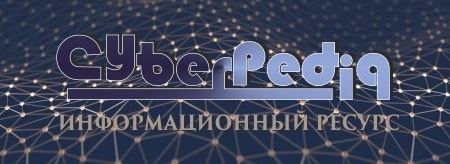
Кормораздатчик мобильный электрифицированный: схема и процесс работы устройства...
Историки об Елизавете Петровне: Елизавета попала между двумя встречными культурными течениями, воспитывалась среди новых европейских веяний и преданий...
Топ:
Особенности труда и отдыха в условиях низких температур: К работам при низких температурах на открытом воздухе и в не отапливаемых помещениях допускаются лица не моложе 18 лет, прошедшие...
Устройство и оснащение процедурного кабинета: Решающая роль в обеспечении правильного лечения пациентов отводится процедурной медсестре...
Эволюция кровеносной системы позвоночных животных: Биологическая эволюция – необратимый процесс исторического развития живой природы...
Интересное:
Подходы к решению темы фильма: Существует три основных типа исторического фильма, имеющих между собой много общего...
Национальное богатство страны и его составляющие: для оценки элементов национального богатства используются...
Принципы управления денежными потоками: одним из методов контроля за состоянием денежной наличности является...
Дисциплины:
![]() |
![]() |
5.00
из
|
Заказать работу |
|
|
Методические указаниЯ
к лабораторным работам № 4…6
по дисциплине «Теория резания»
для студентов направления 6.09.02 "Инженерная механика"
Всех форм обучения
Часть 2
Севастополь
УДК 621.001
Теория резания. Методические указания к лабораторным работам. Часть 2 /Разраб. С.М. Братан, Д.Е. Сидоров. – Севастополь: Изд-во СевНТУ, 2007. – 36с.
Целью методических указаний является оказание помощи студентам при выполнении лабораторных работ.
Методические указания предназначены для студентов направления “Инженерная механика” всех форм обучения.
Методические указания утверждены на заседании кафедры "Технологии машиностроения" протокол №2 от 10 октября 2006 г.
Допущено учебно-методическим центром и научно-методическим советом СевНТУ в качестве методических указаний.
Рецензент: А.В. Троценко, канд. техн. наук, доцент каф. “Технологии машиностроения”.
Ответственный за выпуск: Ю.К. Новоселов, зав. каф. “Технологии машиностроения”, доктор техн. наук.
Содержание
1. | Лабораторная работа №4. Исследование деформации металла и процесса образования стружки при точении………….………….……………. | |
2. | Лабораторная работа №5. Нарост и налипы при точении………….…………. | |
3. | Лабораторная работа №6. Влияние элементов процесса резания на температуру резания …………………………………………………………. | |
Библиографический список………….………….………….………….………… |
ЛАБОРАТОРНАЯ РАБОТА № 4
ИССЛЕДОВАНИЕ ДЕФОРМАЦИИ МЕТАЛЛА И ПРОЦЕССА ОБРАЗОВАНИЯ стружки при точении
(Продолжительность выполнения – 4 часа)
Цель работы: Исследование деформации металла и процесса образования стружки при точении.
|
ОБЩИЕ СВЕДЕНИЯ
4.1.1. Описание стружкообразования
Резец, действуя передней поверхностью на срезаемый слой, деформирует его, вследствие чего возникают упругие, а затем пластические деформации, после чего при определенных условиях может иметь место отделение деформированного элемента слоя (стружки) от остальной массы металла.
На характер получающихся стружек влияет качество обрабатываемого металла, параметры резания, геометрические параметры инструмента и свойства смазывающе-охлаждающей жидкости.
На рисунке 4.1 дана микрофотографиястальной стружки, из которой видно, что по сравнению с зернами основной массы металла зерна стружки сильно деформированы в направлении плоскостей скольжения под углом .
![]() |
Рисунок 4.1 – Микрофотографиястальной стружки |
Применив впервые к исследованию процесса резания металлографический метод (1912 — 1914 г.), Я. Г. Усачев показал, что микроструктура стружки отлична от микроструктуры основной массы обрабатываемого металла и что в самой стружке имеются плоскости скольжения (рисунок 4.2), не совпадающие по направлению с направлением поверхности сдвига
. Позднее (1929 г.) проф. А.М. Розенберг показал, что углы
и
увеличиваются с увеличением толщины среза и уменьшением угла резания, и что разность между углами
и
константа, которая приблизительно равна 18° — 20°.
