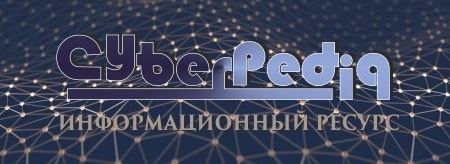
Опора деревянной одностоечной и способы укрепление угловых опор: Опоры ВЛ - конструкции, предназначенные для поддерживания проводов на необходимой высоте над землей, водой...
Эмиссия газов от очистных сооружений канализации: В последние годы внимание мирового сообщества сосредоточено на экологических проблемах...
Топ:
История развития методов оптимизации: теорема Куна-Таккера, метод Лагранжа, роль выпуклости в оптимизации...
Марксистская теория происхождения государства: По мнению Маркса и Энгельса, в основе развития общества, происходящих в нем изменений лежит...
Оценка эффективности инструментов коммуникационной политики: Внешние коммуникации - обмен информацией между организацией и её внешней средой...
Интересное:
Мероприятия для защиты от морозного пучения грунтов: Инженерная защита от морозного (криогенного) пучения грунтов необходима для легких малоэтажных зданий и других сооружений...
Уполаживание и террасирование склонов: Если глубина оврага более 5 м необходимо устройство берм. Варианты использования оврагов для градостроительных целей...
Как мы говорим и как мы слушаем: общение можно сравнить с огромным зонтиком, под которым скрыто все...
Дисциплины:
![]() |
![]() |
5.00
из
|
Заказать работу |
|
|
Путей сообщения Императора Николая II»
Институт транспортной техники и систем управления
Кафедра технологии транспортного машиностроения
И ремонта подвижного состава
С.В. РОГОВОЙ
ТЕХНОЛОГИЧЕСКОЕ ОБОРУДОВАНИЕ ПРОИЗВОДСТВА ПО КАПИТАЛЬНОМУ РЕМОНТУ ТЯГОВЫХ ЭЛЕКТРИЧЕСКИХ МАШИН
Учебное пособие
Москва – 2016
Федеральное государственное бюджетное образовательное учреждение высшего образования
«Московский государственный университет
Путей сообщения Императора Николая II»
Институт транспортной техники и систем управления
Кафедра технологии транспортного машиностроения
И ремонта подвижного состава
С.В. РОГОВОЙ
ТЕХНОЛОГИЧЕСКОЕ ОБОРУДОВАНИЕ ПРОИЗВОДСТВА ПО КАПИТАЛЬНОМУ РЕМОНТУ ТЯГОВЫХ ЭЛЕКТРИЧЕСКИХ МАШИН
Рекомендовано редакционно-издательским
советом университета в качестве
Учебного пособия
для студентов специальности
Технология
Машиностроения»
Москва - 2016
УДК 629.05;621.9 - 05
Р –59
РОГОВОЙ С.В. Технологическое оборудование производства по капитальному ремонту тяговых электрических машин: Учебное пособие. – М.: МГУПС (МИИТ), 2016. - с.
Учебное пособие содержит изложение основных особенностей технологического оборудования по капитальному ремонту тягового подвижного состава. Приведены возможные варианты выбора оборудования в зависимости от параметров технологического процесса. Показаны основные направления развития и совершенствования технологии и технологического оборудования. Пособие может быть использовано при выполнении курсового и дипломного проектирования.
