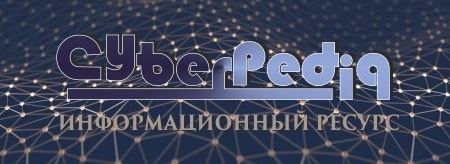
Семя – орган полового размножения и расселения растений: наружи у семян имеется плотный покров – кожура...
История создания датчика движения: Первый прибор для обнаружения движения был изобретен немецким физиком Генрихом Герцем...
Топ:
Процедура выполнения команд. Рабочий цикл процессора: Функционирование процессора в основном состоит из повторяющихся рабочих циклов, каждый из которых соответствует...
Характеристика АТП и сварочно-жестяницкого участка: Транспорт в настоящее время является одной из важнейших отраслей народного...
Особенности труда и отдыха в условиях низких температур: К работам при низких температурах на открытом воздухе и в не отапливаемых помещениях допускаются лица не моложе 18 лет, прошедшие...
Интересное:
Национальное богатство страны и его составляющие: для оценки элементов национального богатства используются...
Уполаживание и террасирование склонов: Если глубина оврага более 5 м необходимо устройство берм. Варианты использования оврагов для градостроительных целей...
Влияние предпринимательской среды на эффективное функционирование предприятия: Предпринимательская среда – это совокупность внешних и внутренних факторов, оказывающих влияние на функционирование фирмы...
Дисциплины:
![]() |
![]() |
5.00
из
|
Заказать работу |
|
|
Назначение футеровки подины – сформировать ванну соответствующей формы и размеров (см. § 4) для жидкого металла и шлака, а также обеспечить тепловую изоляцию металла в ванне. В подине современных ДСП располагают донные продувочные устройства, выпускное отверстие (в ДСП четвертого поколения – см. рис. 9), подовые электроды – аноды (в ДСП ПТ).
Рабочий слой подины испытывает механические нагрузки и резкое охлаждение при загрузке холодной твердой металлошихты, активно участвует в физико-химических процессах, происходящих в жидком металле, взаимодействует со шлаком, испытывает эрозионный и коррозионный износ в условиях высокой температуры, ферростатического давления и возможного электромагнитного перемешивания жидкого металла. Разрушение подины происходит двумя путями: оплавлением и вымыванием участков футеровки с пониженной огнеупорностью; при охлаждении печи в период ремонтов возможно рассыпание в порошок поверхностного слоя, содержащего двухкальциевый силикат.
Из назначения и условий работы подины вытекают основные требования к ее футеровке:
1) достаточная огнеупорность;
2) устойчивость против резких колебаний температуры;
3) механическая прочность при высокой температуре против ударов при загрузке шихты (температура подины не менее 1100 К) и против эрозионного износа при воздействии жидкого металла;
4) достаточно большое тепловое сопротивление.
Тепловое сопротивление подины, ограничивающее тепловые потери ванны, можно оценить из условия равномерности температуры по глубине металла, рассматривая ванну и подину как два последовательно соединенных тепловых проводника. При стационарном тепловом потоке имеем
|
, (109)
где и
– тепловое сопротивление соответственно ванны и подины;
и
– перепад температуры соответственно по глубине ванны и по толщине подины.
Поскольку тепловое сопротивление теплопроводности через 1 м2 прямо пропорционально толщине (глубине) слоя, то для определенной, технологически допустимой величины температурного перепада в ванне тепловое сопротивление подины
пропорционально глубине ванны
. С учетом соотношения величин эквивалентных коэффициентов теплопроводности жидкого металла и многослойной футеровки, перепада температуры
К и
К толщина подины
примерно равна максимальной глубине ванны
,т.е.
. (110а)
При современной одношлаковой технологии с применением донной продувки ванны жидкого металла отпадают ограничения по величине температурного перепада. Поэтому в соответствии с законом Фурье, при стационарной теплопроводности в последовательной тепловой цепи «ванна – подина» возможно снижение теплового сопротивления подины за счет уменьшения ее толщины на 20…25 % (аналогичное решение предлагал Н.В. Окороков для ДСП, оборудованных статором электромагнитного перемешивания), т.е.
, (110б)
и применения более теплопроводных, но имеющих большую стойкость периклазоуглеродистых огнеупоров.
Футеровка подины ДСП состоит из двух основных слоев: верхнего – рабочего набивного слоя, образующего прочную и плотную чашу жидкого металла и шлака, и нижнего слоя – кирпичной кладки.
