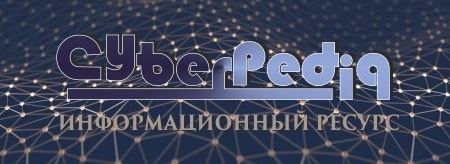
Организация стока поверхностных вод: Наибольшее количество влаги на земном шаре испаряется с поверхности морей и океанов (88‰)...
История развития пистолетов-пулеметов: Предпосылкой для возникновения пистолетов-пулеметов послужила давняя тенденция тяготения винтовок...
Топ:
Оснащения врачебно-сестринской бригады.
Теоретическая значимость работы: Описание теоретической значимости (ценности) результатов исследования должно присутствовать во введении...
Выпускная квалификационная работа: Основная часть ВКР, как правило, состоит из двух-трех глав, каждая из которых, в свою очередь...
Интересное:
Аура как энергетическое поле: многослойную ауру человека можно представить себе подобным...
Лечение прогрессирующих форм рака: Одним из наиболее важных достижений экспериментальной химиотерапии опухолей, начатой в 60-х и реализованной в 70-х годах, является...
Средства для ингаляционного наркоза: Наркоз наступает в результате вдыхания (ингаляции) средств, которое осуществляют или с помощью маски...
Дисциплины:
![]() |
![]() |
5.00
из
|
Заказать работу |
|
|
При сборке механических передач более широко, чем подшипники скольжения, используются подшипники качения: шарико– и роликоподшипники (игольчатые и конические). Основное назначение подшипников в сборочном узле – воспринимать радиальные и осевые нагрузки на вал и перераспределять их на корпус и станину механизма. В зависимости от направления действия этих нагрузок подшипники подразделяются на радиальные, радиально-упорные и упорные. Методы их установки имеют некоторые различия.
Но сначала о том, как правильно подготовить подшипники к установке. Первоначально подшипники нужно расконсервировать, то есть снять с их поверхности заводскую предохранительную смазку, очистить, затем промывать 5–20 минут в горячем масле, или горячем антикоррозионном растворе (температура масла или раствора – 75–80 °C), или бензине (керосине), разумеется
без подогрева. Промывку следует осуществлять таким образом, чтобы избежать контакта подшипников с осевшей на дно промывочной ванны грязью, для чего их следует поместить в корзину из проволоки и в ходе промывки периодически встряхивать. Чистые подшипники тщательно просушить. Теперь следует произвести предварительный контроль качества подшипников: они не должны иметь видимые дефекты, вращение их должно быть плавным, без толчков. В завершение подготовки подшипники подгоняют под посадочные места, а также покрывают посадочные места вала, корпуса и подшипника тонким слоем рабочей смазки (литолом, циатимом, в крайнем случае солидолом).
Шариковые подшипники устанавливают по двум неподвижным посадкам: внутреннее кольцо на вал, а наружное в отверстие корпуса. Крупногабаритные подшипники запрессовывают в подогретом виде гидравлическим прессом – метод практически неосуществимый в условиях домашней мастерской.
|
Мелкие и средние подшипники запрессовывают на неподвижный вал вручную или на прессах в холодном состоянии (рисунок 6).
а – запрессовка подшипника на вал; б – запрессовка подшипника одновременно на вал и в отверстие корпуса; 1 – подшипник; 2 – вал; 3 – молоток
или ручной пресс; 4 – оправка; 5 – оправка с буртиком; 6 – корпус; в – фиксация подшипника пружинными кольцами; г – щипцы для разводки концов пружинных колец.
Рисунок 6 - Установка шарикоподшипников
При этом следует обеспечить соосность вала и подшипника, для чего используется оправка, которая передает усилие запрессовки непосредственно на торец кольца. В том случае, если подшипник одновременно запрессовывают на вал и в отверстие корпуса, применяют оправку с буртиком. Для установки подшипников на длинный вал используют выколотку, которая должна плотно прилегать к торцу внутреннего кольца подшипника, чтобы уберечь его от повреждения.
В целях предотвращения осевого смещения колец подшипника во время работы механизма их фиксируют пружинными кольцами, которые закладывают в канавки вала или корпуса после установки подшипника на посадочные места. Кольца эти имеют разъемную конструкцию, и после установки их на вал концы разводят специальными щипцами.
Контроль качества запрессовки подшипника осуществляется щупом толщиной 0,03 мм: он не должен проходить между торцами колец подшипника и буртом корпуса механизма или вала.
Конические роликоподшипники монтируют из отдельных сборочных единиц: внутреннее кольцо с роликами напрессовывают на вал, наружное кольцо отдельно устанавливают в корпус. Радиальный зазор между наружным кольцом и роликами в таких подшипниках можно регулировать прокладками, которые устанавливаются под крышку перед окончательной затяжкой винтов. Регулировка осуществляется следующим образом (рисунок 8): сначала крышку без прокладок устанавливают на место, затягивают винтами до отказа и щупом измеряют зазор k; вал несколько раз прокручивают для самоустановки роликов подшипника; затем определяют величину С, на которую необходимо увеличить k, для чего определяют отношение С = е/tg в (значения е и k на рисунке). Полученная величина указывает толщину комплекта прокладок, которые устанавливают под крышку.
|
Иначе поступают, если в конструкции крышки предусмотрен винт для регулировки данного зазора: винт завинчивают до отказа, затем отвинчивают на число оборотов n = С/P, где P – шаг резьбы винта, и в таком положении стопорят контргайкой.
