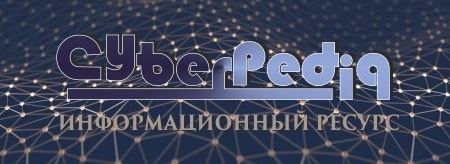
Состав сооружений: решетки и песколовки: Решетки – это первое устройство в схеме очистных сооружений. Они представляют...
Адаптации растений и животных к жизни в горах: Большое значение для жизни организмов в горах имеют степень расчленения, крутизна и экспозиционные различия склонов...
Топ:
Эволюция кровеносной системы позвоночных животных: Биологическая эволюция – необратимый процесс исторического развития живой природы...
Когда производится ограждение поезда, остановившегося на перегоне: Во всех случаях немедленно должно быть ограждено место препятствия для движения поездов на смежном пути двухпутного...
Проблема типологии научных революций: Глобальные научные революции и типы научной рациональности...
Интересное:
Аура как энергетическое поле: многослойную ауру человека можно представить себе подобным...
Уполаживание и террасирование склонов: Если глубина оврага более 5 м необходимо устройство берм. Варианты использования оврагов для градостроительных целей...
Влияние предпринимательской среды на эффективное функционирование предприятия: Предпринимательская среда – это совокупность внешних и внутренних факторов, оказывающих влияние на функционирование фирмы...
Дисциплины:
![]() |
![]() |
5.00
из
|
Заказать работу |
Содержание книги
Поиск на нашем сайте
|
|
ТЕРМОФОРМОВАНИЯ ПЛАСТМАСС
Цель работы:
Приобретение навыков технологических расчетов процесса производства изделий из пластмасс методом термоформования.
1. Общие определения
Методом термоформования перерабатывают лишь термопластичные листовые полимеры.
Изделия из листовых термопластов могут изготовляться различными методами: штампованием, формованием с проскальзыванием листа в прижимной раме, пневмоформованием и вакуумформованием.
При штамповании лист термопласта нагревают до температуры размягчения, а затем формуют с помощью матрицы и пуансона.
При формовании способом проскальзывания листа в прижимной рамке разогретая листовая заготовка натягивается на выпуклую (позитивную) форму и оформляется в изделие пневматическим прессом с верхним и нижним давлением.
При пневмоформовании листовую заготовку закрепляют по периметру формы прижимной рамой, нагревают излучающими электронагревателями до температуры, при которой термопласт переходит в высокоэластическое состояние, и затем формуют на позитивной или негативной форме с помощью подогретого сжатого воздуха. После охлаждения, необходимого для фиксации формы изделия, его удаляют из формы. Преимуществом пневмоформования является возможность использования высокого давления формования (0,15 – 2,5 МПа), что способствует переработке толстостенных листовых заготовок и получению крупногабаритных изделий. При этом способе формования изделия имеют четкий контур и обладают высокой точностью размеров. Изделия получают с хорошей равнотолщинностью.
При вакуум-формовании листовая заготовка закрепляется по периметру формы прижимной рамкой, нагревается плоскими радиационными электронагревателями до высокоэластического состояния и затем формуется под давлением, которое создается за счет разности между атмосферным давлением и разряжением, возникающим в формующей полости между поверхностью листа и формой при отсасывании из нее воздуха вакуум-насосом. Практически давление составляет 0,06-0,085 МПа. Его обычно достаточно для формования листов толщиной до 5 мм. Далее изделие охлаждается для фиксирования формы, а затем удаляется.
Для изготовления глубоких изделий сложной формы применяют различные комбинированные способы, при которых используют и механическую вытяжку пуансонами и пневмовакуумформование.
Машины для термоформования могут быть одно- и многопозиционными. Последние отличаются тем, что основные технологические операции, требующие наибольшей затраты времени (процессы нагрева листовой заготовки, формования и охлаждения изделий) осуществляются одновременно в различных рабочих позициях.
|
Наибольшее распространение получили трехпозиционные револьверные (карусельные) машины. Основным рабочим органом такой машины является ротор с укрепленными на нем тремя прижимными рамами. В первой позиции листовая заготовка зажимается прижимной рамой, после чего ротор поворачивается на 120 оС. Листовая заготовка попадает во вторую позицию, где осуществляется ее разогрев до высокоэластического состояния. Затем ротор вновь поворачивается на 120 оС, где в третьей позиции происходит формование изделия и его охлаждение. В это же время на первой позиции происходит выгрузка готового изделия и укладка нового листа термопласта.
