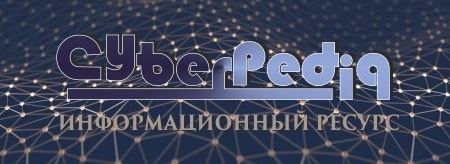
История создания датчика движения: Первый прибор для обнаружения движения был изобретен немецким физиком Генрихом Герцем...
Адаптации растений и животных к жизни в горах: Большое значение для жизни организмов в горах имеют степень расчленения, крутизна и экспозиционные различия склонов...
Топ:
Теоретическая значимость работы: Описание теоретической значимости (ценности) результатов исследования должно присутствовать во введении...
Оснащения врачебно-сестринской бригады.
Комплексной системы оценки состояния охраны труда на производственном объекте (КСОТ-П): Цели и задачи Комплексной системы оценки состояния охраны труда и определению факторов рисков по охране труда...
Интересное:
Отражение на счетах бухгалтерского учета процесса приобретения: Процесс заготовления представляет систему экономических событий, включающих приобретение организацией у поставщиков сырья...
Что нужно делать при лейкемии: Прежде всего, необходимо выяснить, не страдаете ли вы каким-либо душевным недугом...
Инженерная защита территорий, зданий и сооружений от опасных геологических процессов: Изучение оползневых явлений, оценка устойчивости склонов и проектирование противооползневых сооружений — актуальнейшие задачи, стоящие перед отечественными...
Дисциплины:
![]() |
![]() |
5.00
из
|
Заказать работу |
Содержание книги
Поиск на нашем сайте
|
|
Группа высокопористых материалов на основе вспученного жидкого стекла является продуктом термического или химического вспучивания гидратированного растворимого стекла (щелочных силикатов), или композитов, включающих гранулированное вспученное жидкое стекло и связующее. В зависимости от способа вспучивания материалы делят на: 1) термовспученные - зернистые и обжиговые монолитные; 2) вспученные химическим путем – заливочные композиции, в которые вводят газообразующий элемент. Зернистые материалы в зависимости от гранулометрического состава подразделяют на крупнозернистые (стеклопор) – с размером зерен более 5 мм и мелкозернистые (силипор) – от 0,1 до 5 мм. Основным различием эксплуатационных свойств материалов на основе жидкого стекла является их отношение к действию воды.
Различают неводостойкие материалы, эксплуатация которых возможна при относительной влажности воздуха до 75 %, и материалы с повышенной водостойкостью, способные длительное время выдерживать действие воды. Композиционные материалы, изготавливаемые в виде изделий на основе зернистых продуктов, в зависимости от заполнения межзерновой пустотности связующими веществами делят на материалы с контактным и объемным омоноличиванием. Особой формой композитов можно считать сотопластовые изделия, представляющие собой сотопластовый каркас из бумаги или ткани, пропитанных специальными растворами, заполненный мелкодисперсным зерновым материалом из вспученного жидкого стекла, например силипором. К недостаткам материалов на основе вспученного жидкого стекла относятся ограниченная водостойкость и дефицитность гидратированных натриевых силикатов.
Технологический процесс получения гранулированного стеклопора включает [87]: приготовление смеси из раствора жидкого стекла и технологических добавок; частичную дегидратацию полученной смеси; диспергирование (грануляцию) смеси и вспучивание гранулята. При этом сырьём служат: натриевое жидкое стекло (93-95 %, с плотностью 1,4-1,45 г/см³); тонкодисперсные минеральные наполнители с удельной поверхностью 2000-3000 см²/г (7-5 %), например, мел, известняк, песок, тальк, каолин, оксид алюминия, маршаллит, асбестовая пыль, трепел, перлит, зола ТЭС и другие; специальные добавки предназначенные для направленного регулирования эксплуатационных свойств (0,5-1 %), такие, как упрочняющие, гидрофобизирующие, повышающие водостойкость и вспучиваемость, например гидрофобизирующие добавки – кремнийорганические жидкости ГКЖ-94, ГКЖ-10 или ГКЖ-11. Схема процесса получения стеклопора включает (рис. 54): приготовление смеси в двух смесителях вертикального типа 1, перекачивание ее в расходный бак 3 гранулятора 4. Далее смесь, через фильерную пластину 2 самотеком в виде капель поступает в ванну гранулятора, заполненную раствором хлорида кальция плотностью 1,29-1,35 г/см³. Попадая в раствор хлорида кальция, капли образуют гранулы (бисер) с упрочненным поверхностным слоем, представляющим собой кремнегель, содержащий адсорбированный оксид кальция.
|
Рис. 54. Технологическая схема получения стеклопора
Образовавшиеся гранулы оседают на сетку конвейера и выносятся ею в приемное устройство гранулятора, из которого непрерывным потоком через пересыпное устройство попадают в сушильный барабан 5. Оптимальными параметрами формирования гранул с прочным поверхностным слоем являются 40-минутное пребывание их в растворе CaCl2, что обеспечивается определенной скоростью движения сетки конвейера и температурой раствора, равной 22-30 ºС, поддерживаемой паровым змеевиком. В сушильном барабане гранулы высушиваются при t = 85-90 ºC в течение 10-20 мин до влажности 27-30 % и направляются в печь кипящего слоя 6 для вспучивания при t = 350-500 ºC в течение 1-3 мин или непосредственно на затаривание 7.
