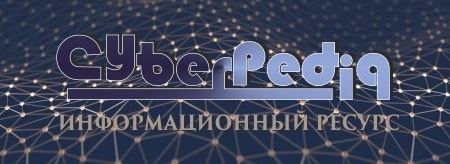
Особенности сооружения опор в сложных условиях: Сооружение ВЛ в районах с суровыми климатическими и тяжелыми геологическими условиями...
Папиллярные узоры пальцев рук - маркер спортивных способностей: дерматоглифические признаки формируются на 3-5 месяце беременности, не изменяются в течение жизни...
Топ:
Эволюция кровеносной системы позвоночных животных: Биологическая эволюция – необратимый процесс исторического развития живой природы...
Определение места расположения распределительного центра: Фирма реализует продукцию на рынках сбыта и имеет постоянных поставщиков в разных регионах. Увеличение объема продаж...
Интересное:
Подходы к решению темы фильма: Существует три основных типа исторического фильма, имеющих между собой много общего...
Искусственное повышение поверхности территории: Варианты искусственного повышения поверхности территории необходимо выбирать на основе анализа следующих характеристик защищаемой территории...
Распространение рака на другие отдаленные от желудка органы: Характерных симптомов рака желудка не существует. Выраженные симптомы появляются, когда опухоль...
Дисциплины:
![]() |
![]() |
5.00
из
|
Заказать работу |
|
|
Министерство сельского хозяйства РФ
Федеральное государственное образовательное учреждение высшего профессионального образования
«Пермская сельскохозяйственная академия имени академика
Д.Н. Прянишникова»
Кафедра «Технического сервиса и ремонта машин»
Контрольная работа
«Основы работоспособности ТС»
Выполнил:
студент заочного факультета
Шифр: Эт-13-158
Гусельников С.И.
Проверил:
Куимов Ю.Е.
Пермь 2016
Теоретическая часть
Основные причины изменения технического состояния объектов.
Под техническим состоянием объекта подразумевается состояние его свойств в данный момент времени, в процессе эксплуатации свойства объекта изменяются под воздействием различных факторов. Внешне это проявляется как отклонение параметров, характеризующих эти свойства, от установленных нормативно-технической документацией. Как отмечалось, изменение свойств объекта отображается в совокупности выходных его параметров, в том числе параметров материальных и энергетических выходных потоков, геометрических размеров и физических параметров (прочности, вязкости, твердости и т. п.) конструкционных материалов, часто называемых структурными. По изменению параметров материальных и энергетических потоков (на фиксированном режиме работы) можно судить только о том, изменилось ТС объекта или нет. На вопрос же о том, что явилось причиной изменения ТС, позволяет ответить только информация об изменении структурных параметров.
В связи с этим принято считать, что по отклонению технико-экономических показателей оценивается изменение качества функционирования технического объекта, а по отклонениям структурных параметров - изменение его технического состояния. Поэтому эффективная техническая эксплуатация любого технического объекта невозможна, если неизвестны основные причины и закономерности изменения структурных параметров под воздействием рабочих процессов и внешних воздействий.
|
Изнашивание
Трение поверхностей сопровождается изнашиванием. В зависимости от условий и режимов трения, физико-механических свойств применяемых материалов, микрорельефа поверхностей и других параметров, определяющих характер изнашивания, при трении двух сопряжённых поверхностей происходят сложные процессы, которые приводят к их износу.
Под износом понимается результат изнашивания, проявляющийся в виде отделения или остаточной деформации материала. Износы могут быть естественные, ускоренные и аварийные. В процессе эксплуатации автомобилей происходит естественное изнашивание деталей. Графически процесс изнашивания двух сопряжённых деталей обычно изображают следующим образом.
Рис. Характер протекания процесса изнашивания сопряженных деталей: 1 — при установившейся скорости изнашивания; 2 — при снижении скорости изнашивания; 3 — при уменьшении зазора в конце приработки
По вертикальной оси прямоугольной системы координат откладывают, в выбранном масштабе, величину износа деталей, а по горизонтальной пробег автомобиля. Точки соединяют плавными линиями. Полученные кривые показывают характер нарастания износа каждой детали по мере увеличения пробега автомобиля. Расстояние между кривыми свидетельствует о характере изменения зазора в сопряжении. Зазор SH устанавливается между деталями при сборке.
