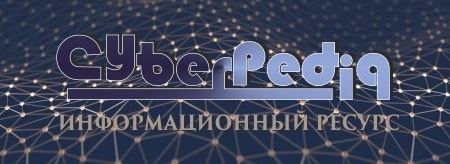
Опора деревянной одностоечной и способы укрепление угловых опор: Опоры ВЛ - конструкции, предназначенные для поддерживания проводов на необходимой высоте над землей, водой...
Кормораздатчик мобильный электрифицированный: схема и процесс работы устройства...
Топ:
Оснащения врачебно-сестринской бригады.
Комплексной системы оценки состояния охраны труда на производственном объекте (КСОТ-П): Цели и задачи Комплексной системы оценки состояния охраны труда и определению факторов рисков по охране труда...
Характеристика АТП и сварочно-жестяницкого участка: Транспорт в настоящее время является одной из важнейших отраслей народного хозяйства...
Интересное:
Средства для ингаляционного наркоза: Наркоз наступает в результате вдыхания (ингаляции) средств, которое осуществляют или с помощью маски...
Наиболее распространенные виды рака: Раковая опухоль — это самостоятельное новообразование, которое может возникнуть и от повышенного давления...
Берегоукрепление оползневых склонов: На прибрежных склонах основной причиной развития оползневых процессов является подмыв водами рек естественных склонов...
Дисциплины:
![]() |
![]() |
5.00
из
|
Заказать работу |
Степень оснащенности операций
Основным средством увеличения производительности является автоматизация металлорежущих станков, их работа в непрерывном режиме с минимальным участием людей, что и определяет степень оснащенности операций. В данном технологическом процессе обработка осуществляется станках с ручным управлением. Использование станков с ручным управлением снижает производительность в 2-4 раза. Также не используются автооператоры, промышленные роботы, поэтому установка и снятие заготовок осуществляется вручную, что в значительной степени увеличивает штучное время обработки.
Для закрепления заготовок на станках в большинстве случаев на предприятии используются непрогрессивные и устаревшие приспособления (механические), не только повышающие затраты времени на снятие-установку заготовок, но и увеличивающие погрешность обработки.
Для оснащения зенкера применяют трехгранный пластины с положительными задними углами и отверстием. Крепление и точная фиксация пластины в корпусе производятся винтом с конической головкой. Диаметр винта меньше диаметра отверстия пластины. При завинчивании винта коническая головка давит на криволинейную образующую пластины и фиксирует ее в корпусе зенкера, при этом ось отверстия пластины смещается относительно оси винта.
3.1.4 Резец
При токарной обработке наиболее рационально использовать резцы со сменными многогранными пластинами (СМП) из твердого сплава, поскольку они не требуют переточек и позволяют повысить режимы резания.
На практике наибольшую применяемость имеют режущие пластины квадратной, ромбической (угол при вершине ), шестигранной (
), трехгранной и круглой форм. Пластины из твердого сплава со сферическими лунками зарекомендовали себя с положительной точки зрения стружколома.
Выбираем проходной резец с шестигранной твердосплавной пластиной().
Материал заготовки – сталь 45, вид – поковка, твердость ≥240 НВ, предел прочности на растяжение s в=600МПа. Качество обработанной поверхности Rz40 мкм.
Станок токарный с ЧПУ 1П426ДФ3, размеры державки (В´Н) 20´20 мм.
Данная пластина имеет сферические лунки для обеспечения стружколомания. Чтобы оставить переднюю поверхность свободной при закреплении, принимаем конструкцию пластины с отверстием выбираем наиболее оптимальный способ базирования по боковым сторонам. Способ крепления используем угловым рычагом (через отверстие). Исходя из конструктивных соображений наиболее оптимальную конструкцию являеться крепления неперетачиваемой пластины, которая оставляет свободной переднюю поверхность пластины, обеспечивает четкое её позиционирование по трем точкам и максимальную быстросменность. Наиболее оптимальный вариант – крепление пластины угловым рычагом.
Рисунок 3.10 – Крепление СМП угловым рычагом
Определим материал режущей части резца. Для чистовой обработки стали согласно таблице П1 [7] можно использовать твердый сплав марки Т15К6 по ГОСТ 3882-74.