При получении силипора (материала с гранулами менее 5 мм) грануляция жидкостекольной смеси осуществляется путем ее распыления в башенной сушилке.
Вспучивание гранулята происходит одновременно в жидком стекле связанной воды в момент перехода материала в пиропластическое состояние. Причем температура размягчения растворимого стекла тем ниже, чем больше воды в нем содержится. Однако чрезмерное содержание воды (более 40 %) во вспученных гранулах приводит к их растрескиванию или образованию крупных пор с тонкими непрочными перегородками.
При изготовлении штучных изделий смесь из жидкого стекла, минерализованного наполнителя и добавок вспучивается в формах при тепловой обработке. Стабилизация пористой структуры осуществляется при постепенном охлаждении. Для повышения прочностных показателей и снижения трещинообразования в формовочные смеси вводят пористые заполнители (вспученные перлит или вермикулит).
|
Технология изделий из стеклопора заключается в подготовке связующего [гипс (стеклогипс), жидкое стекло (стеклосиликат), расплавленный битум марки БН-IV (стеклобитум), цементное молоко (стеклоцемент), термопластов (стеклополимер)], приготовлении формовочной массы из стеклопора и связующего, формовании изделий и создании условий для быстрого отверждения связующего. Введение связующего в формовочную смесь можно проводить одним из известных способов: приготовлением гидромасс в мешалках периодического действия, проливом гранул в форме с перфорированным днищем или способом распыления непосредственно при укладке стеклопора в форму. Расход связующего 30-80 кг на 1м³ смеси.
Гранулированные утеплители «Стеклопор» и «Бисипор» получают [220] путем термического вспенивания (350-600 ºС) жидкого стекла, модифицированного 2-3- валентными элементами с помощью золь-гель метода. Недостатком щелочно-силикатных материалов горячего вспенивания является трудность их получения в плитчатой форме из-за неравномерности нагрева по объему. Низкотемпературное (30-100 ºС) вспенивание жидко-стекольных смесей за счет использования неорганических газообразователей (алюминий, кремний, карбид кальция и др.), не обеспечивает низкой плотности и достаточной водостойкости.
Ячеистые бетоны со средней плотностью 300 кг/м³ и ниже имеют значительные усадки и низкую прочность. Предлагаются [221] технологии получения пенобетона на основе стеклобоя. В основе технологии полжены закономерности растворения в воде аморфного кремнезема и его осаждение из раствора посредством процесса конденсационной полимеризации кремневой кислоты Si(OH)4 [222]. Изменяя температуру и величину pH среды, можно управлять этим процессом. Однако, из-за многокомпонентного состава стекол, процесс структурообразования прочного камня из порошков стеклобоя, затворенных водой, затруднен. От автоклавной обработки для выщелачивания порошка стекла можно отказаться, создав аналогичные условия протекания химических реакций при помощи растворимого гидросиликата натрия при температуре не выше 40-50 ºС. Растворенное в воде до определенной концентрации жидкое стекло представляет собой щелочной раствор, который необходим для повышения растворимости аморфного кремнезема с поверхности вводимого в систему порошка стеклобоя. При этом не принципиально, какое стекло используется, то есть, содержание в стекле щелочных оксидов не играет роли. Достаточно высокое значение pH активизирует ионизацию Si(OH)4, и происходит взаимодействие силикат-ионов с гидратированными ионами других компонентов стекла, переходящими в раствор уже при температуре 35ºС. По мере растворения SiO2 и повышения концентрации в растворе, понижается рH среды и происходит реакция поликонденсации с образованием геля кремниевой кислоты, который скрепляет в монолит не полностью растворившиеся и крупные частицы стекла. В следствие высокой степени агрегации полимерных частиц жидкое стекло приближается к состоянию малой устойчивости-кремнеземистый модуль растет, переводя систему в водонерастворимое состояние. Это позволяет рассматривать тонкомолотый порошок стеклобоя как активный поставщик SiO2 в систему, обеспечивающего повышение кремнеземистого модуля жидкого стекла и тем самым решающего проблему водостойкости пенобетона [223]. На основе выявленных закономерностей предложена технология получения пенобетона с использованием “сухой минерализации пены”, безавтоклавной обработки и применением стеклобоя. Технологическая схема включает: дробление и помол стеклобоя, приготовление формовочной массы, формирование блоков, тепловую обработку, выдержку и доводку изделий, распалубку.
|
Используя выщелачивание порошка стеклобоя при помощи гидросиликата натрия при температуре 40-50ºС [224] можно получить ячеистые пенобетоны, например, при помощи способа по пат. 2016886 России, СО4В 40/02, опубл.20.05.1991, при котором изготавливают строительные блоки, сформированные из смеси легких пористых заполнителей с жидким стеклом, путем спекания, например, в СВЧ поле с удельным расходом энергии 0,7-1,5 кДж/см³.
