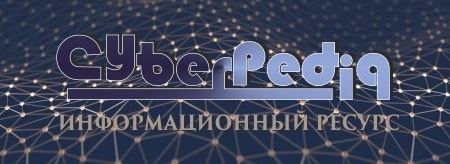
Кормораздатчик мобильный электрифицированный: схема и процесс работы устройства...
Общие условия выбора системы дренажа: Система дренажа выбирается в зависимости от характера защищаемого...
Топ:
Определение места расположения распределительного центра: Фирма реализует продукцию на рынках сбыта и имеет постоянных поставщиков в разных регионах. Увеличение объема продаж...
Комплексной системы оценки состояния охраны труда на производственном объекте (КСОТ-П): Цели и задачи Комплексной системы оценки состояния охраны труда и определению факторов рисков по охране труда...
Основы обеспечения единства измерений: Обеспечение единства измерений - деятельность метрологических служб, направленная на достижение...
Интересное:
Что нужно делать при лейкемии: Прежде всего, необходимо выяснить, не страдаете ли вы каким-либо душевным недугом...
Инженерная защита территорий, зданий и сооружений от опасных геологических процессов: Изучение оползневых явлений, оценка устойчивости склонов и проектирование противооползневых сооружений — актуальнейшие задачи, стоящие перед отечественными...
Национальное богатство страны и его составляющие: для оценки элементов национального богатства используются...
Дисциплины:
![]() |
![]() |
5.00
из
|
Заказать работу |
|
|
Вагон Еж-3 — моторный, четырехосный, на двух двухос-
ных поворотных тележках, цельнометаллический, сварной
конструкции. Каждый вагон имеет кабину управления и
представляет собой самостоятельную подвижную единицу, из
любого количества которых (но не более восьми) может быть
составлен поезд.
Управление поездом дистанционное по системе многих
единиц.
Все колесные пары вагона обмоторены, вращающий мо-
мент от тяговых двигателей передается к колесным парам
через карданные муфты и одноступенчатые цилиндрические
редукторы.
Для входа в пассажирское помещение вагон с каждой
боковой стороны имеет по четыре дверных проема, которые
закрываются задвижными дверными створками с помощью
привода с централизованным управлением.
Тормозные устройства вагона включают в себя:
— рабочий тормоз — электродинамический реостат-
ный, действующий при переводе
тяговых электродвигателей на
генераторный режим;
— экстренный тормоз — пневматический колодочный;
— стояночный тормоз
— ручной механический, действую-
щий на тормозные колодки ле-
вой стороны только одного ваго-
на.
1. Динамические показатели
— Максимальная допустимая скорость — 90 км/час
— Среднее ускорение при пуске — 1,2 м/сек2
— Среднее замедление при торможении — 1,2 м/сек2
2. Габаритные размеры
— Длина вагона по торцевым стенкам
— Длина по центрам автосцепок
— 18810 мм
— 19206 мм
Ширина вагона — 2712 мм
Номинальная высота порожнего вагона от
уровня головок рельс —- 3662 мм
Высота порожнего вагона от уровня головки
рельс до уровня пола — 1208 мм
Высота от уровня головок рельс до оси
автосцепки (порожнего вагона) — 829 мм
|
База вагона — 12600 мм
3. Весовая характеристика
Вес порожнего вагона (тара) — 34,5 т
Вес кузова с оборудованием — 17,6 т
Вес электрооборудования — 3,5 т
Вес пневматического оборудования — 1,3 т
4. Населенность вагона
Количество мест для сидения — 42 чел.
Полная максимальная населенность вагона — 262 чел.
КУЗОВ ВАГОНА
При изучении темы «Кузов вагона» преподаватель должен
показать, какие основные нагрузки действуют на кузов при
движении вагона. Необходимо обратить внимание учащихся
на цельносварную конструкцию кузова и на преимущества та-
кой конструкции перед другими. Затем преподаватель дол-
жен рассказать о назначении, конструкции и работе каждого
узла кузова.
При изучении конструкции и работы дверей, следует об-
ращать внимание учащихся на основные неисправности узла
подвески в эксплуатации и на способы их устранения, подро-
бно остановиться на изучении конструкции и работы блоки-
ровочного устройства дверей.
Кузов — цельносварной конструкции, несущими частями
его являются рама с полом, каркас и наружная обшивка.
В оборудование кузова входят также внутренняя отделка
и потолок, перегородка кабины машиниста, двери, окна, вен-
тиляция, поручни, диваны и арматура освещения.