На идеализированной схеме можно выделить три этапа процесса изнашивания:
Каждый из этих этапов отражает е состояние сопряженной пары. Переход от одного этапа к другому определяется количественным накоплением отдельных повреждений. На этапе приработки скорость изнашивания повышенная. Новые или отремонтированные детали прирабатываются. С трущихся поверхностей удаляются заусенцы, уменьшается их шероховатость, в отдельных случаях материал дает усадку. На этапе установившегося изнашивания (при работе в обычных условиях эксплуатации) скорость изменения изнашивания (tgα) почти постоянна. Этап установившегося изнашивания составляет наибольшую часть ресурса сопряжённой пары. При увеличении зазора до предельно допустимого S2 скорость изнашивания деталей интенсивно возрастает, заканчивается период нормальной работы деталей и наступает аварийное изнашивание. При этом на скорость изнашивания начинают влиять новые факторы: ударные нагрузки, биение, изменение теплового режима и условий смазки. Детали могут выйти из строя, что ведет к аварии.
|
Многие детали не имеют отчетливо выраженных этапов приработки, установившегося и аварийного изнашивания деталей. Бывает, что скорость изнашивания почти постоянная, износ деталей меняется линейно с течением времени. В ряде случаев детали имеют четко выделяющиеся периоды приработки и естественного износа, или наоборот, скорость их изнашивания в процессе приработки и нормальной эксплуатации практически одинакова, но зато резко выделяется аварийный этап работы.
На рисунке видны возможности увеличения этапа установившегося изнашивания при номинальном зазоре Sн и заданной величине предельно допустимого зазора S2: во-первых, за счет уменьшения зазора конца приработки S1 и, во-вторых, за счет снижения скорости изнашивания деталей сопряжения (уменьшения tgα). Согласно рисунку, уменьшение зазора конца приработки с S1 до S1′ повышает ресурс работы сопряжения на величину ∆l’2. Уменьшение скорости изнашивания, выраженное уменьшением угла наклона кривой износа от α1 до α2, повышает ресурс работы сопряжения на ∆l2″.
Выделяют три группы изнашивания:
Каждая из групп изнашивания делится на виды.
Абразивное изнашивание возникает при трении скольжения и наличии между трущимися поверхностями мелкораздробленной твердой среды (например, песка), вызывающей выкрашивание частиц, металла из поверхности деталей. При этом процесс изнашивания не зависит от попадания абразивных частиц на поверхности трения.
|
Необходимо отметить, что размеры абразивных частиц с увеличением длительности работы их в масле уменьшаются, поэтому их агрессивность постепенно снижается до нуля.
Изменение размеров деталей при абразивном изнашивании зависит от ряда факторов:
Примером может служить изнашивание цилиндропоршневой группы двигателя в результате попадания в цилиндры с воздухом пыли, зубьев шестерен и подшипников агрегатов трансмиссии, открытых сопряжений деталей ходовой части. По результатам исследований абразивный износ деталей агрегатов трансмиссии автомобилей составляет от 2 до 11 мкм на 1000 км пробега.
Гидроабразивное изнашивание возникает в результате действия твердых тел или частиц, увлекаемых потоком жидкости. Гидроабразивное изнашивание деталей топливных, масляных и водяных насосов, гидроприводов тормозов, гидроусилителей нередко проявляется совместно с эрозионным изнашиванием, возникающим в результате действия потока жидкости (газа). Трение потока жидкости о металл приводит к разрушению оксидной пленки, образующейся на поверхности детали, и сопутствует коррозионному разрушению материала, особенно под действием абразивных частиц и микро ударов в случае возникновения кавитации.
Кавитационное изнашивание — это гидр эрозионное изнашивание при движении твердого тела относительно жидкости, когда пузырьки газа захлопываются вблизи поверхности, что создает местное повышение давления или температуры.
Газоабразивное изнашивание происходит в результате воздействия твердых частиц, увлекаемых потоком газа и перемещающихся относительно изнашивающейся поверхности.
