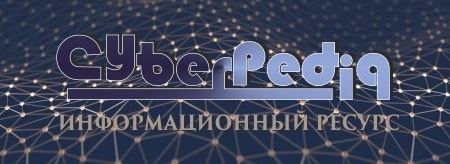
Кормораздатчик мобильный электрифицированный: схема и процесс работы устройства...
История создания датчика движения: Первый прибор для обнаружения движения был изобретен немецким физиком Генрихом Герцем...
Топ:
Методика измерений сопротивления растеканию тока анодного заземления: Анодный заземлитель (анод) – проводник, погруженный в электролитическую среду (грунт, раствор электролита) и подключенный к положительному...
Проблема типологии научных революций: Глобальные научные революции и типы научной рациональности...
Интересное:
Мероприятия для защиты от морозного пучения грунтов: Инженерная защита от морозного (криогенного) пучения грунтов необходима для легких малоэтажных зданий и других сооружений...
Как мы говорим и как мы слушаем: общение можно сравнить с огромным зонтиком, под которым скрыто все...
Подходы к решению темы фильма: Существует три основных типа исторического фильма, имеющих между собой много общего...
Дисциплины:
![]() |
![]() |
5.00
из
|
Заказать работу |
|
|
Информация о комплектующих составных частях изделия характерна для документов, разрабатываемых на технологические процессы сборки, является основной и в связи с этим записывается в операциях перед указанием информации о материалах. К указанной информации относят:
- наименование детали (сборочной единицы);
- обозначение, код детали (сборочной единицы);
- обозначение подразделения предприятия (ОПП), откуда поступают составные части изделия на сборку (склад, комплектующее отделение);
- код единицы величины или единица величины (ЕВ);
- единица нормирования (ЕН);
- количество составных частей, входящих в изделие (КИ).
Правила записи информации о требованиях к выполняемым действиям
Информация о требованиях к выполняемым действиям имеет массовый характер и применяется в документах при описании содержания операций.
Для описания содержания процесса (операций) в соответствии с ГОСТ 3.1109 применяют следующие три вида:
- маршрутное;
- операционное;
- маршрутно-операционное.
Описание операций всегда выполняют с привязкой к служебному символу "О".
Маршрутное описание ТП, в основном, следует применять в документах на процессы, выполняемые в опытном и мелкосерийном типах производства.
Примечание - Указанные типы производства характеризуют частой сменой объектов изготовления, применением в основном средств технологического оснащения универсального назначения и рабочих высокой квалификации, что позволяет в такой ситуации пользоваться упрощенной документацией.
Выбор маршрутного описания операций устанавливает разработчик документов.
Не рекомендуется применять маршрутное описание для операций, связанных с опасностью выполняемых работ, с надежностью изготовления изделий и их эксплуа-тацией и т.п., например, операции литья, ковки, штамповки, сварки, пайки, обработки и др.
|
Маршрутное описание следует применять для операций обработки резанием, разъемной сборки, отдельных действий, связанных с техническим контролем.
Примечание - Выполнение таких операций не связано с жесткой регламентацией режимов (за исключением операций обработки резанием, но в этих случаях квалификация исполнителей позволяет за счет производственного опыта самостоятельно настраивать оборудование на оптимальный режим работы).
Последовательность записи содержания операции маршрутного описания следующая:
- ключевое слово;
- дополнительная информация;
- наименование предметов производства, обрабатываемых поверхностей и конструктивных элементов;
- условное обозначение поверхностей конструктивных элементов и указание параметров;
- дополнительная информация.
Запись содержания операции следует начинать с ключевого слова, которое характеризует выполняемое действие, выраженное глаголом в неопределенной форме, например, точить, собрать, проверить и т.п.
На втором месте при необходимости следует указывать дополнительную информацию, под которой подразумевают одновременное количество обрабатываемых, собираемых (проверяемых и т.п.) поверхностей деталей (элементов деталей), собираемых составных частей изделия, контролируемых параметров и т.п., например:
"Сверлить 4 отверстия..."
"Собрать 2 прокладки...".
На третьем месте, при необходимости, также вводят уточняющую информацию, характеризующую вид предмета производства, обрабатываемой поверхности и т.п., например:
"Сверлить 4 сквозных отверстия..."
