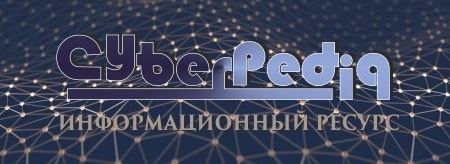
Эмиссия газов от очистных сооружений канализации: В последние годы внимание мирового сообщества сосредоточено на экологических проблемах...
Своеобразие русской архитектуры: Основной материал – дерево – быстрота постройки, но недолговечность и необходимость деления...
Топ:
Когда производится ограждение поезда, остановившегося на перегоне: Во всех случаях немедленно должно быть ограждено место препятствия для движения поездов на смежном пути двухпутного...
Основы обеспечения единства измерений: Обеспечение единства измерений - деятельность метрологических служб, направленная на достижение...
Оценка эффективности инструментов коммуникационной политики: Внешние коммуникации - обмен информацией между организацией и её внешней средой...
Интересное:
Искусственное повышение поверхности территории: Варианты искусственного повышения поверхности территории необходимо выбирать на основе анализа следующих характеристик защищаемой территории...
Отражение на счетах бухгалтерского учета процесса приобретения: Процесс заготовления представляет систему экономических событий, включающих приобретение организацией у поставщиков сырья...
Распространение рака на другие отдаленные от желудка органы: Характерных симптомов рака желудка не существует. Выраженные симптомы появляются, когда опухоль...
Дисциплины:
![]() |
![]() |
5.00
из
|
Заказать работу |
|
|
Вследствие высоких требований к поверхности холоднокатаных полос и листов, а также сложности процесса деформирования к качеству подката для станов холодной прокатки предъявляются высокие требования.
Определенные требования предъявляются и к профилю подката. Для обеспечения устойчивого процесса прокатки подкат не должен иметь короба и волны. Ширина травленой горячекатаной полосы не должна отличаться от заданной больше чем на 5,0 мм. Если подкат имеет большие отклонения ширины, то на стане холодной прокатки возможны завороты полосы при прохождении через боковые линейки, установленные на определенную ширину. Заворот, попадая в валки, как правило, приводит к навару прокатываемой полосы на поверхность рабочего валка, способствует обрыву полосы и остановке вследствие этого стана.
При значительном отклонении ширины подката от заданных размеров могут быть «выбросы» полосы, когда последняя вследствие уменьшения натяжения уходит к одной из боковых линеек. Это приводит к изменению вытяжек по ширине полосы, к надрывам полос и «порезам» поверхности валков.
Для предотвращения указанных явлений в травильных линиях обрезают боковые кромки горячекатаных полос для получения заданной ширины. В отдельных случаях при автоматическом регулировании натяжения и удовлетворительной проработке кромок вертикальными валками обрезку не проводят, что позволяет экономить металл.
Важной характеристикой подката является его продольная и поперечная разнотолщинность.
Автоматическое регулирование толщины на станах горячей прокатки позволяет получать подкат с продольной разнотолщинностью 0,07—0,1 мм. Значительная продольная разнотолщинность (0,30—0,35 мм), изменяя толщину по длине горячекатаной полосы, нарушает равенство секундных объемов металла по клетям непрерывного стана. Последнее приводит к изменению натяжения и условий деформации в каждой клети, что способствует получению холоднокатаных листов, выходящих из допусков по толщине, а иногда приводит к порывам полосы. Кроме того, повышенная разнотолщинность увеличивает порыв сварных швов.
|
Поперечная разнотолщинность также влияет на устойчивость процесса непрерывной прокатки и получение ровных листов. В случае, если горячекатаные полосы одного рулона по всей длине имеют утолщение на одинаковом расстоянии от кромки, то на холоднокатаном рулоне в этом месте может образоваться гребень.
Оптимальным профилем горячекатаной полосы считается выпуклый профиль. При холодной прокатке полос с таким профилем (поперечная разнотолщинность 0,07—0,08 мм) поддерживается высокая скорость, полоса идет в валках устойчиво и получается ровной.
Холодная прокатка углеродистой стали происходит обычно за один передел. В случае прокатки очень тонких профилей из легированных сталей используется прокатка на непрерывном стане, промежуточный отжиг и последующая прокатка на реверсивном одноклетевом или непрерывном двух- или трехклетевом стане.
