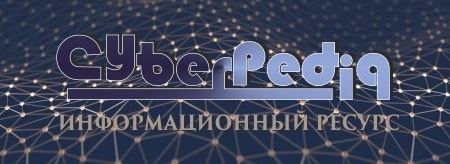
Особенности сооружения опор в сложных условиях: Сооружение ВЛ в районах с суровыми климатическими и тяжелыми геологическими условиями...
История развития пистолетов-пулеметов: Предпосылкой для возникновения пистолетов-пулеметов послужила давняя тенденция тяготения винтовок...
Топ:
Выпускная квалификационная работа: Основная часть ВКР, как правило, состоит из двух-трех глав, каждая из которых, в свою очередь...
Характеристика АТП и сварочно-жестяницкого участка: Транспорт в настоящее время является одной из важнейших отраслей народного...
Проблема типологии научных революций: Глобальные научные революции и типы научной рациональности...
Интересное:
Мероприятия для защиты от морозного пучения грунтов: Инженерная защита от морозного (криогенного) пучения грунтов необходима для легких малоэтажных зданий и других сооружений...
Берегоукрепление оползневых склонов: На прибрежных склонах основной причиной развития оползневых процессов является подмыв водами рек естественных склонов...
Средства для ингаляционного наркоза: Наркоз наступает в результате вдыхания (ингаляции) средств, которое осуществляют или с помощью маски...
Дисциплины:
![]() |
![]() |
5.00
из
|
Заказать работу |
Содержание книги
Поиск на нашем сайте
|
|
Дизель в конструктивном отношении довольно простой, но имеет большие массу и габариты, которые не позволяют транспортировать его в сборе и требуют принципиально нового подхода к вопросам монтажа.
Выбранный мною двигатель является малооборотным, т.к. имеет скорость оборотов равную 170 об/мин, поэтому, учитывая его габариты, блочный метод погрузки двигателя на судно является единственным возможным.
Кроме центровки и крепления на фундаменте необходимо выполнить трудоемкую и точную сборку дизеля с обеспечением повторяемости стендовых допусков в условиях строящегося судна. Поэтому вполне оправдано стремление к разработке агрегатных методов монтажа дизелей на стапеле. Препятствием этому служат влияние деформаций корпуса судна, недостаточная жесткость дизеля, ограниченная транспортабельность монтажных блоков и отсутствие кранов достаточной грузоподъемности. Для некоторых типов судов разработана технология окончательного монтажа дизелей на стапеле, исключающая их перецентровку после спуска судна на воду за счет введения упреждений, обратных по знаку ожидаемому изгибу корпуса.
Трудоемкость монтажа зависит от технологичности отдельных деталей и разбивка дизеля на транспортабельные блоки и узлы.
Детали остова - сварные и имеют недостаточную жесткость. Поэтому в процессе монтажа на судне должно быть уделено особое внимание вопросу контроля и исключения деформаций базовых поверхностей крупногабаритных деталей остова, особенно общей фундаментальной рамы, которую изготовляют из отдельных секций. Важно отметить, что в узлах крепления дизеля типа ДКРН применяют только простые фундаментные болты, бортовые и кормовые упоры. Улучшение технологичности узлов крепления возможно за счет применения самоустанавливающихся сферических подкладок вместо пригоняемых стальных или чугунных клиньев.
Внедрение поставки дизелей крупными блоками, а также применение методов контроля, исключающих влияние деформаций корпуса судна, приводят к значительному сокращению цикла и трудоемкости монтажа.
После тщательной проработки вариантов укрупнения деталей была предложена следующая разбивка дизеля на транспортабельные блоки и узлы:
Блок №1 – фундаментная рама в сборе с поддоном и уложенным коленчатым валом, собранными рамовыми и главным упорным подшипниками (вес 58,7 т, габариты 11100×3000×2000 мм).
Блок №2 – ресивер продувочного воздуха в сборе с газовыпускными коллектором и блоками цилиндров с установленными втулками (вес 30 т, габариты 9000×2000×2000).
|
Узел №1 – картерные стойки (вес 27 т, габариты каждой стойки 2800×2300×200 мм).
