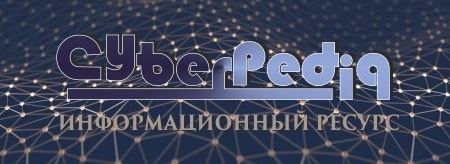
Эмиссия газов от очистных сооружений канализации: В последние годы внимание мирового сообщества сосредоточено на экологических проблемах...
Адаптации растений и животных к жизни в горах: Большое значение для жизни организмов в горах имеют степень расчленения, крутизна и экспозиционные различия склонов...
Топ:
Теоретическая значимость работы: Описание теоретической значимости (ценности) результатов исследования должно присутствовать во введении...
Устройство и оснащение процедурного кабинета: Решающая роль в обеспечении правильного лечения пациентов отводится процедурной медсестре...
Основы обеспечения единства измерений: Обеспечение единства измерений - деятельность метрологических служб, направленная на достижение...
Интересное:
Принципы управления денежными потоками: одним из методов контроля за состоянием денежной наличности является...
Средства для ингаляционного наркоза: Наркоз наступает в результате вдыхания (ингаляции) средств, которое осуществляют или с помощью маски...
Распространение рака на другие отдаленные от желудка органы: Характерных симптомов рака желудка не существует. Выраженные симптомы появляются, когда опухоль...
Дисциплины:
![]() |
![]() |
5.00
из
|
Заказать работу |
Содержание книги
Поиск на нашем сайте
|
|
Недостатками штанговых насосов является ограниченность глубины их подвески и малая подача нефти из скважин.
На заключительной стадии эксплуатации вместе с нефтью из скважин поступает большое количество пластовой воды, применение штанговых насосов становится малоэффективным. Этих недостатков лишены установки электроцентробежных насосов (рис. 11.1, табл. 11.1.).
Электроцентробежные насосы – это малогабаритные (по диаметру) центробежные, секционные, многоступенчатые насосы с приводом от электродвигателя. Обеспечивают подачу 10 – 1300 м3/сут и более, напором 450 – 2000 м вод. ст. и более.
В зависимости от поперечного размера погружного агрегата, УЭЦН делят на три условные группы: 5, 5А и 6 с диаметрами соответственно 93, 103, 114 мм, предназначенные для эксплуатационных колонн соответственно не менее 121,7; 130; 114,3 мм.
Пример условного обозначения – УЭЦНМК5-50-1200,У – установка; Э – привод от погружного электродвигателя; Ц – центробежный; Н – насос; М – модульный; К – коррозионно-стойкого исполнения; 5 – группа насоса; 50 – подача, м3/сут; 1200 – напор, м.
Электродвигатели в установках применяются асинхронные, 3 фазные с короткозамкнутым ротором вертикального исполнения ПЭД40-103– обозначает: погружной электродвигатель, мощностью 40 кВт, диаметром
103 мм. Двигатель заполняется специальным маловязким, высокой диэлектрической прочности маслом, служащим для охлаждения и смазки.
Для погружных электродвигателей напряжение составляет 380 –2300В, сила номинального тока 24,5 – 86 А при частоте 50 Гц, частота вращения ротора 3000 мин –1, температура окружающей среды от + 50 до + 90 0С.
Модуль-секция насос – центробежный многоступенчатый, секционный. Число ступеней в насосном агрегате может составлять от 220 до 400.
|
При откачивании пластовой жидкости, содержащей у сетки входного модуля насоса свыше 25 % (до 55 %) по объему свободного газа, к насосу подсоединяется газосепаратор, который отводит в затрубное пространство часть газа из пластовой жидкости и улучшает работу насоса.
Гидравлическая характеристика погружного электроцентробежного насоса (ПЭЦН) дается заводом – изготовителем при работе насоса на воде плотностью ρ = 1000 кг/м3 (количество ступеней – 100) и представляет собой зависимости (см. рис. 11.2): напора Н от подачи Q (Н=f(Q)); коэффициента полезного действия КПД – η от Q (η = f(Q)); мощности N от Q (на рис. не показано). При закрытой задвижке и подаче Q = 0, насос развивает максимальный напор Hmax (кривая 1). В этом случае КПД равен нулю. Если насос работает без подъема жидкости (Н = 0, η = 0), подача его максимальна (Qmax).