Теплоизоляционный пенобетон можно получить [225] на основе безклинкерного вяжущего, состоящего из тонкомолотого стекла, раствора щелочного силиката и модифицирующих добавок. При этом процесс твердения обусловлен гидратацией молотого стекла в растворе щелочного силиката. Необходимым условием, определяющим гидравлические свойства вяжущего, является присутствие в его составе достаточного количества окислов амфотерных металлов, способных связывать щелочной гидрозоль кремневой кислоты Si(OH)2 в труднорастворимые щелочные гидраты.
Технология получения перлитовых ТИ изделий на основе силикат-натриевых композиций включает [226]: приготовление силикат-натриевой смеси; получение формовочной массы из вспученного перлита и силикат-натриевой композиции; прессование изделий; сушку изделий в сушильной камере, с использованием в качестве теплоносителя продуктов сгорания газа, в течение 6-8 часов при температуре 150-200 ºС.
Используется пресс с давлением от 0,2 до 0,6 МПа и песок перлитовый вспученный рядовой с объемной насыпной плотностью 75-150 кг/м³, обработанный гидрофобизатором.
На основе щелочных и природных силикатов (пеносиликатов) возможно получение различных коллоидных и микрогетерогенных форм кремнезема и материалов из них [227, 228]. Например, технология получения пористых материалов на основе жидкого стекла и природных силикатов [229], включает синтез силикат глыбы, роспуск в автоклаве, получение жидкого стекла, введение в него наполнителя, получение гранул в присутствии отвердителя, термообработку, высушивание при t = 160-200 ºC и вспенивание при t = 300-400 ºC. Применялось жидкое стекло с силикатным модулем 2,5 в качестве связующего, в качестве отвердителя – раствор CaCl2, в качестве наполнителей (10-30 % по массе) – магнезиальные силикаты (тремолит, диопсид, волластонит, порошок обожженной глины).
|
В качестве теплоизоляционного материала может использоваться легкий жаростойкий бетон на жидкостекольной основе, с созданием в нем большого количества пор по пенобетонной технологии или применяя в качестве заполнителя материалы, имеющие пористую структуру [230-232]. Расход материалов на 1 м³ жаростойкого бетона составляет (в кг): жидкое стекло - 385; нефелиновый шлам (или другие материалы, содержащие 1- и 2-х кальцевые силикаты кальция-ß- и j- 2 CaO·SiO2 и CaO-SiO2 в качестве отвердителя) – 115; тонкомолотая шамотная добавка - 396; шамотный заполнитель мелкий - 530 и крупный - 720. Смесь готовят в смесителях с принудительным перемешиванием, причем свойства бетона не зависят от последовательности перемешивания исходных материалов. При введении в смесь жидкого стекла в количестве 300 кг на 1 м ³ бетона, смесь быстро схватывается и твердеет. При увеличении расхода жидкого стекла всего на 50 кг такого явления не наблюдается. Промежуток времени с момента изготовления смеси до момента её укладки в форму не более 30-45 мин. Температура укладки и твердения-10-20 ºC, рост прочности заканчивается к 7-м суткам.
Кислотоупорные бетоны на жидком стекле имеют [233] состав (кг на 1м ³ раствора): жидкое натриевое стекло - (400-500); кремнефтористый натрий (Na2SiF6) - (60-65); тонкомолотый наполнитель - 440; песок кварцевый-1320. Раствор приготавливают в бетономешалке принудительного действия до однородной массы. Материалы загружают в следующей последовательности: песок, затем смесь тонкомолотого наполнителя с кремнефтористым натрием. Сухие составляющие, загруженные в мешалку, перемешивают не менее 2 мин. После чего загружают требуемое количество жидкого стекла и массу дополнительно перемешивают в течение 3-5 мин до получения однородной массы. Замес расходуют не менее чем в течение часа. Укладывать расслоившуюся или загустевшую смесь недопустимо. Твердение бетона происходит в воздушно-сухих условиях при относительной влажности воздуха 55-60 % и температуре не ниже +10 ºC и не выше 40 ºC.Проектная прочность достигается на 7-10 сутки.
