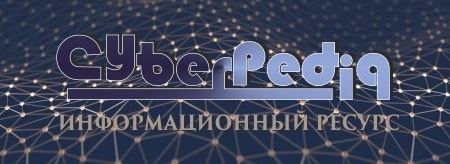
Типы сооружений для обработки осадков: Септиками называются сооружения, в которых одновременно происходят осветление сточной жидкости...
Своеобразие русской архитектуры: Основной материал – дерево – быстрота постройки, но недолговечность и необходимость деления...
Топ:
Определение места расположения распределительного центра: Фирма реализует продукцию на рынках сбыта и имеет постоянных поставщиков в разных регионах. Увеличение объема продаж...
Процедура выполнения команд. Рабочий цикл процессора: Функционирование процессора в основном состоит из повторяющихся рабочих циклов, каждый из которых соответствует...
Техника безопасности при работе на пароконвектомате: К обслуживанию пароконвектомата допускаются лица, прошедшие технический минимум по эксплуатации оборудования...
Интересное:
Отражение на счетах бухгалтерского учета процесса приобретения: Процесс заготовления представляет систему экономических событий, включающих приобретение организацией у поставщиков сырья...
Уполаживание и террасирование склонов: Если глубина оврага более 5 м необходимо устройство берм. Варианты использования оврагов для градостроительных целей...
Лечение прогрессирующих форм рака: Одним из наиболее важных достижений экспериментальной химиотерапии опухолей, начатой в 60-х и реализованной в 70-х годах, является...
Дисциплины:
![]() |
![]() |
5.00
из
|
Заказать работу |
|
|
Содержание
Введение 3
1. Специальная часть. 5
1.1 Сущность процесса резки. 5
1.2 Материалы, применяемые при резке. 8
2. Технологическая часть. 10
2.1 Оборудование и инструменты сварщика. 10
2.2 Режимы резки. 12
2.3 Виды дефектов сварных соединений. 14
2.4 Способы контроля сварных соединений. 28
2.5 Техника безопасности. 30
3. Литература 32
Графическая часть.
1. Схема процесса резки.
2. Оборудование для резки.
Введение.
Плазменная резка— вид плазменной обработки материалов, при котором в качестве режущего инструмента вместо резца используется струя плазмы.
Сама технология плазменной резки появилась уже очень давно, более 50 лет тому назад. Первые их установки появились примерно в 60-е года 20 века. Станки в свое время для процесса плазменной резки были настолько дорогие и громоздкие, что их позволяли приобрести только очень большие предприятия.
В начале 21 века плазменная резка для всех нас стала более доступной и более распространенной. Станки совершенствовались, становились все более удобными, компактными, продуктивными и самое главное дешевыми. В результате всего этого плазменная резка получила довольно широкое распространение в очень разных отраслях современного хозяйства, так как она решает множество задач первостепенной промышленной важности.
Плазменная резка, по сравнению с технологией газокислородной резки, гораздо проще. Поскольку она совершенно не требует постоянной заправки и доставки баллонов с газом. А также дорогих разных присадок для дорогих и ценных металлов либо же строжайшего соблюдения пожарной безопасности. Для такого вида резки нужно иметь в наличии только воздух и электроэнергию, а также сопла и электроды, которые являются самым распространенным расходным материалом.
|
Плазменная резка позволяет резать и толстые, и тонкие листы металла без лишних усилий. Металлы, которые доступны для резки в такой способ: медь, титан, алюминий, бронза и их сплавы (чугун, латунь, сталь). Порог критичной толщины материала для ручной резки составляет около 5 см, но для более мощных станков, которые находятся под управление компьютера можно использовать порог даже до 30 см. стали.
При всех этих плюсах и минусах плазменной резки, она остается лучше всех остальных способов реза металла. Даже тем, что после нее нет никакой деформации продукта, а заусенцы на металле можно легко и быстро убрать, плазменная резка занимает лидирующее положение в промышленном применении.
1.Специальная часть.
1.1 Сущность процесса резки.
Сущность технологии плазменной резки, принцип работы плазменной резки, заключается в локальном расплавлении металла и выдувании этого расплавленного металла при перемещении плазменного резака относительно разрезаемого металла, с образованием полости реза.
