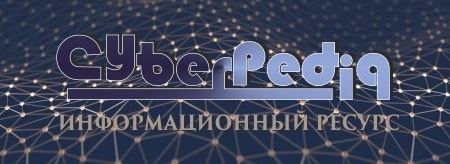
Археология об основании Рима: Новые раскопки проясняют и такой острый дискуссионный вопрос, как дата самого возникновения Рима...
Организация стока поверхностных вод: Наибольшее количество влаги на земном шаре испаряется с поверхности морей и океанов (88‰)...
Топ:
Проблема типологии научных революций: Глобальные научные революции и типы научной рациональности...
Характеристика АТП и сварочно-жестяницкого участка: Транспорт в настоящее время является одной из важнейших отраслей народного хозяйства...
Особенности труда и отдыха в условиях низких температур: К работам при низких температурах на открытом воздухе и в не отапливаемых помещениях допускаются лица не моложе 18 лет, прошедшие...
Интересное:
Распространение рака на другие отдаленные от желудка органы: Характерных симптомов рака желудка не существует. Выраженные симптомы появляются, когда опухоль...
Берегоукрепление оползневых склонов: На прибрежных склонах основной причиной развития оползневых процессов является подмыв водами рек естественных склонов...
Как мы говорим и как мы слушаем: общение можно сравнить с огромным зонтиком, под которым скрыто все...
Дисциплины:
![]() |
![]() |
5.00
из
|
Заказать работу |
|
|
Цель работы: ознакомление студентов с возможными дефектами коленчатого вала двигателя ЗИЛ-130, способами их обнаружения и контроля, устранением отдельных дефектов, рациональной последовательностью выполнения операций по их устранению, а также с устройством и работой шлифовального станка, используемого для шлифования коренных и шатунных шеек коленчатых валов.
Содержание работы
Коленчатый вал (дет. 1З0-1005011-Б) двигателя ЗИЛ-130 после разборки, очистки и мойки подвергается проверке с целью обнаружения дефектов и контролю технического состояния. Прежде всего, проводится внешний осмотр вала, а затем с помощью магнитного дефектоскопа определяется наличие трещин на поверхностях коренных и шатунных шеек. Для производства замеров согласно техническим требованиям на дефектоскопию и ремонт коленчатого вала двигателя ЗИЛ-130 используется различный мерительный инструмент.
После дефектовочных работ коленчатый вал относят к одной из трех групп: годные, требующие ремонта, бракованные.
Наибольшему износу подвержены шейки коленчатого вала. В практике ремонта восстановление изношенных поверхностей шеек проводят или механической обработкой под ремонтный размер, или электродуговой наплавкой с последующей механической обработкой под размер по рабочему чертежу. Наибольшее распространение имеет первый способ восстановления. В общем случае способ механической обработки под ремонтный размер состоит в том, что одна или несколько дефектных поверхностей одной из сопрягаемых деталей (обычно наиболее сложной и дорогостоящей) обрабатываются под ремонтный размер, а другая деталь заменяется новой или восстановленной также до ремонтного размера. Обработка сопряженных деталей под определенные заранее установленные ремонтные размеры дает возможность сохранить взаимозаменяемость в пределах ремонтного размера. В случае с коленчатым валом его шейки обрабатываются под ремонтный размер, а вкладыши подшипников заменяются новыми, соответствующего ремонтного размера.
|
При дефекации коленчатого вала могут быть обнаружены другие дефекты, устранение которых должно быть отражено в технологическом процессе ремонта коленчатого вала. Например, погнутость вала, износы шпоночных пазов, отверстия под подшипник направляющего конца ведущего вала коробки передач, отверстий под болты крепления маховика, фланца вала по диаметру, риски, задиры на поверхностях и др. Поэтому при разработке технологического процесса ремонта коленчатого вала должна быть установлена рациональная последовательность выполнения операций и выбраны наиболее рациональные способы устранения дефектов.
Практикой ремонта коленчатых валов механической обработкой установлена целесообразная последовательность выполнения операций по устранению выявленных дефектов.
1. Проверка погнутости вала и его правка (при установке вала 1-й и 5-й коренными шейками на призме).
2. Правка центровых отверстий вала.
3. Шлифование коренных шеек до ремонтного размера.
4. Шлифование шатунных шеек до ремонтного размера.
