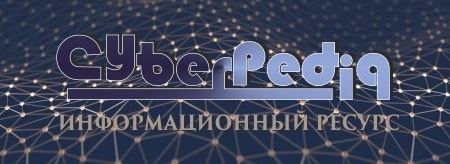
Таксономические единицы (категории) растений: Каждая система классификации состоит из определённых соподчиненных друг другу...
Типы оградительных сооружений в морском порту: По расположению оградительных сооружений в плане различают волноломы, обе оконечности...
Топ:
Особенности труда и отдыха в условиях низких температур: К работам при низких температурах на открытом воздухе и в не отапливаемых помещениях допускаются лица не моложе 18 лет, прошедшие...
Установка замедленного коксования: Чем выше температура и ниже давление, тем место разрыва углеродной цепи всё больше смещается к её концу и значительно возрастает...
Комплексной системы оценки состояния охраны труда на производственном объекте (КСОТ-П): Цели и задачи Комплексной системы оценки состояния охраны труда и определению факторов рисков по охране труда...
Интересное:
Подходы к решению темы фильма: Существует три основных типа исторического фильма, имеющих между собой много общего...
Уполаживание и террасирование склонов: Если глубина оврага более 5 м необходимо устройство берм. Варианты использования оврагов для градостроительных целей...
Средства для ингаляционного наркоза: Наркоз наступает в результате вдыхания (ингаляции) средств, которое осуществляют или с помощью маски...
Дисциплины:
![]() |
![]() |
5.00
из
|
Заказать работу |
|
|
СОДЕРЖАНИЕ
Содержание………………………………………………………………………………….2
Раздел 1. Основы организации и технологии ремонта машин……………………………...4
Тема 1.2. Виды и методы ремонта машин……………………………….………………….4-5
Раздел 2. Производственный процесс ремонта машин………………………………………8
Тема 2.1. Прием автомобилей и агрегатов в ремонт…………………………..……………8
2. Приемка автомобилей и агрегатов в ремонт и их хранение…………..……………….9
Тема 2.2. Разборка автомобилей и агрегатов…………………..……………………………10
3. Организация разборочных работ………………………………..………………………11
4. Особенности разборки резьбовых соединений и соединений с натягом
Тема 2.4. Дефектация и сортировка деталей……………………..………………………...14
5. Назначение и сущность дефектации и сортировки деталей……………………….….14
6. Капиллярные методы дефектации (контроля) деталей…………………………….….17
7. Контроль скрытых дефектов деталей (специальные методы дефектоскопии: магнитный, ультразвуковой)…………………………………………………………………………..…20
Раздел 3. Основные способы восстановления деталей………………………………….…..27
Тема 3.1. Классификация способов восстановления деталей……………………………...27
8. Классификация и краткая характеристика наиболее распространенных
способов восстановления деталей…………………………………………………………..27
9. Восстановление деталей слесарно-механической обработкой………………………….27
10. Ремонт резьбовых отверстий и трещин в корпусных деталях...………………... …….30
|
11. Классификация основных способов сварки и наплавки их краткая характеристика, материалы, область применения……………………………………………………………..30
Тема 3.3. Восстановление деталей сваркой и наплавкой…………………………………….33
12. Восстановление деталей наплавкой под слоем флюса (сущность, применяемое оборудование, достоинства и недостатки способа); материалы применяемые при наплавке под слоем флюса (проволоки, флюсы)…………………………………………………………….33
13. Восстановление деталей вибродуговой наплавкой (сущность процесса, применяемые материалы и оборудование, область применения)………………….……………………….36
14. Электроконтактная сварка и наплавка (приварка ленты, проволоки, порошка). Сущность процесса, область применения, достоинства и недостатки…………………..……………...38
15. Основные виды сварки. Подготовка поверхностей перед сваркой…………………….40
16. Автоматическая наплавка в среде защитных газов (сущность процессов, оборудование, применяемые материалы, достоинства, недостатки)…………………………………............44
17. Восстановление деталей электроискровой обработкой (сущность, оборудование, достоинство, недостатки)…………………………………………………………………….45
Тема 3.4. Восстановление деталей пайкой…………………………………………………...48
