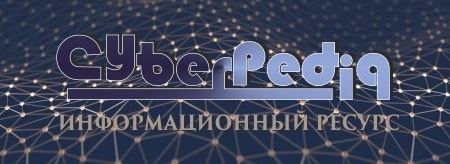
Поперечные профили набережных и береговой полосы: На городских территориях берегоукрепление проектируют с учетом технических и экономических требований, но особое значение придают эстетическим...
Типы оградительных сооружений в морском порту: По расположению оградительных сооружений в плане различают волноломы, обе оконечности...
Топ:
Процедура выполнения команд. Рабочий цикл процессора: Функционирование процессора в основном состоит из повторяющихся рабочих циклов, каждый из которых соответствует...
Методика измерений сопротивления растеканию тока анодного заземления: Анодный заземлитель (анод) – проводник, погруженный в электролитическую среду (грунт, раствор электролита) и подключенный к положительному...
Интересное:
Инженерная защита территорий, зданий и сооружений от опасных геологических процессов: Изучение оползневых явлений, оценка устойчивости склонов и проектирование противооползневых сооружений — актуальнейшие задачи, стоящие перед отечественными...
Аура как энергетическое поле: многослойную ауру человека можно представить себе подобным...
Берегоукрепление оползневых склонов: На прибрежных склонах основной причиной развития оползневых процессов является подмыв водами рек естественных склонов...
Дисциплины:
![]() |
![]() |
5.00
из
|
Заказать работу |
|
|
Введение
Щебеночно-мастичный асфальт (ЩМА) используется в США с 1991 г. (8). Тогда в пяти штатах были реализованы проекты по покрытиям из ЩМА, и с тех пор он находит все более широкое применение. Следует отметить, что до этого ЩМА применялся на протяжении более 20 лет в Европе.
Первоначально ЩМА использовался в Европе для минимизации воздействия шипованных шин. Исследования показали, что эта смесь превосходит все остальные виды горячих асфальтных смесей по устойчивости к воздействию шипованных шин. Несмотря на то, что впоследствии в большинстве европейских стран был введен запрет на использование шипованных шин, ЩМА по-прежнему используется, так как он обладает и иными полезными свойствами. Основными причинами для этого в Европе является сопротивляемости ЩМА колееобразованию и его повышенная долговечность.
По тем же причинам ЩМА используется и в США. Кроме того, было показано, что макротекстура этой смеси способствует более эффективному поверхностному дренажу по сравнению со смесями с непрерывным гранулометрическим составом заполнителя, а также усилению сцепления [между шинами автомобилей и покрытием] в сырую погоду.
На сегодняшний день использование ЩМА является стандартной практикой для нескольких штатов. По мере расширения использования данной смеси стоимость ее тонны в значительной степени снизилась, а именно до уровня, незначительно (как правило, на 20–5%) превышающего таковой для обычных HMA.
Описание
Щебеночно-мастичный асфальт представляет собой смесь измельченных крупных заполнителей, измельченных мелких заполнителей, минерального наполнителя, асфальтоцемента (битумного вяжущего) и стабилизатора. В качестве стабилизаторов обычно используются волокна и/или полимеры, препятствующие стеканию асфальтоцемента.
|
Смеси ЩМА проектируется с высоким содержанием как крупных заполнителей (как правило, 70–80%), так и битума (как правило, свыше 6%) и наполнителя (примерно 10% по весу). Благодаря высокому содержанию крупного заполнителя возникает сцепление между отдельными камнями, что обеспечивает высокую сопротивляемость смеси колееобразованию. На рис. 7–1 показано, как выглядит типичная ЩМА смесь, и для сравнения – типичная смесь с непрерывным гранулометрическим составом заполнителя. Из рисунка видно, что в случае ЩМА смеси высоко содержание каменного материала, а также, что крупный заполнитель в смеси с непрерывным гранулометрическим составом заполнителя как бы плавает в матрице из мелкого заполнителя. Как правило, в смеси ЩМА нагрузку несет крупный заполнитель, тогда как смеси с непрерывным гранулометрическим составом заполнителя эту функцию должен осуществлять мелкий заполнитель. Смеси ЩМА обладают более высоким сопротивлением колееобразованию, так как крупный заполнитель может развивать более высокое сопротивление сдвигу, чем мелкий заполнитель.
