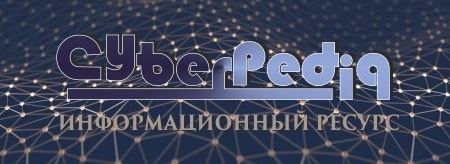
Наброски и зарисовки растений, плодов, цветов: Освоить конструктивное построение структуры дерева через зарисовки отдельных деревьев, группы деревьев...
Автоматическое растормаживание колес: Тормозные устройства колес предназначены для уменьшения длины пробега и улучшения маневрирования ВС при...
Топ:
История развития методов оптимизации: теорема Куна-Таккера, метод Лагранжа, роль выпуклости в оптимизации...
Устройство и оснащение процедурного кабинета: Решающая роль в обеспечении правильного лечения пациентов отводится процедурной медсестре...
Характеристика АТП и сварочно-жестяницкого участка: Транспорт в настоящее время является одной из важнейших отраслей народного...
Интересное:
Искусственное повышение поверхности территории: Варианты искусственного повышения поверхности территории необходимо выбирать на основе анализа следующих характеристик защищаемой территории...
Распространение рака на другие отдаленные от желудка органы: Характерных симптомов рака желудка не существует. Выраженные симптомы появляются, когда опухоль...
Берегоукрепление оползневых склонов: На прибрежных склонах основной причиной развития оползневых процессов является подмыв водами рек естественных склонов...
Дисциплины:
![]() |
![]() |
5.00
из
|
Заказать работу |
|
|
МИНИСТЕРСТВО СЕЛЬСКОГО ХОЗЯЙСТВА РОССИЙСКОЙ ФЕДЕРАЦИИ
ФЕДЕРАЛЬНОЕ ГОСУДАРСТВЕННОЕ БЮДЖЕТНОЕ ОБРАЗОВАТЕЛЬНОЕ УЧРЕЖДЕНИЕ ВЫСШЕГО ОБРАЗОВАНИЯ
«ТВЕРСКАЯ ГОСУДАРСТВЕННАЯ СЕЛЬСКОХОЗЯЙСТВЕННАЯ АКАДЕМИЯ»
Кафедра «Ремонт машин и эксплуатация машинно-тракторного парка»
ОТЧЁТ
По учебной практике по получению первичных профессиональных умений и
Навыков, в том числе первичных умений и навыков
Научно-исследовательской деятельности (учебно-ознакомительная)
студента 1 курса, АС-1802У группы
инженерного факультета (заочное отделение)
Направление – Эксплуатация ТТМ и К
Профиль – Автомобильный серви
Иванов Михаил Николаевич
Выполнил: студент группы АС-1802у
Иванов М.Н.
Принял: Дмитриев Н.Н.
Тверь 2019
Содержание
Предисловие…………………………………………………………….……3
Общее положение……………………………………………………………4
1.1 Слесарная лаборатория………………………………………….…….5
1.1.1 Разметка. Слесарный измерительный инструмент………………….6
1.1.2 Рубка зубилом. Область применения слесарной рубки………….....10
1.1.3 Резка ножовкой. Область ее применения……………………...…….12
1.1.4 Опиливание и ее применение……………………………………...…14
1.1.5 Сверление. Нарезание резьбы……………………………………..…17
1.1.6 Жестяницкие и клепальные работы……………...………………….20
1.1.7 Пайка. Ее способы……………………………………………………23
2.1 Станочная лаборатория……………………………………………….27
|
2.1.1 Работа на токарных станках. Его устройство. Резцы……….……...30
2.1.2 Работа на фрезерных станках. Их особенности…………………….44
2.1.3 Работа на строгальных и долбежных станках…………………..…..49
2.1.4 Работа на шлифовальных станках……………………………….…..51
2.1.5 Работа на обдирочно-шлифовальном станке…………………….…54
2.1.6 Работа на отрезном ножовочном станке………………………....….56
3.1 Кузнечная лаборатория………………………………………………60
4.1 Сварочная лаборатория…………………………………………...….65
5.1 Общие правила техники безопасности при работе в учебных лабораториях…………………………………………………………………73
Индивидуальное задание………………………………………………….…74
Список литературы…………………………………..……………………....75
Предисловие
Учебно-технологическая практика проводится на базе учебно-технологического центра (УТЦ). Целью практики является получение устойчивых практических навыков и умений в обработке металлов резанием вручную и на металлорежущих станках, а также получение навыков в электродуговой и газовой сварке. Учебное пособие составлено в соответствии е требованиями государственного образовательною стандарта высшего профессионального образования и международных конвенционных требований в части, касающейся практической подготовки машинной команды и вахтенных механиков судов. Учебное пособие включает в себя описание технологических процессов обработки материалов, а также правила оформления отчета. Прохождение практики предусматривает работу на слесарном, токарном, фрезерном и сварочном участках. Слесарные работы относятся к процессам холодной