Узел №2 – отсек приводов без роликовых цепей (вес 11 т, габариты 2750×2600×900 мм).
Узел №3 – турбовоздуходувки (вес 12 т, габариты 2350×1250×800 мм).
Остальные детали – поршни со штоками, крейцкопфы с шатунами, топливные насосы, трубопроводы и другие поставляют самостоятельными узлами в индивидуальной упаковке.
В результате число погрузочных мест при транспортировке сократилось почти в два раза по сравнению с раздельной поставкой дизеля.
Внедрение на заводе-изготовителе консервации деталей жидкими ингибиторными смазками исключает трудоемкую расконсервацию их перед монтажом.
В результате рациональной разбивки на блоки и совершенствования технологии цикл монтажа дизелей на серийных судах уменьшился в два с половиной раза, а трудоемкость снизилась на 40% по сравнению с головным судном.
Опыт монтажа показал, что по мере сборки остова дизеля фундаментная рама прогибается до 0,30 мм. Поэтому на стапеле раму устанавливают выпуклостью вверх. Собранный дизель крепят, устанавливая только по два клина в районе каждой картерной стойки, за исключением базовых клиньев. Пригонку остальных клиньев производят на плаву после контрольной проверки положения дизеля.
Наиболее простым и удобным является метод контроля плоскостности, при котором одновременно определяется величина извернутости концов рамы и контролируется прямолинейность каждой ее полки (рис. 1).
1- фундаментная рама, 2- отжимные болты, 3-приспособления для укладки струн, 4 и 5- проверочные линейки, 6 и 7 стальные струны, 8- мерные столбики, 9 – положение линейки в районе 9 цилиндра.
Опыт показывает, что оснастка и метод измерения реперных ординат должны быть одинаковыми на стенде завода-изготовителя и на судне, что уменьшает погрешность снятия реперных линий, максимальная величина которой может составлять 0,05 мм.
|
Для погрузки ГД применяют траверсу (рис.2) и монтажный грузовой кран. Траверса представляет собой сварную балку из двух швеллеров. Между швеллерами на концах балки установлено по блоку для тросов. К осям блоков подвешены тяги, которые заканчиваются грузовой скобой.
Рис.2 Траверса
Рис. 3 Судовой грузовой кран
Использование траверсы связано с невозможностью применить гибкие стропы (в основном металлические троса) из-за неравномерно распределяющихся усилий при подъеме и перемещении длинномерных или тяжеловесных деталей (заготовок) имеющих особенную геометрию. В этом случае траверса обеспечивает надежность производимых погрузочно-разгрузочных работ без опасности для жизни.
Расчет траверс.
Одно из важных назначений траверсы при монтаже тонкостенных аппаратов – воспринимать возникающие сжимающие усилия и изгибающие моменты, чтобы не допустить деформацию поднимаемого аппарата.
Обычно траверса представляет собой балку, изготовленную из одиночных двутавров, швеллеров или стальных труб различных размеров. Иногда траверсу изготавливают из парных двутавров или швеллеров, соединенных стальными пластинами, или стальных труб, усиленных элементами жидкости.
При подъеме оборудования несколькими кранами разной грузоподъемности применяют уравновешивающие или балансирные траверсы, имеющие разные плечи.
Траверса работает на изгиб и на сжатие. Масса траверсы составляет незначительную долю от массы поднимаемого груза (как правило, не более
1 %), поэтому в практических расчетах изгибающим моментом в траверсе и прогибом от ее собственной массы можно пренебречь.
1. Определяем нагрузку, действующую на траверсу:
Р= 10 G о К п К д = 10·58.7·1,1·1,1=710.27 кН.
где - масса механизма;
- коэффициент перегрузки (
);
- коэффициент динамичности (
);
2. Изгибающий момент в траверсе находим по формуле
М= кН·см
где – плечо траверсы;
3. Требуемый момент сопротивления поперечного сечения траверсы рассчитываем следующим образом:
W тр = 3979.10 см3.
