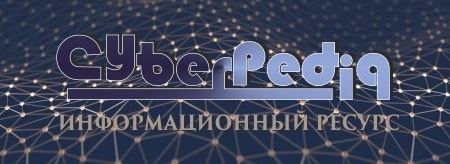
Адаптации растений и животных к жизни в горах: Большое значение для жизни организмов в горах имеют степень расчленения, крутизна и экспозиционные различия склонов...
Папиллярные узоры пальцев рук - маркер спортивных способностей: дерматоглифические признаки формируются на 3-5 месяце беременности, не изменяются в течение жизни...
Топ:
Организация стока поверхностных вод: Наибольшее количество влаги на земном шаре испаряется с поверхности морей и океанов...
Когда производится ограждение поезда, остановившегося на перегоне: Во всех случаях немедленно должно быть ограждено место препятствия для движения поездов на смежном пути двухпутного...
Комплексной системы оценки состояния охраны труда на производственном объекте (КСОТ-П): Цели и задачи Комплексной системы оценки состояния охраны труда и определению факторов рисков по охране труда...
Интересное:
Принципы управления денежными потоками: одним из методов контроля за состоянием денежной наличности является...
Что нужно делать при лейкемии: Прежде всего, необходимо выяснить, не страдаете ли вы каким-либо душевным недугом...
Национальное богатство страны и его составляющие: для оценки элементов национального богатства используются...
Дисциплины:
![]() |
![]() |
5.00
из
|
Заказать работу |
|
|
Сырьем служит этилен, образующийся при пиролизе газов нефтепереработки или попутного нефтяного газа (пирогаз), а также этиленовая фракция, получаемая при разделении коксового газа.
Исходный газ очищают от сероводорода и оксида углерода, сжимают до 40 атм и осушают, пропуская через слой адсорбента – алюмосиликата. затем проводят ректификацию, доводя концентрацию до 99%.синтез этанола осуществляют непосредственным присоединением воды к этилену в присутствии катализатора- фосфорной кислоты, нанесенной на носитель - алюмосиликат в виде шариков. Присоединение воды проводят в жидкой или паровой фазе, в промышленном масштабе преимущественно используют второй вариант.
Гидратация в паровой фазе представляет собой гетерогенно-каталитическую обратимую экзотермическую реакцию, протекающую по уравнению:
С2Н4 + Н2О ↔ С2Н5ОН + 45,6 кДж
В присутствии фосфорной кислоты протекает электрофильное присоединение воды к этилену по схеме:
Активность катализатора достигается лишь при температуре 300ºС, для смещения равновесия применяют повышенное давление (80 атм), но при этих условиях превращению подвергается только 5% этилена, поэтому осуществляют многократную циркуляцию этилена с добавлением исходного газа. В результате выход реакции достигает 95%.
Этилен, сжатый в компрессоре 1 до 8 МПа, смешивается с циркуляционным газом, предварительно поджатым в компрессоре 2, нагревается в теплообменнике 3 продуктами реакции до 300ºС и смешивается с перегретым до 450ºС паром. Образовавшаяся газовая смесь поступает в гидрататор 4 – стальной цилиндр диаметром 1,5 м и высотой 10 м, футерованный изнутри листами меди для защиты от коррозии и заполненный катализатором, т.к. фосфорная кислота частично испаряется из пористого носителя, то в реакционную смесь после выхода ее из гидрататора вводят раствор щелочи для нейтрализации. Что бы восполнить потерю кислоты, ее непрерывно вводят в парогазовую смесь. Реакционная смесь охлаждается в теплообменнике 3 и поступают в котел-утилизатор 5. Далее продукты поступают в сепаратор высокого давления 6, в котором от них отделяется циркуляционный газ, поступающий в компрессор 2. Спирто-водный конденсат, содержащий до 15% этанола, дросселируется через дроссель 7 до давления 5 МПа и поступает в сборник 8, где из него выделяются растворенные газы. Из сборника8 конденсат подается в колонну 9, где происходит отделение паров спирта, загрязненных примесями, от водного раствора фосфата натрия. Спирт очищается перегонкой в ректификационной колонне 10. производительность установки 30 тыс. т в год. Синтетический спирт по качеству мало отличается от пищевого, а себестоимость в 4 раза ниже, 1 т этилена заменяет 6 т ржи или 20 т картофеля, следовательно, этот способ получения спирта позволяет сохранять большое количество пищевых продуктов.
|
55. Получ. пищевого этилового спирта
Наиболее распространенным сырьем в гидролизном производстве, в том числе, для получения этанола, является древесина. Это сложная структурированная система, состоящая из целлюлозы, гемицеллюлозы, лигнина, а также незначительных количеств смол, дубильных и красящих веществ. Элементный состав органической части древесины практически постоянен: углерод 49—51%, водород 6,1—6,9%, кислород 43—45%, азот 1%. Содержание целлюлозы, лигнина и гемицеллюлоз зависит от природы древесины. В сухой древесине хвойных пород, используемой для производства этанола, содержится 52—58% целлюлозы, 28—29% лигнина и около 20% гемицеллюлоз различной степени полимеризации, состоящих из пентозанов (С5Н8О4)n и гексозанов (С6Н10О5)n.