В зависимости от условий обработки срезанный слой (стружка) может иметь тот или иной вид. Так, при обработке пластичных металлов (сталей) имеют место три основных типа стружек – элементная, суставчатая и сливная, а при обработке малопластичных металлов – стружка надлома.
Элементная стружка (рисунок 4.2)получается при обработке твердых и маловязких металлов с малой скоростью резания. Она состоит из отдельных пластически деформированных элементов, слабо связанных или вовсе не связанных между собой.
Образование таких элементов стружки было наглядно показано еще проф. И.А.Тиме, положившим начало научному исследованию процесса стружкообразования (1868 — 1870 гг.).
|
Суставчатая стружка (рисунок 4.3)получается при обработке сталей со средней скоростью резания. Надрезцовая сторона такой стружки гадкая, а противоположная сторона имеет зазубрины с выраженным направлением отдельных, прочно связанных между собой, элементов.
Сливная стружка (рисунок 4.4) получается при обработке материалов с высокой скоростью резания. Она сходит с резца в виде ленты, без зазубрин, присущих суставчатой стружке.
Чем больше скорость резания,вязкость обрабатываемого металла, меньше угол резания и толщина среза, и выше поверхностная активность смазочно-охлаждающей жидкости, тем стружка ближе к сливной.
При обработке малопластичных металлов (твердый чугун, твердая бронза) получается так называемая стружка надлома (рисунок 4.5), состоящая из отдельных, как бы вырванных, элементов, разнообразных по форме и не связанных или очень слабо связанных между собой. Опережающая трещина при образовании стружки надлома распространяется сразу вдоль всей поверхности сдвига, по которой она отделяется от основной массы металла. Такая «сыпучая» стружка пластически мало деформирована, она создает резко неравномерную нагрузку на систему станок – резец – заготовка – приспособление. Обработанная поверхность при такой стружке получается шероховатой, с большими впадинами и выступами. Будучи слабо связанными между собой элементы стружки надлома имеют малое относительное перемещение по передней поверхности резца.
Кроме указанных типов стружек, при обработке сталей могут образовываться и промежуточные виды стружки.
![]() |
![]() |
Рисунок 4.2 – Элементная стружка |
![]() |
![]() |
Рисунок 4.3 – Суставчатая стружка |
![]() |
![]() |
Рисунок 4.4 – Сливная стружка |
![]() |
![]() |
Рисунок 4.5 – Стружка надлома |
Порядок выполнения работы
1. Измерить углы резца: ,
,
;
2. Измерить размеры обрабатываемой детали (диаметр при точении,
при строгании).
3. Выбрать параметры резания (режимы резания).
Для точения рассчитать:
• скорость резания , м/мин [1]
,
где – частота вращения шпинделя, об/мин;
– наибольший диаметр в мм поверхности резания.
|
• скорость подачи (подача) , мм/мин
,
где – подача инструмента в мм/об заготовки.
• глубину резания , мм
.
• толщину срезаемого слоя , мм
.
• ширину срезаемого слоя , мм
,
где – главный угол в плане;
– угол наклона главной режущей кромки.
Для строгания рассчитать:
• скорость резания , м/мин
,
где – число двойных ходов в минуту;
– длина хода стола (ползуна) в мм;
– отношение скорости рабочего хода к скорости холостого хода (дается в паспорте на станок;
= 0,75).
• скорость подачи (подача) , мм/мин
,
где – подача в мм двойной ход.
• глубину резания , мм
.
4. Данные занести в таблицу 4.1.
Таблица 4.1
№ п/п | Режим резания | Данные резца | Данные детали | Рассчитанные данные | |||||||||||
Строгание | |||||||||||||||
![]() | ![]() | ![]() | ![]() | ![]() | ![]() | ![]() | ![]() | ![]() | ![]() | ![]() | ![]() | ![]() | |||
Точение | |||||||||||||||
![]() | ![]() | ![]() | ![]() | ![]() | ![]() | ![]() | ![]() | ![]() | ![]() | ![]() | ![]() | ||||
5. Пользуясь данными таблицы 4.1, определить коэффициенты усадки стружки:
а) приняв = const (число оборотов постоянное) при 4 разных подачах
,
,
,
определить коэффициенты усадки стружки, по методике, изложенной в разделе 4.1 (непосредственным измерением длины
пути резца и соответствующей ему длине стружки
);
б) приняв = const (подача постоянная) при числах оборотов
,
,
,
определить коэффициенты усадки стружки через оценку площадей сечений припуска
и сечения стружки
, путем ее взвешивания.
