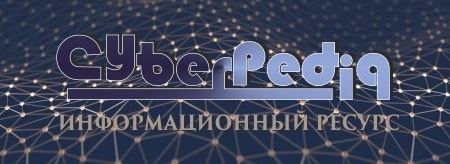
История развития хранилищ для нефти: Первые склады нефти появились в XVII веке. Они представляли собой землянные ямы-амбара глубиной 4…5 м...
История развития пистолетов-пулеметов: Предпосылкой для возникновения пистолетов-пулеметов послужила давняя тенденция тяготения винтовок...
Топ:
Оценка эффективности инструментов коммуникационной политики: Внешние коммуникации - обмен информацией между организацией и её внешней средой...
Процедура выполнения команд. Рабочий цикл процессора: Функционирование процессора в основном состоит из повторяющихся рабочих циклов, каждый из которых соответствует...
История развития методов оптимизации: теорема Куна-Таккера, метод Лагранжа, роль выпуклости в оптимизации...
Интересное:
Что нужно делать при лейкемии: Прежде всего, необходимо выяснить, не страдаете ли вы каким-либо душевным недугом...
Уполаживание и террасирование склонов: Если глубина оврага более 5 м необходимо устройство берм. Варианты использования оврагов для градостроительных целей...
Как мы говорим и как мы слушаем: общение можно сравнить с огромным зонтиком, под которым скрыто все...
Дисциплины:
![]() |
![]() |
5.00
из
|
Заказать работу |
|
|
Служебное назначение шпинделя и принцип работы.
Шпиндельный узел токарного автомата и полуавтомата предназначен для вращения заготовки и передачи на нее крутящего момента, необходимого для осуществления процесса резания. Этот узел является самым ответственным в автоматах и полуавтоматах, определяющим точность и чистоту обработки. В качестве опор шпинделей в большинстве автоматов и полуавтоматов применя-ются точные подшипники качения. В некоторых моделях применяются под-шипники скольжения. Шпиндельная бабка полуавтомата представлена на рис 1.
В автоматах продольного точения главный шпиндель 11 смонтирован в шпиндельной бабке, перемещающейся в продольном направлении. Шпиндель установлен на 2 – х опорах. Передней опорой служит игольчатый подшипник ка-чения 16. Задней опорой являются 2 радиально – упорных шарикоподшипника 8. Зазор в подшипнике передней опоры регулируют затягиванием гайки 15 и контролируют индикатором, установленным так, чтобы его измерительный штифт касался цилиндрической поверхности переднего конца шпинделя (при снятом колпачке 1). После регулировки гайку 15 фиксируют стопором 4 с винтом 3. Зазор в шарикоподшипниках задней опоры регулируют поворотом лимба 9.
Приводной шкив 7 установлен непосредственно на шпинделе автомата. В отверстии передней части шпинделя установлена конусная втулка 17, в которую вставлена пружина 2 и сменная зажимная цанга. Пружина 2, сжатая при завин-чивании гайки 18 между торцом зажимной цанги и внутренним буртиком конусной втулки, бедет постоянно двигать конусную втулку вправо, разжимая цангу и освобождая пруток. При перемещении конусной втулки влево цанга освобождает пруток.
|
В средней части шпинделя прорезаны два продольных паза, в которые вставлены два кулачка 13. При повороте рачага – вилки 14 стакан 5 с шарико – подшипником перемещает конусную втулку 6. Последняя при этом раздвигает длинные плечи кулачков 13, которые поворачиваясь вокруг оси 12, короткими плечами призводят зажим цанги. При отходе конусной втулки 6 длинные плечи кулачков 13 под действием пружины 2 сходятся, а цанга разжимается. Усилие зажима цанги регулируют гайкой 10.
Подачи прутка для обработки в автоматах продольного точения как таковой нет. Пруток в них подается вперед вместе с шпиндельной бабкой в процессе обработки заготовки. Поэтому после отрезки готовой детали пруток остается на месте, цанга разжимается и вместе со шпиндельной бабкой быстро отходит назад.
![]() |
Рис.1.1. Шпиндельная бабка
Анализ технических условий.
1. Термообработка всех поверхностей, кроме резьб HRC 40 – 45.
2. Поверхность Ф38h5 служит для установки игольчатого подшипника качения, что обуславливает допуск отклонения формы – отклонение от цилиндричности составляет 0,016 мм.