1. Рама кузова (рис. 1)
Рама сварная состоит из боковых поясов, двенадцати по-
перечных балок, двух шкворневых балок, двух сварных тор-
цевых брусьев. Между торцевыми брусьями и шкворневыми
балками веерообразно расположены две хребтовые балки.
Они служат для передачи продольных нагрузок на боковые
пояса рамы и стенки кузова. Средние продольные балки от-
сутствуют. Вместо этого по всей длине кузова применяется
гофрированный металлический настил пола (гофрами вдоль
вагона).
Боковые пояса рамы представляют собой штампованное
швеллерное сечение (180x70X6 мм). Для приварки листов на-
ружной обшивки стен кузова в боковых поясах предусмотре-
ны овальные отверстия. Боковые пояса изготовляются из от-
|
дельных балок, которые сварены между собой встык электро-
дутовой сваркой (под углом 45°).
Стыки усилены накладками 10x40 мм на нижних горизон-
тальных полках балок.
Поперечные балки рамы также выполнены штампованны-
ми и имеют швеллерное сечение (174x65X6 мм). В балках
имеются овальные отверстия для облегчения веса и монтажа
трубопроводов. Все поперечные балки рамы унифицированы.
Шкворневые балки сварены из двух вертикальных и двух
горизонтальных листов толщиной 8 мм. Верхние горизонталь-
ные листы удлинены для сварки с боковыми поясами. В ме-
стах установки пятника и боковых скользунов между гори-
зонтальными листами вварены ребра жесткости.
Торцевые брусья выполнены из штампованных швеллер-
ных профилей, сверху и снизу они перекрыты усиливающими
диафрагменными листами толщиной 5 мм.
Хребтовые балки состоят из двух балок 2-образно-
го профиля с высотой 180 мм и шириной горизонталь-
ных полок 75 мм. Их штампуют из листа толщиной 8 мм.
К хребтовым балкам приклепаны гнезда автосцепок. От тор-
цевого бруса балки идут сначала параллельно, а затем рас-
ходятся веерообразно, за счет чего продольные ударные и тя-
говые усилия при работе автосцепок передаются на боковые
пояса рамы кузова и на стенки кузова.
Все рамы балки кузова изготавливают из стали 20 или
стали 3.
В устройство рамы кузова входят также рамки люков по-
ла и различные угольники, скобы, ребра, косынки для под-
вески оборудования, электрических и пневматических аппара-
тов и для раскладки труб внизу рамы.
Раму кузова сваривают в специальных кондукторах, что
исключает перекосы и обеспечивает большую точность изго-
товления.
2. Боковые и торцевые стенки кузова
Боковые и торцевые стенки кузова собираются из верти-
кальных стоек, подоконных балок, верхнего пояса и обшивоч-
ных листов толщиной 2 мм.
Для увеличения жесткости обшивки и уменьшения коро-
бления при сварке наружная обшивка выполнена гофриро-
ванной. Каркас выполняют из 2-образных и омегооб-
разных профилей, что обеспечивает необходимую жест-
кость и хорошие условия контактной сварки. Сборка
и сварка отдельных секций стенок кузова выполняет-
ся электроконтактной сваркой с последующим соедине-
нием отдельных секций боковин с торцевыми стенками и кры-
|
шей электродуговой сваркой в специальном кондукторе.
Приварка стенок кузова к раме производится прерыви-
стой электродуговой сваркой через овальные отверстия в бо-
ковых поясах рамы и сплошным швом по нижней кромке об-
шивки к вертикальной стенке бокового пояса.
3. Крыша кузова
Крыша кузова полуфонарного типа выполнена из омего-
образных дуг толщиной 2 мм, опирающихся на верхние бо-
ковые пояса кузова, и обшивки толщиной 1,4 мм. В верхней
части крыши имеются шесть продольных гофров жесткости.
В продольном направлении дуги связаны между собой се-
мью параллельными рядами стрингеров. Боковые ряды стрин-
геров образуют армировку для вентиляционных отверстий.
Конструкция крыши позволяет производить ее сборку как
целиком, так и секциями.
4. Вентиляция
На боковых скатах крыши, заподлицо со средней частью,
приварены вентиляционные черпаки по тринадцать штук с
каждой стороны. Черпаки правой стороны своим зевом на-
правлены в сторону кабины. Черпаки левой стороны — в про-
тивоположном направлении.
Вентиляция приточно-вытяжная естественная. Недостат-
ком существующей конструкции вентиляции является то, что
она работает только во время движения поезда и не всегда
достаточно эффективна, что вызывает необходимость иметь
форточки.
5. Перегородка
Внутреннее помещение кузова разделяется перегородкой
на пассажирский салон и кабину управления.