Вакуум-формование осуществляется как позитивным, так и негативным методами. Выбор того или иного метода зависит от следующих факторов: требования к качеству внутренней или внешней поверхности изделий, требуемая равнотолщинность и местоположение наиболее тонких стенок изделия, угол наклона вертикальных стенок формы. При негативном формовании изделие после охлаждения в форме усаживается, а при позитивном сильно обтягивает поверхность формы, поэтому съем изделия может быть затруднен при непрерывном угле наклона вертикальных стенок формы. Минимальный угол наклона стенок формы в зависимости от типа перерабатываемого материала составляет при негативном формовании 1-2о, а при позитивном – 3-5о.
2. Листовые термопласты и их свойства
Традиционно термоформованием перерабатываются следующие материалы: целлулоид, полиметилметакрилат (ПММА), полистирол (ПС) и его сополимеры, пластифицированнный поливинилхлорид (ПВХ), ПЭВД и ПЭНД, в меньших объемах – листовые полипропилен (ПП), полиамид (ПА), поликарбонат (ПК), полиэтилентерефталат (ПЭТФ) и некоторые наполненные термопласты.
Наибольшей жесткостью (модулем упругости) обладают изделия из органических стекол типа ПАНМА (материал на основе акрилонитрила с метакрилатом), ПММА и ПК. Наибольшая ударная вязкость характерна для ПК, а изделия из ПММА и ПАНМА не выдерживают ударных нагрузок.
|
Важнейшим свойством термопластичного листового материала, предназначенного для переработки термоформованием, является его способность к значительному удлинению без разрыва. Это свойство зависит от температуры.
При глубокой вытяжке листовая заготовка деформируется пуансоном, матрицей и просто давлением воздуха. Они вытягивают разогретую заготовку по профилю формы. Выделяют три основных вида деформаций, возникающих при формовании листовой заготовки:
1) двухосное растяжение в плоскости листа, вызывающее натяжение материала вокруг формующей части пуансона;
2) радиальное растяжение, сопровождающееся усадкой материала по периметру;
3) изгиб материала под натяжением.
Различие листовых материалов по способности к формованию оценивают по степени вытяжки, которую рассчитывают как отношение начальной и конечной толщины дна изделия при максимально возможной глубине вытяжки, принятой равной 0,95 от глубины вытяжки, при которой происходит разрыв изделия.
На практике под степенью вытяжки понимают отношение высоты изделия Н к характерному размеру его наибольшего отверстия D, т.е. Н/D. Вытяжка связана с увеличением поверхности заготовки, поэтому при вытяжке изменяется толщина листа, что оказывает влияние на механические свойства получаемого изделия.
Оптимальная глубина вытяжки зависит от природы перерабатываемого листового термопласта и от способа термоформования.
Большое значение имеет также направление вытяжки, которое определяет ориентацию цепей макромолекул полимера, а значит и механические свойства изделия. При вытяжке в одном направлении механическая прочность изделия резко возрастает в направлении вытяжки и сильно снижается в перпендикулярном направлении. Поэтому при конструировании изделий, получаемых методами термоформования, необходимо стремиться к тому, чтобы разность степеней вытяжки в разных направлениях не превышала 50-60 %. Ориентация термопластов при термоформовании зависит, главным образом, от степени вытяжки и температуры формования. Повышение степени вытяжки и снижение температуры формования приводят к увеличению прочности при растяжении и ударной вязкости материала.
