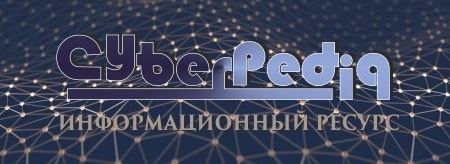
Механическое удерживание земляных масс: Механическое удерживание земляных масс на склоне обеспечивают контрфорсными сооружениями различных конструкций...
Эмиссия газов от очистных сооружений канализации: В последние годы внимание мирового сообщества сосредоточено на экологических проблемах...
Топ:
Комплексной системы оценки состояния охраны труда на производственном объекте (КСОТ-П): Цели и задачи Комплексной системы оценки состояния охраны труда и определению факторов рисков по охране труда...
Установка замедленного коксования: Чем выше температура и ниже давление, тем место разрыва углеродной цепи всё больше смещается к её концу и значительно возрастает...
Интересное:
Наиболее распространенные виды рака: Раковая опухоль — это самостоятельное новообразование, которое может возникнуть и от повышенного давления...
Мероприятия для защиты от морозного пучения грунтов: Инженерная защита от морозного (криогенного) пучения грунтов необходима для легких малоэтажных зданий и других сооружений...
Отражение на счетах бухгалтерского учета процесса приобретения: Процесс заготовления представляет систему экономических событий, включающих приобретение организацией у поставщиков сырья...
Дисциплины:
![]() |
![]() |
5.00
из
|
Заказать работу |
|
|
df = d -2.5mn = 163 – 2.5*1.5=159.25мм. (2.35)
2) Определяем длины участков входного вала.
Зазор между колесом и внутренней стенкой корпуса по таблице 10.4(1):
(2.36)
где - толщина стенки основания корпуса, находится по формуле:
(2.37)
Принимаем , подставляя в (2.36)
Принимаем
Рассчитываем размер гнезда подшипника
, (2.38)
где к1 – ширина фланца разъема корпуса, находится по формуле
(2.39)
где d'2 –диаметр стяжных болтов, находим по формуле:
(2.40)
где d'1 –диаметр фундаментных болтов, определяется по формуле:
(2.41)
Принимаем болты М16, значение подставляем в формулу (2.40):
По ГОСТ 7808 – 76 принимаем болты М12, при этом:
,
L = 6,5 + 36 + 3 = 45,5 мм.
Принимаем накладные крышки гнезд подшипников. Толщина фланца крышки h1 =12мм. Толщина прокладок Между торцом муфты и крышкой подшипника оставляем зазор h = 8мм. Длина L2 шейки вала с номинальным диаметром d = 35мм, отодвигая подшипник от стенки на
:
(2.42)
Длину вала L1 с d = 32мм принимаем равной длине ступицы муфты:
= 138 – 80 – 3 = 55мм (2.43)
Длину участка d4 определяем из чертежа. Правый подшипник входного вала по условиям унификации принимаем таким же как и левый, и устанавливаем симметрично
относительно шестерни.
3) Конструируем выходной вал с опорами и колесом.
Ранее найден диаметр d7 = 67мм. По расчетам приведенным ниже, принята зубчатая
муфта d5 = 45мм. Учитывая фаску в отверстии муфты 1,5мм, принимаем диаметр вала
под уплотнение и подшипник d6 =65мм.
Правый и левый подшипники принимаем одинаковыми. Намечаем шарикоподшипники
средней узкой серии № 313: d = 65мм, D = 140мм, В = 33мм. По таблице 8.3 (1) d8 = 74мм.
Расстояние между подшипниками в средней опоре 3=5мм и зависит от способа крепления подшипников на валах. Ширину буртика диаметром d8 принимаем
. Длина шейки d7 определяется длиной l ступицы колеса. Учитывая рекомендации, назначаем l = b2 = 102мм, где b2 – ширина колеса. Причем отношение
находится в рекомендуемых пределах. Центровка колеса на валу обеспечивается прессовой посадкой и прижимом ступицы к буртику вала при запрессовке.
|
Размер l проверяем по условию передачи крутящего момента.
Назначаем посадку и проверяем возможность передачи момента только за счет по
садки. По таблице 3.7 (4) минимальный натяг посадки = 31мкм.