В результате гидролиза полисахаридов образуются водные растворы моносахаридов — гидролизаты. Из них кристаллизацией получают пищевую глюкозу и техническую ксилозу; гидрированием — ксилит и сорбит; дегидратацией — фурфурол; окислением — органические кислоты; микробиологической переработкой — этанол, бутанол, ацетон, кормовые дрожжи, антибиотики.
|
Таким образом, гидролизное производство — это пример малоотходного производства, в котором используются все компоненты сырья.
Физико-химические основы производства. Получение гидролизного этанола складывается из двух последовательных стадий: гидролиза древесины и брожения гидролизата.
Гидролиз древесины представляет каталитический процесс взаимодействия полисахаридов (целлюлозы, пентзанов и гексозанов гемицеллюлоз) с водой с образованием соответствующих моносахаридов - ксилозы, а-D-глюкозы и т.д., например:
(С5Н804)n + nН20 (Н+)/ à nС5Н10О5
(С6Н10О5)n + nН20 (Н+)/ à nС6Н12О6
Процесс гидролиза протекает в несколько стадий и катализируется кислотами и кислыми солями, причем каталитическое действие кислот тем сильнее, чем выше степень их диссоциации.
Брожение или ферментация — процесс разложения углеводов под воздействием микроорганизмов или выделенных из них ферментов.Из моносахаридов брожению подвергаются только гексозы. Процесс спиртового брожения а-D-глюкозы являющейся структурной единицей глюкозы, происходит без доступа кислорода (анаэробное брожение) и состоит из ряда стадий с участием фосфорорганических соединений, играющих роль переносчиков фосфора. В результате сложных превращений из глюкозы образуется этанол и оксид углерода (IV), что может быть выражено суммарным уравнением:
С6Н1206 = 2С2Н5ОН + 2С02
Технологическая схема производства. В нашей стране распространен метод гидролиза древесины разбавленной серной кислотой, для которого в качестве сырья используют отходы хвойной древесины с высоким содержанием гексозанов.
По этой схеме производство этанола представляет полунепрерывный перколяционный процесс, в основе которого лежит принцип непрерывной фильтрации кислоты через периодически загружаемое в реактор сырье с непрерывным отбором образующегося гидролизата в течение нескольких часов. Древесное сырье в виде опилок или измельченной щепы загружается в гидролиз-аппарат 1, представляющий цилиндрический стальной сосуд.футерованный изнутри кислотоупорным материалом. Затем в аппарат через специальное оросительное устройство подается нагретая до 180—190°С серная кислота концентрацией 0,5% массовых. Вода для разбавления кислоты подогревается в подогревателе 2. В гидролиз-аппарат подается пар под давлением 1—1,2 МПа. Образующийся гидролизат непрерывно выводится из нижней части аппарата черв» фильтрующее устройство в виде перфорированных медных трубок и направляется в испаритель 4. Вследствие снижения давления гидролизат вскипает и пары, содержащие фурфурол (тем пература кипения 161,7°С при атмосферном давлении) поступают в конденсатор 5. Цикл непрерывной работы гидролиз-аппарата от загрузки до выгрузки составляет несколько часов, после чего оставшийся в аппарате лигнин передавливается в сборник 3. Затем в аппарат загружается новая порция сырья. Гидролизат после отделения фурфурола поступает из испарителя 4 в нейтрализатор 6, куда вводится раствор гидроксида кальция для нейтрализации серной кислоты, и из него в отстойник гипса 7. После охлаждения до 30°С в холодильнике 8 гидролизат перекачивается через сборник 9 в бродильный чан 10, где происходит процесс сбраживания и размножения дрожжевых клеток. Продукт сбраживания (бражка) подается в сепаратор 11, где от бражки отделяются дрожжи. Часть дрожжей возвращается в бродильный чан, а остальные выводятся из системы в качестве кормовых дрожжей. Оксид углерода (IV), выделяющийся из бродильного чана, собирается в газгольдере 12 и в дальнейшем перерабатывается на сухой лед. Осветленная бражка, содержащая около 1,5% об. этанола, поступает в сборник 13 и оттуда подается в систему ректификации, состоящую из трех колонн. В бражной колонне 14 от бражки отделяется барда, после чего жидкость с содержанием этанола 15—20% об. поступает сначала в спиртовую колонну 15, а затем в метанольную колонну, в которой этанол концентрируется и освобождается от примеси метанола.
|
Из 1 т абсолютно сухой хвойной древесины получается 150— 180 кг этанола и до 120 кг оксида углерода (IV).