В зависимости от вида термоформования и применяемых формующих устройств технологический процесс может состоять из следующих операций: разметка листового термопласта (получение заготовки), закрепление листовой заготовки, нагревание, предварительная вытяжка заготовки, формование, охлаждение, вырубка и извлечение готового изделия.
|
3. Расчет размеров листовой заготовки
Рассчитать необходимые размеры листовой заготовки можно по формуле:
L = [ nl + 2 z + (n - 1) z 1]·(1 + У/100). (16)
Здесь L – размер листовой заготовки, мм; n – число гнезд, расположенных вдоль искомой стороны заготовки; l – размер изделия, мм; z – припуск на зажим (z = 1÷10,0 мм в зависимости от размеров и конфигурации изделия, а также от конструкции зажимного устройства); z 1 – расстояние между гнездами; У – усадка заготовки при нагреве (зависит от температуры формования).
На практике усадку листа определяют следующим образом: вырезают из листа три образца размером 120x120 мм: один образец вырезают из центра листа, а два других на расстоянии 30 мм от каждого края. На образцах проводят две взаимоперпендикулярные линии – вдоль листа и в поперечном направлении и окружность диаметром 100 ± 5 мм. Образцы помещают в термостат. После нагревания измеряют диаметр деформированной в результате усадки окружности в продольном и поперечном направлениях и вычисляют усадку:
У = (D – D о) · 100/ D, (17)
где D и D о – диаметр окружности до и после нагревания образца.
4. Расчет времени нагрева заготовки
Наиболее часто для нагревания листов применяют инфракрасные нагреватели. При таком нагреве по толщине листа возникает большой температурный градиент Т. Разность температур на поверхностях листа зависит от мощности нагревателя, толщины листа и его теплопроводности.
В качестве нагревателей используют элементы сопротивления, изготовленные из нихромовой проволоки, лент или стержней.
Проволочные элементы со стеклянной изоляцией имеют максимальную температуру поверхности 643-693 К. Удельная мощность таких нагревателей при максимальной температуре равна 2,2 – 3,3 Вт/см2. Керамическая изоляция позволяет поднять температуру поверхности нагревателя до 873 К, а удельную мощность довести до 6 Вт/см2. Недостатком керамической изоляции является большая масса нагревателя.
Рабочая температура ленточных и стержневых нагревателей составляет 773 – 1073 К. Их удельная мощность зависит от плотности монтажа отдельных элементов и достигает 10 Вт/см2.
Рабочая температура трубчатых нагревателей достигает 1023–1273 К.
Вольфрамовая спираль кварцевых излучателей, трубка которых заполнена инертным газом, нагревается до 2473 К. Эти нагреватели работают в коротковолновом диапазоне инфракрасного излучения. Они обладают малой инерционностью и высоким КПД.
В любом случае конструкция нагревателей должна быть такой, чтобы изменение величины поверхности обогрева (за счет отключения части элементов) обеспечивало соответствие поверхности рабочей (тепловой) зоны нагревателей, поверхности любого установленного в данный момент зажимного устройства.
Приближенно продолжительность нагрева листовой заготовки можно рассчитать, определив тепловой поток, излучаемый нагревателем.
|
В соответствии с законом Стефана – Больцмана интенсивность излучения нагревателя g (в кДж/с) можно определить по формуле:
g = CS εφ S н [(Т 1 /100)4- (Т 2 /100)4]. (18)
S н = S /(0,91÷0,95). (19)
Здесь CS = 5,7 · 10-3 кДж / (м2 ·с ·К4) – константа излучения абсолютно черного тела; ε = 0,8÷0,9 – приведенная степень черноты для параллельных поверхностей пластика и радиационного нагревателя; φ – коэффициент использования лучистого потока, зависящий от соотношения размеров заготовки и нагревателя, а также от расстояния между ними (принимают φ = 0,45÷0,65); S н – общая площадь нагревателя, м2; Т 1 – температура на поверхности нагревателя, К; Т 2 – средняя температура листовой заготовки за цикл нагрева, К;
Т 2 = (Т к + Т н) / 2, (20)
Т н, Т к – начальная и конечная температура листовой заготовки, К.
Количество лучистой теплоты, которое должна получить полимерная заготовка, чтобы нагреться до требуемой температуры, можно определить по формуле:
E = S δρср с ср (Т к – Т н), (21)
где S – площадь листовой заготовки, м2; δ – толщина заготовки, м; ρср –среднее значение плотности полимерного листа, кг/м3; с ср – среднее значение удельной теплоемкости в интервале температур разогрева (Т к – Т н).