|
Рецензенты:
© МГУПС (МИИТ), 2016
ОГЛАВЛЕНИЕ
Введение…………………………………………………………. | |
1. Особенности производства по ремонту тяговых электрических машин………………………………………… | |
2. Общая характеристика маршрутной технологии электромашинного производства…………………………… | |
3. Оборудование, применяемое при ремонте остовов | |
4. Оборудование для разборки якорей | |
4.1. Снятие бандажей…………………………………… | |
4.2. Снятие пазовых клиньев…………………………………… | |
4.3. Удаления обмотки из пазов………………………………. | |
4.4. Разборка якорей с применением метода гидролитической деструкции…………………………………………………… | |
5. Изготовление и ремонт коллекторов…………………… | |
5.1. Особенности конструкции коллекторов………………… | |
5.2 Сборка пакета пластин……………………………………… | |
5.3. Динамическая формовка коллектора……………………… | |
6. Соединение обмотки с коллектором……………………… | |
6.1 Пайка в паяльной ванне оловянисто-свинцовыми припоями............................................................................ | |
6.2. Высокочастотная пайка твердыми припоями…………… | |
6.3. Метод сварки обмотки неплавящимся электродом в среде инертного газа…………………………………………… | |
7. Оборудование для сушильно-пропиточных работ……… | |
7.1. Общая характеристика технологических процессов…….. | |
7.2. Автоклавы…………………………………………………… | |
7.3. Пульты управления………………………………………… | |
7.4. Вакуум насосы……………………………………………… | |
7.5. Система аварийного слива………………………………… | |
7.6. Сушильные печи…………………………………………… | |
8. Оборудование участка отделки якорей………………… | |
8.1. Обточка коллектора………………………………………… | |
8.2. Продорожка коллектора и снятие фасок………………… | |
8.3. Динамическая балансировка якорей……………………… | |
9. Оборудование для испытания тяговых электрических машин………………………………………………………… | |
10. Перспективы развития технологии и технологического оборудования для ремонта | |
Список рекомендуемой литературы………………………… |
|
ВВЕДЕНИЕ
Существенную часть в общем объеме производства по ремонту подвижного состава составляет производства ремонта тяговых электрических машин. Эта величина на разных заводах по ремонту подвижного состава может составлять от 30 до 60 % себестоимости продукции.
Специфичность электромашинного производства заключается в одновременном применении в общем технологическом маршруте технологий и оборудования связанного с химическими, термическими процессами, а так же с механической обработкой и сборкой.
Рассматривается в основном оборудование наиболее специфичное для технологии электрических машин и определяющее технологический уровень производства, а также уровень качества выпускаемой продукции.
Настоящее учебное пособие является логическим продолжением ранее выпущенных кафедрой «Технология транспортного машиностроения и ремонта подвижного состава» учебных пособий в которых рассматривались методы и средства очистки деталей подвижного состава, применения специальных металлорежущих станков, модернизации существующего оборудования, методики определения критериев по выбору технологического оборудования.
Рис.1 Основная структура электромашинного производства
Рис. 3 Схема технологических маршрутов катушечно-секционного производства
Якорное производство
После проведения дефектировки и определения объема ремонта якоря предназначенные к ремонту КР2 со сменой изоляции поступают на позиции разборки.
На токарно-винторезном станке отрезным резцом отрезаются концы секций якоря непосредственно перед пластинами коллектора.
Бандажи разрезаются электрической дугой при помощи специального приспособления для закрепления электрода.
Пазовые клинья удаляются из якоря на специальной установке с гидравлическим приводом, либо на специально приспособленном поперечно-строгальном станке.
Собственно обмотка из пазов удаляется на специальной центробежной установке.
При ремонте якорей выполненных с изоляцией на эпоксидных компаундах в специальных автоклавах производится обработка якорей методом гидролитической деструкции.
|
Ремонт коллекторов
При помощи гидравлического пресса с якоря демонтируется коллектор. Ремонт коллекторов тепловозных электромашин ведется по состоянию. Коллектора электровозных тяговых электрических машин разбираются в обязательном порядке.
По состоянию меняются собственно коллекторные пластины. Изолирующие пластины коллектора и миканитовые манжеты, миканитовые конусы заменяются на новые, независимо от состояния. Пакеты медных и изолирующих пластин собираются на специальных градационных шайбах. Собранный пакет фиксируется специальным хомутом.
После чего выполняется расточка «ласточкиного хвоста» с обеих сторон пакета. На паз «ласточкиного хвоста» устанавливаются изолирующие миканитовые манжеты. Соединяются в единый сборочный узел пакет с манжетами, нажимный конуса и закрепляются коллекторными болтами.
После этого выполняются неоднократные технологические циклы динамической формовки коллектора. Циклы состоят из нагрева коллектора, разгон до частоты вращения в два раза превышающей номинальную частоту вращения якоря, затяжки коллекторных болтов.
Выполняется статическая балансировка коллектора.
Сердечник и вал якоря.
Вал при необходимости восстанавливают наплавкой, либо заменяют на новый.
Пластины сердечника якоря при необходимости заменяют новым пакетом. После запрессовки пакета пазы сердечника якоря калибруют протяжкой. Готовый сердечник покрываются лаком БТ-99 либо ФЛ-03К.