где m – коэффициент условий работы (для грузозахватного приспособления )
R – Сопротивления металла (для стали класса С 38/23 )
Если принять конструкцию балки траверсы состоящей из двух двутавров, соединенных стальными пластинами сваркой, то этому условию удовлетворяют два двутавра № 40 с моментом сопротивления Wх= 2560 см3
Таким образом момент сопротивления сечения траверсы в целом составит:
Wх= 2 Wхд= 2·2560=5120см3; причем Wх>W тр.
Анализ способа монтажа
В процессе установки блока №1 необходимо одновременно обеспечить: соосность коленчатого вала и валопровода; плоскостность базовой поверхности рамы; оптимальное положение коленчатого вала в рамовых подшипниках.
Центровку блока по плазовым точкам А и Б теоретической оси валопровода выполняют оптическим методом.
|
Рис. 4 Центровка блока фундаментная рама- коленчатый вал дизеля типа ДКРН
Оптический прибор 7 устанавливают с носового конца полого коленчатого вала 3, вращение которого осуществляется валоповоротным устройством 1. Положение блока по длине судна определяют путем совмещения рисок 5, нанесенных на раме по оси кормового цилиндра, с рисками 4 на фундаменте. Допуски на центровку те же, что при агрегатном монтаже двигателя. Раму 2 перемещают отжимными болтами 6.
Центровку дизеля по оси валопровода и контроль его положения в процессе сборки удобно выполнять с применением измерительных устройств типа «оптическая струна»: визирной трубы ДП-477 или ДП-725 и марок с точечным источником света.
Плазовые точки А и Б материализуют базовым маркам 2 и 7 (рис.4) и дополнительно по теоретической оси валопровода на шергенях устанавливают выносные марки 3 и 6. На торцах коленчатого вала дизеля крепят марки 4 и 5. Визирные трубы 1 и 8 центруют по маркам 2 и 3 с кормы и по маркам 6,7 – с носа дизеля. Контроль соосности блока или собранного дизеля относительно оси валопровода сводится к наблюдению в объективе прибора за положением светящейся точки каждой марки коленчатого вала. При необходимости производится корректировка положения дизеля с помощью отжимных устройств 9. Контрольные проверки производят после установки картерных стоек, блоков цилиндров и затяжки анкерных связей.
3.Технические требования.
3.1 Технические требования к погрузке дизелей.
До погрузки ДВС в корпус судна должна быть сделана проверка с целью выявления дефектов, что препятствуют правильной установке ДВЗ. Опорная поверхность фундамента должна быть очищена от смазки, для консервации, и следов ржавчины. Выявленные дефекты стоит устранить.
Узлы и детали, что препятствуют установке погружающего приспособления ДВС, должны быть сняты соответственно требованиям инструкции по эксплуатации ДВС. Снятые детали должны быть замаркерованы, законсервированные и сданы на сохранение.
Конструкции приспособления для погрузки ДВС, а также инструкция их установки должны быть согласованный с предприятием-поставщиком.
Стропование ДВС для погрузки необходимо делать по схеме, разработанной предприятием-поставщиком.
Перед погрузкой ДВС на судно, что находится на стапеле, необходимо нагрузить корпус нагрузками, что опережают деформацию.
Перед погрузкой ДВС их нижние опорные поверхности и поверхности фланцев должны быть очищены и осмотрены; выявленные заусенецы и выбоины стоит устранить.
ДВС необходимо устанавливать на судовые фундаменты на временных деревянных прокладках, толщина которых должна равняться чертежным размерам компенсирующих клиньев. Прокладки должны быть расставлены так, чтобы не препятствовать следующей установке отжимных болтов или других приспособлений для перемещения главного двигателя.
|
В продольном направлении двигатель должен устанавливаться посредствам мерного рельса, на котором зафиксировано расстояние соответственно чертежу от кормового торца кронштейна, яблока ахтерштевня или принятой базовой линии к кормовому торцу вала ДВС. Допускаются и другие материальные инструменты при условии обеспечения необходимой точности контроля.
После погрузки главного двигателя, погружающие приспособления стоит снять, а главные двигатели накрыть чехлами.
3.2 Технические требования, предъявляемые к фундаментам.