56. Производство уксусной кислоты
Наиболее важной из карбоновых кислот является уксусная кислота.
|
СН3СООН – бесцветная жидкость с резким запахом, Ткип=118,1ºС, Тпл=16,75ºС, ρ=1,05 г/мл. Уксусная кислота слабая, Кдис=1,75·10-5.
Впервые была получена И.Глаубером в 1648 г. В 1667 г Шталем была получена концентрированная уксусная кислота путем вымораживания ее водных растворов. Элементный состав уксусной кислоты был установлен Я.Берцелиусом в 1814 г.
До начала XIX века уксусную кислоту производили исключительно из природного сырья окислительным уксуснокислым брожением жидкостей, содержащих этиловый спирт, н-р, вина, пива. Этот способ применяется и в настоящее время для получения столового уксуса.
В значительно больших количествах получают уксусную кислоту в лесохимической промышленности при сухой перегонке древесины. В этом методе уксусную кислоту выделяют из конденсированной части парообразных продуктов термической обработки древесины, при этом выход кислоты составляет 20 кг на 1 м3 древесины.
Но потребность в уксусной кислоте очень велика, т.к. она широко применяется в самых различных отраслях промышленности.
Применение уксусной кислоты
Получение ацетилцеллюлозы, из которой изготавливают ацетатное волокно, пластмассы, лаки, кинопленку.
Является ацилирующим средством в органическом синтезе.
Консервант в пищевой промышленности.
в текстильной промышленности как закрепитель красителей.
Соли уксусной кислоты, например, ацетат натрия, применяется при крашении и печатании тканей.
Сложней эфиры уксусной кислоты применяются в качестве растворителей и, фруктовых эссенций и душистых веществ.
Получение уксусного ангидрида и ацетилхлорида.
В производстве фармацевтических препаратов.
В производстве ацетона.
Для получения монохлоруксусной кислоты – промежуточного продукта в производстве инсектицидов, фунгицидов и моющих средств.
В качестве растворителя и коагулянта латексов.
Для выделки кож.
Производство уксусной кислоты из карбида кальция
Во время первой мировой войны возникло производство синтетической уксусной кислоты из ацетилена. Этот способ основан на выдающемся открытии известного русского химика Кучерова. В 1881 г он установил, что в присутствии катализатора – солей ртути в кислой среде идет гидратация ацетилена с образованием уксусного альдегида (реакция Кучерова):
Альдегид легко окисляется до уксусной кислоты. Другой предпосылкой для осуществления этого производства явилась разработка в 90-х годах XIX века технического способа получения из кокса и извести карбида кальция, из которого под действием воды легко образуется ацетилен.
Таким образом, синтез уксусной кислоты включает в себе 4 стадии:
получение карбида кальция;
|
получение ацетилена и его очистка
получение уксусного альдегида по реакции Кучерова;
окисление альдегида до уксусной кислоты.
Рассмотрим синтез подробнее.
1 стадия: Производство карбида кальция.
Карбид кальция получают из извести и кокса при температуре 2000ºС
Процесс осуществляется в электрической печи непрерывного действия. Карбид кальция из печи в жидком состоянии выпускается через летку во вращающейся барабан, охлаждаемый снаружи водой, где он застывает и дробится на куски.
2 стадия: получение ацетилена
Осуществляется двумя способами:
1 способ: из карбида кальция
При соприкосновении карбида кальция с водой бурно протекает реакция образования ацетилена в генераторе 2:
Содержащийся в техническом карбиде фосфид кальция (Са3Р2) и сульфид кальция (СаS) при действии воды также разлагается с образованием фосфористого водорода (РН3) и сероводорода (Н2S), следовательно, ацетилен необходимо очистить от этих примесей действием окислителя, так как эти примеси являются каталитическими ядами в следующей стадии синтеза и загрязняют продукт. С этой целью ацетилен пропускают через промывную башню 5, орошаемой хромовой смесью:
3Н2S + K2Cr2O7 ++ 4H2SO4 → 3S + Cr2(SO4)3 + K2SO4 + 7H2O
Если применять при разложении карбида избыток воды (мокрый способ), то в качестве побочного продукта получается известковое молоко, переработка которого затруднена из-за большого объема, поэтому в производстве используют сухой способ, когда карбид кальция разлагают минимальным количеством воды. Причем, вода частично испаряется за счет теплоты реакции и гашеная известь (Са(ОН)2) получается в виде пушонки – влажного порошка.
