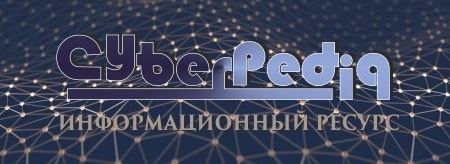
Общие условия выбора системы дренажа: Система дренажа выбирается в зависимости от характера защищаемого...
Эмиссия газов от очистных сооружений канализации: В последние годы внимание мирового сообщества сосредоточено на экологических проблемах...
Топ:
Устройство и оснащение процедурного кабинета: Решающая роль в обеспечении правильного лечения пациентов отводится процедурной медсестре...
Характеристика АТП и сварочно-жестяницкого участка: Транспорт в настоящее время является одной из важнейших отраслей народного...
Теоретическая значимость работы: Описание теоретической значимости (ценности) результатов исследования должно присутствовать во введении...
Интересное:
Наиболее распространенные виды рака: Раковая опухоль — это самостоятельное новообразование, которое может возникнуть и от повышенного давления...
Распространение рака на другие отдаленные от желудка органы: Характерных симптомов рака желудка не существует. Выраженные симптомы появляются, когда опухоль...
Искусственное повышение поверхности территории: Варианты искусственного повышения поверхности территории необходимо выбирать на основе анализа следующих характеристик защищаемой территории...
Дисциплины:
![]() |
![]() |
5.00
из
|
Заказать работу |
|
|
А. В. Селиванов
ЛОГИСТИКА ПРОИЗВОДСТВА
Утверждено редакционно-издательским
советом университета в качестве учебного пособия
для студентов бакалавриата по направлению подготовки
38.03.02 «Менеджмент», направленность «Логистика»,
всех форм обучения
Красноярск 2016
УДК 658.7(075.8)
ББК 65.291.592я7
С29
Рецензенты:
кандидат технических наук, старший научный сотрудник И. И. Вашлаев
(Институт химии и химических технологий
Сибирского отделения Российской академии наук);
доктор экономических наук, профессор Е. В. Белякова
(Сибирский государственный аэрокосмический университет
имени академика М. Ф. Решетнева)
Селиванов, А. В.
С29 Логистика производства: учеб. пособие / А. В. Селиванов; Сиб. гос. аэрокосмич. ун-т. – Красноярск, 2016. – 106 с.
Рассмотрен ряд тем дисциплины «Логистика производства» в соответствии с общеобразовательной программой. Предлагаемая тематика позволяет ознакомиться со структурой изучаемой дисциплины, принципами логистической организации производственных процессов, логическими взаимосвязями, возникающими в производственной системе, теоретическими особенностями и обеспечивает возможность практического применения приобретенных знаний. Пособие подготовлено для студентов бакалавриата, по направлению подготовки 38.03.02 «Менеджмент», направленность «Логистика», всех форм обучения, но может быть также полезным практикам и специалистам в области логистики.
