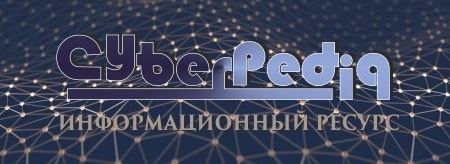
Историки об Елизавете Петровне: Елизавета попала между двумя встречными культурными течениями, воспитывалась среди новых европейских веяний и преданий...
Своеобразие русской архитектуры: Основной материал – дерево – быстрота постройки, но недолговечность и необходимость деления...
Топ:
Оснащения врачебно-сестринской бригады.
Проблема типологии научных революций: Глобальные научные революции и типы научной рациональности...
Отражение на счетах бухгалтерского учета процесса приобретения: Процесс заготовления представляет систему экономических событий, включающих приобретение организацией у поставщиков сырья...
Интересное:
Что нужно делать при лейкемии: Прежде всего, необходимо выяснить, не страдаете ли вы каким-либо душевным недугом...
Отражение на счетах бухгалтерского учета процесса приобретения: Процесс заготовления представляет систему экономических событий, включающих приобретение организацией у поставщиков сырья...
Инженерная защита территорий, зданий и сооружений от опасных геологических процессов: Изучение оползневых явлений, оценка устойчивости склонов и проектирование противооползневых сооружений — актуальнейшие задачи, стоящие перед отечественными...
Дисциплины:
![]() |
![]() |
5.00
из
|
Заказать работу |
|
|
Примером безотходной технологии является изготовление деталей из порошковых материалов. Ознакомьтесь с технологией получения порошков исходных материалов, изготовлением из них деталей. Уясните их преимущества и недостатки, применение в машиностроении. Разберитесь с классификацией и маркировкой порошковых сплавов но ГОСТ.
Вопросы для самопроверки
1. В чем заключается сущность технологии изготовления деталей из порошковых сплавов?
2. Какие порошковые сплавы нашли применение для изготовления деталей машин?
Неметаллические материалы
Изучение этого подраздела нужно начинать с повторения соответствующих разделов курса органической химии. Необходимо знать строение и свойства полимерных материалов. Разобраться с классификацией полимеров и особенностями свойств полимерных материалов. Знать основные термореактивные и термопластичные полимерные смолы и пластические массы на их основе. Разобрать состав, классификацию и физико-механические свойства резин. Познакомиться с основными методами переработки пластмасс и резины в изделия и технико-экономической эффективностью их применения в автотракторном и сельхозмашиностроении.
Вопросы для самопроверки
1. Какие термореактивные и термопластичные пластмассы нашли применение в автотракторном и сельскохозяйственном машиностроении?
2. Какими основными методами получают детали из пластмасс и резины?
2.2 МОДУЛЬ 2 - ГОРЯЧАЯ ОБРАБОТКА МЕТАЛЛОВ
Введение
Материал этого раздела посвящен рассмотрению методов получения конкретных деталей, конструкций и полуфабрикатов литьем, обработкой давлением и сваркой. Познакомьтесь с историей развития этих методов, вкладом русских и советских ученых и производственников в совершенствование процессов литья, обработки давлением и сварки.
|
Литейное производство
Литье является одним из древних методов получения конкретных деталей машин из металлов, который в наше время получил большое развитие. Уясните значение литейного производства для сельскохозяйственного машиностроения и тракторостроения.
Изучение начните с рассмотрения общей схемы технологического процесса получения отливки. Затем разберитесь с каждой частью этого процесса подробнее. Изучите литейные сплавы и теоретические основы литейного производства отливок, изготовление отливок в песчано-глинистых формах, заострив внимание на модельном комплекте, формовочных и стержневых смесях, литниковых системах и технологии изготовления литейной формы. Познакомьтесь с машинной формовкой механизацией и автоматизацией изготовления литейных форм.
Все большее применение при массовом производстве находят такие прогрессивные способы литья, как литье в металлические формы, центробежное литье, литье под давлением, оболочковое литье, литье по выплавляемым моделям. Уясните схемы технологий получения отливок этими методами, их преимущества и недостатки.