Фундаменты должны быть изготовлены в соответствии с ОСТ 5.0015-70 и действующей технической документацией.
Правильность установки фундаментов должна проверяться по ВОН 9-915-69 относительно теоретической оси валопровода, что задается контрольными точками, нанесенными по координатам с плаза на специальных шергенях в районе носовой и кормовой переборок машинного отделения в блоке судна.
При отсутствии дополнительных требований, отмеченных в чертеже, координаты установки фундамента должны быть выдержаны в следующих допусках:
а) не параллельность оси фундамента относительно теоретической оси валопровода в горизонтальной плоскости допускается не более 1 мм на 1 м длины фундамента. Сдвиг оси фундамента относительно теоретической оси линии вала не должно превышать ±8 мм;
б) не параллельность опорных поверхностей фундамента относительно теоретической оси линии вала в вертикальной плоскости допускается не более 1 мм на 1 м длины фундамента. При этом отклонение расстояния от опорных поверхностей фундамента к теоретической оси линии вала по высоте не должно превышать +10, -3 мм;
в) допустимое отклонение расстояния фундамента от поперечной переборки составляет ±10 мм;
Установка фундаментов должна быть принята техническим контролем и одобрена организацией, что осуществляет наблюдение.
До обработки опорных поверхностей фундамента на судне в районе расположения фундамента должны быть закончены все работы, что могут вызывать деформацию фундамента (сварка, клепка, экзамены на непроницаемость и др.).
Обработка опорных поверхностей фундамента должна быть выполнена соответственно действующей технической документации. Допускается выполнять обработку не всей опорной поверхности фундамента, а только тех участков, где будут устанавливаться компенсирующие звенья. При этом обработанный участок должен быть на 15 мм больше размера устанавливаемого компенсирующего звена из каждой ее стороны.
Проверка правильности обработки опорных поверхностей фундамента должна выполняться посредством щупа и линейки длиной не менее длины компенсирующего звена. При этом пластина щупа толщиной 0.05 мм не должна проходить между поверхностью, что проверяется, и линейкой.
|
При установке ДВС на пластмассе обработку опорных поверхностей фундамента делать не следует.
Края обработанных поверхностей должны быть притуплены, опорные поверхности фундамента смазаны маслом, для консервации, и защищены от механических повреждений, необработанные поверхности окрашены.
Требования к спариванию валов
Фланцы спариваемых валов должны быть развернуты относительно друг друга так, чтобы места с максимальным торцевым боем располагались через 180°.
При спаривании фланцы должны быть прицентровані один к одному в вертикальной и горизонтальной плоскостях с точностью 0,1 мм на сдвиг и 0,15 мм/м на излом. Сдвиг повинный измеряться посредством стрел при общем повороте валов, что спариваются. Излом стоит измерять щупом по разнице зазоров непосредственно между фланцами.
Отцентрованные фланцы с рознесеним торцевым боем необходимо стянуть временными болтами, после чего стоит выполнить обработку отверстий одновременно в обоих фланцах под соединительные болты.
Требования к центровке ДВС
При использовании оптического метода центрования механизмов, установку и центрования оптического прибора на фланце ДВЗ необходимо осуществлять соответственно к ОСТ 5.4078-73 или ОСТ 5.4038-71.
Главные двигатели ориентируют на судне по оси валопровода, материализованной двумя точками, координаты которых берут с плаза. Плазовые точки необходимо нанести на корпусные конструкции с точностью не менее ±1мм от размеров отмеченных в чертеже. Применяемое оптическое оснащение должно обеспечивать высокую точность измерений.
Теоретическая ось валопровода должна фиксироваться перекресткам двух линий, нанесенных на мишени. Толщина линий скрещивание мишеней t зависит от расстояния наблюдения и должна определяться по формуле:
t = 0,025×L, мм
где L - расстояние наблюдения, м.
По завершении центровки ДВс, его крепление на фундаменте и в процессе сдачи монтажа ДВС техническому контролю, производится измерение раскепов каждого кривошипа. При этом все рамовые шейки коленного вала должны прилегать к вкладышам ромовых подшипников. Раскепы необходимо измерять в 2-х плоскостях:
а) в вертикальной - при положении кривошипа в верхней (ВМТ) и нижней (НМТ) «мертвых точках»;
б) в горизонтальной - при положении кривошипа со стороны левого и правого бортов.