Для тепловой изоляции днище кожуха ДСП покрывают одним или двумя листами асбестового картона марки КАОН (ГОСТ 2850–80) толщиной 10…20 мм, насыпают выравнивающий слой шамотного порошка толщиной 20…30 мм, на который укладывают один-два ряда шамотного марки ША (по ГОСТ 390–96 содержание Al2O3 не менее 30 %) или пеношамотного кирпича на «плашку» толщиной 65 или 130 мм, общая толщина теплоизоляции может быть 75…200 мм для ДСП разной вместимости.
Огнеупорную кладку сферической части подины выполняют из прямых периклазовых кирпичей марки П-91 (по ГОСТ 4689–94 содержание MgO не менее 91 %) размером 230´115´65. Кладку ведут «елочкой» от центра печи к периферии. Кирпичи устанавливают на «ребро» в несколько рядов со смещением каждого последующего ряда относительно предыдущего на 45°, чтобы перекрыть вертикальные швы. Швы кладки заполняют просеянным, предварительно нагретым периклазовым порошком мелкой фракции. Количество рядов зависит от толщины набивного рабочего слоя.
|
Огнеупорную кладку конической части подины (так называемый откос ванны, см. рис. 25) выполняют из прямых и радиальных клиновых (размером 230´115´93/65) периклазовых или периклазоуглеродистых (марки ПУПК) кирпичей, укладываемых на «плашку», обеспечивая угол наклона кладки к горизонтали 50…55° для последующей набивки под углом 45°. При этом необходимо обратить внимание на качество сочленения сферической или конической (и цилиндрической в случае ДСП с СКЦ-ванной) кладки как вероятного места ухода жидкого металла по причине изменения размера сферической кладки при нагреве. Поэтому между кладкой и боковой частью днища должен быть компенсационный температурный зазор, заполняемый периклазовым порошком после завершения кладки каждого слоя.
Рабочий слой подины набивают из сухого (так называемая сухая подина) мелкозернистого «электрометаллургического» периклазового порошка марки ППЭ-88 (по ГОСТ 24862–81 содержание MgO не менее 88 %) с постоянным армированием массива набивки крупнозернистыми фракциями. Толщина набивного слоя в зависимости от конструкции футеровки подины составляет от 100 до 800 мм.
Масса футеровки подины отечественных ДСП численно примерно равна вместимости печи т о,т.е. удельная масса футеровки составляет около 1 т/т.
Стойкость подины в значительной степени зависит от организации ремонта рабочего слоя. Поэтому одним из важных моментов ухода за футеровкой подины является тщательный осмотр ее после выпуска предыдущей плавки, очистка от шлака и металла с последующим ремонтом («заправка») разрушенных участков футеровки с применением периклазового порошка марки ППО3-86 (по ГОСТ 24862–81 содержание MgO не менее 86 %).
Как правило, износоустойчивость заправляемых участков набивных подин тем выше, чем быстрее и на большую глубину формируется прочная «рабочая зона» и чем медленнее она затем разрушается под действием механических нагрузок (например, при загрузке металлошихты). По данным ВостИО и завода «Амурсталь», применение порошков с сухой спекающей добавкой обеспечивает спекание в интервале температур 1400…1700 К и образование весьма прочного слоя толщиной до 100 мм. Применение таких «ремонтных» масс целесообразно при формировании «откоса» подины для получения заданной геометрии ванны как в начале кампании, так и в течение эксплуатации ДСП.
|
Подины ДСП служат от одного капитального ремонта до другого, который планируют в связи с необходимостью ремонта электрического и механического оборудования, т.е. стойкость подины, как правило, не лимитирует работы ДСП, она составляет 3000…4000 плавок на основе порошка ППЭ-88 и более 6000 плавок на основе набивной массы Ankerhearth австрийской фирмы Radex. Удельный расход огнеупорных и заправочных материалов составляет, по данным Гипромеза, 20…30 кг/т.
В футеровке эркерной части подины ДСП четвертого поколения расположено донное выпускное отверстие. Ось отверстия диаметром 160…180 мм делают вертикальной или под некоторым углом (до 5°), обеспечивая определенную траекторию струи жидкого металла. Футеровка отверстия (рис. 40) состоит из внешнего длинного стакана, набранного из колец высотой 150…200 мм и диаметром 550/400 мм, и сменного внутреннего стакана, формирующего выпускное отверстие (рабочий канал). Оба стакана изготовляют из периклазоуглеродистых или карборундовых огнеупоров, обладающих высокой термостойкостью и сопротивлением эрозионному износу, что обеспечивает срок службы (150–200 выпусков), достаточный для недельных кампаний между полными выпусками металла из ДСП.
Рабочий канал внизу заканчивается графитовой или периклазоуглеродистой концевой втулкой, которую перекрывают графитовой запорной плитой, установленной на шарнирном откидном клапане (см. рис. 40), или шибером с пневматическим или гидравлическим приводом.
