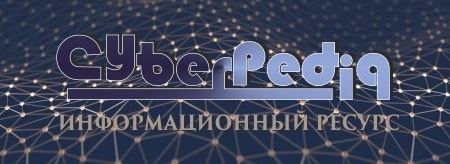
Адаптации растений и животных к жизни в горах: Большое значение для жизни организмов в горах имеют степень расчленения, крутизна и экспозиционные различия склонов...
Кормораздатчик мобильный электрифицированный: схема и процесс работы устройства...
Топ:
Теоретическая значимость работы: Описание теоретической значимости (ценности) результатов исследования должно присутствовать во введении...
Характеристика АТП и сварочно-жестяницкого участка: Транспорт в настоящее время является одной из важнейших отраслей народного...
Интересное:
Принципы управления денежными потоками: одним из методов контроля за состоянием денежной наличности является...
Подходы к решению темы фильма: Существует три основных типа исторического фильма, имеющих между собой много общего...
Лечение прогрессирующих форм рака: Одним из наиболее важных достижений экспериментальной химиотерапии опухолей, начатой в 60-х и реализованной в 70-х годах, является...
Дисциплины:
![]() |
![]() |
5.00
из
|
Заказать работу |
|
|
Введение
Редуктором называют механизм, состоящий из зубчатых или червячных передач, выполненный в виде отдельного агрегата и служащий для передачи вращения от вала электродвигателя к валу рабочей машины. Кинематическая схема привода может включать, помимо редуктора, открытые зубчатые передачи, цепные или ременные передачи.
Назначение редуктора – понижение угловой скорости и соответственно повышение вращающего момента ведомого вала по сравнению с ведущим. Механизмы для повышения угловой скорости, выполненные в виде отдельных агрегатов, называют ускорителями или мультипликаторами.
Редуктор состоит из корпуса с крышкой (литые чугунные или сварные стальные), в котором помещаются элементы передачи – зубчатые колеса, валы, подшипники и т.д.
Редуктор проектируют либо для привода определенной машины, либо по заданной нагрузке и передаточному числу без указания конкретного назначения.
Редукторы классифицируют по следующим основным признакам: типу передачи (зубчатые, червячные или зубчато-червячные); числу ступеней (одноступенчатые, двухступенчатые и т.д.); типу зубчатых колес (цилиндрические, конические, коническо-цилиндрические и т.д.); относительному расположению валов редуктора в пространстве (горизонтальные, вертикальные); особенностям кинематической схемы (развернутая, соосная, с раздвоенной ступенью и т.д.).
Энергетический и кинематический расчёт
Выбор электродвигателя
Определение требуемой мощности электродвигателя
, (1.1)
где - окружная сила на звездочке цепного конвейера, кН;
- скорость движения цепи, м/с;
- общий КПД привода.
Общий КПД привода определяется как:
, (1.2)
|
где - КПД муфты,
[1];
- КПД быстроходной передачи,
[1];
- КПД тихоходной передачи,
[1].
Тогда
Предполагаемая частота вращения вала электродвигателя
, (1.3)
где nэ – частота вращения вала электродвигателя, мин – 1;
- рекомендуемые средние значения передаточных чисел быстроходной и тихоходной ступени (предварительно принимаем;
[1]);
nвых – частота вращения выходного вала редуктора, .
Частота вращения выходного вала редуктора определяется по формуле
, (1.4)
где D - диаметр барабана, м.
Тогда
По найденным значениям мощности и частоты вращения с учётом пусковых качеств выбираем электродвигатель [2]:
4А90L4 ГОСТ 1923-81, ;
; кп = 2,4.
Определение передаточного числа редуктора
. (1.5)
1.3. Разбивка передаточного числа редуктора по ступеням (1.6)
По ГОСТ 2185-66 принимаем [2]. Тогда
(1.7)
По ГОСТ 2185-66 принимаем ,6 [2], тогда
[3]. (1.8)
Определение мощности на валах
; (1.9)
; (1.10)
(1.11)
Определение частоты вращения валов
; (1.12)
(1.13)
(1.14)
Определение крутящих моментов на валах
, (1.15)
где – мощность на валах, кВт,
– частоты вращения валов, мин - 1.
Расчёт червячной передачи передач
Проектный расчёт валов.
Быстроходный вал.