18. Восстановление деталей пайкой (сущность процесса, технология, припои и флюсы, применяемые при пайке, достоинства, недостатки)……………………………………….48
Тема 3.5. Восстановление деталей напылением…………………………………………….51
19. Восстановление деталей напылением (металлизацией). Виды, сущность, применяемое оборудование, материалы……………………………………………………...........….…...51
Тема 3.6. Восстановление деталей давлением (пластические деформации)…..….………54
20. Восстановление деталей давлением (пластическим деформированием: сущность, назначение, виды)………………………………………………………………...…...……..54
Тема 3.7. Восстановление деталей электролитическими покрытиями…………………....55
|
21. Восстановление деталей электролитическими покрытиями: сущность
процесса, достоинства, недостатки………………………………………………………….56
22. Восстановление деталей хромированием: применяемое оборудование
материалы, технологический процесс, область применения………………………………57
23. Восстановление деталей осталиванием. Свойства покрытий, электролиты, оборудование, преимущества способа……………………………………………………………………….62
Тема 3.8. Восстановление деталей с применением синтетических материалов…………...64
24. Восстановление деталей полимерными материалами (синтетическими): применяемые материалы, оборудование……………………………………………………………………64
Раздел 4. Ремонт типовых деталей…………………………………………………………..67
Тема 4.1. Выбор способа ремонта деталей, разработка технологических
процессов ремонта и изготовления типовых деталей………………………….……………67
25. Выбор рационального способа ремонта деталей, факторы, влияющие
на выбор способа ремонта…………………….…….……………………………………….67
Раздел 1.
Тема 1.2. Виды и методы ремонта машин
Раздел 2.
Технология капитального ремонта автомобилей.
Тема 2.1. Прием автомобилей и агрегатов в ремонт.
Тема 2.2. Разборка автомобилей и агрегатов
Особенности разборки резьбовых соединений и соединений с натягом.
Тема 2.4. Дефектация и сортировка деталей
Капиллярные методы дефектации (контроля) деталей
Раздел 3.
Основные способы восстановления деталей.
Тема 3.1. Классификация способов восстановления деталей.
Тема 3.2.
Восстановление деталей слесарно-механической обработкой.
Основные виды сварки. Подготовка поверхностей перед сваркой.
Сваркой называют технологический процесс получения механически неразъемных соединений, характеризующихся непрерывностью структур – непрерывной структурной связью.
Механическая сварка.
Она же сварка взрывом. Выделение тепла происходит за счет трения между соединяемыми материалами. Трение происходит за счет взрыва, который сжимает соприкасающиеся поверхности деталей. Данный метод применяется для плакирования металлов инородным материалом. Например, сталь плакируется алюминием.
Термическая сварка.
Данный тип сварки включает в себя несколько разновидностей, которые мы сейчас и рассмотрим.
|
Электродуговая сварка.
Данный вид сварки наиболее часто используемый. Расплавление свариваемых материалов и/или деталей происходит за счет выделяемой электрической дугой теплоты. После застывания свариваемые поверхности образуют единое сварное соединение. Для данного типа сварки необходим сильноточный источник питания низкого напряжения. К его зажиму присоединяется сварочный электрод, к которому, в свою очередь, прикасается свариваемая деталь.
Основными «подвидами» электродуговой сварки являются: ручная дуговая сварка, сварка неплавящимся электродом, сварка плавящимся электродом, сварка под флюсом, электрошлаковая сварка.
Ручная дуговая сварка.
Является универсальным технологическим процессом. С её помощью можно производить сварочные работы в любом пространственном положении, из различных марок сталей, даже при отсутствии необходимого оборудования. Используется специальный покрытый флюсом электрод. Покрытие используется для защиты шва металла от внешних воздействий. Сварка проводится на постоянном токе прямой или обратной полярности и на переменном токе. Данный вид сварки применяется для выполнения коротких и криволинейных швов в труднодоступных местах, а также при монтажных работах.
