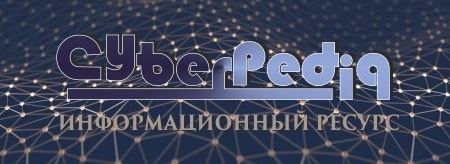
Состав сооружений: решетки и песколовки: Решетки – это первое устройство в схеме очистных сооружений. Они представляют...
Историки об Елизавете Петровне: Елизавета попала между двумя встречными культурными течениями, воспитывалась среди новых европейских веяний и преданий...
Топ:
Генеалогическое древо Султанов Османской империи: Османские правители, вначале, будучи еще бейлербеями Анатолии, женились на дочерях византийских императоров...
Организация стока поверхностных вод: Наибольшее количество влаги на земном шаре испаряется с поверхности морей и океанов...
Отражение на счетах бухгалтерского учета процесса приобретения: Процесс заготовления представляет систему экономических событий, включающих приобретение организацией у поставщиков сырья...
Интересное:
Принципы управления денежными потоками: одним из методов контроля за состоянием денежной наличности является...
Средства для ингаляционного наркоза: Наркоз наступает в результате вдыхания (ингаляции) средств, которое осуществляют или с помощью маски...
Отражение на счетах бухгалтерского учета процесса приобретения: Процесс заготовления представляет систему экономических событий, включающих приобретение организацией у поставщиков сырья...
Дисциплины:
![]() |
![]() |
5.00
из
|
Заказать работу |
|
|
Методические указания
Данные для расчета режимов резания при нормировании
Определение основного времени
1. Определить основное время на каждый переход по формулам:
- для токарной обработки
где: L – длина хода резца
i – число проходов
n – частота вращения шпинделя
Sn – подача
- для сверления
где: L – длина хода сверла
n – частота вращения шпинделя
S – подача
- для шлифования
где: L – длина хода круга
i – число проходов
n – частота вращения детали
Sn – продольная подача
B – ширина шлифовального круга
Кз – 1,2... 1,7 – коэффициент зачисных ходов
- для наплавки
где: G – вес наплавленного металла
I – сила тока
ан – коэффициент наплавки
- для хромирования
где: h – толщина стоя покрытия.
y – плотность электролитического хрома (y = 6,9…7,1 г/см3 )
Е – электрохимический эквивалент (Е = 0,323 г/Ач)
Д – плотность тока на катоде (табл.31)
η – выход металла то току (η = 0,12…0,18)
2. Определить вспомогательное время (на все переходы) по формуле:
где: tB1 - время на установку детали.
tB2 - время, связанное с переходом.
3. Определить оперативное время по формуле:
где ΣΤ0 - сумма основного времени всех переходов.
4. Определить дополнительное время по формуле:
где: к = 0,08 - для токарной обработки,
к = 0,09 - для шлифования,
к = 0,06 - для сверления.
5. Определить штучное время по формуле:
6. Определить техническую норму времени по формуле:
где ΤΠ3. - подготовительно-заключительное время, n – кол-во деталей в партии. |
Таблица 29
Основные параметры пористого хромирования электролитическим способом
Вид пористого покрытия | Состав электролита, г/л | Режим | ||
хромирования | анодного травления | |||
Точечный | СгОз = 250-300 H2S04 = 2,5-3 | D = 45 t = 50-52 | D = 40 t = 50 T =10-12 | |
Канальчатый | СгОз = 250 H2S04 = 2 | D = 50 t = 58-60 | D = 40 t= 58-60 T = 6-8 | |
Примечание. D – плотность тока в а/дм2; t – температура в оС; Т – продолжительность травления, мин. | ||||