Давление на поверхность посадки определяем по формуле:
(2.44)
где С1=0.7;
;
u = 1.2(RZ1 – RZ2) = 1.2(6+10) = 19мкм;
(2.45)
Тогда подставляя в 2.44:
Крутящий момент, который может передать посадка,
Запас сцепления:
(2.46)
Усиливаем прессовое соединение шпонкой. По таблице 2.29(1) выбираем шпонку
b = 16мм, h = 10мм. Рабочая длина шпонки:
, (2.47)
где принято [sсм] = 1500 кг/см2 с учетом прессовой посадки. Учитывая закругления
концов шпонки, получаем:
l = lp + b = 28.42 + 16 = 44.42мм (2.48)
По таблице 2.29(1) назначаем l = 45мм. Отмечаем, что длина ступицы достаточна для
размещения шпонки, так как b2 = 102мм.
Далее, по аналогии с входным валом определяем все недостающие размеры, учитывая,
что L = 45мм.
Принимаем d = 6.46 мм.
Δ ≥ 0,6d = 0,6 ∙ 6.46 = 3,88 мм
мм,
,
h1 = 13мм, Δ1 = 1,5мм, h = 8мм, Δ2 = 4,5 мм
L2 = L + Δ1 + Δ + h1 + h = 45.5 + 3.6 + 1.5 + 13 + 8 = 71.6
L1 = L1м – Lм – 3 = 115 – 55 – 3 = 57 мм.
4) Рассчитываем промежуточный вал
Ранее был найден диаметр под колесо d10 = 33.7 мм, d9 = 22 мм. Намечаем шарикоподшипник
средней узкой серии № 305: d=25 мм, D=62 мм, В = 17 мм.
Принимаем d9 = 25 мм, d10 = 30 мм. Диаметр d11 принимаем равным диаметру вершин
второй ступени:
d11 = da = dw1 + 2mn = 155 + 2 ∙ 2.5 = 160 мм (2.49)
Так как размер L остаётся одинаковым, то размеры d, D, остаются теми же.
Длина размера посадки колеса d10 принимаем b2= 17мм. Рассчитываем размер l по условию передачи крутящего момента аналогично выходному валу.
Назначаем посадку .
dр = 0,012мм, С1 = 0,7, С2 = 2,19.
(кг/м2)
Усиливаем шпонкой b = 12, h = 8
Назначаем l = lp + b = 15,4 + 12 = 27.4 мм, принимаем l = 28 мм
|
Длина ступицы l = 32мм, что достаточно для размещения шпонки.
Таблица 2.4.1
Геометрические размеры зубчатой передачи
Ступень | Параметр | |||||||
mn мм | Z1 | Z2 | d1 мм | d2 мм | ![]() | bw мм | ![]() | |
1.5 | ![]() | |||||||
2,5 | ![]() |
Рисунок 2.3.1. - Эскизная компоновка редуктора
2.5 Проверочный расчет зубчатых передач
Проверочный расчет на усталость по наименьшим напряжениям для второй ступени.
Находим окружную скорость по формуле:
(2.34)
По таблице 8.2(2) назначаем 9-10 степень точности. По таблице 8.3(2) находим коэффициент динамической нагрузки . Ранее был найден
. Находим коэффициент расчетной нагрузки:
= 1,09. 1,04 = 1,133 (2.35)
Принимая , находим контактные напряжения по формуле:
=
(2.36)
Выполняем проверочный расчет по напряжениям изгиба.
По графику рис.8.20(2) при значении коэффициента смешения Х = 0 находим значение коэффициента формы зуба:
для шестерни - YF1 = 3.70
для колеса - YF2 = 3.75.
Находим отношение :
;
.