Сварка неплавящимся электродом.
В качестве электрода используется стержень из графита или вольфрама. Температура плавления данных материалов выше температуры, при которой протекает сварочный процесс. Сварка чаще всего проводится в среде защитного газа (аргон, гелий, азот и их смесях) для защиты шва и электрода от влияния атмосферы. Сварку может проводить как без присадочного материала, так и с ним. В качестве присадочного материала используются металлические прутки, проволока, полосы.
Сварка плавящимся электродом.
В качестве электрода используется проволока (стальная, медная или алюминиевая), к которой через токопроводящий наконечник подводится ток. Электрическая дуга расплавляет проволоку, и для обеспечения её постоянной длины проволока подаётся автоматически механизмом подачи. Для защиты от атмосферы применяются защитные газы (аргон, гелий, углекислый газ и их смеси), подающиеся из сварочной головки вместе с электродной проволокой.
Сварка под флюсом.
В этом виде сварки конец электрода также представлен в виде металлической проволоки или стержня, на конец которой (-го) подается слой флюса. В качестве флюсов применяют прокаленную буру, борную кислоту, кремниевую кислоту и др. Флюсы используются в виде порошков, паст, водных растворов. Горение дуги происходит в газовом пузыре, находящемся между металлом и слоем флюса. Сама дуга при этом не видна. Благодаря этой технологии усиливается защита металла от вредного воздействия атмосферы и улучшается глубина проплавления металла.
Электрошлаковая сварка.
При электрошлаковой сварке в качестве электродов служат: электродная проволока, стержни, пластины. Источником теплоты является расплавленный шлак, через который протекает электрический ток. При этом теплота, выделяемая флюсом, расплавляет кромки свариваемых деталей и присадочную проволоку. Способ находит своё применение при сварке вертикальных швов толстостенных изделий. Электрошлаковую сварку используют в машиностроении для изготовления ковано-сварных и лито-сварных конструкций.
Плазменная сварка.
Источником теплоты является плазменная струя, получаемая при нагреве электрическим током электрода. Струя плазмы сжимается и ускоряется под действием электромагнитных сил, оказывая на свариваемое изделие как тепловое, так и газодинамическое воздействие. Теплом струи расплавляется основной металл около дуги, а также присадочный металл. Помимо сварки этот способ часто используется для наплавки, напыления и резки.
Электронно-лучевая сварка.
Источником теплоты является электронный луч. Луч получается за счёт термоэлектронной эмиссии с катода электронно-лучевой пушки. Данный вид сварки применяется в промышленных условиях в вакуумных камерах. Известна также технология сварки электронным лучом в атмосфере нормального давления, когда электронный луч покидает область вакуума непосредственно перед свариваемыми деталями.
|
Лазерная сварка.
Источником теплоты служит сфокусированный лазерный луч. Применяют твердотельные, газовые, жидкостные и полупроводниковые лазерные установки. Лазерный луч также используется для резки различных материалов. Основными достоинствами лазерной сварки являются: возможность вести процесс на больших скоростях, практически отсутствие деформаций изделия и узкий шов.
Газопламенная сварка.
Источником теплоты является газовый факел, образующийся при сгорании смеси кислорода и горючего газа. В качестве горючего газа могут быть использованы ацетилен, водород, пропан, бутан и их смеси. Тепло, выделяющееся при горении смеси кислорода и горючего газа, оплавляет свариваемые поверхности и присадочный материал с образованием сварочной ванны. Пламя может быть «окислительным» или «восстановительным», это регулируется количеством кислорода.
Термомеханическая сварка
Сварка происходит за счет нагревания свариваемых поверхностей. У этого вида сварки тоже имеются свои разновидности.
Контактная сварка.