обработки металлов резанием. Они осуществляются как вручную, так и с помощью механизированного инструмента. Целью слесарных работ является придание обрабатываемой детали заданных чертежом форм, размеров и необходимой шероховатости поверхности. Качество выполняемых слесарных работ зависит от умения и навыков, применяемого инструмента и свойств обрабатываемого материала. Технология слесарной обработки содержит ряд следующих операций: разметка, рубка, правка, гибка, резка, опиливание, сверление, зенкование и развертывание отверстий, нарезание резьбы, клёпка, шабрение, притирка, доводка, паяние, лужение, заливка подшипников, соединение склеиванием и др. Помимо освоения основных слесарных операций, учебно-технологической практикой предусматривается овладение приёмами и приобретение навыков механической обработки поверхностей на таких металлорежущих станках, как токарный, сверлильный и фрезерный, а также приобретение навыков по электродуговой и газовой сварке.
|
Общее положение
Слесарные работы - технологические операции, обычно дополняющие станочную механическую обработку или завершающие изготовление металлических изделий соединением деталей, сборкой машин и механизмов, а также их регулировкой. Слесарные работы выполняются с помощью ручного или механизированного слесарного инструмента и проводятся с целью придания обрабатываемой детали заданных чертежом формы, размеров и определенной шероховатости поверхности. Все виды слесарных работ объединяет единая технология выполнения операций, к которым относятся разметка, рубка, правка и гибка, резка металлов, опиливание, сверление, зенкование и зенкерование, развертывание отверстий, нарезание резьбы, распиливание и подгонка, шабрение, притирка и доводка, шлифование и полирование, клепка, паяние и др. Основным условием успешного выполнения вышеуказанных работ является рациональное использование оборудования и инструментов, применяемых При слесарной обработке и сборке, а также знание приемов их выполнения.
Слесарная лаборатория
Это помещение, специально предназначенное для слесарных работ и укомплектованное необходимым оборудованием, приспособлениями, инструментом и техническим инвентарем.
![]() |
|
|
|
1 – Слесарные верстаки с тисками.
2 – Слесарный верстак с заточным и настольным сверлильным станком.
3 – Шкаф инструментальный.
4 - Разметочная плита.
Опиливание и ее применение
Опиливание металла - простейшая операция металлообработки.
|
Опиливание –это слесарная металлообработка, во время которой происходит снятие материала с поверхности детали с помощью напильника. Напильник – это инструмент, который служит для обработки металлов, состоит из многолезвийных режущих элементов, он обеспечивает высокую точность проделываемых работ, а также не значительную шероховатость обрабатываемой поверхности детали. Сама резка металла, проводится качественно и с малой погрешностью.
С помощью опиливание, детали придается нужный размер и форма, подгоняют деталь друг под друга и проводят множество других работ. Напильниками обрабатывают металлы различной формы: криволинейные поверхности, плоскости, пазы, отверстия различных форм, канавки, различного рода поверхности и т.д. Припуски во время опиливания оставляют небольшого размера - от 0.55 до 0.015 мм. А погрешность после проведенной работы может составляет от 0.1 до 0.05, а в определенных случаях еще меньше – до 0.005 мм., что обеспечивает качественную металлообработку.
Инструмент напильник – это брусок из стали определенной длины и профиля, у которого на поверхности стоит нарезка. Нарезка (насечка) формирует маленькие и острые зубья, которые определяют в сечении форму клина. Угол сечения напильника с сеченым зубом обычно равен 65-70 градусов, задний угол от 35 до 50 градусов, передний угол – 16 градусов.
Инструменты с одинарной нарезкой убирают с металла широкую стружку, по всей насечке. Они применяются при металлообработке мягких металлов.
Напильник с двойной нарезкой используются при опиливании чугуна, стали и других твердых металлов, из-за того, что перекрестная нарезка измельчает стружку, в связи с чем – облегчает работу.
