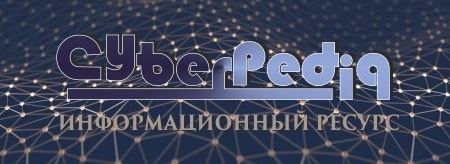
Автоматическое растормаживание колес: Тормозные устройства колес предназначены для уменьшения длины пробега и улучшения маневрирования ВС при...
Особенности сооружения опор в сложных условиях: Сооружение ВЛ в районах с суровыми климатическими и тяжелыми геологическими условиями...
Топ:
Эволюция кровеносной системы позвоночных животных: Биологическая эволюция – необратимый процесс исторического развития живой природы...
Методика измерений сопротивления растеканию тока анодного заземления: Анодный заземлитель (анод) – проводник, погруженный в электролитическую среду (грунт, раствор электролита) и подключенный к положительному...
Интересное:
Мероприятия для защиты от морозного пучения грунтов: Инженерная защита от морозного (криогенного) пучения грунтов необходима для легких малоэтажных зданий и других сооружений...
Отражение на счетах бухгалтерского учета процесса приобретения: Процесс заготовления представляет систему экономических событий, включающих приобретение организацией у поставщиков сырья...
Принципы управления денежными потоками: одним из методов контроля за состоянием денежной наличности является...
Дисциплины:
![]() |
![]() |
5.00
из
|
Заказать работу |
Содержание книги
Поиск на нашем сайте
|
|
С момента появления первых станков с ЧПУ до внедрения новейших обрабатывающих центров появились различные языки для программирования обработки. Сегодня программирование в G- и М-кодах является наиболее популярным. Язык G- и М-кодов основывается на положениях Международной организации по стандартизации (ISO) и Ассоциации электронной промышленности (EIA). Официально этот язык считается стандартом для американских и европейских производителей оборудования с ЧПУ, и иногда его называют «ИСО 7 бит». Однако производители систем ЧПУ хоть и придерживаются этих стандартов для описания основных функций, но допускают вольности и отступления от правил, когда речь заходит о каких-либо специальных возможностях своих систем.
Системы ЧПУ Fanuc (Япония) были одними из первых, адаптированных под работу с G- и М-кодами ISO и использующими этот стандарт наиболее полно. В настоящее время стойки Fanuc являются очень популярными и наиболее распространенными как за рубежом, так и в России. Поэтому в этой книге основой для описания программирования в G- и М-кодах будет именно стиль СЧПУ Fanuc.
Стойки ЧПУ других известных производителей, напримерHeidenhain и Sinumerik (Siemens), также имеют возможности по работе с G- и М-кодами, однако некоторые коды все же могут отличаться. Но не стоит этого пугаться. Нет никакой необходимости знать все коды всех систем ЧПУ. Достаточно знать набор основных G- и М-кодов, а о возникшей разнице в программировании специфических функций можно узнать из документации к конкретной системе. Освоив стиль программирования Fanuc, скорее всего, вы сможете работать на любом другом оборудовании с ЧПУ.
Некоторые производители систем ЧПУ предлагают диалоговый язык программирования. Этот язык упрощает общение с системой, особенно для новых операторов, так как основой для него служат англоязычные предложения, сокращения, вопросы и графические элементы, которые вводятся оператором станка в интерактивном режиме.
Процесс фрезерования
Существуют различные виды механической обработки: точение, фрезерование, сверление, строгание и т. д. Несмотря на конструкционные отличия станков и особенности технологий, управляющие программы для фрезерных, токарных, электроэрозионных, деревообрабатывающих и других станков с ЧПУ создаются по одному принципу. В этой книге основное внимание будет уделено программированию фрезерной обработки. Освоив эту разностороннюю технологию, вероят- нее всего, вы самостоятельно разберетесь и с программированием других видов обработки. Вспомним некоторые элементы теории фрезерования, которые вам обязательно пригодятся при создании управляющих программ и работе на станке.
Рис. 2.1. Процесс формирования кармана
Процесс фрезерования заключается в срезании с заготовки лишнего слоя материала для получения детали требуемой формы, размеров и шероховатости об- работанных поверхностей. При этом на станке осуществляется перемещение инструмента (фрезы) относительно заготовки или, как в нашем случае (для станка на рис. 1.4–1.5), перемещение заготовки относительно инструмента.