5. Зенкование фасок в отверстиях масляных каналов и механическая очистка масляных каналов.
6. Суперфиниширование коренных и шатунных шеек.
После проведения вышеуказанных операций проводится мойка коленчатого вала, продувка его масляных каналов сжатым воздухом. В заключение проводится контроль коленчатого вала.
В случае износа отверстий под болты крепления маховика их обрабатывают до одного из ремонтных размеров. Развертывание этих отверстий проводят в сборе с маховиком.
При устранении износа в отверстии под подшипник направляющего конца ведущего вала коробки передач это отверстие растачивают на токарном станке под ремонтную втулку. Затем проводят расточку отверстия в самой втулке под подшипник (до размера го чертежу).
|
Для устранения износа шейки под шестерню и шкив коленчатого вала можно использовать способ восстановления давлением (в данном случае - накатывание). Шейка подвергается накатке специальным накатным роликом на токарном станке, а затем шлифуется под шестерню и шкив коленчатого вала на круглошлифовальном станке. Восстановление шейки может быть также осуществлено электродуговой наплавкой с последующим обдирочным и чистовым шлифованием на круглошлифовальном станке (до размера по чертежу).
Биение торцевой поверхности фланца и износ его по диаметру может устраняться соответственно подрезкой торца фланца на токарном станке и закатыванием наружной поверхности фланца с последующей обточкой на токарном станке. Допускается износ поверхности фланца по диаметру устранять электродуговой наплавкой с последующей механической обработкой.
Срыв до двух ниток или износ резьбы М27х1,5-7Н под храповик может устраняться прогонкой резьбы или нарезкой ремонтной резьбы М30х1,5-6Н. При повреждении резьбы до двух ниток М30х1,5-7Н под пробку масляного канала этот дефект устраняют прогонкой резьбы метчиком.
Риски, задиры и износ шейки вала под сальник устраняют шлифованием на круглошлифовальном станке до размера не менее 78,8мм. Микрошнек на этой поверхности может быть восстановлен на специальном стенде для накатки.
Износ шпоночных пазов может устраняться электродуговой наплавкой с последующим фрезерованием шпоночных пазов на фрезерном станке.
Для подбора пресса для правки погнутых коленчатых валов необходимо определить усилие Р, достаточное для правки вала
(1)
где Р - усилие необходимое для правки вала, кг;
f - величина прогиба вала, необходимая для правки (принимается равной шестикратному прогибу вала), см;
Е - модуль упругости в кг/см2, для стали принимается 2∙106;
J - момент инерции круглого сечения J = 0,05 d4, см;
l - расстояние между призмами, на которых установлен вал, см (l≈570 мм).
Припуск на шлифование коренных и шатунных шеек рассчитывается по формуле
мм (2)
где Нa - высота поверхностных неровностей, которая определяется или путем измерения или путем сравнения с эталонной шероховатостью, мм (Нa = 0,05 мм);
|
Тa - глубина поврежденного слоя, учитываемая при наличии следов коррозии или цветов побежалости, мм (Т a = 0,04 мм);
ρ0 - коэффициент, учитывающий прогиб вала;
εb - коэффициент, учитывающий неточность установки вала на станок (εb = 0,05 мм).
Определив припуск для шейки вала, можно определить, под какой ремонтный размер можно шлифовать
(3)
где dр - наибольший размер, который может быть получен после шлифования шейки;
dз - замерный размер шейки вала до шлифования.
Сравнивая диаметр шейки dр с таблицей ремонтных размеров, определяют фактический припуск на шлифование, который должен быть равен расчетному, либо быть больше расчетного.
Режим шлифования шеек определяется скоростью шлифовального круга, которая зависит от подачи, профиля и связки круга. Она принимается в этой работе не более 35-50 м/с. Частота вращения вала при шлифовании коренных шеек 25 м/мин, шатунных шеек - 12 м/мин. Круг для шлифования шеек принимается Э25СМ-Б.