Удельная теплоемкость с (в Дж / (кг·К)) для разных полимеров при различных температурах рассчитывается следующим образом.
Для ПЭВД:
t, оС | с, Дж / (кг.К) |
20 – 108 оС | (1,8 t 3 – 249 t 2 + 12600 t – 26000) · 10-2 |
108 – 115 оС | 91000 – 775 t |
Выше 115 оС | 1160 + 5,24 t |
Для ПЭНД:
t, оС | c, Дж / (кг. К) |
20 – 120 | 18,8 t + 262 |
120 – 128 | 1080 t + 127500 |
128 – 134 | 198500 – 1470 t |
134 - 180 | 1380 + 8 t |
Для наполненных ПВХ
t,оС | с, Дж / (кг. К) |
20 – 140 | 3,07 t + 778 |
140 - 180 | 1820 – 4,48 t |
Для пластифицированных ПВХ
t, оС | с, Дж / (кг.К) |
20 – 180 | 5 t + 960 |
180 – 200 | 3660 – 10 t |
Для ПС
t, оС | с, Дж / (кг.К) |
20 – 110 | 7,3 t + 686 |
110 – 150 | 246 + 8,95 t |
150 – 190 | 3,5 t + 630 |
Время нагрева листовой заготовки τн (с) можно приближенно рассчитать по формуле:
τн = E / g = S δρср с ср (Т к – Т н)/ C Sεφ S н [(Т 1 /100)4 – (Т 2 /100)4]. (22)
ПРИМЕРЫ РАСЧЕТОВ
Пример 1. Рассчитать необходимые размеры листовой заготовки при изготовлении упаковочной тары с размерами 120х60 мм. Исходные данные: усадка вдоль листа У|| = 18 %, усадка в перпендикулярном (поперечном) направлении У = 10 %, z = 15 мм, z 1 = 10 мм, число гнезд в продольном направлении листа n || = 4, в поперечном n
= 6.
Решение.
L 1 = (4∙120 + 2∙15 + 3∙10) ∙(1 + 18/100) = 637 мм.
L 2 = (6∙60 + 2∙15 + 5∙10) ∙ (1 + 10/100) = 484 мм.
Пример 2. Рассчитать время нагрева листовой заготовки из ПЭВД. Исходные данные: толщина листа δ = 3 мм; площадь S = 0,3 м2. Поверхность нагревателя имеет температуру Т 1 = 700 К. Температура нагрева заготовки Т к = 403 К; Т н = 293 К, S н = 0,33 м2; Т 2 = (403+293)/2 = 348 К. Среднюю удельную теплоемкость с ср рассчитать при t = 20, 60, 110, 130 оС. Среднее значение плотности полимерного листа ρср = 874 кг/м3; ε = 0,9; φ = 0,6.
|
Решение.
τн = 0,3∙3∙10-3∙874∙2,8∙110/{(5,7∙10-3∙0,9∙0,6∙0,33 [74-(3,48)4]} = 105,8 с.
ЗАДАЧИ
1. Рассчитать площадь поверхности листовой заготовки при изготовлении изделия с размерами 170х110 мм. Исходные данные: усадка вдоль листа У|| = 12 %, усадка в перпендикулярном направлении У = 8 %; z = 10 мм, z 1 = 10 мм, число гнезд в продольном направлении листа n || = 6, в поперечном n
= 8.
2. Рассчитать размеры изделия, заготовка которой имеет размеры 520х280 мм. Исходные данные: У|| = 15 %, У = 11 %; z = 12 мм, z 1 = 10 мм, n || = 5, n
= 7.
3. Рассчитать необходимые размеры листовой заготовки при изготовлении изделия с размерами 13х5 см. Исходные данные: У|| = 16 %, У = 9 %; z = 12 мм, z 1 = 1,2 см, n || = 4, n
= 6.
4. Рассчитать необходимые размеры листовой заготовки при изготовлении изделия с размерами 130х70 мм. Исходные данные: У|| = 17 %, У = 10 %; z = 9 мм, z 1 = 15 мм, n || = 6, n
= 8.