Композиция для изготовления ТИ материала (а. с. 1204596 СССР, СО4В 18/06, опубл. 15. 01. 1986) содержит (масс. %): жидкое стекло - 20-25; золу ТЭС - 74,5-79,6; пенообразователь-омыленную канифоль - 0,4-0,6. При изготовлении перемешивают жидкое стекло плотностью 1,35-1,40 с омыленной канифолью до получения вспененной массы, затем добавляют золу с размером зерен 0,315-0,63мм и продолжают перемешивание до получения пористой и подвижной смеси, которую формуют, уплотняют на вибропрессе в течение 10-20 сек, сушат сначала до температуры 60 ºC, а затем постепенно увеличивают температуру до 105-110 ºC.
|
Теплоизоляционный материал (заявка 1215742 Японии, СОЗС 11/00, опубл. 29. 08. 1989) получают на основе стеклобоя в качестве основного компонента с добавками Al2O3, бентонита и растворимого стекла в качестве пенообразователя. В другом варианте (заявка 1208346 Японии, СОЗС 27/12, опубл. 22. 08. 1989) порошок боя стекла, к которому добавляют порошок алюминия, кварцевый песок и другие, загружают в форму, сверху накладывают проволочную сетку и спекают материал, причем стекломасса заполняет ячейки сетки.
В способе непрерывного производства формованного пеностекла (заявка 3941732 ФРГ, СОЗВ 19/08,опубл. 12. 07. 1990) используют стеклобой, силикат натрия, минеральные вещества, смешанные силикаты, стеклообразователи, плавни и пенообразователи. Для снижения температуры размягчения стекла его смешивают с водным раствором остальных компонентов в присутствии связок, обеспечивающих гранулирование шихты.
На 100 частей стекла приходится от 5 до 85 частей суммы остальных компонентов. Смешение производится при 90 ºC, вспенивание в интервале 700-900 ºC, охлаждение до 50 ºC. Силикат натрия должен иметь модуль 3,2-3,6. В качестве плавня используется тетраборат натрия. Растворяемый силикат натрия добавляется в стеклообразующее борное сырье (тетраборат) и/или кернит, и/или сульфат цинка, и/или доменные шлаки, и/или карбонаты щелочно-земельных металлов, и/или оксиды металлов в количестве 0,2-20 %. Порообразователями служат разорит и/или меласса, и/или сахар, и/или сульфат цинка, и/или глицерин, и/или гликоль в количестве до 15 %.
Состав для изготовления вспученного материала (пат. 2173674 России, СО4В 28/26, опубл. 13. 08. 1998) содержит (масс. %): жидкое стекло 47-92; измельченный пеносиликат 5-18; наполнитель тонкоизмельченный минеральный 0,1-43; гелеобразователь, включающий олеиновую кислоту 0,02-0,04 и насыщенный водный раствор сахара 1-3.
При изготовлении вспученного материала смешивают жидкое стекло, пеносиликат, наполнитель и гелеобразователь, полученную смесь гранулируют в экструдере, гранулы подсушивают на воздухе в течение 2 часов или в сушилке при t > 100 ºC в течение 30 мин, укладывают в перфорированную металлическую форму и вспучивают в замкнутом объеме формы в печи при t = 400-500 ºC в течение 30-80мин. В варианте реализации получаемый при гранулировании бисер фиксируют в растворе CaCl2, высушивают при 50-70 ºC до конечной влажности 30-35 %.
Для повышения служебных характеристик жидкого стекла [234] его можно обрабатывать в электролизере (Стекло и керамика, 1991, №4, С.3-4) с повышением текучести в 2 раза и клеющей способности в 1,5-2 раза, также увеличивается значение рН.
С целью повышения теплового сопротивления ограждающих конструкций используют многослойные панели с полимерными утеплителями. Однако, такое решение не учитывает долговечности таких утеплителей и возможности выделения ими в процессе пожара токсичных продуктов сгорания. Для повышения теплового сопротивления ограждений рациональным является использование высокопористых неорганических композиций (ВНК), изготовленных полностью на неорганической основе или с введением небольшого количества (до 4 %) полимерных модификаторов. В связи с этим, предлагается [235] утеплитель “Силаст” на основе жидкого стекла, получаемый в установке для производства ВНК, содержащей (рис. 55, а): 1 - бак-смеситель; 2 - перемешивающее устройство; 3 - фильтр; 4 - бак для пенообразователя; 5 - пеногенератор; 6 - пневматический пульт распределения; 7 - распыливающая форсунка-смеситель; 8 - раздатчик-гомогенизатор, 9 - бак для технологических добавок; 10 - компрессор. При работе цементная суспензия готовится в баке 1, туда же могут подаваться полимерные добавки. Раствор пенообразователя заливается в бак 4. После приготовления суспензии в баки подается сжатый воздух от компрессора 10. При установлении рабочего давления открываются соответствующие краны на пульте управление, и в пеногенератор 5 подается сжатый воздух и раствор пенообразователя из бака 4. В пеногенераторе 5 формируется пена, которая направляется в раздатчик 8. Туда же направляется цементная суспензия, которая распыляется на форсунке 7 и впрыскивается в пену. В распылительную форсунку может направляться технологическая добавка из бака 9. В раздатчике смесь интенсивно перемешивается и заливается в утепляемую полость или форму. За счет действия технологических добавок, ВНК через 5-15 мин приобретают структурную прочность, которая не позволяет сформированной пористой структуре разрушаться. При этом вводимые технологические добавки из бака 9 и полимерные добавки, вводимые вместе с цементом, ускоряют твердение и придают ВНК повышенную прочность. По данной технологии возможно получение ТИ материалов на различных вяжущих (портландцементах, магнезиальных и жидкостекольных вяжущих и высокоглиноземистых цементах).