Рабочий канал перед началом очередной плавки засыпают периклазовым порошком через сводик эркера или через сводовое отверстие ДСП с овальным рабочим пространством.
Конструкция футеровки подины ДСП ПТ зависит от типа подовых электродов-анодов, которые могут быть* (рис. 41):
|
– стержневые (один или несколько в зависимости от электрической схемы питания). Верхняя часть стержня диаметром 150…180 мм стальная, контактирующая с жидким металлом и потому расходуемая, но возобновляемая за счет остатка металла на подине. Нижняя часть выполнена в виде медного корпуса с водяным охлаждением и термопарами для контроля теплового состояния (см. рис. 41, а);
– пластинчатые в виде медной плиты толщиной 15…20 мм и диаметром порядка 80 % диаметра кожуха, укладываемой на днище и имеющей воздушное охлаждение; контакт с ванной жидкого металла обеспечивается двухслойной токопроводящей футеровкой подины: верхний рабочий слой – периклазовые кирпичи с металлическими Г-образными прокладками – пластинами или кирпичи, плакированные медью (допустимая плотность тока – до 1,7 А/см2), нижний арматурный слой – периклазоуглеродистые кирпичи с содержанием углерода (графита) до 18 % (см. рис. 41, б);
– многоштырьевые в виде 80–200 стальных контактных стержней – штырей (рис. 41, в и г) или до 500 стальных игл (игольчатые) диаметром 6 мм, вертикально пронизывающие набивную подину и охлаждаемых сжатым воздухом;
– многопластинчатые (рис. 41, д и е).
Рис. 41. Схемы подовых электродов-анодов ДСП ПТ:
а – стержневой; б – пластинчатый с токопроводящей футеровкой;
в и г – многоштырьевой; д и е – многопластинчатый
Стойкость подовых электродов-анодов составляет 1200–1500 плавок; их замена происходит вместе с центральной набивной частью футеровки подины, что осложняет эксплуатацию ДСП ПТ.
Конструкция футеровки стены
Назначение стены – сформировать «свободное» пространство как часть рабочего пространства ДСП для размещения загружаемой металлошихты и обеспечения соответствующей схемы направленного теплообмена (см. § 4). Температурные условия тепловой работы футеровки стены значительно тяжелее, чем подины, так как она в период «открытого» горения дуг подвергается непосредственному излучению от них. Скорость изменения температуры внутренней поверхности достигает 30…100 К/мин к концу периода расплавления и даже 150…170 К/мин при открывании рабочего пространства во время заправки или загрузки металлошихты. В нижних горизонтах стены футеровка подвержена комплексному разрушающему воздействию металла, шлака, печной атмосферы и высоких температур. Разрушение огнеупорной футеровки стены происходит в результате оплавления и стекания расплавленной массы с пониженной огнеупорностью или сколов, вызванных термическими или структурными изменениями.
Из назначения стены и условий ее работы вытекают основные требования к ее футеровке:
а) высокая огнеупорность;
|
б) высокая термическая устойчивость (термостойкость);
в) малое тепловое сопротивление.
Последнее условие исключает требование тепловой изоляции, как противоречащее проблеме снижения максимальных температур на внутренней поверхности футеровки с целью повышения стойкости стены.
В зависимости от величины тепловой мощности ДСП стены могут быть:
1) футерованы огнеупорной кладкой (на ДСП обычной и повышенной мощности);
2) выполнены из водоохлаждаемых панелей* (на ДСП высокой и сверхвысокой мощности).
Конструкцию огнеупорной кладки выбирают в зависимости от характера износа кирпичей, от формы «свободного» пространства и кожуха ДСП. Как уже было отмечено, износ основных огнеупоров происходит оплавлением в «горячем поясе» вблизи зеркала ванны; под воздействием шлака – в шлаковом поясе; скалыванием и оплавлением – выше шлакового пояса. Износ кирпича в верхних рядах составляет не более 40 %, однако возможно обрушение кладки при разгаре нижележащих слоев. Поэтому верхние ряды целесообразно выкладывать из кирпичей меньшей длины. Такая кладка стены уступами способствует более равномерному износу по высоте за кампанию футеровки.
Обычно стена имеет рабочий слой толщиной . Во избежание повреждения кожуха ДСП при аварийном полном разрушении рабочего слоя целесообразно применять дополнительный, арматурный («броневой») слой толщиной
. Для этого кожух обкладывают прямым периклазовым кирпичом (ГОСТ 4689–94) на «плашку» (65 мм) или на «ребро» (115 мм). Арматурный слой служит от одного капитального ремонта до другого.
