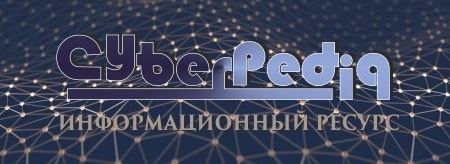
История развития пистолетов-пулеметов: Предпосылкой для возникновения пистолетов-пулеметов послужила давняя тенденция тяготения винтовок...
Опора деревянной одностоечной и способы укрепление угловых опор: Опоры ВЛ - конструкции, предназначенные для поддерживания проводов на необходимой высоте над землей, водой...
Топ:
Основы обеспечения единства измерений: Обеспечение единства измерений - деятельность метрологических служб, направленная на достижение...
Отражение на счетах бухгалтерского учета процесса приобретения: Процесс заготовления представляет систему экономических событий, включающих приобретение организацией у поставщиков сырья...
Генеалогическое древо Султанов Османской империи: Османские правители, вначале, будучи еще бейлербеями Анатолии, женились на дочерях византийских императоров...
Интересное:
Аура как энергетическое поле: многослойную ауру человека можно представить себе подобным...
Как мы говорим и как мы слушаем: общение можно сравнить с огромным зонтиком, под которым скрыто все...
Средства для ингаляционного наркоза: Наркоз наступает в результате вдыхания (ингаляции) средств, которое осуществляют или с помощью маски...
Дисциплины:
![]() |
![]() |
5.00
из
|
Заказать работу |
|
|
Толщина стенок и дна изделия оказывает влияние на: возникновение внутренних напряжений, являющихся причиной образования вздутий, коробления во время выдержке детали в матрице или пресс-форме.
Толщина стенки детали зависит от длины (высоты) стенки, текучести пластмассы, механической прочности материала, конфигурации элемента детали.
Соотношение между толщиной стенки и длиной детали должно иметь строго определенное значение, но устанавливают его окончательно с учетом других факторов. Влияние текучести материала особенно резко проявляется при использовании термореактивных пластмасс, текучесть которых значительно ниже текучести термопластов. Из пластмасс, обладающих низкой текучестью, можно получать изделия небольшой высоты с тонкими стенками, а из пластмасс, имеющих большую текучесть, высокие тонкостенные конструкции.
Толщину стенок можно уменьшить применением ребер жесткости или придания стенкам рациональных профилей.
Толщина стенок и дна изделий из пластмасс оказывает существенное влияние на возникновение напряжений в изделии, на точность изготовления и время выдержки при формовании, т. е. на эксплуатационные и технико-экономические показатели. Разнотолщинность изделий вызывает неравномерную усадку, являющуюся причиной образования вздутий, трещин и коробления. Значительная толщина стенки вызывает большую по величине усадку, также приводящую к короблению. Все это объясняется главным образом неравномерностью протекания процессов формования пластмассы в форме и охлаждения изделий после их извлечения из формы. Отсюда одно из главных условий наивысшей технологичности конструкции изделия- оно должно быть равнотолщинным. Реально это возможно нечасто, но конструктор изделия обязан всегда стремиться к достижению наименьшей разностенности; имеются проверенные опытом рекомендации допустимой разносторонности- 1:2 для изделий из термопластов и 1:3 для изделий из реактопластов, но они являются весьма ориентировочными.
|
Толщину стенок назначают, как правило, в зависимости от габаритных размеров, необходимой механической прочности изделия и текучести данной пластмассы. Минимальную толщину стенок можно выбирать в зависимости от высоты прессованного изделия или от длины пути потока расплава термопласта в форме (рис. 3).
Для изделий из пластмасс рекомендуют также следующие эмпирические формулы - для реактопластов и для термопластов соответственно:
;
,
где - наименьшая допускаемая толщина стенки, мм;
- текучесть пресс- материала по Рашигу, мм;
- предполагаемая высота стенки, мм;
- ударная вязкость пластмассы в Н·см/см2.
Идеальное условие — это равнотолщинное изделие, оно редко выполнимо и в общем случае считается, что разнотолщинность не должна превышать 30%.