Горячекатаный рулон с подающего конвейера сталкивателем подается на механизм поворота рулона. Посредством магнитного или скребкового отгибателя передний конец полосы отгибается и подается на подвижные проводки расположенные над опорным роликом. Рулон при этом разворачивается механизмом поворота для возможности задачи отогнутого переднего конца полосы в тянущие ролики правильно-натяжной машины. Одновременно с подачей переднего конца полосы тянущими роликами в рабочие валки первой клети рулон при помощи механизма поворота опускается на ролики приемного стола, поднимается до уровня головок разматывателя, центрируется и путем разжатия головок закрепляется на них. Внутренний диаметр рулона не должен быть больше диаметра головок разматывателя. После этого рулон приводом разматывателя поворачивается в таком направлении, которое способствует распушиванию наружных витков и дальнейшему продвижению переднего конца полосы в рабочие валки остальных клетей непрерывного стана и к барабану моталки.
|
Перед поступлением полосы в рабочие валки клетей верхние проводки подняты, после захвата полосы рабочими валками они опускаются и прижимают полосу к нижним проводковым столам. Пройдя последнюю клеть, полоса наматывается на барабан моталки. На этом заканчиваются операции подготовки полосы к прокатке. Стан, разматыватель и барабан моталки разгоняются до рабочей скорости, верхние проводковые столы поднимаются и начинается установившийся процесс прокатки, который продолжается до тех пор, пока на головке разматывателя не останется два — три витка полосы. При этом скорость прокатки снижается До заправочной, верхние проводковые столы опускаются, создавая возможность прокатки заднего конца полосы с натяжением. Заправочная скорость находится в пределах 0,5—2,0 м/с.
На барабане моталки задний конец полосы (т. е. наружный виток холоднокатаного рулона) фиксируется прижимным роликом. Смотанный рулон снимателем убирается с барабана моталки, передается на отводящий конвейер, упаковывается и передается для отжига.
Особенностью шестиклетевого стана является наличие специального оборудования, обеспечивающего надевание шпульки на барабан моталки при прокатке жести толщиной менее 0,2 мм, что придает необходимую жесткость холоднокатаному рулону.
При прокатке переднего конца на заправочной скорости нажимные винты клетей опускаются ниже установленного (условного нулевого) уровня, который обусловлен настройкой стана по показаниям продуктиметров (приборы, показывающие величину подъема или опускания валков). Величина опускания винтов зависит от марки стали, типа стана, прокатываемого профиля и может, например, для четырехклетевых станов составлять для первой клети 0,5—1,0, второй 0,3—0,6, третьей 0,15—0,30 мм. Аналогично поступают и при выходе заднего конца из валков стана. Это делается для уменьшения влияния скоростного эффекта на неавтоматизированных станах.
Скорость прокатки снижается и при прохождении сварных швов. Однако при удовлетворительном качестве сварки и зачистки грата рулоны можно прокатывать без снижения скорости.
|
В зависимости от размеров прокатываемых полос суммарное обжатие на четырехклетевых станах колеблется от 50 до 80, а на шестиклетевых от 90 до 95%.
Чрезвычайно важное значение имеет режим натяжения при прокатке холоднокатаных листов на непрерывных станах. Правильно выбранное натяжение способствует получению заданной планшетности полосы и исключает ее порывы. Важным технологическим параметром на непрерывных станах холодной прокатки является натяжение между последней клетью и моталками. Не достаточное натяжение затрудняет получение листов заданной толщины и требуемой планшетности, а слишком большое может привести к свариванию витков рулонов во время отжига.
Величины обжатий контролируются по показаниям продуктиметров, а натяжений — по показаниям приборов, получающих г импульс от тензороликов. Натяжение между последней клетью и моталкой контролируется по току двигателя моталки.
При работе в автоматическом режиме технологические параметры закладываются в память электронных машин и поддерживаются автоматически.
Все станы холодной прокатки оборудованы системами для охлаждения валков и подачи технологической смазки на полосу во время прокатки. Смазка снижает коэффициент трения между валками и прокатываемой полосой, благодаря чему уменьшается давление металла на валки. Смазка не должна подвергаться разложению в очаге деформации при высоких температурах. Это в большинстве случаев определяет допустимую скорость прокатки. В качестве смазки применяют органические жиры, минеральные масла и различные синтетические соединения.
При холодной прокатке углеродистой листовой стали для смазки и охлаждения валков используют эмульсии, приготовленные на эмульсоле различных марок. Такая эмульсия имеет следующий состав: 5—7% эмульсола, 3% кальцинированной соды и 91— 95% подогретой воды. В качестве смазки применяют также полимеризованное хлопковое масло (полимеризация — длительная выдержка при 240—260° С), смазку ПКС, пальмовое масло и др.
|
На реверсивных четырехвалковых станах, на которых прокатывают обычно легированные и нержавеющие стали, в качестве технологических смазок используют минеральные масла.
Иногда считают, что избыток смазки повышает вытяжку полосы. Однако это не так. Избыток смазки вытесняется из очага деформации и частично оседает на торцах кромок холоднокатаного рулона. При отжиге рулоной полоса может загрязняться затвердевшими остатками смазки.
Валки станов холодной прокатки наряду с достаточной прочностью должны иметь высокую твердость, которая обеспечила бы получение листовой стали с чистой и гладкой поверхностью.