Рис. 7-1. Типичная ЩМА смесь и HMA с непрерывным гранулометрическим составом заполнителя в разрезе
Методы проектирования, производства и укладки для ЩМА смесей подобны таковым для смесей с непрерывным гранулометрическим составом заполнителя. Однако между ними существуют и некоторые различия, которые обсуждаются в последующих параграфах.
Материалы
Как указывалось выше, для производства ЩМА смесей используются заполнитель, наполнитель, асфальтоцемент и стабилизатор. Для обеспечения максимального сопротивления колееобразованию в большинстве построенных покрытий из ЩМА применяется дробленый заполнитель. Типичные нормативы (9) содержат следующие требования: 100% крупного заполнителя должно иметь, хотя бы одну грань, образовавшуюся в результате дробления, и не менее 90% – две или более таких граней. Это – высокосортная асфальтовая смесь, в которой следует использовать высококачественные материалы для обеспечения оптимальных эксплуатационных характеристик покрытия.
|
Нормативы для показателя истираемости (определяемого в Лос-Анджелесском барабане) для ЩМА в некоторых штатах установлены на более низком уровне, чем для смесей с непрерывным гранулометрическим составом заполнителя. Вследствие сцепления между отдельными камнями в ЩМА смесях частицы крупного заполнителя испытывают более высокие стрессы от транспортных нагрузок, и многие инженеры полагают, что по этой причине норматив по истираемости необходимо установить на более низком уровне. Как правило, этот показатель для заполнителя в ЩМА устанавливается на уровне 30, однако, из-за дефицита высококачественных заполнителей многие штаты допускают более высокую величину.
В таблице 7–2 (9) приведены типичные требования по гранулометрическому составу для ЩМА смеси. Следует отметить, что эта смесь характеризуется относительно низким процентным содержанием частиц, просеивающихся через сита с размером отверстий 4,75 мм (20–28%), и относительно высоким процентным содержанием частиц, просеивающихся через сита с размером отверстий 0,075 мм (8–10%). Первое необходимо для обеспечения сцепления между отдельными камнями, а также для выполнения минимальных требований в отношении показателя VMA (пористость минерального остова – как правило, на уровне 17%). Высокий процент частиц, просеивающихся через сита с размером частиц 0,075 мм, важен для адекватного схватывания вяжущего, что обеспечивает сопротивление колееобразованию, а также предотвращает стекание асфальтоцемента во время строительства.
Для достижения высокого процентного содержания частиц, просеивающихся через сита с размером отверстий 0,075 мм, в смесь необходимо добавить промышленный наполнитель. В случае смесей с непрерывным гранулометрическим составом заполнителя до 6% материала, просеивающегося через сита с размером отверстий 0,075 мм, как правило, приходится на мелкозернистый заполнитель. В то же время, ЩМА смеси характеризуются более низким процентным содержанием мелкозернистого заполнителя, что снижет процентное содержание материала с размером частиц 0,075 мм, который можно получить из данного источника. Следовательно, обычно в ЩМА смеси добавляется 3–5% промышленного наполнителя.
|
Таблица 7-2. Типичные требования к гранулометрическому составу заполнителя для ЩМА смесей (9)
Размер отверстий сита | Процент просеивающегося материала |
19,0 мм | 100 |
12,5 мм | 85–95 |
9,5 мм | макс. 75 |
4,75 мм | 20–28 |
2,36 мм | 16–24 |
0,60 мм | 12–16 |
0,30 мм | 12–15 |
0,075 мм | 8–10 |
0,020 мм | менее 3 |
В ЩМА, как правило, используется асфальтоцемент того же сорта (или несколько более густой), что и в смесях с непрерывным гранулометрическим составом заполнителя.