2 способ: Получение ацетилена из природного газа – метана путем крекинга при температуре 1500ºС:
2СН4 → 3Н2 + С2Н2
Но при этой температуре метан быстро разлагается на С и Н2, поэтому пребывание газа в зоне высокой температуры должно быть кратковременным (тысячные доли сек), после чего газ быстро охлаждается.
3 стадия: жидкофазная гидратация ацетилена с образованием уксусного альдегида по реакции Кучерова
Осуществляется в гидрататоре 9, температура реакции 90ºС поддерживается за счет подачи снизу гидрататора водяного пара. Катализатором является сульфат ртути (II) в 20%-ной серной кислоте. Кроме того, в раствор добавляют окислитель – Fe2(SO4)3 для того, что бы предотвратить побочные реакции восстановления сульфата ртути (II) образовавшимся альдегидом до свободной Hgº. Отработанный катализатор непрерывно регенерируется: образовавшийся в результате восстановления FeSO4 окисляется азотной кислотой до Fe2(SO4)3 в регенераторе 10, затем снова подается в гидрататор.
В гидрататоре реакцию ведут лишь на 50-60% продукта, что бы предотвратить дальнейшее превращение образовавшегося уксусного альдегида – конденсацию в кротоновый альдегид
затем и осмоление.
Продукт быстро удаляют из реакционной смеси. С этой целью в аппарат подается небольшое количество ацетилена, чтобы в реакцию вступило его 50-60% и непрореагировавший ацетилен в смеси с парами альдегида и воды выводится из гидрататора и подаются в конденсатор 11 для охлаждения. Пары воды и частично уксусного альдегида конденсируются и газ промывается водой при температуре 5-10ºС в промывной башне12 для удаления непрореагировавшего ацетилена от растворимого в воде альдегида, смешивается со свежей порцией ацетилена в смесителе 8 и снова поступает в гидрататор 9 (принцип циркуляции).
Из конденсатора 10%-ный водный раствор альдегида поступает в ректификационную колонну 13 для очистки от примесей. Выход альдегида составляет 90-95% в расчете на прореагировавший ацетилен.
4 стадия: окисление уксусного альдегида в уксусную кислоту молекулярным кислородом
Реакция протекает в газовой фазе по цепному механизму через стадию образования надуксусной кислоты:
которая является окислителем и окисляет ацетальдегид до уксусного ангидрида:
Уксусный ангидрид при достаточном количестве воды гидролизуется до уксусной кислоты:
Если остановить процесс окисления на второй стадии, то можно получить в качестве конечного продукта не уксусную кислоту, а уксусный ангидрид.
Процессы получения уксусной кислота и уксусного ангидрида различаются: - природой катализатора,
- составов окислительного газа,
- методом удаления воды.
При получении уксусной кислоты:
• катализатор – ацетат марганца – Mn(CH3COO)2,
• в качестве окислительного газа – чистый кислород,
• во избежание накопления легко разлагающейся с взрывом надуксусной кислоты процесс проводят в растворе циркулирующей уксусной кислоты при температуре не выше 70º и добавлении инертного газа – азота.
При совместном получении уксусной кислоты и уксусного ангидрида в качестве катализатора используют смесь растворимых ацетатов кобальта и меди в соотношении 1:3. а чтобы снизить гидролиз образовавшегося уксусного ангидрида из системы необходимо удалять воду, для этого добавляют этилацетат, который с водой образует легко удаляемую азеотропную смесь.
Окисление проводят в окислительной колонне 14, заполненной катализатором. Кислород под давлением 4 атм вводят в колонну через несколько труб и он равномерно распределяется в виде мельчайших пузырьков. Для охлаждения и поддержания оптимальной температуры 65-70ºС служат змеевики 15.
Из верхней части колонны уксусную кислоту отводят на ректификацию и туда же вводят азот для разбавления выходящего из колонны газа, чтобы устранить опасность взрыва.
После двойной ректификации:
в 1-ой ректификационной колонне удаляются легко кипящие примеси,
во 2-ой ректификационной колонне удаляются высоко кипящие примеси и катализатор.
В результате получается синтетическая уксусная кислота концентрацией 95-97%. Выход ее достигает 92%.
Кроме того, уксусную кислоту в промышленных масштабах производят следующими методами:
из ацетона пиролизом его до кетена с последующей гидратацией:
из метанола карбонилированием его на кобальтовом катализаторе:
из алканов окислением их в жидкой и паровой фазе пропановых фракций и бензиновых фракций прямой перегонки,
из продуктов окисления парафина при синтезе высших жирных кислот,
при сухой перегонке древесины,
уксуснокислым брожением этанол содержащих жидкостей.