Входной конец вала также необходимо согласовать с диаметром вала электродвигателя и выбранной упругой в тулочно пальцевой муфтой 4A90L4
= 24 мм. – диаметр вала электродвигателя
L ступицы = 50 мм dbx = (0,8 … 1,2) dx
Выбираем муфту
Трасч = Кр × Тном ≤ [T]
где: Кр – коэффициент режима работы муфты
Тном – наиболее длительно действующий крутящий момент, H×m
[T] – допускаемый крутящий момент
Для данной муфты: = 1,5 × 14,4 = 21,6 H×m
Принимаем dbx = 20 мм
Принимаем, согласовывая с диаметром вала электродвигателя муфты
63-24- -2 УЗ ГОСТ 21424 – 83
(муфта упругая, втулочно-кольцевая, допускаемый крутящий момент
[T] = 63 H×m и частота вращения (n) = 5700 , цилиндрическое отверстие в полумуфтах – Ø24 с длиной ступицы и Ø20 с короткой ступицей, климатическое исполнение УЗ), поэтому dbx = 20мм.,
= 50мм.
|
Выбираем диаметр подшипников
dп ≥ dbx + 2 × t= 20 + 2 × 3 = 26м
Маркировка подшипников
Л – особенные подшипники (1 – сеператор латунный)
0,6 – внутренний диаметр подшипника
а) начиная с 0,4 × 5 = 20мм => Ø20
0,5 × 5 = 25мм => Ø25
0,6 × 5 = 30мм => Ø30
0,3 => Ø17мм
0,2 => Ø15мм
0,1 => Ø12мм
2 – серия подшипника
· 1 – особо лёгкая
· 2 – лёгкая
· 3 – средняя
· 4 – тяжёлая
О – типы: шариковый, радиальный, однородный
· 1 – радиальный, сферический 2-х рядный, шариковый
· 2 – роликовый, радиальный, с короткими цилиндрическими роликами
· 3 – роликовый, радиальный, 2-х рядный, сферический
· 4 – игольчатый
· 6 – шариковый, однородный, радиальный, упорный
· 7 – роликовый, конический, однорядный
· 8 – шариковый, однорядный, упорный
Принимаем dп = 30мм (принимаем роликовый, конический, однородный подшипник лёгкой серии 7206 с размерами Ø30×62×16; внутренний диаметр - 30мм., наружный диаметр – 62мм., толщина подшипника – 16мм..
Манжета Ø30×52×10
Расчёт шпоночных соединений
Шпоночное соединение с применением шпонок по ГОСТ на срез не рассчитывают, а расчёт ведут только на смятие.
lp = l – 0,5 × b – 0,5 × b = l – b
Напряжение =
F =
= (l – b) ×(h -
)
Момент = сила × плечо
T = F ×
F = T: = T×
=
×(h -
) = (l – b) × (h –
)
Напряжение смятия: Gсм = ≤ [G] см (допуск напряж.)
Шпонки
· Призматические
· Сегментные
· Клиновидные
Шлицевые соединения образуются наружными зубьями на валу и внутренними зубьями на ступице.
Зубья на валу получают фрезерованием, строганием, редко - накатыванием
Зубья в отверстии изготавливают протягиванием или долблением.
По форме боковых поверхностей шпонки делятся на:
· Прямобочные (наиболее распространённые)
· Эвольвентные (более технологичны, передают большие нагрузки)
· Треугольные
Центрирование
· По валу (d) (внутренний диаметр)
· По наружному диаметру (D)
· По ширине шлицов
При твердости HB < 350 (деталь не закалена) чаще всего центрируют по D
При HB > 350 (закалена) центрируют по d
Центрирование по ширине шлица b применяют при больших динамических нагрузках или реверсивных, т.к. нагрузка между зубьями здесь распределяется больше.
Расчет шлицовых соединений
Критерием работоспособности соединения является сопротивление смятию боковых поверхностей. Расчёт ведётся по длительно действующим крутящим моментам t.
|
Стандартом предусмотрено 3 серии соединений:
· Лёгкая серия
· Средняя
· Тяжёлая
=
≤[G] см.
× e × z
=
≤ [G] см
×D + d×D - d×D - d×d) =
Для прямобочных шлицев:
=
≤ [G] см
Для эвомвельных шлицев:
=
≤ [G] см
Назначаем модуль передачи
m=(0 016…0
0315)
aw=(0
016…0
0315)
112=1,8…3,15 мм
По ГОСТ 9563 – 60 принимаем m= 2 мм [1].
Расчет валов
Определяем диаметр под установку муфты на быстроходном валу по формуле
(4.1)
Вал быстроходный
Диаметр вала выходной электродвигателя составляет dэ =28 мм [1]
(4.2
Принимаем мм.
Принимаем муфту ГОСТ 20720-75
d=24 мм; l=20 мм; T=50 н/м.
Определяем диаметр вала под подшипник по формуле
, (4.3)
где t - высота буртика
Принимаем подшипник 207 ГОСТ 8338-75
D=72мм; B=17мм.