Рис. 55. Схема для производства высокопористой неорганической композиции (а) и кинетика параметров твердения и структурообразования этой композиции (б)
В соответствии с традиционными представлениями реакции твердения большинства неорганических строительных вяжущих как воздушных, так и гидравлических, протекают на границе раздела твердой фазы. В общем виде кривая А (рис. 55, б) кинетики твердения проходит следующие этапы. В течение индукционного периода 0-1 происходит активация поверхности раздела, формирование на ней термодинамических и структурных условий для начала образования новой фазы и начинается растворение продуктов новообразований. Реакция при этом протекает медленно и многие физические свойства вяжущей композиции, в частности ее вязкость, остаются практически неизменными. На участке 1-2 в жидкой фазе происходит появление зародышей новообразований, их рост и слияние, что сопровождается ростом структурной вязкости композиции. В целом данный участок характеризует протекание кинетической части реакции. Завершение процесса формирования новообразований характеризуется замедлением реакции и переходом в диффузионную фазу (2-3), то есть дальнейшие процессы взаимодействия реагирующих веществ протекают через поверхность раздела вновь образовавшейся твердой фазы. В высокопористой неорганической композиции параллельно протекают процессы формирования пористой структуры и ее разрушение. Поведение такой композиции схематично представлено кривой В. Формирование пористой структуры производится в течении индукционного периода (участок ОК кривой В). При этом если период пеноустойчивости (участок KL) меньше индукционного периода пористой композиции, то произойдет ее разрушение. Если же период пеноустойчивости (участок KN), превосходит индукционный период, то на кинетическом участке (кривая А), произойдет фиксация сформированной пористой структуры с последующим нормальным ее твердением. Вышеприведенный анализ показывает, что возможны два пути формирования пористой структуры: повышение пеноустойчивости и уменьшение индукционного периода твердения композиции. Характер твердения композиции с коротким индукционным периодом схематично иллюстрируется кривой С (рис. 55, б), согласно которой реализуются различные варианты пенобетонной технологии. Однако при заливке монолитных объектов композициями с большим индукционным периодом твердения происходит вытекание раствора через любые щели опалубки. Высокий гидростатический напор такой ВНК приводит к раздуву заливаемой опалубки, а если осуществляется заливка блоков в стационарных условиях, то данное обстоятельство резко снижает оборачиваемость формовочной оснастки. С практической точки зрения, индукционный период твердения ВНК не должен превышать 30 мин, а в идеале- 5 мин. Применительно к цементным композициям для снижения индукционного периода твердения возможно применение известных ускорителей. Однако во многих технологиях пена вводится в перемешиваемое цементно-песчаное тесто, с последующей перекачкой пенобетонной смеси насосами в заливаемую полость. Причем введение эффективных ускорителей в пенобетон может привести к забивке перекачивающего насоса и транспортировочных шлангов. Наиболее эффективным механизмом предотвращения разрушения ВНК на стадии свежего пенообразования является введение добавок, предотвращающих отток жидкости из пленок. Можно выделить несколько групп стабилизаторов пористой структуры ВНК, реализующих данный механизм: мелкодисперсные добавки, способные поглощать большое количество воды; органические добавки, повышающие вязкость жидкости внутри пленок (протеин, сапонин); добавки, способные поглощать большое количество кристаллизационной влаги. Добавки, способные создать в цементной композиции соединения из третьей группы организуются [235], когда в цементный клинкер при помоле вводится дигидрат сульфата кальция, являющийся замедлителем твердения цемента, а для ускорения твердения можно нейтрализовать действие гипса, связав его в другие химические соединения поглощающие воду. При этом связывание дигидрата сульфата кальция помимо стабилизации пористой структуры приводит к общему ускорению твердения композиции, так как алюминатная С3А и ферритная С4АF фазы клинкера начинают быстрее гидратироваться. Известно, что наилучшими соединениями, в которые может быть преобразован дигидрат сульфата кальция, являются гидросульфоалюминаты кальция или алюмокалиевые квасцы, поскольку одна молекула гидросульфоалюмината кальция способна связать 31 молекулу воды, а алюмокалиевые квасцы- 14 молекул. Для сокращения индукционного периода необходимо создавать данные соединения сразу после смешения цементной суспензии с пеной. Минимальный индукционный период достигается при стехиометрическом соотношении дигидрата сульфата кальция, содержащегося в цементе, и добавки, что приводит к образованию в композиции эттингита или алюмокалиевых квасцов. Получение ТИ ВНК с плотностью 200 кг/м³ на чисто цементной основе с высокими физико-механическими характеристиками затруднено, поскольку при производстве вместе с водой затворения и пеной в систему вводится большое количество воды (В/Ц = 0,8-0,9), что препятствует формированию прочной структуры. Для повышения свойств ТИ ВНК может использоваться: активация цементного теста при перемешивании, введение типовых пластификаторов и высокомолекулярных полимеров. При этом перед смешением цементной суспензии с пеной в суспензию вводится упрочняющая добавка и с водой затворения могут также вводится ускоряющие добавки. При твердении в структуре ВНК формируются зародыши новообразований, отличающиеся от структуры цементной композиции. Зародыши новообразований блокируются высокомолекулярным полимером, не позволяющим сформироваться крупнокристаллической структуре. В результате в стенках ВНК образуется мелкокристаллическая полимерсиликатная композиция, обладающая высокой когезионной прочностью.
