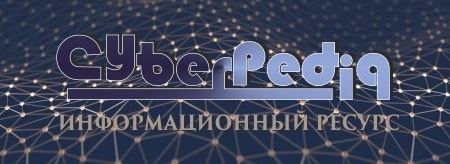
Семя – орган полового размножения и расселения растений: наружи у семян имеется плотный покров – кожура...
Кормораздатчик мобильный электрифицированный: схема и процесс работы устройства...
Топ:
Организация стока поверхностных вод: Наибольшее количество влаги на земном шаре испаряется с поверхности морей и океанов...
Определение места расположения распределительного центра: Фирма реализует продукцию на рынках сбыта и имеет постоянных поставщиков в разных регионах. Увеличение объема продаж...
Процедура выполнения команд. Рабочий цикл процессора: Функционирование процессора в основном состоит из повторяющихся рабочих циклов, каждый из которых соответствует...
Интересное:
Принципы управления денежными потоками: одним из методов контроля за состоянием денежной наличности является...
Отражение на счетах бухгалтерского учета процесса приобретения: Процесс заготовления представляет систему экономических событий, включающих приобретение организацией у поставщиков сырья...
Лечение прогрессирующих форм рака: Одним из наиболее важных достижений экспериментальной химиотерапии опухолей, начатой в 60-х и реализованной в 70-х годах, является...
Дисциплины:
![]() |
![]() |
5.00
из
|
Заказать работу |
Содержание книги
Поиск на нашем сайте
|
|
Благодаря своей простоте, система Линде - Хэмпсона вполне подходит для установок ожижения небольшой мощности. Однако, было показано, что базовая система Линде - Хэмпсона без предварительного охлаждения является неработоспособной для неона, водорода и гелия, так как максимальная температура инверсии этих газов ниже температуры окружающей среды. Применяя систему с предварительным охлаждением, температуру газа, поступающего на вход основной части ожижителя Линде - Хэмпсона, можно понизить ниже температуры окружающей среды, выбрав соответствующее рабочее тело для системы предварительного охлаждения.
В принципе в качестве предварительного хладагента может быть выбрано любое рабочее вещество, имеющее тройную точку ниже максимальной температуры инверсии неона или водорода. В качестве предварительного криоагента для систем ожижения водорода и неона выбор можно остановить на жидком азоте.
,
Система Линде - Хэмпсона с предварительным охлаждением жидким азотом схематично показана на рисунке. Для небольших лабораторных ожижителей подсистема жидкого азота может быть заменена небольшой емкостью для хранения, из которой жидкий азот переталкивается в ванну предварительного охлаждения и пары отводятся через трехпоточный теплообменник в атмосферу. Для крупных систем вопрос об использовании отдельной установки ожижения азота должен решаться на основе экономического анализа.
Выход жидкости в системе Линде - Хэмпсона с предохлаждением может быть увеличен за счет снижения температуры на входе в холодный теплообменник. В системе ожижения водорода или неона это может быть легко выполнено снижением давления в ванне с жидким азотом. Так как в ванне предварительного охлаждения происходит кипение азота, снижение давления приводит к снижению температуры кипения или температуры ванны. Однако, существует технический предел процессу снижения температуры ванны. При 63.2 К происходит затвердевание жидкого азота при давлении насыщения собственных паров (тройная точка азота), и дальнейшее уменьшение давления приводит к тому, что вся жидкость в ванне превращается в твердое тело. Между теплообменными поверхностями и твердым азотом трудно достичь хорошего теплового контакта из-за парового слоя, образующегося между твердым телом и стенками. Это явление лимитирует температуру ванны предохлаждения значением 63.2 К.