Наиболее целесообразная область работы насоса – зона максимального КПД (кривая 2). Значение ηmax достигает 0,5 – 0,6. Режим эксплуатации насоса, когда напор Нопт и подачи Qопт соответствуют точке с максимальным КПД, называют оптимальным (точка М).
Под режимом эксплуатации насоса понимается пересечение гидравлической характеристики насоса (кривая 1) с его «внешней сетью», в данном случае гидродинамической характеристикой скважины (кривая 3). Под гидродинамической характеристикой скважины понимается совокупная характеристика работы пласта и подъемника, которая выражается графической зависимостью напора (давления) в функции дебита (подачи)
(H = f (Q)).
Задача рационального выбора компоновки УЭЦН сводится к подбору такого режима насоса, когда пересечение кривых 1 и 3 будет находиться в «рабочей зоне», которая лежит на кривой 1, где ηм (0,8 – 0,85)ηmax. Регулирование режима возможно как изменением характеристики насоса (изменением числа оборотов, изменением числа ступеней и др.), так и изменением характеристики «внешней сети» (изменением диаметра НКТ, применением штуцеров и др.).
|
|
Рисунок 11.2 – Гидравлическая характеристика ПЭЦН
Таблица 11.1 – Установки электроцентробежных насосов
Наименование установок | Мин. (внутр.) диаметр эксплуатацион-ной колон-ны | Поперечный габарит установки, мм | Подача, м3/сут | Напор, м | Мощность двигателя, кВт | Тип газосепаратора |
УЭЦНМ5-50 | 121,7 | 990 – 1980 | 32 – 45 | |||
УЭЦНМ5-80 | 900 – 1950 | 32 – 63 | ||||
УЭЦНМК5-80 | ||||||
УЭЦНМ5-125 | 745 – 1770 | 1МНГ5 | ||||
УЭЦНМК5-125 | ||||||
УЭЦНМ5-200 | 640 – 1395 | 45 – 90 | 1МНГК5 | |||
УЭЦНМ5А-160 | 130,0 | 790 – 1705 | 32 – 90 | МНГА5 | ||
УЭЦНМ5А-250 | 795 – 1800 | 45 – 90 | МНГА5 | |||
УЭЦНМК5-250 | ||||||
УЭЦНМ5А-400 | 555 – 1255 | 63 – 125 | МНГК5А | |||
УЭЦНМК5А-400 | ||||||
УЭЦНМ6-250 | 144,3 | 920 – 1840 | 63 – 125 | |||
УЭЦНМ6-320 | 755 – 1545 | |||||
УЭЦНМ6-500 | 144,3 или 148,3 | или 140,5 | 800 – 1425 | 90 – 180 | ||
УЭЦНМ6-800 | 148,3 | 140,5 | 725 – 1100 | 125 – 250 | ||
УЭЦНМ6-1000 | 148,3 | 140,5 | 615 – 1030 | 180 –250 |
Погружной насос, электродвигатель, гидрозащита соединяются между собой фланцами и шпильками. Валы насоса двигателя и гидрозащита имеют на концах шлицы и соединяются между собой шлицевыми муфтами.
Гидрозащита предназначена для защиты ПЭД от проникновения в его полость пластовой жидкости и смазки сальника насоса и состоит из протектора и компенсатора.
Кабель с поверхности до погружного агрегата подводят питающий, полиэтиленовый бронированный (эластичная стальная оцинкованная лента) круглый кабель (типа КПБК), а в пределах погружного агрегата – плоский типа (КПБП).
Станция управления обеспечивает включение и отключение установки, само запуск после появления исчезнувшего напряжения и аварийное отключение (перегрузки, короткое замыкание, колебания давления, отсутствие притока и др.).
Станции управления (ШГС-5804 для двигателей с мощностью N до 100 кВт, КУПНА-79 для двигателей с N больше 100 кВт). Они имеют ручное и автоматическое управление, дистанционное управление с диспетчерского пункта, работают по программе.
|
Имеется отсекатель манифольдного типа РОМ-1, который перекрывает выкидную линию при повышении или резком снижении давления (вследствие прорыва трубопровода).