Укладка обмотки
Пазы якоря выстилаются изолирующим материалом типа «Изофлекс» или аналогичным. Укладываются якорные катушки обмотки якоря (секции). Производится их осадка в пазу на специальных установках. Окончательно обмотка в пазу фиксируется установкой пазовых клиньев.
На якоре формируют бандаж намоткой специальной стеклобандажной ленты. При этом контролируются требуемая величина натяга ленты и гемотрические размеры бандажа.
Выполняется соединение обмотки якоря с коллектором, В зависимости от конструктивных особенностей это мажет быть пайка в ванной свинцовисто-оловянным припоем, пайкой на установке ТВЧ серебросодержащим припоем, или сваркой неплавящимся электродом (W) в среде инертного газа (He).
|
Сушильно-пропиточное отделение
На этом участке осуществляется вакуум-нагнетательная пропитка якорей и полюсных катушек лаком или компаундом. После пропитки в циркуляционных печах осуществляется технологические циклы сушки, запечки или полимеризации, в зависимости от материалов входящих в систему изоляции. От этого также зависит количество циклов, их продолжительность и температурные параметры процесса.
На этом же участки на якоря наносят покровную эмаль.
Участок отделки
После выполнения работ по окончательному формированию изоляционной системы якорей, они из сушильно-пропиточного отделения поступают на участок отделки, где выполняются все финишные операции, осуществляется приемка якорей, как готового изделия.
Это обточка коллектора. Фрезеровка ламелей и снятие фасок. Динамическая балансировка якоря.
С участка отделки якорь передается на сборку электрических машин.
![]() |
Рис. 4 Структурная схема технологического маршрута ремонта якоря
Рис.5.Автомат для наплавки цилиндрических поверхностей остовов
1. Колона. 2. Пульт управления. 3. Управление подачей проволоки. 4. Механизм подачи сварочной проволоки. 5.Рабочий орган (мундштук). 6 Источник сварочного тока.
После наплавки производится механическая обработка фрезерованием до чертежных размеров.
Горловина установки подшипниковых щитов (якорная горловина).
Замеры производятся одновременно с проверкой резьбовых отверстий крепления подшипникового щита. Проверяется, как состояние резьбы (износ, повреждения ниток) так и соосность окружности, которая проходит через оси отверстий с посадочной поверхностью установки щита.
В случае отклонений превышающих ремонтные допуски, одновременно производится наплавка посадочной поверхности горловины и полная заварка резьбовых отверстий с полным заполнением металла на всю глубину.
Остов устанавливается на стол горизонтально-расточного станка. Базирование осуществляется по оси моторно-осевой горловины и линии соединяющей оси моторно-осевой и якорной горловины, так называемая централь. При этом централь должна быть параллельной поверхности стола станка, то есть размещаться строго горизонтально.
Перемещением стола или передней бабки станка от оси моторно-осевой горловины на расстояние равное чертежному размеру централи. Например, для большинства тепловозных ТЭД централь равна – 468,8 мм. Расточка осуществляется с помощью борштанги установленной в люнетах, или суппорта планшайбы передней бабки, сосной шпинделю.
|
Такая схема базирования гарантирует, что оси якорной и моторно-осевой горловин сосны и находятся в одной плоскости, а расстояние между осями соответствует чертежному размеру централи. Соответственно будет обеспечено отсутствие перекоса в тяговой зубчатой передаче и совпадение делительных окружностей ведущей шестерни и ведомого зубчатого колеса.
