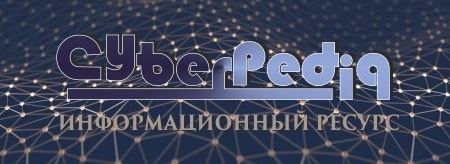
Архитектура электронного правительства: Единая архитектура – это методологический подход при создании системы управления государства, который строится...
Археология об основании Рима: Новые раскопки проясняют и такой острый дискуссионный вопрос, как дата самого возникновения Рима...
Топ:
Выпускная квалификационная работа: Основная часть ВКР, как правило, состоит из двух-трех глав, каждая из которых, в свою очередь...
Марксистская теория происхождения государства: По мнению Маркса и Энгельса, в основе развития общества, происходящих в нем изменений лежит...
Теоретическая значимость работы: Описание теоретической значимости (ценности) результатов исследования должно присутствовать во введении...
Интересное:
Уполаживание и террасирование склонов: Если глубина оврага более 5 м необходимо устройство берм. Варианты использования оврагов для градостроительных целей...
Финансовый рынок и его значение в управлении денежными потоками на современном этапе: любому предприятию для расширения производства и увеличения прибыли нужны...
Берегоукрепление оползневых склонов: На прибрежных склонах основной причиной развития оползневых процессов является подмыв водами рек естественных склонов...
Дисциплины:
![]() |
![]() |
5.00
из
|
Заказать работу |
|
|
Сплавы алюминия разделяются на литейные, применяемые в виде отливок, и деформируемые, катаные, прессованные и т.д.
Литейные славы отличаются повышенным содержанием легированных примесей и имеют в структуре эвтектику, которая обеспечивает у них низкую температуру плавления и жидкотекучесть.
Деформируемые сплавы имеют более низкое содержание легированных примесей. Находясь в твердом растворе, легирующие элементы позволяют получать достаточно пластичные, особенно в нагретом состоянии сплавы и производить их термическую обработку.
Литейные сплавы алюминия широко применяются для фасонного литья. Они должны обладать хорошей жидкотекучестью, малой усадкой, высокой прочностью, создаваемой модифицированием и термической обработкой; хорошей обрабатываемостью режущим инструментом.
Основными элементами литейных сплавов являются Si, Cu, Mg и Zn, присутствие значительного числа которых в различных комбинациях обеспечивает упрочнение при старении.
Mn, Ni и Cr добавляются в эти сплавы в небольших количествах, оказывают меньшее влияние на их прочность, но повышают коррозионную стойкость и жаропрочность.
Присадки Ti, Cr и Be придают алюминиевым сплавам мелкозернистость, вязкость, прочность.
Литейные сплавы обозначают АЛ с цифрой, указывающей их условный номер. Но есть жаропрочный литейный алюминиевый сплав, например, В300: где буква В указывает, что отливки изготавливаются из вторичного алюминия. Данный сплав содержит 0,8-1,5% Mg, 0,18-0,30 Mn; 4,6-6,0 Cu; 2,6-3,6 Ni; 0,1-0,5 Cr.
Литейные сплавы Al с Si эвтектического и доэвтектического типа с невысокой температурой плавления обладают хорошей жидкотекучестью, хорошо заполняют форму и дают малую усадку.
|
Для улучшения свойств силуминов, их модифицируют смесью 62,5% NaCl+25%NaF+12,5%KCl. Этот модификатор добавляют в жидкий сплав при температуре 730-7400С за 10-12 мин. До разливки металла.
Недостатками силуминов типа АЛ2 [Si 10-13%] является образование в отливках оксидов; большая газонасыщенность и пористость отливок, снижение ударной вязкости при загрязнении железом, вызывающим образование в микроструктуре хрупких, игольчатых (пластинчатых) составляющих. Кроме того, отливки насыщены газом и пористы. Кристаллизация под давлением снижает газонасыщенность и пористость.
Механические свойства и обрабатываемость силуминов повышает добавка Си.
Присадка Mg, Cu и Zn значительно упрочняет силумины путем термической обработки, заключающейся в закалке при 520-5300С и искусственное старение в течение 10-20 часов при 150-1800С.
При этом такие соединения как Mg2Si; CuAl2; MgZn2; CuMgAl2 и другие растворяются в алюминии и могут быть сохранены в твердом растворе путем закалки.