Расчет выполняем по тому колесу пары у которого отношение меньшее. В нашем
случае расчет ведется по колесу. Находим по графику рис.8.15(2) коэффициент концентрации нагрузки . По таблице 8.3(2) находим коэффициент динамической нагрузки
. Тогда коэффициент расчетной нагрузки:
(2.37)
Находим окружную силу по формуле:
(2.38)
Находим напряжения изгиба:
(2.39)
Выполняем проверочный расчет на заданную нагрузку (допускаемые напряжения). Определяем максимальные контактные напряжения и напряжения изгиба:
(2.40)
(2.41)
Выполняем проверочный расчет на усталость по контактным напряжениям для первой ступени. Определяем окружную скорость:
(2.42)
По таблице 8.2(2) назначаем 8-ю степень точности. По таблице 8.3(2) находим коэффициент
динамической нагрузки Кнv = 1,05, по рис. 8.15 . Находим коэффициент расчетной
нагрузки по формуле (2.34):
По таблице 8.7 находим дополнительный коэффициент . Находим коэффициент
торцевого перекрытия:
(2.43)
Находится в рекомендуемых пределах .
Находим коэффициент повышения прочности косозубых передач:
(2.44)
.При находим контактное напряжение по формуле:
=
(2.45)
Выполняем проверочный расчет по напряжениям изгиба.
Находим число зубьев эквивалентной прямозубой шестерни и колес:
(2.46)
(2.46`)
По графику рис. 8.20(2) при Х = 0 находим YF1 = 3.69, YF2 =3.74. Находим отношения [
|
Для шестерни:
Для колеса: .
Расчет выполняем по наименьшему значению, т.е. по колесу.
По таблице 8.7 (2) коэффициент не равномерности нагрузки . Коэффициент учитывающий повышение изгибной прочности определяется по формуле:
(2.47)
Находим коэффициент повышения прочности:
(2.48)
По графику рис. 8.15(2) , по таблице 8.3 КFV = 1.11, тогда коэффициент расчетной
нагрузки определяем как:
Находим окружную силу по формуле (2.38):
Находим напряжение изгиба по формуле:
(2.49)
Заносим геометрические параметры зубчатой передачи в таблицу 2.4.1
2.6 Расчет (выбор) подшипников и уплотнений
Проверяем подшипники предварительно назначенные в пункте 2.3.
1) Подшипники выходного вала.
Были назначены радиальные, однорядные, шарикоподшипники средней узкой серии №313 с параметрами: динамическая грузоподъемность С = 72400Н, статическая С0 = 56700Н, L =20000ч, t < 100°C.
Находим реакции опор, для определения нагружения подшипника:
(2.50)
(2.51)
(2.52)
Знак ² - ² означает, что реакция В2 направлена в противоположную сторону.
(2.53)
Для левой опоры:
(2.54)
Правая опора:
(2.55)
Правый подшипник нагружен больше, поэтому выполняем только его расчет.
Отношение , находим по таблице 16.5(2) значения коэффициентов радиальной и осевой нагрузок: x = 1, y = 0. По рекомендации к формуле 16.29(2) принимаем коэффициент безопасности, учитывающий характер нагрузки Кб = 1.4, температурный коэффициент Кt =1, V коэффициент вращения, зависящий от того, какое кольцо вращается V = 1.
Находим постоянную радиальную нагрузку по формуле
(2.56)
По таблице 8.10(2) для 3 режима нагружения находим коэффициент Кне = 0,18. Находим эквивалентную долговечность по формуле:
(2.57)
Находим ресурс работы:
(2.58)
По таблице 16.3(2) находим значение коэффициента надежности а1 = 1, обобщенный коэффициент совместного влияния качества металла и условий эксплуатации а2 = 0,8.
Динамическая грузоподъемность:
(2.59)
Условие С < Сг выполняется, но паспортное значение С превышает потребное С0 на 30% < 60%, что допустимо.
Проверяем подшипник по статической грузоподъемности:
x0 = 0.6, y0 = 0.5, тогда
(2.60)
Условие Р0 [С0 соблюдается.
|
2) Подшипники входного вала.
Проверку проводим аналогично проверке выходного вала.
Используется подшипник №307. Параметры: С = 26200 Н, С0 = 17900Н, L = 20000 ч.
Реакции опор:
Для опоры А и В:
Правый подшипник нагружен больше.
V = 1, тогда:
При этом: x = 1, y = 0, Kб = 1,4, Kt = 1, Kне = 0,18.
а1 = 1, а2 = 0,8
Разница составляет 12%, что допустимо.