Для запрессовки ремонтной втулки в расточенное отверстие под подшипник направляющего конца ведущего вала коробки передач необходимо подсчитать усилие запрессовки Р
(4)
где f Т - коэффициент трения при запрессовке стальной втулки в расточенное отверстие стального вала, f Т = 0,06...0,22;
d - наружный диаметр втулки, мм;
l - длина запрессовки, мм;
p - напряжение сжатия на контактной поверхности в кг/cм2, подсчитывается по формуле
(5)
где Δ - натяг, мкм;
E1 и E2 - модули упругости материала втулки и вала, для стали 2,1∙104 кг/мм2;
С1 и С2 - коэффициенты, принимаемые по таблице 1 в зависимости от отношения внутреннего диаметра втулки к наружному.
Таблица 1
![]() | С1 | С2 | ![]() | С1 | С2 |
0,0 | 0,70 | - | 0,5 | 1,37 | 1,97 |
0,1 | 0,72 | 1,32 | 0,6 | 1,83 | 2,43 |
0,2 | 0,78 | 1,38 | 0,7 | 2,62 | 3,22 |
0,3 | 0,79 | 1,49 | 0,8 | 4,25 | 4,85 |
0,4 | 0,80 | 1,68 | 0,9 | 9,82 | 9,85 |
Последовательность выполнения работы
1. Произвести наружный осмотр коленчатого вала в соответствии с техническими требованиями на дефекацию и ремонт.
2. Наметить пояса и плоскости замеров на шейках коленчатого вала. Составить схему замеров.
|
3. Произвести измерения шеек в намеченных поясах и плоскостях в соответствии со схемой замеров.
4. Замерить длину установочной шейки вала.
5. Замерить диаметры отверстий под болты во фланце маховика и отверстия под подшипник направлявшего конца ведущего вала коробки передач.
6. Определить величину прогиба коленчатого вала по средней шейке.
7. Определить величину биения фланца вала.
8. Замерить диаметр шейки под ступицу шкива и шестерню.
9. Замерить диаметр маслогонных канавок.
10. Замерять наружный диаметр фланца вала.
11. Проанализировать результаты внешнего осмотра и измерений. Составить обоснованное заключение с определением группы, к которой относится продефектованный вал (годен, требует ремонта, брак).
12. При отнесении коленчатого вала к группе требующих ремонта, выбрать наиболее целесообразные способы устранения выявленных дефектов и наметить наиболее рациональную последовательность ремонта коленчатого вала.
13. Рассчитать припуск на шлифование шеек, определить ремонтный размер, установить режим шлифования.
14. Прошлифовать одну из шеек коленчатого вала (по указанию преподавателя).
Перечень оборудования и инструмента
Станок 3423 с настроечными призмами.
Приспособление для правки шлифовального камня.
Микрометр с пределом измерения 50-75 мм.
Подставка для микрометров.
Штангенциркуль от 0 до 250 мм, цена деления 0,02мм.
Индикаторная головка (цена деления 0,01 мм) с подставкой.
Эталоны шероховатости.
Стальные линейки с пределом измерения 300 мм.
Установочная плита.
Установочные призмы.
Устройство станка 3423 и работа на нем
Шлифовка шеек коленчатого вала производится на специальных станках типа 3423, позволяющих шлифовать коренные и шатунные шейки. Однако в практике ремонта в целях обеспечения большей точности обработки их настраивают на шлифовку либо шатунных, либо коренных шеек. Поэтому изучение процесса шлифовки шеек коленчатого вала желательно осуществлять на примере шлифовки шатунных шеек вала. Прежде чем приступить к выполнению работ, необходимо ознакомиться с устройством станка, работой на нем и правилами техники безопасности.
Режим резания при шлифовке вала принять близким к расчетному. После шлифовки шейки проверить качество путем измерения геометрических размеров шейки и определения шероховатости поверхности.
Общий вид станка показан на рисунке 1. Станок имеет станину 100, шлифовальную бабку 0201, переднюю бабку 600, заднюю бабку 700, механизм ручного перемещения стола 400, механизм поперечной подачи шлифовальной бабки 500, систему охлаждения 8501, люнет 9601, зажимные патроны - левый и правый, рукоятку 1 стопора планшайбы, маховичок 2 ручного перемещения стола, подвод люнета 3, кран пуска охлаждающей жидкости 4, рукоятку фиксатора ускоренного отвода шлифовальной бабки 5, рукоятку компенсации износа шлифовального круга 6, кнопочную станцию электродвигателя шлифовальной бабки, привод изделия и насос подачи охлаждающей жидкости 7, рукоятку стопора планшайбы задней бабки 8, рукоятку отжима пиноли задней бабки 9, маховик ручного перемещения пиноли при шлифовании тяжелых валов 10. Взаимодействие отдельных деталей и механизмов, а также работу на станке можно уяснить при рассмотрении кинематической схемы станка, представленной на рисунке 2.