Двойные сплавы алюминия с медью, например, АЛ7 (4,0-5,0 Си) уступают по качеству силуминам.
Более высокие механические свойства и коррозионную стойкость имеет Al-Mg сплав АЛ8 (9,5-11,5 Mg), предел прочности которого после закалки достигает σв=30кГ/мм2) при удлиненном d=12%, но литейные свойства у него хуже, чем у силуминов.
Алюминиевые сплавы широко применяются для изготовления автомобильных поршней. По сравнению с серым чугуном преимуществом этих сплавов является высокая теплопроводимость, низкий удельный вес и хорошая обрабатываемость. Однако, чугун более износостоек.
Деформируемые сплавы алюминия должны обладать высокой прочностью и способностью подвергаться пластической деформации. Структура деформируемых сплавов Аl состоит из твердого раствора на алюминиевой основе и избыточных фаз.
Наиболее распространенными являются сплавы типа дуралюмина, имеющие после термообработки высокую прочность. Маркируются они буквами Д или В, а кованые сплавы буквой К, цифра обозначает номер сплава.
|
После термической обработки прокатанный и отожженный дуралюмин, например, Д1 [3,8-4,8 Cu, Mg 0,4-0,8, Mn 0,4-0,8, прочие примеси 0,1] имеет сравнительно невысокие механические свойства. Структура его содержит a - твердый раствор на основе алюминия, светлые выделения CuAl2 и фазы S, т.е.(CuMgAl2) и темные включения нерастворимых соединений Fe.
Путем закалки и старения можно повысить механические свойства дуралюмина.
Закалка дуралюмина производится обычно путем нагрева его в соляных ванных или электрических печах до температуры около 495-5100С для перевода CuAl2 и фазы S, т.е. CuMgAl2 в твердый раствор с последующим быстрым охлаждением в воде.
Для различных марок дуралюмина закалочные температуры различны, причем интервал очень узок, например, Д1 505-510 оС, что осложняет практику их термообработки.
В результате быстрого охлаждения у дуралюмина легко фиксируется структура пересыщенного (неустойчивого) твердого раствора и темных нерастворившихся соединений Fе. Твердость и прочность дуралюмина при этом не меняются.
Старение дуралюмина при 20 оС, т.е. естественное старение, обеспечивает в течение 4х-5-ти суток наиболее высокие его механические свойства – предел прочности σв до 43 кГ/мм2 (422Мн/мм2).
При искусственном старении может наблюдаться разупрочнение из-за процесса коагуляции выделяющихся фаз. Предел прочности на растяжение и твердость состаренного дуралюмина можно еще повысить [σв до 55 кГ/мм2, НВ до 160] путем холодной обработки давлением, но относительное удлинение при этом сильно уменьшается.
Основной причиной повышения прочности и твердости дуралюмина при старении является перегруппировка в твердом растворе атомов Cu, что создает напряжения и дробит блоки твердого раствора. Из деформированных сплавов алюминия наиболее прочны сплавы системы Al-Cu-Mg-Zn, например, сплав В95 [1,7 Си; 2,3 Mg; 0,4 Mn; 0,2 Cr; Zn 6, прочие примеси 0,1] после закалки при 450 оС и длительного искусственного старения при 120-150 оС в течение 10-20 часов имеет σв ≈ 60 кг/мм2 (588 Мн/м2). Однако, он обладает повышенной, по сравнению с Д1 и Д16 склонностью к коррозии. Кроме того, механические свойства В95 быстро понижаются при повышении температуры.
Крупным недостатком сплавов типа дуралюмина является их низкая коррозионная стойкость, особенно в морской воде. Чтобы предохранить эти сплавы от коррозии, изделия подвергают плакированию. Покрывают заготовку из дуралюмина с обеих сторон тонкими листами самого чистого алюминия, нагревают ее и прокатывают до требуемой толщины. В результате на поверхности образуется равномерный слой чистого алюминия (толщиной 4% от общей толщины), очень стойкого против коррозии.
|
Для штампованных деталей повышенной жаропрочности применяются сплавы АК2 и АК4 [3,5-4,5 Cu; 0,4-0,8 Mg; 1,8-2,3 Ni; Si 0,5-1,0; Fe 0,5-1,0 и 0,1 прочие примеси] и [1,9-2,5 Cu; Mg 1,4-1,8; 1,0-1,5 Ni; 0,5-1,2 Si; 1,1-1,6 Fe; 0,1 прочие] соответственно, в которые добавляется 0,1-0,12% Ti для создания мелкозернистости благодаря образования мельчайших частиц Al3Ti и для облегчения обрабатываемости режущим инструментом.