"Установить 2 герметизирующие прокладки..."
Примечание - Дополнительная информация, приведенная в 12.3.4.2 и 12.3.4.3, не имеет обязательного характера и устанавливается разработчиком документов по своему усмотрению.
|
На четвертом месте, а может быть на 2-м или 3-м, в структуре описания содержания операции предусматривают указание наименования предметов производства, обрабатываемых поверхностей и конструктивных элементов, например:
"Точить поверхности..."
"Фрезеровать фасонную поверхность..."
"Развернуть два глухих отверстия...".
На пятом месте предусматривают указание условных обозначений поверхностей, конструктивных элементов и параметров. Под условными обозначениями поверхностей и конструктивных элементов следует понимать соответствующие обозначения, применяемые разработчиком документов в целях исключения текстовой записи, например:
"" - диаметр;
"" - длина;
"" - ширина;
"" - радиус;
"" - угол.
Указание такой информации рекомендуется выполнять с дополнительным словом - "выдерживая...", например:
"Точить поверхности, выдерживая ;
; =7±0,2; =12±0,2...";
"Строгать уклон, выдерживая < 45°...".
Допускается в тексте для отдельных размеров не приводить соответствующие условные обозначения поверхностей и конструктивных элементов (для указания длины, ширины, углов и т.д.), например:
"Точить поверхности, выдерживая ;
; 7±0,2; 12±0,2...";
"Строгать уклон, выдерживая 45°
...".
На шестом месте предусматривают указание дополнительной информации, которая выражается в указании условных обозначений радиусов (); фасок () с данными, если они встречаются в тексте содержания операции, например:
"Точить поверхности, выдерживая ;
; =7±0,2; =12±0,2 с =2 …".
На седьмом месте предусматривают указание дополнительной информации, устанавливаемой по усмотрению разработчика документов, выражающейся в применении следующих слов: "окончательно"; "одновременно"; "по копиру"; "по программе"; "согласно чертежу"; "предварительно" и т.п.
Например "Точить поверхности, выдерживая ;
; 7±0,2; 12±0,2 с =1,5; =2,0 по копиру".
Помимо указанных предложений в тексте маршрутного описания следует дополнительно указывать и другие требования по выполнению операции, например указания по вспомогательным действиям, связанным с установкой на оборудование и снятием с оборудования крупногабаритных изделий, отражением действий по техническому контролю, например:
"Контроль производственным мастером - 10%, исполнителем - 100%";
|
"Уложить деталь в тару" и т.п.
Примечание - При маршрутном описании операций в тексте не должна отражаться информация по вспомогательным переходам. Исключение составляют действия, связанные с обработкой изделий большой массы и оказывающие влияние на охрану труда исполнителей.
Пример оформления технологического процесса маршрутного описания приведен в приложении «З».
Правила записи информации по технологической оснастке
Информацию по технологической оснастке следует записывать во всех документах, где описывают содержание операций.
Указанная информация может быть записана и в сводный документ по оснастке на процесс - в ведомость оснастки (ВО) по ГОСТ 3.1122.
В документах, где описывают содержание операции, указание информации по технологической оснастке выполняют после содержания:
операции - при маршрутном описании технологического процесса;
перехода - при операционном описании технологического процесса.
Порядок очередности записи информации по технологической оснастке в документах к операции и переходу представлен в таблице 12.
Таблица 12
Очередность записи информации | Наименование видов технологической оснастки |
Приспособление, штамп, пресс-форма, опока, кокиль, форма, модельный комплект и т.п. | |
Вспомогательный инструмент, наладки и базовым приспособлениям | |
Режущий инструмент, слесарный инструмент | |
Средства измерения (приборы, измерительные устройства, калибры, скобы и т.п.) |
В основном информация по технологической оснастке состоит из двух основных частей:
- обозначения;
- наименования, модели, типа обозначения стандарта и т.п.
Коды или обозначение технологической оснастки устанавливаются предприятиями (организациями) в соответствии с НД и записываются на первом месте в строке документа с привязкой к служебному символу "Т".
Наименование технологической оснастки следует указывать в соответствии с имеющимся технологическим паспортом или нормативной документацией (НД).
В целях сокращения текста записи наименования технологической оснастки рекомендуется применять допускаемые сокращения и обозначения.
|
Запись кода (обозначения) технологической оснастки следует выполнять перед ее наименованием с интервалом в 3-4 знака (рисунок 23).