Изучите особенности изготовления отливок из различных сплавов; чугуна (серого, высокопрочного, ковкого), стали, алюминиевых, магниевых и медных сплавов. Обратите при этом внимание па литейные свойства этих сплавов (температура плавления и заливки, жидкотекучесть, усадка), способы плавления их и материалы для шихтовки, заливку сплавом форм, особенности литниковой системы.
Познакомьтесь с технологичностью конструкций литых деталей, основой их конструирования, дефектами литья, причинами их возникновения и методами исправления.
Уясните основные вопросы техники безопасности в литейных цехах.
Вопросы для самопроверки
1. Из каких элементов состоит схема технологического процесса изготовления отливки?
|
2. Какие требования предъявляются к формовочным и стержневым материалам, какие материалы отвечают этим требованиям?
3. В чем сущность получения отливок в металлические, и оболочковые формы, центробежного литья, литья по выплавляемым моделям, под давлением?
2.2.1 Обработка металлов давлением
Обработка давлением широко применяется при изготовлении и ремонте деталей тракторов, автомобилей и сельскохозяйственных машин Изучение этого очень важного подраздела следует начать с рассмотрения теоретических основ обработки давлением Необходимо хорошо усвоить понятие физической природы упругой и пластической деформации, влияние обработки давлением на структуру и свойства металлов. Повторить часть первого раздела по пластической деформации и рекристаллизации.
Изучая процессы, происходящие в металле при нагреве, уясните сущность явлений пережога, перегрева, обезуглероживания, угара и способы их предотвращения. Научитесь определять температурный интервал горячей обработки давлением углеродистых сталей и обосновывать этот выбор. Познакомьтесь с печами и устройствами, применяемыми для нагрева заготовок.
Сначала уясните сущность процесса продольной прокатки как наиболее распространенной. Уясните, благодаря чему и как происходит захват заготовки валками, как происходит деформация металла в валках. Ознакомьтесь с устройством прокатного стана, схемами расположения рабочих клетей. Рассмотрите поперечную и поперечно-винтовую прокатку. Необходимо запомнить названия и назначение прокатных станов для проката различных заготовок, последовательность выполнения операций прокатки разных видов продукции, знать основные сортовые профили, некоторые специальные виды проката и их применение в сельхозмашиностроении.
При рассмотрении процесса волочения поймите его сущность, возможности. Разберите различные схемы волочения для получения большого разнообразия продуктов волочения. Уясните весь технологический процесс волочения в целом, обратите внимание на предварительную подготовку заготовки перед волочением. Познакомьтесь с продукцией волочильного производства и ее применением. Приступая к изучению процесса прессования, вникните в его сущность и широкие возможности применения благодаря увеличению пластичности металла за счет его всестороннего неравномерного сжатия. Познакомьтесь с различными схемами прессования, продукцией и областью ее применения.
|
Изучение процесса свободной ковки начните с рассмотрения основных операций ковки. При этом обратите внимание на процессы, протекающие в очаге деформации, изменение микроструктуры и свойств обрабатываемого металла. Изучите применяемое при ковке оборудование. Познакомьтесь с последовательностью и методикой разработки технологического процесса: разработкой чертежа поковки, расчетом размеров заготовки, выбором оборудования, последовательностью операций ковки, технологическими требованиями к деталям.
Перейдя к изучению объемной штамповки, поймите ее отличие, преимущества и недостатки перед свободной ковкой. Разберитесь с разновидностями объемной штамповки: горячей и холодной, в открытых и закрытых штампах. Познакомьтесь с технологией одноручьевой, многоручьевой и раздельной штамповки на молотах, применяемыми инструментом и оборудованием. Поймите сущность холодной высадки.
Разберитесь с технологией листовой штамповки.
Изучение технологий обработки давлением закрепите рассмотрением изготовления поковки конкретной детали
Рассмотрите основные вопросы по технике безопасности при обработке металлов давлением.
Вопросы для самопроверки
1. Чем обусловливается выбор температурного режима горячей обработки давлением?
2. Чем отличается структура и свойства литого металла от кованого?
3. В чем сущность технологий ковки, прокатки, волочения, прессования, объемной и листовой штамповки?
2.2.3 Сварка металлов
Изучение материала рекомендуется начинать с рассмотрения общих сведений о сварке как о технологическом процессе, в результате которого достигается неразъемное соединение вследствие образования межатомных связей между соединяемыми деталями. При этом следует обратить внимание на преимущества сварки по сравнению с другими видами соединений металлов.