Широко применяются сплавы авиаль (АВ). По прочности они уступают дуралюминам, но обладают лучшей пластичностью в холодом и горячем состояниях, [0,1-0,5 Cu; 0,45-0,9 Mg; 0,15-0,35 Mn; 0,5-1,2 Si] обладают высокой общей сопротивляемости коррозии, но склоны к межкристаллической коррозии.
Не все деформированные алюминиевые сплавы упрочняются термообработкой. Не упрочняются сплавы Al с Mn или Mg, например, АМц – это твердый раствор Mn в Al, в котором в небольшом количестве имеются частицы соединения Al6Mn [1,0-1,6 Mn] или АМг2 [0,2-0,6 Мн; 1,8-2,8 Mg]. Сплавы АМг и АМц применяют в отожженном состоянии, т.к. эффект закалки и старения невелик. Прочность повышают нагартовкой, но пластичность при этом несколько снижается.
Сплавы применяются для сварных и клепаных элементов конструкций, испытывающих небольшие нагрузки и требующих высокого сопротивления коррозии.
Подшипниковые сплавы алюминия должны обладать высокими антифрикционными свойствами. Основными элементами таких сплавов являются Sn; Cu; Ni; Si, образующие с алюминием гетерогенные структуры.
В настоящее время широко используют спеченные алюминиевые сплавы на основе Al-Al2O3 (САП – спеченные алюминиевый порошок).
Подобные сплавы получают путем холодного брикетирования алюминиевого порошка (пудры), вакуумной дегазации брикетов (отжига) и последующего спекания нагретых брикетов под давлением.
По сравнению с другими алюминиевыми сплавами САП обладают высокой жаропрочностью при длительном нагреве до 500 оС. Кроме того, изготавливают САС (спеченные алюминиевые сплавы) с высоким содержанием легирующих элементов. САС обладают особыми физическими свойствами [например, САС1 25-30% Si, 5-7% Ni и Al применяют для деталей, работающих в паре со сталью при температуре 20-2000С, которые требуют сочетания низкого коэффициента линейного расширения и малой теплопроводности].
|
Магний и его сплавы.
Из применяемых в машиностроении металлов и сплавов магний является наиболее легким (d»1,7). Температура кипения 10970С. При температуре, близкой к Тпл (6500С), Mg легко воспламеняется и горит ослепительным пламенем, выделяя много тепла.
Механические свойства Mg, особенно предел текучести, очень низки и потому он применяется только в сплавах.
Mg и его сплавы отличаются относительно плохой деформированностью. Основными легирующими элементами в сплавах Mg являются Al, Zn и Mn. Алюминий добавляется в сплавы магния в количестве 11% и увеличивает их механические свойства. Цинк добавляется в количестве до 2%, повышая механические свойства меньше, чем алюминий, увеличивает пластичность и улучшает их литейные качества.
Mn увеличивает сопротивление коррозии, для чего добавляют 0,1-0,5% Mn.
Вредными примесями в сплавах магния являются Ni, Fe, Cu и Si.
Магниевые, как и алюминиевые сплавы подразделяют на 2 группы:
1. Литейные сплавы – для получения деталей методом фасонного литья, маркируются буквами Мл.
2. Деформируемые сплавы, подвергаемые прессованию, прокатке, ковке, штамповке и другим видам обработки давлением, маркируются буквами МА.
Термическая обработка магниевых сплавов имеет много общего с термической обработкой алюминиевых сплавов. Обычно их отжигают в течение 15-20 часов при температуре 400-4200С. Для устранения наклепа магниевые сплавы подвергают рекристаллизационному отжигу при температуре ~ 350 oС.
Некоторые магниевые сплавы могут быть упрочнены закалкой и старением. В зависимости от состава закалку осуществляют при нагреве до 380-540 oС, а последующее старение – при 150-200 oС. Прочность магниевых сплавов в процессе старения можно повысить на 20-35%.