Технология плазменной резки является одним из наиболее экономически эффективных способов раскроя металла при толщинах металла от 1 до 50 мм. Преимущества плазменной резки:
1.УНИВЕРСАЛЬНОСТЬ. С помощью технологии плазменной резки режутся все типы металлов (чёрные, легированные (в т.ч. нержавеющие), сплавы алюминия, сплавы меди, титан и проч.);
2.ВЫСОКАЯ СКОРОСТЬ РЕЗКИ МЕТАЛЛА – портальная машина плазменной резки – например МТР «Юпитер», станки «Омега» и даже бюджетный станок для раскроя металла «Гермес»- может резать металл со скоростью до 12 метров в минуту;
3.МАЛАЯ ЗОНА ТЕРМИЧЕСКОГО ВОЗДЕЙСТВИЯ в области реза на разрезаемый лист металла;
4.ВЫСОКОЕ КАЧЕСТВО РЕЗА. Современные плазменные резаки (плазмотроны) в совокупности с правильным подбором плазмообразующих и охлаждающих газов обеспечивают минимальную ширину реза, крайне низкую конусность реза, чистые (без наплывов и грата) кромки, почти не требующие дополнительной обработки. Таким условиям отвечает прецизионная плазменная резка;
|
5.БЕЗОПАСНОСТЬ. При использовании технологии плазменной резки не используются горючие газы (пропан, ацетилен), которые используются пригазовой резке.
Принцип работы плазменной резки основан на использовании плазменной дуги постоянного тока прямого действия (электрод - катод, где разрезаемый металл – анод).
При образовании плазменной дуги нагретый электрической дугой до высокой температуры (порядка 25 000 °C) газ переходит в ионизированное состоянии – четвёртое агрегатное состояние вещества - плазму. Последнее означает, что этот газ утрачивает свойства диэлектрика и приобретает способность проводить электрический ток. В процессе резки плазменный поток становится проводником для тока, расплавляющего металл, и сам же его выдувает.
Для генерации и поддержания плазменной дуги используется специальное устройство, называемое плазменным резаком или плазмотроном.
Плазмообразующий газ (смесь газов, а при воздушно-плазменной резке - воздух), пройдя через канал внутри электродного узла и механизм закрутки (завихрения) образует вихревой газовый поток, закрученный вдоль продольной оси электрода плазмотрона и выходящий через геометрически соосный с ним канал сопла.
Рабочая дуга локально (в месте контакта) расплавляет металл и за счёт давления плазмообразующего газа и его высокой скорости истечения из сопла выдувает расплавленный металл из массива, образую полость реза. Таким образом, при перемещении плазмотрона (для обеспечения непрерывности контакта рабочей дуги с металлом) относительно листа, при соблюдении рабочего зазора между плазмотроном и листом металла, получается рез.
По способу возбуждения плазменной дуги плазмотроны делятся на два типа – осцилляторные и безосцилляторные.
Рассмотрим осцилляторный способ возбуждения дуги:
Осциллятор образует электрический потенциал для возникновения разряда между соплом и электродом плазмотрона. Разряд зажигает электрическую дугу. Возникая, она горит в промежутке электрод-сопло. Потоком воздуха выдувается через канал сопла наружу. Это дежурная дуга, ее ток составляет 20 – 60 А. Он определяется токоограничивающим резистром. Коснувшись металла, дежурная дуга шунтирует резистор. Далее, не контактируя с соплом, замыкается на металл. Аппарат плазменной резки начинает работать в режиме рабочей дуги. Поток воздуха, закрученный по спирали, стабилизирует и сжимает столб рабочей дуги. Он предотвращает касание электрической дуги стенок соплового канала плазмотрона.
|
1.2 Материалы, применяемые при резке.
Плазмообразующая среда должна обеспечивать наибольшую удельную тепловую мощность при заданном расходе газа и затраченной электроэнергии, а также позволять сконцентрировать полученную энергию в тонкий плазменный шнур и сосредоточить её на минимальном участке поверхности разрезаемого металла. Для этих целей подходят газы, химически неактивные по отношению к обрабатываемому металлу (аргон, азот их смеси с водородом), применяют также аммиак, гелий, смешанные газы; газы, химически активные по отношению к обрабатываемому металлу (кислород, часто в смеси с азотом, сжатый воздух, углекислый газ), иногда используется вода, которая превращается частично в пар, а частично диссоциирует на водород и кислород. Воду так же используют как добавку к основному плазмообразующему газу. Кроме того, вода может использоваться во время плазменной резки металла в качестве защитного «зонтика» (от излучения, шума, пыли и аэрозолей).
Таким образом, для образования плазмы используются газы:
· активные – кислород, воздух. Применяются при резке черных металлов
· неактивные – азот, аргон, водород. Применяются при резке цветных металлов и сплавов.