Пеногипсовые изделия
Технология изделий на основе пеногипсовых систем включает [236-239] следующие технологические операции: предварительную подготовку исходных компонентов; вспенивание раствора ПАВ; минерализацию полученной пены; виброформование пеногипсовой массы; тепловую обработку заготовок и их механическую обработку. Регулирование средней плотности пеногипса достигается путём изменения кратности пены и степени её заполнения гипсовым вяжущим, размера пор – изменением скорости вращения рабочего органа пеногенератора, прочностных показателей – применением полимерных добавок и степенью армирования диспергированным минеральным волокном, теплоизоляционных свойств – кратностью и кинетической устойчивостью пены. Исходными компонентами являются (с расходом на 1 м2 и 1 м3 в кг и содержание в вес/ч, соответственно): гипсовое вяжущее марки не ниже Г-5-8; 400 и 100; вода (по В/Г) – 4,8; 240 и 40-70; синтетическое ПАВ анионоактивного класса – 0,016; 0,8 и 0,1-0,2; полимерная дисперсия ПВА – 0,3; 15 и 1-5; рубленное стекловолокно – 0,04; 2 и 0,5-1. Подготовка исходных компонентов заключается в приготовлении раствора ПАВ нужной концентрации и рубки стекложгута на волокна длиной 0,5-1 см. Приготовление раствора ПАВ предусматривает также введение в него дисперсии ПВА и части рубленного волокна. Основная часть волокна (80 %) вводится в массу вместе с гипсовым вяжущим. Таким образом, в результате выполнения предварительной подготовки компонентов все материалы находятся либо в гидромассе (ПАВ, волокно ПВА), либо в гипсовом вяжущем (волокно).
Вспенивание раствора ПАВ осуществляется в вертикальном лопастном смесителе. При этом обеспечивается получение пены с нужным размером ячеек и с равномерным распределением волокна по объему пены. Минерализация пены является процессом приготовления формовочной пеномассы, который должен обеспечивать равномерное распределение гипсового вяжущего и волокна по объему пены и структурирование массы путем регулирования продолжительности и интенсивности перемешивания. Минерализация пены путем введения в техническую пену сухого гипса осуществляется в лопастных или пальчиковых смесителях с n = 500-800 мин-1. Пластично-вязкие свойства пеномассы регулируются за счет изменения соотношения пены и гипсового вяжущего.
Формование изделий из пеногипсовых масс заключается в равномерном распределении массы на плоскости конвейера, ее уплотнении и калибровке. Для облегчения процесса формования целесообразно применять вибрацию со следующими параметрами: продолжительность – 20-30 с, частота – 50 Гц, амплитуда – 0,5 мм. За счет тиксотропных свойств массы снижаются предельное напряжение сдвига и вязкость, в результате чего обеспечивается удаление крупных воздушных пузырей и улучшается растекание массы в форме-поддоне. Сушка начинается через 25-30 мин после схватывания гипсового вяжущего, причем на первой стадии обеспечивают обдув заготовок теплоносителем с t = 45-50 ºC, с последующим повышением до t = 70-75 ºC. Общая продолжительность сушки не превышает 5 часов.
Производство пеногипса, из-за коротких сроков схватывания вяжущего, осуществляется поризацией гипсовых материалов с применением ПАВ, обеспечивающих необходимое воздухововлечение при приготовлении раствора или при перемешивании гипсового теста с заранее приготовленной пеной [240]. Возможно получение пеногипсовых материалов методом сухой минерализации пены [241], включающем две основные операции: приготовление пены и ее минерализация путем подачи сухого порошка вяжущего на поверхность пены при одновременном перемешивании получаемой массы. Введение гипсового вяжущего в виде порошка на заключительной стадии вспенивания позволяет стабилизировать структуру пеномассы, перевести жидкую дисперсную среду в пластично-вязкую, а после гидратации и схватывания вяжущего в – твердую. Для получения пеногипса может использоваться гипсовое вяжущее марки Г-7, А-III, ПАВ анионактивного типа («Прогресс»), в качестве заполнителя – перлитовый песок М-75; отношение вода/гипс = 0,65-0,85, гипс/заполнитель = 1/3, интенсивность перемешивания массы – 400-800 об/мин; пенообразователи – струйные или дисковые.