Рис. 3. Определение минимальной толщины стенок изделий из пластмасс:
а – термореактивных; б – термопластичных: - высота изделия;
- толщина изделия;
- длина пути расплава теропласта
Рис. 4. Типовые сопряжения стенок:
а- лобовое; б – L-образное (угловое); в – Т-образное (тавровое); г – V-образное; д – вилкообразное; е – К-образное; ж – К-образное шахматное; з – Х-образное; и - крестообразное
Наиболее часто равнотолщинность нарушается в узлах-местах переходов от стенки к дну изделия, при пересечении стенок друг с другом или ребрами жесткости, ребер жесткости между собой - даже при одинаковых толщинах соединяющихся или пересекающихся элементов.
Это объясняется увеличением массы материала в узлах, из-за чего увеличивается вероятность появления дефектов: усадочных утяжек, микро- и макротрещин и т. д. На рис. 4 показаны возможные варианты сопряжения стенок одинаковых толщин.
|
На тонкостенных изделиях небольшая разнотолщинность, соизмеримая с точностью изготовления формы, часто отрицательно не проявляется, и отмеченное выше относится к изделиям относительно толстостенным, на которых дефекты становятся заметными.
Слишком тонкие стенки вызывают значительные трудности при изготовлении изделий. Опыт показывает, что возможно получить в серийном производстве изделий из пресс-порошков с диаметральными размерами до 50 мм и высотой до 10 мм толщины стенок до 0,5 мм; такие же и меньшие (до 0,3 мм) - при пресс-литье малогабаритных изделий из волокнистых пресс-материалов типа АГ-4 и литье под прессования минимальная толщина стенок должна составлять 4- 6 мм.
Вопрос назначения оптимальных толщин стенок связан не только с конструкционной целесообразностью, но и с технологическими возможностями. Необходимо предусматривать опасности незаполнения расплавом узких щелей в полости формы, например при литье под давлением располагать впускные каналы для расплава в соответствующих тонкостенных участках и учитывать повышение вязкости расплава за счет его саморазогрева; с другой стороны, и утолщенные участки требуется лучше подпитывать для компенсации дефицита массы, возникающего при охлаждении расплава, усадке его.
Минимальная толщина стенок для термопластов: ПП, ПЭ — минимум 0,5 мм; ПА — 0,7 мм; ПС, АБС-пластик — 0,75 мм; ПВХ — 1 мм.
Максимальная толщина стенок и дна, для штучных изделий, рекомендуется не более 4–5 мм, для реактопластов — до 50 мм. Оптимальная толщина стенок для реактопластов — 1–4 мм, для малогабаритных изделий — 0,5 мм.
По конструктивным соображениям стенки утолщают в следующих случаях:
- при наличии отверстий (рис. 5,а);
- при конструировании деталей с резьбой (рис. 5, б);
- для увеличения прочности элементов деталей, работающих в абразивной среде (рис. 5, в);
- при проектировании ступиц шкивов и зубчатых колес необходимо предусматривать прилив над местом расположения шпоночной канавки для компенсации местного ослабления детали (рис. 5, г);
- для увеличения сопрягаемых поверхностей (рис. 5, д);
- при конструировании деталей с рифлением (рис. 5, е);
- при проектировании армированных деталей; для создания вокруг арматуры стенок соответствующей толщины (рис. 5, ж).
Рис. 5. Примеры утолщения стенок по конструктивным соображениям:
|
а – колпачок (пресс-материал СП1-342-02); б – корпус шифона (ПЭВД); в – ковш ленточноного элеватора (волокнит); г – ступица шкива; д – колено (капрон); е – маховик (пресс материал 01-040-02); ж – каркас катушки (текстолитовая крошка)
Ребра жесткости
Для увеличения жесткости и прочности пластмассовых деталей, усиления особо нагруженных мест или выступающих частей, а иногда по технологическим соображениям рекомендуется предусматривать в конструкции детали ребра жесткости.
Ребра жесткости позволяют уменьшить сечения отдельных элементов детали, снизить внутренние напряжения в местах сопряжения стенок различного сечения, а также способствуют предотвращению коробления или брака по трещинам. В зависимости от назначения ребра жесткости подразделяют на следующие виды:
– усиливающие – они служат для увеличения прочности детали в определенных сечениях, уменьшения напряжений, особенно в тонкостенных деталях;
– разводящие – эти ребра воспринимают сосредоточенные нагрузки и переносят их рассредоточено на большую площадь стенки детали (например, ребра крышки золотника, находящегося в масляной среде и подвергающегося динамической нагрузке);
– обеспечивающие равностенность детали;
– конструктивные – имеющие целевое назначение (например, крыльчатка насоса, лопасти которой служат основными эксплуатационными элементами);
- технологические – применяемые в зависимости от технологического процесса изготовления пластмассовой детали (например, ребра применяемые для устранения коробления детали, облегчения извлечения детали из формы, уменьшения времени выдержки детали в форме).