6. Рассчитать величину угла относительного сдвига .
7. Данные занести в таблицу 4.2.
8. Сделать выводы по работе.
Таблица 4.2
№ изм. | ![]() | ![]() | ![]() | ![]() | ![]() | ![]() | ![]() | ![]() |
1. | ![]() | |||||||
2. | ![]() | |||||||
3. | ![]() | |||||||
4. | ![]() |
4.4. Контрольные вопросы
1. Каков характер образования стружки?
2. При каких условиях образуется сливная стружка?
3. При каких условиях образуется стружка надлома?
|
4. При каких условиях образуется стружка скалывания?
5. Каков физический смысл коэффициентов усадки?
6. Назовите способы оценки усадки стружки.
7. Как влияет подача на коэффициент усадки?
8. Как изменяется коэффициент усадки с увеличением глубины резания?
ЛАБОРАТОРНАЯ РАБОТА № 5
НАРОСТ И НАЛИПЫ ПРИ ТОЧЕНИИ
(Продолжительность выполнения – 4 часа)
Цель работы:
1. Ознакомиться с наростообразованием и налипами во время резания, влиянием различных факторов на их образование;
2. Ознакомиться с приборами, используемыми для изучения и измерения нароста и налипов;
3. Получить навыки в проведении экспериментальных исследований с использованием приборов.
ОБЩИЕ СВЕДЕНИЯ
При некоторых условиях процесса резания на передней поверхности режущего инструмента при внедрении его в обрабатываемый материал образуется нарост, представляющий собой скопление частичек металла, спрессовавшегося под влиянием высокого давления и температуры. Нарост принимает различную форму и размеры в зависимости от обрабатываемого материала и условий резания, его можно видеть на передней поверхности режущего инструмента после прекращения резания (см. рисунки 5.1, 5.2).
![]() |
Рисунок 5.1 – Микроструктура нароста (застойной зоны) на лезвии резца |
![]() |
Рисунок 5.2 – Микроструктура нароста на вершине резца |
Нарост значительно тверже обрабатываемого материала (его твердость может в 2 – 3 раза превосходить твердость обрабатываемого материала). Он выполняет роль нового режущего лезвия, предохраняет основное лезвие от истирания.
Нарост не является стабильным и равномерным вдоль всей длины режущей кромки даже при условиях, особо благоприятных для его образования. Вследствие сильного трения между стружкой и наростом и трения в месте контакта нароста с обработанной поверхностью и поверхностью резания частицы нароста уносятся как стружкой, так и этими поверхностями. Потерянные объемы нароста восстанавливаются за счет притока новых частиц металла из основной его массы.
Являясь как бы продолжением резца, нарост изменяет его геометрию (угол резания при наросте меньше угла резания резца
, полученного при заточке), а потому, перемещаясь вместе с резцом, нарост оказывает влияние на деформацию срезаемого слоя на износ резца, на силы, действующие на резец, и на качество обработанной поверхности (рисунок 5.3).
Однако при чистовой обработке, когда необходимо получить высокое качество обработанной поверхности, нарост является вредным, так как частицы его, срываясь под действием сил трения и прилипая к обработанной поверхности, увеличивает шероховатость обработанной поверхности.
Образование нароста сопровождается ухудшением обработанной поверхности, вследствие того, что, образовавшись, нарост растет до определенных величин ,
,
, затем разрушается и уносится стружкой или остается в виде налипов на обработанной поверхности.
|
При работе многолезвийного инструмента нарост, образуясь на одном из лезвий, вызывает его перегрузку, при этом другие лезвия (на соответствующих участках) работают частично, либо вообще не работают. Неравномерность нагрузки многолезвийного инструмента приводит к неточности его работы и более быстрому затуплению перегруженного лезвия.
Поэтому явлению наростообразования при резании уделяется большое внимание.
На величину и область распространения нароста оказывают влияние следующие факторы:
1. Свойства обрабатываемого материала.
К наростообразованию склонныконструкционные, углеродистые и большинство легированных сталей, серый чугун, алюминиевые сплавы.
Для этой группы размеры нароста и
возрастают с уменьшением твердости и повышением пластичности (рисунок 5.3). Величина нароста тем больше, чем больше свободного феррита и меньше углерода в стали.
Не склонны к наростообразованию медь и ее сплавы, олово, свинец, большинство титановых сплавов, белый чугун, закаленные стали, легированные стали с высоким содержанием хрома и никеля.