Рисунок 23
При необходимости указания к операции (переходу) нескольких видов оснастки ее следует указывать в порядке очередности, представленной в таблице 2.
При маршрутном описании технологического процесса допускается указание по стандартизованной оснастке не приводить, при условии соответствующей организации производства и квалификации исполнителей.
В случае, если одно и то же обозначение технологической оснастки при операционном описании технологического процесса применяют в других переходах, в целях сокращения соответствующей информации и исключения ее дублирования, допускается после ее наименования (в том переходе, где ее применяют в первый раз) указывать в скобках номера соответствующих переходов (рисунок 24).
Рисунок 24
В этом случае в последующих переходах соответствующую информацию указывать не следует. Состав видов информации в привязке к служебным символам приведён в таблице13.
Состав видов информации в привязке к служебным символам Таблица 13
Номер подгрупп информации | Наименование подгрупп информации | Расположение поля подшивки в документе | Обозначение служебного символа | ||
горизонтальное | вертикальное | ||||
Адресная информация о технологическом процессе | + | + | - | ||
Адресная информация о операции (операциях) | + | + | А В | ||
Информация о применяемых в операции документах | + | + | А Г | ||
Информация о рабочих местах | + | + | Б Д | ||
Информация о трудозатратах | + | + | Б Е | ||
Информация о применяемых материалах | + | + | М | ||
Информация о комплектующих составных частях изделия | + | + | К Л, Н | ||
Информация общего характера к процессу и к операции | + | + | - | ||
Информация о требованиях к выполняемым действиям | + | + | О | ||
Информация о технологической оснастке | + | + | Т | ||
Информация о технологических режимах | + | + | Р | ||
Примечание - Состав указанной в таблице информации дан на примере форм МК, применяемых в качестве универсальных документов, обеспечивающих возможность использования взамен других видов. | |||||
Ход выполнения работы:
Тема: Заполнение карты технологического процесса ремонта ЭПС.
Цель работы: Приобрести навыки составления карты технологического
процесса ремонта ЭПС.
Ход работы:
1. Описать назначение карты технологического процесса ремонта.
2. Привести требования нормативно-технической документации к выбранному процессу ремонта.
3. Заполнить карту технологического процесса ремонта ЭПС на примере замены лобового стекла электровоза ВЛ-80с. (Допускается оформление карты эскизов на любую другую тему, связанную с ремонтной тематикой, выданную преподавателем).
|
При описании процесса необходимо учитывать требования нормативно – технической документации, предъявляемые к конкретному технологическому процессу.
Содержание отчёта:
7. Титульный лист
8. Пояснительная записка
9. Заполненная карта технологического процесса ремонта ЭПС на выбранный технологический процесс.
Практическая работа №5
Тема: Составление технолого-нормировочной карты (ТНК)
ТНК – документ, разрабатываемый совместно с другими технологическими документами к технологического процессу и содержащий расчетные данные по нормам времени и описанию приемов. Может составляться как на специальном бланке технолого-нормировочной карты, так и на основе маршрутной карты. Учитывая, что дополнительные графы для составления ТНК в МК не требуются, процесс рекомендуется разрабатывать на маршрутной карте (МК/ТНК).
При применении форм маршрутных карт (МК), выполняющих функции других видов документов, их следует оформлять в соответствии с требованиями стандартов ЕСТД. При этом в графе28 блока Б6 основной надписи, выполненной по ГОСТ 3.1103—82, следует проставлять через дробь условное обозначение соответствующего вида документа, функцию которого выполняет МК. Например, МК/КТПР, МК/КТПД, МК/КТТПО и т. д.
ТНК применяется при нормировании технологических процессов в массовом и серийном типах производства и не зависит от технологических методов обработки, изготовления, контроля и ремонта.
Правила записи информации о трудозатратах
Информацию о трудозатратах применяют в документах на процессы (МК, КТП, КТТП и т.п.) и операции.
Кроме указанных документов, исходная информация о нормировании труда исполнителей, участвующих в выполнении технологического процесса, содержится в технико-нормировочных картах.