Существует мнение, согласно которому расточку остовов на горизонтально-расточном станке можно производить только борштангой с использование стойки. Иначе достичь чертежных требований параллельности и размещения в одной плоскости горловин остовов двигателя невозможно
Но как показывает практика при грамотном технологическом подходе можно достигать требуемой точности и без применения борштанги и задней стойки. Для этого необходимо соблюдение следующих условий:
- горизонтально-расточной станок должен быть оснащен поворотным столом;
- стол должен иметь систему оптического контроля угла поворота;
- состояние подшипников шпиндельного узла должно обеспечивать величину биения шпинделя не более 0,05мм (при полном вылете)
Рис. 6 Расточка остовов ТЭД на горизонтально расточном станке
Отличительной особенностью конструкции остовов тяговых электродвигателей отсутствие плоских поверхностей, которые можно было бы использовать в качестве технологической базы. В процессе механической обработки при изготовлении новых ТЭД на электромашиностроительных предприятиях расточка горловин осуществляется одновременно двумя борштангами специальными двухшпиндельными станками. И поэтому единственной базой является централь. Этим также объясняется отсутствие ремонтного допуска на изменение межосевого расстояния, как и тем, что централь является и межосевым размером зубчатого зацепления. Таким образом, процесс технологического базирования является многоступенчатым и носит косвенный характер. Это вызывает увеличение вспомогательного технологического времени затраченного на установку и базирование остова на станке.
В начале 80-х годов на остовах тяговых электродвигателях ЭД118Б по требованию МПС предприняты попытки создания дополнительных технологических баз для ремонтных нужд. Эти базы представляют собой приливы на верхней части остова в виде паралепипеда с фрезерованной верхней плоскостью. Но это не упростило задач технологического базирования и обеспечения точности ремонтного процесса.
В середине 80-х годов НПО станкостроения г. Иваново разработаны и изготовлены для электромашинного производства специальные расточные станки ИР-375. В его конструкции базирования остовов осуществляется не на столе станка, а на специальных приспособлениях – спутниках, входящих в комплект поставки станка. Спутник представляет собой точно изготовленную плиту. Плита оборудована всем необходимым для базирования, фиксации и крепления остова. На спутнике линия централи устанавливается горизонтально, то есть параллельно поверхности спутника. Спутник вместе с закрепленным остовом устанавливается на стол станка и фиксируется в одном из крайних положений. Крайние положения остова точно соответствуют положению, при которых ось шпинделей станка совпадает с осью той или иной горловины. Шпиндели станка, расположенные с двух противоположных сторон остова, оборудованы суппортами установки резцов для расточки моторно-осевой и якорной горловин, а также обработки их торцевых поверхностей. Фиксированный размер перемещения из одного крайнего положения спутника в другое строго соответствует размеру централи.
В случае износа отверстий или повреждения резьбы они заплавляются электродуговой сваркой с использованием порошковой проволоки или в среде углекислого газа. После расточки остов устанавливается с вертикальным направлением осей горловин. Производится сверление отверстий и нарезание резьбы. Сверление осуществляется при помощи кондуктора, который базируется на внутренней цилиндрической поверхности якорной горловины. Обычно используется радиально сверлильный станок 2М55 или 2К555.
Снятие бандажей
С якорей срезают бандажи. Для того чтобы снять бандаж выполненный из полимерных материалов армированных стеклянными нитями, и представляющий собой, по сути, предварительно напряженную конструкцию. Для снятия достаточно разрушить ее целостность в каком-нибудь одном поперечном сечении.
Для этого на бандаж устанавливается специальное приспособление. Данное приспособление состоит из внешнего кольца и внутреннего электрода, к которым подводится напряжение от сварочного генератора или трансформатора.
Электрическая дуга выжигает полимерный материал бандажа. Тонкие стеклянные нити при отсутствии полимерного наполнителя и при воздействии электрической дуги становятся ломкими и легко разрушаются при обычном механическом воздействии. После нарушения целостности бандажа в данном сечении, он легко снимается в виде разрезанного кольца.
Снятие пазовых клиньев
При небольшой производственной программе на ряде предприятий снятие пазовых клиньев выполняется вручную. Якорь, предварительно пропаренный и разогретый в ванне, устанавливается на опорах. Специально заправленным инструментом – оправкой, при помощи ударов малой кувалды по очереди выбивается каждый клин в отдельности.
С целью улучшения условий труда и повышения производительности данной технологической операции применяется специальное оборудование, выполненное в различных вариантах.
Первый вариант: использование поперечно- строгального станка.
Со станка снимается стол с механизмом поперечной подачи. По оси станка устанавливается механизм вращения якоря. В суппорт станка на место резца устанавливается специальный упор. Движением ползуна клин удаляется из якорного паза за один ход станка.
Второй вариант: специальная установка с гидравлическим рабочим механизмом.