2. Состояние поверхностей и химическое сродство материалов инструмента и детали.
Например, нарост не образуется при обработке материалов инструментами, режущая часть которых снабжена металлокерамическими пластинами, и сверхтвердыми синтетическими материалами, обладающими малым сродством с обрабатываемыми материалами.
![]() |
Рисунок 5.3 – Нарост на резце |
3. Скорость резания.
При малых скоростях, когда деформация незначительна, нароста нет. Например, для среднеуглеродистых сталей (рисунок 5.4) зона 1, где нарост еще не образуется, соответствует скоростям 1 – 2
м/мин. В зоне 2, по мере возрастания температуры резания, нарост появляется и растет, достигая максимальных значений при температуре примерно 300 – 500°С, что соответствуем скоростям резания 15 – 30 м/мин. Именно в том диапазоне, при максимальном значении нароста, наблюдается и минимальное значение усадки.
В зоне 3 по мере прекращения заторможенного слоя в текущей уменьшается сила адгезии нароста к передней поверхности, а также снижается сопротивление нароста пластичному сдвигу. Величина на роста уменьшается и при температуре 580 – 600°С, что соответствует скоростям 80 – 100 м/мин.
![]() |
![]() |
Рисунок 6.4 |
4. Передний угол .
При уменьшении угла увеличивается тепловыделение, и значение температур, где нарост имеет максимальное значение и где он исчезает, достигается при малых скоростях. В результате кривая "высота нароста – скорость" (рисунок 5.4) сдвигается влево. Одновременно снижается угол сдвига, возрастает деформация, и нарост увеличивается по высоте. При увеличении угла нарост снижается и при более 40 – 46° полностью исчезает.
5. Толщина среза.
Увеличение толщины среза влияет аналогично уменьшению переднего угла. Поскольку с увеличением толщины температура, соответствующая максимуму усадки, достигается при меньших скоростях, кривая также смещается влево.
Менее упрочненная стружка активнее налипает на переднюю поверхность, вызывая увеличение нароста.
Таким образом, максимальные значения нароста при меньших скоростях имеют место при увеличении пластичности материала, уменьшении переднего угла, увеличении толщины среза. Для каждого обрабатываемого материала существуют зоны I и III, где нарост не существует. Это может быть как при достаточно больших толщинах и малых передних углах, так и достаточно больших передних углах и очень малых толщинах.
Порядок выполнения работы
1. Ознакомиться с основными понятиями, связанными с наростом.
2. Ознакомиться с оборудованием, инструментам и приборами, использованными при работе.
3. Измерить нарост с помощью микроскопа (лупы с измерительной шкалой) после обработки заготовок из различных материалов и при различных режимах резания.
4. По полученным данным построить графические зависимости нароста от различных факторов.
5. Оформление отчета.
СОДЕРЖАНИЕ ОТЧЕТА
Отчет должен содержать:
1. Таблицу исходных данных и результатов измерений.
2. Графики зависимостей нароста от различных факторов.
3. Выводы по работе.
КОНТРОЛЬНЫЕ ВОПРОСЫ
1. Что такое нарост?
2. Что влияет на появление нароста?
3. Как влияет нарост на процесс обработки и качество обрабатываемой заготовки?
4. Как влияют на наростообразование материал заготовки, материал инструмента, скорость резания, подача (толщина среза), передний угол, применение СОЖ?
5. Как влияют на наростообразование скорость резания, подача (толщина среза), СОЖ?
6. Как влияют на наростообразование геометрия инструмента?
ЛАБОРАТОРНАЯ РАБОТА № 6
Общие сведения
ПОРЯДОК ВЫПОЛНЕНИЯ РАБОТЫ
1. Изучить основные закономерности, характеризующие влияние элементов процесса резания (,
,
) на температуру резания.
2. Ознакомиться с методами измерения температуры.
3. Ознакомиться с аппаратурой и оборудованием, применяемыми при исследованиях. Сделать эскиз естественной термопары.
4. Провести эксперименты, необходимые для раскрытия изучаемых закономерностей.
4.1. В первом эксперименте снимаются четыре показания миллиамперметра при const и
const.
Скорости резания вычисляются по формуле [1]
,
где – диаметр обрабатываемой поверхности, мм;
– рабочая частота вращения, об/мин;
– номер опыта.
Затем в логарифмической системе координат строится график зависимости тангенсу угла наклона которого определяется показатель степени
.