|
Рис. 1. Общий вид станка 3423
Рис. 2. а) привод изделия, б) привод главного движения
Станина станка состоит из двух частей: передней и задней. На передней станине имеются направляющие для нижнего стола. На нижнем столе крепится верхний стол, который может поворачиваться на небольшой угол. Поворот верхнего стола позволяет шлифовать конические детали. Поворот стола производится вращением винта, расположенного с правой стороны стола. Крепление верхнего стола на нижнем после его правильной установки производится двумя зацепленными планками с правой и левой сторон. Продольное перемещение стола осуществляется вручную при помощи маховика 2. При выдвижении маховика на себя стол перемещается медленно, за один оборот маховика стол перемещается на 14,6 мм. На задней станине крепятся направляющие шлифовальной бабки.
Шлифовальная бабка имеет шпиндель, который приводится во вращение от индивидуального электродвигателя клиноременной передачей. Шпиндель имеет бронзовые подшипники скольжения. Верхние вкладыши прижимаются к шпинделю пружинами и поршеньками. Шпиндель имеет также распорные втулки, которые распираются пружинами и стопорятся винтами. Шлифовальный круг закрепляется на планшайбе, насаженной на конусную шейку шпинделя и заклиненную шпонкой. Шлифовальный круг должен быть тщательно отбалансирован. Новый круг балансируется вместе с планшайбой дважды. Сначала, до постановки на станок, круг балансируется на специальной оправке, прилагаемой к станку. Вторично балансируется после правки круга алмазом на станке. При балансировке круга пользуются смещением сегментов, которые устанавливаются на планшайбе. Подача шлифовальной бабки производится вручную вращением маховика через червяк, червячную шестерню, валик с шестерней и рейку, закрепленную на направляющей станине шлифовальной бабки.
Дня компенсация износа шлифовального круга служит рукоятка, при вращении которой (предварительно нажимая на нее) устанавливается лимб в требуемое положение. Ускоренный отвод шлифовальной бабки осуществляется поворотом хобота механизма подачи шлифовальной бабки. Ускоренный подвод производится поворотом хобота к себе до тех пор, пока фиксатор зайдет в гнездо и зафиксирует хобот на станке.
Передняя бабка является ведущей. Шпиндель вращается на шариковых подшипниках, получая вращение от электродвигателя через шкивы, промежуточный вал и звездочки. Шпиндель имеет, три скорости, изменяющиеся за счет переброски клиновидного ремня в соответствующие ручьи шкивов. На передний конец на шарикоподшипниках установлена планшайба, к которой крепится патрон при шлифовке шатунных шеек коленчатого вала или поводок при работе в центрах.
Трехкулачковые патроны, закрепленные на плитах, могут перемещаться радиально по планшайбе, обеспечивая возможность изменения радиуса кривошипа от 0 до 110 мм. На нижней части планшайбы устанавливаются балансировочные контр-грузы, которые также могут перемещаться в радиальном направлении. Грубая балансировка коленчатого вала в патронах достигается изменением числа грузов в зависимости от массы шлифуемого вала. Грузы крепятся к планшайбе с помощью болтов. При точной балансировке коленчатого вала необходимо отсоединить цепную звездочку от планшайбы, для чего надо вывернуть два болта 1 (рис. 3), благодаря чему достигается свободное вращение планшайбы передней бабки на шарикоподшипниках. Вал, установленный в патронах станка, считается отбалансированным, если при его повороте в любое положение он остается неподвижный.
Задняя бабка имеет шпиндель, который вращается на шарикоподшипниках. Конструкция планшайбы патрона и фиксатора аналогична передней бабке. Для шлифования в центрах внутри шпинделя имеется пиноль с постоянно действующей пружиной. Отвод пиноли для установки вала производится рукояткой через шестерню и втулку с рейкой. Предусмотрен зажим пиноли, который осуществляется при помощи той же рукоятки при отводе ее в крайнее заднее положение. При этом внутренний конус втулки через два сухаря зажимает пиноль во время работы. К станку придаются два съемных люнета, которые закрепляются на столе. При работе люнеты устанавливаются против шлифуемых шатунных шеек. Установка люнета на определенный диаметр шейки вала производится с помощью винтов. Горизонтальный винт подводит или отводит горизонтальную губку, а вертикальный винт-нижнюю губку.