|
Таблица 30
Типы ванн для хромирования
Тип ванн по концентрации электролита | Содержание в воде, г/л | Назначение покрытия | |
СгОз | H2S04 | ||
Низкая (разведенная ванна) | 150-200 | 1,5-2 | Для восстановления изношенных деталей |
Средняя (универсальная ванна) | 200-250 | 2-2,5 | Для износостойкого и декоративного хромирования |
Высокая (концентрированная ванна) | 350-450 | 3,5-4,5 | Для декоративного хромирования |
Таблица 31
Данные для выборов режима хромирования (состав электролита ванны: СгОз = 150 г/л; H2S04 = 1,5 г/л)
Условия работы деталей | Вид осадка | Режим хромирования |
Неподвижные сопряжения (шейки валов под прессовые и подшипниковые посадки) | Блестящий и молочный. Толщина слоя 0,05-0,3 мм (на сторону) | D = 30 t = 45-50 |
Хромированная поверхность детали работает на истирание при нагрузках до 5 кгс/см' | Блестящий. Толщина слоя 0,08-0,12 мм (на сторону) | D = 50 t = 50-55 |
То же, при нагрузках 5-20 кгс/см2 | Блестящий. Толщина слоя 0,05-0,1 мм (на сторону) | D = 20-30 t = 50-55 |
Молочный | D = 35-40 t = 60-65 | |
То же, при динамических нагрузках и давлениях свыше 20 кгс/см2 | Молочный. Толщина слоя 0,03-0,05 мм (на сторону) | D = 30-40 t = 60-65 |
Примечание. D – плотность тока, А/дм2; t – температура, оС |
Таблица 32
Электролиты для осталивания
Состав электролита, г/л | Тип электролитов | ||
Хлористое железо Соляная кислота | 680 0,8-1 | 0,6-0,8 | 200-250 0,8-1,2 |
Таблица 33
Таблица 34
Таблица 35
Таблица 36
Режимы металлизации
Параметры режима при диаметре проволоки 2 мм и давлении воздуха 6 кгс/см" | Содержание углерода в проволоке, % | ||
0,07-0,3 | 0,3-0,5 | 0.5-0,8 | |
Напряжение, В Величина тока, А Расстояние от сопла до детали, мм Скорость подачи проволоки, м/мин | 25 40 50 0,9 | 25-30 40-50 1,2 | 50-70 75-100 1,5-2,5 |
|
Таблица 37
Режимы металлизации
Диаметр (начальный) детали, мм | Межоперационные припуски на сторону, мм | ||||
на обточку без последующего шлифования | на обточку с последующим шлифованием | на шлифование без предварительной обточки | |||
общий | на обточку | на шлифование | |||
До 50 50-75 75-100 100-125 125-150 Более 150 | 0,6 0,65 0,7 0,8 0,9 1,0 | 0,75 0,8 0,9 1,0 1,15 1,25 | 0,6 0,65 0,7 0.8 0,9 1,0 | 0,15 0,15 0,2 0,2 0,25 0,25 | 0,4-0,45 0,45-0,5 0,5-0,57 0,57-0,65 0,65-0,72 0,8-0,85 |
Таблица 38
Таблица 39
Таблица 40
Таблица 41
Таблица 42
Таблица 43
Подачи при подрезке, мм/об
Чистота обработки | Диаметр обрабатываемой детали, мм | ||||
V1-V3 ' V4-V6 | 0,15-0,25 0,15-0,2 | 0,25-0,4 0,2-0,3 | 0,35-0,5 0,25-0,35 | 0,45-0,6 0,35-0,5 | 0,6-0,8 0,4-0,6 |
Таблица 44
Таблица 45
Скорость резания, м/мин при продольном обтачивании с охлаждением углеродистой стали σΒ = 45 кгс/мм (резцы из быстрорежущей стали)
Подача, мм\об | Глубина резания не более, мм | |||||||
0,5 | 1,5 | |||||||
0,1 | - | - | - | - | - | - | ||
0,2 | - | - | - | - | ||||
0,3 | - | - | - | - | ||||
0,4 | - | |||||||
0,5 | - | |||||||
0,6 | - | |||||||
0,7 | - | |||||||
0.8 | - | |||||||
0,9 | - | - | - | - | ||||
- | - | - | - |
Таблица 46
Скорость резания, м/мин при отрезке и прорезке без охлаждения углеродистой стали σΒ = 60 кгс/мм2 (резец из быстрорежущей стали)
Подача, мм/об | 0,04 | 0.06 | 0,08 | 0,1 0,2 | 0.3 | 0,4 |