Рабочий слой огнеупорной кладки стены ДСП второго поколения выполняют из большемерных прямых и торцевых клиновых термостойких периклазохромитовых кирпичей марки ПХСУТ (по ГОСТ 10888–93 массовая доля Сr2O3 7…15 %, MgO не менее 70 %), укладываемых на «ребро» (150 мм) с постепенным уменьшением толщины (для средних и крупных ДСП): нижняя часть 460, средняя часть 380 и верхняя часть 300 мм.
Для компенсации теплового расширения кирпичной кладки по окружности через четыре – шесть кирпичей укладывают выгорающие (деревянные или толевые) прокладки толщиной 0,5…1 мм. Кладку выполняют насухо, с пересыпкой швов периклазовым порошком.
Стойкость футеровки стены зависит от конструкции огнеупорной кладки, вида и качества кирпича, сортамента выплавляемых сталей, размера и мощности ДСП. По данным Гипромеза, стойкость коническо-цилиндрической стены малых печей составляет 1500–2000 плавок, крупных 100–150 плавок. Низкая стойкость футеровки увеличивает число ремонтов, расход огнеупоров, длительность простоев и т.п., т.е. ухудшает технико-экономические показатели ДСП. Поэтому на мощных и сверхмощных ДСП вместо огнеупорной кладки применяют водоохлаждаемые панели различной конструкции:
– трубчатые панели прямоугольной (для стены) или трапециевидной (для комбинированного свода) формы,
– сварные коробки (кессоны*), в которых полости формируют перегородками для обеспечения скорости охлаждающей воды 2…6 м/с; при этом возможна неравномерность потока воды, протекающей по лабиринту полостей, и неизбежная термическая деформация сварных швов.
Для уменьшения тепловых нагрузок на водоохлаждаемые элементы к тепловоспринимающей поверхности приваривают шлакодержатели («шипы») для удержания огнеупорной обмазки и конденсирующихся брызг шлака и металла в виде гарнисажа** [теплопроводность 0,1…0,4 Вт/(м·К)]. Толщина гарнисажа зависит от плотности падающего теплового потока, поскольку его тепловоспринимающая поверхность является подвижной границей раздела твердой и жидкой (оплавляющейся) фаз, имеющих постоянную температуру «солидус» (порядка 1635…1675 К). Например, на стальной [коэффициент теплопроводности порядка 50 Вт/(м×К)] трубе 90´16 при тепловом потоке 100, 300 и 450 кВт/м2 формируется гарнисаж толщиной 35, 10 и 6 мм соответственно. Для увеличения толщины гарнисажа при плотности теплового потока 400…600 кВт/м2 применяют стальную трубу с меньшей толщиной стенки (70´12), а при тепловой нагрузке свыше 600 кВт/м2 (на нижних горизонтах стены) – медную трубу [коэффициент теплопроводности порядка 390 Вт/(м×К)]. При тепловой нагрузке более 1 МВт/м2 в системе охлаждения возможен режим пленочного кипения воды (так называемый кризис конвективной теплоотдачи) и разрушение водохлаждаемого элемента.
Труба как конструктивный элемент системы водяного охлаждения обладает высокой механической и усталостной прочностью, минимальными термическими напряжениями в конструкциях и достаточно высокой надежностью в условиях давления охлаждающей воды при максимальной температуре 380 К, особенно в случае пароиспарительной системы охлаждения. Недостаток трубчатых панелей связан с повышенным гидравлическим сопротивлением, что требует увеличения напора в системе охлаждения (до 1 МПа).
Трубчатые панели изготовляют в виде:
– двух гнутых (наподобие плоской архимедовой спирали) змеевиков, вложенных один в другой (двойная спираль конструкции ОАО СКБ «Сибэлектротерм»); ресурс работы 2000–3000 плавок;
– ряда горизонтальных и вертикальных прямых труб, к концам которых для обеспечения циркуляции охлаждающей воды приваривают штампованные переходники. Такая конструкция более надежна в работе, обеспечивает минимальные зазоры между трубами и исключает возможность загиба отдельных витков в рабочее пространство печи; ресурс работы 14 000 ч;
– труб с межтрубными пазами шириной 0,9…1,6 диаметра трубы для прочного формирования и длительного удержания гарнисажа (энергосберегающие панели конструкции ОАО СКБ «Сибэлектротерм», снижающие тепловые потери с охлаждающей водой на 30…40 %); ресурс работы 7000–9000 плавок;
– труб с переменной плотностью укладки, с неодинаковыми межтрубными пазами в зависимости от падающих тепловых потоков (решетчатые сводовые элементы).