Насечку рашпилем получают с помощью вдавливания металла специальными зубцами состоящими из трехгранника. Обработка металлов рашпилем производится только на мягких металлах и неметаллических материалах.
Также можно получить другую насечку с помощью фрезерования. У нее дугообразная форма и большие выемки между зубьями – это обеспечивает хорошее качество поверхностей и высокую производительность при металлообработке. Напильники производятся из стали У13А и У13, а еще из хромистой стали ШХ 15. Когда заканчивается насечка зубьев напильники термически обрабатываются. Ручки напильников изготавливаются из древесины (клен, береза и другие).
|
По своему назначению резки металла напильники делятся на следующие группы:
Общего назначения.
Надфили.
Специального назначения.
Машинные напильники.
Рашпили.
Для общих слесарных работы, чаще всего применяются напильники общего назначения.
По количеству насечек на 1 см. напильники разделяют на 6 разных номеров:
Напильники с нарезкой от номер 0 до 1 (драчевые), применяются для более грубого опиливания, так как состоят из крупных зубьев. При обработке металлов погрешность составляет от 0.6- 0.3 мм.
Напильники с нарезкой № 2-3, применяются для чистого опиливания деталей. Погрешность при металлообработке составляет 0.2-0.005 мм.
Напильники с нарезкой номером 4-5, служат окончательным обрабатываемым процессом. Погрешности при этом процессе составляет 0.1- 0.004 мм.
По своей длине напильники изготавливаются от 150 до 400 мм. По форме сечения их делят на квадратные, плоские, круглые, трехгранные, ромбические, ножничные и полукруглые. Для обработки металлов небольших форм используются малогабаритные напильники - надфили. Обработка твердых и закаленных сталей производится специальными надфилями, а на стальных стержнях закрепляются зерна алмаза. Улучшение производительности и условий труда при металлообработке опиливанием достигается путем использования механизированных (пневматических и электрических) напильников. Сменяемые угловые и прямые головки при помощи круглых фасонных инструментов способствуют опиливанию под разными углами и в труднодоступных местах.
Качество работы контролируется различного рода инструментами. Качество опиливаемой плоскости проверяется проверочной линейкой. Если плоскость должны быть опилена достаточно точно, ее подвергают проверке на проверочной плите. Если нужно опилить плоскость под определенным углом, ее проверяют с помощью угломера или угольника. Для контроля параллельности двух плоскостей используют штангенциркуль, где расстояние между плоскостями должно быть одинаковым.
Если контроль нужно провести по криволинейным поверхностям, его производят с помощью линий разметки и специальных шаблонов.
Опиливание служит для разрезания и обработки поверхности и значительно отличается от процесса плазменной резки металла, которая в свою очередь используется для полного разрезания изделия, а также для обработки его.
Сверление. Нарезание резьбы
Сверление — вид механической обработки материалов резанием, при котором с помощью специального вращающегося режущего инструмента (сверла) получают отверстия различного диаметра и глубины, или многогранные отверстия различного сечения и глубины.
|
Сверление — необходимая операция для получения отверстий в различных материалах при их обработке, целью которой является:
Изготовление отверстий под нарезание резьбы, зенкерование, развёртывание или растачивание.
Изготовление отверстий (технологических) для размещения в них электрических кабелей, анкерных болтов, крепёжных элементов и др.
Отделение (отрезка) заготовок из листов материала.
Ослабление разрушаемых конструкций.
Закладка заряда взрывчатого вещества при добыче природного камня.
Виды сверления
Сверление цилиндрических отверстий.
Сверление многогранных и овальных отверстий.
Рассверливание цилиндрических отверстий (увеличение диаметра).
Центровка: высверливание небольшого количества материала для позиционирования другого сверла (например, при глубоком сверлении) или для фиксирования детали задним центром.
Глубокое сверление: Сверление на глубину 5 и более диаметров отверстия. Часто требует специальных технических решений.
Большой проблемой при сверлении является сильный разогрев сверла и обрабатываемого материала из-за трения. В месте сверления температура может достигать нескольких сотен градусов Цельсия.