Усталостное изнашивание поверхности трения или отдельных ее участков в результате повторного деформирования микрообъемов материала, приводящего к возникновению трещин и отделению частиц, происходит при качении и скольжении. Износ обусловливается микропластическими деформациями и упрочнением поверхностных слоев трущихся деталей. При этом имеют место напряженное состояние активных объемов металла у поверхности трения и особые явления усталости при знакопеременных нагрузках, вызывающих трение металла в поверхностных слоях и как следствие их разрушение. Пульсирующие нагрузки резко усиливают темпы осповидного износа.
|
Разрушение при таком износе характеризуется появлением микро- и макротрещин, расположенных под небольшими углами к поверхности трения, с последующим развитием их в осповидные углубления в впадины. В результате износа частицы поверхностного слоя откалываются, поверхность становится неровной и приобретает матовый вид.
Усталостное изнашивание наиболее характерно для рабочих поверхностей подшипников качения и поверхностей зубьев шестерен.
Изнашивание при фреттинге происходит в результате механического изнашивания соприкасающихся тел при малых колебательных относительных перемещениях.
Изнашивание при заедании возникает в результате схватывания, глубокого вырывания материала, переноса его с одной поверхности трения на другую и воздействия возникших неровностей на сопряженную поверхность. Этот вид изнашивания имеет место в зубчатых зацеплениях агрегатов трансмиссии при использовании несоответствующего сорта масла или при его малом уровне.
Коррозионно-механическое изнашивание происходит при трении материалов, вступивших в химическое взаимодействие со средой. К коррозионно-механическим видам изнашивания относятся окислительное и изнашивание при фреттинг-коррозии.
Окислительное изнашивание возникает при наличии на поверхностях трения защитных пленок, образовавшихся в результате взаимодействия материала с кислородом. Окислительное изнашивание характеризуется протеканием одновременно двух процессов — пластической деформации микроскопических объемов металла поверхностных слоев деталей и диффузии кислорода воздуха в деформируемые слои.
На первой стадии износа окисление происходит в небольших объемах металла, расположенных у плоскостей скольжения при трении. На второй стадии окисление захватывает большие объемы поверхностных слоев, и глубина его соответствует глубине пластической деформации.
На первой стадии износа, на поверхности трущихся деталей образуются пленки твердых растворов кислорода, на второй — химические соединения кислорода с металлом. Процесс окислительного изнашивания происходит в тонких поверхностных слоях и условно может быть разделен на три этапа: деформирование и активизация, образование вторичных структур и их разрушение.
|
На первом этапе происходит особый вид пластической деформации — текстурирование и резкая активизация металла. На втором этапе благодаря наличию в зоне трения агрессивных компонентов среды происходит физико-химическое взаимодействие их с активизированным слоем — образование вторичных структур. На третьем этапе в результате многократного нагружения и внутренних напряжений в пленках вторичных структур происходит образование и развитие микротрещин, ослабление связей на поверхности раздела и отслаивание пленки.
Последующее механическое воздействие приводит к разрушению и износу пленки. На обнаженных участках процесс повторяется вновь. Окислительному износу подвергаются шейки коленчатого вала, гильзы цилиндров, поршневые пальцы, зубчатые зацепления и другие детали, работающие при трении скольжения.
Изнашивание при фриттинг-коррозии — это коррозионно-механическое изнашивание соприкасающихся тел при малых колебательных перемещениях. В случае динамического нагружения и наличия вибрации и ударов окисление трущихся поверхностей происходит особенно интенсивно вследствие резкой активизации пластически деформируемого металла. Динамический характер нагружения приводит к резкому повышению градиента деформации и температур, к окислению и схватыванию. Фриттинг-процесс возникает при трении скольжения с очень малыми возвратно-поступательными перемещениями в условиях динамической нагрузки.
Этот процесс можно считать пограничным между процессами химической коррозии и эрозии, поскольку интенсивность фриттинг-коррозии повышается с увеличением доступа кислорода, но уменьшается при увлажнении воздуха.
При фриттинг-коррозии наблюдается изнашивание посадочных поверхностей подшипников поворотных цапф, шестерен, болтовых и заклепочных соединений рам и других деталей.