Определим оптимальные параметры режущей части резца. Угол в плане j зависит от назначения резца, j=95° [6]. Главный задний угол выбираем по таблице П2 [7], для чистовой обработки стали a=12°. Вспомогательный задний угол у проходного резца принимаем равным a1=8°. Угол при вершине пластины e =80°.
Угол в корпусе h, под которым должна быть установлена пластина для создания задних углов определим по формулам (1) и (2).
![]() ![]() ![]() ![]() ![]() | (3.48) (3.49) |
С учетом всех известных параметров получим:
.
Следовательно θ = 50,3°.
.
Угол h=12°.
Угол наклона режущей кромки l определим по формуле (3):
tgl=tga×tgq; | (3.50) |
tgl =tg12°×сtg50,3°=0,176.
Принимаем l=10.
При конструировании резца выбираем форму сечения державки – квадратную, так как при врезании пластины обеспечивается наименьшее снижение прочности державки и данная форма является наиболее оптимальной для данного резца с механическим креплением пластины.
Для определения минимальных размеров сечения державки резца используем формулу:
, (3.51)
где Pz – главная составляющая силы резания, кгс;
σu – допускаемое напряжение на изгиб материала державки, кгс/мм2; в нашем случае σu = 20 кгс/мм2 для незакаленной державки из конструкционной углеродистой стали [7].
Главная составляющая силы резания Рz [3] определяется по эмпирической формуле:
, (3.52)
где t – глубина резания, мм; t = 1;
S – подача, мм/об; S = 0,3;
V – скорость резания, м/мин; V = 160;
Сpz– коэффициент; Сpz = 300;
x, y, n- показатели степени; x = 1, y = 0.75, n = - 0,15;
Kpz- поправочный коэффициент.
Поправочный коэффициент Кpz представляет собой произведение ряда коэффициентов учитывающих фактические условия резания.
Крz= Кмр× Кjр× Кgр× Кlр×Кrр, | (3.53) |
где Кмр - коэффициент, учитывающий влияние качества материала заготовки на силовые зависимости, по таблице 9 [3]. Для стали Kмр = (sв/750)n, показатель степени n=0,75 при расчете силы Рz.
Кjр, Кgр, Кlр, Кrр – коэффициенты, учитывающие влияние геометрии инструмента на силу резания. По таблице 23 [3] Кjр=0,89, Кgр=1,1, Кlр=1,0, Кrр=0,9.
Кр=(800/750) 0,75×0,89×1,1×1×0,9=0.92.
Таким образом, главная составляющая силы резания:
кгс.
Ширину державки определяем по формуле (4):
=16,2 мм.
Округляем до 20 мм. Высоту державки принимаем H = 20 мм. Сверяясь со стандартами выбираем державку , где L = 120 мм – длина державки.
Из условия прочности приравняем действующий изгибающий момент максимальному моменту допускаемому прочностью державки:
, (3.54)
где вылет резца.
.
Проведем проверочный расчет по жесткости державки резца. Максимальная нагрузка, допустимая жесткостью резца:
, (3.55)
где f – допустимая стрела прогиба, мм; f = 0.05;
Е – модуль упругости материала державки резца, кгс/мм2; E = 20∙103;
I – момент инерции сечения державки, мм4;
, (3.56)
.
Необходимо, чтобы было Pz ≤ Pzж.
.
- условие выполняется.
Сила, действующая при резании, не превышает допустимой жесткостью резца, следовательно, резец обеспечивает необходимую при обработке жесткость.
Таблица 4.3 – Сравнение таблиц калькуляции себестоимости проектируемого и изготавливаемого изделий
Наименование статей | Проектируемый технологический процесс | Базовый технологический процесс | ||
Затраты | Затраты | |||
на деталь, руб. | на программу, руб. | на деталь, руб. | на програм-му, руб. | |
Основные материалы за вычетом отходов | 25,65 | 51,30 | 61,64 | 123,28 |
Транспортно-заготовительные расходы | 0,62 | 1,24 | 1,63 | 3,26 |
Топливо и энергия на технологические цели | 4,5 | 4,5 | ||
Основная з/п производственных рабочих | 28,30 | 56,60 | 47,59 | 95,18 |
Дополнительная заработная плата | 2,04 | 4,08 | 3,43 | 6,86 |
Отчисления на соц. страхование | 8,46 | 16,93 | 14,24 | 28,48 |
Расходы по содержанию и эксплуатации оборудования | 56,60 | 113,20 | 142,77 | 285,54 |
Общецеховые расходы | 24,06 | 48,11 | 40,45 | 80,9 |
Общезаводские расходы | 19,81 | 39,62 | 33,31 | 66,26 |
Расходы будущих периодов | 1,61 | 3,22 | 3,67 | 7,34 |
ИТОГО производственная себестоимость | 171,65 | 343,31 | 353,24 | 706,48 |
Внепроизводственные расходы | 6,89 | 13,74 | 14,13 | 28,26 |
Налоги, включаемые в себестоимость | ||||
ИТОГО полная себестоимость, в том числе | 179,51 | 359,03 | 368,37 | 736,74 |
План маркетинга (ценообразование).