Скорость резания, м\ мин | 32 21 |
Таблица 47
Поправочные коэффициенты км на скорость резания в зависимости от материала обрабатываемой детали
Углеродистая сталь с пределом прочности, кгс/мм2 | Легированная сталь с пределом прочности, кгс/мм2 | Чугун (работа без охлаждения) твёрдостью, НВ | ||||||||||
0,75 | 0,65 | 0,45 | 0,35 | 0,7 | 0,5 | 0,4 | 0,25 | 0,9 | 0,6 | 0,5 | 0,3 |
Таблица 48
Поправочный коэффициент кх на скорость резания в зависимости от характера заготовки и состояния ее поверхности
|
Характер поверхности | Обрабатываемый материал | |||
чугун с твердостью, НВ | стальное литье и поковки | |||
До 160 | 160-200 | 200-240 | ||
Чистая Загрязненная | 0,7 0,5 | 0,85 0,5 | 0,9 0,5 | 0,85 0,75 |
Таблица 49
Поправочный коэффициент кох на скорость резания при работе без охлаждения
Вид обработки | Обрабатываемый материал | Поправочный коэффициент Кох |
Черновое обтачивание Черновое обтачивание | Сталь и стальное литье Ковкий чугун | 0,8-0,9 0,85-0,9 |
Чистовое обтачивание | Все материалы | 0,9-0,95 |
Таблица 50
Рекомендуемые варианты обработки цилиндрических отверстий
Класс точности отверстий | Размер Отверстия, мм | Отверстия в сплошном материале | Отверстия прошитые и отлитые |
- | Сверление без кондуктора | Расточка | |
≤ 30 | Сверление и зенкерование | - | |
> 30 | Сверление и зенкерование или сверление и расточка | Расточка черновая и черновая | |
≤ 25 | Сверление и зенкерование | ||
3 и 3 а | > 20 д/стали | Сверление и расточка или сверление, зенкерование и развертывание | _ |
> 25 д/чугуна | Сверление и две расточки или сверление, зенкерование и шлифование | Две расточки или две расточки и развертывание или шлифование | |
≤ 12 | Сверление и одно- или двукратное ~ развертывание | - |
Продолжение таблицы 50
Класс точности отверстий | Размер отверстия, мм | Отверстия в сплошном материале | Отверстия прошитые и отлитые |
2 и 2а | >12 | Сверление, зенкерование и одно- или двукратное развертывание или: сверление, зенкерование и шлифование | Две расточки и одно- или двукратное развертывание; две расточки и шлифование |
Таблица 51
Величина врезания и перебега (l1 + I2) при токарной обработке
Наименование резцов | Глубина резания, мм | |||||||
-Проходные и расточные | ||||||||
Подрезные и отрезные Резьбовые | От 2 до 5 2-3 шага резьбы |
Таблица 52
Основное времяна обточку фасок, мин
Диаметр детали, мм | Ширина фаски, мм | |||
2 | ||||
0,05 | 0,1 | 0,13 | - | |
0,14 | 0,27 | 0,36 | 0,5 | |
- | 0,48 | 0,6 | 0,8 | |
- | 0,62 | 0,75 | ||
- | - | 0.94 | 1.2 | |
- | - | - | 1.28 | |
- | - | - | 1,42 | |
- | - | - |
Таблица 53
|
Вспомогательное время на установку и снятие детали, мин (количество деталей в партии n = 4-10 шт.)
Способ установки | Длина детали, мм | Все детали, кг при работе | ||||||||
вручную | с подъемником | |||||||||
до 5 | 5-15 | 15-30 | до 50 | 50-80 | 80-120 | 120-200 | 200-300 | 300-500 | ||
В центрах | До 1000 | 0,9 | 1,5 | 1,8 | 2,8 | 3,2 | 3,5 | 3,8 | 4,1 | |
В центрах с люнетом | До 1000 До 2000 | 1,2 1,3 | 1,9 2,2 | 2,4 2,8 | - 4,3 | - 4,9 | - 5,4 | - | - 6,6 | - - |
Продолжение таблицы 53
В центрах на гладкой оправке | Любая | 1,3 | 1,9 | 2,3 | - | - | - | - | - | |
В центрах на оправке с гайкой | Любая | 1,6 | 2,4 | 2,8 | - | - | - | - | - | - |