При данном типе сварки изделия нагреваются, и происходит их деформация, что обеспечивает их взаимное проникновение. Свариваемые детали зажимаются в сварочных клещах, и по электродам пускают ток высокого напряжения, который плавит детали. Затем ток отключают и сильно сжимают клещи, из-за чего металл кристаллизируется, образуя, сварной шов.
Диффузионная сварка.
При диффузионной сварке соединяемые поверхности сдавливают и нагревают. Обычно этот процесс происходит в вакууме. В результате этого действия образуется сварочный шов. Данная технология весьма дорогостоящая и поэтому находит свое применение в основном в авиакосмической, электронной и инструментальной промышленности.
Кузнечная сварка.
Сваривание поверхностей происходит за счет ударов кованым молотом по раскаленным деталям. Данный тип сварки не надежен, малопроизводителен и пригоден для ограниченного числа сплавов. Кузнечная сварка на сегодняшний день практически нигде не используется.
Сварка высокочастотными токами.
Свариваемые изделия располагают вплотную друг к другу и разогревают за счет пропускания тока высокой частоты, затем детали сжимают. После этого полученному изделию необходимо остыть, и оно готово. Метод применяется в основном для изготовления труб и фасонных изделий из сортовой стали.
|
Разнообразие способов сварки, отраслей промышленности, в которых её используют, свариваемых материалов, видов конструкций и огромные объёмы применения позволяют охарактеризовать технологический процесс сварки, как один из важнейших в металлообработке
Подготовка к сварке предусматривает разметку, правку, резку, гибку, обработку кромок.
Правка. Цель этой операции — устранение деформаций. Сортовой и листовой металл небольшой толщины правится в холодном состоянии, а толстый (как и значительно деформированный) предварительно надо подогреть до 250—300°С.
Разметка выполняется с целью нанесения размеров Детали на металл. Разметка может быть выполнена индивидуально, по шаблонам, а также оптическим и машинным методами. Индивидуальная разметка — очень трудоемкий процесс. Шаблоны обычно изготовляют из алюминиевого листа. Для разметки используют инструменты: линейку, угольник, рулетку и чертилку.
Резка как этап подготовки к сварке может быть термической или механической. По производительности термическая резка уступает механической, но она более универсальна и позволяет точно выкроить заготовки разной геометрической формы (в том числе криволинейной). Механическая резка не может дать такой результат, так как возможности ножниц и прессов ограничены.
Кромки подготавливаются также двумя способами — термическим и механическим. Но чаще используется механический способ.
Кромки с односторонним или двусторонним скосом можно получить, используя одновременно два или три резака, расположенных под соответствующими углами. Механическая обработка кромок на станках выполняется для обеспечения требуемой точности сборки, для образования фасок, имеющих заданное очертание, в случаях, если технические условия требуют удаления металла с поверхности кромок после резки.
Гибка может осуществляться разным инструментом и разными способами, но классическим является гибка на листогибочных вальцах. Кроме этого используется и штамповка (в промышленных условиях).
Кроме этих операций обязательно надо хорошо очистить поверхности свариваемых деталей от грязи, ржавчины, окалины, масел.
Электроискровая обработка.
Общие сведения. Электроискровой способ обработки деталей основан на явлении электрической эрозии (разрушение материала электродов) при искровом разряде. Во время проскакивания искры между электродами поток электронов, движущийся с огромной скоростью, мгновенно нагревает часть поверхности анода до высокой температуры (10 000…15 000° С); металл плавится и даже переходит в газообразное состояние, в результате чего происходит взрыв. Частицы оторвавшегося расплавленного металла анода выбрасываются в межэлектродное пространство и в зависимости от его среды (газовая или жидкая) достигают катода и оседают на нем или рассеиваются. Это свойство искрового разряда (обработке)- к аноду. Инструменту (одному из электродов) придают колебательное движение от вибратора для замыкания и размыкания цепи и получение искрового разряда. Необходимый режим устанавливают применением переменного сопротивления и постоянной или переменной емкости конденсаторов, но имеются установки и без конденсаторов.