1. Сжатый воздух. Используется для резки:
· меди и ее сплавов – при толщине до 60 mm;
· алюминия и его сплавов – при толщине до 70 mm;
· стали – при толщине до 60 mm.
Сжатый воздух не рекомендуется для резки титана;
2. Азот с аргоном. Применяется для резки:
· высоколегированной стали толщиной до 50 mm.
Применять эту газовую смесь для резания меди, алюминия, титана и черной стали не рекомендуется;
3. Чистый азот. Используется для резания (h=толщина материала):
· меди h равной до 20 mm;
· латуни h равной до 90 mm;
· алюминия и его сплавов h равной до 20 mm;
|
· высоколегированных сталей h равной до 75 mm, низколегированных и низкоуглеродистых — h равной до 30 mm;
· титана – любой толщины.
4. Азот с водородом. Применяется для резки:
· меди и ее сплавов средних толщин (до 100 mm);
· алюминия и сплавов средних толщин – до 100 mm.
Азотоводородная смесь непригодна для резки любых сталей и титана.
5. Аргон с водородом. Применяется при резке:
· Меди, алюминия и сплавов на их основе толщиной от 100 мм и выше;
· Высоколегированной стали толщиной до 100 мм.
Для резки углеродистых, низкоуглеродистых и низколегированных сталей, а также для титана аргон с водородом применять не рекомендуется.
2. Технологическая часть.
2.1 Оборудование и инструменты сварщика.
В комплект оборудования для воздушно-плазменной резки входят:
· Плазмотрон - это резак, с помощью которого и выполняются все основные задачи. Устройство горелки плазмореза может быть прямого и косвенного воздействия:
o Плазморез прямого воздействия используется для обработки токопроводящих материалов, в таких случаях заготовка включается в электрическую цепь и отвечает за возникновение искры.
o Плазморез косвенного воздействия применяется в более дорогих и сложных устройствах и используется для обработки материалов, не проводящих электричество. Электрод в таких устройствах находится непосредственно в резаке.
· Сопло - одна из самых функциональных деталей плазматрона. В зависимости от диаметра сопла, плазморезом можно делать либо простые операции, либо сложную фигурную резку. Скорость разрезания материала в основном зависит от длины сопла. Максимальным считается соотношение 1,5; 1,8 к диаметру сопла.
· Электрод - используется в дорогих моделях плазморезов косвенного воздействия. Преимущественно электроды изготавливаются из гафния.
· Компрессор - чтобы трансформировать воздух в плазму необходимо не только довести его до определенной температуры, но и создать поток определенной скорости. Именно по этой причине для плазмореза нужен компрессор. К качеству компрессора предъявляются высокие требования. Так, чтобы была возможность производства плазмы, воздух в горелку должен подаваться сухой и без примесей машинного масла. Важным является обеспечение равномерного потока воздушных масс без пульсации. Ручные плазменные резаки по металлу со встроенным компрессором являются оптимальным вариантом, так как в них производитель установил оборудование полностью соответствующее требованиям для проведения работ. В плазморезах со встроенным компрессором по умолчанию установлен влагоочиститель или осушитель. Плазморез с компрессором обеспечивает максимальную производительность и увеличивает срок эксплуатации резака.
|
К инструменту сварщика относятся:
1.Электрододержатель от которого зависит производительность и безопасность труда. Электрододержатель должен быть лёгким (ни более 0,5кг) и удобный в обращении.
2. Щиток или маска применяется для предохранения глаз и кожи лица сварщика от вредного влияния инфракрасного излучения и брызг металла.
К пренодлежностям сварщика относятся:
- стальная щётка применяемая для зачистки металла от грязи, ржавчины перед сваркой и шлака после сварки.
- молоток с заострённым концом для отбивки шлака со сварочных швов и для поставки личного клейма.
- зубило для вырубки дефектных мест сварного шва.
- для замера геометрического размеров швов, сварщику выдают набор шаблонов. Также сварщик пользуется некоторыми измерительными инструментами (линейка, рулетка). Для проверки углов используется угольник.
2.2 Режимы резки.
Для обеспечения нормального процесса необходим рациональный выбор параметров режима. Параметрами режима являются: диаметр сопла, сила тока, напряжение дуги, скорость резки, расстояние между торцом сопла и изделием и расход воздуха. Форма и размеры соплового канала обуславливают свойства и параметры дуги. С уменьшением диаметра и увеличением длины канала возрастают скорость потока плазмы, концентрация энергии в дуге, её напряжение и режущая способность. Срок службы сопла и катода зависят от интенсивности их охлаждения (водой или воздухом), рациональных энергетических, технологических параметров и величины расхода воздуха.