Валки подвергают частым перешлифовкам, особенно при прокатке тонких листов и жести. Практически уменьшение диаметра валков на станах холодной прокатки допускается в пределах 3—4% от их первоначального размера.
17 Рабочие валки выходят из строя вследствие естественного износа закаленного слоя, выкрошки его, навара, порезка, надавов и иногда вследствие поломок.. Рабочие валки первой и последней клетей непрерывного стана насекают чугунной или стальной дробью. Валки первой клети насекают с целью улучшения условий захвата, а последней —для предотвращения сваривания витков рулона при отжиге.
При смотке холоднокатаной полосы в рулоны нельзя допускать попадания эмульсии между витками во избежание появления на полосе темных пятен. Поэтому на высокоскоростных станах применяют различные приспособления для предотвращения попадания эмульсии на полосу.
На точность размеров получаемых холоднокатаных листов влияет ряд факторов: жесткость клети, работа системы автоматического регулирования толщины, стабильность размеров и профиль подката и др.
При оценке точности прокатки холоднокатаных и горячекатаных листов различают продольную и поперечную разнотолщинность. Последняя тесно связана с профилем холоднокатаных листов — волнистостью и коробоватостью.
Большое влияние на точность холоднокатаных листов оказывает жесткость клети. Жесткость клети характеризуется усилием, Которое вызывает увеличение зазора между валками на 1 мм за счет упругой деформации всех элементов рабочей клети.
Причиной появления продольной разнотолщинности холоднокатаных полос может явиться изменение скорости прокатки (скоростной эффект), колебание натяжения, изменение профилировки валков вследствие износа и влияния температуры.
Поперечная разнотолщинность определяется степенью равенства вытяжек по ширине полосы, которая зависит от состояния валков, поперечного профиля подката и устойчивости технологических параметров процесса.
Увеличение точности холоднокатаных полос по длине достигается применением систем автоматического регулирования толщины полосы, а по ширине — регулированием теплового профиля валков или применением гидроизгиба.
|
С целью компенсации прогиба валков, их упругого сплющивания, возмещения теплового влияния пластической деформации, учета ширины, толщины и марки прокатываемой стали рабочие валки станов холодной прокатки профилируют, т. е. им придается определенная выпуклость.
В процессе прокатки вытяжки по ширине холоднокатаной полосы не всегда компенсируются межклетевым натяжением или заданной профилировкой валков, что проявляется в поперечной разнотолщинности и появлении волны или короба на прокатываемой полосе и сопровождается характерным хлопанием. Одним из способов устранения этого является тепловое регулирование профиля валков. Вальцовщик, подавая различные количества охлаждающей жидкости на середину и края бочки валков, повышает или понижает температуру разных частей валка по длине бочки. Это приводит к изменению первоначальной профилировки и выравниванию вытяжек по ширине листа. Однако тепловое регулирование профиля валка обладает значительной инерцией.
Следует отметить, что при тепловом регулировании появляются дополнительные термические напряжения, из-за которых рабочий валок может выйти из строя.
Для соблюдения теплового режима работы валков необходимо соблюдать следующие правила:
1) при любых остановках стана немедленно прекратить подачу охлаждающей жидкости;
2) при остановках валков в момент прокатки подачу воды прекратить, освободить раскат; последующее включение охладителя проводить только после охлаждения валков при вращении их;
3) после перевалки горячие валки укладывать осторожно на подкладки;
4) после отключения подачи охлаждающей жидкости последующее ее включение осуществлять постепенно.
Наиболее эффективный способ исправления поперечного профиля и неплоскостности полосы — изменение характера распределения обжатий, а следовательно, и вытяжек по ширине полосы путем принудительного изгиба рабочих или опорных валков.
Изгибая валок, вальцовщик меняет первоначальную форму щели между валками и тем самым изменяет величины вытяжек по ширине полосы.
Перевалки рабочих валков производят по причине перехода на другой профиль или из-за износа насеченных поверхностей валков. Опорные валки переваливаются по износу. Например, для четвертой клети перевалка рабочих валков осуществляется после прокатки 600—1100 т металла.
Для измерения толщины прокатываемого металла применяют приборы ИТ-5250, использующие γ-излучение, ИТХ-5736 —рентгеновское.
Показания приборов передаются на пульт управления или в систему автоматики стана.
18 Настройку стана холодной прокатки начинают с установки направляющих проводок в соответствии с шириной прокатываемой полосы и проверки плотности прилегания откидных проводок к бочке нижнего рабочего валка.
Настройка валков станов холодной прокатки сводится к установке параллельности валков, установке раствора валков и подбору скоростей прокатки по клетям, обеспечивающих получение заданных размеров и межклетевых натяжений после каждой клети.