|
Получение параводорода. Равновесным состояниям водорода при нормальной температуре и в жидком состоянии (20 К) соответствуют различные соотношения концентрации его орто- и парамодификации. Это обусловлено зависимостью вращательных уровней энергии молекулы водорода от температуры. Состав нормального водорода (75 %орто- и 25 % параводорода) не меняется от нормальной температуры до 200 К, затем доля параводорода увеличивается, достигая 99.8 % при 20 К. Определяющий фактор при конверсии (переходе) — выделение теплоты, эквивалентной изменению энергии вращательных уровней молекул при орто-парапереходе. При конверсии нормального водорода в 100 %-ный параводород эта теплота достаточно велика (525 кДж/кг). Это больше, чем теплота испарения жидкого водорода (455 кДж/кг). В результате ожиженный нормальный водород при переходе его в равновесный параводород полностью испаряется. Теплота перехода 100 % -ного ортоводорода в 100 %-ный параводород составляет 705 кДж/кг, т. е. на 1 % изменения ортопарасостава приходится 7.05 кДж/кг выделяющейся теплоты. Теплота перехода qK при низких температурах постоянна и уменьшается с 50 К.
Ортопараконверсия протекает самопроизвольно, но медленно.
1-реактор скатализатором; 2- сборник жидкости; 3, 5- дроссели; 4,8 -,вентили; 6, 7 - теплообменники; 9 – промежуточный сборник; 10 - клапан
|
Соответственно доля параводорода хр-Н, в смеси увеличивается в процессе конверсии от 25 % до 100 %, а доля жидкого водорода хнж - уменьшается. Этот процесс сильно растянут по во времени: за 24 ч испаряется около 20 % жидкости, за 100 ч - около 40 %.
Конверсию можно резко ускорить, применяя катализаторы. Следовательно, для длительного хранения жидкого продукта следует производить устойчивый параводород, осуществляя орто-пара-конверсию непосредственно в ожижителе с применением катализаторов. Естественно, что при этом теплота конверсии выделяется непосредственно в ожижителе и существенно влияет на его работу. Конверсия происходит в реакторе, заполненном катализатором.
Существуют различные схемы включения реакторов (рис. 5.13), в которых применяют различные типы катализаторов. Нижние части всех схем даны применительно к циклу, приведенному на рис. 5.7.Вариант схемы, показанной на рис. 5.13, а, — простейший. Он предусматривает помещение открытого реактора 1 с катализатором в сборник 2 жидкого водорода. При этом вся жидкость переходит в параводород, часть которого испаряется в результате конверсии, а другая часть отводится через вентиль 4 в виде продукта. Этот вариант малоэффективен, так как в результате испарения обратный поток обогащается параводородом, что приводит к уменьшению его энтальпии ic по сравнению с энтальпией поступающего нормального водорода. В итоге уменьшается дроссель-эффект, а, следовательно, и производительность по жидкому продукту. По этой схеме невозможно получать нормальный водород. Кроме того, при этой схеме затруднена активация катализатора.
Схема, приведенная на рис. 5.13, б, лишена этих недостатков. Ее широко применяют в небольших ожижителях. Поток водорода делится на две части. Доля потока х через дроссель 3 поступает в теплообменник 6, затем в реактор 1 и теплообменник 7 и выходит через вентиль 4 в виде продукта. Конверсия происходит в закрытом реакторе, теплота конверсии отводится через его поверхность и в теплообменнике 7. Через дроссель 5 идет основной поток нормального водорода. При необходимости через вентиль 8 можно получать нормальный водород, отключив реактор 1.
Схема на рис. 5.13, в отличается от схемы на рис. 5.13, б отсутствием дросселя 5. Весь поток водорода дросселируется в промежуточный сборник 9, откуда доля потока х поступает в реактор, а оставшийся нормальный водород выходит через газовый клапан 10 в сборник 2 жидкого водорода.
|
Вариант, показанный на рис. 5.13, г, целесообразнее для крупных ожижителей. Согласно этой схеме доля потока водорода, равная доле получаемой жидкости х, при низком давлении проходит по отдельному каналу. В остальном схема соответствует схеме на рис. 5.13, б. Организация потоков по схеме на рис. 5.13, г позволяет проводить предварительную конверсию ожижаемой части газа на более высоком температурном уровне в азотной ванне, отдавая часть теплоты жидкому азоту. Эта теплота эквивалентна изменению доли параводорода от 25 до 50 % - это массовый % или что. В итоге количество теплоты qK, выделяемой в реакторе 1, уменьшается, что ведет к увеличению производительности ожижителя.