Нефть и ее переработка
Нефть — единственное жидкое горючее ископаемое — представляет собой маслянистую жидкость, имеющую обычно окраску от желтого до темно-коричневого, иногда и черного цвета, легче воды (плотность от 0,73 до 0,95 е/см). Элементарный состав нефти из различных месторождений довольно постоянен и изменяется лишь в узких пределах: 84—87% С, 12—14% Н и 0,5—2% О, N. 5. Но встречаются нефти и с более высоким содержанием серы — до 5%. Нефти представляют собой сложные смеси большого числа органических соединений. Основную часть всех нефтей (до 80—95% по весу) составляют жидкие и находящиеся в растворе твердые углеводороды, принадлежащие к жирному (предельные углеводороды, или парафины, или алканы), алициклическому (полиметиленовые углеводороды, или нафтены, или цикланы) и ароматическому рядам, а также растворенные в нефти газообразные алканы — от метана до бутанов. Непредельные углеводороды жирного ряда в нефти (за редкими исключениями) не содержатся. В нефтях различных месторождений углеводороды содержатся в различном соотношении, которое в значительной степени и определяет качество получающихся при переработке данной нефти продуктов.
Помимо углеводородов, в состав нефтей входят:
1)смолы и асфальтены, представляющие собой многоядерные гетероциклические соединения со значительной молекулярной массой, содержащие в качестве гетероатомов кислород, серу и азот;
2)различные сернистые соединения (меркаптаны R-SН, сульфиды R-S-R1, полисульфиды R-(S)n-R', производные тиофена и т. д.);
3)нафтеновые кислоты — карбоновые кислоты алициклического ряда. Все эти вещества являются примесями, которые весьма затрудняют переработку нефти.
Общепризнанной является в настоящее время теория органического происхождения нефти, высказанная впервые М. В. Ломоносовым (1763). Согласно взглядам акад. И. М. Губкина, источником происхождения нефти были остатки растений и животных, скоплявшиеся на дне мелководных морей и их заливов в прошлые геологические эпохи и перекрытые в дальнейшем слоями осадочных горных пород.
Перегонка нефти
Нефть как топливо непосредственно почти не применяется, а перерабатывается в товарные нефтепродукты. Вследствие сложности состава нефть перегоняется в широком интервале температур. Сначала фракционированной перегонкой получают несколько фракций (дистиллятов) с более узкими пределами температуры кипения.
Прежде чем подвергнуть нефть перегонке, ее из скважин направляют по трубопроводам в газоотделители — стальные вертикальные цилиндры, где давление снижается до атмосферного. При этом из нефти выделяется попутный нефтяной газ. В нефти содержится вода с растворенными в ней солями в виде стойкой эмульсии, которую разрушают на электрообессоливающей установке (ЭЛОУ). Нагретую до 60—80° С нефть смешивают с горячей водой, содержащей едкий натр и деэмульгатор; чаще всего это нейтрализованный щелочью «черный контакт» (НЧК)— отход от очистки нефтепродуктов СК. В последнее время его начинают заменять более элективными синтетическими деэмульгаторами. После отстаиваний отводы нефть пропускают последовательно через два шарообразных; электродегидратора. Здесь нефть проходит тонким слоем между электродами и подвергается действию переменного электрического поля высокого напряжения (20—40 тыс. в), что приводит к слиянию мелких капелек воды в крупные; вода отделяется в отстойнике. В настоящее время фракционированная перегонка (прямая гонка) нефти осуществляется в виде непрерывного процесса в так называемых атмосферных трубчатых установках, основными аппаратами которых являются трубчатая печь и ректификационная колонна. В трубчатой печи за счет теплоты, выделяющейся при сжигании нефтяного газа или жидкого котельного топлива, нефть нагревается до достаточно высокой температуры, при которой, однако, еще не наблюдается разложения (крекинга) углеводородов. В ректификационной колонне смесь паров углеводородов отделяется от неиспарившегося остатка и разделяется на фракции путем ректификации в присутствии перегретого водяного пара при атмосферном давлении.
Трубчатая печь представляет собой камеру из огнеупорного кирпича. Нефть нагревается предварительно в теплообменниках горячими продуктами перегонки до 150—180° С и з/м подается под давлением 10 — 12атм от внутрь печи. Здесь нефть разделяется на два потока и проходит длинный (до 1000 —1500 м) путь по змеевику, состоящему из большого числа соединенных между собой стальных труб. Во внутренней части камеры эти трубы обогреваются отходящими топочными газами, а в наружных частях — гл.образом за счет лучеиспускания факела горящего топлива. Температура нефти достигает 330—3500 С, а давление вследствие трения в трубах снижается почти до атмосферного. Во внутренней части печи расположен также змеевик для перегрева водяного пара до 400° С.
