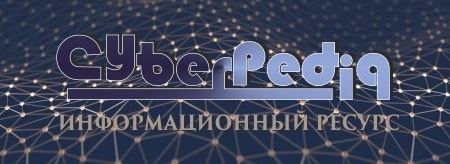
Историки об Елизавете Петровне: Елизавета попала между двумя встречными культурными течениями, воспитывалась среди новых европейских веяний и преданий...
История создания датчика движения: Первый прибор для обнаружения движения был изобретен немецким физиком Генрихом Герцем...
Топ:
Основы обеспечения единства измерений: Обеспечение единства измерений - деятельность метрологических служб, направленная на достижение...
Генеалогическое древо Султанов Османской империи: Османские правители, вначале, будучи еще бейлербеями Анатолии, женились на дочерях византийских императоров...
Интересное:
Финансовый рынок и его значение в управлении денежными потоками на современном этапе: любому предприятию для расширения производства и увеличения прибыли нужны...
Искусственное повышение поверхности территории: Варианты искусственного повышения поверхности территории необходимо выбирать на основе анализа следующих характеристик защищаемой территории...
Распространение рака на другие отдаленные от желудка органы: Характерных симптомов рака желудка не существует. Выраженные симптомы появляются, когда опухоль...
Дисциплины:
![]() |
![]() |
5.00
из
|
Заказать работу |
|
|
Теоретические сведения
Технологическая оснастка представляет собой дополнительные или вспомогательные устройства, предназначенные для реализации технологических возможностей оборудования или работающие автономно на рабочем месте с использованием ручного, пневматического, электромеханического и других приводов. При выборе технологической оснастки в соответствии с ГОСТ14.305.-73 ЕСТПП определяют по каталогам исходя из вида работы принадлежность конструкции к определенной системе технологической оснастки. К системам технологической оснастки относятся:
· неразборная специальная оснастка (НСО);
· универсально-наладочная оснастка (УНО);
· сборно-разборная оснастка (СРО);
· универсально-безналадочная оснастка (УБО);
· специализированная наладочная оснастка (СНО).
Конструкцию оснастки выбирают с учетом стандартных и типовых решений для данного вида технологической операции с учетом габаритных размеров изделия, вида заготовки, характеристики материала изделия, точности параметров изделия, технологических схем базирования и фиксации изделий, характеристик оборудования, типа производства.
Технологическая оснастка применяется для выполнения следующих операций:
1) подготовка выводов радиоэлементов к монтажу (гибка, обрезка, формовка, лужение);
2) подготовка проводов и кабелей к монтажу (снятие изоляции, зачистка, заделка, маркировка, вязка жгутов, лужение);
3) механосборка (расклепка, развальцовка, запрессовка, расчеканка, свинчивание, стопорение резьбовых соединений);
4) установка радиоэлементов на печатные платы (укладка, закрепление, склеивание);
5) монтажные работы (пайка, сварка, накрутка, демонтаж элементов);
|
6) регулировочные и контрольные операции (подстройка параметров, визуальный и автоматический контроль) и т.д.
Использование технологической оснастки имеет целью механизировать или автоматизировать отдельные операции технологического процесса. Выбор технологической оснастки проводят в соответствии с ГОСТ14.305-73 путем сравнивания вариантов и определения принадлежности к стандартным системам оснастки. На первом этапе используют стандарты: ОСТ4ГО.054.263 – ОСТ4Г0.054.268, научно-технические журналы, патентную и справочную литературу.
Выбор конструкции оснастки осуществляют путем расчета следующих технико-экономических показателей: коэффициент загрузки единицы технологической оснастки и затраты на оснащение технологической операции.
Коэффициент загрузки Кз единицы оснастки рассчитывается по формуле
Кз = ТштN/Фд, (6.1)
где Тшт – штучно-калькуляционное время выполнения технологической операции;
N – программа выпуска;
Фд – годовой фонд рабочего времени.
На втором этапе осуществляется доработка конструкции рабочих узлов технологической оснастки в соответствии с размерами обрабатываемых деталей и радиоэлементов и техническими условиями на изделие. Конструкция приспособления должна быть увязана с конструкцией технологического оборудования, например, расположением стола станка, пресса, крепежных пазов на нем.
К проектированию специализированных групповых приспособлений предъявляются следующие требования:
1) приспособление должно иметь комплект сменных или регулируемых элементов (направляющие, установочные, зажимные и др.), обеспечивающих стабильность установки любой из деталей группы;
2) количество деталей, входящих в сменный комплект, должно быть минимальным;
3) переналадка приспособления должна быть простой, доступной рабочему 2-3 разряда, и проводиться не более 5–10 мин.
Сборочный чертеж технологической оснастки содержит обычно две–три проекции общего вида с соответствующими разрезами и сечениями, обеспечивающими возможность деталирования. На нем указывают габаритные и присоединительные размеры, а также размеры, износ которые влияет на точность приспособления. К таким размерам относятся различного рода посадки, обозначаемые в соответствии со СТ СЭВ 144-75. В технических требованиях приводят следующие сведения:
|
– характеристики совместно используемого оборудования, тип привода;
– наибольшие габаритные размеры обрабатываемых деталей или элементов;
– характер смазки трущихся деталей и др.
На завершающем этапе проектирования технологической оснастки выполняют поверочный расчет, который имеет целью определение ее работоспособности, производительности и других технических характеристик.
При расчетах чаще всего определяют механические характеристики работы приспособления. Усилие, разрабатываемое винтовым механизмом, зависит от величины приложенного момента, формы рабочего торца винта и вида резьбы.