Приступая к изучению классификации способов сварки, следует уяснить, что сближение атомов может быть достигнуто путем пластического деформирования (в холодном или нагретом состоянии) или расплавлением соединяемых кромок, что и определяет физическую сущность сварки давлением и сварки плавлением. Необходимо также уяснить, как сварочные процессы при сварке плавлением классифицируются по виду энергии, применяемой для нагревания металла. Следует разобраться, почему однородные металлы хорошо свариваются, а разнородные плохо, какие надо принимать меры для улучшения свариваемости.
|
Необходимо знать роль русских (Н. Н. Бенардос, Н. Г.Славянов) и советских (Е. О. Патон и др.) ученых в развитии сварочного производства.
Прежде чем приступить к изучению отдельных видов сварки, надо четко уяснить сварочные свойства электрической дуги, а затем рассмотреть способы ручной дуговой сварки, полуавтоматической и автоматической сварки плавлением: сварку под флюсом, сварку в среде защитных газов, электрошлаковую сварку, плазменную сварку и др. При этом необходимо уяснить сущность каждого способа сварки, применяемого оборудования и сварочных материалов, а также изучить их технологические возможности и область применения.
При изучении газовой сварки рекомендуется, в первую очередь, рассмотреть получение и строение отдельных видов сварочного ацетиленокислородного пламени, способы получения и хранения ацетилена и кислорода, после чего приступить к изучению способов сварки, процессов, протекающих при газовой сварке, устройства и работы оборудования; указать технологические возможности и область применения газовой сварки.
При изучении огневой резки металлов следует уяснить сущность способов резки металлов: кислородной, кислородо-флюсовой, плазменной, воздушно-дуговой. Изучить технологические особенности каждого способа резки и применяемую аппаратуру.
Изучение способов сварки давлением следует начинать с рассмотрения трех основных разновидностей контактной сварки: стыковой, точечной и шовной. Следует усвоить физическую сущность, устройство и электрические схемы каждого вида контактной сварки, разобраться в основах их технологии. При этом надо уяснить, что общим для всех видов контактной сварки является то, что металл в зоне контакта двух свариваемых элементов при прохождении электрического тока достаточно большой силы нагревается в одних случаях до пластического состояния, в других — до температуры плавления, после чего производится сжатие.
Следует также уделить внимание изучению новых способов сварки давлением: диффузионной в вакууме, ультразвуковой, трением. Нужно четко уяснить сущность и технологические особенности каждого из этих способов сварки, область их применения.
|
Изучите особенности кристаллизации сварного шва. Возникновение деформаций и напряжений в сварных деталях. Классификация материалов по их свариваемости.
Сварка конструкционных сталей: углеродистых, низколегированных и легированных. Понятие о сварке высоколегированных сталей, чугуна, меди, алюминия, титана и их сплавов.
Для усвоения теоретических основ сварки плавлением необходимо знать диаграмму железо-углерод, температурные точки аллотропических превращений. Знание диаграммы поможет изучить структурные изменения в зоне шва и близлежащих зонах при кристаллизации и охлаждении сварного шва, а также уяснить, какие структурные превращения происходят в металле в зоне термического влияния, возникающего в процессе сварки. Особое внимание следует уделить причинам и механизму образования напряжений и деформации при сварке, мерам по их уменьшению и устранению.
Необходимо внимательно изучить три основные причины: неравномерный нагрев свариваемого металла, линейную усадку расплавленного металла и структурные изменения в металле шва при его затвердевании.
Изучая особенности технологии сварки различных сталей, чугуна, металлов и сплавов, а также наплавки твердых сплавов необходимо, прежде всего, запомнить зависимость свариваемости углеродистых и низкоуглеродистых сталей от процентного содержания в них углерода. Далее необходимо обратить внимание на холодную и горячую сварку чугуна, различие в подготовке к сварке чугунных изделий, электроды. Надо знать меры, предупреждающие отбеливание чугуна при холодной сварке, а также недостатки и достоинства каждого из этих видов сварки чугуна.