Определяем диаметр буртика под подшипник
, (4.4)
где r–фаска под подшипник, мм (r=2 5). [4]
Округляем до .
Для уплотнения принимаем манжету по ГОСТ 8752 – 79
d=35 мм, D=58 мм, h=10 мм
Тихоходный вал
Выходной конец тихоходного вала:
Согласуем выходной конец вала редуктора с параметрами муфты.
Принимаем цепную муфту ГОСТ 20742-81
d=50; l=82.
Принимаем dвых=50 мм
Определяем диаметр под подшипник
Принимаем
Принимаем подшипник 212 ГОСТ 8338-75
d=60 мм, D=110 мм, B=22 мм
Для уплотнения принимаем манжету по ГОСТ 8752-79
d=60мм; D=85мм; .
Определяем диаметр буртика под подшипник
Округляем до .
Определяем диаметр вала под колесо
принимаем
Диаметр стяжных винтов
(4.8)
принимаем d
Расстояние между стяжными винтами
l=(10…12) d
=(10…12)
10=100…120 мм
к=2 7
d
=2
7
10=27 мм
с=0 5
к=0
5
27=13
5 мм
Расчет валов
Расчет быстроходного вала
Определяем величину консольных сил на входной конец вала со стороны муфты по формуле
(4.9)
принимаем FМб=300 H.
Составляем расчетную схему
Определяем реакции в опорах в вертикальной плоскости (от действия силыFr1)
Проверка:
0 452+0
-0.83=0.24
Расчет тихоходного вала
I. Определяем реакцию в опорах в вертикальной плоскости
= 125
= 2 кН.
Проверка:
0.42 – 0.84 +0.42= 0
Определяем изгибающий момент в первом сечении
Определяем изгибающий момент во втором сечении
II. Определяем реакции в опорах в горизонтальной плоскости
|
Определяем изгибающий момент в первом сечении
Определяем изгибающий момент во втором сечении
Определяем изгибающий момент в третьем сечении
III. Крутящий момент действует от конца входного вала до точки приложения силы ;
.
По эпюрам устанавливаем опасные сечения;
1. шпоночный паз на входном конце вала;
2. галтель у входного конца вала;
3. галтель;
4. шпоночной паз;
IV. Определяем прочность вала в опасных сечениях.
Проверяем первое опасное сечение
Принимаем материал вала - сталь 45,
Принимаем для вала
Прочность вала в данном опасном сечении обеспечена
Проверяем второе опасное сечение
МПа
принимаем
Прочность вала в данном сечении обеспечена
Проверяем третье опасное сечение
=
МПа
принимаем k
= 1,65 [4]
Прочность вала в данном опасном сечении обеспечена
Проверяем четвертое опасное сечение
Прочность вала в данном опасном сечении обеспечена
Расчет подшипников
Расчет шпоночных соединений
Производим расчет шпонки по формуле
, (6.1)
где Т – крутящий момент на валу, Н·м;
диаметр вала, мм;
рабочая длина шпонки, мм;
- высота шпонки, мм;
глубина шпоночного паза на валу, мм;
допускаемые напряжение смятия, МПа.
, (6.2)
где l – длина шпонки, мм;
ширина шпонки, мм.
, (6.3)
где – предел текучести материала шпонки, МПа;
– допускаемый коэффициент запаса прочности.
Принимаем шпонку из стали 40, поэтому .
.
ВЫБОР МАСЛА
Смазывание зубчатых зацеплений и подшипников применяют в целях защиты от коррозии, снижения коэффициента трения, уменьшения износа, отвода тепла и продуктов износа от трущихся поверхностей, снижения шума и вибраций.
Для редуктора общего назначения применяем непрерывное смазывание жидким маслом картерным непроточным методом – окунанием. Этот способ применяют для зубчатых передач при окружных скоростях от 0,3 до 12,5 м/с.
Выбор сорта масла зависит от расчётного контактного напряжения sн и фактической окружной скорости.
Контактное напряжение sн = 573,7 МПа.
Окружную скорость определяем по формуле:
(м/с)
По табл. 8.3 [4] выбираем масло И-Г-А-68 ГОСТ 17479.4-87
индустриальное, для гидравлических систем, без присадок, класса кинематической вязкости 61…75 сСт при 40 °С.
Объём заливаемого масла определяем из расчёта 0,5…1,0 литра на 1 кВт мощности. Vм = 2,75 л3.
Поскольку Vs ³ 1 м/c, то смазывание подшипников происходит за счёт масляного тумана. Для свободного проникновения масла полость подшипника должна быть открыта внутрь корпуса.