Цена с возмещением издержек производства детали, производимой по проектному ТП:
, (4.3)
где С – фактические издержки производства изделия, С = 179,51 руб.;
З – административные расходы и расходы по реализации, З = 66,8 руб.;
Р – средняя норма прибыли на данном рынке, Р=20%.
Ц=179,51+66,8+0,2·(179,51+66,8)= 295,573 руб.
Цена с возмещением издержек производства детали, производимой по базовому ТП по формуле (4.3):
Ц=368,37+66,8+0,2(368,37+66,8)= 522,204 руб.
Рациональность метода получения заготовки для данного производства
Заготовка – поковка поступает на механическую обработку из штамповочного цеха. Способ получения заготовки – ковка. Поковка, заготовка или готовое изделие, получаемое ковкой или горячей объёмной штамповкой в кузнечно-штамповочном производстве.
Наиболее эффективным способом изготовления данной заготовки, является обработка металлов давлением, так как по сравнению с литьем обладает:
1) высокой производительностью, поскольку в результате однократноного приложения усилия можно значительно изменить форму и размер деформируемой заготовки;
2) формообразование заготовок при относительно малой величине отходов материала;
Также основным недостатком литейного производства является то, что плотность металла отливок в большинстве случае, как правило, ниже, чем у заготовок, полученные способом обработки металлов давления. Кроме того, пластическая деформация сопровождается изменением физико-механических свойств металла заготовки, что можно использовать для получения деталей с наилучшими эксплуатационными свойствами при наименьшей их массе.
Заготовка изготовляется способом горячей штамповкой, что объясняется меньшей трудоемкостью и энергозатратами.
Соответствие параметров установленного оборудования требованиям данной операции.
Рисунок 1.4 – Заготовка чашки
Базовый технологический процесс состоит из 38 операций, из которых 4 автоматно-токарных, 4 моечных, 5 токарно-винторезных, 2 сверлильные, 2 горизонтально-фрезерных, 6 слесарных, 2 протяжных, 2 укладки, 2 транспортных, 1 термообработка, 1 пескоструйная, 2 консервации, 1 круглошлифовальная, 1 АВЖ и 3 контрольных.
Рассмотрим порядок операций.
002 – Автоматная токарная.
Обработка производится на токарном полуавтомате, станок относится к станкам нормальной точности, что вполне достаточно для обеспечения требований предъявляемых к операции (шероховатость = Rz80, 10-14 квалитет точности). Выполняется обработка цилиндрической поверхности Æ64-0,4 и подрезается торец на расстоянии 37-0,62 от базового торца на данной операции.
Закрепление детали производится за цилиндрическую поверхность большего диаметра и торец. После обработки, цилиндрическая поверхность Æ64-0,4 используется в качестве базы на дальнейшей операции.
На данной операции достигается расположение обрабатываемой поверхности. На данной операции производится контроль, в качестве измерительного инструмента используют шаблон радиусный и штангенциркуль.
Рисунок 1.5 – операция 002
010 – Автоматная токарная.
Обработка производится на токарном полуавтомате, станок относится к станкам нормальной точности, что вполне достаточно для обеспечения требований предъявляемых к операции (шероховатость = Rz80, Rz40, 10-14 квалитет точности). На данной операции подрезается торец, обтачивается цилиндрически поверхность Æ92,5мм, светлится отверстие Æ23, растачивается отверстие Æ78+0,74, на глубине 22+0,28,и растачивается отверстие Æ60+0,4, на глубине 10+0,2, точится канавка. Закрепление детали производится за цилиндрическую поверхность меньшего диаметра и торец.