Установка представляет собой силовой цилиндр с гидростанцией и системой управления. Якорь устанавливается в центра с электроприводом. Автоматика управления синхронизирует поворот якоря на один паза и рабочий ход цилиндра. Синхронизация осуществляется следящей системой оборудованной датчиками.
Удаление обмотки из пазов
Первоначально выполняется отделение обмотки от коллектора. Отделение обмотки от коллектора выполняется разными способами в зависимости от конструктивных особенностей якоря.
Первый вариант.
Обмотка якоря соединена с коллектором пайкой твердыми припоями (ПСр2.5).
В этом случае с помощью высокочастотных установок для пайки производится распайка коллектора, то есть операция обратная пайке.
На ряде заводов для этой цели используются установки с источниками питания ВЧИ-70, ВЧГ -100
Второй вариант
Обмотка якоря соединена с коллектором сваркой.
Якорь устанавливается в центра токарно-винторезного станка. Резцом протачивается торцевая поверхность петушков коллектора. При этом снимаемый слой металла должен соответствовать глубине провара сварного соединения. (1,5-2,0мм).
При этом неизбежно уменьшается ширина петушков коллектора. Чертежный размер петушка составляет 30 мм, а предельный размер ремонтного допуска после КР2 составлял 16 мм, а впоследствии был согласован до 10мм.
Собственно удаление обмотки осуществляется в специальной центробежной установке. Конструктивно установка выполнена следующим образом.
Корпус, представляющий собой цилиндр с толщиной стенок не менее 15мм, заглублен в массивный железобетонный фундамент не менее чем на 85-95% своей высоты. В нижней части корпуса закреплена опора, состоящая из корпуса, втулки установленной на упорный подшипник. Втулка клиноременной передачей соединена с приводным двигателем, расположенным в приямке. В верхней части корпуса имеется массивная крышка. В крышке для центровки якоря встроено прижимное устройство с упорным подшипником, ходовым винтом и приводным маховиком. Крышка оборудована запорным устройством.
Якорь конусом со стороны противоположной коллектору устанавливается на нижнюю опору. Крышка закрывается и вращением маховика якорь центруется в установке. Крышка запирается. Включается привод двигателя. Обычно время технологического цикла составляет одну- две минуты. Под действием центробежной силы обмотка выходит из пазов со стороны коллектора. Задние части якорных секций будучи связанными между собой за счет перегибов в лобовых частях опираются на заднюю нажимную шайбу. Якорь извлекается из установки. Обмотка снимается вручную.
Размеры установки, ее узлов и деталей, типы подшипников могут варьироваться в зависимости от размеров и массы якорей различных электрических машин.
Рис.7. Автоклав для гидролитической деструкции
Оборудование представляет собой автоклав горизонтального исполнения. В автоклав загружают два якоря. Закрывают крышку автоклава и заполняют внутренний объем насыщенные углекислым газом. После наполнения, автоклав герметизируют. Включают систему подогрева автоклава и систему подачи газа СО2 под давлением около 4 кгс/см2, для дальнейшего насыщения воды углекислым газом. Температурный режим устанавливают максимально возможный для существующей магистрали системы подачи технологического пара. На практике это обычно составляет 150-200С. Технологическое время цикла обычно составляет не больше 8 часов.
В результате воздействия углекислого газа в среде воды высокой температуры и воздействия внешнего давления на жидкость все неметаллические узлы, детали и сборочные единицы изоляционной системы якоря реструктуризируются в мелкодисперсную суспензию. После окончания цикла вода насыщенная СО2, окачивается в рабочую емкость, где осуществляется отделение от нее суспензии. Остатки суспензии легко смывается с поверхности якоря и всех внутренних его полостей струей воды.
1 — бак оборотного водоснабжения; 2 - баллон с углекислотой; 3 - автоклав; 4 — индукционный обогрев; 5 — насос
Рис. 8 Технологическая схема установки для гидролитической деструкции изоляции "Монолит"
Применение метода гидролитической деструкции и соответствующего технологического оборудования весьма эффективно
- абсолютно экологически чистая технология, исключающая применение агрессивных веществ и необходимость нейтрализации отходов
- возможность исключения в производственном цикле технологических операций снятия бандажей, удаления пазовых клиньев, удаления обмотки из пазов с применением с применением больших силовых усилий;
- исключения необходимости в соответствующем технологическом оборудовании.