Перегородка со стороны салона имеет дверь для прохода
в кабину. Двойные стенки перегородки справа и слева двер-
ного проема образуют отсеки для размещения оборудования
АРС и радиовещания. Отсеки со стороны салона закрываются
створками люков, которые навешиваются на петлях. Створ-
ки люков открываются в сторону боковых стен кузова. Запо-
ры створок выполнены со скрытыми приводами и расположе-
ны в проходе из салона в кабину.
Поворотом рукоятки на себя освобождаются одновремен-
но два замка створки люка. Створка открывается под дейст-
вием упругого натяга в петлях, а рукоятка с замками под
действием пружины возвращается в первоначальное положе-
ние. При закрытии створки замки просто защелкиваются.
|
Штатив с оборудованием установлен в отсеке на специ-
альных петлях и может быть повернут в сторону салона, от-
крывая доступ к оборудованию со всех сторон.
6. Пол вагона (рис. 2)
На раму кузова укладывается и приваривается к ней элек-
тросваркой гофрированный металлический настил, гофрами
вдоль вагона. На настил укладываются два слоя асбеста и
фанера толщиной десять миллиметров. Листы фанеры при-
крепляют к металлическому настилу самонарезающими вин-
тами. Нижняя поверхность фанеры покрывается антисепти-
ческой (противогнилостной) пастой. Верхняя поверхность фа-
неры окрашивается грунтом, и свободная от диванов плос-
кость покрывается линолеумом на тканевой основе толщиной
4 мм.
Около шкворневых балок в полу имеются люки для ос-
мотра и ухода за двигателями, редуктором и карданной муф-
той. Кроме того, у каждой шкворневой балки в полу имеются
отверстия, закрываемые резьбовыми крышками, для доступа
к шкворню и масленке пятника.
7. Внутренняя отделка стен и потолка
Потолок и стены салона и кабины управления обшивают-
ся декоративным бумажно-слоистым пластиком толщиной 3
мм. Стыки листов пластика перекрываются специальными
профилями из алюминиевых сплавов.
Наддверные люки, где установлены механизмы задвиж-
ных створок и дверные блокировки, закрываются крышками
из бумажно-слоистого пластика толщиной 1,6 мм, армиро-
ванными алюминиевыми профилями. Крышки люков запира-
ются трехгранным ключом, а для удержания их в открытом
положении имеются специальные опорные планки, прикре-
пленные к верхнему поясу каркаса кузова.
8. Двери, дверное подвешивание и блокировка
В пассажирском помещении, на каждой боковой стенке,
расположено по четыре дверных проема для входа и выхода
пассажиров. Каждый дверной проем оборудован двумя за-
движными створками. Для служебного пользования по тор-
цам вагона, в перегородке и в левой стороне кабины управ-
ления имеются.одностворчатые двери (4 штуки), оборудован-
ные замками под трехгранный ключ и ручками для открыва-
ния и закрывания. Створчатые двери подвешиваются на пет-
лях. Конструкция петель обеспечивает возможность регули-
ровки высоты подвески створки над уровнем пола.
Петли подвески створчатых дверей шарнирные, приверну-
ты винтами к стойкам кузова с опорой через шарик диамет-
ром 5/16", то есть 7,38 мм.
Створки всех дверей изготовлены из листового алюминие-
вого сплава. Конструкция створки бескаркасная. Сборка
штампованных профилей производится на одном листе с при-
варкой контактной сваркой. Затем все это перекрывается вто-
рым листом, также приваренным контактной сваркой.
|
Верхние половины створок застеклены. Стекла вставляют-
ся в специальное резиновое уплотнение. Заделка стекол вы-
полнена таким образом, что исключает их выпадание (рис. 3).
Раздвижные створки подвешиваются к верхнему обвязоч-
ному поясу кузова через специальные арочные балки. Закре-
пление этих балок к верхнему обвязочному поясу производит-
ся болтами и специальными гайками с контргайками, с по-
мощью которых можно производить регулировку высоты под-
вески створок. Подвеска створок к арочной балке осущест-
вляется через два ряда шариков, размещенных в сепараторе.
В балке имеются продольные пазы для размещения в них ша-
риков. На шариках перекатывается специальная планка, в
которой тоже имеются продольные пазы для шариков. К
планке болтами крепится щечка, которая в свою очередь при-
креплена к створке двери болтами (рис. 4).