3. Поверхности Ф30 –0,006 Ф35 h6 служат для установки двух радиально – упорных подшипников, что также объясняет жесткий допуск на размер и отклонение формы, в данном случае – отклонение от цилиндричности 0,016 мм.
4. Несоосность поверхности А и Б относительно их общей оси не более 0,005 мм, что вызвано тем, что на поверхности А (резьба М30х1,5 – 6g) устанавливается гайка, которой регулируется усилие зажима цанги, находящейся на поверхности Б.
Выбор баз.
При составлении технологических процессов большое значение с точки зрения обеспечения заданной точности имеет выбор баз. Наибольшей точности обработки детали можно достигнуть в том случае, когда весь процесс обработки ведется от одной базы с одной установкой, т.к. в виду возможных смещений при каждой новой установке вносится ошибка во взаимное расположение осей повер-хностей.
|
Обработку заготовок обычно начинают с создания технологических баз. В начале за технологическую приходится принимать черновую базу, т.е. необрабо-танные поверхности заготовки. Выбранная черновая база должна обеспечивать равномерное снятие припуска при последующей обработке поверхностей с базированием на обработанную технологическую базу и наиболее точное взаимное положение обработанных и необработанных поверхностей детали. Черновые базовые поверхности должны быть по возможности гладкими; не иметь штампо-вочных и литейных уклонов.
При выборе технологических баз для обработки заготовок следует исполь-зовать принцип совмещения баз, т.е. в качестве технологической база брать поверх-ность, являющейся измерительной базой. Лучшие результаты достигаются при совмещении технологической, измерительной и конструкторской баз, т.е. тех поверхностей, которые определяют положение детали в собранном виде.
При составлении маршрута обработки следует соблюдать принцип постоянства баз; на всех основных технологических операциях использовать в качестве технологических баз одни и те же поверхности заготовки. Когда постоянство технологической базы не может быть обеспечено, в качестве новой технологической базы обязательно выбирают обработанные поверхности.
Основными базами шпинделя являются поверхности его опорных шеек (поверхности Ø38h5, Ø30-0,002), но их использование в качестве технологических баз на большинстве операций невозможно. Поэтому для большинства операций за технологические базы принимаем поверхности центровых отверстий, что позволяет обрабатывать большую часть рабочих поверхностей на них. Обработку сквозного отверстия L=464мм будем проводить на опорных шейках шпинделя.
В связи с этим механическую обработку начинаем с операции подготовки технологической базы – обработки торцов и центровки.
Чистовую и отделочную обработки опорных шеек и соосных с ними наружных поверхностей производим на специальных пробках с центрованными отверстиями. Пробки вставляем в цилиндрические отверстия Ø19 и Ø33, которые служат технологическими базами. Однако пробки, входящие дополнительным звеном в технологическую размерную цепь при смене их на различных операциях, могут дать существенные погрешности установки, которые повлияют на положение исполнительной поверхности центрального отверстия относительно поверхности опорных шеек. Поэтому, чтобы уменьшить влияние погрешности на конечную точность шпинделя, чистовые и отделочные операции обработки наружных поверхностей будут выполняться на одних и тех же пробках, вставленных в шпиндель, без их смены.
|
При обработке шпоночных пазов базирование производим на опорные шейки после их чистовой обработки, обработку ведем на призмах.
2.3 Маршруты обработки поверхностей Ø38h5 и Ø28H6.
Маршруты обработки поверхностей Ø38h5 и Ø28H6 приведены в таблицах №3 и №4
Поверхность Ø38 h 5:
1. Точение черновое - 12кв;
2. Точение чистовое – 9кв;
3. Шлифование чистовое – 7кв;
4. Шлифование тонкое – 5 кв.
Поверхность Ø28Н6:
1. Сверление – 13 кв;
2. Рассверливание – 11кв;
3. Чистовое растачивание – 8 кв;
4. Шлифование - 6кв.
2.4 Расчет припусков на Ø38h5 и Ø28H6.
Для ступенчатых валов расчет ведут по ступени с наибольшим диаметром, а при равных диаметрах – по ступени, к которой предъявляют наиболее высокие требования по точности и качеству поверхности.
