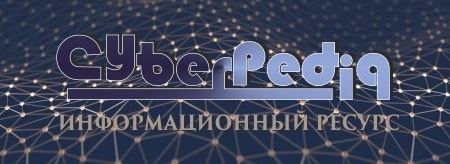
Кормораздатчик мобильный электрифицированный: схема и процесс работы устройства...
Типы оградительных сооружений в морском порту: По расположению оградительных сооружений в плане различают волноломы, обе оконечности...
Топ:
Оценка эффективности инструментов коммуникационной политики: Внешние коммуникации - обмен информацией между организацией и её внешней средой...
Установка замедленного коксования: Чем выше температура и ниже давление, тем место разрыва углеродной цепи всё больше смещается к её концу и значительно возрастает...
Интересное:
Подходы к решению темы фильма: Существует три основных типа исторического фильма, имеющих между собой много общего...
Финансовый рынок и его значение в управлении денежными потоками на современном этапе: любому предприятию для расширения производства и увеличения прибыли нужны...
Принципы управления денежными потоками: одним из методов контроля за состоянием денежной наличности является...
Дисциплины:
![]() |
![]() |
5.00
из
|
Заказать работу |
|
|
За рубежом основное количество дорожных битумов получают компаундированием остатков глубоковакуумной перегонки и деасфальтизации с маловязкими остатками и газойлевыми фракциями на специальных установках периодического и непрерывного действия, оснащенных дозаторами для регулировки смешения и достижения однородности конечного продукта. Отечественные разработки в области получения компаундированных битумов сдерживаются отсутствием необходимого промышленного оборудования. На долю окисленных битумов в некоторых странах приходится только 12 ÷14 % всех производимых битумов, в России же их доля в общем производстве битумов велика.
Окисленные битумы, получаемые в процессе окисления нефтяных остатков, в основном гудрона, воздухом в аппаратах различного типа (кубах периодического действия, трубчатых змеевиковых реакторах и пустотелых колоннах непрерывного действия) наиболее широко используются в дорожных покрытиях.
Основными факторами процесса окисления (точнее, окислительной дегидроконденсации) являются температура, расход воздуха и давление.
Интервал температур в промышленных условиях составляет 230 ÷ 270 оС, расход воздуха – 2,8 ÷ 5,5 м3/ (м2∙мин) при диаметре колонны 3,2 ÷ 3,4 м и высоте 14 ÷ 15 м [1].
Природа сырья
Природа сырья оказывает существенное влияние на свойства окисленных битумов. Соответствующим подбором сырья можно получать окисленные битумы с различными свойствами. С понижением содержания масел в исходном гудроне повы-шаются значения растяжимости, температур хрупкости и вспышки битумов, понижаются значения их теплостойкости и интервала пластичности, уменьшаются расход воздуха и продолжительность окисления.
|
Битумы из асфальта деасфальтизации содержат меньше парафино-нафтеновых соединений и больше смол и асфальтенов, что обусловливает их меньшие значения пенетрации, интервала пластичности и улучшенные низкотемпературные, пластические и когезионные свойства по сравнению с битумами с аналогичной температурой размягчения, но полученными окислением гудрона из той же нефти.
Действие парафиновых соединений зависит от дисперсной структуры битума; содержание их в сырье допустимо до 3 % мас. Парафины хрупки, ломки, как кристаллические вещества, не обладают пластическими и клеящими свойствами. Повышение содержания парафиновых соединений в сырье понижает растяжимость битумов, адгезию к минеральным материалам, а также увеличивает расход воздуха и продолжительность окисления, но при этом увеличивает значение пенетрации.
Парафино-нафтеновые соединения в сырье являются разжижителями и пластификаторами, улучшающими свойства битумов; желательно их присутствие в сырье до 10 ÷ 12 %.
Присутствие серы и сернистых соединений в сырье способствует улучшению свойств окисленных битумов.
Моноциклические ароматические соединения ведут себя аналогично парафино-нафтеновым углеводородам: улучшают пластичность и снижают температуру хрупкости окисленных битумов.
Одинаковое поведение парафино-нафтеновых и моноциклических ароматических соединений, выражающееся в торможении процесса окисления, объясняется сходством структуры их молекул. Лучшим сырьем для получения окисленных битумов являются остатки высокосмолистых нефтей ароматического основания.
Температура процесса
Чем выше температура окисления, тем быстрее протекает процесс. Однако при слишком высокой температуре ускоряются реакции образования карбенов и карбоидов, что недопустимо.
При окислении сырья до битумов протекает очень много реакций, константы скоростей которых различны. С повышением температуры процесса возрастает скорость реакций дегидри-рования молекул сырья, увеличивается содержание диоксида углерода в отходящих газах окисления и доля кислорода, расходуемого на образование воды. При этом также уменьшается количество карбоксильных групп в результате их разложения, увеличивается доля сложноэфирных групп, слабых кислот, фенолов в окисленном битуме, а также коэффициент рефракции полицик-лических ароматических соединений в битуме. Остатки высокосмолистых нефтей окисляют при 250 ÷ 280°С, парафинистых – при 270 ÷ 290 °С. С повышением температуры выше 250 °С увеличиваются значения температур размягчения и хрупкости битума, а значения пенетрации, растяжимости, теплостойкости и интервала пластичности понижаются.
|
По мере повышения температуры процесса ее влияние на скорость окисления сырья несколько уменьшается. С повышением температуры продолжительность окисления и суммарный расход воздуха снижаются, причем при температуре выше 270 °С степень использования кислорода воздуха понижается.
