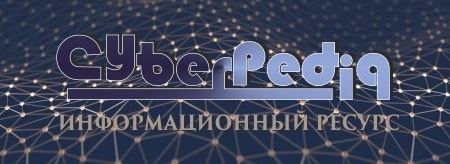
Архитектура электронного правительства: Единая архитектура – это методологический подход при создании системы управления государства, который строится...
Биохимия спиртового брожения: Основу технологии получения пива составляет спиртовое брожение, - при котором сахар превращается...
Топ:
Установка замедленного коксования: Чем выше температура и ниже давление, тем место разрыва углеродной цепи всё больше смещается к её концу и значительно возрастает...
Характеристика АТП и сварочно-жестяницкого участка: Транспорт в настоящее время является одной из важнейших отраслей народного хозяйства...
Интересное:
Влияние предпринимательской среды на эффективное функционирование предприятия: Предпринимательская среда – это совокупность внешних и внутренних факторов, оказывающих влияние на функционирование фирмы...
Что нужно делать при лейкемии: Прежде всего, необходимо выяснить, не страдаете ли вы каким-либо душевным недугом...
Принципы управления денежными потоками: одним из методов контроля за состоянием денежной наличности является...
Дисциплины:
![]() |
![]() |
5.00
из
|
Заказать работу |
Содержание книги
Поиск на нашем сайте
|
|
В процессе эксплуатации сварных изделий происходит старение материала, сопровождающееся износом и разрушением. Эти явления приводят к появлению неисправностей и отказов изделий.
Неисправность – это состояние сварного соединения, при котором оно не соответствует хотя бы одному требованию НТД. Изделие, характеризующееся неисправностью, можно эксплуатировать с учётом обеспечения постоянного контроля за его эксплуатацией.
Отказ – это полное нарушение работоспособности изделия, при котором дальнейшая его эксплуатация невозможна. Отказы могут быть постепенные и внезапные.
Постепенные отказы связаны с медленным (вязким) разрушением изделия, а внезапные отказы - с хрупким разрушением изделия.
Износ – изменение размеров, формы и состояния поверхности сварного соединения. При износе наблюдается углубление, увеличивается шероховатость поверхности и имеет место остаточная деформация поверхностного слоя (наклеп).
Среди сварных соединений наиболее склонны к износу сварные соединения, выполненные контактной сваркой.
Износ классифицируют на виды:
• механический износ, возникает в трущихся элементах;
•абразивный износ, возникает в результате попадания твёрдых частиц в зазор между трущимися элементами;
•коррозионный износ, возникает при наличии нагрузок и коррозионной среды;
•усталостный износ, возникает при переменных нагрузках.
Износ сопровождается разрушением и возникновением поверхностных микротрещин.
В сварных изделиях возникают также усталостные трещины, а также трещины, связанные с явлением ползучести.
Появление усталостных трещин связано в первую очередь с влиянием концентраторов напряжений (забоины, риски, резкие переходы от шва к основному металлу, от одной толщины к другой, наличие отверстий). При действии переменных нагрузок в наиболее слабом месте изделия, где возникают остаточные напряжения, превышающие предел выносливости, появляются микротрещины, развивающиеся в дальнейшем в усталостные трещины, которые приводят к внезапному разрушению соединения (отказу) без видимых пластических деформаций.
Большое влияние на усталость оказывает изменение температурных условий эксплуатации (теплосмены) и воздействие коррозионной среды.
При этом разрушение соединения происходит при значительно меньших напряжениях. Появление трещин ползучести связано с медленным нарастанием во времени пластической деформации материала при длительных механических воздействиях и нагреве.
Материалы и сварные соединения, работающие длительное время при высоких температурах, постепенно разрушаются при напряжениях значительно меньших предела текучести.
|
На появление трещин усталости и ползучести оказывает влияние низкая пластичность металла, наличие дефектов – несплошностей в сварном шве, а также структурные изменения, связанные с упрочнением и разупрочнением металла в процессе эксплуатации..
При эксплуатационном контроле важно фиксировать не только появление трещин, но и знать кинетику их развития во времени. Исследование кинетики развития трещин и разрушений является задачей технической диагностики сварного соединения.