Построение алгоритма расчета припусков сводится к следующим основным этапам:
1.Определяют составляющие элементы минимального припуска Rzi-1, hi-1, Δi-1 и εi, где (i-1) относится к элементу, полученному на смежном предшествующем технологическом переходе, а i – к выполняемому переходу.
2. Рассчитывают: минимальный припуск; максимальные и номинальные припуски на весь технологический процесс обработки поверхностей; минимальные и максимальные размеры, определяющие положение обрабатываемых поверхностей по технологическим переходам, и размеры заготовки.
Нормативные материалы предназначены для расчета припусков на поверх-ности типовых деталей машин, обрабатываемых как на предварительно настро-енных, так и на универсальных станках. Для каждого вида заготовки и способа обработки в нормативных материалах приведены методические указания, отмечающие особенности расчета припусков для данного вида заготовки.
|
Расчет минимального припуска ведут по формуле:
,
где: Rz i-1 – высота неровностей профиля на предшествующем переходе;
h i-1 – глубина дефектного поверхностного слоя на предшествующим переходе;
D i -1 - суммарные отклонения расположения поверхностей;
Еу i – погрешность установки.
Δ включает в себя:
Δк- кривизна профиля проката (стр. 180 табл. 4) [1]
Δц.о – погрешность центрирования, которая равна:
,
где Т-допуск на диаметральный размер базы заготовки. (стр. 178 формула 16.) [1]
Берем поверхность ф38 h5
2.4.1.Элементы припуска проката:
ф38h5 Rz=160мкм; h=250 мкм,
Δ= ;
где Δк – кривизна профиля;
Δц - смещение оси заготовки в результате погрешности центрирования.
Δц= ,
где Т – допуск на диаметральный размер заготовки,
Δц= =0,53мм,
Δк=0,5 – кривизна профиля проката на 1 мм длины, т.е. в нашем случае
при длине заготовки 466 мм общая величина кривизны профиля равна:
Δк = =1165мкм, следовательно
Δ =
2.2.1. Токарная операция:
Элементы припуска:
Rz=63мкм; h=60мкм; Δ= =76,74мкм, где Ку = 0,06 - коэффициент уточнения для отливок, поковок, штампованных заготовок и сортового проката. (стр. 190 табл. 29) [1]
2.4.2. Токарная операция.
Элементы припуска:
Rz=30мкм; h=20 мкм; Δ= =3,06мкм, где Ку = 0,04-коэффициент уточнения для отливок, поковок, штампованных заготовок и сортового проката (для чистового обтачивания). (стр. 190 табл. 29) [1]
Результаты расчетов припуска приведены в таблице 2.
Таблица №2
Тех. Мар. Обработки детали
Эл-ты припуска, мкм
Расчетный мин. Размер, мм
Тех. мар. Обработки детали
Эл-ты припуска, мкм
Расчетный мин. Размер, мм
Электробезопасность.
По опасности поражения электрическим током проектируемый участок цеха относится к помещениям особо опасным, т.к. характеризуется наличием следующих условий, создающих повышенную опасность;
- токопроводящих полов – металлических и железобетонных;
- коэффициента заполнения площади металлоконструкциями и электрооборудованием, превышающим 0,2.
По доступности электрического оборудования проектируемый участок цеха относится к производственным помещениям, т.к. доступ к электроустановкам имеют квалифицированный персонал и производственные рабочие. Основное рабочее напряжение 380 В, переносимое электрооборудование работает при 36 (42) В.
Меры защиты:
§ от перегрузок в электросети:
- использование в электросети слабых звеньев (плавких предохранителей, рассчитанных на силу тока, превышающую номинальную на 25%, тепловых реле);
- правильный расчет сети и ее монтаж;
- не допускается подключать в сеть источники, на которые сеть не рассчитана.
|
§ от прикосновения к токоведущим частям электрооборудования:
- все токоведущие части электрооборудования изолированы. Проводку сети напряжением более 200 В заключают в металлические шланги, а напря-жением более 300 В – в стальные трубы;
- все соединенные кабели уложены в траншеи, которые перекрыты сверху бетонными плитами;
- токоведущие части электрических установок изолированы недоступным расположением (высота от пола более 3,5 м в цехе и 2,5 метра в машинном зале), дистанционным управлением, блокировкой, их ограждение дости-гается размещением в отдельной камере, укрытой кожухом или сетчатым заграждением и предупредительной сигнализацией;
- меры защиты от пробоя на корпус: сопротивление контурного заземления в сети до 1000 В не превышает 4 Ом.