Трансформаторы регулируют напряжение питания с учетом потерь в кабеле (25 – 125 В на 1000 м).
Погружные винтовые и гидропоршневые насосы
Это новые виды погружных насосов.
Винтовой насос – это тоже погружной насос с приводом от электродвигателя, но жидкость в насосе перемещается за счет вращения ротора-винта. Особенно эффективны насосы этого типа при извлечении из скважин нефтей с повышенной вязкостью.
Применяются насосы с приводом на устье скважин, производительность которых до 185 м3/сут; напор до 1830 м.
Гидропоршневой насос – это погружной насос, приводимый в действие потоком жидкости, подаваемой в скважину с поверхности насосной установкой. При этом в скважину опускают два ряда концентрических труб диаметром 63 и 102 мм. Насос опускают в скважину внутрь трубы диаметром 63 мм и давлением жидкости прижимают к посадочному седлу, находящемуся в конце этой трубы. Поступающая с поверхности жидкость приводит в движение поршень двигателя, а вместе с ним и поршень насоса. Поршень насоса откачивает жидкость из скважины и вместе с рабочей жидкостью подает ее по межтрубному пространству на поверхность.
10. УСТАНОВЛЕНИЕ ОПТИМАЛЬНОГО ТЕХНОЛОГИЧЕСКОГО РЕЖИМА [6]
Геологическая служба ежеквартально или один раз в полгода в соответствии с данными проекта разработки, опыта эксплуатации и результатами исследования скважин, устанавливает технологический режим работы скважин. Этот режим называется фактическим.
Технологический режим, который устанавливается при составлении проектов разработки газовых месторождений на много лет вперед, называется расчетным.
Существуют три тенденции в обосновании технологического режима эксплуатации газовых и газоконденсатных скважин:
1. Режим работы скважины должен соответствовать 10 – 25 % абсолютно свободного дебита скважины, т. е. дебиту, соответствующему забойному давлению 0,1 МПа.
|
2. Скважина должна эксплуатироваться при дебитах, сохраняющих линейный закон фильтрации газа в призабойной зоне, с целью экономии энергии газа в процессе разработки.
3. Режим эксплуатации каждой скважины должен обосновываться с учетом возможности разрушения призабойной зоны, образования песчано-жидкостной пробки на забое, конуса подошвенной воды (нефти при наличии оторочки), гидратов и др.
Среди различных факторов, влияющих на режим работы газовых скважин, наиболее трудными считаются научное обоснование и точный прогноз безводного дебита газовых скважин, вскрывших неоднородные терригенные и трещинно-пористые пласты с подошвенной водой, а также дебита скважин, вскрывших неустойчивые и слабоустойчивые пласты, с обоснованным количеством песка в продукции скважины.
Под технологическим режимом эксплуатации понимается режим, при котором поддерживается определённое соотношение между дебитом скважины и забойным давлением или его градиентом.
При установлении технологического режима эксплуатации используют исходные данные, накопленные в процессе поиска залежи, разведки и опытной эксплуатации месторождения. На технологический режим эксплуатации влияет множество факторов, причем влияние различных факторов может быть как однонаправленным, так и разнонаправленным. Поэтому при недостаточно глубоком изучении этих вопросов установленный режим может оказаться неправильным.
Нередко влияние одного фактора противоречит другому, что не позволяет учесть всю совокупность факторов. Поэтому для установления технологического режима эксплуатации газовых скважин с учетом «всех» факторов должны быть обоснованы и рекомендованы соответствующие принципы и математические критерии. Такие принципы и критерии могут быть реализованы путем обобщения по группам различных факторов. Причем, используя накопленный опыт установления технологического режима эксплуатации газовых скважин, заблаговременно можно исключить часть факторов, связанных с условиями вскрытия, свойствами промывочной жидкости, совершенством скважины, образованием пробок, техникой и технологией сбора, осушки и очистки газа и др. Тогда к основным факторам, влияющим на технологический режим эксплуатации газовых и газоконденсатных скважин, можно отнести следующие:
· деформацию и устойчивость к разрушению продуктивного разреза;
· наличие активной подошвенной или контурной воды, способной по сверхпроницаемым пропласткам сравнительно быстро обводнить скважины, вскрывшие газоносную толщину, включая сверхпроницаемый пропласток;
· условия вскрытия пласта, степень и характер вскрытия с учетом близости контактов газ – нефть или газ – вода;
|
· возможность образования жидкостных или песчано-жидкостных пробок в процессе эксплуатации.