Створки приводятся в действие на закрытие или открытие
пневматическим цилиндром, связанным с одной из створок
дверного проема. Усилие на вторую створку дверного проема
передается от первой при помощи двух втулочнороликовых
цепей. Цепи заведены через звездочки, установленные на
арочных балках. Натяжение цепей регулируется натяжными
винтами.
В нижней части задвижных створок закреплены направ-
ляющие хромированные планки, а на стойках дверного прое-
ма установлены обрезиненные ролики. Это сделано с целью
уменьшения раскачки створок при открытии и закрытии.
В открытом положении створки входят в пазухи простен-
ков вагона, а в закрытом состоянии уплотняются специаль-
ными резиновыми уплотнениями замкового типа (рис. 5).
При необходимости снять створки требуется:
— открыть наддверные люки;
— отсоединить шток цилиндра;
— снять цепи;
— передвинуть створки в дверной проем;
— отвернуть болты крепления створки к щечке и вынуть
створку внутрь вагона.
Механизм подвески снимается после освобождения болтов
подвески путем отвертывания контргаек и гаек.
Сигнализация открытия и закрытия дверей осуществляет-
ся механизмом блокировки путем подачи напряжения на лам-
пу в пульте управления. При открывании створок лампа за-
горается, при закрывании она гаснет. Механизм блокировки
(рис. 6) состоит из конечного выключателя, маятника с пру-
жинами и толкателя. Выключатель и маятник установлены
на боковине кузова. Толкатель закреплен на ведомой створ-
ке двери.
При закрытых дверях толкатель на створке отжимает
маятник от толкателя конечного выключателя — цепь размы-
кается, и сигнальная лампа гаснет. При открытых дверях тол-
катель створки освобождает маятник, который под действием
пружины нажимает на толкатель выключателя — цепь
замыкается, и сигнальная лампа загорается.
Регулировку механизма производят путем изменения дли-
ны толкателя на створке, который, перемещая маятник,
уменьшает или увеличивает силу нажатия маятника на тол-
катель. Сигнальная лампа должна загораться при растворе
створок в свете не более 20 мм.
9. Окна
Окна застекляются стеклом толщиной 6 мм. Окна безра-
мочные. Стекла устанавливаются через специальные резино-
вые армировки в оконные проемы и прижимаются к буртику
наружной обшивки внутренними облицовками из бука или
алюминиевых сплавов. Широкие окна салона оборудованы
форточками с задвижным стеклом толщиной 5 мм, остальные
окна глухие. Боковое окно в кабине управления опускное.
Для облегчения его перемещения по направляющим пазам в
оконной пазухе имеется противовес. В закрытом (поднятом)
положении стекло удерживается пружинным фиксатором.
Для замены вышедшего из строя стекла в салоне необхо-
димо снять облицовки окна и вынуть стекло вместе с резино-
вой армировкой внутрь салона. Для смены стекла форточки
требуется снять только верхнюю часть внутренней облицов-
ки и разобрать рамку.
10. Диваны
В промежутках между раздвижными дверями расположе-
ны шестиместные диваны, между торцевой стенкой и послед-
ним дверным проемом установлен трехместный диван.
Диван состоит из спинки, подушки и каркаса. Каркас со-
стоит из вертикальных стоек, продольных связей, боковых ще-
ковин и щитков, закрывающих поддиванное пространство.
Подушки и спинки диванов полумягкие. На деревянную
рамку подушек накладывается фанера толщиной 10 мм и на
нее наклеивается поропласт толщиной 20 мм. На спинках
вместо фанеры применяется дюралюминий толщиной 1,5 мм
и на него наклеивается поропласт толщиной 10 мм. Снаружи
подушки и спинки обшивают искусственной кожей на трико-
тажной основе,
11. Поручни
Между дверными проемами, на высоте 1830 мм от уровня
пола, над диванами устанавливаются на специальных крон-
штейнах продольные поручни. У торцевых стенок по обе сто-
роны створчатой двери установлены вертикальные поручни.
Поручни изготавливают из труб диаметром 27 мм и хроми-
руют.
ТЕЛЕЖКА
При изучении этой темы преподавателю необходимо объ-
яснить учащимся для чего служат тележки вагона, какие на-
грузки они испытывают в процессе работы, из каких узлов
они состоят и каково назначение каждого узла тележки.
Изложение материала необходимо увязать с показом те-
лежек под вагоном, т. к. это даст учащимся возможность яс-
нее представить конструкцию отдельных узлов и их располо-
жение на вагоне.
Плакаты, используемые при изучении данной темы, долж-
ны быть выполнены с особой тщательностью, обладать как
можно большей наглядностью.