Для осуществления процесса резания необходимо иметь два движения – главное и движение подачи. При фрезеровании главным движением является враще- ние инструмента, а движением подачи – поступательное движение заготовки. В процессе резания происходит образование новых поверхностей путем деформирования и отделения поверхностных слоев с образованием стружки.
При обработке различают встречное и попутное фрезерование. Попутное фрезерование, или фрезерование по подаче, – способ, при котором направления движения заготовки и вектора скорости резания совпадают. При этом толщина стружки на входе зуба в резание максимальна и уменьшается до нулевого значения на выходе. При попутном фрезеровании условия входа пластины в резание более благоприятные. Удается избежать высоких температур в зоне резания и минимизировать склонность материала заготовки к упрочнению. Большая толщина стружки является в данном случае преимуществом. Силы резания прижимают заготовку к столу станка, а пластины – в гнезда корпуса, способствуя их надежному креплению. Попутное фрезерование является предпочтительным при условии, что жесткость оборудования, крепления и сам обрабатываемый материал позволяют применять данный метод.
Рис. 2.2. Попутное фрезерование
Встречное фрезерование, которое иногда называют традиционным, наблюдается, когда скорости резания и движение подачи заготовки направлены в противоположные стороны. При врезании толщина стружки равна нулю, на выходе – максимальна. В случае встречного фрезерования, когда пластина начинает работу со стружкой нулевой толщины, возникают высокие силы трения, отжимающие фрезу и заготовку друг от друга. В начальный момент врезания зуба процесс резания больше напоминает выглаживание, с сопутствующими ему высокими тем пературами и повышенным трением. Зачастую это грозит нежелательным упрочнением поверхностного слоя детали. На выходе из-за большой толщины стружки в результате внезапной разгрузки зубья фрезы испытывают динамический удар, приводящий к выкрашиванию и значительному снижению стойкости.
Рис. 2.3. Встречное фрезерование
В процессе фрезерования стружка налипает на режущую кромку и препятствует ее работе в следующий момент врезания. При встречном фрезеровании это может привести к заклиниванию стружки между пластиной и заготовкой и, со ответственно, к повреждению пластины. Попутное фрезерование позволяет избежать подобных ситуаций. На современных станках с ЧПУ, которые обладают высокой жесткостью, виброустойчивостью и у которых отсутствуют люфты в сопряжении ходовой винт-гайка, применяется в основном попутное фрезерование.
Припуск – слой материала заготовки, который необходимо удалить при обработке. Припуск можно удалить в зависимости от его величины за один или не- сколько проходов фрезы.
Принято различать черновое и чистовое фрезерования. При черновом фрезеровании обработку производят с максимально допустимыми режимами резания для выборки наибольшего объема материала за минимальное время. При этом, как правило, оставляют небольшой припуск для последующей чистовой обработки. Чистовое фрезерование используется для получения деталей с окончательными размерами и высоким качеством поверхностей.
Режущий инструмент
Весь инструмент, использующийся в металлообработке, можно условно подразделить на режущий инструмент (фрезы, сверла, метчики и др.), непосредственно осуществляющий механическую обработку (резание), и вспомогательный, служащий для закрепления режущего инструмента в шпинделе станка (патроны, державки, оправки).
Станки могут иметь различные базовые конусы шпинделя, а режущий инструмент, в свою очередь, изготавливается с различными видами хвостовиков.
Базовый конус станка – выход шпинделя, выполненный в соответствии с одним из стандартных вариантов исполнения. Различают метрические конусы (7:24 или ISO 7388.1), конусы Морзе (отечественные фрезерные станки или оборудование сверлильной группы), HSK (современные станки, предназначенные для высокоскоростной обработки).
Таким образом, вспомогательный инструмент является неким переходником между шпинделем станка и режущим инструментом. Совокупность режущего и вспомогательного инструментов называется инструментальным блоком. Отметим, что в инструментальном блоке могут находиться несколько вспомогательных инструментов и только один режущий (основной). Большие инструментальные блоки снижают жесткость технологической системы и уменьшают точность установки режущего инструмента, в результате чего ухудшаются условия обработки и качество изделия.