При воздушно-плазменной резке сталей диапазон разрезаемых толщин может быть разделён на два - до 50 мм и выше. В первом диапазоне, когда необходима надёжность процесса при небольших скоростях резки, рекомендуемый ток 200-250 А. Увеличение силы тока до 300 А и выше приводит к возрастанию скорости резки в 1,5-2 раза. Повышение силы тока до 400 А не даёт существенного прироста скоростей резки металла толщиной до 50 мм. При резке металла толщиной более 50 мм следует применять силу тока от 400 А и выше. С увеличением толщины разрезаемого металла скорость резки быстро падает.
При воздушно-плазменной резке меди рекомендуется применять силу тока 400 А и выше. Замечено, что при резке меди с использованием воздуха во всём диапазоне толщины и токов образуется легко удаляемый грат.
Хорошего качества реза при резке алюминия, с использованием воздуха в качестве плазмообразующего газа, удаётся достигнуть лишь для небольших толщин (до 30 мм) на токах 200 А. Удаление грата с листов большой толщины затруднительно. Воздушно-плазменная резка алюминия может быть рекомендована лишь как разделительная при заготовкедеталей,требующих последующей механической обработки. Припуск на обработку допускается не менее 3 мм.
2.3 Виды дефектов сварных соединений.
При производстве сварных деталей и конструкций образуются дефекты различного вида, которые условно можно классифицировать на:
· дефекты подготовки и сборки;
· дефекты формы шва;
· наружные и внутренние дефекты.
Дефекты подготовки и сборки. Характерными видами дефектов при сварке плавлением являются:
· неправильный угол скоса кромок шва с V-, X- и U-образной разделкой;
· слишком большое или малое притупление по длине стыкуемых кромок;
· непостоянство зазора между кромками по длине стыкуемых элементов;
· несовпадение стыкуемых плоскостей;
· слишком большой зазор между кромками свариваемых деталей;
· расслоения и загрязнения кромок.
Указанные дефекты могут возникнуть из-за:
· неисправности станочного оборудования, на котором обрабатывали заготовки;
· недоброкачественности исходных материалов;
· ошибок в чертежах;
· низкой квалификации слесарей и сборщиков.
Дефекты формы шва. Форма и размеры сварных швов обычно задаются техническими условиями, указываются на чертежах и регламентируются стандартами. Конструктивными элементами стыковых швов (рис. 1) являются их ширина e, высота выпуклости q и подварки q1, угловых швов тавровых и нахлесточных соединений без скоса кромок (рис. 2)– катет К и толщина а. Размеры швов зависят от толщины s свариваемого металла и условий эксплуатации конструкций.
Рис. 1. Основные конструктивные элементы сварных швов: а - без подготовки кромок малых толщин (b - ширина зазора); б - с V-образной разделкой
Рис. 2. Основные конструктивные элементы валиков: а – нормального; б – выпуклого; в – вогнутог о
При выполнении сварных соединений любыми методами сварки плавлением швы могут иметь неравномерную ширину и высоту, бугры, седловины, неравномерную высоту катетов в угловых швах рис. 3.
Рис. 3. Дефекты формы швов: а – неравномерная ширина шва при ручной сварке; б – то же, при автоматической сварке; в – неравномерная выпуклость – бугры и седловины
Неравномерная ширина швов образуется при неправильном движении электрода, зависящем от зрительно-двигательной координации (ЗДК) сварщика, а также в результате возникших отклонений от заданного зазора кромок при сборке. При автоматической сварке причиной образования этого дефекта является нарушение скорости подачи проволоки, скорости сварки и т. д.
Неравномерность выпуклости по длине шва, местные бугры и седловины получаются при ручной сварке из-за недостаточной квалификации сварщика и в первую очередь объясняются особенностью ЗДК сварщика; неправильными приемами заварки прихваток; неудовлетворительным качеством электродов.
При автоматической сварке эти дефекты встречаются редко и являются следствием неполадок в механизме автомата, регулирующем скорость сварки.
Перечисленные дефекты формы шва снижают прочность соединения и косвенно сказывают на возможность образования внутренних дефектов.
Наружные дефекты. К ним относят
· наплывы,
· подрезы,
· незаделанные кратеры,
· прожоги.