При изучении отдельных узлов оборудования, входящих
в комплект тележки, преподаватель также должен стремить-
ся к обязательному натурному показу этих узлов на вагоне.
На каждом вагоне установлены две двухосные поворот-
ные моторные тележки с двойным подрессориванием, то есть
с двойным рессорным подвешиванием — центральным и над-
буксовым.
Вес тележки с тяговыми двигателями — 7500 кг.
База тележки — 2100 мм. Диаметр колес по кругу ката-
ния — 780 мм.
Диаметр шейки оси — 110 мм.
В комплект входят:
— рама тележки;
— две колесные пары с редукторами;
— два тяговых двигателя и узлы их подвешивания на раме
тележки;
— тормозное оборудование;
— центральное подвешивание с гидравлическими гасителями
колебаний (гидроамортизаторами);
— надбуксовое подвешивание;
— пятниковое устройство.
Передача вращающего момента с тягового двигателя на
колесную пару осуществляется через карданную муфту.
1. Рама тележки (рис. 7)
Изучение темы «Рама тележки» необходимо начинать с
изложения особенностей конструкции рамы тележки вагона
Еж-3 и преимуществ ее по сравнению с рамами тележек более раннего выпуска. Еще раз необходимо остановиться на ее
назначении и перейти к изложению конструкции, обратить
внимание учащихся на имевшие место неисправности в ра-
мах тележек вагонов типа Е и способы их устранения.
Рама тележки состоит из двух продольных и двух попе-
речных балок и имеет Н-образную форму. И продольные, и
поперечные балки имеют коробчатое сечение. Каждая балка
сварена из двух корытообразных профилей, штампованных
из стального листа толщиной 10 мм.
Поперечные балки соединяются с продольными при помо-
щи сварки встык. Места стыковки перекрываются сверху и
снизу усиливающими косынками толщиной 6 мм. Косынки с
каждой стороны рамы состыковываются на боковых стенках
средних поперечных балок в общий замкнутый контур и ча-
стично отбортовываются в проем центрального подвешива-
ния.
Косынки по контуру привариваются электросваркой и до-
полнительно крепятся в широкой части продольных балок
сварными заклепками.
На каждой продольной балке имеется два кронштейна
крепления тормозных цилиндров, кронштейны крепления бук-
совых поводков (средние и концевые) и кронштейны крепле-
ния рычагов тормозной рычажной передачи.
На поперечных балках приварены кронштейны подвески
тяговых двигателей, кронштейн подвески редуктора и кронш-
тейн крепления комплексного предохранения подвески редук-
тора. Со стороны установки бруса центрального подвешива-
ния, для ограничения его продольных перемещений, на попе-
речных балках приварены плоские скользуны. По концам по-
перечных балок вварены опорные гнезда со сменными втул-
ками под валики центрального подвешивания. В нижних стен
ках балок под опорными гнездами вырезаны окна для прохо-
да подвесных серег центрального подвешивания. Окна арми-
рованы по всему периметру специальными коробочками.
Кронштейн для подвешивания корпуса редуктора цельно-
кованный, с проушиной и стержневой частью. Стержень крон-
штейна проходит сквозь отверстия в обеих вертикальных
стенках поперечной балки и обваривается.
Для подвешивания тяговых двигателей на каждой попе-
речной балке имеется три кронштейна. Два верхних кронш-
тейна выполнены одинаковыми. Втулочными основаниями
они вварены в поперечную балку, а их опорные ступенчатые
плиты служат опорами для верхних приливов (лап) тягового
двигателя. Плиты наклонены под углом 15° к вертикали.
Нижний кронштейн подвески тягового двигателя совкового
типа. Он имеет форму открытой коробки. Задняя наклонная
стенка этой коробки служит опорной поверхностью для ниж-
ней лапы двигателя. Боковые стенки кронштейна поставлены
шире лапы двигателя и обеспечивают возможность переме-
щения двигателя вдоль оси. Боковые стенки коробки имеют
резьбовые отверстия для опорных болтов. Этими же болтами
осуществляют регулировку положения тягового двигателя. От-
вертывая один из болтов и подвертывая другой, можно пере-
мещать двигатель в ту или другую сторону и этим регулиро-
вать разбег карданной муфты.
На всех трех кронштейнах подвешивания тягового двига-
теля имеется по одному овальному отверстию для болтов кре-
пления тягового двигателя при его окончательной фиксации.
Кронштейн комплексного предохранения изготовлен из
листовой стали толщиной 10 мм. На нем имеется гребенчатая
насечка и два овальных отверстия под болты для фиксации
вилки комплексного предохранителя на необходимом уровне.