Стена имеет сегментную водоохлаждаемую футеровку из 12–16 элементов (в зависимости от диаметра корпуса), которые навешивают на специальные кронштейны на внутренней поверхности корпуса (рис. 42). Воду подводят (в нижнюю полость панели) и отводят (из верхней полости) от кольцевых коллекторов, установленных снаружи, через разъемные фланцевые соединения. Конструкция крепления и водопровода должна обеспечивать независимый монтаж и демонтаж панели на случай аварийного ремонта.
Рис. 42. Конструкция стены с водоохлаждаемой футеровкой:
1 – рабочий слой футеровки подины; 2 – откос ванны;
3 – огнеупорная футеровка стены; 4 – заправочная масса;
5 – трубчатый водоохлаждаемый элемент; 6 – гарнисаж; 7 – песчаный затвор; 8 – сливной коллектор; 9 – напорный коллектор; 10 – днище
Такие стены выдерживают тысячи плавок, в результате чего сокращаются простои оборудования и уменьшаются затраты на ремонт. Отсутствие больших масс огнеупорных материалов исключает энергозатраты на их нагрев («аккумулируемая» энергия), оплавление и соответствующее дополнительное шлакообразование. Кроме этого, увеличивается объем рабочего пространства на 10…30 % при неизменных диаметрах ванны и корпуса, что снижает требования к насыпной плотности металлошихты.
Вместе с тем водоохлаждаемые стены неблагоприятно влияют на тепловую работу ДСП:
1) возрастают тепловые потери в системе водяного охлаждения, что требует дополнительного ввода тепловой мощности в рабочее пространство;
2) возможно увеличение удельного расхода электроэнергии на 10…20 кВт·ч/т;
3) снижается температура теплоизлучающих поверхностей «свободного» пространства, нарушая условие направленного косвенного радиационного теплообмена (см. рис. 25);
4) существует опасность соприкосновения жидкого металла с металлическими (медными) водоохлаждаемыми панелями при барботаже ванны в окислительный период и при сливе металла из печи. Поэтому панели устанавливают на некоторой высоте над откосом ванны (не менее двух-трех рядов кладки), уступами поднимая их вблизи выпускного отверстия. Такая мера уменьшает поверхность охлаждения до 55…65 % (в ДСП третьего поколения) и до 70…80 % (в ДСП четвертого поколения) от величины площади внутренней поверхности стены (рис. 43).
Рис. 43. Развертка водоохлаждаемой футеровки стены ДСП третьего (а) и четвертого (б) поколений
Для повышения стойкости огнеупорной футеровки нижней части стены применяют теплопроводные периклазоуглеродистые огнеупорные кирпичи марки ПУПК с последующим восстановлением изношенного слоя футеровки после каждой или нескольких плавок методом торкретирования*.
Как уже отмечалось, для эксплуатации ДСП сверхвысокой мощности применение водоохлаждаемой футеровки является необходимым условием. На таких печах в результате значительного сокращения длительности плавки возможно даже уменьшение удельного расхода электроэнергии согласно уравнению (23), несмотря на увеличение мощности тепловых потерь.
Расход воды (на 1 м2 тепловоспринимающей поверхности стены) составляет 5…10 м3/ч при плотности тепловых потоков 100…300 кВт/м2.
Конструкция футеровки свода
Свод имеет такое же назначение, как и стена, но работает в более тяжелых условиях: более высокие тепловые нагрузки от дуг и от зеркала ванны из-за больших значений локальных и средних угловых коэффициентов; более резкие колебания температуры внутренней поверхности при открывании печи поворотом свода. Конструкция свода осложняется необходимостью иметь отверстия для электродов (с соответствующей электроизоляцией, если материал свода обладает электрической проводимостью), газоотсоса, кислородной фурмы, ТКГ и т.д.
В зависимости от величины тепловой мощности ДСП свод может быть:
1) кирпичным сферической (купольной) формы на ДСП обычной и повышенной мощности;
2) комбинированным, плоским, водоохлаждаемым на ДСП высокой и сверхвысокой мощности.
Огнеупорная кладка сферического свода, помимо отмеченных особенностей тепловой работы, испытывает постоянную сжимающую механическую нагрузку от распора, возникающего из-за формы кладки свода (так называемая стрела подъема купола). Механические напряжения в футеровке своде:
а) возрастают пропорционально диаметру свода или корпуса ДСП;
б) резко увеличиваются при ;
в) изменяется незначительно при .
Поскольку увеличение влияет на массу (расход материалов) и вес свода, а также на величину площади его теплоотдающей поверхности, целесообразно иметь
(111)
в зависимости от механической прочности огнеупорного кирпича.