Толщина ребер жесткости всегда является частью от толщины стенки S. Ее значение составляет: для ПЭ, ПП - (0,3-0,6)S; для ПА - (0,15- 0,35)S; для ПС и ПК -0,5 S. Рекомендуемая высота ребер при отсутствии конструктивной необходимости — до (3-5)S. Ребро жесткости ориентируется по направлению течения расплава в форме.
Наиболее часто на практике встречается форма ребра жесткости в виде усеченного конуса с закругленной вершиной и плавным переходом от стенки ребра к изделию. Если выталкивание изделий из формы осуществляется по ребру жесткости (для чего особенно часто используют ребра по внутренней поверхности), то следует иметь в точках выталкивания местные небольшие утолщения с плоской вершиной. Высота ребер определяется их числом и конструкцией изделия: у плоских изделий она обычно равна удвоенной ширине его у основания. Высота внутренних ребер должна быть не менее чем на 0,5 мм меньше общей высоты изделия. Это делается для упрощения последующей механической обработки поверхности, а также для того, чтобы облегчить монтаж или сборку изделий.
|
При конструировании изделий с ребрами жесткости следует либо вообще избегать замкнутых контуров, либо стремиться к тому, чтобы периметр замкнутых контуров ребер жесткости был по возможности минимальным, так как пластмасса, находящаяся внутри контура, не имеет возможности свободно усаживаться, что приводит (особенно при малой толщине стенок) к появлению трещин.
При конструировании пластмассовых деталей с ребрами жесткости необходимо принимать во внимание следующие рекомендации.
Ребра жесткости не должны быть толще стенки детали или ее элемента, к которому примыкают. Оптимальная толщина ребер жесткости не должна превышать 0,6 – 0,8 толщины сопрягаемой стенки (рис. 6). При большей толщине ребер возможно появление трещин в местах скопления массы на стыке ребра жесткости со стенкой.
Сечение ребер жесткости должно иметь треугольную или трапецеидальную форму с закругленной вершиной и плавными переходами к основаниями (рис. 7).
Ребра жесткости не должны доходить до опорной поверхности или до края примыкающего к нему элемента на 0,5 – 1,0 мм. Это гарантирует от выхода ребра за пределы опорной поверхности при формообразовании и допускает незначительные деформации поверхности детали, которая усилена этими ребрами. Кроме того, желательно, чтобы ребра жесткости примыкали к опорной поверхности плавно (рис. 8). Ребра жесткости рекомендуется располагать на прямых участках элементов детали (рис. 9).
Необходимо стремиться к диагональному или диаметральному расположению ребер жесткости. Предпочтение таким ребрам следует отдавать и по технологическим соображениям, так как при производстве деталей значительно уменьшается коробление стенок и днищ (рис. 10). В случае примыкания к стенке нескольких ребер жесткости их следует располагать в шахматном порядке (рис. 11).
Рис. 6 Пример оформления ребер жесткости на детали
Рис. 7. Рекомендуемые соотношения элементов ребер жесткости
Ребра жесткости, которые служат для укрепления элементов деталей (муфт, втулок, фланцев), рекомендуется размещать симметрично оси детали во избежание ее коробления. Форма ребер жесткости должна обеспечивать их свободную деформацию при усадке пластмассы во время затвердевания.
|
![]() | ![]() |
Рис. 8. Пример оформления ребер жесткости | Рис. 9. Пример оформления ребер жесткости |
![]() | ![]() |
Рис. 10. Примеры расположения ребер жесткости | Рис. 11. Примеры расположения ребер жесткости (![]() |
Ребрам жесткости придают наибольший допустимый технологический уклон и располагают их в плоскости разъема пресс-формы или перпендикулярно к ней (рис. 12). Исходя из конструкционных свойств пластмасс ребра жесткости, если позволяет их конструкция, желательно располагать так, чтобы они работали на сжатие, а не на растяжение (рис. 13).