По осям базы тележки (над серединами букс колесных
пар) в продольные балки вварены направляющие вертикаль-
ные втулки для предохранительных штырей букс. В случае
излома поводков предохранительные штыри обеспечат связь
колесной пары с рамой тележки. С двух сторон по отношению
к каждой из этих втулок снизу продольной балки приварены
втулки для фиксации резиновых амортизаторов и верхних
опор пружин надбуксового подвешивания.
Кронштейны тормозных подвесок ковано-сварной конст-
рукции. Крепятся к продольным балкам как кронштейны под-
вески редукторов или как верхние кронштейны подвески тя-
говых двигателей.
Поскольку тележка вагона типа Еж-3 выполнена бесче-
люстной, рама тележки не имеет буксовых челюстей. Снизу
продольных балок в средней части привариваются стальные
литые кронштейны с гребенками для крепления к ним упру-
гих буксовых поводков.
По торцам продольных балок приварены гребенчатые на-
кладки для крепления концевых изогнутых компенсационных
поводков. Поводки служат для связи колесной пары с рамой
тележки. Каждая букса связана с рамой двумя прямыми и
одним изогнутым поводками. Всего на вагоне 24 поводка (16
прямых и 8 изогнутых). Кроме того, на каждой продольной
балке, в районе расположения центрального подвешивания,
имеются проушины для крепления гидравлического гасителя
колебаний.
При изготовлении и ремонте рамы необходимо произво-
дить замеры базы тележки и ее диагоналей (по отверстиям
под предохранительные штыри букс). База тележки состав-
ляет 2100 мм. Применение бесчелюстной рамы тележки име-
ет ряд преимуществ — отсутствие буксовых лап и налични-
ков на буксовых лапах и на буксах упрощает процесс изго-
товления рамы, нет необходимости следить за величинами
разбегов колесных пар; достигнуты лучшие динамические по-
казатели, улучшен ход вагона, особенно при движении с боль-
шими скоростями; улучшены условия работы карданной муф-
ты. При этом необходимо учитывать, что поводки работают
в крайне сложных условиях. На них одновременно действуют
различные нагрузки — растяжение, продольное сжатие, изгиб
(в вертикальной и горизонтальной плоскостях). Поэтому для
нормальной работы поводков большое значение имеет не
только качество изготовления поводков, но и правильность их
монтажа на тележке. Для повышения усталостной прочности
поводков применяют сталеструйный наклеп их поверхности.
2. КОЛЕСНЫЕ ПАРЫ
Изучение темы начать с назначения колесных пар, нагру-
зок, действующих на них при движении вагона. При этом не-
обходимо обратить внимание на сложные условия работы оси
колесной пары и на требования, предъявляемые в связи с
этим к изготовлению и эксплуатации осей. Следует объяс-
нить учащимся преимущества применения подрезиненных ко-
лес и колес с удлиненными ступицами.
При изложении конструкции подрезиненного колеса не-
обходимо обратить внимание на конструкцию и назначение
отдельных его элементов, а также на особую тщательность
соблюдения технологии сборки колеса.
Преподавателю необходимо остановиться на слабых ме-
стах конструкции колеса и способах обнаружения неисправ-
ностей.
Следует также обратить внимание учащихся на требова-
ния ПТЭ к состоянию поверхности катания колеса и др. его
элементов.
При дальнейшем изучении темы необходимо подробно
остановиться на формировании колесных пар, сборке редук-
торного узла и монтаже букс, обратить внимание учащихся
на методы контроля правильности проведения этих операций.
Учащиеся должны ясно представлять себе назначение,
конструкцию и работу редукторного и буксового узлов ко-
лесной пары.
При изучении редукторного узла учащиеся должны понять
преимущества косозубой передачи с эвольвентным профилем
зуба по сравнению с другими типами зубчатых колес.
Каждая колесная пара состоит из оси, двух подрезинен-
ных колес, редукторного узла и двух букс.
Ось изготовляют из углеродистой стали марки Ос М (осе-
вая метро) по ГОСТу 6690-53.
Заготовки осей (поковки) отковывают на молотах, при-
чем уковка слитка металла должна быть пятикратной. Отко-
ванные заготовки подвергают нормализации (нагрев до тем-
пературы 870-890° С с последующим охлаждением на возду-
хе) или нормализации с дополнительным отпуском — для уст-
ранения ковочных напряжений и выравнивания структуры ме-
талла. Каждая поковка должна иметь следующие клейма,
которые наносятся на среднюю или подступичную часть оси
в горячем состоянии:
— номер завода — изготовителя поковки;
— номер оси;
— номер плавки;
— год изготовления поковки;
— клеймо приемщика МПС.