Своды отечественных ДСП набирают преимущественно из термостойкого периклазохромитового кирпича марки ПХСУТ (ГОСТ 10888–93). Стойкость кирпичного свода зависит не только от условий эксплуатации, но и от способа и тщательности кладки. Свод набирают вне печи, на специальном шаблоне, имеющем форму внутренних очертаний свода с соответствующими «знаками» для необходимых отверстий.
Схема кладки может быть секторно-арочная, кольцевая или комбинированная.
Сферичность кладки радиусом
(112)
достигают сочетанием прямых и клиновых (клин торцевой, или ребровый, или радиальный) кирпичей. Наибольшая строительная прочность периклазохромитовых сводов обеспечивается с учетом условия (111) при
.
Кирпичный свод имеет один слой кладки, без тепловой изоляции. Толщина футеровки свода соответствует длине стандартного кирпича и зависит от вместимости ДСП т о (по данным Л.Е. Никольского и И.Ю. Зинурова):
m о, т …….... | до 12 | 25…50 | ||
Δсв, мм …… |
Периклазохромитовые кирпичи создают недостаточную электроизоляцию электродов разных фаз, что приводит к электрическим пробоям между уплотнителями электродных отверстий и механическим повреждениям центральной части свода.
Стойкость периклазохромитовых сводов в зависимости от вместимости ДСП и сортамента выплавляемой стали составляет, по данным Гипромеза, 200–250 плавок на малых ДСП и 50–100 плавок на крупных.
Высокоглиноземистые [муллитокорундовые марки МКС (ГОСТ 24704–96) или корундовые марки КС] огнеупоры обеспечивают более высокую (в 2,5–3 раза) стойкость свода, но имеют и более высокую (в 2–5 раз) стоимость.
На ДСП высокой и сверхвысокой мощности (третьего и четвертого поколений) применяют комбинированные водоохлаждаемые своды*(см. рис. 9).
Конструкция металлического водоохлаждаемого свода ДСП должна иметь минимальные электрические потери из-за перемагничивания магнитных масс и вихревых токов под влиянием мощных переменных магнитных полей, создаваемых переменными токами до 70…100 кА в графитированных электродах. Потенциальные возможности металлических водоохлаждаемых сводов по повышению стойкости футеровки и снижению затрат на ремонт не удается полностью реализовать из-за проблем эксплуатации таких сводов (наводки токов, дуговые разряды). Желание снизить мощность тепловых потерь, уменьшив площадь тепловоспринимающей поверхности плоского свода по сравнению со сводом сферической (купольной) формы, также осложнило их эксплуатацию, поскольку появилась возможность возникновения электрических дуг между плоским сводом и шихтой на начальном этапе периода расплавления.
Комбинированный свод (рис. 44) сверхмощных ДСП состоит из водоохлаждаемого каркаса – опорной рамы, съемных водоохлаждаемых элементов и центральной огнеупорной (т.е. неэлектропроводной во избежание электромагнитной индукции вихревых токов) секции. Опорная рама образует периферийную водоохлаждаемую часть комбинированного свода и состоит из двух или трех концентрически расположенных труб, соединенных радиальными трубами-пилонами**. Внутреннее кольцо располагают выше внешнего (наружного) кольца, и таким образом пилоны расположены наклонно под углом 5…20° к горизонтали, формируя каркас в виде усеченной многогранной пирамиды. Число пилонов так же, как и число панелей, зависит от размера печи и может составлять 9–12. Сводовое кольцо может состоять из двух колец, выполненных из стальных (целесообразно аустенитного класса) труб диаметром 159/135 или 219/195 и служащих напорным и сливным коллекторами для подвода и отвода охлаждающей воды. Соединение элементов опорной рамы выполняют с учетом необходимости электрической изоляции для разрыва возможных контуров токов, индуктируемых магнитными полями работающей ДСП. Отдельные панели соединяют обычно по оси пилонов каркаса. Соседние пилоны, участки внутреннего и внешнего колец и панели образуют зону коробчатого типа, в которой располагают рукава подвода и отвода воды, термопары, клапаны и элементы подвески свода. Эти коробчатые зоны сверху закрывают съемными плитами, которые служат рабочей площадкой во время обслуживания свода и проведения его ремонта.
Рис. 44. Конструкция комбинированного свода ДСП вместимостью 150 т:
1 – малое (внутреннее) сводовое кольцо; 2 – огнеупорный свод; 3 – сводовое кольцо – коллектор воды; 4 – панели; 5 – пилоны; стрелками показана схема подачи и отвода воды
Центральную огнеупорную секцию свода набирают в собственном опорном сводовом кольце. С учетом низкой стойкости огнеупорной футеровки центральной секции (120–150 плавок) ее размеры принимают минимально необходимыми. При круглой форме свободного кольца доля неохлаждаемой части свода составляет 0,20…0,25; при дельтавидной форме (см. рис. 44) сводового кольца ее удается уменьшить до 0,05…0,15. При этом с увеличением вместимости печи и диаметра ее свода доля огнеупорной секции снижается.