В зависимости от природы сырья и требуемых свойств битума следует подбирать соответствующую температуру окисления. Для большинства видов сырья с учетом экономической целесообразности она близка к 250 °С [2].
Расход воздуха
Расход воздуха, степень его диспергирования по сечению окислительной колонны существенно влияют на интенсивность процесса и свойства битумов. Традиционно тонкое диспергирование кислорода в гудроне достигается применением маточных устройств специальной конструкции.
Увеличение расхода воздуха до определенного предела при прочих равных условиях ведет к пропорциональному повышению скорости окисления (то есть кислород является инициатором процесса). При слишком большой подаче воздуха температура в реакционной зоне может подняться выше допустимой. Так как реакция окисления экзотермическая, то изменением расхода воздуха можно регулировать температуру процесса.
Как уже указывалось, для процесса окисления характерны реакции дегидрирования, приводящие к образованию водяных паров. На это расходуется значительная часть кислорода, вводимого с воздухом.
При небольшой скорости подачи воздуха и при более продолжительном времени окисления окисленный битум обладает низкой пенетрацией, поэтому для получения битума с повышенными значениями пенетрации и теплостойкости целесообразно увеличить скорость подачи сжатого воздуха.
|
С увеличением расхода воздуха до определенного значения (1,4 м3/мин на 1т сырья) эффективность процесса повышается, а при дальнейшем увеличении снижается, ухудшается степень использования кислорода воздуха, что недопустимо с точки зрения техники безопасности (концентрация кислорода в отработанных газах окисления составляет 8 ÷ 10%, что соответствует минимальному взрывоопасному содержанию кислорода). Теплостойкость окисленных битумов при этом повышается.
Общий расход воздуха зависит от химического состава сырья и от качества получаемого битума.
На некоторых НПЗ проведена модернизация и переобвязка действующих окислительных колонн с целью повышения степени использования кислорода воздуха. К ним, прежде всего, следует отнести создание колонн с внутренним или наружным разделением зон реакции и сепарации (ОАО «Рязанская НПК») и колонн с квенчинг-секцией. Такие решения позволяют повысить эффективность работы окислительной колонны за счет снижения нагрузок по воздуху и повышения температуры окисления в зоне реакции. Для этой же цели достаточно эффективно механическое перемешивание фаз в колоннах (ОАО «Ярославнефтеоргсинтез», «ТАИФ –НК»), применение газожидкостных кавитационно-вихревых или ультразвуковых диспергаторов (ОАО «Пермнефтеоргсинтез», «Новокуйбышевский НПЗ»)
Давление
Повышение давления в зоне реакции способствует интенсификации процесса окисления и улучшению качества окисленных битумов.
С повышением давления в зоне реакции улучшается диффузия кислорода в жидкую фазу, сокращается продолжительность окисления; в результате конденсации части масляных паров из газовой фазы улучшаются тепло- и морозостойкость и увеличивается интервал пластичности получаемых битумов.
Соответствующим подбором давления в системе можно регулировать состав и свойства получаемых битумов.
Интенсивность окисления сырья до битумов на непрерывной установке колонного типа повышается с увеличением температуры, расхода воздуха и давления в реакторе. Наилучшей теплостойкостью обладают битумы, полученные непрерывным окислением сырья при низкой температуре, умеренном расходе воздуха и повышенном давлении.
|
Применение подогретого до 313 ÷ 482 °С сжатого воздуха повышает скорость окисления, особенно при получении высокоплавких битумов, не оказывая существенного влияния на их качество. Увеличение высоты столба жидкости в реакторе значительно повышает температуру размягчения битума, не меняя соотношения между температурой размягчения и пенетрацией, что подтверждает преимущество вертикальных окислительных колонн. Увеличение уровня жидкой фазы повышает эффективность процесса, так как при этом увеличивается длина пути газовых пузырьков. Однако для аппаратов такого типа существует некоторый предел заполнения жидкой фазой, выше которого эффективность процесса уже не меняется.
Давление обычно колеблется от 0,3 до 0,8 МПа. Несмотря на увеличение интенсивности процесса с повышением давления, окисление под давлением не нашло широкого применения в связи с усложнением оборудования, и обычное давление не превышает 0,25 ÷ 0,30 МПа.
|
|
Папиллярные узоры пальцев рук - маркер спортивных способностей: дерматоглифические признаки формируются на 3-5 месяце беременности, не изменяются в течение жизни...
Историки об Елизавете Петровне: Елизавета попала между двумя встречными культурными течениями, воспитывалась среди новых европейских веяний и преданий...
Механическое удерживание земляных масс: Механическое удерживание земляных масс на склоне обеспечивают контрфорсными сооружениями различных конструкций...
История создания датчика движения: Первый прибор для обнаружения движения был изобретен немецким физиком Генрихом Герцем...
© cyberpedia.su 2017-2024 - Не является автором материалов. Исключительное право сохранено за автором текста.
Если вы не хотите, чтобы данный материал был у нас на сайте, перейдите по ссылке: Нарушение авторских прав. Мы поможем в написании вашей работы!