§ индивидуальные средства защиты:
- диэлектрические перчатки;
- инструменты с изолированными ручками;
- диэлектрические коврики;
- изолирующие подставки.
Схема 4.1.1.1.
Схема подключения оборудования к внешнему контуру
1 – Оборудование
2 – Стена
3 – Внутренний контур
4 – Ответвление
5 – Внешний контур
6 – Заземлители
- на рисунке 5.1.1.1. приведена контурная схема заземления.
Защита от шума и вибрации.
Шум - представляет собой беспорядочное сочетание звуков различной интенсивности и частоты.
Рост мощностей современного оборудования и машин, развитие всех видов транспорта привели к тому, что человек на производстве и в быту постоянно под-вергается воздействию шума высокой интенсивности.
Таблица 4.1.3.1.
Допустимые уровни звукового давления и уровня звука на постоянных рабочих местах.
(ГОСТ 12.1.003-83)
Вид помещения | Среднегеометрические частоты октавных полос, Гц | Уровни звука, дБА | |
250 | 500 | ||
Уровни звукового давления, дБ | |||
При шуме, возникаю-щем на постоянных рабочих местах | 86 | 83 | 85 |
Для снижения шума предусмотрены:
- применение звукопоглощающих материалов и конструкций с высоким коэффициентами звукопоглощения для стен и потолка;
- глушение аэродинамических шумов глушителями шума, установленных на воздуховодах;
- средства индивидуальной защиты (вкладыши);
- смазка трущихся деталей;
Вибрацией -называют механические колебания упругих тел или колебательные движения механических систем
Таблица 4.1.3.2.
Допустимые параметры вибрации. (ГОСТ 12.1.003-76)
Среднегеометрические и граничные частоты октавных полос, Гц | Среднеквадратичное значение колебательной скорости | Амплитуда перемещений гармоничных колебаний | |
мм/сек | дБ | ||
4 | 4,5 | 99 | 0,25 |
Мероприятия по борьбе с производственными вибрациями:
- для ослабления вибрации кожухов станка применяют резиновые прокладки;
- фундаменты для станков и оборудования с неуравновешенными частями выполняются с акустическими разрывами, заполненными пористым мате-риалом, и акустическим швом, расположенным в нижней части фундамента;
- при установке станков и оборудования, создающих при работе вибрации, под их станины на междуэтажные перекрытия укладывают прослойку из виброизоляционных материалов.
Защита воздушного бассейна.
Для защиты атмосферы окружающей среды проектом предусмотрено улавливание всех вредных отходов и выделений системой местных отсосов с обязательной очисткой отходящих газовых потоков и контроля их по ПДК.
См пункт 4.1.4.
Защита водного бассейна.
Источниками водоснабжения являются: городская водопроводная вода для бытовых нужд, для технических - вода берется из реки Клязьма.
Вода для технических нужд в цехе используется по замкнутому внутри-заводскому циклу. Вода с применением эмульсии и масла поступает через общий коллектор в отстойники, масло с поверхности воды собирается, далее вода проходит нейтрализацию и фильтрацию.
Не имеющие вредных примесей бытовые и производственные сточные воды, поступающие в городскую канализацию, очищаются и обезвреживаются на полях орошения, полях фильтрации или на современных канализационных станциях. Очищенные сточные воды поступают в естественные водоемы.
Утилизация отходов.
Отходами производства является обрезы, металлическая стружка, отработанные ГСМ. Складируется по маркам стали и отправляется на переплав. Отработанные ГСМ в металлических емкостях отправляются на специальные заводы, для регенерации с целью дальнейшего использования.
Все отходы вывозятся с территории завода централизовано в специально оборудованные для переработки либо утилизации места.
1.Организация производственного участка.
1.1.Формы организации производственного процесса в зависимости от типа производства.
Тип производства – серийный. Его характерной особенностью является изготовление деталей партиями. В серийном типе производства применяется форма организации технологических процессов – групповая, характеризуются однородностью технологических признаков изделия и специализацией рабочих мест.
Под размером партий деталей принимаем число деталей,обрабатываемых с одной наладки оборудования.