Техническая диагностика – занимается установлением и изучением признаков, характеризующих техническое состояние изделий, для предсказания возможных отклонений контролируемых параметров (например, длина трещины или толщина изделия) за допустимые пределы, вследствие чего возникают внезапные отказы.
Техническая диагностика даёт возможность оценить продолжительность эксплуатации изделия, т.е. его долговечность при появлении дефектов. Методы технической диагностики применяют для рациональной организации контроля работоспособности сварных изделий в процессе эксплуатации. Методы технической диагностики разделяют на:
•экспериментальные;
•расчётные.
В расчётных методах определяют напряжённое состояние контролируемого сварного изделия при наличии дефектов. При этом выполняют моделирование состояния дефектного соединения с помощью компьютерной техники.
К экспериментальным методам исследования работоспособности дефектного соединения, относят механические испытание, например, испытания на хрупкость (трещиностойкость), используемое в механике разрушение, для оценки стойкости сварного соединения к хрупкому разрушению.
Испытания на хрупкость проводятся на сварных соединениях со статическим изгибом образца, у которого выполнен надрез, в вершине которого имеется искусственная усталостная трещина. Образец нагружают до момента быстрого (нестабильного) развития трещины. Затем по величине нагрузки и длине трещины рассчитывают коэффициент интенсивности напряжения:
|
КIC = σа √π lтр,
σа- максимальное (амплитудное) напряжение,
lтр- длина трещины, при которой начинается быстрый ее рост;
Этот коэффициент является главным критерием оценки хрупкости разрушения сварного соединения.
Если σ √ π l < КIC, где σ- напряжение в данный момент нагружения, а l – текущая длина трещины, то трещина не развивается и разрушение не наступает. Если σ √ π l > КIC,то трещина нестабильна, быстро развивается по длине и возникает хрупкое разрушение.
Испытания на хрупкость проводят для различных условий нагружения, что позволяет установить ресурс работы изделия и оценить вероятность возникновения отказа. Зная коэффициент интенсивности напряжения и предел текучести металла можно по приведенной формуле определить критическую величину трещины, превышение которой вызывает хрупкое разрушение сварного соединения.
Аналогичные коэффициенты можно определить не только при статических, но и динамических нагружениях.
Большую информацию по определению характера зон разрушения и связь её с дефектами и концентраторами дают методы фрактографии (методы анализа изломов).
По виду излома можно определить пластичность или хрупкость металла, или сварного изделия.
Пластичные вязкие металлы дают волокнистый (с выступами) серый излом с матовой поверхностью, т.к. характеризуются мелкозернистой структурой. Хрупкие материалы имеют блестящий, кристаллического вида излом, т.к. характеризуются крупнозернистой структурой. Для изучения макро- и микроизломов используют металлографические и электронные микроскопы.
По виду излома можно судить также о дефектах сварного шва:
•поры выглядят как округлые или вытянутые пустоты;
•горячие трещины имеют темную окисленную поверхность;
•холодные трещины имеют блестящую поверхность;
•металлические включения имеют вид пустот с острыми краями;
•оксидные пленки, например на алюминиевых сплавах, имеют волокнистый вид.
К экспериментальным методам технической диагностики относят также методы толщинометрии, структуроскопии и интроскопии, являющиеся методами неразрушающего контроля.
|
|
Индивидуальные и групповые автопоилки: для животных. Схемы и конструкции...
Механическое удерживание земляных масс: Механическое удерживание земляных масс на склоне обеспечивают контрфорсными сооружениями различных конструкций...
Своеобразие русской архитектуры: Основной материал – дерево – быстрота постройки, но недолговечность и необходимость деления...
Общие условия выбора системы дренажа: Система дренажа выбирается в зависимости от характера защищаемого...
© cyberpedia.su 2017-2024 - Не является автором материалов. Исключительное право сохранено за автором текста.
Если вы не хотите, чтобы данный материал был у нас на сайте, перейдите по ссылке: Нарушение авторских прав. Мы поможем в написании вашей работы!