В случае применения неохлаждаемого опорного сводового кольца центральная секция может быть установлена поверх периферийной части комбинированного свода или во внутреннем кольце его каркаса при условии, что водоохлаждемые панели будут снизу прикрывать опорное кольцо от теплового излучения из рабочего пространства печи.
Водоохлаждаемый свод ДСП ПТ может быть плоским металлическим с необходимой электрической изоляцией электродного отверстия кирпичной кладкой и обмазкой рабочей поверхности панелей огнеупорным бетоном толщиной 50..70 мм (во избежание дуговых разрядов на начальном этапе периода расплавления). При плоской периферийной части длина электрода, находящегося в рабочем пространстве печи, уменьшается на 10…15 %, что снижает расход электродов на 5…10 % за счет уменьшения окисления боковой поверхности.
Масса водоохлаждаемого свода примерно на 30 % меньше по сравнению с огнеупорным (кирпичным) сводом, что снижает механическую нагрузку на его несущую конструкцию. Помимо ранее отмеченных преимуществ водоохлаждаемых элементов комбинированный свод позволяет работать на мощных длинных электрических дугах с высоким коэффициентом использования мощности электропечной установки ДСП и ДСП ПТ.
Расход воды (на 1 м2 тепловоспринимающей поверхности свода) составляет 3…6 м3/ч. Для снижения расхода воды можно применить оросительное («спреерное»*) охлаждение периферии комбинированного свода (конструкция немецкой фирмы BSE).
Механическое оборудование
Механическое оборудование ДСП (рис. 45) включает корпус, свод, опорную платформу, механизм наклона, электрододержатель, механизмы передвижения электродов, вспомогательные механизмы и устройства, систему удаления технологических газов.
Рис. 45. ДСП второго поколения:
1 – гидроцилиндр механизма наклона; 2 – опорный сегмент; 3 – рабочее окно;
4 – песчаный затвор; 5 – сводовое кольцо; 6 – уплотнитель электродного отверстия в своде; 7 – кронштейн; 8 – сливной желоб; 9 – статор электромагнитного перемешивания; 10 – фундаментная балка; 11 – опорная платформа; 12 – опорная тумба; 13 – корпус; 14 – газоотборный патрубок; 15 – графитированный электрод; 16 – электрододержатель; 17 – трубошины; 18 – гибкие кабели; 19 – Г-образная стойка; 20 – опорно-поворотный вал; 21 – 23 соответственно гидроцилиндры механизмов передвижения электрода, поворота свода и подъема свода
Корпус
Корпус, футерованный изнутри, формирует рабочее пространство ДСП. На корпус действуют различные механические нагрузки: статическая – от веса футеровки и металла, динамическая – при загрузке металлошихты через верх печи, термические напряжения вследствие неравномерного нагрева корпуса до 375…475 К, давление футеровки подины и стены вследствие ее теплового расширения во время плавки. Поэтому корпус ДСП должен быть достаточно жестким и прочным.
Корпус ДСП включает днище, кожух, песчаный затвор, рабочее окно, сливное окно («летка») и сливной желоб («носок»).
Днище может быть сферическим или коническим. Сферическое днище придает корпусу наибольшую жесткость. Однако отношение стрелы выпуклости днища к его диаметру ограничено (не более 0,1): чем больше кривизна, тем труднее изготовить сферическое днище. Поэтому откос ванны приходится располагать в цилиндрической обечайке верхней части составного днища, что увеличивает объем футеровки.
Коническое днище (см. рис. 45) и особенно днище с двойным конусом легче в изготовлении, чем сферическое, создает достаточную жесткость корпуса, требует наименьшего объема футеровки вокруг откоса ванны.
Толщина листа днища для ДСП вместимостью 12…150 т составляет 16…35 мм. Для выхода паров при сушке футеровки подины в днище просверливают отверстия диаметром 20…30 мм на расстоянии 400…500 мм одно от другого. На днище современных ДСП монтируют арматуру и газопроводы для продувочных устройств, в эркерной части днища ДСП четвертого поколения – арматуру донного выпускного отверстия с соответствующим приводом (см. рис. 40), для ДСП ПТ – арматуру подового электрода–анода и токопровод от положительного полюса источника питания с электроизоляцией и системой водяного охлаждения. На ДСП, оборудованных устройством электромагнитного перемешивания, днище изготовляют из немагнитной стали. Поскольку коэффициенты теплового расширения обычной и немагнитной стали различны, немагнитное днище крепят не сваркой, а болтами или заклепками.