Определение нормативного размера партии деталей определяется в два этапа:
1.минимальный размер партии определяется по формуле:
Nmin= Тпз.
tшт*К
где Тпз – подготовительно – заключительное время на переналадку оборудования по операции, имеющей наибольшие затраты времени на переналадку, мин.
tшт – штучное время операции, имеющей наибольшее подготовительно – заключительное время, мин.
К – коэффициент допустимых потерь времени на переналадку станка принимаем К=0,03.
2.Оптимальный размер партии деталей должен быть равным или больше минимального размера партии и кратным сменно – суточной программе (Nгод/Ф).
Nопт= N год * t
Ф
где Nопт – оптимальный размер партии деталей
Nгод – годовая программа, шт.
Ф = 252 – число рабочих дней в году
t=10 дней – необходимый запас деталей
заданная программа на год – 9480
Таблица 1 нормы времени по операциям.
№ операции | Наименование операции | Время подготовительно- заключительное Тпз (мин). | Штучное время tшт(мин) |
005 | Токарная | 18 | 360 |
010 | Сверлильная | 12 | 180 |
015 | Фрезерная | 20 | 180 |
020 | Шлифовальная | 16 | 300 |
Минимальный размер партии составит:
Nmin=20/(180*0,03)=3,703 дет принимаем 4 деталей.
Оптимальный размер партии деталей составит:
Nопт=(9480/252)*10=376деталей
Сменно-штучная программа составит:
N=9480/52=37,6 дет
1.2.Расчет количества оборудования и коэффициента загрузки.
Построение графика загрузки оборудования.
При серийном типе производства расчет количества рабочих мест на участке ведется по операциям на основе трудоемкости программы и эффективного годового фондавремени работы одного станка по формуле:
Cp= N год* S t ш-к
Fэф*60
Где Nгод-годовая программа выпуска деталей шт.
Stш-к-штучно-калькуляционное время на операциях, выполняемых на однотипных станках, мин.
Fэф- годовой эффективный фонд времени работы станков, час.
Расчет Fэф ведется по формуле:
Fэф=[(Дк-ДВ-Дпр)*Тсм-Дпред*Тсок]*С(1-a/100)
Где Дк=365-количество календарных дней в году
Дв=103-количествовыходных дней в году
Дпр=10-количество праздничных дней в году
Дпред=8-количествопредпраздничных дней в году
Тсм=8-продолжительность смены
Тсок=1ч.-сокращение продолжительности смены в предпраздничные дни
С=2- -количество смен работы оборудования в течении суток
a=3%-процент времени работы на ремонт и перерывы.
Fэф=3895,52ч.
Коэффициент загрузки рабочих мест устанавливаются по формуле:
Кзагр= Ср.
Спр
Где Ср - расчетное количество раб мест, округляем до ближайшегоцелого числа – принятого количества станков
Спр – количество принятых раб мест
Средний коэффициент загрузки участка (Кзагр.ср)определяется отношением суммы рабочих мест к сумме принятых раб мест, должен быть не менее 85%.
Кзагр.ср= S С р
SСпр
Для расчета количества оборудования и его загрузки используем данные таблицы 1.
Штучно – калькуляционное время по операциям определяется по формуле:
tш-к= Тпз + tшт
Nопт
t005 ш-к=(18/376)+360=360,04
t025 ш-к=(20/376)+180=180,05
t025 ш-к=(20/376)+180=180,05
t045 ш-к=(16/376)+300=300,04
Расчет количества мест на участке:
С005р=9480*360.04/3895,52*60=10.23 Спр=11
С025р=9480*180,05 /3895,52*60=5.114 Спр=6
С025р=9480*180,05 /3895,52*60=5.114 Спр=6
С045р=9480*300.04 /3895,52*60=8.52 Спр=9
Кзагр= 10,23+5,114+5,114+8,52 = 0.905
11+6+6+9
Кзагр.ср=90,5%
Таблица 2 количество станков и их загрузка.
№ операции | Наименование операции | Штучно-калькуляционное время tш-к | Количество станков | Коэффициент загрузки Кзагр % | |
Расчетное Ср | Принятое Спр | ||||
005 | Токарная | 360.04 | 10.23 | 11 | 93 |
010 | Сверлильная | 180,05 | 5,114 | 6 | 85,2 |
015 | Фрезерная | 180.05 | 5.114 | 6 | 85.2 |
020 | Шлифовальная | 300.04 | 8.52 | 9 | 94.6 |
Итого | 1020,18 | 28,978 | 32 | К ср. загр.=90,5% |
Для построения графика загрузки оборудования используем таблицу 2.