В 3-кулачковом патроне | Без выверки С выверкой | 0,8 1,3 | 0,9 1,8 | 2,2 | - | - | - | - | - | - |
В 3-кулачковом пат- роне с поджатием центром задней бабки | Более 5 d | 0,9 | 1,3 | 1,5 | - | - | - | - | - | - |
В 3-кулачковом патроне с люнетом | До 1000 Свыше 1000 | 0,9 - | 1,4 1,8 | 1,7 2.2 | - - | - - | - - | - - | - - | - - |
В 4-кулачковом патроне с люнетом | До 1000 До 2500 | - - | 5,3 ~ | 6,3 ~ | 9,2 - | 11,8 - | 12,1 | 16,7 | 17,5 | |
На планшайбе с креплением болтами и планками | Средней сложности | 6,3 | 7,7 | 10,8 | 17,5 | |||||
В 4-кулачковом патроне | Простая Средней сложности Сложная | 2.2 3,2 5.4 | 3,3 4.9 7,3 | 3,9 5,8 8,4 | 10,8 | 7,2 10,5 13 | 8,3 11.9 15,5 | 13,4 18,5 | 11.8 15,5 | 18,5 |
На планшайбе с угольником | Простая Средней сложности Сложная | 3,8 5,9 9,2 | 5,3 8,3 13 | 6,3 10 15 | 8,3 12 18,5 | 14,5 21 | 11,7 17 23 | 13,8 | ||
В 4-кулачковом патроне с поджатием центром задней бабки | 1000-2500 | - | - | - | - | 9,6 | 10,7 | 13,7 | 15,5 |
Таблица 54
Вспомогательное время, мин, связанное с переходом (на один проход)
Наименование перехода (операции) | Высота центров, мм | ||
Обточка или расточка по 3-му классу точности на первый проход | 1,1 | 1,3 | |
То же, по 4-5-му классу точности: на первый проход на последующие проходы | |||
0,6 | 0,7 | 0,9 | |
0,2 | 0.3- | 0.4 | |
Подрезка или отрезка | 0.2 | 0,3 | 0,3 |
Обточка фасок и радиусов | 0,1 | 0,1 | 0,1 |
Нарезание резьбы резцов | 0,05 | 0,05 | 0,1 |
Сверление и центровка | 0,7 | 1,0 | 1,5 |
Примечание. В таблице указано время на выполнение всех приемов, связанных с проходом. |
|
Таблица 55
Подготовительно-заключительное время при токарной обработке, мин
Сложность работы | Высота центров, мм | |
до 200 | свыше 200 | |
Простая работа (болты, втулки и др.) Работа средней сложности (валы, шестерни, фланцы, катки и др.) Сложная работа (корпусы, блоки и др.) |
Таблица 56
Скорость резания в м/мин при нарезании резьбы машинными метчиками из стали Р9 и Р18 с охлаждением
Диаметр нарезаемойрезьбы, мм | Шаг резьбы, мм мм | ||||||
0.5 | 0,75 | 1,25 | 1,5 | ||||
3-6 | - | - | - | - | |||
8-10 | . - | - | |||||
12-16 | - | ||||||
18-24 | - | ||||||
27 и более | - | - |
Таблица 57
Продолжение таблицы 57
Шаг резьбы,мм | Обрабатываемый материал | |||||
углеродистые стали | легированные стали | чугун, бронза, латунь | ||||
Число проходов | ||||||
черновых | чистовых | черновых | чистовых | черновых | чистовых | |
2-3 3,5-4,5 5-5,5 | 6 7 8 9 | 3 4 4 4 | 9 10 12 | 4 5 5 5 | 6 6 6 6 |
Таблица 58
Скорости резания при нарезании метрической резьбы резцами из быстрорежущей стали, м/мин (работа с охлаждением)
Шаг резьбы, мм | Проходы | ||
черновые | чистовые | зачистные | |
До 2 | |||
Примечание. При нарезании внутренней резьбы указанную в таблице скорость следует умножить на коэффициент 0,8. |
Таблица 59
Таблица 60
Скорости резания, м/мин при нарезании трапецеидальных наружных резьб быстрорежущими резцами (материал детали - конструкционная сталь, работа с охлаждением сульфофрезолом)
Проходы | Шаг резьбы, мм | ||||||||
до 5 | |||||||||
Черновые Чистовые Зачистные | 57 64 | 32 64 4 | 25 64 4 | 21 64 | 18 63 | ||||