Следует хорошо разобраться в особенностях сварки некоторых легированных сталей, обладающих плохой теплопроводностью, а также, цветных металлов и сплавов. Особое внимание при этом необходимо обратить на окисление алюминия затрудняющее сварку, и на способы его уменьшения.
При пайке возможно соединение не только всех однородных металлов и сплавов, но и разнородных, нередко с резко различными свойствами. Поэтому при таком разнообразии соединяемых металлов и сплавов и применяемых припоев необходимо усвоить сущность и схемы процесса пайки, его принципиальное различие от процесса сварки плавлением, а также следует знать, как классифицируются припои, указать основные технологические требования, которым они должны удовлетворять. Следует также изучить способы пайки, их характерные особенности в зависимости от используемых источников нагрева и оборудования.
Изучение вопросов контроля сварных и паяных соединений рекомендуется начинать с классификации дефектов. При этом нужно уяснить, что дефекты подразделяются на две группы.
1. Дефекты, возникающие в связи с особенностями металлургических и тепловых процессов (кристаллизационные трещины, поры, холодные трещины, неметаллические включения и др.).
2. Дефекты формирования шва, происхождение которых связано с нарушением режима сварки, неправильной подготовкой под сварку, неисправностью сварочной аппаратуры и другими причинами.
Дефекты могут быть внешние и внутренние. Надо знать причины их появления и способы устранения. Затем необходимо перейти к изучению методов контроля дефектов. При этом следует усвоить, что для обнаружения наружных дефектов. Кроме визуального осмотра, применяют контроль красками, люминофорами, магнитно-порошковым методом. Для обнаружения внутренних дефектов применяют физические методы контроля: просвечивание проникающим излучением, ультразвуковую дефектоскопию, магнитно-индукционный метод и др.
Дефекты структуры шва сварного соединения и зоны термического влияния, внутренние и наружные трещины, шлаковые включения могут бьть выявлены при металлографическом исследовании.
Изучение вопросов техники безопасности при сварочных работах следует начинать с изучения Правил устройства и безопасной эксплуатации сосудов, работающих под давлением, и Правил устройства электроустановок (ПУЭ) в части безопасности их эксплуатации. Прежде всего, необходимо уяснить возможные виды и причины травм при электрогазосварочных работах. Особо следует звать о вредном влиянии на организм пыли, продуктов сгорания электродных покрытий и флюсов, паров цинка при сварке латуней, окислов хрома, кремния, а также газов, выделяющихся при сварке различных металлов и сплавов. Затем следует рассмотреть меры защиты от вышеприведенных вредностей и ознакомиться с основными приемами оказания первой помощи пострадавшему Необходимо также ознакомиться со сваркой пластмасс.
Вопросы для самопроверки
1. Как классифицируются сварочные процессы?
2. Изложите физическую сущность сварки давлением и сварки плавлением.
3. Как влияет содержание углерода на свариваемость стали?
4. Изложите сущность автоматической сварки под флюсом, область применения.
5. В чем сущность кислородной и плазменной резки металлов?
6. Изложите сущность контактной сварки.
7. Изложите сущность диффузионной сварки в вакууме и ультразвуковой сварки, область их применения.
8. Каковы особенности кристаллизации в сварочной ванне?
9. Каковы причины возникновения напряжений и деформаций при сварке?
10. В чем трудность сварки чугуна и легированных сталей?
11. Чем отличается пайка металлов от сварки плавлением?
12. Перечислите способы контроля сварных швов.
13. Объясните сущность ультразвуковой дефектоскопии,
14. В чем состоят правила безопасности при обслуживании электросварочного оборудования?
2.2 МОДУЛЬ 3 - ОБРАБОТКА КОНСТРУКЦИОННЫХ
МАТЕРИАЛОВ РЕЗАНИЕМ
2.2.1 Цель и задачи темы
Для бакалавра техники и технологий сельскохозяйственного производства и особенно для ремонтника знания по обработке резанием имеют очень большое значение, так как необходимое качество поверхности детали достигается, как правило, этой обработкой. Поэтому задачами темы являются: изучение явлений и закономерностей процесса резания, режущего инструмента, установление режима резания для различных видов обработки, устройства металлорежущих станков и их эксплуатации, упрочняющей обработки пластическим деформированием, физико-химических методов обработки.