При сильном разогреве материал может начать гореть или плавиться. Многие стали при сильном разогреве теряют твердость, в результате режущие кромки стальных свёрл быстрее изнашиваются, из-за чего трение только усиливается, что в итоге приводит к быстрому выходу свёрл из строя и резкому снижению эффективности сверления. Аналогично, при использовании твердосплавного сверла или сверла со сменными пластинами, твердый сплав при перегреве теряет твердость, и начинается пластическая деформация режущей кромки, что является нежелательным типом износа.
Для борьбы с разогревом применяют охлаждение с помощью охлаждающих эмульсий или смазочно-охлаждающих жидкостей (СОЖ). При сверлении на станке часто возможно организовать подачу жидкости непосредственно к месту сверления. Подача охлаждающей жидкости также может осуществляться через каналы в самом сверле, если это позволяет станок. Такие каналы делаются во многих цельных сверлах и во всех корпусных. Внутренняя подача СОЖ необходима при сверлении глубоких отверстий (глубиной 10 и более диаметров). При этом важно не столько охлаждение, сколько удаление стружки. Давление СОЖ вымывает стружку из зоны резания, что позволяет избежать её пакетирования или повторного резания. Если в таком случае невозможно организовать подачу СОЖ, то приходится осуществлять сверление с периодическими выводами сверла для удаления стружки. Такой метод крайне непроизводителен.
При сверлении ручным инструментом сверление время от времени прерывают и окунают сверло в ёмкость с жидкостью.
Подготовка отверстий под резьбу заключается в соответствующем выборе диаметра сверла, которым будет просверливаться отверстие под нарезание резьбы.
Отверстие, в котором нарезают резьбу метчиком, должно быть чистым, т. е. просверлено, обработано зенкером или же проточено. При нарезании резьбы материал частично выдавливается, поэтому диаметр сверла должен быть несколько больше, чем внутренний диаметр резьбы.
Металлы твердые и хрупкие дают меньшие изменения величины отверстие при нарезании резьбы, чем металлы мягкие и вязкие. Если просверлить под резьбу отверстие диаметром, точно соответствующим внутреннему диаметру резьбы, то материал, выдавливаемый при нарезании, будет давить на зубья метчика, отчего они нагреваются и к ним прилипают частицы металла. Резьба может получиться с рваными нитками, а в некоторых случаях возможна поломка метчика.
При сверлении слишком большого диаметра резьба получится неполной..
размер диаметра отверстия под резьбу можно вычислить по формуле D= d-1,6t,
где D - диаметр отверстия, мм;
d - диаметр нарезаемой резьбы, мм; t - глубина резьбы, мм. Размеры воротка для закрепления метчика при нарезании резьбы подбираются в зависимости от диаметра нарезаемой резьбы. Примерная длина воротка может быть определена по формуле
L=20D+100 мм,
где D - диаметр резьбы.
После подготовки отверстия под резьбу и выбора воротка заготовку закрепляют в тисках и вставляют вертикально (без перекоса) в ее отверстие черновой метчик; а затем, прижимая левой рукой, правой поворачивают вороток вправо до тех пор, пока он не врежется на несколько ниток в металл и не займет устойчивое положение, после чего вороток с метчиком берут Обеими руками и вращают.
В целях облегчения работы вороток с метчиком вращают не все время по направлению часовой стрелки, а один-два оборота вправо и пол-оборота влево и т. д. Благодаря такому возвратно-вращательному движению метчика стружка ломается, получается короткой (дробленой), а процесс резания значительно облегчается.
Пайка. Ее способы
Пайка — технологическая операция, применяемая для получения неразъёмного соединения деталей из различных материалов путём введения между этими деталями расплавленного металла (припоя), имеющего более низкую температуру плавления, чем материал соединяемых деталей.
Спаиваемые элементы деталей, а также припой и флюс вводятся в соприкосновение и подвергаются нагреву с температурой выше температуры плавления припоя, но ниже температуры плавления спаиваемых деталей. В результате припой переходит в жидкое состояние и смачивает поверхности деталей. После этого нагрев прекращается, и припой переходит в твёрдую фазу, образуя соединение.
Прочность соединения во многом зависит от смачиваемости припоем соединяемых поверхностей. При пайке металлов качество смачивания обычно зависит от чистоты поверхности — на ней не должно быть окислов металлов или органических жиров и масел. Для удаления загрязнений, понижения поверхностного натяжения и улучшения растекания припоя применяют флюсы или ультразвуковые методы активации поверхности. При пайке неметаллических поверхностей (керамики, стекла) или легкоплавкими припоями химические флюсы не помогают смачиванию, поэтому применяют ультразвуковую активацию поверхности.