Рис. 2.4. Фрезы с механическим креплением режущих пластин
По технологическому признаку различают фрезы для обработки плоскостей, пазов и шлицев, зубчатых колес, резьбы, фасонных поверхностей, для разрезки материала и т. д.
По конструктивному признаку различают:
· по устройству фрезы (цельные, составные, со вставными зубьями);
· по конструкции зуба (с острозаточенными, с затылованными зубьями);
· по направлению зуба (прямые, наклонные, винтовые зубья);
· по способу крепления (насадные, хвостовые – с цилиндрическим или коническим хвостовиком).
По материалу, из которого они изготовлены: быстрорежущая сталь, твердый сплав и др. В современной инструментальной практике львиную долю составляет цель- ный твердосплавный или быстрорежущий инструмент, а также инструмент с механическим креплением режущих частей (пластин). Твердые сплавы допускают работу со скоростями резания, превышающими в 5–10 раз скорости обработки быстрорежущими инструментальными сталями, обладают большей температурной стойкостью и износостойкостью. При выборе фрезы технолог прежде всего руководствуется следующими параметрами:
· диаметр и длина рабочей части;
· форма профиля рабочей части;
· материал рабочей части;
· количество зубьев (режущих граней);
· форма и размер крепежной части.
Рис. 2.5. Цельные концевые фрезы
Обычная концевая фреза имеет несколько режущих зубьев (2, 3, 4, 6 или 8) и прямоугольный профиль режущей части. Зубья фрезы разделены винтовыми канавками, которые обеспечивают отвод стружки из зоны резания. В случае, когда необходимо получить переход от одной поверхности к другой с определенным радиусом, применяют фрезы со сферическим концом или с небольшим радиусом в основании профиля. Фрезы со сферическим концом и шаровые фрезы часто ис пользуются при обработке поверхностей сложной формы, например штампов и пресс-форм. Конические фрезы предназначены для фрезерования наклонных поверхностей и поднутрений.
Концевые фрезы наиболее универсальны – они позволяют обрабатывать плоскости, пазы и уступы. Существуют и другие типы фрез: торцовые, дисковые, пазовые. Эти фрезы, как правило, служат для выполнения фрезерных операций «узкой» направленности. Например, торцовая фреза – это лучший инструмент для фрезерования открытой плоскости, а дисковая – для обработки глубокого узкогопаза за один проход.
Рис. 2.6. Торцовая фреза и режущая пластина
Широкое распространение получили фрезы с механическим креплениемплас тин из твердого сплава и других инструментальных материалов. На корпусах таких фрез имеются специальные посадочные места, в которые устанавливаются пластины. Крепление пластин к стальному корпусу, как правило, осуществляется при помощи обычных винтов. Пластины имеют несколько граней, и в случае износа одной из них существует возможность развернуть пластину «свежей» гранью. Когда износятся все грани, то пластину можно выбросить и поставить новую. Получается очень экономичное решение, поскольку цельные твердосплавные фрезы стоят довольно дорого. Современные режущие пластины проектируются с учетом работы в различных условиях и отличаются геометрией передней поверхности.
Шаг зубьев фрезы может быть крупным, нормальным и мелким. Фрезы с различным шагом зубьев предназначены для различных условий обработки с точки зрения ее стабильности, энергозатрат и наличия склонности к вибрациям. Уменьшенное количество пластин – стандартное решение для производительной обработки при недостаточной мощности станка или низкой жесткости системы СПИД (станок – приспособление – инструмент – деталь). Фрезы с нормальным шагом универсальны для большинства операций. Мелкий шаг или максимальное число пластин на корпусе фрезы данного диаметра рекомендуется использовать для обработки при высокой жесткости системы СПИД, а также при фрезеровании материалов, дающих элементную стружку, титановых и жаропрочных сплавов.