Для винтов со сферическим торцом:
(6.2)
где Fприл – усилие, приложенное к рукоятке винтового механизма,
Н; L – длина рукоятки,
м; rср – средний радиус резьбы, м;
a – угол подъема резьбы;
x – приведенные угол и радиус трения.
Угол подъема резьбы и приведенный угол трения:
(6.3)
где S – шаг резьбы, мм;
f – коэффициент трения на плоскости;
b – половина угла при вершине профиля резьбы, град.
Для винтов с плоским торцом:
F = , (6.4)
где m – коэффициент трения на плоском торце;
D – наружный диаметр плоского торца, м.
Условие самоторможения винтового механизма определяется неравенством:
a < xпр. (6.5)
Для резьбы величина угла подъема лежит в пределах 1,5 – 4o, а приведенный угол трения изменяется в зависимости от величины коэффициента трения в пределах от 6 до 16o, условие торможения, как правило, выполняется. Для проверочных расчетов винтового механизма выбирают исходные данные в пределах:
Fприл = 15–25 Н; L = 0,08–0,24 м; f = 0,1–0,15; rср = 0,45d;
D = 0,8d; m = 0,1; b = 120o,
где d – номинальный диаметр резьбы, в мм.
КПД винтового механизма рассчитывается по формуле:
z= . (6.6)
Для самотормозящихся винтовых механизмов КПД меньше 0,5. Выбрав номинальный диаметр винта в зависимости от требуемого усилия зажима F, проверяют прочность винта:
sр = < sр.доп, (6.7)
где sр – напряжение растяжения винта, Мпа;
sр.доп – допустимое напряжение растяжения материала винта, Мпа;
|
K – коэффициент, для метрической резьбы с крупным шагом – 0,5.
Для винтов с резьбой М6-М18, изготовленных из углеродистых сталей обыкновенного качества марок Ст3, Ст5, допустимое напряжение до 200 Мпа, качественных сталей 10…85 – до 430 Мпа.
Усилие, развиваемое рычажным механизмом (рисунок 6.1), определяется по формуле
F = Fприл , (6.8)
где L1, L2 – плечи рычага;
fo – коэффициент трения на оси;
r – радиус оси.
В эксцентриковых механизмах применяются круговые и криволинейные эксцентрики, представляющие собой диск или валик со смещенной осью вращения относительно геометрической оси. Угол подъема кругового эксцентрика достигает максимального значения при угле поворота 90°. Однако при этом возможна нестабильность усилия. В связи с этим для обеспечения незначительного изменения зажимного усилия выбирают рабочий участок профиля кругового эксцентрика в пределах 30-45о влево и вправо от расчетной точки контакта детали с эксцентриком. Усилие зажима круговым эксцентриком определяют по формуле
, (6.9)
где Fприл – сила, приложенная к рукоятке эксцентрика (100–150 Н);
L1 – плечо приложения силы, м, L1 = L + 0,5D, где L – длина рукоятки;
D – диаметр кругового эксцентрика;
L2 – расстояние от оси вращения эксцентрика до точки соприкосновения с изделием;
м; f – угол трения между эксцентриком и изделием, град;
f1 – угол трения на оси эксцентрика, град;
a – угол подъема кривой эксцентрика, град.
Условие самоторможения кругового эксцентрика:
D/L ³ 14, (6.10)
где L – эксцентриситет (1,5–5,0 мм).
При выполнении операций сборки неразъемных соединений путем расклепывания усилие, прикладываемое к детали, определяют таким образом:
F = (2 – 2,5)sвS, (6.11)
где sв – предел прочности материала детали на растяжение;
S – площадь приложения давления.
Для развальцовки это усилие определяется так:
F = sвS. (6.12)
При свободной гибке выводов радиоэлементов усилие выбирается из условия
Fr = sт, (6.13)
где L – длина линии изгиба;
d – диаметр вывода;
B – плечо гибки, равное r+1,25d, где r – внутренний радиус гибки;
sт – предел текучести материала выводов.
Рассчитанное усилие, необходимое для работоспособности приспособления, должно быть в 5–8 раз меньше усилия, развиваемого приводом приспособления или технологическим оборудованием.
|
Усилие, развиваемое пневмоприводом (рисунок 6.2):
Fп = pD2pz/4 – Fc, (6.14)
где D – диаметр поршня или диафрагмы в пневмоцилиндре;
p – давление сжатого воздуха;
Fc – усилие сопротивления возвратной пружины в крайнем рабочем положении поршня.
![]() |
![]() |
Время срабатывания пневмопривода:
(6.15) |
где L – длина хода поршня;
d – диаметр воздухопровода;
v – скорость подачи воздуха (150–250 м/с).
Порядок выполнения задания
10 Составить эскиз технологической оснастки и определить параметры, подлежащие расчету.
11 Выполнить расчет параметров технологической оснастки по 2–3 вариантам.
12 Выбрать тип привода и рассчитать потребляемую мощность.
Практическое занятие №7
|
|
Типы оградительных сооружений в морском порту: По расположению оградительных сооружений в плане различают волноломы, обе оконечности...
Особенности сооружения опор в сложных условиях: Сооружение ВЛ в районах с суровыми климатическими и тяжелыми геологическими условиями...
Семя – орган полового размножения и расселения растений: наружи у семян имеется плотный покров – кожура...
История развития хранилищ для нефти: Первые склады нефти появились в XVII веке. Они представляли собой землянные ямы-амбара глубиной 4…5 м...
© cyberpedia.su 2017-2024 - Не является автором материалов. Исключительное право сохранено за автором текста.
Если вы не хотите, чтобы данный материал был у нас на сайте, перейдите по ссылке: Нарушение авторских прав. Мы поможем в написании вашей работы!