Для контроля уровня масла имеется маслоуказатель.
При работе зубчатой передачи масло постепенно загрязняется продуктами износа деталей. Оно стареет, его свойства ухудшаются. Поэтому масло, налитое в корпус редуктора периодически меняют. Для этой цели в корпусе предусмотрено сливное отверстие и сливная пробка.
|
ПОРЯДОК СБОРКИ РЕДУКТОРА
Перед сборкой внутреннюю полость корпуса редуктора очищают и покрывают краской. Сборку производят в соответствии со сборочным чертежом редуктора.
Сначала запрессовывают шпонки, затем надевают колесо и запрессовывают подшипники. На валы надевают маслоудерживающие манжеты.
Собранные валы укладывают в основание корпуса редуктора и надевают крышку корпуса, покрывая предварительно поверхности стыка крышки и корпуса спиртовым лаком. Для центровки устанавливают крышку на корпус с помощью двух диагонально расположенных штифтов и затягивают болты.
Заливают в корпус масло и закрывают смотровое отверстие.
Собранный редуктор обкатывают и подвергают испытаниям на стенде.
Для нормальной работы роликовых подшипников следует следить, чтобы вращение подвижных элементов (внутренних колец) происходило легко и свободно, с другой стороны, чтобы в подшипниках не было излишне больших зазоров. Это достигается с помощью регулировки, для чего применяют наборы тонких металлических прокладок, устанавливаемые под фланцы крышек подшипников. Необходимая толщина набора прокладок может быть составлена из тонких металлических колец.
Список литературы
1. Дунаев, П.Ф. Конструирование узлов и деталей машин: Учеб. пособие для студ. высш. учеб. заведений / П.Ф.Дунаев, О.П.Леликов – 10-е изд., стер. – М.: Издат. центр «Академия», 2007. – 496 с.
2. Детали машин и основы конструирования / Под ред. М.Н.Ерохина. – М.: КолосС, 2005. – 462 с.
3. Черемисинов В.И. Курсовое проектирование деталей машин. / В.И.Черемисинов. - 4-е изд., перераб. и доп. - Киров: Вятская гос. с.-х. академия, 2008. – 187 с.
4. Черемисинов, В.И. Расчет закрытой прямозубой цилиндрической передачи (Методические указания к выполнению курсового проекта по дисциплине «Детали машин и основы проектирования») / В.И.Черемисинов. – Княгинино: Нижегород. гос. инженерно-эконом. ин-т, 2013. – 29 с.
Введение
Редуктором называют механизм, состоящий из зубчатых или червячных передач, выполненный в виде отдельного агрегата и служащий для передачи вращения от вала электродвигателя к валу рабочей машины. Кинематическая схема привода может включать, помимо редуктора, открытые зубчатые передачи, цепные или ременные передачи.
Назначение редуктора – понижение угловой скорости и соответственно повышение вращающего момента ведомого вала по сравнению с ведущим. Механизмы для повышения угловой скорости, выполненные в виде отдельных агрегатов, называют ускорителями или мультипликаторами.
Редуктор состоит из корпуса с крышкой (литые чугунные или сварные стальные), в котором помещаются элементы передачи – зубчатые колеса, валы, подшипники и т.д.
Редуктор проектируют либо для привода определенной машины, либо по заданной нагрузке и передаточному числу без указания конкретного назначения.
Редукторы классифицируют по следующим основным признакам: типу передачи (зубчатые, червячные или зубчато-червячные); числу ступеней (одноступенчатые, двухступенчатые и т.д.); типу зубчатых колес (цилиндрические, конические, коническо-цилиндрические и т.д.); относительному расположению валов редуктора в пространстве (горизонтальные, вертикальные); особенностям кинематической схемы (развернутая, соосная, с раздвоенной ступенью и т.д.).
Энергетический и кинематический расчёт
Выбор электродвигателя
|
|
Своеобразие русской архитектуры: Основной материал – дерево – быстрота постройки, но недолговечность и необходимость деления...
Наброски и зарисовки растений, плодов, цветов: Освоить конструктивное построение структуры дерева через зарисовки отдельных деревьев, группы деревьев...
История развития хранилищ для нефти: Первые склады нефти появились в XVII веке. Они представляли собой землянные ямы-амбара глубиной 4…5 м...
Археология об основании Рима: Новые раскопки проясняют и такой острый дискуссионный вопрос, как дата самого возникновения Рима...
© cyberpedia.su 2017-2024 - Не является автором материалов. Исключительное право сохранено за автором текста.
Если вы не хотите, чтобы данный материал был у нас на сайте, перейдите по ссылке: Нарушение авторских прав. Мы поможем в написании вашей работы!