На толщину срезаемого слоя при фрезеровании влияет главный угол в плане, который измеряется между главной режущей кромкой пластины и обрабатываемой поверхностью. Уменьшение угла в плане ведет к образованию более тонкой стружки для данного диапазона подач. Уменьшение толщины стружки происходит из-за распределения одного и того же объема снимаемого металла на большей длине режущей кромки. При меньшем угле в плане режущая кромка постепенно входит в работу и выходит из нее. Это уменьшает радиальную составляющую силы резания и защищает режущую кромку от возможных поломок. С другой стороны, неблагоприятным фактором является увеличение осевой составляющей силы резания, что вызывает ухудшение шероховатости поверхности тонкостенных деталей.
При угле в плане 90° сила резания направлена радиально в соответствии с направлением подачи. Основная область применения таких фрез – обработка прямоугольных уступов.
Рис. 2.7. Угол в плане 90°
При работе фрезой с углом в плане 45° осевые и радиальные силы резания практически одинаковы и потребляемая мощность невысока. Это фрезы универ- сального применения. Особенно они рекомендуются для обработки материалов, дающих элементную стружку и склонных к выкрашиванию при значительных радиальных усилиях на выходе инструмента. При врезании инструмента меньше нагрузка на режущую кромку и меньше склонность к вибрациям при закреплении в приспособлениях с небольшими усилиями зажима. Меньшая толщина срезаемого слоя при угле в плане 45° позволяет увеличивать минутную подачу стола, то есть повысить производительность обработки.
Фрезы с углом в плане 10° рекомендуются для продольного фрезерования с большими подачами и плунжерного фрезерования, когда характерны небольшие толщины стружки и высокие скоростные параметры. Преимуществом обработки такими фрезами являются низкие радиальные усилия резания. А также преобладание осевой составляющей силы резания как при радиальном, так и при осевом направлении подачи, что уменьшает склонность к вибрациям и предоставляет большие возможности для увеличения скоростей снятия материала.
Рис. 2.8. Угол в плане 45°
У фрез с круглыми пластинами главный угол в плане меняется от 0 до 90° в зависимости от глубины резания. Эти фрезы имеют очень прочную режущую кромку и могут работать при больших подачах, поскольку образуют довольно тонкую стружку на большой длине режущей кромки. Фрезы с круглыми пластинами рекомендуется применять для обработки труднообрабатываемых материалов, таких как титан и жаропрочные сплавы. Направление сил резания меняется вдоль радиуса пластины, поэтому направление суммарной нагрузки зависит от глубины резания. Современная геометрия круглых пластин делает их более универсальными, обеспечивая стабильность процесса резания, меньшую потребляемую мощность и, соответственно, меньшие требования к жесткости оборудования. В настоящее время эти фрезы широко используются для снятия больших объемов металла.
Вспомогательный инструмент
Основная задача вспомогательного инструмента – надежная фиксация режущего инструмента в шпинделе и передача ему крутящего момента от станка. В качестве вспомогательного инструмента на операциях фрезерования используютпатроны и оправки.
Оправки главным образом предназначены для операций с большими усилиями резания, таких как торцовое фрезерование, фрезерование пазов дисковыми фрезами, растачивание отверстий большого диаметра.
Элементом, передающим крутящий момент у оправок, является шпонка, которая предотвращает проворот режущего инструмента относительно оправки. Этим обеспечиваются надежное закрепление и передача крутящего момента. Однако оправки не способны обеспечить хорошее центрирование инструмента, поэтому основное их применение – черновые операции с удалением основного объема материала.
Патроны обеспечивают лучшее центрирование и обычно используются для зажатия режущих инструментов небольшого размера. Следует различать патроны с механическим креплением режущего инструмента (для сверл, инструментов с коническими хвостовиками типа конусов Морзе, WhistleNotch, Weldon и др.) и патроны с упруго-деформируемой зажимной частью (цанговые, гидромеханические, гидропластовые и др.).
Особое внимание следует уделить цанговым патронам (рис. 2.10), которые наиболее час то используются при работе на станках с ЧПУ. Принцип действия такого пат рона очень прост. В коническое отверстие патрона вставляются сменные цанги. Цанга имеет цилиндрическое отверстие, в которое устанавливается цилиндрический хвостовик режущего инструмента (диаметр хвостовика режущего инструмента должен соответствовать номеру цанги). При затягивании гайки давление передается на торец цанги, что приводит к вдавливанию последней в коническое отверстие патрона и сжатию в радиальном направлении. Сжимаясь, цанга передает давление на цилиндрический хвостовик режущего инструмента и надежно его закрепляет. После снятия давления (откручивания гайки) с цанги она разжимается и позволяет извлечь режущий инструмент из патрона.