Рис. 3
Для установки вала на станке применяются приспособления; грубая установка вала осуществляется с помощью двух призм (рис.4).
Рис. 4
Точная установка вала осуществляется с помощью индикаторного прибора, который устанавливается на корпус люнета (рис. 5).
Рис. 5
При шлифовании работа выполняется в следующей последовательности:
а) с помощью специального патронного ключа разжать кулачки правого и левого патронов таким образом, чтобы было легче установить коленчатый вал. В левый патрон устанавливается фланец, в правый - шейка под шестерню распределения;
б) зажимные патроны правой и левой бабок зафиксировать в верхнем положении с помощью фиксаторов, которые входят в отверстия планшайбы при повороте рукояток 1 и 8, (рис. 1);
в) установить зажимные патроны на требуемый радиус кривошипа с помощью масштабных линеек. Установить патроны на радиус кривошипа вращением винта специальным торцовым ключом, предварительно отпустив четыре болта 2 (рис. 3);
г) установить коленчатый вал в зажимные патроны и несильно зажать его концы кулачками;
д) произвести предварительную установку вала для шлифовки шатунных шеек с помощью двух специальных приспособлений. С помощью специального приспособления а (рис. 4) достигается положение кривошипа в горизонтальной плоскости. Для этого приспособление устанавливается на направляющую плоскость верхнего стола, а под шатунную шейку, повернутую вниз, подводится выдвижная призма приспособления. Путем поворота вала добиваются прилегания шатунной шейки вала к двум лицевым поверхностям призмы. С помощью приспособления б (рис. 4) проверяется положение вала в вертикальной плоскости. После установки вал зажимается в патронах, а установочные приспособления снимаются;
е) окончательно установить положение вала на станке с помощью индикаторного прибора, который устанавливается на верхнюю часть люнета. Установив люнет против шатунной шейки и закрепив гайкой, устанавливают индикаторный прибор на люнет (рис. 5). С помощью двух рукояток фиксаторы выводятся из отверстий планшайб. Поворачивая вал вручную, по показаниям индикатора определяют смещение шейки относительно оси вращения вала в плоскости кривошипа. С помощью радиального перемещения зажимного патрона добиваются совмещения оси шейки с осью вращения вала с точностью, равной овальности шатунной шейки.
Добиваясь совмещения оси шатунной шейки с осью вращения вала, проделывают то же самое со второй, после чего затягивают окончательно болты 2 (рис. 3) крепления ползунов патронов на планшайбе.
Далее добиваются совмещения оси вращения шатунной шейки вала в плоскости, перпендикулярной кривошипу. Это достигается путем незначительного поворота коленчатого вала относительно зажимных патронов путем вращения винта специального поворотного устройства, установленного на левом зажимном патроне. Предварительно необходимо ослабить крепление вала в патронах. Вращая вал, определяют по индикатору, в какую сторону необходимо произвести его поворот относительно зажимных патронов. После окончательной установки вал зажимается в патронах, индикаторный прибор с люнета снимается;
ж) проверять балансировку установленного вала. При балансировке коленчатого вала на передней бабке необходимо вывернуть болты 1 (рис. 3), освободив тем самым шпиндель с планшайбой и зажимным патроном от звёздочки. Балансировка производится перемещением грузов 3 на планшайбах передней и задней бабок винтами. После балансировки грузы необходимо зажать болтами.