УДК 658.7(075.8)
ББК 65.291.592я7
© Сибирский государственный аэрокосмический
университет имени академика М. Ф. Решетнева, 2016
© Селиванов А. В., 2016
|
СОДЕРЖАНИЕ
Предисловие 5
Основы логистики производства промышленного
предприятия 8
1.1. Место логистики производства в интегрированной
логистической системе 8
1.2. Промышленное предприятие
как производственная система 11
1.3. Расчет потребностей материально технического
обеспечения производства продукции 15
1 4. Интегрированная система управления материальными
потоками предприятия на основе MRP-2 19
Контрольные вопросы и задания. 24
2. Типы производства и методы его организации 26
2.1. Общая характеристика типов производства 26
2.2. Методы организации производства 28
2.3. Поточное производство и разновидности
поточных линий 29
2.4. Основные параметры поточных линий 31
Контрольные вопросы и задания. 33
Структура производственного процесса
промышленного предприятия 34
3.1. Производственные структуры процессов
производства 34
3.2. Понятие «производственный цикл» 40
3.3. Факторы, влияющие на длительность
производственного цикла 42
3.4.Принципы организации производственного процесса 46
3.5. Сочетание технологических и трудовых процессов 49
Контрольные вопросы и задания. 52
Логистическое обеспечение процессов
управления и производства 54
4.1. Логистическая система управления
компанией «Тойота» 54
4.2. Формирование локальных контуров управления
логистическими процессами предприятия 56
4.3. Логистическое управление подсистемой
материально-технического снабжения 61
4.4. Транспортно-складская логистика производственной
системы машиностроительного предприятия 68
4.5. Сбалансированная подсистема показателей
возвратной логистики промышленного предприятия 75
Контрольные вопросы и задания. 78
Организация инструментального
и ремонтного хозяйства 80
5.1. Логистическое обеспечение инструментом
производственных процессов 80
5.2. Определение потребности в инструменте 82
5.3. Организация работы центрального
инструментального склада 86
5.4. Логистическое обеспечение ремонта оборудования 88
|
Контрольные вопросы и задания. 91
Оценка воздействия логистических затрат
на технико-экономические показатели предприятия 92
6.1. Основные технико-экономические показатели
логистических и производственных систем 92
6.2. Показатели и методы оценки эффективности
логистических систем 93
6.3. Факторный анализ воздействия логистических затрат
на технико-экономические показатели предприятия 96
Контрольные вопросы и задания. 98
Послесловие 100
Библиографический список 102
Приложение 104
ПРЕДИСЛОВИЕ
Логистика производства (ЛП) образует базовую функциональную область логистики. Ее изучение необходимо для накопления знаний, способствующих планированию исследований и налаживанию бесперебойного синхронизированного обеспечения материальными, информационными и финансовыми ресурсами производства и распределения конечной продукции или услуги на предприятии.
Объектом дисциплины «Логистика производства» является внутренняя и внешняя хозяйственная деятельность промышленного производства предприятия (организации).
В качестве предмета дисциплины «Логистика производства» рассматриваются производственные отношения, возникающие в процессе хозяйственной деятельности на исследуемом объекте.
Целью изучения учебной дисциплины является освоение бакалаврами основных положений разработки и поддержки управленческих решений в области логистики производства, способствующих не только стабилизации, но и развитию экономического состояния предприятия. В результате освоения дисциплины студенты должны знать взаимосвязи между стратегическим, тактическим и оперативным видами планирования логистической деятельности предприятия; процессы и явления, протекающие в производственной системе; уметь использовать методы и инструменты логистики производства в целях повышения эффективности функционирования производственной системы; владеть методами планирования и управления логистическими процессами предприятия.
К основным задачам дисциплины «Логистика производства» относят:
– совершенствование логистической структуры производства
и производственного процесса;
– контроль и обновление норм расхода материальных ресурсов (МР) по рабочим процессам и операциям производства продукции;
|
– оптимизация темпа производства, всех запасов МР, незавершенного производства (НП), объемов выпуска готовой продукции (ГП) внутрипроизводственно-технологического цикла и складской системы промышленного предприятия;
– улучшение технико-экономических показателей (ТЭП) работы внутрипроизводственного транспортного комплекса (маршрутизация, диспетчеризация, грузовместимость, грузоподъемность и др.);
– нормирование времени производственно-технологического цикла;
– учет, анализ и оптимизация операционных логистических издержек;
– выбор внутрипроизводственной информационно-управляю-
щей системы оптимизации материально-технических ресурсов;
– имитационное моделирование расхода МР;
– учет отходов производства и оценка эффективного использования вторичных МР (устранение потерь от брака);
– формирование синхронизированных и интегрированных материальных, информационных и финансовых потоков в производственных системах;
– расчет параметров графика поставки МР на производственные объекты предприятия;
– обоснование потребности инструментального оснащения процессов производства продукции;
– ведение рейтинговых оценок участников логистического обеспечения производственного процесса предприятия;
– обоснование методов управления логистическими рисками производства на промышленном предприятии.