Игольчатые роликоподшипники монтируют также по сборочным единицам либо на вал, либо в отверстие охватывающей детали.
При установке подшипника на вал на поверхность шейки вала наносят слой густой смазки, шейку вала устанавливают в посадочное полукольцо, а в образовавшийся зазор последовательно вводят игольчатые ролики (рисунок 7).
а – установка: 1 – внутреннее кольцо; 2 – ролики; 3 – вал; 4 – наружное кольцо; б – регулировка прокладками: 1 – крышка; 2 – прокладки; 3 – вал; в – винтовая регулировка: 1 – крышка; 2 – контргайка; 3 – винт.
Рисунок 7 - Установка и регулировка конического роликоподшипника
а – на шейку вала; б – в отверстие охватывающей детали; в – собранный подшипниковый узел; 1 – вал; 2 – монтажное полукольцо; 3 – игольчатые ролики, 4 – монтажная втулка; 5 – ограничительные кольца; 6 – рабочая ось; 7 – прокладка.
Рисунок 8 - Установка игольчатых подшипников
Затем устанавливают ограничительные кольца и на шейку вала надевают охватывающую деталь, смещая ею монтажное полукольцо.
Для монтажа игольчатых подшипников в отверстии охватывающей детали используют монтажную втулку (рисунок 9): поверхность отверстия покрывают тонким слоем смазки и вставляют втулку, диаметр которой должен быть на 0,1-0,2 мм меньше диаметра шейки вала. Игольчатые ролики также последовательно вводят в зазор, последний ролик должен входить свободно, при этом нужен некоторый зазор. Далее устанавливают ограничительные кольца и рабочей осью выталкивают монтажную втулку.
Зазор между роликами в подшипнике можно регулировать прокладками: их толщина равна разнице между фактическим зазором роликов и зазором по
|
чертежу. Правильность сборки игольчатого подшипника контролируют вращением – оно должно быть плавным, без рывков.
Гарантией нормальной работы подшипникового узла (как шариковых, так и роликовых подшипников) является его защита от загрязнения и вытекания смазочного материала. Для этого подшипники качения закрывают крышками, а на выходах валов при монтаже подшипников устанавливают уплотняющие устройства: фетровые (войлочные) кольца, манжеты, защитные фланцы, защитные шайбы, лабиринтные уплотнители и т. п.
Для долговечности работы подшипникового узла немаловажное значение имеет вид применяемой смазки: она должна не только обеспечивать защиту от пыли, влаги, коррозии; но и снижать шум и предохранять детали от перегрева. Для смазки подшипников используют минеральные (турбинное, автотранспортное, индустриальное и др.) и растительные (хлопковое, касторовое, льняное, репейное) масла.
Монтаж насоса 9МГР
Отремонтированное и окрашенное оборудование подлежит консервации и упаковке. Консервация различными покрытиями предохраняет обработанные поверхности металлических деталей от коррозии, а упаковка защищает окрашенное и законсервированное оборудование от механических повреждений и атмосферного влияния в процессе транспортирования и хранения на складах до начала монтажа.
Сохранность законсервированного изделия зависит от качества удаления с его поверхности химических и механических загрязнений. Метод подготовки определяется маркой металла, из которого изготовлено изделие, классом чистоты обработки поверхности, наличием постоянных покрытий (гальванических, химических, лакокрасочных и т. д.), габаритными размерами изделий, степенью загрязнения.
Влагу, жировые пятна, эмульсию, оставшиеся после механической обработки на поверхности крупногабаритных деталей, удаляют бензином или уайт-спиртом, пользуясь кистями или пульверизаторами. Смоченные моющим материалом поверхности насухо обтирают и просушивают очищенным от влаги и масла сжатым воздухом.
|
Химические загрязнения на поверхностях деталей небольших размеров смывают щелочными растворами в ваннах или моечных машинах.
Коррозию на поверхностях деталей из черных металлов удаляют мелкой шлифовальной шкуркой, пропитанной индустриальным маслом, на поверхностях из цветных металлов - тонким порошком пемзы или шлифовальной шкуркой, смоченной уайт-спиртом или трансформаторным маслом.
С поверхностей высокого класса чистоты коррозию снимают тонкой
(7-10 мкм) пастой ГОИ, растертой с индустриальным маслом в соотношении 1:1. Шероховатость поверхности после зачистки должна иметь класс чистоты, заданный в чертеже. После механического удаления коррозии поверхности промывают бензином или уайт-спиртом, тщательно протирают и высушивают. Химический способ удаления ржавчины с поверхностей заключается в обработке пораженных мест 10 %-ным раствором ортофосфорной кислоты.