Разновидности
Пайка бывает
- низкотемпературная (нагрев припоя до 450 °C);
- высокотемпературная (нагрев припоя свыше 450 °C).
Соответственно — припои бывают
- легкоплавкие;
- тугоплавкие.
Для низкотемпературной пайки используют, в основном, электрический нагрев, для высокотемпературной — в основном, нагрев горелкой. В качестве припоя используют сплавы
оловянно-свинцовые (Sn — 90 %, Pb — 10 %, t° пл. 220 °C);
медно-серебряные (Ag — 72 %, Cu — 28 %, t° пл. 779 °C);
медно-цинковые (Cu — 48 %, Zn — 52 %, t° пл. 865 °C);
галлиевые (t° пл. ~50°С);
висмутовые (сплав Вуда с t° пл. 70 °C, сплав Розе с t° пл. 96 °C)
и т. д.
Пайка является высокопроизводительным процессом, обеспечивает надёжное электрическое соединение, позволяет соединять разнородные материалы (в различной комбинации металлы и неметаллы), отсутствие значительных температурных короблений (по сравнению со сваркой). Паяные соединения допускают многократное разъединение и соединение соединяемых деталей (в отличие от сварки). К недостаткам можно отнести относительно невысокую механическую прочность.
Исходя из физико-химической природы процесса, пайку можно определить следующим образом. Процесс соединения металлов в твёрдом состоянии путём введения в зазор припоя, взаимодействующего с основным металлом и образующего жидкую металлическую прослойку, кристаллизация которой приводит к образованию паяного шва. На границе между припоем и основным металлом образуются переходные слои, состоящие из продуктов их взаимодействия — твёрдых растворов и интерметаллидов. Они обеспечивают адгезию между припоем и основным металлом, однако слишком толстые слои интерметаллидов проявляют хрупкость и приводят к разрушению пайки.
Виды пайки:
капиллярная (смачивание деталей и затекание припоя в зазор между ними происходит за счёт капиллярных сил):
горизонтальная;
вертикальная;
диффузионная (пайка происходит при температуре выше точки плавления припоя за счёт взаимной диффузии припоя и основного металла):
атомно-диффузионная;
реакционно-диффузионная;
контактно-реакционная или контактно-реактивная:
с образованием эвтектики;
с образованием твёрдого раствора;
реакционно-флюсовая или реактивно-флюсовая (во время нагрева припой образуется за счёт реакции металла и флюса):
без припоя;
с припоем;
пайка-сварка:
без оплавления;
с оплавлением.
Анализируя сущность физико-химических процессов, протекающих на границе основной металл — расплав припоя (при формировании соединения в существующих видах пайки), можно видеть, что различия между капиллярной пайкой, диффузионной пайкой и пайкой-сваркой не носят принципиального характера. Капиллярность является общим признаком пайки. Отличительным признаком диффузионной пайки является длительная выдержка при температуре пайки и изотермическая кристаллизация металла шва в процессе пайки. Других характерных признаков этот метод не имеет, основное назначение его — повысить температуру распая шва и прочность паяного соединения. Диффузионная пайка может быть развитием любого вида пайки, в том числе капиллярной, реакционно-флюсовой или контактно-реакционной. В последнем случае диффузионная пайка возможна, если второй металл взаимодействующей пары вводится в виде прослойки между соединяемыми металлами. При реакционно-флюсовой пайке происходит совмещение процессов вытеснения из флюса металла, служащего припоем, и его взаимодействия с основным металлом. Наконец, пайка-сварка отличается от других методов пайки количеством вводимого припоя и характером формирования шва, делающим этот метод пайки похожим на сварку плавлением. При соединении разнородных металлов при пайке-сварке возможно оплавление кромки одной из деталей, изготовленной из более легкоплавкого металла.
Станочная лаборатория
Это помещение, специально предназначенное для работ на станках, укомплектованное необходимым оборудованием, приспособлениями, инструментом и техническим инвентарем.
Оно предназначено для ознакомления студентов с работой и обширным разнообразием станков.