Рис. 2.10. Цанговые патроны и сменные цанги
Основное преимущество цангового патрона – способность осуществлять закрепление широкого диапазона режущих инструментов при помощи комплекта сменных цанг. В комплекте цанг к одному и тому же патрону вы, как правило, найдете цанги для закрепления инструментов с хвостовиками от 6 до 30 мм и более. Цанга производит хорошее центрирование инструмента и надежное закрепление, однако плохо сбалансирована для скоростных методов обработки.
Следует уделять должное внимание вспомогательному инструменту, так как от него зависят: стойкость режущего инструмента, стабильность технологического процесса, точность и качество обработки.
Основные определения и формулы
Скорость резания V (м/мин) – это окружная скорость перемещения режущих кромок фрезы. Эта величина определяет эффективность обработки и лежит в рекомендованных для каждого инструментального материала пределах. За один оборот фрезы точка режущей кромки, находящаяся на окружности фрезы диаметра D (мм), сможет пройти путь, равный длине окружности, то есть πD. Для того чтобы определить длину пути, пройденного точкой за одну минуту, нужно умножить длину пути за один оборот на частоту вращения фрезы, то есть πDN (мм/мин). Таким образом, формула для определения скорости резания будет следующей:
V = πDN/1000 (мм/мин).
Частота вращения шпинделя N (об/мин) равняется числу оборотов фрезы в минуту. Вычисляется в соответствии с рекомендованной для данного типа обработки скоростью резания:
N = 1000V/nD (об/мин).
При фрезеровании различают минутную подачу, подачу на зуб и подачу наоборот фрезы.
Подача на зуб Fz (мм/зуб) – величина перемещения фрезы или рабочего стола с заготовкой за время поворота фрезы на один зуб.
Подача на оборот Fo (мм/об) – величина перемещения фрезы или рабочего стола с заготовкой за один оборот фрезы. Подача на оборот равняется произведению подачи на зуб на число зубьев фрезы Z:
Fo = FzZ (мм/об).
Минутной подачей Fm (мм/мин) называется величина относительного перемещения фрезы или рабочего стола с заготовкой за одну минуту. Минутная подача равняется произведению подачи на оборот на частоту вращения фрезы:
Fm = FoN = FzZN (мм/мин).
Глубиной фрезерования h (мм) называется расстояние между обработанной и необработанной поверхностями, измеряемое вдоль оси фрезы.
Шириной фрезерования b (мм) называется величина срезаемого припуска, измеренная в радиальном направлении, или ширина контакта заготовки и инструмента.
Производительность снятия материала Q (см3) – это объем удаляемого материала в единицу времени, определяемый глубиной, шириной обработки и величиной подачи.
Q = (h × b × Fm)/1000.
Рекомендации по фрезерованию
Выбор диаметра фрезы зависит, как правило, от ширины обрабатываемой заготовки, а также от мощностных характеристик станка. При этом важным фактором, определяющим успешное выполнение операции фрезерования, является взаимное расположение обрабатываемой поверхности и фрезы.
Ширина фрезерования особенно сильно влияет на выбор диаметра фрезы приобработке торцовыми фрезами. В этом случае рекомендуется выбирать диаметр фрезы, превышающий ширину фрезерования на 20–50%.
Если обработка может быть произведена за несколько проходов, то ширина резания за каждый проход должна быть равной 3/4 диаметра фрезы. При этом формирование стружки и нагрузка на режущую кромку будут оптимальными.
Рис. 2.11. Варианты расположения фрезы относительно заготовки
Когда диаметр фрезы значительно превышает ширину заготовки, то ось фрезы следует сместить с оси симметрии заготовки. Конечно, близкое расположение оси фрезы к оси заготовки позволяет обеспечить наикратчайший путь зубьев фрезы в металле, надежное формирование стружки на входе и благоприятную ситуацию относительно ударных нагрузок на пластину. Но когда ось фрезы расположена точно по оси симметрии заготовки, циклическое изменение силы резания при врезании и выходе может привести к возникновению вибраций, которые приведут к повреждению пластины и плохой шероховатости поверхности.