Данная технология была внедрена лабораторией Всероссийского института электроизоляционных материалов на Улан-Удэнском локомотиво-вагоноремонтном заводе.
Рис. 9 Общее устройство коллектора арочной конструкции
Арочная конструкция коллектора образована двумя нажимными конусами. Стянутые коллекторными болтами, конуса сжимают и фиксируют между собой пакет коллекторных пластин медных и выполненных из изоляционного материала. Чаще всего в качестве изоляционного материала используется прокладочный миканит. В последнее время все чаще применяется различные слюдопласты. Пакет пластин своими упорами, выполненными в конфигурации «ласточкиного хвоста» упирается в соответствующие пазы нажимных коллекторных конусов. Пакет пластин и конуса разделяются между собой изолирующими манжетами. Изолирующие манжеты выполняются из формовочного миканита запеканием в пресс-форме под давлением.
Сборка пакета пластин
Медные пластины коллектора, полученные штамповкой из специального проката конического сечения, с выполненной фрезеровкой пазов в петушке устанавливают на градационной шайбе. Каждая медная пластина отделяется от соседних пластин изолирующей пластиной из миканита. Весь пакет фиксируется и закрепляется технологическим хомутом с соответствующим креплением.
Пакет собирается совместно с конусами, изолирующими манжетами, и изоляцией конуса. После этого устанавливается комплект коллекторных болтов и производится их затяжка. Собранный коллектор устанавливается в печь и производится первоначальный нагрев до 130-150 С в зависимости от класса изоляции.
В процессе нагрева происходит первоначальная усадка пластин и манжет из миканита. За счет температурного расширения медных пластин происходит их притирка к соседним пластинам. Определяется первоначально позиционирование пластин в пакете. Опрессовка пакета медных и миканитовых пластин осуществляется на зонтичном прессе
1. Гидравлические цилиндры. 2. Опорная плита. 3. Прижимная плита. 4. Направляющая колона
Рис.10. Общий вид зонтичного пресса
На рисунке коллектор не показан. Конструктивно пресс выполнен по вертикальной схеме. Рабочее усилие осуществляется несколькими гидравлическими цилиндрами, равномерно распределенными по окружности. Усилие передается на нижнюю плиту. В свою очередь нижняя плита прижимает через шток верхнюю плиту с коллектором к рабочему столу. В верхней плите выполняются отверстия, обеспечивающие доступ механизированного инструмента для затяжки коллекторных болтов.
Эта конструкция позволяет изготавливать пресс в условиях ремонтного завода. Сама конструкция малогабаритная и легко размещается на площадях коллекторного участка. В качестве источника давления применяются серийно выпускаемые гидростанции.
Рис.11 Общий вид станка РТ36
Станок выполнен с вертикальным расположением основной оси. В нижней части станка находится станина с основным приводом. Управление приводом осуществляется статическим преобразователем выполненных на базе тиристоров.
Коллектор устанавливается на планшайбу станка и закрепляется специальной конической оправкой. Рабочую зону станка полностью охватывает нагреватель, выполненный на элементах ТВЭЛ и представляющий собой кольцо. Нагреватель выполнен из двух половин - подвижной и неподвижной. Подвижная часть расположена со стороны рабочего места станка и после выполнения нагрева коллектора может перемещаться на шарнирах, обеспечивая доступ в рабочую зону для выполнения остальных технологических операций формовки.
Станок оборудован простейшим суппортом на котором может быть закреплен резец для проточки контрольной канавки на рабочей поверхности коллектора. На этом же суппорте при помощи оправки закрепляется индикатор часового типа для контроля качества формовки коллектора путем замера биения рабочей поверхности. В рабочую зону суппорта подведен воздуховод технологической вентиляции.
Впоследствии, на ремонтных заводах станок был модернизирован путем установки на поворотной штанге гайковерта. (На рисунке не показан.)
Технологический цикл осуществляется в следующем порядке
Коллектор устанавливается на планшайбу станка и закрепляется
Производится проточка контрольной канавки (При необходимости)
Суппорт отводится из рабочей зоны. Замыкается кольцо нагревателя. Включается приводной двигатель, Частота вращения коллектора доводится до номинальной (Для ЭД118А – 2190 об/мин). Включается нагрев. По достижении установленной температуры, нагрев продолжается около двух минут.