В качестве основных методов решения задач ЛП применяются системный анализ, исследование операций, статистический анализ, информационные технологии, методы сетевого планирования
и управления, финансовый анализ проектов.
Основным критерием выбора вариантов мероприятий ЛП принимается минимизация упущенной выгоды в процессе функционирования предприятия/организации.
Знания, полученные студентами в результате изучения дисциплины, будут способствовать системному пониманию сферы деятельности бакалавров в области логистики производства, значимости логистики как науки и практики системного управления потоковыми процессами в организационно-экономических системах.
Рассматриваются основные положения, принципы, методы теории логистики производства, которые способствуют формированию стабильного технологического цикла выпуска и реализации конечной продукции предприятия. Применяемые методы должны исключать появление таких производственных ситуаций на промышленных предприятиях, которые могут привести к сбоям производства продукции, прерыванию синхронизации обеспечивающих процессов, что
в итоге понижало бы эффективность производства в целом.
|
Знание теории ЛП и профессиональные навыки приложения теоретических знаний к решению практических задач по расчету параметров графика поставок материально-технических ресурсов востребованы в логистической деятельности персонала промышленного предприятия при обеспечении бесперебойности процесса производства.
Содержание учебного пособия включает примеры решения практических задач с оценкой эффективности предлагаемых мероприятий. Данный материал может служить аналогом при выполнении студентами практических работ.
Важной задачей учебного пособия является знакомство студентов не только с теорией логистики производства, но и с практическими навыками планирования и управления производственной деятельностью с использованием современных методов управления. В учебном пособии представлены задачи для самостоятельной проработки материала и примеры их решения. В конце глав приведены контрольные вопросы, которые помогут студентам проводить самопроверку накопленных знаний в области логистики производства. Изучив литературу библиографического списка, студенты смогут расширить знания по дисциплине.
В учебном пособии достаточно материала для подготовки к сдаче экзамена по дисциплине «Логистика производства» и выполнения практических заданий по ее разделам. Имеется справочный материал, необходимый при выполнении практических заданий.
ПРОМЫШЛЕННОГО ПРЕДПРИЯТИЯ
Промышленное предприятие
Расчет потребностей
Производства продукции
Нормативная база материально-технического обеспече-
ния (МТО) – система нормативов, необходимых для определения потребностей производства в материальных ресурсах. Номенклатура материалов промышленного предприятия средней мощности насчитывает более 1,5…2,0 тыс. наименований. Так, например, известно,
что для автомобильной промышленности подобный список набирает до 7 тыс. наименований, а для производства спутника – до 30 тыс. наименований, и для каждой номенклатурной единицы определяется норма расхода материала.
Норма расхода материала – максимально допустимый расход материалов в натуральном измерении на единицу продукции (или изделия, услуги) при рациональных организационно-технических условиях производства. Нормы расхода должны быть прогрессивными
и технически обоснованными.
|
Нормы расхода материалов делятся на пять видов:
1) нормы расхода основных и вспомогательных материалов;
2) по времени действия различают перспективные, годовые и оперативные нормы расхода материалов;
3) в зависимости от объекта нормирования устанавливают нормы расхода на деталь (например, кронштейн, шестерню), узел (двигатель, кабину), изделие в целом (например, автомобиль, станок);
4) укрупненные (или сводные) нормы, по которым определяют расход материала на 1 тыс. руб. валовой продукции, или на единицу конечной продукции;
5) в зависимости от масштаба применения нормы подразделяют на индивидуальные, групповые и отраслевые:
– устанавливаются для определенного предприятия;
– для групп предприятий, изготавливающих одинаковую продукцию;
– на определенный вид продукции (независимо от того, какие предприятия ее выпускают).
Технически обоснованная норма расхода материалов рассчитывается по формуле
, (1.1)
где Нр – норма расхода материалов, м, шт. и др.; Вч – чистый вес (расход) материала на единицу конечной продукции (или изделия, услуги); Ов – отходы возвратные; Пб – потери безвозвратные (например, припуск на обработку детали).