Изнашивание при действии электрического тока (эрозионное изнашивание) поверхностей происходит в результате воздействия разрядов при прохождении электрического тока.
Работа агрегатов и узлов автомобилей сопровождается одновременно несколькими видами изнашивания. В чистом виде ни один из видов изнашивания не наблюдается. Как правило, в каждом работающем сопряжении деталей имеется вид изнашивания, определяющий износостойкость деталей. Остальные виды изнашивания в большей или меньшей мере ему сопутствуют. Определяющий вид изнашивания зависит от условий эксплуатации, нагрузок и других причин и лимитирует время безотказной работы сопряжения.
Определяющим видом изнашивания металлических деталей автомобилей при их эксплуатации является механическое изнашивание. Правильное определение вида изнашивания, знание приемов уменьшения интенсивности того или иного изнашивания позволят в значительной степени увеличить срок службы деталей автомобилей.
Усталостные разрушения
Этот вид разрушений возникает при циклическом приложении нагрузок, превышающих предел выносливости металла детали. При этом происходят постепенное накопление и рост усталостных трещин, приводящие при определенном числе циклов нагружения к усталостному разрушению деталей. Совершенствование методов расчета и технологии изготовления автомобилей (повышение качества металла и точности изготовления, исключение концентраторов напряжения) привело к значительному сокращению случаев усталостного разрушения деталей. Как правило, оно наблюдается в экстремальных условиях эксплуатации (длительные перегрузки, низкие или высокие температуры) у рессор, полуосей, рамы.
Коррозия
Это явление происходит вследствие агрессивного воздействия среды на детали, приводящего к окислению (ржавлению) металла и, как следствие, к уменьшению прочности и ухудшению внешнего вида. Основными активными агентами внешней среды, вызывающими коррозию, являются соль, которой посыпают дороги зимой, кислоты, содержащиеся в воде и почве, а также компоненты, входящие в состав отработавших газов автомобилей, и их химические соединения. Коррозия главным образом поражает детали кузова, кабины, рамы. Для деталей кузова, расположенных снизу, коррозия сопровождается абразивным изнашиванием в результате воздействия на поверхность при движении автомобиля абразивных частиц — песка, гравия. Сильно способствует коррозии сохранение влаги на металлических поверхностях, в том числе под слоем дорожной грязи, что особенно характерно для всякого рода скрытых полостей и ниш.
Коррозия способствует усталостному изнашиванию и разрушению, так как создает на поверхности металла концентраторы напряжения в виде коррозионных язв. Такой вид разрушений наблюдается, например, в местах сварки, крепления кронштейнов рессор.
Старение
Показатели технического состояния деталей и эксплуатационных материалов изменяются под действием внешней среды. Так, резинотехнические изделия теряют прочность и эластичность в результате окисления, термического воздействия (разогрев или охлаждение), химического воздействия масла, топлива и жидкостей, а также солнечной радиации и влажности.
В процессе эксплуатации свойства смазочных материалов и эксплуатационных жидкостей ухудшаются в результате накопления в них продуктов износа, изменения вязкости и потери свойств присадок. Детали и материалы изменяются не только при их использовании, но и при хранении:
Организационное управление
С развитием вычислительной техники и математических методов автоматизация распространилась на управление объектами социальной природы.
Управления этого типа принципиально не может быть автоматическими. Объясняется это рядом причин:
· сложность объектов социальной природы не позволяет разработать формальные процедуры вывода параметров управляющего воздействия;
· субъект управления является составным элементом объекта управления;
· исполнительные орган не является техническим устройством, он также является элементом объекта управления;
· социальный объект имеет очень разносторонние связи и отношения, что иногда трудно его выделить из внешней среды, однозначно описать границы объекта и внешней среды;
· время становится во многих случаях основным фактором оценки результатов управляющих воздействий.
Управление объектами социальной природы является автоматизированным.
Автоматизированное управление это процесс, при котором формальные процедуры выполняются людьми с использованием средств вычислительной техники (сбор, хранение, обработка информации, ведение документооборота, вычисления, анализ, моделирование сценариев развития), а принятие решения о способах, форме, динамике поведения выполняется уполномоченными людьми или группами людей. Они при этом самым непосредственным образом участвуют в процессе реализации принятого решения.