В документах на процессы указывают полную информацию по трудозатратам на операции, которую рассчитывают по соответствующим технико-нормировочным и хронометражным картам, а также по расчетным данным, содержащимся в ОК.
Заполнение соответствующих граф, содержащих данные по трудозатратам в документах, предусматривающих внесение указанной информации, следует выполнять согласно существующим правилам заполнения по НД.
В документах на операцию указывают основные данные по расчету на операцию. В отличие от сводных документов на процесс они не содержат данных по степени механизации (СМ); обозначению или наименованию профессии (ПРОФ); разряду исполнителей (Р); условиям труда (УТ); количеству исполнителей, участвующих в выполнении операции (КР); единице нормирования (ЕН); коэффициенту штучного времени (Кшт.) и объему партии (ОП).
Основными документами, предусматривающими возможность машинной обработки информации по трудозатратам, являются документы на процессы.
Ответственность по расчету трудозатрат и заполнению соответствующих граф в документах устанавливается по усмотрению организации - разработчика документов.
При расчете трудозатрат исполнителем, ответственным за разработку комплекта документов на процесс, в блоке Б2 основных надписей по ГОСТ 3.1103 следует проставлять одну подпись в графе "Разраб.".
При расчете данных лицами, ответственными за разработку трудозатрат, соответствующую подпись следует выполнять в графе "Нормир.", расположенной на второй строке графы "Разраб.".
В условиях планомерного снижения данных по трудозатратам без изменений сущности процесса, а также при автоматизированной разработке документов допускается в документы на процесс их не вносить, а указывать в дополнительно вводимый в комплект документ МК/ТНК, КТП/ТНК и т.п.
Указанный документ должен иметь обозначение ТНК по ГОСТ 3.1201 и располагаться после сводного документа на процесс.
Соответствующую ссылку на его обозначение следует выполнять в МК(КТП, КТТП...) к любой первой операции в графе "Обозначение документа" (после ВО, КК, ВУД).
Пример оформления МК/ТНК приведен в приложении Е.
Ход выполнения работы:
Тема: Составление технолого-нормировочной карты.
Цель работы: Приобрести навыки составления карты технологического
процесса ремонта ЭПС.
Ход работы:
1. Описать назначение карты технологического процесса ремонта.
2. Привести требования нормативно-технической документации к выбранному процессу ремонта.
3. Заполнить технолого-нормировочную карту.
Содержание отчёта:
1. Титульный лист
2. Пояснительная записка
3. Заполненная карта технологического процесса ремонта
ЭПС на выбранный технологический процесс.
Практическая работа №6.
Проверка колёсной пары шаблонами и измерительным инструментом.
Сложные условия работы Э. П. С. вызывают ускоренное появление у его деталей различного вида износов, которые приводят к изменению геометрических параметров деталей, увеличению между ними зазоров, появлению местных вырывов металла, изменению поверхностной или внутренней структуры. Наиболее характерны износ от сил трения (механический), а также термический, электроэрозионный и коррозионный износы. При прохождении неровностей пути колесные пары э. п. с. воспринимают значительные динамические силы (особенно при высоких скоростях) В нарастании механического износа деталей любого механизма можно отметить три периода:- 1 приработки, 2 нормальной эксплуатации, усиленного износа. Наступление периода усиленного износа часто характеризуется возникновением шума, иногда нагрева, а затем и стука деталей. Если не принять необходимых мер, то дальнейшая работа механизма может вызвать поломку его деталей. Нормы предельно допустимых износов приведены в руководящих документах и установлены по результатам длительных наблюдений за работой узлов и точного обмера деталей. Основными руководящими документами при ремонте колёсных пар Электроподвижного состава в настоящий момент являются «инструкция по формированию, ремонту и содержанию колесных пар тягового подвижного состава железных дорог колеи 1520 мм ЦТ-439» и руководство по эксплуатации техническому обслуживанию и ремонту колёсных пар подвижного состава КМБШ.667120.001РЭ. Согласно требованиям этих документов колесные пары должны подвергаться осмотру под ТПС, обыкновенному и полному освидетельствованию.
