроение, 1980. – 387 с.
15. Экономический раздел в дипломном проекте: учебное пособие / В.Н. Голиков. – Челябинск: Изд-во ЮУрГУ, 2006. – 50 с.
16. http://msd.com.ua/svarka-i-rezka-metallov/avtomaticheskaya-svarka-pod-flyusom-legirovannyx-stalej/
17. http://steel-guide.ru/klassifikaciya/nerzhaveyushhie-stali/austenitnye-nerzhaveyushhie-stali-struktura-i-svojstva.html
18. http://www.bestreferat.ru/referat-402889.html
Введение
В дипломном проекте предполагается совершенствование технологии сборки и сварки цистерны из коррозионностойкой стали изготавливаемой на ООО «Озерский завод нестандартного оборудования». Цистерна из коррозионностойкой стали применяется в химической промышленности для транспортировки и хранения химически активных веществ, в том числе и кислот.
Существующая технология сборки и сварки цистерны была основана на применении ручного труда сборщиков и использовании механизированной сварки с более низким уровнем механизации, нежели автоматическая сварка. Такая технология является устаревшей и малоэффективной при современном уровне развития сварочного производства.
В данной работе разработано специализированное оборудование для сборки цистерны, позволяющее механизировать процесс сборки, что позволило существенно снизить долю ручного труда. Разработана также установка для автоматической сварки цистерны на основе поворотной колонны, роликового стенда и подвесных сварочных автоматов для сварки под флюсом.
Таким образом достигается улучшения условий труда сборщиков, увеличение производительности труда при сборке. Разработанная технология автоматической сварки позволила избежать необходимости привлечения для выполнения работ высококвалифицированных сварщиков для выполнения полуавтоматической сварки, повысить производительность труда, снизить потери на угар и разбрызгивание при сварке, улучшить внешний вид и качество сварных швов.
Технологический раздел
Анализ сварного узла
Конструкция цистерны
Цистерна состоит из обечайки, и двух штампованных днищ, изготавливаемых из листовой стали 12Х18Н9Т толщиной 12 мм. Для заливки продукта в цистерну предусмотрена горловина, которая герметизируется крышкой, закрепляемой к горловине при помощи фланца. Для слива продукта из цистерны предусмотрен патрубок. Конструкция изделия показана на рисунке 1.
Материал изделия, его свойства
Для изготовления цистерны применяется коррозионностойкая листовая сталь 12Х18Н9Т, которая содержит 0,12% углерода, 18% хрома, 9% никеля и 1% титана. Данная сталь имеет аустенитную структуру.
Способность к пассивации обеспечивает хромоникелевым аустенитным сталям достаточно высокую стойкость в азотной кислоте. Аустенитные хромоникелевые стали имеют также высокую стойкость в растворах органических кислот — уксусной, лимонной и муравьиной, а также в щелочах КОН и NaOH.
Данные стали нашли широкое применение в химической промышленности.
Рисунок 1.1 – Цистерна: 1 днище, 2 обечайка, 3 горловина, 4 фланец, 5 кольцо подкладочное кольцевое, 6 подкладка обечайки.
|
|
Опора деревянной одностоечной и способы укрепление угловых опор: Опоры ВЛ - конструкции, предназначенные для поддерживания проводов на необходимой высоте над землей, водой...
Наброски и зарисовки растений, плодов, цветов: Освоить конструктивное построение структуры дерева через зарисовки отдельных деревьев, группы деревьев...
Состав сооружений: решетки и песколовки: Решетки – это первое устройство в схеме очистных сооружений. Они представляют...
Типы оградительных сооружений в морском порту: По расположению оградительных сооружений в плане различают волноломы, обе оконечности...
© cyberpedia.su 2017-2024 - Не является автором материалов. Исключительное право сохранено за автором текста.
Если вы не хотите, чтобы данный материал был у нас на сайте, перейдите по ссылке: Нарушение авторских прав. Мы поможем в написании вашей работы!