Целью автоматизации управления является эффективное использование всех видов «ресурсов». При этом достигается:
Повышение оперативности управления за счёт использования следующих базовых информационных процессов:
· сбор информации,
· поиск информации,
· предварительная обработка информации
· передача информации, шифрование и дешифрование информации,
· производство расчётов,
· решение логических задач,
Снижение трудовых затрат на выполнение различных вспомогательных процессов. При управлении, трудовые затраты распределяются примерно следующим образом, как показано на рис. 2.
Повышение формализованности принимаемых решений. Принятие решений проходит на основе анализа и последующего имитационного моделирования развития ситуации с применением современного математического аппарата.
Эффект от автоматизации управления достигается не за счет уменьшения численности людей в системе управления, а за счет перераспределение специалистов:
· сокращается численность должностных лиц, занятых непосредственно управлением,
· увеличивается инженерный и технический персонал, обслуживающий технические средства.
Эффект автоматизации достигается за счёт своевременности и рациональности принимаемых решений.
рис. 2.
Практическая часть
Цель работы: освоить методы обработки данных наблюдений (испытаний) и расчета основных показателей надежности машин: безотказности, ремонтопригодности и долговечности.
Исходные данные: Результаты наблюдений 10 зерноуборочных комбайнов «Нива» в условиях рядовой эксплуатации.
В процессе испытаний все периоды работы и время простоя по причине отказа записываются в журнал наблюдения за каждым объектом. Результаты испытаний партии комбайнов (выборки) примерно одинакового технического состояния (новые или капитально отремонтированные) сводятся в общую таблицу1 для статистического анализа, которая является исходными данными для определения показателей надежности.
1. Определение показателей безотказности
Основными показателями безотказности являются:
Р(Т) – вероятность безотказной работы – вероятность того, что в пределах заданной наработки отказ объекта не возникает
–параметр потока отказа – плотность вероятности возникновения отказа восстанавливаемого объекта, определяемая для рассматриваемого момента времени;
- средняя наработка на отказ - отношение наработки восстанавливаемого объекта к математическому ожиданию числа его отказов в течение этой наработки.
Определение показателей безотказности ведется по интервалам наработки и в целом за весь период испытаний. Для этого наработка комбайна за весь период испытаний разбивается на 8-12 интервалов. Величина интервала должна быть целым числом (обычно кратным 10). Она определяется по формуле:
(1)
- наибольшая наработка комбайна в данной партии, га;
- наработка машины до начала испытаний, га (обычно
);
К – число интервалов.
Принимаем га, тогда К=11 интервалов.
На основании таблицы 1 все отказы каждого комбайна распределяются по интервалам наработки и заносятся в таблицу 2 (независимо от группы сложности).
Для удобства дальнейших расчетов в таблице 2 все комбайны располагаются
в порядке увеличения наработки за период испытаний, а в таблице 3 подсчитывают время восстановления отказов по группам сложности.
Определяется суммарное число отказов всех машин в каждом интервале
(табл.2), а также суммарное время восстановления отказов по группам сложности и общее время, затраченное на восстановление всех отказов (табл.3).
Условное количество всех машин, работающих в каждом интервале, определяется по формуле
(2)
Где - суммарная наработка всех комбайнов в данном интервале, га
Далее определяется среднее число отказов на один комбайн в каждом интервале по формуле:
(3)
Применительно к пятому интервалу условное количество комбайнов будет равно (см. формулу 2):
Так наработка комбайна №11 за период испытаний в данном сезоне составила 123 га, то в пятом интервале (121-150) этот комбайн убрал 3 га(121,122,123 га), т.е. 3/30=0,1 интервала. Следовательно, можно считать, что в шестом интервале условно работало 9,1 комбайнов из 10, находившихся на испытаниях.
Среднее число отказов (формула 3) в этом интервале составит:
отказов
Аналогичным образом подсчитывается условное количество комбайнов и среднее число отказов в каждом интервале и записывается в таблицу 2.