Из литейных сплавов наибольшее применение получили сплавы Мл5 [7,5-9,0 Al; 0,2-0,8 Zn; 0,15-0,5 Mn] и Мл6 [9-10,2 Al; 0,6-1,2 Zn; 0,1-0,15 Mn]. Достоинства литейных сплавов: меньший удельный вес по сравнению со сплавами Al, хорошая обрабатываемость режущим инструментом.
Недостатки: низкая устойчивость против коррозии, худшие, по сравнению с алюминиевыми сплавами литейные свойства, необходимость мер предосторожности для предотвращения загорания сплава.
Деформированные сплавы магния близки к литейным и принадлежат к системам Mg-Mn; Mg-Al-Zn. Применяют их в основном для изготовления деталей горячей штамповкой в интервале температур 280-4500С для улучшения их пластичности, т.к. гексагональная решетка магния затрудняет их пластическую деформацию при комнатной температуре.
|
Наиболее прочны деформируемые сплавы – МАЗ и МА5, содержащие в среднем (соответственно) 6 и 8,5% алюминия при 1,0 и 0,5 цинка и 0,3% марганца.
Предел прочности у этих сплавов достигает σв 30-35 кГ/мм2 (294-343 Мн/м2). Сплав МА1, содержащий в среднем 2% Mn без других компонентов, применяется как листовой материал и имеет повышенную пластичность, но меньший предел прочности (σв ≈ 20 кГ/мм2, 196 Мн/м2).
Для предохранения от коррозии магниевые сплавы обрабатываются раствором Н2О+К2Cr207+HNO3 и тщательно окрашиваются.
МЕДЬ И ЕЕ СПЛАВЫ
1. Характеристика меди.
2. Классификация медных сплавов. Латуни.
3. Оловянные бронзы.
4. Алюминиевые бронзы.
5. Кремниевые, бериллиевые, свинцовые бронзы.
В электромашиностроении и при производстве проводов очень широко применяется чистая медь, которая по электропроводимости занимает среди металлов 2-е место после серебра. Медь – вязкий металл красновато-розового цвета. Кристаллическая решетка меди – куб с центрированными гранями.
Микроструктура чистой меди состоит из зерен с характерными двойниками. Медь отличается хорошей теплопроводимостью и стойкостью против атмосферной коррозии.
Присутствие даже незначительных количеств других элементов может сильно понизить ее электропроводимость. Нерастворимые в меди и неметаллические включения (Pb, Bi, S-стые и О2-е включения) мало изменяют ее электропроводимость.
Элементы, образующие твердые растворы с медью по-разному влияют на ее электропроводимость. Например, полностью растворимое в медь серебро очень мало снижает ее электропроводимость. Элементы, ограниченно растворимые в твердом состоянии, например, As резко снижают электропроводимость меди, причем, чем меньше растворимость, тем больше снижается электропроводимость.
Различные элементы могут сжижать или расширять решетку меди, но чем сильнее они искажают ее, тем больше снижение электропроводимости. Так, Ni полностью может растворяться в меди, но вызывает большое снижение электропроводимости вероятно потому, что Ni сильно сжимает решетку меди.
Медную проволоку используют тогда, когда не требуется высокая механическая прочность. Утроить предел прочности в случае необходимости можно добавками Cd (0,8-1,0%). Электропроводимость при этом составляет приближенно 90% от электропроводимости чистой меди.
|
|
Поперечные профили набережных и береговой полосы: На городских территориях берегоукрепление проектируют с учетом технических и экономических требований, но особое значение придают эстетическим...
Археология об основании Рима: Новые раскопки проясняют и такой острый дискуссионный вопрос, как дата самого возникновения Рима...
Архитектура электронного правительства: Единая архитектура – это методологический подход при создании системы управления государства, который строится...
Своеобразие русской архитектуры: Основной материал – дерево – быстрота постройки, но недолговечность и необходимость деления...
© cyberpedia.su 2017-2024 - Не является автором материалов. Исключительное право сохранено за автором текста.
Если вы не хотите, чтобы данный материал был у нас на сайте, перейдите по ссылке: Нарушение авторских прав. Мы поможем в написании вашей работы!