План лаборатории
![]() |
Спецификация оборудования станочной лаборатории
1. Токарно-винторезный станок 16К25;
2. Токарно-винторезный станок 1В62Г;
3. Токарно-винторезный станок 16К20;
4. Токарно-винторезный станок 16К20;
5. Токарно-винторезный станок 16К20;
6. Токарно-винторезный станок 1В62Г;
7. Токарно-винторезный станок 1Д95;
8. Токарно-винторезный станок 1М95;
9. Калорифер;
10. Вертикально-сверлильный станок 2Н135;
11. Универсально-фрезерный станок 6Р80Г;
12. Строгальный станок 7Б35;
13. Отрезной ножовочный станок 872М;
14. Горизонтально-фрезерный станок 6Н81Г;
15. Горизонтально-фрезерный станок 6М82;
16. Горизонтально-фрезерный станок 6Н83;
17. Вертикально-фрезерный станок с кнопочной станцией 6А62П;
18. Вертикально-фрезерный станок 6В11;
19. Круглошлифовальный станок 312М;
20. Плоскошлифовальный станок 3Г71;
21. Заточной станок;
22. Силовой щит для питания станков 1…9 (рубильник № 4);
23. Силовой щит для питания станков 10,11,12, и 21, и слесарной лаборатории (рубильник № 5);
24. Силовой щит для питания станков 13…20 (рубильник № 6);
Токарные центры
Токарный центр совмещает в себе функции токарного и фрезерного станков. Современное оборудование позволяет осуществить комплексные токарно-фрезерные работы, а также выполнить сверление, создание резьбы, гидростатическое накатывание и многие другие специфические задачи. Токарные центры применяются для обработки деталей различных ступенчатых и криволинейных тел: крышек, валиков, корпусов, втулок и т.п. Многофункциональность токарного центра также позволяет реализовать такие виды работ, как обработка внецентровых отверстий в деталях, фрезеровка канавок, лысков и сложных криволинейных поверхностей.
Токарные станки с ЧПУ
Инновационные станки с числовым программным управлением (ЧПУ) относятся к новому поколению токарного оборудования и позволяют в короткий срок выполнить высокоточные токарные работы по металлу по заданной программе. Благодаря возможности объединить несколько станков с ЧПУ в одну крупную производственную линию, данная разновидность токарного оборудования чаще всего используется на крупных предприятиях, оснащённых автоматическими производственными линиями. Конструктивно станок с ЧПУ дополнен операторским пультом, дисплеем, памятью (ПЗУ и ОЗУ) и контроллером – компьютеризированным устройством, формирующим траекторию движения режущего инструмента в соответствии с имеющимися данными.
Резе́ц — режущий инструмент, предназначен для обработки деталей различных размеров, форм, точности и материалов. Является основным инструментом, применяемым при токарных, строгальных и долбёжных работах (и на соответствующих станках).
Для достижения требуемых размеров, формы и точности изделия с заготовки снимаются (последовательно срезаются) слои материала при помощи резца. Жёстко закреплённые в станке резец и заготовка в результате относительного перемещения контактируют друг с другом, происходит врезание рабочего элемента резца в слой материала и последующее его срезание в виде стружки. Рабочий элемент резца представляет собой острую кромку (клин), который врезается в слой материала и деформирует его, после чего сжатый элемент материала скалывается и сдвигается передней поверхностью резца (поверхностью схода стружки). При дальнейшем продвижении резца процесс скалывания повторяется и из отдельных элементов образуется стружка. Вид стружки зависит от подачи станка, скорости вращения заготовки, материала заготовки, относительного расположения резца и заготовки, использования СОЖ и других причин.
Наибольшую стойкость имеют резцы с пластинками из твердых сплавов, наименьшую — резцы из углеродистой стали.
Вот, например, какие скорости резания можно рекомендовать при точении различных материалов резцом из быстрорежущей стали. Стойкость его без охлаждения равна 60 минутам.
Примерные данные о скорости резания металлов:
Материал | Скорость резания в м/мин. |
Серый чугун | 25 |
Твердая сталь | 25 |
Мягкая сталь | 50 |
Бронза | 75 |
Латунь | 100 |
Алюминий | 250 |
Подрезание торцов и уступов
Для подрезания торцов и уступов на токарном станке пользуются обычно подрезными резцами. Такой резец изображен на следующем рисунке:
Подрезание в центрах: а — подрезной резец; б — подрезание торца с полуцентром.