100
90
80
70
60
50
40
30
20
10
0 11 6 6 9 станки
Таблица 3 сводная ведомость оборудования.
Полна стоимость всего оборудования | 1610000 | 4485000 | 2496375 | 3783500 | 4451880 | 4020975 | 20847730 | |
На 1 станок | Полная стоимость | 402500 | 747500 | 832125 | 540500 | 741980 | 670162,5 | |
Монтаж 15% от цены | 52500 | 97500 | 108538 | 70500 | 96780 | 87412,5 | ||
Цена руб | 350000 | 650000 | 723587 | 470000 | 645200 | 582750 | ||
Сумарная мощность | Всех станков | 40 | 66 | 22,5 | 22,5 | 66 | 66 | 283 |
На 1 станок | 10 | 11 | 7,5 | 7,5 | 11 | 11 | ||
Группа
оборудования
Габаритные размеры мм.
Количество
станков
Наименование оборудования
1.3.Расчет численности рабочих, работающих на учаске.
Численность работающих на участке определяются по группам и категориям работающих: производственные рабочие, вспомогательные рабочие,ИТР, служащие.
А)расчет численности производственных рабочих.
В серийном производстве определение количества производственных рабочих ведется по каждой профессии, по каждому квалифицированному разряду отдельно, исходя из трудоемкости работ за год, с учетом многостаночного обслуживания.
Р= Q.
Fэф.р*Sм
Где Q- трудоемкость годовой программы с догрузкой, в норма часах.
Fэф.р- эффективный годовой фонд рабочего времени одного рабочего, ч. принимаем Fэф.р= 1860ч.
Исходные данные для расчета производственных рабочих таблицы: 2,3,4.
Количество станков дублеров,которые может обслуживать один рабочий, определяется по формуле:
Sм£ t м. авт. +1
tруч.
В том числе
Принятое Спр
Проверяем возможность многостаночного обслуживания на операциях: 005,010,025, так как на этих операциях принято более 1 станка.
Sм=252 /108 +1=3,3 Sм=6
Sм= 126/54 +1=3,3 Sм=3
Sм= 126/54 +1=3,3 Sм=3
Sм=210 /90 +1=3,3 Sм=4
Численность производственных рабочих на участке составит:
Р005= 360,04*9480/1860* 6 *60=5,09 Рпр=6
Р010= 180,05*9480/1860* 3 *60=5,1 Рпр=6
Р015= 180,05*9480/1860* 3 *60=5,1 Рпр=6
Р020= 300,04*9480/1860* 4 *60=6,37 Рпр=7
S Р. рас.=25чел
б) расчет численности вспомогательных рабочих.
Количество вспомогательных рабочих принимается укрупнено в процентном отношении от количества производственных рабочих, по рабочим местам, по нормам обслуживания. Принимаем численность вспомогательных рабочих равную15%от численности производственных рабочих.
Рвсп=25*0,15=3,75 принимаем Рвсп=4 чел.
Наладчик оборудования 6 разряда – 2 чел.
Слесарь по ремонту оборудования 5 разряда – 2чел.
В)Расчет численности ИТР и МОП.
В соответствии с нормативами численности ИТР на участке, где работает 14 человек не подходит.
Численность МОП не включается в план участка, так как к ним относятся профессии: дворник, садовник, гардеробщик и др.
Табл. 5 сводная ведомость списочного состава работающих на участке.
Категория работающих | Количество работающих | В % от производственных рабочих | В % от общего количества рабочих | |||
Всего | По сменам | |||||
1 | 2 | |||||
Производственные рабочие | 25 | 13 | 12 | __________ | 86,3 | |
Вспомогательные рабочие | 4 | 2 | 2 | 16 | 13,7 | |
Всего | 29 | 15 | 14 | 100 | ||
1.4.расчет площади участка и стоимости здания.
Общая площадь участка (Роб)стоимость из производственной (Рпр) и вспомогательной (Рвсп) площади.