Необходимо знать развитие учения о резании металлов, роль отечественных ученых (И. А. Тиме, К. А. Зворыкина, Я. Г. Усачева. В. Д. Кузнецова) и новаторов производства, а также совершенствование станков, инструментов и инструментальных материалов.
Теоретической основой обработки резанием является теория дислокаций. Необходимо иметь представление об основах этой теории.
Вопросы для самопроверки
1. Какой вклад внесли в учение о резании металлов И. А. Тиме, К. А. Зворыкин, Я. Г. Усачев?
2. Что представляют собой дислокации в кристаллах?
2.3.2 Процесс резания и его основные элементы
Сначала следует иметь четкое представление об основных видах обработки металлов резанием: точении, сверлении, фрезеровании, строгании и шлифовании. Знать, какие движения совершают заготовка и инструмент и с помощью какого оборудования, какая поверхность при этом будет обрабатываемой, обработанной и поверхностью резания.
Особое внимание обратить на изучение конструктивных и геометрических элементов резца: части, поверхности, режущие кромки, углы. Необходимо иметь понятие о кинематических углах резца; знать элементы режима резания: глубину резания, подачу, скорость резания для каждого вида обработки.
При изучении инструментальных материалов особое внимание следует обратить на новые марки быстрорежущих сталей, металлокерамические твердые сплавы, минералокерамические материалы, а также на инструментальные материалы (алмазы природные и синтетические, эльбор, гексанит и др.).
Вопросы для самопроверки
1. Нарисуйте схемы точения, сверления, фрезерования и покажите на них поверхности: обрабатываемую, обработанную и поверхность резани я.
2. Как будут изменяться углы альфа и гамма токарного резня при продольном точении?
3. Расшифруйте процентный Состав марок инструментальных материалов: Р18К6, ВК8, Т15К6.
2.3.3 Физические основы процесса резания металлов
При изучении физических основ процесса резания металлов необходимо обратить особое внимание на явления, протекающие при стружкообразовании, ознакомиться с видами стружки и с процессом образования стружки при резании пластичных металлов.
Чрезвычайно важным является вопрос о качестве обработанной поверхности: критерии оценки шероховатости обработанной поверхности по ГОСТ 25142—82, влияние элементов режима резания на шероховатость поверхности.
Важно хорошо понять тепловые явления в процессе резания: причины возникновения тепла, распределение тепла, зависимость температуры в зоне резания от элементов режима резания. Уясните, как и с какой целью определяется температура в зоне резания.
Вибрации при резании металлов, возникающие и системе СПИД (станок -приспособление – инструмент - деталь), могут быть двух видов — вынужденные колебания и автоколебания. Следует изучить причины их возникновения, влияние на процесс резания и способы устранения.
Следует хорошо разобраться в процессе изнашивания режущего инструмента, знать виды, величины, критерии износа. Необходимо усвоить понятие стойкости режущего инструмента знать способы ее повышения, в частности применение смазочно-охлаждающих жидкостей, и способы подвода жидкости в зону резания с целью повышения стойкости режущего инструмента.
Вопросы для самопроверки
1. Что понимается под шероховатостью поверхности (ГОСТ 25142-82)?
2. Напишите уравнение теплового баланса. Как распределяется тепло между стружкой, заготовкой и резцом?
3. Способы подвода в зону резания смазочно-охлаждающей жидкости
4. Виды износа инструмента: абразивный, адгезионный, окислительный, электродиффузионный.
2.3.3 Металлорежущие станки
|
|
Особенности сооружения опор в сложных условиях: Сооружение ВЛ в районах с суровыми климатическими и тяжелыми геологическими условиями...
Кормораздатчик мобильный электрифицированный: схема и процесс работы устройства...
Папиллярные узоры пальцев рук - маркер спортивных способностей: дерматоглифические признаки формируются на 3-5 месяце беременности, не изменяются в течение жизни...
Архитектура электронного правительства: Единая архитектура – это методологический подход при создании системы управления государства, который строится...
© cyberpedia.su 2017-2024 - Не является автором материалов. Исключительное право сохранено за автором текста.
Если вы не хотите, чтобы данный материал был у нас на сайте, перейдите по ссылке: Нарушение авторских прав. Мы поможем в написании вашей работы!