Окончательно параллельность установки валков проверяют при прокатке переднего конца полосы. Если передний конец выходит по оси прокатки, то валки установлены параллельно. Перекос устраняют работой одного из нажимных винтов. После этого продуктиметры устанавливают в нулевое положение. Далее растворы валков и скорость их вращения настраивают в соответствии с таблицами режимов прокатки.
Соответствие действительных растворов заданным контролируют, измеряя толщину полосы ручным микрометром после каждой клети или определяя ее по показаниям измерителя толщины. Контролируют также величину межклетевых натяжений полосы по приборам. По данным контроля проводят подстройку стана. Обязательное условие настройки стана — загрузка электродвигателей без превышения допустимых значений. После окончательной настройки стана продуктиметры выставляются в нулевое положение. Станы перестраивают в соответствии с таблицами режимов прокатки.
Настройку станов холодной прокатки проводят после перевалки опорных и рабочих или только рабочих валков, после планово-предупредительных и капитальных ремонтов и других длительных остановок.
Процесс прокатки на реверсивных станах начинается с того, что передний конец рулона, зажатого головками разматывателя, задают в предварительно разведенные валки, наматывают его на барабан моталки, нажимными винтами устанавливают зазор между валками и начинают прокатку. После первого прохода задний конец рулона остается в валках, а валки стана реверсируются и конец полосы задается в переднюю моталку. Полоса до заданной толщины прокатывается вследствие реверса валков стана и последовательного опускания рабочих валков; при этом концы полосы остаются в передней и задней моталках, обеспечивающих натяжение. Аналогичен процесс прокатки и на многовалковых станах.
Настройка реверсивных четырехвалковых станов включает следующие операции: установку проводок, проверку параллельности осей валков в вертикальной плоскости (по характеру распределения охлаждающей жидкости по длине бочки валка), установку условного нулевого положения рабочих валков по проходам для обеспечения того или иного режима обжатий (с учетом жесткости клети) и установление режима скоростей и натяжений по проходам.
Термическая обработка
После холодной прокатки вследствие наклепа углеродистая сталь становится твердой и обладает пониженной пластичностью.
Для устранения наклепа и получения структуры, обеспечивающей необходимые механические и технологические свойства, холоднокатаная сталь должна быть отожжена.
Рекристаллизационный отжиг проводят при 650—720° С. Он обеспечивает достаточно высокие механические и технологические свойства металла.
В цехах холодной прокатки для отжига углеродистой листовой стали широко применяют колпаковые печи. Холоднокатаные рулоны устанавливают на стенд, в центре которого помещен вентилятор. Между рулонами прокладывают конвекционные кольца, обеспечивающие лучшую циркуляцию защитного газа.
Стопа рулонов накрывается муфелем из жаропрочной стали. Из-под муфеля удаляется воздух и подается защитный газ. Внизу муфеля имеется песочный затвор. Муфель накрывается футерованным колпаком. На колпаке имеются горелки, продукты сгорания циркулируют между муфелем и колпаком. Колпаковые печи отапливают чаще всего коксовым или смешанным газом.
Отжиг углеродистой стали проводят в среде защитного газа, предохраняющего поверхность листа от окисления.
Листы и рулоны холоднокатаной стали отжигают также в четырехстопных колпаковых электрических печах. В состав печи входят четыре стенда, четыре муфеля и один колпак.
Масса садки в современных одностопных колпаковых печах достигает 120—180 т. Средняя производительность печи в зависимости от сортамента и условий отжига 1,4—2,4 т/ч.
Колпаковые печи являются печами периодического действия: цикл термической обработки в них длится несколько десятков часов. Для отжига холоднокатаных полос широко применяют непрерывные горизонтальные и вертикальные (башенные) печи (рис. 175), в которых продолжительность процесса отжига составляет всего 1,5—2,0 мин.
Производительность горизонтальных печей ниже печей башенного типа и составляет 10—15 т/ч.
Термическая обработка полос в агрегатах непрерывного отжига уменьшает длительность производственного цикла и обеспечивает получение более однородных свойств металла, чем при отжиге в колпаковых печах. Нагрев и охлаждение полосы во всех зонах происходят в атмосфере защитного газа.
|
|
Организация стока поверхностных вод: Наибольшее количество влаги на земном шаре испаряется с поверхности морей и океанов (88‰)...
Кормораздатчик мобильный электрифицированный: схема и процесс работы устройства...
Архитектура электронного правительства: Единая архитектура – это методологический подход при создании системы управления государства, который строится...
Общие условия выбора системы дренажа: Система дренажа выбирается в зависимости от характера защищаемого...
© cyberpedia.su 2017-2024 - Не является автором материалов. Исключительное право сохранено за автором текста.
Если вы не хотите, чтобы данный материал был у нас на сайте, перейдите по ссылке: Нарушение авторских прав. Мы поможем в написании вашей работы!