Используются три метода установления норм:
– отчетно-статистический: на основе отчетов о расходовании материала (или аналогичных ему) в прошлом;
– опытно-лабораторный: проводятся опыты в лабораторных условиях (качество зависит от приближения условий опыта к конкретным производственным условиям);
– подробных инженерных расчетов и анализа результатов.
Производственная потребность в материалах определяется следующим образом[1]:
, (1.2)
где M ij – потребность j- го материала на производство i- й конечной продукции объема Qi (rj); Qi (rj) – объем производства i- го вида продукции за период между двумя очередными партиями поставок
j- го материала, ед. продукции (или шт.); rj – длительность цикла возобновления между двумя очередными партиями поставок j -го материала, дн.; H ij – плановая норма расхода j- го материала на производство i- й единицы продукции, ед. материала / ед. продукции;
j – индекс материала, j J; J – конечное множество номенклатурных единиц материалов; К ij – планируемый коэффициент снижения норм расхода, К ij ≈ 0,94–1,0; n – общее количество выпускаемой продукции.
Общий расход j -го материала на общее количество выпускаемой продукции определяется по выражению
Фактическая норма расхода (по данным складского учета) рассчитывается по формуле
(1.3)
при условии
Периодически фактическая норма () сопоставляется с плановой (H ij):
Размер экономии можно рассчитать по выражению
,
где Эм – размер экономии j- го материала в стоимостном выражении, руб.; Ц j – цена единицы j- го материала, руб.
Нормы расхода предлагается контролировать по однородным массивам входной информации по мере накопления статистики по периодам поставок материалов. Для этого строится двухсторонний интервал (по t -критерию Стьюдента):
(1.4)
где – средняя арифметическая (или средневзвешенная) величина контролируемого удельного расхода j- го материала:
(1.5)
– табличное значение квантилей Стьюдента по заданному α-уровню значимости и (N – 1)-й степени свободы; N – количество наблюдений (объем выборки) случайной величины за фиксированный период производства однородной продукции; S – средне-квадратическое отклонение случайной величины, рассчитанное из N наблюдений (N min = 30):
(1.6)
По границам доверительного интервала K можно судить о значимости контролируемого планового норматива H ij, с помощью которого определяется производственная потребность в материалах по выражению (1.2) на rj дней работы предприятия.
Значение H ij, первоначально принятое по местным нормативам (или отраслевым), может заменяться оценкой математического ожидания, для которой строится двухсторонний интервал (1.4), так как известно, что нормативно-справочные показатели рассчитываются постепенным приближением статистического значения к наиболее вероятному его значению.
Такие процедуры контроля должны производиться в условиях автоматизированного учета и анализа расхода материалов (т. е. должно быть налажено использование информационных технологий (ИТ).
Контроль расходования материалов по двухстороннему интервалу K можно сочетать с имитационным моделированием, что позволяет получить по истечении tj дней работы предприятия с начала завоза j -го материала опережающую информацию о движении материалов до определенного срока, например до окончания цикла поставки μ j = rj – tj. В результате сопоставления потребности с запасом определяется опережающий момент остановки производства предприятия по причине исчерпания текущих запасов j -го материала. Дата возможной остановки заблаговременно сообщается руководству предприятия
и службе снабжения с целью организации работ по пополнению запасов за приемлемые сроки.
Рекомендуемые мероприятия осуществляются на массовых
и серийных производствах. Для мелкосерийных или единичных типов производств используются вероятностные методы оценок и устанавливается ожидаемая норма расхода материалов[2]:
(1.7)
(1.8)
где Нож1, Нож2 – ожидаемые нормы расхода j- го материала, при этом принимается, что случайная величина, т. е. норма расхода материала, распределяется по β-закону в интервале [ a, в ]; Нопт – оптимистическая оценка – минимальная норма расхода материала, необходимого для выполнения данной работы при наиболее благоприятных условиях ее выполнения (Нопт = a); Нпес – пессимистическая оценка – максимальная норма расхода материала при неблагоприятных условиях выполнения данной работы (Нпес = в); Нн.в – наиболее вероятная оценка – норма расхода материала при нормальных (штатных) условиях выполнения данной работы.