При торцевом фрезеровании по возможности избегайте фрезерования плоскостей с пересечением пазов и отверстий, так как при этом режущие кромки будут работать в неудовлетворительных условиях прерывистого резания. Выполняйте операцию изготовления отверстий после фрезерования. Если такой вариант невозможен, то при пересечении фрезой отверстия снижайте величину подачи на 50% от рекомендованной.
При обработке больших плоскостей старайтесь не прерывать контакт фрезы с заготовкой, обходя поверхность по периметру, а не за несколько параллельных проходов. Обработку углов необходимо осуществлять по радиусу, превышающему радиус фрезы, чтобы исключить возможность возникновения вибраций, связанных с резким увеличением угла охвата фрезы.
При обработке закрытого паза (замкнутой области) основная проблема заключается в трудности первоначального входа инструмента в материал заготовки, так как большинство концевых фрез плохо работают на засверливание. Существует несколько способов решения этой проблемы. Самый простой выход из ситуации – предварительно просверлить технологическое отверстие и затем спокойно опустить в него фрезу. Более интересные способы – маятниковое и спиральное врезания. В этом случае отпадает необходимость предварительного сверления, режущий инструмент входит в материал заготовки плавно.
![]() | ![]() |
![]() |
Особую осторожность нужно соблюдать при обработке тонкостенных карманов. Желательно, чтобы материал выбирался постепенно и обязательно при попутном способе фрезерования. В противном случае появляется вероятность «подрыва» тонкой стенки.
Обрабатывая внутренние радиусы, старайтесь, чтобы радиус фрезы был немного меньше, чем радиус в углу кармана (контура). Дело в том, что в момент, когда фреза входит в угол, ширина фрезерования возрастает скачкообразно, что может привести к «подхвату» инструмента и, как следствие, подрезать обрабатываемый контур или сломать фрезу. При назначении диаметра фрезы для черновой обработки внутренних радиусов желательно, чтобы оставляемый в углах припуск не превышал 0,20×D, где D – диаметр последующей чистовой фрезы.
При обработке глубоких контуров и уступов необходимо обеспечить достаточную жесткость инструмента во избежание его отжима и исключения «конусности» обработанной поверхности. Желательно, чтобы диаметр инструмента D удовлетворял условию H < 2,5D, где Н – максимальная высота стенки обрабатываемой детали.
Часто фрезерование производится в два этапа: черновой – контур обрабатывается послойно с небольшим припуском, чистовой – оставшийся припуск удаляется за один проход фрезы на финальной глубине.
Рис. 2.15. Простейшие способы подвода инструмента
При выполнении чернового и особенно чистового фрезерования инструмент следует подводить к обрабатываемой поверхности по касательной или по прямой линии под острым углом. Следуя этому правилу, необходимо и отводить инструмент. Дело в том, что при первоначальном врезании в материал заготовки фреза подвергается резкой нагрузке, что может привести к ее поломке или к тому, что на поверхности детали в месте входа фрезы в материал останется след или неровность. Если врезание будет плавным, то нагрузка на инструмент будет возрастать постепенно и поверхность останется «чистой».
|
|
Адаптации растений и животных к жизни в горах: Большое значение для жизни организмов в горах имеют степень расчленения, крутизна и экспозиционные различия склонов...
Архитектура электронного правительства: Единая архитектура – это методологический подход при создании системы управления государства, который строится...
Общие условия выбора системы дренажа: Система дренажа выбирается в зависимости от характера защищаемого...
История создания датчика движения: Первый прибор для обнаружения движения был изобретен немецким физиком Генрихом Герцем...
© cyberpedia.su 2017-2025 - Не является автором материалов. Исключительное право сохранено за автором текста.
Если вы не хотите, чтобы данный материал был у нас на сайте, перейдите по ссылке: Нарушение авторских прав. Мы поможем в написании вашей работы!