5. Рассчитать необходимые размеры листовой заготовки при изготовлении изделия с размерами 110х80 мм. Исходные данные: У|| = 15 %, У = 8 %; z = 10 мм, z 1 = 12 мм, n || = 5, n
= 10.
6. Рассчитать площадь поверхности листовой заготовки при изготовлении изделия с размерами 160х90 мм. Исходные данные: У|| = 11 %, У = 6 %; z = 12 мм, z 1 = 15 мм, n || = 5, n
= 7.
7. Рассчитать площадь поверхности листовой заготовки при изготовлении изделия с размерами 150х80 мм. Исходные данные: У|| = 18 %, У = 10 %; z = 10 мм, z 1 = 12 мм, n || = 4, n
= 7.
8. Рассчитать размеры изделия, заготовка которой имеет размеры 480х250 мм. Исходные данные: У|| = 16 %, У = 9 %; z = 10 мм, z 1 = 15 мм, n || = 5, n
= 8.
9. Рассчитать размеры изделия, заготовка которой имеет размеры 515х270 мм. Исходные данные: У|| = 15 %, У = 8 %; z = 8 мм, z 1 = 8 мм, n || = 6, n
= 9.
10. Рассчитать размеры изделия, заготовка которой имеет размеры 530х290 мм. Исходные данные: У|| = 18 %, У = 9 %; z = 9 мм, z 1 = 15 мм, n || = 4, n
= 6.
11. Рассчитать время нагрева листовой заготовки из ПЭВД. Исходные данные: толщина листа δ = 5 мм, площадь S = 0,6 м2. Поверхность нагревателя имеет температуру Т 1 = 870 К. Температура нагрева заготовки Т к = 401 К; Т н = 293 К, S н = 0,37 м2; ρср = 876 кг/м3; с ср (при t = 20, 50, 110, 120 оС); ε = 0,9; φ = 0,6.
12. Рассчитать время нагрева листовой заготовки из ПЭНД. Исходные данные: толщина листа δ = 3 мм, площадь S = 0,4 м2. Поверхность нагревателя имеет температуру Т 1 = 700 К. Температура нагрева заготовки Т к = 136 оС; S н = 0,34 м2; ρср = 893 кг/м3; с ср (при t = 20, 60, 118, 130 оС); ε = 0,9; φ = 0,65.
13. Рассчитать время нагрева листовой заготовки из ПЭНД. Исходные данные: толщина листа δ = 4 мм, площадь S = 0,5 м2. Поверхность нагревателя имеет температуру Т 1 = 750 К. Температура нагрева заготовки Т к = 407 К; S н = 0,34 м2; ρср = 891 кг/м3; с ср (при t = 20, 70, 110, 132 оС); ε = 0,8; φ = 0,58.
14. Рассчитать время нагрева листовой заготовки из наполненного ПВХ. Исходные данные: толщина листа δ = 2 мм, площадь S = 0,3 м2. Поверхность нагревателя имеет температуру Т 1 = 800 К. Температура нагрева заготовки Т к = 497 К; S н = 0,36 м2; ρср = 1292 кг/м3; с ср (при t = 20, 60, 120, 150 оС); ε = 0,9; φ = 0,6.
15. Рассчитать время нагрева листовой заготовки из наполненного ПВХ. Исходные данные: толщина листа δ = 3 мм, площадь S = 0,36 м2. Поверхность нагревателя имеет температуру Т 1 = 780 К. Температура нагрева заготовки Т к = 493 К; S н = 0,32 м2; ρср = 1290 кг/м3; с ср (при t = 20, 50, 130, 150,170 оС); ε = 0,8; φ = 0,6.
16. Рассчитать время нагрева листовой заготовки из пластифицированного ПВХ. Исходные данные: толщина листа δ = 1,5 мм, площадь S = 0,4 м2. Поверхность нагревателя имеет температуру Т 1 = 700 К. Температура нагрева заготовки Т к = 500 К; S н = 0,33 м2; ρср = 1230 кг/м3; с ср (при t = 20, 60, 120, 160 оС); ε = 0,9; φ = 0,65.