Находим при статической нагрузке: хо = 0,6, уо = 0,5
Условие Р0 [С0 соблюдается.
3) Подшипники промежуточного вала
Используется подшипник №305. Параметры: С = 17600 Н, С0 =11600 Н, L=20000 ч.
Реакции опор А и В:
Н
Для опор А и В:
Левый подшипник нагружен больше.
Принимаем x = 1, y = 0, Кб = 1.4, Кt = 1, Кне = 0,18.
а1 = 1, а2 = 0,8
Разница составляет 57%, что допустимо
x0 = 0.6, y0 = 0.5
Условие Р0 [С0 соблюдается.
Значения расчета заносим в таблицу 2.6.1
Таблица 2.6.1
Паспортные и расчетные значения нагрузок подшипников
Подшипники | Параметр | |||
Сг, Н | Сп, Н | С0, Н | Р0, Н | |
Входной вал №307 | ||||
Промежуточный вал №305 | 7625,6 | |||
Выходной вал №313 |
2.7 Конструирование и проверочные расчеты валов на прочность, жесткость и колебания
1) Рассчитываем выходной вал.
Для выходного вала рассчитаны следующие величины: Т3 =2800 Нм, n3 = 31 об/мин,
b2 = 102 мм, sв=850 мПа, [t] = 18 мПа, sт = 550 мПа.
Определяем силы в зацеплении.
Диаметр в месте посадки колеса d = 53 мм. Допускаемая радиальная нагрузка при использовании редуктора для общего назначения:
(2.61)
Определяем соответственно окружную, осевую и радиальную силы в зацеплении по формулам:
(2.62)
(2.63)
(2.64)
Из компоновочной схемы находим размеры пролетов: а = 66 мм, b = 70 мм, с = 131 мм. Вычерчиваем расчетную схему вала (рис. 2.1) с соответствующими размерами и строим эпюру от приложенных сил.
Определяем моменты сил по формулам.
Момент от радиальной силы:
(2.65)
Рисунок 2.7.1.-Эпюра нагрузки выходного вала
Моменты от окружной силы:
(2.66)
Моменты от силы муфты:
(2.67)
(2.68)
Просчитываем два предполагаемых опасных сечения: 1-1 – ослабленное шпоночным пазом и сечение 2-2 – ослабленное галтелью.
Для 1-1 изгибающий момент:
(2.69)
Для 2-2 изгибающий момент М»Fм × с = 8242 × 0,131 =1080 Нм,
Крутящий момент Т3 = 2800 Нм.
Больше напряженно второе сечение.
Расчет на прочность.
Предел выносливости.
= 0,4 × 850 = 340 МПа (2.70)
= 0,2 × 850 = 170 МПА (2.71)
Амплитуды переменных составляющих циклов напряжений.
Напряжения изгиба:
(2.72)
Напряжение кручения:
(2.73)
Коэффициенты, корректирующие влияние постоянной составляющей цикла напряжений на сопротивление усталости ys = 0,15 и yt = 0,1. Находим по таблице 15.1(2) эффективные коэффициенты концентрации напряжений при изгибе и кручении ks = 1,62 и kt = 1,3. По рис.15.5 (2) находим значения масштабного фактора kd = 0.7, по рис.15.6 (2) находим фактор шероховатости kF = 1. Находим запас сопротивления усталости по изгибу и кручению, по следующим формулам:
|
(2.74)
(2.75)
При совместном действии напряжений кручения и изгиба запас сопротивления усталости определяют по формуле:
(2.76)
.
Расчет на жесткость.
По условиям работы зубчатого зацепления опасным является прогиб вала под шестерней. Минимальный диаметр вала d = 45 мм.
Определяем момент инерции сечения по формуле:
(2.77)
Прогиб в вертикальной плоскости от силы Fr:
(2.78)
Прогиб в горизонтальной плоскости от силы Ft и Fм:
=
(2.79)
Суммарный прогиб:
(2.80)
Допускаемый прогиб [f]» 0,01m = 0,01 × 2 = 0,02<0.00486 мм.
Необходимое условие работы вала - f[[f] выполняется.
Расчет на критические колебания
(2.81)
Вал работает в до критической области.