Ось обрабатывают на токарном станке. Перед обработкой
поковка должна быть проверена на ультразвуковом дефекто-
скопе. При наличии дефектов или при непрозвучивании по-
ковка бракуется. Обработанную на токарном станке ось под-
вергают упрочняющей накатке роликами. Накатку произво-
дят двумя роликами высокой твердости. Ролик вращается на
подшипниках в специальных державках. Они располагаются
в горизонтальной плоскости по обе стороны оси и гидравли-
ческими цилиндрами прижимаются к ней с усилием 1700-2200
кг, одновременно перемещаясь вдоль оси. Ось при этом поли-
вают машинным маслом. Усилие, производимое роликами,
контролируется по манометрам. После накатки поверхност-
ная твердость металла увеличивается на 25-30%, и почти
вдвое повышается усталостная прочность. Накатке подвер-
гают всю ось, кроме предподступичных частей.
С целью исключения концентрации напряжений под кром-
кой лабиринтного кольца и внутреннего кольца роликопод-
шипника буксы на оси перед галтелью перехода от шейки оси
к предподступичной части выполняют разгрузочную канавку
глубиной 0,15-0,3 мм.
Обработанная ось клеймится. Клейма ставят на торце пер-
вой шейки в одном из сегментов. Клейма содержат:
— номер оси;
— номер плавки металла;
— две последние цифры года отковки оси;
— месяц и две последние цифры года обработки оси;
— в основании паза под стопорную планку ставят клейма ма-
стера ОТК и инспектора службы подвижного состава.
Номер плавки металла необходимо иметь для того, чтобы
в случае обнаружения на одной оси каких-либо дефектов ме-
талла, можно было бы взять под контроль все другие оси
данной плавки.
Размеры основных элементов оси (рис. 8) следующие:
— диаметр резьбовой части М 95;
— диаметр шейки ПО мм;
— диаметр предподступичной части 145 мм;
— диаметр подступичной части 155 мм;
диаметр средней части 145 мм;
— длина оси 2302 + 2 мм;
— расстояние между серединами шеек 2036 мм.
На средней части оси имеется керн глубиной 2 мм с углом
60°, относительно которого по специальным шаблонам опре-
деляются места расположения на оси того или иного элемен-
та колесной пары при напрессовке.
Расстояние между серединами шеек желательно иметь
меньше, так как от его величины зависит величина изгибаю-
щего момента, действующего на ось.
Подрезиненное колесо (рис. 9)
Подрезиненное колесо состоит из следующих деталей:
— колесный центр;
— центральный диск;
— нажимной диск;
— бандаж;
— 16 резиновых вкладышей;
— 8 шпилек;
— 8 болтов;
— 8 штифтов;
— 2 медных шунта.
Колесный центр стальной литой, имеет нормальную или
удлиненную ступицу и дисковую часть. Ступица со стороны
установки нажимного диска выполнена ступенчатой (рассто-
яние от дисковой части до торца ступени — 66 мм). В торце
этой части ступицы имеется 8 отверстий диаметром 26 мм для
установки штифтов, фиксирующих нажимную шайбу, и во-
семь отверстий с резьбой М20, куда ввертываются болты кре-
пления нажимного диска. В диске колесного центра на внут-
ренней поверхности выполнено восемь углублений для разме-
щения центрирующих резиновых вкладышей. Кроме того, име-
ется восемь сквозных отверстий для прохода резьбовых кон-
цов шпилек.
Шпильки имеют на концах резьбу М 27x3, гладкую сред-
нюю часть диаметром 28 мм и два буртика, расстояние меж-
ду наружными гранями которых 66 мм. (Такое же, как рас-
стояние от торца ступицы до дисковой части колесного цен-
тра).
Резиновый вкладыш представляет собой плоский шестиу-
гольник с двумя цилиндрическими выступами диаметром 32
мм в центре. Изготовляют вкладыш из специальной твердой
резины формовым способом. С обеих сторон вкладыш имеет
армировки из листовой стали толщиной 3 мм, которые при-
вулканизированы к резине или ставятся на клею. Общая тол-
щина вкладыша в свободном состоянии 26 мм (в сжатом —
24 мм).
Выступы вкладышей служат только для их центровки и
фиксации, а не для передачи нагрузки сдвига. Эта нагрузка
передается на армировку вкладышей благодаря силе трения,
возникающей между поверхностями дисков и армировок, в
результате сжатия вкладышей.