Режимы электроискровой обработки определяются в основном силой тока и ориентировочно делятся на три группы: грубые- ток от 1 до 10А (на этих режимах получается небольшая производительность - съем или наращивание металла, но шероховатость поверхности большая – 1-го и 2-го классов); средние- ток от 1 до 10 А (шероховатость 2…4-го классов); чистые- ток менее 1 А (шероховатость до 10-го класса, но низкая производительность).
При ремонте машин электроискровую обработку применяют для обдирки деталей после наплавки твердыми сплавами, наращивания и упрочнения изношенных поверхностей, а также для удаления сломанных сверл, метчиков, шпилек, болтов и других деталей, вырезание канавок и прошивки отверстий любой конфигурации в металле любой твердости.
Для вырезки углублений и прошивки отверстий изготавливают инструмент из меди или ее сплавов по форме необходимого профиля и подключают ее к катоду. Процесс лучше вести в жидкой среде (керосин, минеральное масло и другие жидкости, не проводящие электрический ток), чтобы исключить наращивание инструмента(катода).
Наращивание и упрочнение деталей- наиболее перспективные приемы использования электроискровой обработки при ремонте машин. Эти процессы ведут на установках, изготовленных по схеме. Деталь, подключенная к катоду, наращивается инструментом (анодом), изготовленным из материала, предназначенного для нанесения на поверхность детали. Колебание анод получает от магнитного вибратора, подключенного к сети переменного тока обычной частоты. Этим способом получают покрытия до 0,5 мм.
При наращивании посадочных мест под подшипники в корпусных чугунных деталях в качестве анода часто применяют медный наконечник или вращающийся от гибкого вала диск. Наращивание поверхности проводят вручную, вводя анод в посадочное место.
ЭЛЕКТРОИСКРОВЫЕ СТАНКИ
Электроискровые станки изготавливаются универсальными и специализированными.
Универсальный прошивочно-копировальный электро-искровой станок. Станок предназначен для изготовления электроискровым способом сквозных и глухих отверстий произвольной формы в любых токопроводящих материалах, преимущественно трудно обрабатываемых. На станке могут изготовляться ковочные и вырубные штампы, а также пресс формы, прошиваться отверстия в закаленных сталях и деталях из твердых сплавов. Осуществлению указанных операций должен обязательно предшествовать технико-экономический расчет, так как не во всех случаях эффективно производить указанные операции на этом станке. Эффективность увеличивается при обработке деталей из трудно обрабатываемых сплавов, при сложной конфигурации детали или выполнении операций, не поддающихся механической обработке.
На электроискровых станках можно прошивать отверстия, начиная с диаметра 0,1 мм, а в некоторых случаях и ниже, что механическим сверлением осуществить трудно.
Электролитическими
Покрытиями.
Раздел 4.