Поверхности крупногабаритных деталей консервируют техническим вазелином, смазкой УНЗ, смазками ЦИАТИМ-201, 203 и др. Консистентные смазки наносят на поверхность в расплавленном состоянии, нагретыми до температуры 70—90 °С в ваннах с электро- и пароподогревом.
Детали небольших размеров, все поверхности которых должны быть законсервированы, погружают в нагретую смазку. Смазки ЦИАТИМ используют в холодном состоянии. Ингибированные смазки марок НГ-203А, Б, В; К-17 наносят кистью, ветошью или пульверизатором, нагревая смазку до температуры 50-80 °С.
Для консервации деталей из алюминия, меди и их сплавов используют расплавленный технический вазелин или смазку ПВК. Зубчатые передачи после испытания и удаления рабочей смазки консервируют ингибиторными смазками, обладающими антикоррозионными свойствами и антифрикционными качествами. Для удаления ингибиторной смазки в механизм заливают рабочее масло, вхолостую прокручивают в течение 20-30 мин, сливают смесь, вновь заливают рабочее масло, после чего механизм готов к эксплуатации.
Внутренние поверхности стальных крупногабаритных емкостей консервируют 30 %-ным раствором нитрита натрия. В большинстве случаев консервацию совмещают с процессом гидравлического испытания емкости на герметичность, при котором раствор в емкость подается насосами из специальных баков. После испытания раствор сливают. Пленка нитрита натрия, оставшаяся на стенках сосуда, является надежным консервационным слоем для защиты изделия от ржавчины. После консервации емкость герметически закупоривают.
Консервацию оборудования производят на специальных участках, оснащенных вентиляцией и отопительной системой, с относительной влажностью воздуха не выше 70 % и температурой не ниже 12 °С.
Законсервированное оборудование подлежит внутренней (барьерной) и внешней (транспортировочной) упаковке.
|
Внутренняя упаковка с помощью парафинированной, ингибированной и биостойкой бумаги, пергамента, льняной ткани или полимерных пленок заменяет консервацию и лакокрасочные покрытия. Получает распространение новый вид внутренней упаковки в чехлы из полимерных пленок для изделий, которые невозможно защитить консервационными смазками, и для запасных частей, требующих длительного срока хранения (пневмо- и гидроцилиндры, подшипники и т. д.).
Внешняя транспортировочная упаковка, изготовляемая в виде деревянных
ящиков и обрешеток, должна иметь аккуратный внешний вид, оптимальный объем, достаточную прочность и обеспечивать надежную изоляцию от проникновения воды.
Изделия крепят к таре болтами, шпильками, металлическими хомутами, деревянными брусками или досками. В местах соприкосновения изделия с деревом применяют различные прокладки.
При транспортировании насоса на большие расстояния незакрытые крышками люки и отверстия должны быть защищены временными пробками и щитками, исключающими попадание атмосферных осадков внутрь насоса. Выступающие клапаны трансмиссионного вала должны быть защищены от механических повреждений.
Выходные отверстия насоса закрываются деревянными пробками, а отверстие приемной коробки - деревянными щитками.
Поршни И резиновые детали, не входящие в сборки, упаковываются отдельно от металлических деталей, без смазывания их маслом, в ящики по ГОСТ 15623-84.
Насос транспортируется в собранном виде. На небольшие расстояния насос может перевозится на тяжеловозных тележках. В случае транспортирования насоса волоком рекомендуется насос устанавливать на специальные сани.
Насос следует хранить в местах, защищенных от прямого попадания осадков, солнечных лучей. Запасные части и сменные детали, следует хранить в складских помещениях или будках, специально предназначенных для этого.
Поршня необходимо хранить в вертикальном положении во избежание остаточных деформаций уплотняющих кромок. При хранении поршней, надетых на шток, рекомендуется изготовить специальный стеллаж для установки штоков в вертикальном положении.
Резиновые детали должны храниться отдельно от металлических деталей вдали от отопительных приборов и не должны подвергаться действию масел, бензина и других агрессивных сред.
Рекомендуется хранить запасные уплотнения в отдельных ящиках или картонных коробках.
|
|
Кормораздатчик мобильный электрифицированный: схема и процесс работы устройства...
Наброски и зарисовки растений, плодов, цветов: Освоить конструктивное построение структуры дерева через зарисовки отдельных деревьев, группы деревьев...
Опора деревянной одностоечной и способы укрепление угловых опор: Опоры ВЛ - конструкции, предназначенные для поддерживания проводов на необходимой высоте над землей, водой...
Папиллярные узоры пальцев рук - маркер спортивных способностей: дерматоглифические признаки формируются на 3-5 месяце беременности, не изменяются в течение жизни...
© cyberpedia.su 2017-2024 - Не является автором материалов. Исключительное право сохранено за автором текста.
Если вы не хотите, чтобы данный материал был у нас на сайте, перейдите по ссылке: Нарушение авторских прав. Мы поможем в написании вашей работы!