На ДСП с разъемным корпусом к днищу крепят сливной желоб («носок») с помощью основания («постели») под углом к горизонтали 8…12° вверх. Желоб имеет корытообразное поперечное сечение в форме трапеции или шестигранника. Длина желоба должна быть минимально возможной и составляет 1,5…3 м в зависимости от расположения ДСП и ковша (на кране или ковшевозе). Конец желоба длиной 500...800 мм, разрушаемый жидким металлом, делают съемным («насадка»). В некоторых случаях насадку выполняют с закруглением для изменения траектории струи при наклоне печи и уменьшения износа футеровки ковша. Толщина листа сварного сливного желоба примерно равна половине толщины листа обечайки кожуха. Сливной желоб футеруют шамотным кирпичом или огнеупорной массой. ДСП четвертого поколения сливного желоба не имеют.
Кожух может иметь цилиндрическую, коническую или комбинированную коническо-цилиндрическую обечайку (на ДСП второго поколения) в зависимости от формы «свободного» пространства и профиля футеровки стены ДСП. Для увеличения жесткости кожух иногда снабжают вертикальными и горизонтальными ребрами. Для облегчения условий труда при холодных ремонтах футеровки стены корпус ДСП делают разъемным в горизонтальной плоскости на уровне откоса ванны. В этом случае нижний фланец кожуха соединяют с верхним фланцем днища штырями, в которых имеются пазы для забивки клиньев с целью ускорения монтажа и демонтажа кожуха.
Кожух сваривают из котельной листовой стали толщиной 14…40 мм в зависимости от диаметра кожуха. В среднем толщину кожуха можно принять равной 1/200 его диаметра. В обечайке кожуха делают вырезы для рабочего и сливного окна. Для увеличения жесткости вырезы с внутренней стороны усиливают накладными листами такой же толщины. Для возможности частичного ремонта обечайку кожуха можно выполнять из отдельных щитов, соединенных между собой болтами.
Для контроля температуры огнеупорной футеровки стены ДСП второго поколения на кожухе монтируют водоохлаждаемый термозонд с пневмоприводом конструкции Челябинского НИИМ или датчик непрерывного измерения температуры на основе фотоэлектрического пирометра конструкции МВМИ.
В условиях интенсификации работы современных ДСП высокой и сверхвысокой мощности на кожухе монтируют 3–6 коротко- и длиннофакельных стационарных, выдвижных или поворотных ТКГ тепловой мощностью 3…10 МВт и суммарной мощностью до 50 МВт, обеспечивая циркуляцию продуктов горения в объеме металлошихты и конвективную теплопередачу в «свободном» пространстве; струйные (вихревые) инжекторы кислорода для дожигания монооксида углерода; двух- и трехпроводные фурмы (горелки) типа «труба в трубе» для создания коаксиальных струй (факелов) типа «Cojet»*; манипуляторы с несколькими фурмами (например, две кислородных и одна для инжекции угольного порошка при формировании вспененного шлака) с дистанционным управлением. Такое расположение целесообразно, ибо размещение в проеме рабочего окна усиливает в 2–3 раза подсос воздуха, увеличивает объем технологических газов и осложняет работу системы газоотсоса.
Для ДСП четвертого поколения корпус имеет выступ (эркер) для создания эркерной камеры ванны (§ 7), при этом корпус может быть цилиндрическим, овальным (при обслуживании донного выпускного отверстия через свод) или цилиндрическим со спрямлением со стороны эркерного сливного узла. Спрямление позволяет уменьшить эксцентриситет выпускного отверстия на 10…15 % (по опыту конструирования таких ДСП австрийской фирмы VAI-Fuchs). По данным В.В. Афанасьева (ОАО «СКБ Сибэлектротерм»), радиус скругления эркерной камеры составляет (0,10…0,26)
|
|
Своеобразие русской архитектуры: Основной материал – дерево – быстрота постройки, но недолговечность и необходимость деления...
Археология об основании Рима: Новые раскопки проясняют и такой острый дискуссионный вопрос, как дата самого возникновения Рима...
Архитектура электронного правительства: Единая архитектура – это методологический подход при создании системы управления государства, который строится...
Историки об Елизавете Петровне: Елизавета попала между двумя встречными культурными течениями, воспитывалась среди новых европейских веяний и преданий...
© cyberpedia.su 2017-2024 - Не является автором материалов. Исключительное право сохранено за автором текста.
Если вы не хотите, чтобы данный материал был у нас на сайте, перейдите по ссылке: Нарушение авторских прав. Мы поможем в написании вашей работы!