Одна из проблем конструкционного характера, которые могут возникнуть в случае ЩМА, заключается в стекании асфальтовяжущего из матрицы заполнителя. Этот недостаток минимизируется при использовании более густого вяжущего; это также повышает сопротивление колееобразованию при более высоких температурах. В то же время при применении более густого вяжущего возможно образование низкотемпературных трещин. Однако ЩМА смеси характеризуются сравнительно высоким оптимальным содержанием битума и повышенной толщиной пленки, что делает их более стойкими к низкотемпературному растрескиванию. Соответственно, можно считать, что отрицательные моменты, связанные с использованием несколько более густого асфальтоцемента, более чем компенсируются положительным эффектом от повышенной толщины пленки. Кроме того, полагают, что в случае ЩМА смесей проблема образования низкотемпературных трещин не будет стоять так остро, как в случае смесей с непрерывным гранулометрическим составом заполнителя.
Для получения ЩМА смесей часто используются полимермодифицированные битумы. Модификация битумов снижает интенсивность стекания асфальтоцемента, что облегчает процесс строительства дорожных покрытий. Модификация асфальтоцементов также может привести к улучшению эксплуатационных характеристик в условиях высоких и низких температур. Модификация может повышать жесткость асфальтовяжущего при высоких температурах и реально снижает этот показатель при более низких температурах. Как говорилось в главе 2, при оценке таких высоко- и низкотемпературных свойств можно использовать тесты для вяжущего материал по системе Superpave (Superior Performance Asphalt Pavements – дорожные покрытия с повышенными эксплуатационными характеристиками).
|
Для предотвращения стекания асфальтоцемента в период строительства следует применять некоторые виды стабилизаторов. В этих целях успешно используются волокнистые материалы и модификаторы битума. В рамках многих проектов по ЩМА используются и полимеры, и волокна. В данном случае функция полимеров заключается в улучшении качества асфальтоцемента при высоких и низких температурах и обеспечении некоторого сопротивления стеканию. Что касается волокон, то их основная функция – предотвратить стекание.
В случае ЩМА смесей обычно используются два вида волокон – целлюлозные и минеральные. Большое значение имеет целый ряд свойств волокнистых материалов, в том числе их длина и толщина, но важнее всего то, что они предотвращают стекание асфальтоцемента. Если волокнистые материалы удобны в обращении как в период, предшествующий строительству, так и во время него, и если они предотвращают стекание, то можно считать, что они справляются с этой задачей. Минеральные волокна, как правило, тяжелее целлюлозных, и потому их вводят в смеси в б’ольших по весу количествах, тем самым обеспечивая их достаточный объем.
Проектирование смеси
Процедура проектирования ЩМА смесей подобна таковой для смесей с непрерывным гранулометрическим составом заполнителя, за исключением некоторых существенных отличий (10). В случае ЩМА смесей используются методы проектирования по Маршаллу и по системе Superpave. Критерии, установленные для обоих методов, включают наличие сцепления между отдельными крупными камнями и обеспечение высокого содержания битума.
Первый этап процесса проектирования смеси заключается в обеспечении сцепления между отдельными камнями в ЩМА смеси. Один из возможных способов его измерения заключается в следующем. В форму помещают только фракцию крупного заполнителя и определяют ее плотность после уплотнения штыкованием. Это и есть плотность крупного заполнителя для случая сцепления между отдельными камнями. Конечно, если плотность той части ЩМА, которая приходится на крупный заполнитель, выше плотности крупного заполнителя, уплотненного штыкованием, то можно ожидать наличия сцепления между отдельными камнями для ЩМА. Оно оценивается путем измерения пустотности крупного заполнителя (VCA – voids in coarse aggregate) в ЩМА смеси по формуле:
VCA = (100 (1 – Gmb (Pca)/Gsb)
где
Gmb = насыпной удельный вес крупного заполнителя.
Pca = процентное содержание (по весу) крупного заполнителя во всей смеси.
|
Gsb = насыпной удельный вес заполнителя в целом.