Рисунок 1.6 – операция 010
026 – Автоматная токарная.
Обработка производится на токарно-горизонтальном полуавтомате КСП6-160, станок относится к станкам нормальной точности, что вполне достаточно для обеспечения требований предъявляемых к операции (шероховатость = Rz80, Rz40, 10-14 квалитет точности).
На данной операции подрезается торец, обтачивается цилиндрически поверхность с Æ92,5мм до Æ90,7-0,23мм, светлится отверстие Æ23, растачивается отверстие с Æ78+0,74 до Æ82,09+0,14мм, на глубине 22,6+0,28, зенкеруется отверстие Æ24,3+0,52мм, это отверстие так же развертывается до Æ25,14+0,14мм.
Закрепление детали производится за цилиндрическую поверхность меньшего диаметра и торец.
035 – Автоматная токарная.
Обработка производится на токарно-горизонтальном полуавтомате КСП6-160, станок относится к станкам нормальной точности, что вполне достаточно для обеспечения требований предъявляемых к операции (шероховатость = Rz80, Rz40, 10-14 квалитет точности).
На данной операции подрезается торец, обтачивается цилиндрически поверхность с подрезкой торца, зенкеруется отверстие Æ92,5мм до Æ90,7-0,23мм.
Закрепление детали производится за цилиндрическую поверхность большего диаметра и торец.
Рисунок 1.7 – операция 026
041 – Автоматная токарная.
Обработка производится на токарно-горизонтальном полуавтомате, станок относится к станкам нормальной точности, что вполне достаточно для обеспечения требований предъявляемых к операции (шероховатость = Rz40, 10-14 квалитет точности). Зенкеруется канавка в пять позиций, исходная поверхность имеет размеры Æ38,2 и Æ52+0,4 , глубину 25+0,52 , размеры канавки после обработки Æ38-0,62 и Æ52+0,74 , глубину 31+0,62 . Закрепление детали производится за цилиндрическую поверхность большего диаметра и торец.
Рисунок 1.8 – операция 041
042 – Помывка.
043 – Токарная – винторезная.
Обработка производится на токарно-винторезном станке 1К62, станок относится к станкам нормальной точности, что вполне достаточно для обеспечения требований предъявляемых к операции (шероховатость = Rz40, 10-14 квалитет точности). Производить притупление острых кромок на закрепление детали производится за цилиндрическую поверхность меньшего диаметра и торец. Æ38, Æ52, Æ58.
050 – Сверлильная.
Обработка производится на агрегатно-сверлильном станке. Станок относится к станкам нормальной точности, что вполне достаточно для обеспечения требований предъявляемых к операции (шероховатость = Rz40, 10-14 квалитет точности). Сверлятся 6 отверстий Æ8,1, и зенкеруются до размера Æ8,18. Размер требуемого отверстия Æ8+0,36. Задан зависимый позиционный допуск в радиальном выражении.
Рисунок 1.9 – операция 050
052 – Вертикально-сверлильная.
Обработка производится на вертикально-сверлильном станке МН-10. На данной операции притупляются острые кромки у полученных на предыдущей операции шести отверстиях, обработка производится разверткой с цеховой заточкой.
Рисунок 1.10 – операция 052
055 – Горизонтально - фрезерная.
Обработка производится на Горизонтально фрезерном станке 6Р82. Фрезеруется освобождение. Закрепление детали производится по внутреннему отверстию, большего радиуса и торцу.
Рисунок 1.11 – операция 055
060 – Слесарная.
Зачищаются заусенцы после фрезерования. Оборудование – верстак.
065 – Горизонтально – фрезерная.
Обработка производится на фрезерном полуавтомате. Станок относится к станкам нормальной точности, что вполне достаточно для обеспечения требований предъявляемых к операции (шероховатость = Rz40, 10-14 квалитет точности). Фрезеруются пазы шириной 10,2+0,24 на глубину 11-0,43. Обработка осуществляется в 3 перехода, фрезеруется по 2 паза в двух заготовках одновременно. Поворот осуществляется автоматически.
Рисунок 1.12 – операция 065
067 – Слесарная.
070 – Слесарная.
Зачистка заусенцев после фрезерования с внутренней стороны, производится на станке П-58240 ЗЭМ, борфрезой.
075 – Протяжная.