4.2. Во втором эксперименте снимаются четыре показания миллиамперметра при const и
const. В логарифмической системе координат строится график зависимости
, по тангенсу угла наклона которого определяется показатель степени
.
4.3. В третьем опыте снимаются четыре показания миллиамперметра при const и
const. Строится график зависимости
, no тангенсу угла наклона которого определяется показатель степени
.
5. Обработать экспериментальные данные путем перевода показаний в мВ в °С; используя тарировочный график 5. Результаты внести в протокол.
6. Определить численное значение . Записать уравнение (6.3) в раскрытом виде.
Протокол лабораторной работы №___
«Влияние элементов процесса резания на температуру резания»
Станок______________ Обрабатываемый материал______________
Номер опыта | Резец | Углы резца, град | Материал резца | Диаметр заготовки, D, мм | Скорость вращения, n, об/мин | Скорость резания v, м/мин | Глубина резания t, мм | Подача s, мм/об | Показания милливольтметра, мВ | Значение температуры, θ °С | Примечание | |||
![]() | ![]() | ![]() | ![]() | |||||||||||
Θ1=f(v) | ||||||||||||||
Θ2=f(v) | ||||||||||||||
Θ3=f(v) | ||||||||||||||
6.4. Контрольные вопросы
1. Как зависит температура резания от скорости, подачи и глубины резания?
2. Какие существуют методы измерения температуры в зоне резания?
3. Чем отличается метод измерения температуры резца искусственной термопарой от метода измерения температуры резца полуискусственной термопарой?
БИБЛИОГРАФИЧЕСКИЙ СПИСОК
1. Справочник технолога-машиностроителя. В 2-х т. /Под ред. А.Г.Косиловой и Р.К. Мещерякова. – 6-е изд., перераб. и доп. – М.: Машиностроение, 2003. – Т.2. – 496с.
2. Бобров B.Ф. Основа теории резания металлов / B.Ф. Бобров. – М.: Машиностроение, 1975. – 344с.
3. Аршинов А.В. Резание металлов и режущий инструмент / А.В.Аршинов, Г.А. Алексеев. – М.: Машиностроение, 1976. – 440с.
Заказ №__________от «___»___________200_____. Тираж_________экз.
Изд-во СевНТУ
Методические указаниЯ
к лабораторным работам № 4…6
по дисциплине «Теория резания»
для студентов направления 6.09.02 "Инженерная механика"
Всех форм обучения
Часть 2
Севастополь
УДК 621.001
Теория резания. Методические указания к лабораторным работам. Часть 2 /Разраб. С.М. Братан, Д.Е. Сидоров. – Севастополь: Изд-во СевНТУ, 2007. – 36с.
Целью методических указаний является оказание помощи студентам при выполнении лабораторных работ.
Методические указания предназначены для студентов направления “Инженерная механика” всех форм обучения.
Методические указания утверждены на заседании кафедры "Технологии машиностроения" протокол №2 от 10 октября 2006 г.
Допущено учебно-методическим центром и научно-методическим советом СевНТУ в качестве методических указаний.
Рецензент: А.В. Троценко, канд. техн. наук, доцент каф. “Технологии машиностроения”.
Ответственный за выпуск: Ю.К. Новоселов, зав. каф. “Технологии машиностроения”, доктор техн. наук.
Содержание
1. | Лабораторная работа №4. Исследование деформации металла и процесса образования стружки при точении………….………….……………. | |
2. | Лабораторная работа №5. Нарост и налипы при точении………….…………. | |
3. | Лабораторная работа №6. Влияние элементов процесса резания на температуру резания …………………………………………………………. | |
Библиографический список………….………….………….………….………… |
ЛАБОРАТОРНАЯ РАБОТА № 4
ИССЛЕДОВАНИЕ ДЕФОРМАЦИИ МЕТАЛЛА И ПРОЦЕССА ОБРАЗОВАНИЯ стружки при точении
(Продолжительность выполнения – 4 часа)
Цель работы: Исследование деформации металла и процесса образования стружки при точении.
ОБЩИЕ СВЕДЕНИЯ
4.1.1. Описание стружкообразования
Резец, действуя передней поверхностью на срезаемый слой, деформирует его, вследствие чего возникают упругие, а затем пластические деформации, после чего при определенных условиях может иметь место отделение деформированного элемента слоя (стружки) от остальной массы металла.
На характер получающихся стружек влияет качество обрабатываемого металла, параметры резания, геометрические параметры инструмента и свойства смазывающе-охлаждающей жидкости.