Ввиду того, что показатель VCA обратно пропорционален плотности, для обеспечения сцепления между отдельными камнями случае ЩМА смеси необходима более низкая величина этого показателя, чем в случае уплотнения только крупного заполнителя,
Если величина VCA для смеси выше, чем для образца, в котором уплотнен только крупный заполнитель, то ее можно снизить, уменьшив количество мелкозернистого заполнителя. При этом показатель VMA для ЩМА смесей, как правило, возрастает, а показатель VCA – уменьшается (рис. 7–2 и 7–3).
При проектировании ЩМА смеси варьируют содержание мелкозернистого заполнителя до тех пор, пока не будет получен тот состав заполнителя, при котором обеспечивается необходимая величина показателя VМA и сцепление между отдельными камнями. Иными словами, процент материала, просеивающегося через сито с размером отверстий 4,75 мм, будут снижать в допустимых пределах (начиная с величины, соответствующей верхней границе нормативного диапазона) до тех пор, пока величина показателя VMA не будет соответствовать минимальным, а величина показателя VCA – максимальным требованиям.
Рис. 7-2. Влияние содержания материала, просеивающегося через сито с размером отверстий 4,75 мм, на показатель V MA.
Рис. 7-3. Влияние содержания материала, просеивающегося через сито с размером отверстий 4,75 мм на показатель V CA.
Как показала работа с ЩМА смесями, для большинства заполнителей сцепление между отдельными камнями возникает тогда, когда ~30% материала просеивается через сито с размером отверстий 4,75 мм. В основном, по этой причине верхняя граница диапазона, соответствующего гранулометрическому составу ЩМА смесей, обычно нормируется на уровне ~30% материала, просеивающегося через сито с размером отверстий 4,75 мм.
Для обеспечения высокого оптимального содержания битума в ЩМА смеси минимальное значение показателя VMA устанавливается на относительно высоком уровне; как правило, он равен 17. Показатель VMA обычно начинает быстро возрастать после того, как содержание материала, просеивающегося через сито с размером отверстий 4,75 мм, падает ниже уровня ~30%. Проблему показателя VMA, как правило, можно решить, снизив содержание материала, просеивающегося через сито с размером отверстий 4,75 мм, на несколько единиц по процентной шкале. Некоторые заполнители склонны к избыточному разрушению, что приводит к низким величинам VMA.
После выбора гранулометрического состава, обеспечивающего сцепление между отдельными камнями, а также выполнение минимальных требований по показателю VМA, содержание битума доводится до уровня, соответствующего желаемому содержанию воздушных пор. Смеси ЩМА проектируются с содержанием воздушных пустот на уровне 3–4% (для большинства смесей эта величина ближе к 4%). При более низком значении этого показателя необходимо строго контролировать процесс производства ЩМА смесей во избежание выпотевания после укладки смеси. Содержание воздушных пустот в образцах, уплотненных в лабораторных условиях, следует контролировать во время строительства; оно не должно выходить за пределы установленного диапазона.
При проектировании ЩМА смесей используются процедуры уплотнения по Маршаллу и по системе Superpave. При использовании процедуры уплотнения по системе Маршалла число ударов для уплотняющего усилия равняется 50. Дополнительное уплотнение не вызывает значительного увеличения плотности, но приводит к избыточному разрушению заполнителя. Некоторые ЩМА смеси проектируют с использованием гирационного уплотнителя Superpave. Нормативов для числа оборотов гиратора для ЩМА смесей не существует, но смеси проектируют из расчета 100 оборотов для Ndesign.
Запроектированные смеси следует протестировать на стекание (11). Для измерения потенциала стекания был разработан простой тест. При его проведении образец ЩМА смеси укладывают в проволочную корзину, которую, в свою очередь, помещают на определенное время в печь, нагретую до определенной температуры (обычно это температура смешения). Асфальтовяжущее, которое стекает через корзину, улавливают и взвешивают. Количество вяжущего, стекающее из рыхлых ЩМА смесей, не должно превышать некоторого установленного уровня, как правило, 0,3% в час. На рис. 7–4 приведена фотография такой корзины. Если происходит избыточное стекание, это означает, что смесь нуждается в модификации, как правило, путем увеличения количества полимерного или волокнистого материала.