Таблица 61 Скорости резания и числа проходов при нарезании червяков резцами
Модуль червяка в мм | Материал резца | ||
Т15К6Т | Р18 | ||
Стойкость, мин | |||
Скорость резания, м/мин | |||
150-160 | 20-25 | 50-60 | |
Число проходов | |||
черновых | чистовых | ||
7-9 | |||
10-12 | |||
14-16 | |||
16-19 | |||
20-24 |
Таблица 62
Подачи и скорости резания при черновом фрезеровании стали с пределом прочности σΒ = 65-75 кГ/мм2 цилиндрическими фрезами из быстрорежущей стали
Ширина фрезеро-вания, мм | Диаметр фрезы, мм | Число зубьев | Подача, мм/зуб | Скорости резания, м/мин при глубине резания, мм | |||
2 | 3-4 | 5-6 | 8-10 | ||||
30-60 | 0,2-0,3 | 41-44 | 35-39 | 31-34 | - | ||
45-90 | 0,3-0,4 | 45-46 | 37-41 | 33-36 | 32-36 | ||
50-90 | 0,3-0,4 | 48-50 | 40-44 | 36-41 | 34-39 | ||
50-100 | 0.2-0,3 | 56-59 | 47-53 | 42-47 | 36-41 |
Таблица 63
Таблица 64
Таблица 65
Таблица 66
Вспомогательное время, связанное с переходом (на один проход) при фрезеровании
Наименования проходов | Время, мин |
На первый проход при чистоте обработки 6 | 1,9 |
То же 4 | 1,5 |
На последующие проходы | 0,3 |
То же, с делением при помощи делительной головки | 0,4 |
Таблица 67
Таблица 68
Таблица 69
Скорости резания при фрезеровании пазов в углеродистой конструкционной стали с пределом прочности σ„ = 60 кгс/mm2дисковыми фрезами из стали Р9 с охлаждением
Диаметр фрезы, мм | Подача, мм об, не более | Глубина паза, мм. не более | ||||
Скорости резания, м/мин | ||||||
1,28 | - | |||||
0,8 | - | |||||
0.42 | - | |||||
0.32 | - | |||||
Продолжение таблицы 69
Диаметр фрезы, мм | Подача, мм/об, не более | Глубина паза, мм, не более | |||
Скорости резания, м/мин | |||||
1,44 0,8 0,54 0,35 | 49 52 59 64 | 39 42 48 | 35 37 42 46 | 32 35 38 41 | |
1,6 0.6 0,4 | 50 53 60 65 | 39 43 49 | 36 38 42 | 33 35 39 42 | |
ПО | 1,76 1,1 0,66 0,44 | 52 54 61 66 | 40 43 50 | 86 38 43 48 | 33 36 39 43 |
Таблица 70
Таблица 71
Таблица 72
Таблица 73
Глубина резания в мм и число проходов при нарезании цилиндрических зубчатых колес дисковыми модульными фрезами (материал фрезы - быстрорежущая сталь Р18 или Р9)
Модуль, мм | Диаметр фрезы, мм | Фрезерные станки | Зубофрезерные станки | ||||
Проходы | |||||||
1-й | 2-й | 3-й | 1-й | 2-й | 3-й | ||
2 | 4,33 | - | - | 4,33 | - | - | |
2,5 | 5,42 | - | - | 5,42 | - | - | |
6,5 | - | - | 6,5 | - | - | ||
3.5 | 7,58 | - | - | 7,58 | - | - | |
8,67 | - | - | 8,67 | - | - | ||
10,83 | - | - | 10,83 | - | |||
- | - | - | - | ||||
2.2 | - | 15,2 | - | - | |||
ПО | 4,32 | - | 17,32 | - | - | ||
6,5 | - | 19,5 | - | - | |||
8,67 | - | 21,67 | - | - | |||
- | - | ||||||
4,33 | 17,33 | - | |||||
6,5 | 12,5 | - |
Таблица 74
Подача в мм/мин при нарезании зубьев цилиндрических колес дисковой модульной фрезой
Обрабатываемый материал | Модуль, мм | |||||||||
2 | 10 | |||||||||
Сталь 45; 50 Сталь 40Х; 50Г Сталь ЗОХГТ; 12ХНЗА; ЗОХГС Чугун серый | 190 130 76 285 | 155 106 62 230 | 134 92 54 200 | 120 82 48 180 | 44 164 | 90 70 41 150 | 90 65 38 140 | 89 61 | 84 58 34 127 | 77 52 31 116 |
Таблица 75
Скорости резания, м/мин при нарезании зубьев цилиндрических колес дисковой модульной фрезой
Характер обработки | Обрабатываемый материал | |||
сталь марок | чугун серый | |||
40; 50 | 40Х; 18ХГТ | 12ХНЗА; 30ХГТ | ||