В способе изготовления ТИ материала (заявка 2287978 Франции, В28С 5/00, СО4В 13/14, ЕО4В 1/88, F16L 59/14, опубл. 18. 07. 1976) подготавливают в виде пены смесь воды, ПАВ и гипса, и отливают ее в формы, давая схватиться и высохнуть.
В способе изготовления пористой гипсовой массы (заявка 2534427 ФРГ, СО4В 15/02, опубл. 10. 02. 1977), в закрытой емкости, наполненной на 1/4-3/4 объема водным раствором ПАВ, сжатым воздухом генерируется пена; сжатый воздух подается также в смеситель, в который дозируется вода и гипс. Масса интенсивно перемешивается в течение меньшего отрезка времени, чем время схватывания гипса, и выгружается из смесителя. Количество ПАВ в смеси составляет 0,1-0,08 % от массы гипса, соотношение воды к гипсу от 1:1 до 1:2,5. ПАВ содержат два компонента (мас. %): первый – 27,5 сульфоната С10-С12 эфира; 6,0 С12-С14 эфира; 5,0 натриевой соли олеиновокислого N-метилтуарида; 7,5 С16-С18 олефинсульфоната; 3,5 5 %-ного раствора ПС12 спирта в бутилдигликольэтанольной смеси (1:1); 12,5 бутилдигликоля и остальное – воду; второй – 11,5 сульфата С10-С12 эфира; 10,0 натриевой соли олеинокислого N-метилтаурида; 6,0 С17-С18 олефинсульфоната; 25 бутилдигликоля и воду. Пену средней плотности – 0,04-0,06 г/л получают, продувая 0,1-0,8 м3/час воздуха через раствор, содержащий 5 л воды и 5 мл смеси первого и второго компонентов. Получают пеногипсовые ТИ изделия средней плотности 330 кг/м3 (пористостью 85 %), прочностью на сжатие 0,56 МПа на растяжение при изгибе – 0,51 МПа и λ > 0,08 Вт/(м×К).
В способе производства пеногипса (заявка 2546181 ФРГ, СО4В опубл. 28. 04. 1977) в гипсовое тесто, содержащее добавки разжижителей, регуляторов схватывания и стабилизации пены, вводят 1-30 % пенообразователей, в качестве которых используют изоцианаты и (или) полиуретановые аддитивные соединения, получаемые при взаимодействии пересыщенных изоцианатов с содержащими группы ОН полиэфирами и соединениями с аминогруппами. При введении 5-7 % такого пенообразователя процесс завершается за 20 мин с получением материала с плотностью 0,45-0,8 г/см3. Меламиновую смолу (0,1-3 % в расчете на количество гипса) применяют как разжижитель гипсового теста, карбоксиметилцеллюлозу в количестве 0,1-2 % – как замедлитель схватывания, силиконы или метилцеллюлозу в количестве 0,1-2 % – как стабилизатор пены.
Для производства гипсовых плит с пониженной средней плотностью рекомендуют (пат. 52-32763 Японии, СО4В 21/00, опубл. 24. 08. 1977) в раствор добавлять нормальный α-олефиновый сульфонат с содержанием 10-14 атомов углерода, например алкилбензосульфонат натрия. При этом смесь гипса с добавкой вспенивают воздухом, а затем из этой массы формуют плиты.
Развитием смесителя для приготовления гипсовых поризованных смесей (а. с. 688345 СССР, В28С 5/38, опубл. 1978), содержащего корпус, имеющий загрузочный и разгрузочный патрубки, с трубопроводом для подачи воды и пенообразователя, и расположенным в нем полым валом с распределительной тарелкой, концевая часть которого выполнена перфорированной с расположенными в его полости перемешивающим приспособлением в виде лопастей, а на внешней поверхности вала закреплены радиальные кронштейны с пальцами, причем для повышения эффективности работы путем улучшения качества пены, он снабжен патрубком для подачи сжатого воздуха и, имеющей отверстия на периферийной части, перегородкой, прикрепленной к корпусу по периметру с образованием камер, в каждой из которых расположены радиальные кронштейны с пальцами, перемешивающее приспособление имеет привод вращения с планетарной передачей, на сателлитах которой установлены лопасти, венец жестко закреплен на внутренней поверхности полого вала, причем патрубок для подачи сжатого воздуха расположен соосно в трубопроводе для подачи воды, а последний соединен с полым валом в его концевой части.