Рис. 7-4. Проволочная корзина для теста на стекание.
Строительство
В случае ЩМА смесей установка для получения HMA нуждается в некотором видоизменении (12). В нее загружается большое количество (обычно 3–5%) промышленного наполнителя, тогда как большинство установок не приспособлено для работы с таким большим количеством наполнителя, и это может стать «узким местом» в плане производительности установки. В такой ситуации предпочтительным является вариант с использованием бункера, из которого наполнитель будет точно дозироваться в смесь. Известны случаи, когда наполнитель подавался по одному из питателей для заполнителя, но такой вариант нежелателен.
При использовании полимерного материала его, как правило, смешивают с асфальтоцементом перед доставкой на HMA установку. Однако иногда полимер добавляют и на самой установке. В этом случае полимеры можно одновременно смешивать с асфальтоцементом и заполнителем. Одна из проблем, которые могут возникнуть при предварительном смешении полимера с асфальтоцементом, – разделение при транспортировке и хранении. При смешении на установке основная проблема заключается в отсутствии необходимого оборудования, неадекватном смешении и невозможности протестировать модифицированный битум до его введения в смесь
При использовании волокнистых материалов их введение в смесь должно строго контролироваться, так как даже небольшие количества волокон существенно влияют на свойства смеси. Волокна можно взвешивать и добавлять порциями в установку периодического действия. Обычно их подают в барабан с необходимой скоростью на барабанном смесителе.
Смеси ЩМА, как правило, жестче обычных смесей с непрерывным гранулометрическим составом заполнителя, и для их смешения на установке может потребоваться более высокая температура и более продолжительное время. Повышенная жесткость объясняется, главным образом, высоким содержанием наполнителя и присутствием модифицированного битума и/или волокнистого материала.
Процедуры укладки и уплотнения подобны таковым для смесей с непрерывным гранулометрическим составом заполнителя. Следует отметить, что жесткость смесей ЩМА снижает их удобообрабатываемость. По этой причине, а также из-за высокого содержания крупных частиц заполнителя из этих смесей сложнее получить покрытие с качественными продольными стыками. Однако опыт показывает, что это все же возможно. При неправильном подборе состава смеси или при отсутствии должного контроля может иметь место стекание асфальтоцемента, что приводит к появлению жирных пятен в уплотненных дорожных покрытиях.
Для эффективного уплотнения смеси катки должны следовать непосредственно за укладчиком. При охлаждении смеси ЩМА быстро густеют и, как показывает опыт, тогда их очень трудно уплотнить. Катки на резиновых шинах не используются для ЩМА, главным образом, из-за налипания смеси на шины. В то же время с успехом применяются статические катки на стальных колесах и виброкатки. В некоторых ситуациях использование виброкатков может привести к избыточному разрушению заполнителя. В таком случае следует использовать исключительно катки статического действия. Как правило, ЩМА смеси уплотняют на месте до тех пор, пока содержание воздушных пустот не достигнет уровня 5–6%.
|
|
Индивидуальные и групповые автопоилки: для животных. Схемы и конструкции...
Автоматическое растормаживание колес: Тормозные устройства колес предназначены для уменьшения длины пробега и улучшения маневрирования ВС при...
Поперечные профили набережных и береговой полосы: На городских территориях берегоукрепление проектируют с учетом технических и экономических требований, но особое значение придают эстетическим...
Типы оградительных сооружений в морском порту: По расположению оградительных сооружений в плане различают волноломы, обе оконечности...
© cyberpedia.su 2017-2024 - Не является автором материалов. Исключительное право сохранено за автором текста.
Если вы не хотите, чтобы данный материал был у нас на сайте, перейдите по ссылке: Нарушение авторских прав. Мы поможем в написании вашей работы!