Его лучше употреблять при точении детали в центрах. Для того, чтобы торец можно было обрабатывать целиком, в заднюю бабку вставляется так называемый полуцентр.
Если деталь закреплена только одним своим концом — при обработке в патроне, — то для проточки торца может быть использован и проходной отогнутый резец. Для этой же цели и для проточки уступов используются и специальные подрезные упорные резцы, которые работают с поперечной и с продольной подачей.
Подрезание торцов: а — подрезание проходным отогнутым резцом, б — подрезной упорный резец и его работа.
При подрезании торцов и уступов юный мастер должен следить за тем, чтобы вершина резца была всегда установлена строго на уровне центров. Резец, установленный выше или ниже уровня центров, оставит на середине сплошного торца неподрезанный выступ.
Вытачивание канавок
Для вытачивания канавок служат прорезные резцы. Их режущая кромка точно воспроизводит форму канавки. Так как ширина канавок обычно невелика, режущую кромку прорезного резца приходится делать узкой, поэтому она получается довольно ломкой. Для повышения прочности такого резца высоту его головки делают в несколько раз больше ширины.
Прорезной и отрезной резцы
По этой же причине головка имеет небольшой передний угол.
Отрезные резцы очень похожи на прорезные, но имеют более длинную головку. Более узкая головка делается с целью сократить расход материала при отрезании.
Длина головки должна подбираться по размерам детали и быть несколько больше половины ее диаметра.
При установке прорезных и отрезных резцов нужно тоже быть очень внимательным и точным. Небрежная установка резца, например небольшой его перекос, вызовет трение резца о стенки канавки, брак в работе, поломку инструмента.
Вытачивание узких канавок производится за один проход резца, который подбирается по ширине будущей канавки. Широкие канавки вытачивают в несколько проходов.
Вытачивание конусов
В практике юного токаря вытачивание конусов будет встречаться реже, чем другие работы. Наиболее простой способ— точение небольших конусов (не более 20 мм) специальным широким резцом.
Проверка выточки шаблоном
Меры предосторожности
При работе на токарном станке нужно руководствоваться следующими правилами:
1) начинать работать на станке можно только после детального ознакомления со станком и методами обработки;
2) не работать на неисправном станке или негодным (тупым) инструментом;
3) прочно закреплять деталь и следить за исправностью ограждающих устройств;
4) не работать в свободной одежде: рукава завязывать у кисти, длинные волосы прятать под головной убор;
5) своевременно убирать стружку и следить за порядком на рабочем месте;
6) не останавливать руками вращающийся патрон;
7) в случае неисправности немедленно выключить станок.
Применение защитного щитка при точении
Уход за станком
Чем тщательнее уход за станком, тем лучше и дольше он будет работать. Это простое правило следует твердо запомнить и аккуратно его выполнять. Уход за токарным станком сводится к следующему.
Основное — это смазка всех трущихся частей. Перед началом работы необходимо осмотреть станок и проверить, достаточно ли смазки. Наиболее внимательно нужно следить за смазкой подшипников, заполняя масленки и смазочные отверстия машинным маслом. Станок в это время, во избежание несчастного случая, должен быть остановлен.
После работы нужно вычистить станок, убрать стружку, протереть направляющие станины и суппорта, и смазать их тонким слоем масла.
Абсолютно чистыми должны быть и конические отверстия шпинделя и пиноли задней бабки. Точность работы станка будет зависеть от их хорошего состояния.
До начала работы нужно также проверить состояние приводного ремня. Его нужно оберегать от масляных брызг и капель, так как замасленный ремень проскальзывает и быстро срабатывается. Натяжение ремня должно быть не слишком сильным, но и не слишком слабым: слабо натянутый ремень проскальзывает, а при сильном его натяжении сильно греются и быстро изнашиваются подшипники. Ограждение приводного ремня тоже должно быть в порядке.
Техника безопасноти.
Перед началом работы необходимо проверить соответствие (исправность) блокировочных и защитных устройств, работу органов управления, надежность установки и закрепления обрабатываемой детали и ШК, проверить исправность устройств для смазки, охлаждения, отсоса пыли и т.п. Наладку станка следует производить при выключенном рубильнике. Исправление электроаппаратуры студентом и наладчиком не допускается.