По расчету Нож1 или Нож2 определяют потребность в материалах мелкосерийного или единичного производства. Предприятия единичного типа производства заключают контракты на производство своей уникальной продукции с учетом норм расхода материалов (см. формулы (1.7) и (1.8), чтобы уменьшить риски, связанные с выполнением единичного заказа. А по мере накопления фактической статистики нормы Нож1 или Нож2 могут пересматриваться.
Для сокращения объемов работ, связанных с нормированием, применяется ABC-анализ[3]. Это позволяет использовать методику нормирования, прежде всего для классов A и B. Для класса С процедура контроля норм применяется реже и с меньшей частотой.
На основе MRP-2
Система планирования материальных ресурсов (MRP-1) представляет особый интерес, так как отражает, как правило, общий уровень организации и управления производством на отечественных промышленных фирмах. В этой системе осуществляется календарное планирование по узлам изделий, формируются комплекты заготовок
и деталей по участкам производства, которые включаются в планы производственных участков в соответствии с договорными сроками выполнения заказов. Если пропускная способность участка ниже объема производственных заданий, то ее увеличивают либо за счет найма новых рабочих, либо за счет увеличения сменности работы, либо за счет использования сверхурочных работ и т. д.
Система MRP-2 (рис. 1.7), в отличие от системы MRP-1, является более интегрированной.
Рис. 1.7. Блок-схема полного цикла основных функций интегрированной
системы управления производством в Manufacturing Resource Planning-2
(по О. Г. Туровец)
Обычно система MRP-1 (Materials Requirements Planning) охватывает управление материальным потоком от закупки сырья и комплектующих до реализации готовой продукции (подсистемы прогнозирования сбыта и закупок, управления закупками, управления технической подготовкой производства, управления производством, управления запасами, управления сбытом, калькуляции затрат).
Структура системы MRP-2 включает также следующие подсистемы: внутрифирменного планирования; имитационного моделирования процессов производства и хозяйственной деятельности; бухгалтерского учета и финансового управления; управления контрактами; управления информацией и управленческой деятельностью; управления качеством продукции и другие по мере ее развития. За рубежом интенсивно развивается методология антикризисного управления BRP (Business Process Reengineering – реорганизация процессов производства и управления).
В этой методологии упор делается на маркетинговые исследования; разработку и постановку на производство новой продукции; реорганизацию структуры предприятия, его документооборота и системы управления; переобучение персонала.
Эта методология активно влияет на развитие системы MRP-2. Система MRP-2 более производительна, чем система MRP-1. Система MRP-1 обеспечивает использование рабочего времени рабочих и оборудования до 50 %, система MRP-2 – до 70 %. Это происходит за счет применения более совершенных методов сглаживания динамики движения узких и широких мест при согласовании во времени трудоемкости производственной программы каждого подразделения с его пропускной способностью.
Так как система MRP-2 построена исходя из статического представления о ходе производства, то это как раз порождает непредсказуемое движение узких и широких мест в производстве. Использование имитационного моделирования в системе MRP-2 как информационного сопровождения хода производства, как метода выбора более рациональных решений позволяет несколько сгладить негативные последствия динамики движения узких и широких мест в производстве. Система MRP-2 сегодня является международным стандартом организации и управления предприятием. Этот стандарт построен в соответствии с современными принципами организации и управления производственными процессами. В качестве основных принципов MRP-2 используются следующие положения:
– непрерывный однонаправленный поток взаимодополняющих заказов – основа организации производственной деятельности;
– снабжение, производство, сбыт как типовые этапы движения заказов по сквозным единым графикам выполнения заказов;
– минимизация запасов готовой продукции, материалов и комплектующих;
– оптимизация заделов незавершенного производства;
– учет ограничений ресурсов (времени, материальных, трудовых, финансовых, информационных) для выполнения заказа;
– выполнение заказа только тогда, когда нужно потребителю;
– интеграция и компьютеризация процессов выполнения заказов и управления предприятием.