Нарезание: черновое чистовое | 32 40 | 23 27 |
Таблица 76
Таблица 77
Таблица 78
Таблица 79
Подача So, мм/об при обработке прямобочных шлицевых валов червячными фрезами
Размеры обрабатываемого вала, мм | Черновая обработка под шлифование | Чистовая обработка по сплошному материалу (V6) | |
диаметр | высота шлицов | ||
14-28 30-52 54-70 72-82 | 1,5-2.5 2-3 3-4 | 1,7 1,8 2,1 | 0,6 0,6 0,8 0,8 |
Таблица 80
Поправочные коэффициенты км на подачу и скорость резания при обработке прямобочных шлицевых валов
Марка стали | НВ | Поправочный коэффициент км | |
на подачу | на скорость резания | ||
45; 35Х; 45 и 30ХГТ 30; 12ХНЧА; 20ХНМ; 10ХГТ; 20Х 18ХНВА; 30ХМОА; 5ХНМ | 156-187 170-207 156-241 156-229 158-229 | 1 0,9 0,9 0.8 | 1,1 0,8 0,9 0.8 |
Таблица 81
Скорости резания ν в м/мин при обработке прямобочных шлицевых валов фрезами из быстрорежущей стали Р18
Характер обработки | Подача s0, мм/об фрезы | Высота шлицев И, мм | |||||
Чистовая | 0,5 0,6 0,8 | 45 41,5 36 | 24,5 21,5 | 18,7 14,8 | 14 12,8 11,1 | 11 10,1 8,8 8 | 9,2 |
Черновая | 1 1,3 1,6 | 48 42 38 34 | 22,5 20,5 | 20 17,5 15,7 14,1 | 15 13,2 12 10,6 | 12 10,3 9,3 8,4 | 10,5 9,4 8,4 7,6 |
Таблица 82
Поправочные коэффициенты кш на скорость резания в зависимости от количества шлицев
Количество шлицев | ||||||
Коэффициенты кш | 0,85 | 1,1 | 1,2 | 1,4 | 15 |
Таблица 83
Таблица 84
Таблица 85
Таблица 86
Вспомогательное время на операцию, мин
Способ обработки | Число одновременно уста- навливаемых деталей | Вес детали, кг | |||||||
5 | |||||||||
При работе на зубофрезерных станках | |||||||||
В один проход методом: вертикальной по- дачи | 1,05 | 1Д5 | 1,25 | 3,5 | 6,8 | ||||
1.55 | 1,75 | 4,4 | . | ||||||
1,85 | 2,1 | _ | - | - | . | ||||
поперечной подачи | 1,2 | 1,3 | 1,4 | 3,6 | 4,1 | 6,2 | |||
В два прохода методом вертикальной подачи | 1,95 | 2,05 | 2Д5 | 5,1 | 12 | 8,1 | |||
2,45 | 2,55 | 2,55 | 2,85 | 7,5 | 8,3 | ||||
2,75 | - | - | - | - | - | ||||
При работе на зубодолбежиых станках | |||||||||
В один проход | 1,05 | 1,2 | 1,35 | - | - | - | - | ||
1,45 | 1,85 | 1,8 | - | - | - | - | |||
1,75 | 2,2 | - | - | - | - | ||||
При работе на зубострогальных станках | |||||||||
В один проход | 1,05 | 1,15 | 1,75 | - | - | - | - | ||
В два прохода | 1,15 | 1,25 | 1,35 | - | - | - | - | ||
Таблица 87
Подготовительно-заключительное время при работе на зуборезных станках, мин
Способ установки детали | Наибольший модуль т, мм нарезаемого колеса | |||
На зубофрезерных станках - | ||||
На оправке, укрепленной в конусе стола | ||||
На переходной втулке без крепления на столе | - | |||
На зубодолбежных станках | ||||
На оправке или в приспособлении | ||||
На зубострогальных станках | ||||
На оправке с регулировкой резцовых головок | ||||
Таблица 88
Таблица 89
Скорости резания при строгании и долблении стали с σΒ = 50+65 hzc/mm* (резец из стали Ρ18)
Подача за двойной ход, мм | Скорости резания, м/мин при глубине резания, мм | |||||
5 | ||||||
0,2 | ||||||
0,4 | ||||||
0.6 | ||||||
1,5 | - | |||||
- |
Таблица 90
Таблица 91
Вспомогательное время, мин на установку и снятие детали
Способ установки | Характер выверки | Зес детали, кг | |||||
5 | |||||||
В тисках | Простая Средней сложности | 1,1 1.5 | 1,4 1.9 | 1,6 2,3 | 1,9 2.7 | 2.2 3,2 | 2,2 3,2 |