2) Рассчитываем входной вал.
Расчет производим аналогично расчету выходного вала.
Параметры: Т2 = 95 Нм, n2 = 401 об/мин, d2 = 163 мм, b1 = 34 мм, sв = 850 МПа, [t]=18МПа,sт = 550МПа.
Определяем силы:
Размеры пролетов: а = 27мм, b = 32,5мм, с = 106,5мм, l = 59,5мм.
Определяем моменты сил (рис. 2.2):
Сечение 1-1.
Сечение 2-2.
Опасное сечение 2-2.
Расчет на прочность.
Рисунок 2.7.2.-Эпюра нагружения входного вала
Расчет на жесткость.
Е = 2,1 × 105МПа, d = 32мм.
Прогиб в вертикальной плоскости:
Прогиб в горизонтальной плоскости:
Суммарный прогиб:
Допускаемый прогиб вала [f] = 0,015 мм.
Необходимое условие работы вала - f[[f] выполняется.
Расчет на критические колебания.
Вал работает в до критической области.
3) Рассчитываем промежуточный вал.
Параметры Т¢2 = 332 Нм, d =25 мм, d12 = 301 мм, d22 = 280 мм, sв = 850 МПа, [t] = 18 МПа,
sт = 550 МПа.
Силы определяем для двух сечений (рис. 2.3):
1-1:
2-2:
Размеры пролетов а = 35мм, b = 80мм, с = 55мм, l = 170мм.
Определяем моменты сил.
1-1:
2-2:
Суммарные моменты:
1-1:
,
2-2:
Опасным является сечение 1-1.
Расчет на прочность.
Расчет на жесткость.
Е = 2,1 × 105МПа, d = 35мм.
Рисунок 2.7.3.-Эпюра нагружения промежуточного вала
Допускаемый прогиб [f] = 0,02 мм.
Необходимое условие работы вала - f[[f] выполняется.
Расчет на критические колебания.
Значения прогибов, запасов сопротивления усталости и критических скоростей заносим в таблицу 2.6.1
Таблица 2.7.1
Значения запасов сопротивления усталости, прогибов и критических скоростей.
Вал | Параметр | ||
S | f, м | n, об/мин | |
Входной | 4,95 | 3×10-4 | |
Промежуточный | 2,1 | 1,24×10-12 | 2,4×1014 |
Выходной | 4,86×10-3 | 61728,4 |
2.8 Расчет и конструирование корпуса и крепежных деталей
Основные размеры редуктора рассчитаны в п.2.3. Рассчитываем дополнительные размеры корпуса по следующим формулам и зависимостям.
Высота ребра корпуса Н принимаем равной 5мм. Толщина стенки у основания ребер l = 5
мм, литейный уклон 2°.Диаметр стяжных болтов Принимаем d3 = 12мм. Расстояние между стяжными болтами принимаем по таблице 10.4 (1) l3 = 120мм.
Фланцы разъема корпуса:
Толщина: S = 1.5d3 = 1.5×12=18мм
S1 = 1.3d3 = 1.3×12 = 15.6мм
Принимаем S1 равным 16мм.
Ширина: k1 = 3d3 = 3×12 = 36мм
Фундаментные лапы:
Толщина:S2 = 1.5d3 = 1.5 × 12 = 18мм
Ширина: k2 = 3d3 = 3 × 12 = 36мм.
2.9 Тепловой расчет и смазка редуктора
По рекомендации главы 9(1) выбираем глубину погружения колеса второй ступени на две высоты зуба, но не менее 10мм: 2*2,25mn = 2*2.25*2 = 9мм. (2.82)
Принимаем глубину 12мм с учетом ее уменьшения из-за разбрызгивания масла и прилипания его к стенкам корпуса и другим деталям.
Глубина погружения быстроходного колеса:
(2.83)
По значениям окружных скоростей колес (табл. 9.5(1)) находим соответствующую вязкость
масла: 180 сст. По таблице 9.1(1) выбираем по вязкости автотракторное масло АК-15.
Проводим тепловой расчет.
Находим тепловую мощность
(2.84)
где Р1 = 3960 Вт – мощность на входном валу.
h = 0,9752 – КПД зубчатой передачи.