Наплывы образуются в результате стекания расплавленного металла электрода на нерасплавленный основной металл или ранее выполненный валик без сплавления с ним (рис. 4). Наплывы могут быть местными, в виде отдельных зон, а также значительными по длине.
Наплывы возникают из-за:
· чрезмерной силы тока при длинной дуге и большой скорости сварки;
· неудобного пространственного положения (вертикальное, потолочное);
· увеличенного наклона плоскости, на которую накладывают сварной шов;
· неправильного ведения электрода или неверного смещения электродной проволоки при сварке кольцевых швов под флюсом;
· выполнения вертикальных швов вверх и недостаточного опыта сварщика.
Рис. 4. Наплывы в швах: а – горизонтальном; б – нахлесточного соединения; в – таврового соединения; г – стыкового соединения или при наплавке валиков
Подрезы представляют собой углубления (канавки) в основном металле, идущие по краям шва (рис. 5). Глубина подреза может колебаться от десятых долей миллиметра до нескольких миллиметров. Причинами образования этого дефекта являются:
· значительно силы ток и повышенное напряжение дуги;
· не удобное пространственное положение при сварке;
· небрежность сварщика.
Рис. 5. Подрезы: а – в стыковом шве; б – в горизонтальном шве, расположенном на вертикальной плоскости; в – в угловом шве таврового соединения
Подрезы в шве уменьшают рабочую толщину металла, вызывают местную концентрацию напряжений от рабочих нагрузок и могут быть причиной разрушения швов в процесс эксплуатации. Подрезы в стыковых и угловых швах, расположенные поперек действующи на них сил, приводят к резкому снижению вибрационной прочности; даже достаточно крупные подрезы, проходящие вдоль действующе силы, отражаются на прочности в значительно меньшей степени, чем подрезы, расположенные поперек.
Кратер – углубление, образующееся конце шва при внезапном прекращении сварки особенно часто кратеры возникают при выполнении коротких швов. Размеры кратер зависят от величины сварочного тока. При ручной сварке его диаметр колеблется от 3 до 20 мм, при автоматической он имеет удлиненную форму в виде канавки. Незаделанные кратеры снижают прочность сварного соединения так как концентрируют напряжения. При вибрационной нагрузке снижение прочности соединения из малоуглеродистой стали достигает 25 %, а из низколегированных – 50 % при наличии в шве кратера.
Прожоги – дефекты в виде сквозного отверстия в сварном шве, образующиеся при вытекании сварочной ванны; сварке металл небольшой толщины и корня шва в многослойных швах, а также при сварке снизу-вверх вертикальных швов (рис. 6). Причинами прожогов являются: чрезмерно высокая погонная энергия дуги, неравномерная скорость сварки, остановка источника питания, увеличенный зазор между кромками свариваемых элементов. Во всех случаях отверстие, возникающее при прожогах, хотя и заделывается, однако шов в том месте получается неудовлетворительный по внешнему виду и качеству.
Рис. 6. Прожоги
Поджоги возникают в результате возбуждения дуги («чирканья электродом») на краю кромки. Этот дефект служит источником концентрации напряжений, его обязательно удаляют механическим способом.
Внутренние дефекты. К ним относят поры, шлаковые включения, непровары, несплавения и трещины.
Поры (рис. 7) в виде полости округлой формы, заполненной газом, образуются вследствие: загрязненности кромок свариваемого металла, использования влажного флюса или отсыревших электродов, недостаточной зашиты шва при сварке в углекислом газе, увеличенной скорости и завышенной длины дуги. При сварке в углекислом газе, а в некоторых случаях и под флюсом на больших токах, образуются сквозные поры – так называемые свищи.
Рис. 7. Характер пористости в наплавленном металле шва: а – равномерная пористость; б – скопления пор; в – цепочки пор
Размеры внутренних пор колеблются от 0,1 до 2...3 мм в диаметре, а иногда и более. Поры, выходящие на поверхность шва, могут быть и больше. Свищи при сварке под флюсом и в углекислом газе на больших токах могу иметь диаметр до 6...8 мм. Длина так называемых «червеобразных» пор – до нескольких сантиметров.
Равномерная пористость (рис., а) обычно возникает при постоянно действующих факторах: загрязненности основного металла по свариваемым поверхностям (ржавчина, масло и т.п.), непостоянной толщине покрытия электродов и т.д. Скопление пор (рис. 7, б) наблюдается при местных загрязнениях или отклонениях от установленного режима сварки, также при нарушении сплошности покрытия электрода, сварке в начале шва, обрыве дуги или случайных изменениях ее длины.