Заранее зная плановую наработку ( комбайна на предстоящий сезон
(например, =180 га), можно определить ожидаемое число отказов по каждому комбайну по формуле:
(
(4)
Где – число интервалов плановой наработки
=6
Тогда ожидаемое число отказов данного комбайна за сезон в среднем составит:
9 отказов
Для устранения этих отказов необходимо планировать работу ремонтной службы и заранее приобретать необходимые запчасти, исходя из опыта предыдущих лет, учитывая при этом срок службы комбайнов.
Далее переходят непосредственно к расчету показателей безотказности.
1.1 Параметр потока отказов (отк/га), определяется по формуле:
(5)
Среднее значение параметра потока отказов (отк/га) за весь период испытаний
(t)=
(6)
Где - суммарное число отказов по всем комбайнам за весь период испытаний
– суммарная наработка всех комбайнов за период испытаний, га.
отк./га
1.2 Наработка на отказ определяется в каждом интервале по формуле
(7)
или
(8)
Средняя наработка на отказ за весь период испытаний:
(9)
или
(10)
Наработка на отказ по группам сложности
(11)
(12)
(13)
Где
- число отказов первой, второй и третьей группы сложности, соответственно, зафиксированных за весь период испытаний (см. таблицу1).
1.3 Вероятность безотказной работы в заданный период наработки от и
в общем случае определяется по формуле:
(14)
При этом предполагается, что при наработке комбайн работоспособен.
Для малых промежутков наработки параметр потока отказов можно принять постоянным = const, тогда формула 14 примет вид:
(15)
Принимая постоянным значение параметра потока отказов в пределах одного интервала, определяется вероятность безотказной работы в каждом интервале
(16)
В течении одной смены в любом интервале
(17)
Например, для третьего интервала при сменной наработке -9,3 га, вероятность безотказной работы будет равна:
Это означает, что в течение одной смены безотказно будет работать только 69 комбайнов из 100. У остальных 31следует ожидать появление хотя бы одного отказа.
2. Определение показателей ремонтопригодности
2.1 Показателем ремонтопригодности, определяемым по результатам испытаний, является - среднее время восстановления работоспособности, час.
Оно может быть рассчитано по всем отказам за весь период испытаний
(18)
В каждом интервале
(19)
По отказам каждой группы
(20)
(21)
(22)
Где – суммарное время восстановления всех отказов (или отказов соответствующей группы сложности, см. табл. 1), час;
– общее число отказов всех машин, устраненных за весь период испытаний.
В нашем примере =304,5 час;
=52,5 час;
=160,8 час;
=91,2 час;
=122;
=69;
=40;
=8 по
формулам 18, 19, 20, 21 получаем:
час.;
час.;
час.
Если отказы не устранялись в течении испытаний, то по ним не указывается время восстановления (см. табл. 1). Обычно это ресурсные отказы 3 группы сложности, для устранения которых необходима замена основных агрегатов или капитальный ремонт объекта. При необходимости такого ремонта объект снимается с испытаний и направляется в ремонтное предприятие.
3. Определение комплексного показателя надежности - коэффициента готовности
Это вероятность того, что объект окажется работоспособным в произвольный момент времени.
Полученные данные при проведенных испытаниях позволяют определить
- коэффициент готовности, характеризующий одновременно два свойства - безотказность и ремонтопригодность.
(23)
Где – коэффициент перевода единиц наработки (га, Т, км, моточас) в часы чистой работы. Этот коэффициент для комбайнов может быть определен по расчетной (теоретической)
производительности машины га/час. Для комбайнов СК-5 прием
=1,33 га/час, тогда
=0,75 га/час.
Коэффициент готовности может рассчитываться за весь период испытаний (сезон работы), а также по интервалам наработки.
В третьем интервале (по формуле 23) имеем
Это означает, что 14% рабочего времени комбайн простаивает на устранении отказов.
Список литературы
1. Зорин В.А. Основы работоспособности технических систем. – М.: Издательский центр «Академия», 2009. – 208 с.
2. Исаенко П.В. Основы работоспособности технических систем./П.В. Исаенко, А.В. Исаенко. – Томск: Изд-во ТГАСУ, 2014. – 324 с.
3. Надежность и ремонт машин/В. В. Курчаткин, Н.Ф. Тельнов, К.А. Ачкасов и др.; Под ред. В.В. Курчаткина. – М.: Колос, 2000. – 776 с.