Считается, что вал отбалансирован, когда он при любом положении не имеет стремления повернуться. После балансировки затягиваются болты;
з) проверить поворотом вручную легкость вращения вала на станке;
и) установить на станке шлифовальный камень против шатунной шейки с помощью перемещения стола маховиком 2 (рис. 1). Установить люнет и закрепить;
к) подвести шлифовальный камень к шейке путем поворота хобота к себе до тех пор, пока хобот зафиксируется в определенном положении;
л) пустить электродвигатель привода шлифовального камня и насоса охлаждающей жидкости;
м) включить кнопку поворота изделия и медленно вращая маховик, подвести шлифовальный камень к шейке вала до появления искры. После этого нажать кнопку пуска изделия и маховиком 2 (рис. 1) установить шейку в крайнее положение;
н) произвести шлифовку шейки сначала врезным методом по участкам, а затем до необходимого размера методом продольного прохода. Подачу шлифовального камня в процессе шлифовки необходимо осуществлять очень осторожно, без рывков. Измерение шейки при вращении круга не допускается;
о) после шлифовки шейки отводится индикаторный прибор автоматического контроля, отводится шлифовальный круг, выключаются электродвигатели вращения изделия и круга. Шлифованная шейка изучается, определяется шероховатость поверхности, и результаты контроля вносятся в отчет. Снимается со станка вал, убирается рабочее место.
Технические требования на дефектацию и ремонт коленчатого вала в сборке (1З0-1005011-Б)
У коленчатых валов, поступающих на сборку, масляные каналы и полости должны быть тщательно очищены от шлака. Шатунные и коренные шейки должны соответствовать размеру по рабочему чертежу или одному из ремонтных размеров, указанных в таблице 2.
Для одноименных шеек разные ремонтные размеры не допускаются.
В соответствии с длиной передней коренной шейки должна быть подобрана задняя шайба упорного подшипника по таблице 3.
Шероховатость поверхности коренных и шатунных шеек должна соответствовать по ГОСТ 2789-98 классу (по ГОСТ 2789-99 -
), а овальность и конусность шеек не должна превышать 0,01 мм.
Размеры галтелей коренных и шатунных шеек должны быть в пределах 1,0-3,0 мм.
Таблица 2
Длина передней коренной шейки коленчатого вала и ремонтные размеры задней шайбы упорного подшипника
Длина передней шейки, мм | Толщина задней шайбы, мм |
31,00-31,17 | 2,5-2,4 |
31,17-31,32 | 2,6-2,5 |
31,32-31,47 | 2,7-2,6 |
31,47-31,62 | 2,8-2,7 |
Таблица 3
Размеры по рабочему чертежу и ремонтные размеры коренных и шатунных шеек коленчатого вала
Наименование размера | Уменьшение диаметра, мм | Размеры, мм | |
Коренных шеек | Шатунных шеек | ||
Размер по рабочему чертежу завода изготовителя | - | 74,5-0,02 | 65,5-0,02 |
2-й ремонтный | 0,30 | 74,25-0,02 | 65,25-0,02 |
3-й ремонтный | 0,60 | 74,00-0,02 | 65,00-0,02 |
4-й ремонтный | 1,00 | 73,75-0,02 | 64,75-0,02 |
5-й ремонтный | 1,25 | 73,50-0,02 | 64,50-0,02 |
6-й ремонтный | 1,50 | 73,00-0,02 | 64,00-0,02 |
Длина передней коренной шейки не должна превышать 32,60 мм, а шатунных шеек - 58,32 мм.
При установке вала на крайних коренных шейках биение средних шеек не должно превышать 0,05 мм.
Непараллельность осей шатунных шеек относительно коренных не должна превышать 0,01 мм на длине каждой шатунной шейки. Размеры отверстий во фланце коленчатого вала под болты крепления маховика не должны превышать 14,56 мм (табл.4).
Биение торца фланца коленчатого вала относительно 1-й и 5-й коренных шеек не должно превышать 0,05 мм.