Предприятия/компании могут развивать собственные логистические подразделения, а могут привлекать (нанимать) транспортно-логистические организации для решения вопросов поставок, складирования и сбыта. Управление материальными потоками на предприятии / в организации осуществляется различными способами. Рассмотрим их.
1. «Толкающая (push)» система – предметы труда, поступающие на производственный участок, им не заказаны, а поступают согласно команде из центральной системы управления производством и распределяются по схеме (рис. 1.8).
Система управления
Рынок сбыта
Склад
сырья
Цех № 1
Цех № 2
Спрос
Продукция
Материалы
Заготовки
Детали
– МП (материальный поток)
– ИП (информационный поток)
Цех сборки
Потребность,
график снабжения
Задание,
график работ
Задание,
график работ
Задание
на производство, график работ
Рис. 1.8. «Толкающая (push)» система организации производства
«Толкающие» системы способны увязать сложный производственный процесс в единое целое. Однако их возможности определяются количеством факторов, влияющих на производственную ситуацию. Чем их больше, тем совершеннее должна быть система управления. «Толкающие» системы характеризуются высоким уровнем автоматизации управления. Типичным примером толкающей системы является система MRP – концепция планирования потребностей ресурсов. Входными параметрами являются описание состояния материалов, график производства и список материалов.
На выходе формируется план заказов, исполнительный отчет, отчет о прогнозах.
2. «Тянущая (pull)» система – система организации производства, где предметы труда подаются на последующую технологическую операцию с предыдущей по мере необходимости (рис. 1.9). Здесь центральная система управления не вмешивается в обмен материальными потоками между различными участками предприятия, а ставит задачу лишь перед конечным звеном технологической цепи.
Система управления
Задание
на производство
Склад сырья
Цех сборки
Цех № 1
Цех № 2
Продукция
Материалы
Заготовки
Детали
– МП (материальный поток)
Заказ
материалов
Заказ
заготовок
Заказ
деталей
Рынок сбыта
Спрос
Потребность,
график снабжения
– ИП (информационный поток)
Рис. 1.10. «Тянущая» система организации производства
Примером такой организации является система Just in time – минимальные или нулевые запасы, короткие производственные циклы, небольшие объемы готовой продукции, высокое качество готовой продукции и логистического сервиса, эффективная информационная поддержка. Чем разнообразнее спрос и выше стоимость продукции, тем предпочтительнее данная концепция.
Другой разновидностью управления материальными потоками является японская система Kan Ban, в которой обеспечиваются рациональная организация и сбалансированность производства, повышается профессиональная ответственность и высокая трудовая дисциплина всего персонала. Средством передачи информации в системе является специальная карточка в пластиковом конверте – kanban.
Не может быть изготовлено ни одного изделия до тех пор, пока карточка производственного заказа не разрешит производство. Рабочие могут выполнять регламентные работы, проводить уборку или работать над проектами по улучшению до тех пор, пока не прибудет карточка производственного заказа. Соответственно, карточка отбора контролирует транспортировку изделий между участками обработки (сборки). Могут применяться только стандартные контейнеры, они всегда заполнены предписанным малым объемом продукции. На контейнер точно приходится одна карточка отбора и одна карточка производственного заказа. Основными показателями работы такой системы являются объем контейнера и количество их в системе.
В системе Lean Production исключаются операции, которые
не прибавляют ценности итоговому продукту. Эта система соединяет плюсы массового и мелкосерийного производства, а также исключает складирование и ожидание.
Контрольные вопросы и задания
1. С какими функциональными областями интегрируется логистика производства и чем это вызвано?
2. Назовите причины взаимосвязи деятельности логистического персонала с процессами управления, планирования, экономики, самой логистики, организации и технологии производства.
