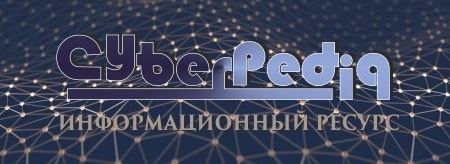
Наброски и зарисовки растений, плодов, цветов: Освоить конструктивное построение структуры дерева через зарисовки отдельных деревьев, группы деревьев...
Семя – орган полового размножения и расселения растений: наружи у семян имеется плотный покров – кожура...
Топ:
Эволюция кровеносной системы позвоночных животных: Биологическая эволюция – необратимый процесс исторического развития живой природы...
Методика измерений сопротивления растеканию тока анодного заземления: Анодный заземлитель (анод) – проводник, погруженный в электролитическую среду (грунт, раствор электролита) и подключенный к положительному...
Характеристика АТП и сварочно-жестяницкого участка: Транспорт в настоящее время является одной из важнейших отраслей народного хозяйства...
Интересное:
Берегоукрепление оползневых склонов: На прибрежных склонах основной причиной развития оползневых процессов является подмыв водами рек естественных склонов...
Принципы управления денежными потоками: одним из методов контроля за состоянием денежной наличности является...
Отражение на счетах бухгалтерского учета процесса приобретения: Процесс заготовления представляет систему экономических событий, включающих приобретение организацией у поставщиков сырья...
Дисциплины:
![]() |
![]() |
5.00
из
|
Заказать работу |
|
|
В химико-фармацевтической промышленности преимущественно используют ситовое разделение. С этой целью применяют механизированные сита, представляющие собой сочетание сеток и специальных механизмов, обеспечивающих их движение. По характеру сетки различают сита плетеные, штампованные и колосниковые.
Плетеные сита. Их получают переплетением тонких нитей или проволок. Используют натуральный шелк, синтетические материалы (капрон), специальные сорта нержавеющей стали, латунь, фосфористую бронзу. Плетеные сита малопрочны. Их сетки легко вытягиваются, нити сдвигаются, в результате чего нарушается первоначальная правильность размеров отверстий. Для повышения прочности проволочные сетки подвергают прессованию под большим давлением, благодаря чему в но местах перекрещивания проволока сминается и закрепляется. В некоторых случаях тонкую проволоку и шелковые нити подкрепляют более прочной, с более крупными отверстиями металлической сеткой.
Штампованные сита. Это сита, которые представляют собой металлические листы толщиной 2—12 мм, с проштампованными (пробивными) отверстиями круглой, овальной или квадратной, формы. Они отличаются прочностью и широко применяются в промышленности, однако имеют довольно крупные отверстия — не менее 0,3 мм.
Колосниковые сита. Применяются редко, в основном устанавливаются в мельницах, работающих по принципу удара. Они представляют собой сочетание металлических (чугунных, стальных) пластин (рис. г); отличаются исключительной прочностью.
• Конструкция сит
В химико-фармацевтической промышленности используют механизированные сита. В зависимости от конструкции механизмов, приводящих в движение рабочую поверхность сита и просеиваемый материал, различают сита качающиеся и вибрационные.
|
Качающиеся сита (трясунки). Эти механизмы совершают принудительное качание сита, которое обеспечивается жесткой связью коленчатого вала, шатун-но-кривошипного или эксцентрикового механизмов с корпусом сита. Сито устанавливается в горизонтальном или наклонном положении (7—14°) на роликахдвигающихся по направляющим, иногда они крепятся на шарнирных или кривошипных опорах или же их подвешивают на шарнирных подвесах. Число качаний в минуту составляет от 50 до 400, а амплитуда колебаний от 5 до 200 мм.
Многоярусные качающиеся сита. Многоярусные сита имеют несколько сеток, расположенных одна над другой, причем верхняя имеет наибольшие отверстия, а нижняя — наименьшие. Такие сита позволяют разделить просеиваемый материал по крупности частиц на отдельные фракции.
Вибрационные сита. При помощи специального механизма (вибратора) вибрационные сита совершают частые колебания с небольшой амплитудой. Числовибраций сита находится в пределах 900—1500 в минуту (иногда до 3600) при амплитуде колебаний от 0,5 до 12 мм. При высокой частоте колебаний сита его отверстия почти не забиваются, так как сортируемый материал непрерывно подбрасывается на сетке. Поэтому вибрационные сита пригодны для просеивания разнообразных материалов (в том числе влажных), обеспечивают высокую производительность и точность просеивания.