Колесные пары для определения их технического состояния и пригодности к эксплуатации подвергаются осмотру с регистрацией в книге формы ТУ-28:
— под ТПС — при всех видах технических обслуживании и текущих ремонтов ТР-1, ТР-2, каждой проверке ТПС в эксплуатации;
— при первой подкатке под ТПС новой колесной пары (после формирования) и после производства полного освидетельствования, если после них прошло не более 2 лет. При этом проверка даты формирования и освидетельствования производится по клеймам на торце (бурте) оси;
— после крушений, аварий, схода с рельсов, если отсутствуют повреждения элементов колесной пары, требующие их замены.
При осмотре колесных пар проверять:
— на бандажах и ободьях цельнокатаных колес — отсутствие трещин, ползунов (выбоин), плен, раздавленностей, вмятин, отколов, раковин, выщербин, ослабления бандажей на ободе центра (остукиванием молотком), сдвига бандажа (по контрольным меткам на бандаже и ободе центра), предельного проката (предельной высоты гребня) или износа, вертикального подреза гребня, ослабления бандажного кольца, опасной формы гребня и остроконечного наката, являющегося признаком возможности опасной формы гребня.
Предельный прок ат (предельная высота гребня) и наличие опасной формы гребня проверяются шаблоном УТ-1 при технических обслуживаниях ТО-2 (при их выполнении в крытых помещениях), ТО-3, ТО-4, ТО-5, текущих ремонтах ТР-1, ТР-2 и ежемесячных обмерах колесных пар. Допускается при проведении технического обслуживания ТО-2 (для МВПС — ремонтными бригадами) контролировать опасную форму гребня шаблоном ДО-1. После выявления колес с опасной формой гребня с помощью этого шаблона необходимо шаблоном УТ-1 измерить величину этого параметра и по результатам этого измерения принимать решение о допуске их к эксплуатации или о назначении ремонта;
· на колесных центрах, цельнокатаных колесах и ступицах дискового тормоза — отсутствие трещин в спицах, дисках, ступицах, ободьях, признаков ослабления или сдвига ступиц на оси;
· на открытых частях осей — отсутствие поперечных, косых и продольных трещин, плен, протертых мест, электроожога и других дефектов;
· отсутствие нагрева букс;
· состояние зубчатой передачи тяговых редукторов ТПС (при текущих ремонтах, когда это предусмотрено по циклу);
· отсутствие нагрева моторно-осевых подшипников, опорных подшипников тяговых редукторов при постановке ТПС на смотровую канаву.
Обыкновенное освидетельствование колесных пар
Обыкновенное освидетельствование колесных пар производится при каждой подкатке под вагон, кроме колесных пар, не бывших в эксплуатации после последнего полного или обыкновенного освидетельствования.
При обыкновенном освидетельствовании колесных пар должны выполняться все проверки, предусмотренные осмотром колесных пар под ТПС и дополнительно проводиться:
— очистка от грязи и смазки или обмывка в моечной машине;
— проверка установленных клейм и знаков;
— проверка магнитным дефектоскопом открытых, частей осей, зубьев зубчатых колес, пальцев тягового привода, у локомотивов с гидравлическими и механическими приводами, имеющими кожуха (корпуса), не позволяющие выполнять магнитную дефектоскопию, проверку состояния зубьев прямозубых зубчатых колес провести ультразвуковой дефектоскопией (УЗД);
— проверка ультразвуковым дефектоскопом шеек и подступичных частей осей моторвагонного подвижного состава. При отсутствии ультразвукового дефектоскопа демонтировать внутренние кольца подшипников и произвести магнитную дефектоскопию шеек;
— проверка соответствия размеров всех элементов колесной пары установленным нормам допусков и износов.
— проверка состояния пружинных пакетов и заклепок зубчатых колес, плотность насадки косозубых венцов, а также болтов, крепящих венцы зубчатых колес;
— проверка состояния упругих элементов, дисков тарелок;
— крепление стопорных колец упругих зубчатых колес тепловозов;
— ревизия узлов с подшипниками качения в случаях, когда это предусмотрено Инструкцией по содержанию и ремонту узлов с подшипниками качения локомотивов и моторвагонного подвижного состава.
— проверка УЗД удлиненных ступиц колесных центров на электровозах серий ВЛ-8, ВЛ-10в/и, ВЛ-11в/и, ВЛ-15, ВЛ-23, ВЛ-6Ов/и, ВЛ-65, ВЛ-80в/и, ВЛ-85, ЧС2, ЧС2Т (кроме колесных пар с приваренными кольцами на внутренних торцевых поверхностях ступиц);
— окраска открытых мест оси.