3. Поясните сущность конфигурации взаимодействия процессов управления, планирования, экономики, логистики, организации, технологии.
4. Перечислите основные обязанности логиста предприятия.
5. Какие этапы включаются в перечень организационного совершенствования логистической системы?
6. Какими особенностями характеризуется динамичность производственной системы?
7. Какие компоненты промышленного предприятия слагают его производственную систему?
8. Перечислите модели, комплексы задач, методы их решения, включающиеся в структуру комплексной модели большой системы, примером которой является производственная система предприятия.
9. Приведите пример укрупненной структуры производственного процесса промышленного предприятия.
10. Напишите формулу расчета производственной потребности в материалах при заданном объеме производства готовой продукции.
11. Сформулируйте принципы контроля норм в условиях автоматизированного учета и анализа расхода материалов на предприятии.
12. Какие методы контроля норм расхода материалов используются для мелкосерийных или единичных типов производств и каким документом закрепляются деловые отношения с заказчиком единичной продукции?
13. Назовите подсистемы, которые входят в структуру системы MRP-2.
14. Перечислите основные принципы MRP-2, которые применялись при ее создании.
15. В чем преимущества «тянущей (pull)» системы организации производства по сравнению с «толкающей (push)» системой?
16. Назовите преимущества концепции Lean Production.
17. Приведите отличие в структурах MRP-1 и MRP-2.
18. Каким образом устанавливаются нормы расхода материальных ресурсов для единичного производства продукции?
19. Какие преимущества обеспечиваются при реализации автоматизированного контроля баланса материальных ресурсов предприятия?
20. Какое количество номенклатурных наименований материалов требуется поставлять для организации промышленного производства на предприятии средней мощности; предприятий автомобильной промышленности; предприятии по производству спутников?
21. Составьте блок-схему алгоритма расчета баланса материалов предприятия/организации.
ТИПЫ ПРОИЗВОДСТВА
И МЕТОДЫ ЕГО ОРГАНИЗАЦИИ
Поточных линий
Поточное производство– форма организации производства, основанная на глубокой специализации, при которой рабочее место, станок или агрегат специализируются на выполнении только одной или нескольких однородных операций обработки детали или сборки изделия.
Основные признаки поточного производства следующие:
– за группой рабочих мест закрепляется обработка или сборка предмета одного наименования или предметов ограниченного количества наименований, родственных в конструктивно-технологическом отношении;
– технологический процесс изготовления изделия разбивается на операции, и на каждом рабочем месте выполняется одна или несколько рабочих операций;
– предметы передаются с операции на операцию поштучно или небольшими передаточными (транспортными) партиями в соответствии с заданным ритмом работы поточной линии, благодаря чему достигается высокая степень параллельности и непрерывности;
– основные и вспомогательные операции вследствие узкой специализации рабочих мест отличаются высоким уровнем механизации и автоматизации. Широко применяется специальный межоперационный транспорт, выполняющий не только функцию перемещения обрабатываемых предметов, но и функцию поддержания ритма производства.
Одним из главных условий эффективности поточного производства является непрерывность потока, которая обеспечивается:
– непрерывностью протекания отдельных частичных процессов;
– непрерывной подачей предмета труда по операциям.
Условием непрерывности служит равномерный выпуск полуфабрикатов по определенным частичным процессам и производственному процессу в целом (т. е. прямоточность и синхронность выполнения смежных операций). Однако на практике эти условия выполняются редко, поэтому ставится задача максимального приближения к ним.
Элементы поточной организации производства имели место уже в мануфактурный период капиталистической промышленности. Впервые поточное производство в его наиболее совершенной форме было организовано Г. Фордом в начале ХХ века при изготовлении автомобилей. В промышленности дореволюционной России поточного производства не существовало. После Октябрьской революции вместе с развитием промышленности и техническим прогрессом поточные методы активно внедряются на предприятиях. В настоящее время поточные методы широко распространены во многих отраслях промышленности; в машиностроении, например в России, выпуск продукции поточным методом составляет более 40 %.