Частота вращения доводится до 3000 об/мин. Этот режим выдерживается в течение одной минуты.
Нагрев выключается. Привод выключается. Отводится половинка нагревателя, осуществляется затяжка болтов коллектора усилием, установленным техническими требованиями чертежа.
Далее цикл повторяется.
Практика применения показала, что для достижения динамической стабильности формы коллектора достаточно произвести три-четыре цикла. При этом в каждом цикле частоту вращения увеличивать. Например, для тягового электродвигателя ЭД118А номинальная частота вращения 2190 об/мин, частота испытания на разнос 4200 об/мин. Соответственно частота вращения первого цикла – 3000 об/мин, второго цикла – 3500 об/мин, третьего цикла – 4000 об/мин.
Впоследствии, для большей эффективности процесса, стали применять многократное увеличение частоты вращения коллектора в течение одного цикла. От номинальной до максимальной три-четыре раза в течение одной минуты.
На Новосибирском электровозоремонтном заводе был разработан и изготовлен станок для динамической формовки коллекторов. Ось станка выполнена горизонтальной. Операции по нагреву, разгону, подводу и отводу нагревателя и гайковерта осуществляются автоматически управляющим устройством. Устройство выполнено на микропроцессорной базе. Это же устройство осуществляет контроль температуры, частоты вращения.
Собранный и прошедший динамическую формовку коллектор проходит в обязательном порядке статическую балансировку на технологических ножах.
СОЕДИНЕНИЕ ОБМОТКИ
С КОЛЛЕКТОРОМ
После укладки обмотки в пазы якоря, установки пазовых клиньев и наложения бандажей осуществляется соединения обмотки якоря с пластинами коллектора.
В зависимости от конструкции якоря п применяются различные технологии соединения.
Рис. 12. Устройство ванны для пайки якорей
Так как в процессе пайки часть припоя уносилась из ванны с коллектором, происходило уменьшение массы припоя в ванной и в процессе пайки изменение удельно-массовых показателей в процессе теплообмена приводили к слишком быстрой кристаллизации припоя и раннему прекращению процесса его капиллярного проникновения в шлиц пластин коллектора.
Аналогичный результат появлялся при недостаточно нагретом коллекторе, что вызывало быстрое снижение температуры припоя в ванной.
Существующие инструментальные методы контроля качества пайки не обеспечивают уровня требуемой достоверности.
Общим результатом было снижение качества паяного соединения. Увеличение переходного сопротивления и снижения прочности соединения вызвало такой вид брака как распайка якоря. Причем он составлял ощутимую долю в отказах как при испытаниях в цеху, так и в процессе эксплуатации.
Отказы при стендовых испытаниях в цеху были вызваны нарушениями технологического процесса и представляли устраняемый вид брака. Отказы в эксплуатации стали выявлять и конструктивные недостатки.
Интенсификация эксплуатации локомотивов связанная с возрастанием нагрузки вызывала перегрев двигателей. Это выражалось изменением цвета коллекторных пластин и следов выброса припоя. Возрастание с нагрузкой величины и интенсивности динамических колебаний вызвала разрушение кристаллической структуры припоя и его выкрашивание. В отдельных случаях ослабление посадки железа на валу или втулке якоря (двигатель ТЛ2К) вызвало интенсивные колебания, приводившие к механическому излому концов секций
Рис. 13. Общий вид установки АДГ507
Установка выполнена в виде станины со стойкой. В станине расположена опора с приводным устройством для установки якоря и его рабочего вращения. Опора воспринимает осевую (вертикальную) нагрузку. Якорь устанавливается в гнездо опоры конусной частью конца вала.
Радиальные (горизонтальные) усилия воспринимаются роликами, установленными на стойке, которые также служат для базирования якоря на установке.
В задней части стойки установлена аппаратура подвода и управления процессом подачи инертного газа.
В средней части на уровне петушков коллектора установлены рабочие органы установки в виде консолей, непосредственно осуществляющие процесс сварки. Консоль может свободно отводится из рабочей зоны установки, а также фиксироваться в рабочем положении.
На консоли установлен мундштук, к которому подводится электрическое питание и инертный газ. Наконечник мундштука выполнен из керамических материалов, способных выдерживать воздействие электрической дуги.