Цепочки пор (рис. 7, в) образуются в условиях, когда газообразные продукты проникают в металл по оси шва на всем его протяжении (при сварке по ржавчине, подсос воздуха через зазор между кромками, подварке корня шва некачественными электродами). Одиночные поры возникают за счет действия случайных факторов (колебания напряжения сети и т.д.). Наиболее вероятно возникновения пор при сварке алюминиевых и титановых сплавов, в меньшей степени – при сварке сталей.
Шлаковые включения в металле сварного шва – это небольшие объемы, заполненные неметаллическими веществами (шлаками, оксидами). Вероятность образования шлаковы включений в значительной мере определяется маркой сварочного электрода. При сварке электродами с тонким покрытием вероятность образования шлаковых включений очень велика. При сварке высококачественными электродами, дающими много шлака, расплавленный металл дольше находится в жидком состоянии и неметаллические включения успеваю всплыть на его поверхность, в результате чего шов засоряется шлаковыми включениями не значительно.
Шлаковые включения можно разделит на макро- и микроскопические. Макроскопические включения имеют сферическую и продолговатую формы в виде вытянутых «хвостов» Эти включения образуются в шве из-за плохой очистки свариваемых кромок от окалины и других загрязнений и чаще всего вследствие внутренних подрезов и плохой зачистки от шлак поверхности первых слоев многослойных швов перед заваркой последующих (рис. 8).
Микроскопические шлаковые включения появляются в результате образования в процессе плавления некоторых химических соединений, остающихся в шве при кристаллизации.
Рис. 8. Шлаковые включения по подрезу кромки в многослойном шве
Оксидные пленки могут возникать при всех видах сварки. Причины их образования такие же, как и шлаковых включений: загрязненность поверхностей свариваемых элементов; плохая зачистка от шлака поверхности слоев шва при многослойной сварке; низкое качество электродного покрытия или флюса; недостаточно хорошая квалификация сварщика и т.п.
Непровары – это дефект в виде местного несплавления в сварном соединении вследствие неполного расплавления кромок или поверхностей ранее выполненных валиков. Непровары (рис. 9, а) в виде несплавления основного металла с наплавленным представляют собой тонкую прослойку оксидов, а в некоторых случаях – грубую шлаковую прослойку между основным и наплавленным металлом. Причинами образования таких непроваров являются:
· – плохая зачистка кромок свариваемых деталей от окалины, ржавчины, краски, шлака, масла и других загрязнений;
· – блуждание или отклонение дуги под влиянием магнитных полей, особенно при варке на постоянном токе;
· – электроды из легкоплавкого материала (при выполнении шва такими электродами жидкий металл натекает на неоплавленные свариваемые кромки);
· – чрезмерная скорость сварки, при которой свариваемые кромки не успевают расплавиться;
· – значительное смещение электрода в сторону одной из свариваемых кромок, при том расплавленный металл натекает на вторую нерасплавленную кромку, прикрывая непровар;
· – неудовлетворительное качество основного металла, сварочной проволоки, электродов, флюсов и т.д.;
· – плохая работа сварочного оборудования – колебания силы сварочного тока и напряжения дуги в процессе сварки;
· – низкая квалификация сварщика.
Рис. 9. Непровары: а – по кромке с основным металлом; б – в корне шва; в – между отдельными слоями; г – между валиками
Причинами образования непроваров в корне шва (рис. 9, б) кроме указанны выше могут быть: недостаточный угол скоса кромок; большая величина их притупления; маленький зазор между кромками свариваемых деталей; большое сечение электрода или присадочной проволоки, укладываемой в разделку шва, что значительно затрудняет расплавление основного металла. Непровары между отдельными слоями (рис. 9, в, г) возникают по следующим причинам: из-за неполностью удаленного шлака, образовавшегося при наложении предыдущего валика, что возможно из-за трудности его удаления или небрежности сварщика; недостаточной тепловой мощности (малый ток, излишне длинная или коротка дуга).