Министерство сельского хозяйства РФ
Федеральное государственное образовательное учреждение высшего профессионального образования
«Пермская сельскохозяйственная академия имени академика
Д.Н. Прянишникова»
Кафедра «Технического сервиса и ремонта машин»
Контрольная работа
«Основы работоспособности ТС»
Выполнил:
студент заочного факультета
Шифр: Эт-13-158
Гусельников С.И.
Проверил:
Куимов Ю.Е.
Пермь 2016
Теоретическая часть
Основные причины изменения технического состояния объектов.
Под техническим состоянием объекта подразумевается состояние его свойств в данный момент времени, в процессе эксплуатации свойства объекта изменяются под воздействием различных факторов. Внешне это проявляется как отклонение параметров, характеризующих эти свойства, от установленных нормативно-технической документацией. Как отмечалось, изменение свойств объекта отображается в совокупности выходных его параметров, в том числе параметров материальных и энергетических выходных потоков, геометрических размеров и физических параметров (прочности, вязкости, твердости и т. п.) конструкционных материалов, часто называемых структурными. По изменению параметров материальных и энергетических потоков (на фиксированном режиме работы) можно судить только о том, изменилось ТС объекта или нет. На вопрос же о том, что явилось причиной изменения ТС, позволяет ответить только информация об изменении структурных параметров.
В связи с этим принято считать, что по отклонению технико-экономических показателей оценивается изменение качества функционирования технического объекта, а по отклонениям структурных параметров - изменение его технического состояния. Поэтому эффективная техническая эксплуатация любого технического объекта невозможна, если неизвестны основные причины и закономерности изменения структурных параметров под воздействием рабочих процессов и внешних воздействий.
Изнашивание
Трение поверхностей сопровождается изнашиванием. В зависимости от условий и режимов трения, физико-механических свойств применяемых материалов, микрорельефа поверхностей и других параметров, определяющих характер изнашивания, при трении двух сопряжённых поверхностей происходят сложные процессы, которые приводят к их износу.
Под износом понимается результат изнашивания, проявляющийся в виде отделения или остаточной деформации материала. Износы могут быть естественные, ускоренные и аварийные. В процессе эксплуатации автомобилей происходит естественное изнашивание деталей. Графически процесс изнашивания двух сопряжённых деталей обычно изображают следующим образом.
Рис. Характер протекания процесса изнашивания сопряженных деталей: 1 — при установившейся скорости изнашивания; 2 — при снижении скорости изнашивания; 3 — при уменьшении зазора в конце приработки
По вертикальной оси прямоугольной системы координат откладывают, в выбранном масштабе, величину износа деталей, а по горизонтальной пробег автомобиля. Точки соединяют плавными линиями. Полученные кривые показывают характер нарастания износа каждой детали по мере увеличения пробега автомобиля. Расстояние между кривыми свидетельствует о характере изменения зазора в сопряжении. Зазор SH устанавливается между деталями при сборке.
На идеализированной схеме можно выделить три этапа процесса изнашивания:
Каждый из этих этапов отражает е состояние сопряженной пары. Переход от одного этапа к другому определяется количественным накоплением отдельных повреждений. На этапе приработки скорость изнашивания повышенная. Новые или отремонтированные детали
|
|
Поперечные профили набережных и береговой полосы: На городских территориях берегоукрепление проектируют с учетом технических и экономических требований, но особое значение придают эстетическим...
Типы сооружений для обработки осадков: Септиками называются сооружения, в которых одновременно происходят осветление сточной жидкости...
Адаптации растений и животных к жизни в горах: Большое значение для жизни организмов в горах имеют степень расчленения, крутизна и экспозиционные различия склонов...
Папиллярные узоры пальцев рук - маркер спортивных способностей: дерматоглифические признаки формируются на 3-5 месяце беременности, не изменяются в течение жизни...
© cyberpedia.su 2017-2024 - Не является автором материалов. Исключительное право сохранено за автором текста.
Если вы не хотите, чтобы данный материал был у нас на сайте, перейдите по ссылке: Нарушение авторских прав. Мы поможем в написании вашей работы!