Операция выполняется на горизонтальном – протяжном станке 7Б510. Станок относится к станкам нормальной точности, что вполне достаточно для обеспечения требований предъявляемых к операции (шероховатость = Rz 20, 7 квалитет точности). На операции задан допуск формы и расположения. Протягивается отверстие, шлицевой протяжкой, DÆ30+0,14, протягивание производится в 2 перехода, черновой и чистовой протяжкой. Закрепление производится по пазам и внутреннему торцу.
077 – Промывка.
Рисунок 1.13 – операция 075
080 – Токарно-винторезная.
Производится на токарно-винторезном станке 1К62. Производится зачистка внутреннего диаметра Æ25, зачищается торец после протягивания, притупляются острые кромки на спирали. Закрепление детали производится за цилиндрическую поверх ность меньшего диаметра и торец.
087- Слесарная. Верстак. Притупляются острые кромки.
088 – Промывка. Мойка тупиковая.
090 – Контроль промежуточный. Стол контролера.
092 – Укладка.
095 – Транспортная.
096 – Термообработка. Высокочастотная установка ЛГЗ -67.
098 – Слесарная. Верстак.
099 – Контроль ОТК.
Проверка твердости. Твердомер Роквелла ТР ГОСТ 23677-79.
100 – Пескоструйная. Камера пескоструйная.
105 – Консервировать детали.
110 – Протяжная.
Выполняется на горизонтально – протяжном станке 7Б510. Протягивается отверстие шлицевой чистовой протяжкой D Æ30+0,14. Закрепление производится по пазам и внутреннему торцу.
113 – Токарно-винторезная.
Обработка осуществляется на токарно-винторезном станке 1К62. Закрепление производится по цилиндрической поверхности меньшего диаметра и внутреннему торцу. На данной операции зачищается внутренний диаметр протягиваемого отверстия Æ25, притупляются острые кромки на спирали.
Рисунок 1.14 – операция 110
114 – Токарно-винторезная.
Обработка осуществляется на токарно-винторезном станке 1К62. Закрепление производится по цилиндрической поверхности большего диаметра и торцу. Станок относится к станкам нормальной точности, что вполне достаточно для обеспечения требований предъявляемых к операции (шероховатость = Rz40, 10квалитет точности). Растачивается отверстие Æ56+0,2 на глубину 5+0,75, после термообработки.
Рисунок 1.15 – операция 114
115- АВЖ.
Закрепление производится по цилиндрической поверхности большего диаметра и торцу. Точится конусная поверхность.
Рисунок 1.16 – операция 115
116 – Круглошлифовальная.
Рисунок 1.17 – операция 116
Обработка осуществляется на токарно-винторезном станке 1К62. Закрепление производится по внутреннему отверстию Æ25 и торцу. Станок относится к станкам нормальной точности, что вполне достаточно для обеспечения требований предъявляемых к операции (шероховатость = Rа2,5, 10 квалитет точности). Шлифуется цилиндрическая поверхность большего диаметра.
117 – Токарно-винторезная.
Обработка осуществляется на токарно-винторезном станке 1К62. Закрепление производится по внутреннему отверстию Æ25 и торцу. Станок относится к станкам нормальной точности, что вполне достаточно для обеспечения требований предъявляемых к операции (шероховатость = Rz40, 10квалитет точности). Зачищается диаметры Æ38 и Æ52, после термообработки и притупляются острые кромки.
120 – Слесарная. Верстак. Притупляются острые кромки после всей механической обработки.
Рисунок 1.18 – операция 120
125 – Промывка.
130 – Контроль. Стол контроллера.
133 – Консервировать детали.
135 – Укладка.
140 – Транспортирование.
История создания датчика движения: Первый прибор для обнаружения движения был изобретен немецким физиком Генрихом Герцем...
Состав сооружений: решетки и песколовки: Решетки – это первое устройство в схеме очистных сооружений. Они представляют...
Общие условия выбора системы дренажа: Система дренажа выбирается в зависимости от характера защищаемого...
Механическое удерживание земляных масс: Механическое удерживание земляных масс на склоне обеспечивают контрфорсными сооружениями различных конструкций...
© cyberpedia.su 2017-2024 - Не является автором материалов. Исключительное право сохранено за автором текста.
Если вы не хотите, чтобы данный материал был у нас на сайте, перейдите по ссылке: Нарушение авторских прав. Мы поможем в написании вашей работы!