Вибрационное сито. Устройство вибрационного (электромагнитного) многоярусного сита представлено на рис.4. В корпусе (1) размещено сито (3), имеющее три сетки, расположенные одна над другой, причем верхняя имеет наибольшие отверстия, а нижняя наименьшие. Просеиваемый материал из бункера (2) непрерывно подается на рабочую поверхность сита, которая установлена с наклоном, регулируемым в пределах 20—40°. Привод сита в движение осуществляется посредством электромагнитного генератора коле баний (4), расположенного под его рабочей поверхностью. Ситовая ткань и генератор колебаний соединены между собой по форме замыкания через толкатель, что обеспечивает возбуждение отдельных точек ткани сита. Каждая просеивающая поверхность имеет несколько точек возбуждения. Сито разделяет просеиваемый материал по крупности частиц на три фракции (5), (6), (7). Электромагнитное сито в результате быстрого ускорения ткани обеспечивает высокую производительность и повышенную точность разделения.
|
Рисунок 4.
СМЕШИВАНИЕ
Смешивание — процесс, при котором несколько раздельно находящихся порошкообразных компонентов после тщательного перемешивания и равномерного распределения каждого из них в смешиваемом объеме материала, образуют однородную смесь. Получение однородной смеси очень важно для обеспечения требования о равномерном распределении лекарственных веществ в объеме готовой лекарственной формы.
Особенно возрастают требования к качеству смешивания для препаратов с сильнодействующим веществом, содержание которого в одной дозе менее 5 мг.
Качественное смешивание порошкообразных компонентов в производстве порошков, таблеток и драже представляет собой сложную задачу. Степень и скорость смешивания зависят от большого числа переменных факторов: физико-химических свойств отдельных компонентов (распределение частиц по размерам, форма частиц, характеристика поверхности, насыпная плотность и плотность частиц, содержание влаги, текучесть, коэффициент трения частиц и др.)"> характеристики смешивающих устройств (размеры и геометрия смесителя, размеры возбудителя, тип и размещение загрузочных и разгрузочных устройств, конструкционные материалы и степень их чистоты) и условий операции смешивания (масса каждого добавляемого компонента, отношение объемов смеси и смесителя, метод, последовательность, место и скорость добавления компонентов, скорость смешивания.
Смесители
Аппараты, в которых сыпучие материалы смешиваются между собой и с жидкостями называют смесителями.
Смесители классифицируют: по характеру процесса смешивания (конвективного или диффузионного), конструктивному признаку (барабанные смесители с вращающимся корпусом и червячно-лопастные), способу воздействия на смесь (гравитационные, центробежные), характеру протекающего в них процесса смешивания (периодический или непрерывный) и другим признакам.
|
По характеру протекающего процесса в отечественной химико-фармацевтической промышленности наибольшее распространение получили смесители периодического действия, которые в зависимости от типа рабочего органа подразделяются на смесители: с вращающимся корпусом, червячно-лопастные, с псевдоожижением сыпучего материала, центробежного действия с вращающимся конусом.
Смесители с вращающимся корпусом. К ним относятся барабанные смесители, применяемые для смешения сухих порошкообразных материалов. Барабанный смеситель (рис. 7.15) представляет собой цилиндрический корпус (1), вращающийся на опорных роликах (2) со скоростью 6—8 об/мин. Для лучшего смешивания материала на внутренних стенках барабана укреплены спиральные перегородки (3), а внутри него — несколько продольных полок (4) с перегородками. Барабанный смеситель является аппаратом периодического действия. Загрузка и выгрузка осуществляется с помощью шнека (5), который при загрузке вращается в одном направлении, а при выгрузке.
Смесители
Аппараты, в которых сыпучие материалы смешиваются между собой и с жидкостями называют смесителями.
Смесители классифицируют: по характеру процесса смешивания (конвективного или диффузионного), конструктивному признаку (барабанные смесители с вращающимся корпусом и червячно-лопастные), способу воздействия на смесь (гравитационные, центробежные), характеру протекающего в них процесса смешивания (периодический или непрерывный) и другим признакам.
По характеру протекающего процесса в отечественной химико-фармацевтической промышленности наибольшее распространение получили смесители периодического действия, которые в зависимости от типа рабочего органа подразделяются на смесители: с вращающимся корпусом, червячно-лопастные, с псевдоожижением сыпучего материала, центробежного действия с вращающимся конусом.