Центральный диск имеет дисковую часть толщиной 18 мм
и обод для насадки на него бандажа. Обод проточен под «ла-
сточкин хвост». В дисковой части выполнено 8 отверстий для
прохода буртиков шпилек и восемь отверстий для центриру-
ющих выступов вкладышей.
Бандаж изготавливают методом раскатки. Он имеет фор-
му кольца, на наружном диаметре которого выполнена по-
верхность катания колеса с гребнем. Внутренний диаметр
бандажа со стороны гребня имеет наклонную канавку для
размещения укрепляющего кольца, а с противоположной сто-
роны — буртик.
Бандаж сажают на центральный диск в горячем состоя-
нии с натягом 0,9-1,1 мм. Подобранный по натягу бандаж
нагревают в индукционной печи до температуры 320°С. Вели-
чина температуры нагрева контролируется термопарой или
свинцовым карандашом. Нагрев свыше 320°С не допускается,
так как при этом может произойти отпуск закаленной поверх-
ности катания. Нагретый бандаж укладывают гребнем вверх,
в него опускают центральный диск и заводят укрепляющее
кольцо в канавку бандажа. Концы кольца плотно пригоняют
друг к другу и зачеканивают, затем подают колесо на заваль-
цовочный станок, где специальным роликом производят при-
жатие буртика бандажа за канавкой к укрепляющему коль-
цу. Температура бандажа при этом должна быть не менее
150°. В случае ослабления посадки бандажа он удержится на
центральном диске с одной стороны буртом, а с другой — ук-
репляющим кольцом. Качество посадки бандажа проверяют
обстукиванием молотком. При ударе по кольцу оно не долж-
но дребезжать, а при ударе по бандажу молоток должен из-
давать чистый звонкий звук и упруго отскакивать. При сла-
бой посадке молоток.вязнет и издает глухой звук. Для кон-
троля за состоянием посадки в процессе эксплуатации на на-
ружных гранях бандажа и центрального диска ставят конт-
рольные риски, которые после окраски колеса окрашивают в
красный цвет. Их ставят притуплённым зубилом глубиной не
более 0,5 мм и длиной не более 25 мм.
Неудовлетворительная посадка (овальность, грубая обра-
ботка посадочных поверхностей, неточный подбор натягов,
плохая очистка посадочных поверхностей от грязи или окали-
ны) или повышенный нагрев при неправильной эксплуата-
ции (например при длительном движении с неотпущенным
ручным тормозом) могут привести к ослаблению и проворо-
ту бандажа. По ПТЭ проворот бандажа не допускается. Ино-
гда, как исключение, после проворота бандажа выпускают
колесо в эксплуатацию при условии, что бандаж после про-
ворота имеет плотную посадку, проворот не превышает 200
мм и произошел впервые. При этом необходимо старую рис-
ку на центральном диске зачеканить и напротив оставшейся
риски бандажа выбить новую риску на ободе центрального
диска.
Чтобы снять бандаж, нужно на токарном станке вырезать
укрепляющее кольцо до уровня внутренней расточки банда-
жа. Затем колесную пару устанавливают вертикально на
электрогорне с опорой на снимаемый бандаж и разогревают
до температуры выше 320°С. Бандаж расширяется, и колес-
ный центр и центральный диск выпадают вниз вместе с ко-
лесной парой. Смена бандажа производится в случае ослаб-
ления или проворота бандажа, при обнаружении трещин в
металле, при изломе гребня и наличии других неисправимых
дефектов на поверхности катания, а также, когда диаметр по
кругу катания и толщина бандажа имеют размеры ниже уста-
новленных нормами.
Нажимной диск представляет собой стальную шайбу, в
которой высверлено восемь отверстий для прохода резьбовых
частей шпилек, восемь отверстий для прохода штифтов, во-
семь отверстий для прохода болтов и восемь углублений под
центрирующие выступы вкладышей.
|
|
Состав сооружений: решетки и песколовки: Решетки – это первое устройство в схеме очистных сооружений. Они представляют...
Типы сооружений для обработки осадков: Септиками называются сооружения, в которых одновременно происходят осветление сточной жидкости...
Биохимия спиртового брожения: Основу технологии получения пива составляет спиртовое брожение, - при котором сахар превращается...
Двойное оплодотворение у цветковых растений: Оплодотворение - это процесс слияния мужской и женской половых клеток с образованием зиготы...
© cyberpedia.su 2017-2024 - Не является автором материалов. Исключительное право сохранено за автором текста.
Если вы не хотите, чтобы данный материал был у нас на сайте, перейдите по ссылке: Нарушение авторских прав. Мы поможем в написании вашей работы!