Ректификационная колонна — это вертикальный стальной цилиндр, диам. 4—5 м и высотой 35—45 м, тщательно изолированный снаружи асбестом. Внутри колонны имеется до 40 стальных или чугунных горизонтальных перегородок, называемых тарелками. В каждой тарелке имеется большое число отверстий, в которых укреплены короткие, направленные вверх трубки, так называемые патрубки, прикрытые сверху колпачками, имеющими зубчатый нижний край. Через эти патрубки и колпачки проходят пары нефти, которые поднимаются по колонне снизу вверх. В тарелках укреплены, кроме того, сливные стаканы, служащие для стекания жидкости (флегмы) с вышележащей на нижележащую тарелку. Смесь паров и жидкости, выходящая из печи, поступает в нижнюю часть колонны, где эта смесь разделяется. Неиспарившаяся часть нефти стекает вниз, перетекая с одной тарелки на другую. На самую нижнюю тарелку подают из печи перегретый водяной пар» что способствует более полному удалению из мазута летучих веществ. Известно, что при перегонке в-ва, не смешивающегося с водой, проводимой с водяным паром, температура его кипения понижается. Помимо этого, пузырьки водяного пара перемешивают жидкость и увеличивают поверхность испарения. Пары летучих УВ-дов, поднимаясь вверх и подвергаясь ректификации, раздел. на фракции.
Обязательными условиями для проведения процесса ректификации являются:
1) непрерывное поступление в колонну холодной флегмы - орошения, для чего часть конденсата, образовавшегося из прошедших через всю колонну паров фракции, наиболее летучих веществ (в нашем случае — часть бензина), возвращается обратно на верхнюю тарелку колонны;
2) установление хорошего контакта на каждой тарелке между стекающей вниз более холодной флегмой и поднимающимися вверх более горячими парами.
Пары в виде пузырьков, выходящих между зубцами колпачков, пробулькивают через слой флегмы на тарелке. Благодаря этому пары нагревают флегму, испаряя из нее более летучие углеводороды, а менее летучие, содержащиеся в парах, вследствие охлаждения флегмой конденсируются и увлекаются ею на нижележащие тарелки. Таким образом, на каждой тарелке происходит как обмен теплом между парами и конденсатом, так и переход веществ из пара в жидкость и обратно — как бы отдельный процесс перегонки. Из поднимающихся вверх паров на первых тарелках конденсируются углеводороды с наибольшими температурами кипения, образуя первую фракцию — дистиллят газойля. Выше отделяется следующая фракция, состоящая из более летучих углеводородов,— дистиллят реактивного топлива (вместо этой фракции иногда отбирают керосиновую фракцию, а в верхней части колонны еще более низкокипящий лигроиновый дистиллят).
Пары бензина и водяной пар покидают колонну сверху и конденсируются в конденсаторе. Смесь бензинового дистиллята с водой разделяется вследствие разности плотностей в водоотделителе и часть бензина подается насосом 6 на орошение колонны. Остальные дистилляты отводят по трубам с соответствующих тарелок колонны для дополнительной отгонки более летучих углеводородов с водяным паром в отпарные секции, состоящие каждая из 6—8 тарелок, причем образующиеся здесь пары вместе с водяным паром поступают обратно в колонну. Дистилляты отдают теплоту нефти в теплообменниках и затем охлаждаются в водяных холодильниках. В настоящее время в нефтяной, а также химической промышленности вместо таких трубчатых печей начинают применяться трубчатые печи «беспламенного» горения. Т.к. они имеют более высокий коэффициент полезного действия. Нефтяной газ, смешанный с воздухом, сгорает в отверстиях керамических призм, образующих стены (панели) камеры. Теплота передается трубам змеевика за счет лучеиспускания раскаленных панелей. Из мазута можно получать смазочные масла непрерывной перегонкой под уменьшенным давлением с перегретым водяным паром (что позволяет сильно уменьшить температуру кипения углеводородов и избежать их разложения) на вакуумных трубчатых установках. Мазут, нагретый в трубчатой печи до 410—430° С, поступает в ректификационную колонну, где ректификацией паров получаются в качестве отдельных фракций различные виды дистиллятных смазочных масел: внизу — автол, выше — машинное и далее — веретенное масло. Уходящие сверху пары после конденсации образуют соляровое масло, часть которого поступает на орошение колонны. Уменьшенное давление (50—70 мм рт. ст.) в колонне создается конденсацией водяного пара вбрызгиванием воды в барометрическом конденсаторе и отсасыванием из него воздуха и паров воды пароструйным насосом (эжектором). Из остатка после перегонки мазута — гудрона — при надлежащем его составе получают после тщательной очистки для удаления смол и асфальтенов высоковязкие остаточные смазочные масла (авиационные, дизельные и др.). Если гудрон
для этого не пригоден, то продувают через него воздух. Тогда гуд-рай превращается в битум, темную жидкую или твердую смолистую массу, которая служит для приготовления дорожного асфальта, а также в качестве электро- и гидроизолирующего материала в электротехнике и в строительном деле. Обычно атмосферная и вакуумная трубчатые установки объединяются в одно целое — атмосферно-вакуумную трубчатую установку (АВТ), что дает большую экономию топлива.