Также на консоли в средней части установлены датчики автоматики синхронизации вращения якоря и импульсов напряжения.
В средней части установлены также металлические щетки с механизмом вращения для очистки мест сварного соединения.
В верхней части стойки установлены устройства автоматики и управления процессом, включающие в себя устройства регулирования импульсного напряжения и их синхронизацией с вращением якоря, устройства управления клапанами включение и отключении подачи газа.
В эксплуатации установка показала себя легко регулируемой и достаточно надежной.
Общие характеристики
Номинальное напряжение сети | 380в |
Диаметр свариваемых коллекторов мм | |
По рабочей части | 180-680 |
По «петушкам» | 235-840 |
Максимальная длина свариваемого якоря мм | 2100 |
Наибольшая потребляемая мощность установка кВа | 32Х2 |
Наибольший сварочный ток а | 500х2 |
Пределы регулирования тока а | 100-500 |
Диаметр вольфрамового электрода мм | 3-4 |
Частота вращения якоря об/мин | 0,12-2,4 |
Автоклавы
Для выполнения технологических операций вакуум-нагнетательной пропитки предназначены специальные автоклавы.
Автоклав представляет собой цилиндрический сосуд, в котором размещаются якоря электрических машин и позволяющий осуществлять следующие функции.
- создание вакуума во внутреннем пространстве;
- создание давления во внутреннем пространстве;
- заполнение и удаление лака из внутреннего пространства;
- обеспечение температурных режимов
Наиболее типичной является конструкция автоклава с вертикальным расположением якорей и с внутренним диаметром 1400мм. В течении 70-80х годов их по заказу ремонтных заводов изготавливал Улан-Удэнский локомотиво-вагоноремонтный завод. Разработчиком чертежей комплекса оборудования сушильно-пропиточного отделения электромашинных цехов, включающих в себя и автоклавы, являлся институт «ГИПРОЗАВОДТРАНС» Г. Харьков.
Размер выбран исходя из размеров якорей тяговых электрических машин. Наибольший диаметр якоря имеет тяговый генератор ГП311Б (D = 1200мм). Размеры якорей тяговых электродвигателей тепловозов и электропоездов (D=430мм.) допускают загрузку одновременно до четырех якорей. При этом используется специальная установочная оснастка.
Автоклав оборудован крышкой сферической формы с пневматическим приводом и системой уплотнения и герметизации, клиновыми затворами позволяющими фиксировать крышку в закрытом положении. В верхней цилиндрической части автоклав оборудован вводными патрубками для подключения внутренней полости к источникам давления и разрежения. В нижней сферической части автоклава имеется устройства для подключения к трубопроводу подачи лака или компаунда через дистанционно управляемый пробковый кран. К нижней сферической части приварены опоры крепления к фундаменту.
Крышка автоклава представляет собой полусферу полученную в результате обработки давлением на прессе с усилием не меньше 3000т. По периметру полусферы приварен кольцевой бурт, совпадающий с размерами с буртом основной цилиндрической части. В сферической части имеется смотровой иллюминатор, предназначенный для контроля уровня пропиточного состава. Снаружи приварены кронштейны для соединения крышки с пневматическим механизмом открытия и закрытия, а также крепления противовесов.
Система уплотнения представляет собой уплотнительное кольцо П – образного сечения, расположенное в кольцевой проточке торцевого бурта. Пневматический механизм прижимает крышку к торцевому бурту. После этого дав
|
|
Эмиссия газов от очистных сооружений канализации: В последние годы внимание мирового сообщества сосредоточено на экологических проблемах...
Типы сооружений для обработки осадков: Септиками называются сооружения, в которых одновременно происходят осветление сточной жидкости...
Автоматическое растормаживание колес: Тормозные устройства колес предназначены для уменьшения длины пробега и улучшения маневрирования ВС при...
Состав сооружений: решетки и песколовки: Решетки – это первое устройство в схеме очистных сооружений. Они представляют...
© cyberpedia.su 2017-2024 - Не является автором материалов. Исключительное право сохранено за автором текста.
Если вы не хотите, чтобы данный материал был у нас на сайте, перейдите по ссылке: Нарушение авторских прав. Мы поможем в написании вашей работы!