Результаты контроля при обыкновенном освидетельствовании заносят в книгу формы ТУ-21 и формуляр (технический паспорт) колесной пары.
Полное освидетельствование колесных пар проводят:
- при ремонте с заменой составных частей;
- при неясности клейм и знаков последнего полного освидетельствования;
- при наличии повреждений колесной пары после крушения, аварии, столкновения или схода ТПС с рельсов, а также любых видимых повреждений, выявленных при осмотре, кроме повреждений, которые могут быть устранены обточкой или шлифовкой (зачисткой).
При полном освидетельствовании колесной пары выполняют все работы, предусмотренные при проведении для обыкновенного освидетельствования, и дополнительно проводят:
- очистку колесной пары от краски (на литых необработанных поверхностях колесных центров допускается неполная очистка от краски, не мешающая визуальной проверке наличия трещин);
- проверку наличия и ясности установленных клейм и знаков на составных частях колесной пары;
- выявление дефектов колесной пары*;
- проверку соответствия размеров и параметров составных частей колесной пары требованиям ремонтных чертежей*;
- проверку плотности посадки призонных болтов зубчатых колес остукиванием двухсотграммовым молотком по головке болта;
- проверку магнитным дефектоскопом призонных болтов зубчатых колес в случае их замены;
- УЗД закрытых частей оси (у колесных пар дизель-поездов – только подступичных частей оси);
- проверку магнитным дефектоскопом посадочной поверхности бандажа и прижимного бурта после его обжима;
- переформирование (выпрессовку оси) с проверкой неразрушающим контролем всех составных частей колесной пары электровоза с удлиненными ступицами колесных центров, если от даты формирования колесной пары или выпрессовки оси прошло более 8 лет;
- проверку на сдвиг колесных центров без удлиненных ступиц, если от формирования или выпрессовки оси прошло более 10 лет.
По результатам полного освидетельствования осуществляют замену забракованных составных частей и постановку клейм и знаков полного освидетельствования. Данные о колесной паре, результатах измерений и проведенном ремонте при полном освидетельствовании заносят в формуляр (технический паспорт) колесной пары и формуляр (технический паспорт) большого зубчатого колеса, а также:
- в книгу регистрации освидетельствования колесных пар по единой учетной форме при полном освидетельствовании и переформировании колесной пары;
- в технологический (производственный) паспорт при ремонте с заменой составных частей.
Таким образом, при проведении проверки параметров колёсных пар на всех видах ремонта при помощи шаблонов и инструментов, производятся следующие измерения:
Предельный прокат. Прокат измеряют абсолютным шаблоном на расстоянии 70 мм от внутренней грани колеса, т.е. в наиболее изнашиваемой части. при скоростях движения свыше 120 км/ч до 140 км/ч: прокат по кругу катания у локомотивов, мотор-вагонного подвижного состава, пассажирских вагонов более 5 мм; при скоростях движения до 120 км/ч: прокат по кругу катания у локомотивов, а также у мотор-вагонного и специального самоходного подвижного состава и пассажирских вагонов в поездах дальнего сообщения - более 7 мм, у мотор-вагонного подвижного состава и пассажирских вагонов в поездах местного и пригородного сообщений - более 8 мм, у вагонов рефрижераторного парка и грузовых вагонов - более 9 мм.
Ползун. Этим же шаблоном измеряют ползун на поверхности катания. ползун (выбоина) на поверхности катания у локомотивов, моторвагонного и специального подвижного состава, а также у тендеров паровозов и вагонов с роликовыми буксовыми подшипниками более 1 мм, а у тендеров и вагонов с подшипниками скольжения более 2 мм.
Толщина гребня. Толщину гребня измеряют абсолютным шаблоном (рис. 7) при скоростях движения свыше 120 км/ч до 140 км/ч: толщина гребня более 33 мм или менее 28 мм у локомотивов при измерении на расстоянии 20 мм от вершины гребня при высоте гребня 30 мм, а у подвижного состава с высотой гребня 28 мм - при измерении на расстоянии 18 мм от вершины гребня, при скоростях движения до 120 км/ч: толщина гребня более 33 мм или менее 25 мм у локомотивов,при измерении на расстоянии 20 мм от вершины гребня при высоте гребня 30 мм, а у подвижного состава с высотой гребня 28 мм - при измерении на расстоянии 18 мм от вершины гребня.