Трещины – частичное местное разрушение сварного соединения в виде разрыв (рис. 10). Образованию трещин способствуют следующие факторы:
· – сварка легированных сталей в жестко закрепленных конструкциях;
· – высокая скорость охлаждения при сварке углеродистых сталей, склонных к закалке на воздухе;
· – применение высокоуглеродистой электродной проволоки при автоматической сварки конструкционной легированной стали;
· – использование повышенных плотностей сварочного тока при наложении первого слоя многослойного шва толстостенных сосудов и изделий;
· – недостаточный зазор между кромками деталей при электрошлаковой сварке;
· – слишком глубокие и узкие швы при автоматической сварке под флюсом;
· – выполнение сварочных работ при низкой температуре;
· – чрезмерное нагромождение швов для усиления конструкции (применение накладок и т.п.), в результате чего возрастают сварочные напряжения, способствующие образованию трещин в сварном соединении;
· – наличие в сварных соединениях других дефектов, являющихся концентраторами напряжений, под действием которых в области дефектов начинают развиваться трещины.
Рис. 10. Трещины в сварных швах и соединениях: а – в наплавленном металле; б – в зонах оплавления и термического влияния
Существенным фактором, влияющим на образование горячих трещин (ГТ), является засоренность основного и присадочного металлов вредными примесями серы и фосфора. Холодные трещины (ХТ) образуются при наличии составляющих мартенситного и бейнитного типов, концентрации диффузного водорода в зоне зарождения трещин и растягивающих напряжений 1 рода. Трещины относятся к наиболее опасным дефектам и по всем действующим нормативно-техническим документам (НТД) недопустимы.
Для электронно-лучевой (ЭЛС) и лазерной сварки (ЛС) наиболее характерны: несплавления за счет смещения луча вследствие намагничивания (ЭЛС) или непостоянства зазора по длине (ЛС); газовые полости, возникающие из-за неполного закрытия газодинамического канала; дефекты формирования шва из-за выброса металла; пористость.
Металлические включения. В практик наиболее распространены вольфрамовы включения при сварке алюминиевых сплавов. Они обычно возникают при аргонодуговой сварке вольфрамовым электродом При этом могут наблюдаться мгновенная нестабильность дуги и появление одновременно вольфрамовыми включениями оксидных включений. Вольфрамовые включения могут располагаться внутри шва и на поверхности соединений в виде брызг. При попадании вольфрама жидкую ванну он обычно погружается на дно ванны. Вольфрам в алюминии нерастворим обладает большой плотностью. На рентгеновском снимке он дает характерные ясные изображения произвольной формы. Вольфрамовые включения, как правило образуются в местах обрыва дуги, при этом вольфрам скапливается в вершине кратеров, где часто образуются трещины.
Вольфрамовые включения подразделяю на две основные группы: изолированные и групповые. Размер диаметра изолированны включений 0,4...3.2 мм. Групповые включения описываются (по рентгенограмме) размером группы, количеством и размером отдельных (изолированных) включений в группе, при этом размер группы характеризуется размером минимальной окружности, в которую вписывается группа включений. Если изображение нескольких включений сливается, то их принимают за одно включение.
2.4 Способы контроля сварных соединений.
После завершения сварочных работ, изделия должны подвергаться контролю сварных соединений с целью обнаружения и исправления дефектов. Невооруженным глазом можно рассмотреть лишь часть из них - крупные наружные трещины и поры, непровары, подрезы и т.п. Большая часть дефектов скрыта в глубине металла или имеет такие малые размеры, что обнаружить их можно только с использованием специальных приборов и материалов.
Существует много способов контроля сварных швов, различающихся по принципу действия, способности к обнаружению тех или иных видов дефектов, техническому оснащению. Методы контроля сварных соединений подразделяются на разрушающие и неразрушающие. Последние, в силу понятных причин, являются наиболее широко используемыми. Применяются следующие основные методы неразрушающего контроля сварных соединений:
Содержание
Введение 3
1. Специальная часть. 5
1.1 Сущность процесса резки. 5
1.2 Материалы, применяемые при резке. 8
2. Технологическая часть. 10
2.1 Оборудование и инструменты сварщика. 10
2.2 Режимы резки. 12
2.3 Виды дефектов сварных соединений. 14
2.4 Способы контроля сварных соединений. 28
2.5 Техника безопасности. 30
3. Литература 32
Графическая часть.
1. Схема процесса резки.
2. Оборудование для резки.
Введение.
Плазменная резка— вид плазменной обработки материалов, при котором в качестве режущего инструмента вместо резца используется струя плазмы.
Сама технология плазменной резки появилась уже очень давно, более 50 лет тому назад. Первые их установки появились примерно в 60-е года 20 века. Станки в свое время для процесса плазменной резки были настолько дорогие и громоздкие, что их позволяли приобрести только очень большие предприятия.