Прибор для измерения раскепа стоит устанавливать в местах, отмеченных предприятием-поставщиком ДВС. Разница измерений в одном кривошипе (раскеп) не должна превышать величины, установленной предприятием-поставщиком ДВС. Максимальная величина раскепов 0,12 мм
Проверка плоскости рамы производится при наличии данных ее проверки в формуляре ДВС. Способ проверки и допускаемые отклонения от прямолинейности устанавливает предприятие-поставщик ДВС.
После центровки необходимо проверить положение поршня во втулке цилиндра. Это выполняется посредством приспособления для дистанционного определения радиальных зазоров между поршнем и втулкой цилиндра. Масляный зазор между крейцкопфом и направляющими не должен превышать зазору между поршнем и цилиндром. При необходимости зазоры возобновляются путем перемещения направляющих крейцкопфа.
Требования к фиксации механизмов
Механизм необходимо устанавливать так, чтобы до узлов крепления был свободный доступ с механическим инструментом. На опорной поверхности двигателя не должно быть глухих отверстий с резьбой для его крепления вкручиванием болтов снизу наверх. В полках рамы или лапах обязательно предусматривают отверстия с резьбой для отжимных болтов вертикального перемещения при центрировании механизма. В судовом фундаменте не следует делать отверстия с резьбой для крепежных и отжимных болтов.
Конструкции подкладок должны исключать их пригон за местом и обработку фундамента.
Требования к креплению механизмов
Сверление отверстий в фундаменте под крепежные болты стоит делать по завершению центровки главного двигателя.
Установку шпилек стоит выполнять в присутствии технического контроля. После проверки стержень шпильки и стенки отверстия должны быть смазанны техническим жиром (ГОСТ 1045-73) или другой смазкой, что применяется при защите его от коррозии.
Гайки крепежных шпилек после закрепления должны впритирку прилегать к фундаменту и лапам главного двигателя. Для обеспечения этого требования допускается подрезание лап главного двигателя и полок фундамента. Глубина подрезания под головки болтов и под гайки не должна превышать 10% толщины лапы главного двигателя или полки фундамента. Шероховатость плоскости не должна быть более Rz = 80 мкм за ГОСТ 2789-73. Острые кромки отверстий должны быть притуплены.
Затяг крепежных шпилек выполняют с помощью гидравлическим домкратом. Затяг крепежных шпилек стоит делать по правилу «крест-накрест».
Величина момента затягивания крепежных болтов должна быть отмечена в установочном чертеже соответственно требованиям предприятия-поставщика двигателя.
После затягивания пластина щупа толщиной 0,05 мм не должна проходить под гайку шпильки. В глубь узла соединения щуп не должен проходить более чем на 10% длины подкладки (в отдельных местах).
Все гайки крепежных шпилек должны быть обеспечены от самоотвинчивания постановкой контрогаек или другими стопорными средствами. Для стопора гаек чаще всего используют корончатую гайку.
Крепежные шпильки и гайки должны быть защищены покрытиями.
По окончанию установки главного двигателя на компенсирующих клиньях, работы должны быть предъявлены техническому контролю.
|
|
Механическое удерживание земляных масс: Механическое удерживание земляных масс на склоне обеспечивают контрфорсными сооружениями различных конструкций...
Таксономические единицы (категории) растений: Каждая система классификации состоит из определённых соподчиненных друг другу...
История развития пистолетов-пулеметов: Предпосылкой для возникновения пистолетов-пулеметов послужила давняя тенденция тяготения винтовок...
Поперечные профили набережных и береговой полосы: На городских территориях берегоукрепление проектируют с учетом технических и экономических требований, но особое значение придают эстетическим...
© cyberpedia.su 2017-2024 - Не является автором материалов. Исключительное право сохранено за автором текста.
Если вы не хотите, чтобы данный материал был у нас на сайте, перейдите по ссылке: Нарушение авторских прав. Мы поможем в написании вашей работы!