Через стенки корпуса редуктора тепло передается в окружающую среду, тем самым происходит естественное охлаждение. Количество теплоты, отданной в секунду или мощность теплоотдачи:
(2.85)
где k – коэффициент теплоотдачи, принимаем k = 18 Вт/м2 ×°С,
А – площадь поверхности охлаждения:
(2.86)
где S1 = 0,920 × 0,250 = 0,23 м2 – площадь поверхности днища, которая учитывается, т.к. редуктор свободно обдувается воздухом.
S2 = 0,920 × 0,012 = 0,011 м2 - площадь боковой стороны редуктора соприкасаемая с маслом.
S3 = 0,250 × 0,012 = 0,003 м2 – площадь торцевой стороны редуктора соприкасаемая с маслом.
S4 = 0,005 × 0,3 × 2 = 0,003 м2 – площадь ребер охлаждения.
Подставляем значения в формулу (2.86):
А = 0,23+0,011+0,003+0,003 = 0,247 м2
t0 = 20°C – температура окружающего воздуха,
t1 = 90°C – внутренняя температура редуктора или температура масла.
Подставляем значения в формулу 2.85:
Необходимое условие выполнено.
Естественного охлаждения достаточно.
Удаление масла производится через сливную масленую пробку М24х1,5 ГОСТ 9833-73.
Контроль уровня масла производим с помощь трубчатого масло указателя Н = 210мм.
3. Расчет клиноременной передачи
По графику рис.12.23 (2) выбираем сечение ремня. Рекомендуют сечение Б. По графику рис.12.26 (2), учитывая рекомендацию 12.31(2), принимаем dр1= 250 мм и находим Р0=4.5 кВт. Рассчитываем геометрические параметры передачи: dр2= dр1.iрем=250.2.5=625 мм, по ряду Ra40 принимаем dр2=630 мм. По рекомендации 12.29(2) предварительно принимаем а9= dр2 =630мм. По формуле:
l=2.a+0.5(d1+d2)+(d1-d2)2 (5.1)
находим: l=2.630+0.53.14(630+250)+(630-250)2=2699 мм.
По таблице 12.2 принимаем l=2700 мм.
По формуле:
, (5.2)
где l - длинна ремня,l=2700 мм,
d1 и d2 - диаметры соответствующих шкивов, d1=630 мм и d2=250 мм,
а - межосевое расстояние,
уточняем:
По формуле:
a=1808-57(d2-d1)/a=1808-57(630-250)/627=1448 (5.3)
вычисляем угол обхвата ремня малого шкива. Значение находится в допускаемых пределах [см.рекомендации.12.29(2)]
По формуле:
Pp=P0.Ca.Cl.Ci/Cp, (5.4)
где Сa - коэффициент угла обхвата. Здесь Сa=0.87[см. стр.272(2)],
Сl - коэффициент длинны ремня, по рис.12.27(2) Сl=1.05,
Ci - коэффициент передаточного отношения, по рис.12.28(2) Ci=1.135,
Cp - коэффициент режима нагрузки, учитывая, что нагрузка с умеренными колебаниями, принимаем Cp=1.2,
определяем мощность Рр передаваемую одним ремнем:
Pp=4,5.0.87.1.05.1.135/1.2=3.94 кВт
По формуле:
Z=P/Pp.Cz, (5.5)
где P - мощность на ведущем валу передачи,
Cz - коэффициент числа ремней, Cz=1, так как 1 ремень,
определяем число ремней. Z=4/3.94.1=1,условие z[6 выполняется.
По формуле:
F0=0.85.P.CP.Cl!(Z.y.Ca.Ci)+Fy, (5.6)
где Fy=r.A.y2 - центробежная сила,
А - площадь сечения, А=138.10-6 м2,
r=1250 кг/м3,
y - скорость ремня при расчетной частоте вращения:
y=P.dp1.n1/60=3.14.0.25.960/60=12.56 м/с,
Fy=1250.138.10-6.12.5652.17 H,
находим предварительное натяжение ремня:
F0=0.85.4.103.1.2.1.05!(1.12.56.0.87.1.135)+2.17=348 H.