Произв-ть 4000—9000 т в сутки.
60.. Втор.переработка нефти. Термический крекинг.
Ввиду того что выход бензина при перегонке нефтей составляет обычно лишь 5—25% от веса нефти, количество его, полученное таким путем, не может покрыть громадной потребности в нем авиации и автотранспорта. Количество получаемого из нефти иензина увеличивают, подвергая часть менее необходимых нефтепродуктов (мазут, газойль, соляровое масло, полугудрон и др.) крекингу — расщеплению их при нагревании до 450—550° С, часто в присутствии катализаторов. Это позволяет повысить общий выход бензина из нефти в несколько раз и довести его до 40—50%.
Впервые такое направление процесса при нагревании нефтепродуктов было установлено исследованиями Д. И. Менделеева и А. А. Летнего. В 1890 г. В. Г. Шухов разработал схему процесса и конструкцию основных аппаратов для проведения крекинга под давлением. Применение крекинга началось лишь с 1913 г. в США, а в СССР — в годы первой пятилетки.
Термический крекинг является в химическим отношении сложным процессом, так как сырье представляет собой смесь многих углеводородов и они подвергаются превращениям в различных направлениях вследствие последовательного и параллельного протекания р/ий нескольких типов: распада молекул с разрывом связей между атомами углерода и образованием веществе меньшей молекулярной массой; конденсации и полимеризации с образованием веществ с большей молекулярной массой; дегидрирования; гидрирования и др.
Из содержащихся в нефти углеводородов наименее устойчивыми к нагреванию являются парафины, наиболее устойчивыми — нафтены и ароматические углеводороды. У парафинов при 450—550° С преобладает распад молекул с разрывом связи близ середины углеродной цепи и с образованием молекулы парафина и молекулы этиленового углеводорода (олефина), например:
С16Н34 -> С8Н18 + С8Н16
С8Н18 -> С4Н10 + С4Н8
У низших парафинов наблюдается также дегидрирование и распад с разрывом связи у конца углеродной цепи:
С4Н10à С4Н8 + Н2;
С4Н10 à С3Н6 + СН4
С увеличением числа углеродных атомов в молекуле устойчивость углеводородов к нагреванию сильно уменьшается.
Превращение нафтенов протекает в следующих направлениях:
1) разрыв боковых цепей (подобный распаду парафинов), а также распад полиметиленовых колец с образованием олефинов и диеновых углеводородов;
2) дегидрирование шестичленных нафтенов с превращением в ароматические углеводороды.
У ароматических углеводородов преобладают реакции конденсации, преимущественно с участием непредельных углеводородов (олефинов, диеновых углеводородов и др.);что постепенно приводит к образованию углеводородов с весьма большим числом бензольных колец и малым содержанием водорода, т. е. к образованию кокса. Наряду с этим происходит разрыв боковых цепей у гомологов бензола и многоядерных ароматических углеводородов.
Образующиеся при крекинге олефины реакционноспособны и подвергаются разнообразным превращениям, важнейшими из котопых являются:
1) полимеризация с образованием олефинов большей молекулярной массы и с разветвленной углеродной цепью;
2) распад с образованием молекулы диенового углеводорода и парафина:
СН2=СН-(СН2)2-СН3àСН2=СН-СН=СН2+СН4
или двух молекул олефина:
С8Н16à2С4Н8;
3) конденсация с диеновыми углеводородами, что может при
вести к образованию ароматических углеводородов:
Таким образом, при крекинге, с одной стороны, в результате распада углеводородов образуются вещества с меньшей молекулярной массой и более низкими температурами кипения; при этом наряду с бензиновой фракцией получается газ крекинга, состоящий из низших парафинов и олефинов и водорода; с другой стороны, в результате реакций конденсации образуются в-ва с большей, чем у исходных углеводородов, молекулярной массой, - входящие в состав неперегоняющегося остатка (крекинг-остаток) и кокса. Обычно термическому крекингу подвергают тяжелое (состоящее из углеводородов с большей молекулярной массой) сырье - мазут и полугудрон; — на двухпечной установке. Чтобы избежать образования большого количества газа и закоксовывания аппаратов, мазут подвергают сперва крекингу в более мягких условиях так называемому легкому крекингу при 470—490° С, нагревая его в трубчатой печи1. При этом наряду с небольшим количеством бензина (8—15%) образуется также газойль — соляровая фракция, которую направляют на глубокий крекинг, проводимый в более жестких условиях 530-550град. в др.печь2. Образовавшаяся смесь паров и жидкости из обеих печей поступает в реакционную камеру3, которую она проходит сверху вниз, для продолжения крекинга. Вся эта часть установки находится под повышенным давлением, что препятствует образованию газа крекинга, уменьшает объем паров и тем самым способствует улучшению передачи теплоты и повышению производительности установки. Из реакционной камеры смесь поступает тонкой струей через редукционный вентиль 4, снижающий давление до 8-12атм, в нижнюю часть испарителя5, где жидкость (при 400° С) частично испаряется и отделяется крекинг-остаток (55-80% от сырья). Пары проходят последовательно через две ректификационные колонны 6 и 7. В первой колонне конденсируется тяжелая фракция высокой температурой кипения, с которой смешивается поступающий сюда мазут, во второй — не успевший полностью прокрекироваться газойль — соляровая фракция. Осуществляя циркуляцию обеих фракций, проводя крекинг осторожно и постепенно, достигают выхода бензина 30—35%, считая на мазут; выход бензина из полугудрона составляет всего 15—20%. Производительность установки — до 1500 т мазута в сутки.