СОДЕРЖАНИЕ
Содержание………………………………………………………………………………….2
Раздел 1. Основы организации и технологии ремонта машин……………………………...4
Тема 1.2. Виды и методы ремонта машин……………………………….………………….4-5
Раздел 2. Производственный процесс ремонта машин………………………………………8
Тема 2.1. Прием автомобилей и агрегатов в ремонт…………………………..……………8
2. Приемка автомобилей и агрегатов в ремонт и их хранение…………..……………….9
Тема 2.2. Разборка автомобилей и агрегатов…………………..……………………………10
3. Организация разборочных работ………………………………..………………………11
4. Особенности разборки резьбовых соединений и соединений с натягом
Тема 2.4. Дефектация и сортировка деталей……………………..………………………...14
5. Назначение и сущность дефектации и сортировки деталей……………………….….14
6. Капиллярные методы дефектации (контроля) деталей…………………………….….17
7. Контроль скрытых дефектов деталей (специальные методы дефектоскопии: магнитный, ультразвуковой)…………………………………………………………………………..…20
Раздел 3. Основные способы восстановления деталей………………………………….…..27
Тема 3.1. Классификация способов восстановления деталей……………………………...27
8. Классификация и краткая характеристика наиболее распространенных
способов восстановления деталей…………………………………………………………..27
9. Восстановление деталей слесарно-механической обработкой………………………….27
10. Ремонт резьбовых отверстий и трещин в корпусных деталях...………………... …….30
11. Классификация основных способов сварки и наплавки их краткая характеристика, материалы, область применения……………………………………………………………..30
Тема 3.3. Восстановление деталей сваркой и наплавкой…………………………………….33
12. Восстановление деталей наплавкой под слоем флюса (сущность, применяемое оборудование, достоинства и недостатки способа); материалы применяемые при наплавке под слоем флюса (проволоки, флюсы)…………………………………………………………….33
13. Восстановление деталей вибродуговой наплавкой (сущность процесса, применяемые материалы и оборудование, область применения)………………….……………………….36
14. Электроконтактная сварка и наплавка (приварка ленты, проволоки, порошка). Сущность процесса, область применения, достоинства и недостатки…………………..……………...38
15. Основные виды сварки. Подготовка поверхностей перед сваркой…………………….40
16. Автоматическая наплавка в среде защитных газов (сущность процессов, оборудование, применяемые материалы, достоинства, недостатки)…………………………………............44
17. Восстановление деталей электроискровой обработкой (сущность, оборудование, достоинство, недостатки)…………………………………………………………………….45
Тема 3.4. Восстановление деталей пайкой…………………………………………………...48
18. Восстановление деталей пайкой (сущность процесса, технология, припои и флюсы, применяемые при пайке, достоинства, недостатки)……………………………………….48
Тема 3.5. Восстановление деталей напылением…………………………………………….51
19. Восстановление деталей напылением (металлизацией). Виды, сущность, применяемое оборудование, материалы……………………………………………………...........….…...51
Тема 3.6. Восстановление деталей давлением (пластические деформации)…..….………54
20. Восстановление деталей давлением (пластическим деформированием: сущность, назначение, виды)………………………………………………………………...…...……..54
Тема 3.7. Восстановление деталей электролитическими покрытиями…………………....55
21. Восстановление деталей электролитическими покрытиями: сущность
процесса, достоинства, недостатки………………………………………………………….56
22. Восстановление деталей хромированием: применяемое оборудование
материалы, технологический процесс, область применения………………………………57
23. Восстановление деталей осталиванием. Свойства покрытий, электролиты, оборудование, преимущества способа……………………………………………………………………….62
Тема 3.8. Восстановление деталей с применением синтетических материалов…………...64
24. Восстановление деталей полимерными материалами (синтетическими): применяемые материалы, оборудование……………………………………………………………………64
Раздел 4. Ремонт типовых деталей…………………………………………………………..67
Тема 4.1. Выбор способа ремонта деталей, разработка технологических
процессов ремонта и изготовления типовых деталей………………………….……………67
25. Выбор рационального способа ремонта деталей, факторы, влияющие
на выбор способа ремонта…………………….…….……………………………………….67
Раздел 1.
Тема 1.2. Виды и методы ремонта машин
|
|
Двойное оплодотворение у цветковых растений: Оплодотворение - это процесс слияния мужской и женской половых клеток с образованием зиготы...
Поперечные профили набережных и береговой полосы: На городских территориях берегоукрепление проектируют с учетом технических и экономических требований, но особое значение придают эстетическим...
История развития пистолетов-пулеметов: Предпосылкой для возникновения пистолетов-пулеметов послужила давняя тенденция тяготения винтовок...
Историки об Елизавете Петровне: Елизавета попала между двумя встречными культурными течениями, воспитывалась среди новых европейских веяний и преданий...
© cyberpedia.su 2017-2024 - Не является автором материалов. Исключительное право сохранено за автором текста.
Если вы не хотите, чтобы данный материал был у нас на сайте, перейдите по ссылке: Нарушение авторских прав. Мы поможем в написании вашей работы!