Вертикальный подрез гребня. Гребень может иметь большой вертикальный износ (подрез), который определяют по отсутствию зазора между вертикальной гранью движка специального шаблона ВПГ (рис 8), более 18 мм запрещается выпускать в эксплуатацию.
Толщина обода колеса. Толщину обода колеса измеряют толщиномером (рис. 3) в наиболее изнашиваемом месте по кругу катания. Толщиномером можно измерить также глубину ползунов, выщербин, высоту наваров. Размеры этих дефектов определяют как разницу между толщиной обода в местах расположения этих дефектов и толщиной обода на таком же расстоянии от внутренней грани обода колеса, но в том месте, где их нет.
Расстояние между внутренними гранями колес. Измерение расстояния между внутренними гранями колес выполняют штангеном РВП.
Диаметр по кругу катания и разности диаметров колес на одной оси. Измерение диаметров по кругу катания и определение разности диаметров колес на одной оси выполняют скобой ДК.
Оборудование: бандаж колесной пары, шаблон для измерения толщины бандажа, шаблон для измерения подреза гребня, штангенциркуль для определения расстояния между внутренними гранями бандажей, шаблон для измерения величины проката и толщины гребня, бандажный штангенциркуль, молоток, колёсная пара, микрометр 200-225 мм.
Порядок проведеения замеров
1. Осмотреть бандажи (рис. 25.1) на предмет наличия трещин: по чистоте звука от ударов молотком по бандажу, по положению контрольных рисок на бандаже и на ободе определить, нет ли ослабления бандажей на колёсных центрах, их сдвига или ослабления бандажного кольца.
Рисунок 25.1 - Колесная пара электровоза:
1 – ось; 2 – колесный центр; 3 – зубчатое колесо ведомое;
4 – бандажное кольцо; 5 – бандаж
Осмотром установить, нет ли на бандажах раздавленностей, вмятин, сколов, раковин, выщерблин.
2. Определить величину проката и толщину гребней бандажей:
а) шаблон установить на бандаже так, чтобы опорный конец скобы шаблона (шаблон состоит из скобы толщиной 3 мм, вертикального указателя для измерения проката и горизонтального указателя для измерения толщины гребня) плотно прилегал к внутренней грани бандажа, а гребневой вырез опирался на вершину гребня. Одной рукой шаблон удерживать в указанном положении на бандаже, другой опускать вертикальный указатель до упора на бандаж и отсчёт величины замеренного проката произвести по шкале (рис.25.2);
б) замер толщины гребня производить этим же шаблоном при помощи горизонтального указателя (рис.25.3).
Рисунок. 25.2 - Измерение проката; Рисунок. 25.3 - Измерение толщины гребня 3. Используя бандажный толщиномер, определить толщину бандажа. Бандажный толщиномер состоит из планки с упорным выступом, движка и мерительной ножки (рис. 3.4). Шаблон установить так, чтобы планка плотно прилегала к внутренней поверхности бандажа, а упорный выступ планки шаблона захватывал за торцевую часть прижимного бурта бандажа. Мерительную ножку установить на расстоянии 70 мм от внутренней грани планки и закрепить на движке при помощи винта. Мерительную ножку упереть в поверхность катания бандажа и по шкале определить толщину бандажа. Толщиномером определить значение местного наплыва металла на наружной боковой поверхности бандажа (рис. 25.5).
Рисунок 25.4 - Измерение толщины бандажа |
Рисунок 25.5 - Определение значения местного наплыва металла (уширения бандажа) |
4.Определить величину вертикального подреза гребня.
Вертикальный подрез определяется по соприкосновению плоскости шаблона
с поверхностью гребня. Гребень браковать в тех случаях, когда вертикальная браковочная грань движка соприкасается (хотя бы в верхней части) с подрезанной поверхностью гребня и подрез его по высоте более 18 мм независимо от оставшейся толщины бандажа. Если же подрез гребня по высоте более 18 мм, но профиль гребня не вертикален и браковочная грань движка шаблона не прилегает по всей поверхности подреза или хотя бы в верхней части, то такой гребень браковке не подлежит (рис. 25.6). Проверить отсутствие остроконечного наката (рис. 25.7).