Очевидно, идеальной является непрерывная конверсия с отводом теплоты при любых равновесных концентрациях параводорода в интервале температур 200...20 К и поглощением ее соответствующими источниками охлаждения. На практике непрерывный процесс заменяют ступенчатым процессом конверсии на нескольких температурных уровнях/ Осуществление процесса по схеме, показанной на рис. 5.13, г, для этой цели является оптимальным, так как конвертируемый поток идет по отдельному каналу. Давление в потоке, идущем через реакторы, 0.2…0.4 МПа, что обеспечивает температурный перепад для отвода теплоты от реактора. Теплообменники 6 и 7 позволяют предварительно охладить конвертируемый поток, а затем сконденсировать его после конверсии. Желательно поддерживать изотермичность конверсии, для повышения доли параводорода.
Необходимая доля параводорода в получаемой смеси зависит от характера его использования. Для кратковременного хранения достаточно обеспечить 80—85 % параводорода, для длительного необходимо обеспечить состав, близкий к равновесному. Чаще всего получают продукт, содержащий 90…95 % параводорода.
Для получения параводорода применяют различные типы катализаторов. Наиболее распространены хромоникелевый, а также гидроокиси хрома, железа и др. Катализаторы имеют зернистую структуру. Для удаления из них влаги проводят предварительную активацию путем вакуумирования до 1…10 Па с прогревом до 100…150 °С. В крупных установках активацию выполняют продувкой сухим горячим водородом. Примеси, содержащиеся в водороде, могут «отравлять» катализаторы, поэтому водород должен иметь высокую степень чистоты. При хорошей очистке длительность непрерывной эксплуатации катализаторов может составлять несколько лет.
|
За 400 часов, в результате конверсии испаряется 60% массы водорода. Для получения пароводорода используется катализатор конверсии (хромоникилиевый сплав).
Ожижитель Клода
С термодинамической точки зрения, расширение в дросселе является необратимым процессом. Таким образом, для того, чтобы приблизиться к идеальной эффективности, нужно найти лучший процесс для получения низких температур.
В системе Клода, показанной на рисунке, энергия отводится от газового потока за счет производства им работы в расширительной машине или детандере. Если процесс в детандере обратимый и адиабатный (что сочтем справедливым для данного анализа), то этот процесс является изоэнтропным, в котором достигается более низкая температура, чем для изоэнтальпного расширения.
1 – баллон сжатого газа; 2 – редуктор; 3 – компрессор; 4…7 – теплообменные аппараты; 8 – поршневой детандер; 9 – дроссель; 10 – сосуд Дьюара
В системе Клода газ первоначально сжимается до давления примерно 4 МПа и затем проходит через первый теплообменник. Около 60…80 % газа отделяется затем от основного потока, расширяется в детандере и вновь объединяется с обратным потоком за вторым теплообменником. Далее ожижаемый поток движется через второй и третий теплообменники и, наконец, дросселирует в сборник жидкости. Холодный пар из сборника жидкости возвращается через теплообменники, охлаждая поступающий газ. Дроссель по-прежнему необходим в системе Клода, так как детандер реальной системы не может выдержать большое влагосодержание. Жидкость имеет значительно меньшую сжимаемость, чем газ. Поэтому, если в цилиндре детандера (поршневого типа) образуется жидкость, это приведет к высоким ударным нагрузкам. Были разработаны некоторые турбодетандеры (осевого типа), успешно работающие с содержанием жидкости до 15 % по весу без разрушения лопаточного аппарата турбины.