Смесители с вращающимся корпусом. К ним относятся барабанные смесители, применяемые для смешения сухих порошкообразных материалов. Барабанный смеситель (рис.5) представляет собой цилиндрический корпус (1), вращающийся на опорных роликах (2) со скоростью 6—8 об/мин. Для лучшего смешивания материала на внутренних стенках барабана укреплены спиральные перегородки (3), а внутри него — несколько продольных полок (4) с перегородками. Барабанный смеситель является аппаратом периодического действия. Загрузка и выгрузка осуществляется с помощью шнека (5), который призагрузке вращается в одном направлении, а при выгрузке в противоположном.
|
Рисунок 5.
Аппараты с псевдоожижением сыпучего материала. Данные смесители нашли широкое применение в таблеточном производстве. Они отличаются высокой эффективностью и малым временем смешивания, отсутствием вращающихся деталей, что обеспечивает высокую чистоту получаемого продукта. Кроме смешивания, в этих аппаратах выполняется ряд последующих технологических операций процесса приготовления таблеточной массы: гранулирование, сушка, опудри-вание.
Смесители центробежного действия с вращающимся конусом. В них достигается качественное смешивание сыпучих материалов при относительно небольшом расходе энергии, обусловленном малой длительностью смешивания и высокой производительностью единицы объема аппарата.
Гранулирование - процесс превращения порошкообразного материала в частицы (зерна) определенной величины – укрупнение с образованием формы и поверхности.
Назначение: • улучшение сыпучести таблетируемой массы; • предотвращение расслаивания многокомпонентной таблетируемой массы; • предотвращения слипания частиц различной величины и удельной плотности; • обеспечение равномерной скорости поступления таблетируемой массы в матрицу таблеточной машины. Виды грануляции: 1) влажная грануляция – осуществляется продавливанием влажных масс с последующим распылительным или контактным высушиванием; 2) сухая грануляция – размол до определенной величины с предварительным уплотнением (компактированием) или без него; 3) структурная грануляция (грануляциия в псевдоожиженном слое).
Влажная грануляция: порошки, имеющие недостаточную способность к сцеплению между частицами и плохую сыпучесть. Грануляторы (протирочные машины) - механизмы, с помощью которых осуществляется гранулирование протиранием масс через сито.
Рисунок 6.
Гранулятор для влажного гранулирования: 1-цилиндр с отверстиями; 2-протирающие лопасти; 3-электродвигатель; 4-коническая передача; 5-приемник для гранул.
Высушивание гранул в сушильных шкафах или сушилках псевдоожиженого слоя. Температура 30-60ºC, время сушки 20-60 мин, остаточная влажность в гранулах не должна превышать 2%.
|
• 1 – воздухозаборное устройство; • 2 - калорифер; • 3 – фильтр; • 4 – тележка; • 5 – продукт; • 6 – резервуар из оргстекла; • 7 – рукавный фильтр со встрях. устройством; • 8 - вентилятор; • 9 - шибер; • 10 – поток воздуха на выходе из сушилки; • 11 – электродвигатель; • 12 – стержневая рамка (снять электростат.эл-во).
Сухая грануляция
Метод сухого гранулирования включает следующие операции: • перемешивании порошка; • компактирование и сжатие в брикеты (плитки) 25-50 мм под высоким давлением в присутствии склеивающих веществ (МЦ, КМЦ, ПЭО); • размол массы в крупный порошок с помощью вальцов или мельницы «Эксцельсиор».
Грануляция размолом используется: • когда увлажненный материал реагирует с материалом при протирке (ЛВ разлагаются в присутствии воды; во время сушки вступают в хим. реакции; подвергаются физическим изменениям). • когда ЛВ обладает хорошей прессуемостью и для него не требуется дополнительного связывания частиц склеивающими веществами. 1 – емкость; 2 – вибросито; 3 – гранулятор; 4 – измельчитель ударного действия; 5 – регулирующее устройство; 6 – валковый пресс 7 – шнек; 8 – смеситель; 9 – трубопровод; 10 – сетка гранулятора; 11 – питатель.
Структурная грануляция - характерное воздействие на увлажненный материал, приводящее к образованию округлых, при соблюдении определенных условий - однородных гранул.
Способы структурной грануляции: 1) грануляция в дражировочном котле: Смесь порошков загружают при вращении котла со скоростью 30 об/мин, и увлажняют через форсунку раствором связывающего вещества. Частицы порошков слипаются между собой, высушиваются теплым воздухом и в результате трения приобретают приблизительно одинаковую форму. В конце процесса к высушиваемому грануляту добавляют скользящие вещества.