На столе с креплением | Простая Средней сложности | 1,4 2,6 | 1,7 3,2 | 2,1 4 | 2,6 4,8 | 3,1 5.8 | 3,6 6.8 |
Таблица 92
Вспомогательное время, мин, связанное с переходом (на один проход)
Наименование проходов и точность обработки | Время |
Первый проход: по 3-му классу по 4-5-му классам Последующие на один проход | 1,7 1,3 0,5 |
Таблица 93
Подготовительно-заключительное время, мин при работе на поперечно-строгальных и долбежных станках
Способ установки детали | Наибольшая длина хода ползуна, мм | |
В станочных тисках На столе с креплением двумя болтами с планками На угольнике с выверкой В приспособлении | 9 8 15 18 |
Таблица 94
Подача, мм/об при сверлении и рассверливании отверстий спиральными сверлами
Диаметр сверла, мм | Диаметр предварительного сверления, мм | Обрабатываемый материал | |||
сталь, σ„, кгс/мм' | Чугун сНВ | ||||
до 200 | свыше 200 | ||||
При сверлении | |||||
- | 0,15 | 0,51 | 0,27 | 0,22 | |
- | 0,18 | 0,14 | 0,35 | 0.22 | |
10-12 | - | 0,22 | 0,16 | 0,4 | 0,3 |
- | 0,22 | 0,16 | 0,4 | 0,24 | |
- | 0,19 | 0,14 | 0,35 | 0,21 | |
- | 0,14 | 0,1 | 0,25 | 0,15 | |
- | 0,11 | 0,08 | 0,21 | 0,12 | |
- | 0,09 | 0,07 | 0,17 | 0,1 | |
При рассверливании | |||||
0,4 | 0,3 | 0,7 | 0,6 | ||
0,45 | 0.4 | 0,9 | 0,7 | ||
0,45 | 0,4 | 0.9 | 0,8 | ||
0,3 | 0.2 | 0,8 | |||
0,4 | 0,3 | 0,8 | |||
0,2 | 0,15 | 0,65 | 0,4 | ||
. 0,4 | 0,6 |
Таблица 95
Скорость резания, м/мин при сверлении и рассверливании углеродистой конструкционной стали, σΒ = 60-r70 кгс/мм2 (сверло из стали Р9; без охлаждения)
Диаметр сверла, мм | Диаметр предварительного сверления, мм | Подача s, мм/об | ||||||||
0,08 | 0,1 | 0,12 | 0,15 | 0,2 | 0,3 | 0,4 | 0,6 | 0,8 | ||
При сверлении | ||||||||||
- | - | - | - | - | ||||||
- | - | - | - | |||||||
- | - | - | - | |||||||
- | - | - | - | - | ||||||
16-20 | - | - | - | - | - | - | ||||
24-30 | - | - | - | - | - | - | ||||
При рассверливании | ||||||||||
- | - | - | - | |||||||
- - | - - | - - | - - | |||||||
- - | - - | - - | - - | |||||||
- - | - - | - - | - - |
Таблица 96
Таблица 97
Скорость резания при зенкеровании стали σΒ = 55 кгс/мм зенкерами из быстрорежущей стали с охлаждением
Подачи, мм об | ||||||||
0.3 | - | - | - | - | - | - | - | |
0,5 | - | - | - | - | - | |||
0,6 | - | - | - | - | ||||
0,7 | - | - | - | |||||
0,8 | - | - | ||||||
- | - | |||||||
1.2 | - | - | ||||||
1,6 | - | - | - | < |
|
|
Индивидуальные очистные сооружения: К классу индивидуальных очистных сооружений относят сооружения, пропускная способность которых...
Наброски и зарисовки растений, плодов, цветов: Освоить конструктивное построение структуры дерева через зарисовки отдельных деревьев, группы деревьев...
Эмиссия газов от очистных сооружений канализации: В последние годы внимание мирового сообщества сосредоточено на экологических проблемах...
Семя – орган полового размножения и расселения растений: наружи у семян имеется плотный покров – кожура...
© cyberpedia.su 2017-2024 - Не является автором материалов. Исключительное право сохранено за автором текста.
Если вы не хотите, чтобы данный материал был у нас на сайте, перейдите по ссылке: Нарушение авторских прав. Мы поможем в написании вашей работы!