На рисунке 4.1 дана микрофотографиястальной стружки, из которой видно, что по сравнению с зернами основной массы металла зерна стружки сильно деформированы в направлении плоскостей скольжения под углом .
![]() |
Рисунок 4.1 – Микрофотографиястальной стружки |
Применив впервые к исследованию процесса резания металлографический метод (1912 — 1914 г.), Я. Г. Усачев показал, что микроструктура стружки отлична от микроструктуры основной массы обрабатываемого металла и что в самой стружке имеются плоскости скольжения (рисунок 4.2), не совпадающие по направлению с направлением поверхности сдвига
. Позднее (1929 г.) проф. А.М. Розенберг показал, что углы
и
увеличиваются с увеличением толщины среза и уменьшением угла резания, и что разность между углами
и
константа, которая приблизительно равна 18° — 20°.
В зависимости от условий обработки срезанный слой (стружка) может иметь тот или иной вид. Так, при обработке пластичных металлов (сталей) имеют место три основных типа стружек – элементная, суставчатая и сливная, а при обработке малопластичных металлов – стружка надлома.
Элементная стружка (рисунок 4.2)получается при обработке твердых и маловязких металлов с малой скоростью резания. Она состоит из отдельных пластически деформированных элементов, слабо связанных или вовсе не связанных между собой.
Образование таких элементов стружки было наглядно показано еще проф. И.А.Тиме, положившим начало научному исследованию процесса стружкообразования (1868 — 1870 гг.).
Суставчатая стружка (рисунок 4.3)получается при обработке сталей со средней скоростью резания. Надрезцовая сторона такой стружки гадкая, а противоположная сторона имеет зазубрины с выраженным направлением отдельных, прочно связанных между собой, элементов.
Сливная стружка (рисунок 4.4) получается при обработке материалов с высокой скоростью резания. Она сходит с резца в виде ленты, без зазубрин, присущих суставчатой стружке.
Чем больше скорость резания,вязкость обрабатываемого металла, меньше угол резания и толщина среза, и выше поверхностная активность смазочно-охлаждающей жидкости, тем стружка ближе к сливной.
При обработке малопластичных металлов (твердый чугун, твердая бронза) получается так называемая стружка надлома (рисунок 4.5), состоящая из отдельных, как бы вырванных, элементов, разнообразных по форме и не связанных или очень слабо связанных между собой. Опережающая трещина при образовании стружки надлома распространяется сразу вдоль всей поверхности сдвига, по которой она отделяется от основной массы металла. Такая «сыпучая» стружка пластически мало деформирована, она создает резко неравномерную нагрузку на систему станок – резец – заготовка – приспособление. Обработанная поверхность при такой стружке получается шероховатой, с большими впадинами и выступами. Будучи слабо связанными между собой элементы стружки надлома имеют малое относительное перемещение по передней поверхности резца.
Кроме указанных типов стружек, при обработке сталей могут образовываться и промежуточные виды стружки.
![]() |
![]() |
Рисунок 4.2 – Элементная стружка |
![]() |
![]() |
Рисунок 4.3 – Суставчатая стружка |
![]() |
![]() |
Рисунок 4.4 – Сливная стружка |
![]() |
![]() |
Рисунок 4.5 – Стружка надлома |
Процесс пластической деформации в стружке
При превращении срезаемого слоя в стружку размеры стружки по длине, толщине и ширине (рисунок 4.6) отличаются от размеров срезаемого слоя.
![]() |
Рисунок 4.6 – Размеры срезаемого слоя и стружки |
При длине срезаемого слоя , толщине
и ширине
соответственно длина стружки равна
, толщина –
, а ширина –
, причем
;
Эмиссия газов от очистных сооружений канализации: В последние годы внимание мирового сообщества сосредоточено на экологических проблемах...
История развития пистолетов-пулеметов: Предпосылкой для возникновения пистолетов-пулеметов послужила давняя тенденция тяготения винтовок...
Таксономические единицы (категории) растений: Каждая система классификации состоит из определённых соподчиненных друг другу...
Общие условия выбора системы дренажа: Система дренажа выбирается в зависимости от характера защищаемого...
© cyberpedia.su 2017-2024 - Не является автором материалов. Исключительное право сохранено за автором текста.
Если вы не хотите, чтобы данный материал был у нас на сайте, перейдите по ссылке: Нарушение авторских прав. Мы поможем в написании вашей работы!