Роб=Рпр+Рвсп
Производственная площадь занята основными рабочими местами, проходами, проездами.
Рпр=S1n(Р1+Р2)*Спр
Заключение.
Служебное назначение шпинделя и принцип работы.
Шпиндельный узел токарного автомата и полуавтомата предназначен для вращения заготовки и передачи на нее крутящего момента, необходимого для осуществления процесса резания. Этот узел является самым ответственным в автоматах и полуавтоматах, определяющим точность и чистоту обработки. В качестве опор шпинделей в большинстве автоматов и полуавтоматов применя-ются точные подшипники качения. В некоторых моделях применяются под-шипники скольжения. Шпиндельная бабка полуавтомата представлена на рис 1.
В автоматах продольного точения главный шпиндель 11 смонтирован в шпиндельной бабке, перемещающейся в продольном направлении. Шпиндель установлен на 2 – х опорах. Передней опорой служит игольчатый подшипник ка-чения 16. Задней опорой являются 2 радиально – упорных шарикоподшипника 8. Зазор в подшипнике передней опоры регулируют затягиванием гайки 15 и контролируют индикатором, установленным так, чтобы его измерительный штифт касался цилиндрической поверхности переднего конца шпинделя (при снятом колпачке 1). После регулировки гайку 15 фиксируют стопором 4 с винтом 3. Зазор в шарикоподшипниках задней опоры регулируют поворотом лимба 9.
Приводной шкив 7 установлен непосредственно на шпинделе автомата. В отверстии передней части шпинделя установлена конусная втулка 17, в которую вставлена пружина 2 и сменная зажимная цанга. Пружина 2, сжатая при завин-чивании гайки 18 между торцом зажимной цанги и внутренним буртиком конусной втулки, бедет постоянно двигать конусную втулку вправо, разжимая цангу и освобождая пруток. При перемещении конусной втулки влево цанга освобождает пруток.
В средней части шпинделя прорезаны два продольных паза, в которые вставлены два кулачка 13. При повороте рачага – вилки 14 стакан 5 с шарико – подшипником перемещает конусную втулку 6. Последняя при этом раздвигает длинные плечи кулачков 13, которые поворачиваясь вокруг оси 12, короткими плечами призводят зажим цанги. При отходе конусной втулки 6 длинные плечи кулачков 13 под действием пружины 2 сходятся, а цанга разжимается. Усилие зажима цанги регулируют гайкой 10.
Подачи прутка для обработки в автоматах продольного точения как таковой нет. Пруток в них подается вперед вместе с шпиндельной бабкой в процессе обработки заготовки. Поэтому после отрезки готовой детали пруток остается на месте, цанга разжимается и вместе со шпиндельной бабкой быстро отходит назад.
![]() |
Рис.1.1. Шпиндельная бабка
Анализ технических условий.
1. Термообработка всех поверхностей, кроме резьб HRC 40 – 45.
2. Поверхность Ф38h5 служит для установки игольчатого подшипника качения, что обуславливает допуск отклонения формы – отклонение от цилиндричности составляет 0,016 мм.
3. Поверхности Ф30 –0,006 Ф35 h6 служат для установки двух радиально – упорных подшипников, что также объясняет жесткий допуск на размер и отклонение формы, в данном случае – отклонение от цилиндричности 0,016 мм.
4. Несоосность поверхности А и Б относительно их общей оси не более 0,005 мм, что вызвано тем, что на поверхности А (резьба М30х1,5 – 6g) устанавливается гайка, которой регулируется усилие зажима цанги, находящейся на поверхности Б.
|
|
Особенности сооружения опор в сложных условиях: Сооружение ВЛ в районах с суровыми климатическими и тяжелыми геологическими условиями...
Кормораздатчик мобильный электрифицированный: схема и процесс работы устройства...
Состав сооружений: решетки и песколовки: Решетки – это первое устройство в схеме очистных сооружений. Они представляют...
Папиллярные узоры пальцев рук - маркер спортивных способностей: дерматоглифические признаки формируются на 3-5 месяце беременности, не изменяются в течение жизни...
© cyberpedia.su 2017-2024 - Не является автором материалов. Исключительное право сохранено за автором текста.
Если вы не хотите, чтобы данный материал был у нас на сайте, перейдите по ссылке: Нарушение авторских прав. Мы поможем в написании вашей работы!