Развитием конструкции мешалки непрерывного действия для приготовления пеногипсовых смесей (а. с. 408813 СССР, В28С 5/16, опубл. 1972), содержащей цилиндрический корпус с загрузочными и разгрузочными патрубками, в котором расположен приводной полый вал с распределительной тарелкой, концевая часть которого выполнена перфорированной и имеет закрепленные на ней радиальные кронштейны с параллельными полому валу кольцами, с целью повышения качества смеси за счет обеспечения равномерного распределения пены, является ее выполнение (а. с. 887202 СССР, В28С 5/38, опубл. 07. 12. 1981), с имеющей на внутренней поверхности радиальные ребра, камерой, сообщенной с полым валом и расположенной на концевой перфорированной части вала между распределительной тарелкой и кронштейнами с пальцами, причем последние выполнены полыми и соединены с камерой посредством выполненных в кронштейнах каналов. Мешалка содержит корпус 1 (рис. 56) с загрузочным 2 и разгрузочным 3 патрубками, в котором расположен приводной полый вал 4 с распределительной тарелкой 5. Концевая часть 6 вала 4 выполнена перфорированной и имеет закрепленные на ней радиальные кронштейны 7 с параллельными полому валу 4 пальцами 8. Мешалка выполнена с имеющей на внутренней поверхности радиальные ребра 9 камерой 10, сообщенной с полым валом 4 и расположенной на концевой перфорированной части вала между распределительной тарелкой 5 и кронштейнами 7 с пальцами 8, которые имеют каналы 11 и соединены с камерой посредством выполненных в кронштейнах 7 каналов 12. Вал 4 приводится во вращение от привода 13.
Рис. 56. Мешалка непрерывного действия для приготовления пеногипсовых смесей
При работе от привода 13 (рис. 56) приводится во вращение полый вал 4 с распределительной тарелкой 5 и кронштейнами 7. В загрузочный патрубок 2 подается гипс, одновременно через полый вал 4 в камеру 10 поступает вода с пенообразователем. При интенсивном перемешивании воды с пенообразователем в камере 10 образуется пена, которая через отверстия перфорации части 6 и одновременно через каналы 11 и 12 за счет избыточного давления жидкости внутри полости вала 4 и камеры 10 и под действием центробежных сил, которые возникают при вращении вала, поступает в корпус 1 и равномерно распределяется в гипсовой массе и смесь удаляется через разгрузочный патрубок 3.
Известно устройство для приготовления гипсовой массы (а. с. 688345 СССР, В28С 5/16, опубл. 1978), содержащее корпус, крышку с перегородками, установленный между ними диск с перемешивающими пальцами. Также известен смеситель, в котором имеется загрузочный и разгрузочный патрубки, корпус с трубопроводом для подачи воды и пенообразователя и расположенным в нем полым валом с распределительной тарелкой, концевая часть которого выполнена перфорированной с расположенным в его полости перемешивающим приспособлением в виде лопастей, а на внешней поверхности вала закреплены радиальные кронштейны с пальцами. Для повышения эффективности работы смесителя за счет улучшения качества пены, он снабжен патрубком для подачи сжатого воздуха и имеющей отверстия на периферийной части перегородкой, прикрепленной к корпусу по периметру с образованием камер, в каждой из которых расположены радиальные кронштейны с пальцами, перемешивающее приспособление имеет привод вращения с планетарной передачей, на сателлитах которой установлены лопасти, венец жестко закреплен на внутренней полости полого вала, причем патрубок для подачи сжатого воздуха расположен соосно в трубопроводе для подачи воды, а последний соединен с полым валом в его концевой части (а. с. 903132 СССР, В28С 5/38, опубл. 07. 02. 1982). Смеситель содержит (рис. 57) загрузочный 1 и разгрузочный 2 патрубки, корпус 3 с трубопроводом 4 для подачи воды и пенообразователя и расположенным в нем полым валом 5 с распределительной тарелкой 6, концевая часть которого выполнена перфорированной с расположенным в его полости перемешивающим приспособлением в виде лоп<
|
|
Индивидуальные очистные сооружения: К классу индивидуальных очистных сооружений относят сооружения, пропускная способность которых...
Адаптации растений и животных к жизни в горах: Большое значение для жизни организмов в горах имеют степень расчленения, крутизна и экспозиционные различия склонов...
История развития хранилищ для нефти: Первые склады нефти появились в XVII веке. Они представляли собой землянные ямы-амбара глубиной 4…5 м...
Архитектура электронного правительства: Единая архитектура – это методологический подход при создании системы управления государства, который строится...
© cyberpedia.su 2017-2024 - Не является автором материалов. Исключительное право сохранено за автором текста.
Если вы не хотите, чтобы данный материал был у нас на сайте, перейдите по ссылке: Нарушение авторских прав. Мы поможем в написании вашей работы!