В начале 21 века плазменная резка для всех нас стала более доступной и более распространенной. Станки совершенствовались, становились все более удобными, компактными, продуктивными и самое главное дешевыми. В результате всего этого плазменная резка получила довольно широкое распространение в очень разных отраслях современного хозяйства, так как она решает множество задач первостепенной промышленной важности.
Плазменная резка, по сравнению с технологией газокислородной резки, гораздо проще. Поскольку она совершенно не требует постоянной заправки и доставки баллонов с газом. А также дорогих разных присадок для дорогих и ценных металлов либо же строжайшего соблюдения пожарной безопасности. Для такого вида резки нужно иметь в наличии только воздух и электроэнергию, а также сопла и электроды, которые являются самым распространенным расходным материалом.
Плазменная резка позволяет резать и толстые, и тонкие листы металла без лишних усилий. Металлы, которые доступны для резки в такой способ: медь, титан, алюминий, бронза и их сплавы (чугун, латунь, сталь). Порог критичной толщины материала для ручной резки составляет около 5 см, но для более мощных станков, которые находятся под управление компьютера можно использовать порог даже до 30 см. стали.
При всех этих плюсах и минусах плазменной резки, она остается лучше всех остальных способов реза металла. Даже тем, что после нее нет никакой деформации продукта, а заусенцы на металле можно легко и быстро убрать, плазменная резка занимает лидирующее положение в промышленном применении.
1.Специальная часть.
1.1 Сущность процесса резки.
Сущность технологии плазменной резки, принцип работы плазменной резки, заключается в локальном расплавлении металла и выдувании этого расплавленного металла при перемещении плазменного резака относительно разрезаемого металла, с образованием полости реза.
Технология плазменной резки является одним из наиболее экономически эффективных способов раскроя металла при толщинах металла от 1 до 50 мм. Преимущества плазменной резки:
1.УНИВЕРСАЛЬНОСТЬ. С помощью технологии плазменной резки режутся все типы металлов (чёрные, легированные (в т.ч. нержавеющие), сплавы алюминия, сплавы меди, титан и проч.);
2.ВЫСОКАЯ СКОРОСТЬ РЕЗКИ МЕТАЛЛА – портальная машина плазменной резки – например МТР «Юпитер», станки «Омега» и даже бюджетный станок для раскроя металла «Гермес»- может резать металл со скоростью до 12 метров в минуту;
3.МАЛАЯ ЗОНА ТЕРМИЧЕСКОГО ВОЗДЕЙСТВИЯ в области реза на разрезаемый лист металла;
4.ВЫСОКОЕ КАЧЕСТВО РЕЗА. Современные плазменные резаки (плазмотроны) в совокупности с правильным подбором плазмообразующих и охлаждающих газов обеспечивают минимальную ширину реза, крайне низкую конусность реза, чистые (без наплывов и грата) кромки, почти не требующие дополнительной обработки. Таким условиям отвечает прецизионная плазменная резка;
5.БЕЗОПАСНОСТЬ. При использовании технологии плазменной резки не используются горючие газы (пропан, ацетилен), которые используются пригазовой резке.
Принцип работы плазменной резки основан на использовании плазменной дуги постоянного тока прямого действия (электрод - катод, где разрезаемый металл – анод).
При образовании плазменной дуги нагретый электрической дугой до высокой температуры (порядка 25 000 °C) газ переходит в ионизированное состоянии – четвёртое агрегатное состояние вещества - плазму. Последнее означает, что этот газ утрачивает свойства диэлектрика и приобретает способность проводить электрический ток. В процессе резки плазменный поток становится проводником для ток
|
|
Организация стока поверхностных вод: Наибольшее количество влаги на земном шаре испаряется с поверхности морей и океанов (88‰)...
Автоматическое растормаживание колес: Тормозные устройства колес предназначены для уменьшения длины пробега и улучшения маневрирования ВС при...
Эмиссия газов от очистных сооружений канализации: В последние годы внимание мирового сообщества сосредоточено на экологических проблемах...
Поперечные профили набережных и береговой полосы: На городских территориях берегоукрепление проектируют с учетом технических и экономических требований, но особое значение придают эстетическим...
© cyberpedia.su 2017-2024 - Не является автором материалов. Исключительное право сохранено за автором текста.
Если вы не хотите, чтобы данный материал был у нас на сайте, перейдите по ссылке: Нарушение авторских прав. Мы поможем в написании вашей работы!