В некоторых системах Клода работа, получаемая в детандере, используется при сжатии газа. В большинстве малых систем энергия рассеивается в тормозах или потребляется воздушным внешним вентилятором. На выход жидкости не оказывает влияния, рассеивается энергия или нет; однако в том случае, когда работа детандера не используется, естественно, увеличиваются затраты работы на сжатие.
|
Цикл Капицы
Капица модернизировал базовую схему Клода, отказавшись от третьего, или низкотемпературного, теплообменника. В систему также введено несколько значительных технических усовершенствований. Вместо поршневого детандера был использован турбодетандер.
Благодаря этому удалось увеличить расход рабочего тела, что позволило уменьшить рабочее давление системы и, как следствие, массу установки.
Первый, или высокотемпературный, теплообменник в системе Капицы представлял собой в действительности набор регенераторов с клапанами, в которых объединяются процессы охлаждения и очистки. Входящий теплый газ охлаждался в одном регенеративном элементе, и в нем же осаждались примеси, в то время как выходящий поток нагревался в другом элементе регенератора и выносил примеси, осажденные в нем ранее. Через несколько минут срабатывали клапаны и переключали потоки высокого и низкого давлений с одного элемента на другой. Система Капицы обычно работала при сравнительно низких давлениях — примерно 700 кПа.
Обратный цикл Стирлинга
В холодильном цикле Стирлинга два поршня движутся в цилиндре прерывисто со сдвигом по фазе. Между поршнями размещен регенератор Р, который делит рабочую полость на теплую и холодную части. Газ изотермически сжимается (процесс 1-2), параллельным движением поршней изохорно перемещается через регенератор (процесс 2-3) и охлаждается до температуры Тх. Затем за счет движения правого поршня газ расширяется, его температура снижается и oт охлаждаемого тела к нему подводится теплота (процесс 3-4). Поршни параллельно сдвигаются влево, холодный газ изохорно перемещается через регенератор, охлаждая его, и после этого процесс повторяется.
Одноступенчатые машины используют для получения холода на уровне 150…70 К и до 40 К при небольшой холодопроизводительности; ,
. Более низких температур достигают, применяя двухступенчатые машины с
, трехступенчатые машины обеспечивают Тх = 8.5 К.
Современные приборы, основанные на цикле Стирлинга, - криокулеры и ожижители. В широких масштабах их начали производить около десяти лет назад - преимущественно для использования в военной технике: на танках и самолетах требовалось устанавливать высокочувствительные, охлаждаемые до температур порядка (-200 ºС) датчики и приемники. Для их охлаждения и были разработаны криокулеры на основе обратного цикла Стирлинга.
Принципиальными особенностями цикла Стирлинга являются следующие.
· Цикл характеризуется нестационарными во времени параметрами потоков рабочего тела в каждой точке системы. Практически это означает, что машина Стирлинга, рабочие полости которой входят в один объем, неизбежно должна быть машиной с периодическим изменением объемов сжатия и расширения, т.е. поршневой машиной. В виду этого, преимущественные области применения таких машин –машины малой и средней мощности.
· Цикл предназначен только для работы с газообразным рабочим телом. Чтобы размеры машин при заданной мощности были приемлемы, а внешний и внутренний теплообмен рабочего тела в этих условиях проходил достаточно эффективно, давление в машине должно быть существенно выше атмосферного. По тем же причинам рабочее тело должно иметь малую вязкость, возможно большуюие теплопроводность и теплоемкость, мало зависящуюие от давления (иначе возникнут большие собственные потери в регенераторе вследствие различных тепловых эквивалентов теплообменивающихся потоков).
· В цикле регенерация тепла позволяет работать в большом интервале температур (верхняя и нижняя температуры цикла) при относительно малых отношениях давлений сжатия и расширения.
· Для реализации цикла в качестве рабочих тел могут быть использованы водород, гелий, азот, воздух и другие газообразные вещества. Использование в качестве рабочего тела газов с высоким значением газовой постоянной (R), например, водорода или гелия, позволяет получать в машинах Стирлинга эксергетический к.п.д. свыше 50%;
· Цикл универсален. На его основе возможно создание преобразователей как прямого, так и обратного цикла.