Основным звеном поточного производства является поточная линия, представляющая собой цепочку рабочих мест, расположенных в последовательности выполнения технологических операций производственного процесса.
Поточная линия – совокупность технологически связанных рабочих мест, занятых изготовлением одного или нескольких однородных
в конструктивном и технологическом отношениях предметов труда.
Пульсирующее движение характерно как для рабочих конвейеров, так и для конвейеров со снятием предметов.
ПРОМЫШЛЕННОГО ПРЕДПРИЯТИЯ
Производства
Основное производство объединяет подразделения, осуществляющие все технологические процессы по изготовлению основной продукции.
Вспомогательное и обслуживающее производства прямо не участвуют в создании основной продукции, но содействуют работе основных цехов и обеспечивают их ритмичную работу.
На практике встречаются разнотипные производственные струк-
туры. Так, например, используются сочетания основной производственной структуры предприятия с обслуживающей или со вспомогательным производством (или с производством в определенных цехах).
Цех – это обособленное в административном отношении подразделение. В каждом цехе выполняется определенная стадия технологического процесса, связанного с производственной деятельностью предприятия.
Состав основных цехов промышленного предприятия приведен в табл. 3.1. При этом в цехах основного производства осуществляется обработка предметов труда для их превращения в готовую продукцию.
Таблица 3.1
Производственного цикла
Длительность структурных составляющих производственногоцикла зависит от факторов конструкторского, технологическогои организационного характера (табл. 3.2).
На длительность производственного цикла существенное влияние оказывают величина партий деталей и вид движения предметов труда в процессе их обработки.
Таблица 3.2
Процесса
Цель организации любого производственного процесса – такое рациональное сочетание во времени и пространстве основных, вспомогательных и обслуживающих процессов, которое позволяет достигнуть наилучшего использования всех трудовых, материальных
и финансовых ресурсов предприятия.
Эти сочетания могут отличаться на разных производствах, что зависит от их технико-экономических особенностей.
Основными принципами рациональной организации любого процесса является пропорциональность, непрерывность, параллельность, прямоточность, ритмичность, а также концентрация однородных предметов труда в одном месте, гибкость процесса. Рассмотрим эти принципы.
Пропорциональность – принцип, выполнение которого обеспечивает равную пропускную способность разных рабочих мест одного процесса, пропорциональное обеспечение рабочих мест информацией, материальными ресурсами, кадрами и т. д.
Коэффициент пропорциональности определяется по формуле
(3.2)
где и – соответственно минимальная и максимальная пропускная способность или параметр рабочего места в технологической цепи (например, мощность, разряд работ, объем и качество информации и т. п.).
Непрерывность – принцип рациональной организации процессов.
Коэффициент непрерывности определяют отношением рабочего времени (Т раб) к общей продолжительности производственного цикла (Т ц):
(3.3)
Параллельность – принцип рациональной организации процессов, характеризующий степень совмещения операций во времени.
Коэффициент параллельности рекомендуется определять по формуле
(3.4)
где – соответственно продолжительность параллельного и последовательного сочетания операций.
Прямоточность –
|
|
Архитектура электронного правительства: Единая архитектура – это методологический подход при создании системы управления государства, который строится...
Индивидуальные очистные сооружения: К классу индивидуальных очистных сооружений относят сооружения, пропускная способность которых...
Адаптации растений и животных к жизни в горах: Большое значение для жизни организмов в горах имеют степень расчленения, крутизна и экспозиционные различия склонов...
Типы сооружений для обработки осадков: Септиками называются сооружения, в которых одновременно происходят осветление сточной жидкости...
© cyberpedia.su 2017-2024 - Не является автором материалов. Исключительное право сохранено за автором текста.
Если вы не хотите, чтобы данный материал был у нас на сайте, перейдите по ссылке: Нарушение авторских прав. Мы поможем в написании вашей работы!