5. Измерить расстояние между внутренними гранями бандажей.
Измерение производится штангенциркулем, имеющим штангу с нониусом, две планки (губки) – неподвижную и подвижную (рис. 25.8)
Рисунок 25.6 - Выявление вертикального подреза гребня:
а – гребень бракуется; б – гребень не бракуется
Рисунок 25.7 - Проверка остроконечного наката гребня:
а – гребень бракуется; б, в – гребень не бракуется
Рисунок 25.8 - Межбандажный штангенциркуль:
1 – неподвижная губка; 2 – трубчатая штанга; 3 – подвижная губка
6.Замерить диаметры бандажей с помощью бандажного штангенциркуля и вычислить их разность (рис. 25.9).
7. С помощью микрометра (индикаторной скобы) измерить диаметры шеек оси колёсной пары под моторно-осевые подшипники.
8. С помощью штангенциркуля измерить ширину бандажа.
Рисунок 25.9 - Бандажный штангенциркуль (скоба ДИ):
1 – штанга; 2 – добавочное устройство; 3 – движок правый; 4 – нониус; 5 – движок левый
Оборудование: бандаж колесной пары, шаблон УТ-1.
Порядок выполнения
Универсальный шаблон для контроля геометрических параметров поверхности катания бандажей колесных пар тягового подвижного состава (ТПС) применяется для выявления опасной формы гребня взамен специального шаблона для выявления вертикального подреза гребня. Шаблон позволяет использовать дополнительный критерий оценки изношенного колеса — параметр крутизны гребня qR и вести инструментальный контроль его величины.
Шаблон может быть применен для замера толщины гребня и определения его высоты. При этом величина проката может быть определена путем вычитания чертежного размера высоты гребня для профиля, применяющегося в депо, из высоты гребня, определяемой с использованием данного шаблона.
Толщина гребня — расстояние, измеренное по горизонтали на высоте 13 мм от поверхности круга катания колеса между двумя точками, лежащими по разные стороны от вершины гребня, одна из которых — в плоскости внутренней грани обода бандажа, другая — на наружной поверхности гребня (рис. 25.10).
Параметр крутизны гребня — это расстояние, измеренное по горизонтали между двумя точками наружной поверхности гребня, одна из которых находится в 2 мм от вершины, а другая — 13 мм от круга катания колеса. Параметр крутизны гребня комплексный и характеризует изменения формы и размеров гребня и всего профиля поверхности катания колеса, связанные с износами в процессе эксплуатации (см. рис. 25.10).
Высота гребня — расстояние, измеренное по вертикали между вершиной гребня и поверхностью круга катания бандажа (см. рис. 25.10).
Рисунок 25.10 - Профиль поверхности катания колеса и контролируемые поверхности
Разность между размером измеренной высоты гребня и чертежным размером высоты гребня бандажа нового или после обточки характеризует величину проката по кругу катания колеса, возникающего в процессе эксплуатации.
Шаблон представляет собой сборный металлический каркас с системой рамок с зажимными устройствами и измерительных линеек. Количество линеек определяется числом контролируемых параметров и равно трем.
П - образный жестко склепанный остов каркаса имеет две вертикальные опоры. Одна опора 1 жестко закреплена на расстоянии 70 мм от внутренней грани бандажа на круге катания (рис. 25.11). Другая опора с посто
|
|
Опора деревянной одностоечной и способы укрепление угловых опор: Опоры ВЛ - конструкции, предназначенные для поддерживания проводов на необходимой высоте над землей, водой...
История создания датчика движения: Первый прибор для обнаружения движения был изобретен немецким физиком Генрихом Герцем...
Археология об основании Рима: Новые раскопки проясняют и такой острый дискуссионный вопрос, как дата самого возникновения Рима...
История развития хранилищ для нефти: Первые склады нефти появились в XVII веке. Они представляли собой землянные ямы-амбара глубиной 4…5 м...
© cyberpedia.su 2017-2024 - Не является автором материалов. Исключительное право сохранено за автором текста.
Если вы не хотите, чтобы данный материал был у нас на сайте, перейдите по ссылке: Нарушение авторских прав. Мы поможем в написании вашей работы!