Таблица 4
Ремонтные и допустимые без ремонта размеры отверстий во фланце коленчатого вала под болты крепления маховика
Название размера | Размеры, мм | |
Ремонтный | Допустимый без ремонта | |
Размер по рабочему чертежу завода изготовителя | 14+0,035 | 14,06 |
1-й ремонтный | 1425+0,035 | 14,31 |
2-й ремонтный | 14,5+0,035 | 14,56 |
Сборочная единица (деталь) Коленчатый вал в сборе (рис. 6) | ||
Номер детали: 1ЗО-I005011-Б | ||
Материал: сталь 45, ГОСТ 1050-99 Твердость НRС 52…62 |
Продолжение таблицы 4
Позиция на рис.6 | Возможные дефекты | Способ установления дефекта и средства контроля | Размеры, мм | Заключение | |
По рабочему чертежу | Допустимая без ремонта | ||||
- | Обломы и трещины | Осмотр и дефектоскопия | - | - | Браковать |
Радиальное биение шейки под ступицу шкива и шестерню | Приспособление для контроля коленчатого вала | Радиальное биение относительно 1 и У коренных шеек не более:0,03…0,,5 На расстоянии 50 мм от передней коренной шейки | -“- | ||
Износ шейки под ступицу шкива и шестерню | Скоба 45, 92 ГОСТ 2015-99 | ![]() | 45,92 | -“- | |
Износ маслогонных канавок по диаметру | Калибр 78,8 | ![]() | 78,8 | -“- | |
Износ шпоночных пазов | Калибр 6,02 ГОСТ 7951-99 | ![]() | 6,02 | -“- | |
Увеличение длины шатунных шеек | Калибр 58,32 | ![]() | 58,32 | -”- | |
Увеличение длины передней коренной шейки, задиры или риски на упорной поверхности | Осмотр Калибр 32, 60 ГОСТ 2534-97 | ![]() | - | Обработать упорную поверхность до устранения задиров и рисок Браковать при размере более 32,60 мм | |
Погнутость вала | Приспособление для контроля коленчатого вала | Радиальное биение средних коренных шеек относительно 1 и У шеек не более: | Обработать коренные шейки до ремонтного размера | ||
0,03 | 0,05 |
Продолжение таблицы 4
Износ шатунных шеек | Скобы 2015-99 | См.табл.1 | Обрабатывать до ремонтного размера | ||
Износ коренных шеек | Скобы ГОСТ 2015-99 | -“- | -“- | ||
Овальность и конусность шеек | Оптиметр ГОСТ 5405-95 | 0,010 | 0,015 | -“- | |
- | Неточность углового расположения шатунных шеек | Приспособление | Смещение по окружности радиуса 47,5 не более 0,02 | -“- | |
Изменение радиуса кривошипа | Приспособление | 47,5±0,08 | --“- | ||
Износ отверстий под болты крепления маховика | Пробки ГОСТ 2015-99 | См.табл.4 | -“- | ||
Биение торцевой поверхности Фланца | Приспособление | Торцевое биение относительно 1 и У коренных шеек не более:0,05 Размер “a”12,2-0,63 | Обработать до устранения дефекта. Браковать при размере “a”менее 11,0 | ||
Износ отверстия под подшипник направляющего конца ведущего вала коробки передач | Нутрометр НИ 50-100 ГОСТ 868-92 | ![]() | 52,01 | Поставить втулку ДР | |
Радиальное биение отверстия под подшипник направляющего конца вала коробки передач | Приспособление | Радиальное биение не более: | -“- | ||
0,006 | 0,07 |
Продолжение таблицы 4
Износ фланца по диаметру | Скоба 139, 96 ГОСТ 2015-99 | ![]() | 139,96 | Накатать и обработать | |
Риски, задиры или износ шейки под сальник | Осмотр Скоба 78,7 ГОСТ 2015-99 | ![]() | - | Обработать до устранения дефектов. Браковать при размере менее 78,8 мм |
Дополнительные указания
1. 1-й ремонтный размер коренных и шатунных шеек коленчатого вала при капитальном ремонте не применяется.
2. При восстановительных ремонтах допускается:
по дефекту 1- наплавка;
по дефекту 2- хромирование или наплавка;
по дефекту 3- наплавка;
по дефекту 4- наплавка;
по дефектам 5 и 6- наплавка;
по дефекту 7- правка;
по дефектам 8,9,10,11 и “Неточность углового расположения шатунных шеек ”- наплавка под флюсом;
по дефектам 16 и 17.
|
|
Археология об основании Рима: Новые раскопки проясняют и такой острый дискуссионный вопрос, как дата самого возникновения Рима...
Индивидуальные очистные сооружения: К классу индивидуальных очистных сооружений относят сооружения, пропускная способность которых...
Эмиссия газов от очистных сооружений канализации: В последние годы внимание мирового сообщества сосредоточено на экологических проблемах...
Семя – орган полового размножения и расселения растений: наружи у семян имеется плотный покров – кожура...
© cyberpedia.su 2017-2024 - Не является автором материалов. Исключительное право сохранено за автором текста.
Если вы не хотите, чтобы данный материал был у нас на сайте, перейдите по ссылке: Нарушение авторских прав. Мы поможем в написании вашей работы!