К достоинствам машин, работающих по циклу Стирлинга, следует отнести высокую степень экологической чистоты, как самих рабочих тел машин Стирлинга, так и отработанных сред, возникающих при их эксплуатации, а также их энергетическую эффективность.
К недостаткам следует отнести сложность конструктивного исполнения отдельных узлов, проблемы в области уплотнений, регулирования мощности и т.д. Особенности конструктивного исполнения обуславливаются применяемыми рабочими телами. Так, например, гелий обладает сверхтекучестью, что определяет повышенные требования к уплотняющим элементам рабочий рабочих поверхностей поршней, штока вытеснителя и т.д. Формирование облика перспективных, предполагаемых к производству машин Стирлинга невозможно без разработки новых технических решений основных узлов.
Следующая проблема - это высокий уровень технологии производства. Данная проблема связана с необходимостью применения в машинах Стирлинга жаростойких сплавов и цветных металлов, их сварки и пайки. Отдельный вопрос - изготовление регенератора и насадки для него, обеспечивающих одновременно высокую теплоемкость и низкое гидравлическое сопротивление. Все это требует высокой квалификации рабочего персонала и современного технологического оборудования.
Ожижитель, построенный с использованием цикла Стирлинга, показан на рисунке.
Особенности:
· отсутствуют клапаны;
· нет расхода рабочего тела.
ЛИТЕРАТУРА
1. Архаров А.М., Марфенина И.В., Микулин Е.И. - Криогенные системы: Основы теории и расчета. - М.: Машиностроение, 1988.- 464 с.
2. Архаров А.М., Беляков В.П., Микулин Е.И., Пронько В.Г., Шургальский - Криогенные системы: Основы проектирования аппаратов и установок. - М.: Машиностроение, 1987. - 536 с.
3. Филин Н.В., Буланов А.Б. - Жидкостные криогенные системы. - Л.: Машиностроение, 1985. - 247 с.
4. Справочник по физико-техническим основам криогеники. - Под ред. М.П.Малкова. - М.: Энергия, 1973. - 392 c.
5. Каганер М.Г. - Тепломассообмен в низкотемпературных конструкциях. - М.: Энергия, 1979. - 256 с.
6. Баррон Р.Ф. - Криогенные системы - пер. с англ. М.: Энергоатомиздат, 1989. - 408 с.
7. Алексеев В.П., Вайнштейн Г.Н., Герасимов П.В. - Расчет и моделирование аппаратов криогенных установок. - Л.: Энергоатомиздат.
8. Теплообменные аппараты холодильных установок. - Под ред. Г.Н.Даниловой. - Л.: Машиностроение, 1986. - 303 с.
9. Шпильрайн Э.Э., Малышенко С.П., Кулешов Г.Г. - Введение в водородную энергетику. - М.: Энергоатомиздат, 1984. - 264 с.
10. Веркин Б.И., Кириченко Ю.А., Русанов К.В. - Теплообмен при кипении криогенных жидкостей. - Киев: Наукова думка, 1987. - 264 с.
11. Григорьев В.А., Павлов Ю.М., Аметистов Е.В. - Кипение криогенных жидкостей. - М.: Энергия, 1977. - 288 с.
|
|
Наброски и зарисовки растений, плодов, цветов: Освоить конструктивное построение структуры дерева через зарисовки отдельных деревьев, группы деревьев...
Эмиссия газов от очистных сооружений канализации: В последние годы внимание мирового сообщества сосредоточено на экологических проблемах...
Индивидуальные очистные сооружения: К классу индивидуальных очистных сооружений относят сооружения, пропускная способность которых...
История создания датчика движения: Первый прибор для обнаружения движения был изобретен немецким физиком Генрихом Герцем...
© cyberpedia.su 2017-2024 - Не является автором материалов. Исключительное право сохранено за автором текста.
Если вы не хотите, чтобы данный материал был у нас на сайте, перейдите по ссылке: Нарушение авторских прав. Мы поможем в написании вашей работы!