Важнейшими отличиями бензина термического крекинга от полученного прямой гонкой из той же нефти являются повышенное содержание ароматических и наличие в нем ненасыщенных углеводородов, в следствие чего его октановое число выше. Из ненасыщенных, углеводородов в результате полимеризации и окисления могут образоваться смолы. Чтобы задержать этот процесс, к крекинг-бензину добавляют небольшое количество (0,005—0,05%) ингибиторов-противоокислителей—а-нафтол, n-оксидифениламин, древесно-смоляной антиокислитель (одна из фракций, получаемых при ректификации древесной смолы, образующейся при сухой перегонке березовой древесины) и др. После добавления этиловой жидкости октановое число полученного таким путем автомобильного бензина составляет 66—76. Сорта автомоб-х бензинов обозначаются буквой А и цифрой, указывающей его октановое число, например бензин А-76. Крекинг -остаток в настоящее время служит основой для изготовления (смешением с другими нефтепродуктами) жидкого кательного топлива.
61. Каталитический крекинг.
Катализатор ускоряет крекинг, что позволяет провести его в более мягких условиях (при 450—600° С и давлении 1,5—2 атм). Сырьем являются широкая фракция с т. кип. 350—500* С, получаемая перегонкой в вакууме мазута, и газойль-соляровая фракция из установок термического крекинга и коксования. Сырье полностью испаряется, и пары его подвергаются крекингу на поверхности катализатора — искусственно полученного алюмосиликата (в виде мелких шариков или пыли) или цеолита.
Под влиянием катализатора наряду с рассмотренными выше реакциями распада, полимеризации и конденсации углеводородов интенсивно протекают также процессы, не наблюдающиеся при термическом крекинге: изомеризация, олефинов, приводящая к разветвлению углеродной цепи; перераспределение водорода (отщепление его от соединений, вступающих в реакции конденсации с постепенным образованием кокса, отлагающегося на поверхности катализатора, и присоединение отщепляющегося водорода к непредельным углеводородам). Поэтому, бензин каталитического крекинга почти не содержит непредельных углеводородов; содержание в нем ароматических углеводородов, нафтенов и изопарафинов выше, чем в бензине термического крекинга. Этот бензин вне зависимости от состава сырья имеет октановое число 77-80 без добавки этиловой жидкости; выход его составляет 30—35%; кроме того, из паров выделяется 25—30% газойля, который по составу значительно отличается от исходного газойля, вследствие чего не может быть использован для каталитического крекинга и уводится в дизельное топливо. Образуется также тяжелая фракция (13—20%), которую вводят в котельное топливо; количество газа крекинга (12—20%) и кокса (8%) значительно больше, чем при те
|
|
Организация стока поверхностных вод: Наибольшее количество влаги на земном шаре испаряется с поверхности морей и океанов (88‰)...
Особенности сооружения опор в сложных условиях: Сооружение ВЛ в районах с суровыми климатическими и тяжелыми геологическими условиями...
Историки об Елизавете Петровне: Елизавета попала между двумя встречными культурными течениями, воспитывалась среди новых европейских веяний и преданий...
Поперечные профили набережных и береговой полосы: На городских территориях берегоукрепление проектируют с учетом технических и экономических требований, но особое значение придают эстетическим...
© cyberpedia.su 2017-2024 - Не является автором материалов. Исключительное право сохранено за автором текста.
Если вы не хотите, чтобы данный материал был у нас на сайте, перейдите по ссылке: Нарушение авторских прав. Мы поможем в написании вашей работы!