![]() | ![]() |
Рис. 12. Расположение ребер жесткости с учетом плоскости разъема пресс-формы | Рис. 13. Расположение ребер жесткости с учетом приложения нагрузки |
Для увеличения жесткости крышек, днищ крупногабаритных изделий, боковых стенок, если допустимо конструктивно, применяют мелкие ребра - нервюры (рис. 14).
Рис. 14. Применение мелких ребер жесткости - нервюр
Нервюры представляют собой невысокие, обычно профилированные валики различного сечения, служащие для усиления гладких поверхностей изделия. Нервюры могут быть самой разнообразной формы. На рис. 15 изображены наиболее распространенные формы нервюр, применяемые в изделиях из пластмасс. Для изделий из термопластичных пластмасс следует по возможности применять нервюры, показанные на рис. 15, а. Каждая нервюра на всем своем протяжении должна иметь не изменяющиеся в сечении форму и высоту, за исключением концов, где делается плавный сбег (рис. 16). Ширина нервюр составляет 1-1,5 толщины стенки. Высота нервюр обычно находится в пределах 0,5-1 их ширины.
![]() | ![]() |
Рис. 15. Нервюры наиболее распространенных форм: а-б - виды нервюр | Рис. 16. Варианты сбега нервюр |
Нервюры выполняют с наружной и с внутренней стороны изделия, но только с тем условием, чтобы они не были помехой при извлечении изделия из формы
Не рекомендуется предусматривать нервюры только с одной стороны изделия, так как это может послужить причиной его деформации. Нервюры, как правило, располагают симметрично одну против другой.
Зиги являются своеобразной разновидностью ребер жесткости. Они применяются, как правило, в тарных емкостях, например в канистрах, для увеличения жесткости стенок. Зиги – это гребнеобразные округлой конфигурации выступы образованные изгибом стенки изделия без изменения ее толщины (рис. 17). Зиги могут быть одиночными (рис. 17, а) и пересекающимися (рис. 17, б), располагаться на стенке гребнями вовнутрь и наружу. Чаще встречается первый вариант, так как в этом случае не затрудняется извлечение изделия из раскрытой формы.
Рис. 17. Зиги, схема устройства:
а – одиночные, б – пересекающиеся
Утолщения, бобышки, приливы служат для создания необходимых при соединении нескольких деталей опорных поверхностей, для размещения гладких и резьбовых отверстий, установки арматуры, для реализации других конструктивных особенностей (проушины, петли, крюки, борты). Основное требование к перечисленным элементам – плавность геометрических переходов между сопрягаемыми поверхностями, что достигается подбором закруглений, уклонов, ребер, рациональных конфигураций элементов изделия при минимальном отклонении от равнотолщинности (рис. 18).
Бобышки не должны сливаться со стенками изделий, но должны сопрягаться с ними ребрами; над торцевой поверхностью изделия они выступают на величину до 0,5 мм.
Приливы, как правило, играют роль опорных поверхностей, декоративных и функциональных буртиков. Необходимо стремиться к уменьшению непрерывной длины приливов, заменяя ее прерывистой.
Утолщения используют для размещения отверстий, а также в качестве технологических выступов для упора в них толкателей, особенно применительно к тонкостенным изделиям сложной конфигурации.
Рис. 18. Схемы устройства бобышек, приливов, утолщений
Тема 1.3 (продолжение)
|
|
Индивидуальные очистные сооружения: К классу индивидуальных очистных сооружений относят сооружения, пропускная способность которых...
Наброски и зарисовки растений, плодов, цветов: Освоить конструктивное построение структуры дерева через зарисовки отдельных деревьев, группы деревьев...
Эмиссия газов от очистных сооружений канализации: В последние годы внимание мирового сообщества сосредоточено на экологических проблемах...
Индивидуальные и групповые автопоилки: для животных. Схемы и конструкции...
© cyberpedia.su 2017-2024 - Не является автором материалов. Исключительное право сохранено за автором текста.
Если вы не хотите, чтобы данный материал был у нас на сайте, перейдите по ссылке: Нарушение авторских прав. Мы поможем в написании вашей работы!