17. Рассчитать время нагрева листовой заготовки из ПЭВД. Исходные данные: толщина листа δ = 2,5 мм, площадь S = 0,3 м2. Поверхность нагревателя имеет температуру Т 1 = 750 К. Температура нагрева заготовки Т к = 402 К; S н = 0,32 м2; ρср = 878 кг/м3; с ср (при t = 20, 40, 110, 130 оС); ε = 0,8; φ = 0,6.
18. Рассчитать время нагрева листовой заготовки из пластифицированного ПВХ. Исходные данные: толщина листа δ = 1,2 мм, площадь S = 0,38 м2. Поверхность нагревателя имеет температуру Т 1 = 800 К. Температура нагрева заготовки Т к = 493 К; S н = 0,36 м2; ρср = 1235 кг/м3; с ср (при t = 20, 70, 130, 160, оС); ε = 0,9; φ = 0,65.
19. Рассчитать время нагрева листовой заготовки из ПС. Исходные данные: толщина листа δ = 1,6 мм, площадь S = 0,34 м2. Поверхность нагревателя имеет температуру Т 1 = 800 К. Температура нагрева заготовки Т к = 529 К; S н = 0,35 м2; ρср = 998 кг/м3; с ср (при t = 20, 60, 80, 130 оС); ε = 0,9; φ = 0,6.
20. Рассчитать время нагрева листовой заготовки из ПС. Исходные данные: толщина листа δ = 1,5 мм, площадь S = 0,36 м2. Поверхность нагревателя имеет температуру Т 1 = 750 К. Температура нагрева заготовки Т к = 525 К; S н = 0,34 м2; ρср = 994 кг/м3; с ср (при t = 20, 70, 120, 170 оС); ε = 0,9; φ = 0,6.
СОДЕРЖАНИЕ ОТЧЕТА ПО РАБОТЕ
Отчет по работе должен содержать следующие разделы:
1. Цель работы.
2. Теоретические положения.
Раздел должен содержать основные определения, принципиальную схему процесса термоформования, основные параметры процесса.
3. Практическая часть.
Раздел должен содержать решение предложенных задач.
Контрольные вопросы
1. Какие полимеры перерабатывают методом термоформования?
2. Какими методами могут изготовляться изделия из листовых термопластов?
3. В чем преимущество пневмоформования?
4. В чем отличие однопозиционной машины для термоформования от многопозиционной?
5. Какими методами осуществляется вакуум-формование? В чем их отличие?
6. Какое свойство термопластичного листового материала используется при термоформовании?
7. Из каких технологических операций может состоять процесс термоформования?
8. Как определяют усадку листа на практике?
9. Какие нагреватели применяют в процессе термоформования?
& Библиографический список
1. Энциклопедия полимеров. В 3-х томах. М.: Советская энциклопедия, 1972. Т.1. 1224 с.; Т.2. 1032 с.; Т.3. 1150 с.
2. Швецов Г.А., Алимова Д.У., Барышникова М.Д. Технология переработки пластических масс. М.: Химия, 1988. 512 с.
3. Шембель А.С. Антипина О.М. Сборник задач и проблемных ситуаций по технологии переработки пластмасс. Л.: Химия, 1990. 272 с.
____________________________
Практическая работа № 3
|
|
История развития пистолетов-пулеметов: Предпосылкой для возникновения пистолетов-пулеметов послужила давняя тенденция тяготения винтовок...
Биохимия спиртового брожения: Основу технологии получения пива составляет спиртовое брожение, - при котором сахар превращается...
Своеобразие русской архитектуры: Основной материал – дерево – быстрота постройки, но недолговечность и необходимость деления...
Общие условия выбора системы дренажа: Система дренажа выбирается в зависимости от характера защищаемого...
© cyberpedia.su 2017-2024 - Не является автором материалов. Исключительное право сохранено за автором текста.
Если вы не хотите, чтобы данный материал был у нас на сайте, перейдите по ссылке: Нарушение авторских прав. Мы поможем в написании вашей работы!