По формуле:
, (5.7)
сила, действующая на вал при b/2=(180-a)/2=(180-144)/2=18, в статическом состоянии передачи: Fr=2.348.cos1885662.4 H, при n5960 мин-1
Fr=662.4-2.Fr.Z=662.4-2.2.7.1=656.64 H
В нашем случае влияние центробежных сил мало.
Ресурс наработки ремней находим по формуле:
T=Tcp.k1.k2, (5.8)
где k1 - коэффициент режима нагрузки, k1=1,
Тср - ресурс наработки для эксплуатации при среднем режиме нагрузки, Тср=2000ч.,
k2 - коэффициент климатических условий, k2=1.
Т= Тср=2000ч.
4. Подбор, проверка и эскизная компоновка муфты
Подбираем муфту для соединения вала редуктора с валом приводного конвейера. По техническим характеристикам требующим обеспечения муфтой передачи крутящего момента Т = 2800Н×м, частоты оборотов n = 31об/мин, перекос валов 0°30¢, радиальное смещение 0,18мм, выбираем зубчатую муфту М3 60 (рис.3.2) с параметрами:
Т = 2900Н×м;
с размерами: b = 20мм, z = 40, D1 = 150мм, h = 7.5мм.
Муфта компенсирует все виды несоосности валов. Допускаемые муфтой смещения валов определяют из условия, чтобы углы между осью обоймы и осью одного или другого вала были не больше 0°30¢.
Коэффициент динамической нагрузки к = 1,7.
Проводим расчет прочности зубьев по формуле:
(3.2)
Принимаем [sсм] = 12... 15МПа
Условие работоспособности выполняются.([sсм]/ sсм)
Рисунок 3.1.-Эскиз зубчатой муфты
5. Расчет и проектирование узла исполнительного механизма (барабана)
Определяем размеры вала.
Диаметр выходного конца муфты d = 60мм, поэтому в этом месте принимаем вал такого же диаметра. Диаметр в месте посадки подшипников и уплотнений d = 65мм. Диаметр вала в месте посадки звёздочки принимаем d = 70мм. Барабан располагается симметрично относительно опор. В качестве опор принимаем самоустанавливающиеся сферические
подшипники № 1209, которые на валу закрепляются в осевом направлении. По рекомендации главы Vlll §9 (1) выбираем неразъемный корпус подшипника СИМ 100.
Выполняем проверочный расчет вала
Параметры: T = 2772 H × м, n = 31 об/мин, [t] = 18 Мпа, sв = 850 Мпа,sт = 550 Мпа.
Определяем силы (для звездочки Fa и Fv малы).
Размеры пролетов из чертежа: , с = 140мм.
Определяем моменты сил (рис. 4.1)
Сечение 1-1:
Сечение 2-2:
Опасное сечение 1-1.
Расчет на прочность.
Рисунок 5.1.-Эпюра нагружения рабочего органа(барабана)
Полученные значения находятся в рекомендуемых пределах.
Расчет на жесткость.
Необходимое условие работы вала - f[[f] выполняется.
Расчет на критические колебания.
Вал работает в до критической области.
Выполняем проверочный расчет подшипников.
Расчет выполняется аналогично расчетам подшипников редуктора.
Параметры выбранных подшипников №1209:
Сг = 17000 Н, С0 = 9770 Н, Ln = 20000 ч.
Реакции опор (рис. 4.1):
Правый подшипни
|
|
Архитектура электронного правительства: Единая архитектура – это методологический подход при создании системы управления государства, который строится...
Семя – орган полового размножения и расселения растений: наружи у семян имеется плотный покров – кожура...
Двойное оплодотворение у цветковых растений: Оплодотворение - это процесс слияния мужской и женской половых клеток с образованием зиготы...
История развития хранилищ для нефти: Первые склады нефти появились в XVII веке. Они представляли собой землянные ямы-амбара глубиной 4…5 м...
© cyberpedia.su 2017-2024 - Не является автором материалов. Исключительное право сохранено за автором текста.
Если вы не хотите, чтобы данный материал был у нас на сайте, перейдите по ссылке: Нарушение авторских прав. Мы поможем в написании вашей работы!