В процессе наладки особое внимание должно уделяться установке и закреплению ШК. До установки круга следует проверить биение шпинделя. ШК должен быть тщательно проверен непосредственно перед установкой. Проверяется отсутствие трений, раковин, пленок и прочих повреждении. Проверяется соответствие маркировки ШК. При зажиме ШK во флянцах его необходимо центрировать. Правка круга должна проводиться в защитных очках с применением соответствующих приспособление, гарантируемых безопасность.
Запуск станка без защитного кожуха не допускается. Перед запуском проверяется надежность закрепления упоров.
После наладки следует осмотреть станок и дать ему отработать 5 - 10 мин. вхолостую.
Техника безопасности.
Перед включением станка убедиться, что его пуск не создает опасности.
Перед началом работы круг, установленный на станок, должен быть подвергнут кратковременному вращению вхолостую при рабочей скорости в течение:
круги диаметром до 400 мм - не менее 2 мин.;
круги диаметром свыше 400 мм - не менее 5 мин.
Обрабатываемую деталь к абразивному кругу подавать плавно, без толчков и резкого нажатия.
Оберегать круг от ударов и толчков. Запрещается при обработке деталей применять рычаги для увеличения нажима на круг.
Не прикасаться руками к шлифовальному кругу до полной его остановки. Запрещается пользоваться боковыми (торцевыми) поверхностями круга, если круг не предназначен для данного вида работ.
Не передавать и не принимать какие-либо предметы через станок во время работы.
Удалять абразивную и металлическую пыль со станка и рабочего места только щеткой-сметкой или скребком.
Обязательно остановить станок и выключить двигатель в следующих случаях:
при отлучке от станка даже на короткое время;
при перерыве в подаче электроэнергии;
при чистке, смазке, уборке станка;
при выявлении какой-либо неисправности оборудования и электродвигателя;
если при пуске или в процессе заточки ощущается сильное биение круга.
Устанавливать инструмент на шлифовальный станок должен специально обученный рабочий или наладчик. Применять круги без отметки об испытании не допускается. Перед установкой на станок круг должен быть тщательно осмотрен и проверен на отсутствие трещин.
Техника безопасности.
Сосредоточить внимание на выполняемой работе, не отвлекаться на посторонние дела и разговоры, не отвлекать других.
Не допускать на свое рабочее место лиц, не имеющих отношения к порученной работе. Без разрешения мастера не доверять свой работающий станок другому рабочему.
Не опираться на станок во время его работы и не позволять делать это другим
О всяком несчастном случае немедленно поставить в известность мастера и обратиться в медицинский пункт.
При всяком перерыве в подаче электроэнергии немедленно выключить электрооборудование станка
Если на металлических частях станка обнаружено напряжение (ощущение тока), электродвигатель работает на две фазы (гудит), заземляющий провод оборван, остановить станок и немедленно доложить мастеру о неисправности электрооборудования.
Надежно и жестко закреплять обрабатываемую деталь.
Запрещается закреплять заготовку во время вращения диска
При использовании для закрепления заготовок пневматических, гидравлических или электромагнитных приспособлений тщательно оберегать от механических повреждений трубки для подачи воздуха, жидкости и электропроводку.
Перед подводом пилы к заготовке убедиться в том, что пила надежно закреплена. Подвести диск к заготовке в начале резания осторожно, плавно, без ударов.
Во время вращения диска исправлять положение трубки охлаждающей системы запрещается.
Не допускать разбрызгивания на пол масла и охлаждающих жидкостей.
Запрещается стоять в плоскости вращения диска во время работы станка.
Запрещается поддерживать руками отрезаемый конец заготовки.
Запрещается выталкивать стружку из <
|
|
Состав сооружений: решетки и песколовки: Решетки – это первое устройство в схеме очистных сооружений. Они представляют...
Организация стока поверхностных вод: Наибольшее количество влаги на земном шаре испаряется с поверхности морей и океанов (88‰)...
Типы сооружений для обработки осадков: Септиками называются сооружения, в которых одновременно происходят осветление сточной жидкости...
Папиллярные узоры пальцев рук - маркер спортивных способностей: дерматоглифические признаки формируются на 3-5 месяце беременности, не изменяются в течение жизни...
© cyberpedia.su 2017-2024 - Не является автором материалов. Исключительное право сохранено за автором текста.
Если вы не хотите, чтобы данный материал был у нас на сайте, перейдите по ссылке: Нарушение авторских прав. Мы поможем в написании вашей работы!