2) грануляция распылительным высушиванием: Готовят раствор (суспензию) из смеси ЛВ и ВВ и увлажнителя и подают их через форсунки в камеру распылительной сушилки, при 150 °С. Распыленные частицы быстро теряют влагу и образуют за несколько секунд сферические пористые гранулы, которые смешивают с ЛВ. Такие гранулы имеют хорошую сыпучесть и прессуемость.
3) гранулирование в условиях псевдоожижения. Образование и рост гранул в псевдоожиженном слое происходит за счет двух физических процессов: комкования при смачивании и слипания с последующей агломерацией. Обрабатываемый материал, и образующийся гранулят непрерывно находятся в движении. Все процессы — смешивание, увлажнение, грануляция, сушка и внесение опудривающих веществ — протекают в одном аппарате. Гранулят, полученный в псевдоожиженном слое, имеет ряд преимуществ: более сбалансированный фракционный состав, округлая форма гранул, лучшая сыпучесть.
Таблетирование
Прессование – это процесс образования таблеток из гранулированного или порошкообразного материала под действием давления (25-250 МПа).
Эксцентриковый таблеточный пресс EP-1 (таблетпресс) с одним пуансоном работает в полностью автоматическом режиме. Все компоненты хромированы, изготовлены из нержавеющей стали AISI 316 и из прозрачного акрилового материала (передняя дверца). Устройство таблетпресс работает в полностью автоматическом режиме, способно производить круглые таблетки и таблетки неправильной формы диаметром до 20 мм, имеет регулируемую глубину наполнения (до 15 мм) и настраиваемое сжимающее усилие (до 3 тонн, устройство оборудовано дисплеем, отображающим величину усилия). Максимальная производительность таблетпресса составляет 4000 ударов в час. Технические данные: Скорость пресса варьируется. Максимальный диаметр таблеток 20 мм. Максимальная глубина наполнения 17 мм. Максимальная сила компрессии 3 тонны. Максимальная производительность 40 000 таблеток в час. Вес нетто 135 кг. Длина/ширина/высота пресса (мм): 425/385/640. Длина/ширина/высота дополнительных частей (мм): 550/400/800. Блок питания 230 вольт/50-60 герц. Электрическая нагрузка 2,2 киловольт-ампер. Рис.7.
Рисунок 7.
Прямое прессование - это процесс прессования негранулированных порошков.
Преимущества: • позволяет исключить 4 технологические операции и, таким образом, сократить время производства; • позволяет понизить себестоимость продукта; • исключает разложение лекарственных веществ, возможное при влажном гранулировании под действием влаги и температуры; • снижает побочное действие лекарственных препаратов за счет снижения продуктов разложения; • повышает срок годности таблеток. • Используется для веществ, имеющих изометрическую форму частиц, приблизительно одинакового гранулометрического состава и, как правило, не содержащие большого количества мелких фракций (т. е. частиц размером менее 0,1 мм).
Например, натрия хлорид, калия иодид, бромкамфара и др. Направления обеспечения прямого прессования: • добавление вспомогательных веществ, улучшающих технологические свойства таблетируемого материала; • предварительная направленная кристаллизация лекарственных веществ; • принудительная подача таблетируемого материала из загрузочной воронки в матрицу. Причины брака и способы их устранения • перед прессованием любая таблеточная машина должна быть тщательно выверена и отрегулирована. • затем проводят пробное таблетирование, в результате которого добиваются необходимой массы таблеток, должной прочности и распадаемости, а также устранения внешних изъянов таблеток.
|
|
Историки об Елизавете Петровне: Елизавета попала между двумя встречными культурными течениями, воспитывалась среди новых европейских веяний и преданий...
Археология об основании Рима: Новые раскопки проясняют и такой острый дискуссионный вопрос, как дата самого возникновения Рима...
Механическое удерживание земляных масс: Механическое удерживание земляных масс на склоне обеспечивают контрфорсными сооружениями различных конструкций...
Типы оградительных сооружений в морском порту: По расположению оградительных сооружений в плане различают волноломы, обе оконечности...
© cyberpedia.su 2017-2024 - Не является автором материалов. Исключительное право сохранено за автором текста.
Если вы не хотите, чтобы данный материал был у нас на сайте, перейдите по ссылке: Нарушение авторских прав. Мы поможем в написании вашей работы!