По мере истощения залежи, продвижения подошвенной и контурной воды, снижения дебита газа во времени, уменьшения пластового и забойного давлений наступает время, когда установленный режим не обеспечивается, и тогда необходимо изменить выбранный технологический режим эксплуатации. Вновь устанавливаемый технологический режим эксплуатации также обосновывается, как и в начале разработки месторождения.
При полном и безусловном соблюдении перечисленных выше принципов установления технологического режима эксплуатации будет достигнута рациональная разработка газовых и газоконденсатных месторождений.
Необходимость изменения установленного технологического режима обусловлена изменением характеристик пласта и скважин в процессе разработки, проведением определенных мероприятий, позволяющих увеличить производительность скважин, или ремонтно-профилактических работ, нередко приводящих к снижению их производительности.
12.1. Изменение технологического режима скважин [6]
В процессе эксплуатации месторождения необходимость изменения технологического режима возникает по ряду причин.
Наличие подошвенной воды при установлении технологического режима. В этом случае допустимая предельная депрессия на пласт для заданной величины вскрытия пласта – величина переменная. С изменением пластового давления величина допустимой депрессии линейно уменьшается с уменьшением пластового давления. При наличии подошвенной воды величина допустимой депрессии должна быть снижена в соответствии со снижением пластового давления. Иначе установленная в начале разработки величина допустимой депрессии на пласт приводит к неизбежному подтягиванию конуса воды в скважину, и при этом необходимо, учесть подъем поверхности контакта газ – вода. Это, в свою очередь, приведет к более интенсивному снижению производительности скважины.
Все изменения технологического режима эксплуатации независимо от того, вызваны ли они изменением пластового давления, подъемом поверхности газ – вода, изменением плотности воды и газа, установкой цементных мостов или созданием искусственного непроницаемого экрана, должны быть предусмотрены проектом разработки месторождения. При установлении технологического режима определяющим фактором может быть близость контурных вод. В этом случае критерием выбора режима могут служить несколько параметров, среди которых на первое место выходит суммарный отбор газа из месторождения до прорыва воды в скважину. Принципиально продвижение контурных вод к скважине связано с двумя показателями: общим истощением месторождения независимо от расположения скважин, в частности рассматриваемой скважины, в результате, которого происходит внедрение в газовую залежь контурной воды; созданием значительной депрессионной воронки, влияющей на темп внедрения воды в зону дренажа рассматриваемой скважины так, что он значительно опережает темп внедрения от общего истощения газоносного пласта. При сравнительно высоких темпах отбора газа из месторождения, что особенно характерно для месторождений с малыми запасами, как правило, темп внедрения контурных вод несколько отстает от темпа отбора газа. Следовательно, для сравнительно однородного пласта (или нескольких пластов) в скважинах, расположенных в зонах, не представляющих опасности прорыва контурных вод, обеспечение максимального дебита (если другие факторы не ограничивают его величину) желательно при установлении технологического режима. В то же время в скважинах, расположенных близко к контурной воде, ограничение депрессии с целью предотвращения преждевременного прорыва воды является необходимым условием. Величина депрессии в приконтурных скважинах в каждом конкретном месторождении и в каждой конкретной скважине выбирается расчетным путем исходя из коллекторских свойств пласта, их изменения от скважины до контура, пластового давления и других геолого-промысловых параметров. При наличии нескольких неоднородных пластов эти расчеты производятся по наиболее опасному с точки зрения быстрого прорыва контурной воды пласту.
Если устойчивость породы к разрушению является основным фактором при установлении технологического режима, то критерии технологического режима эксплуатации скважин устанавливаются в виде постоянного градиента давления, и его изменение в течение всего периода разработки не допускается. Если скважина вскрывает коллектор с низкой устойчивостью пород к разрушению, то в процессе разработки требуется поддерживать его постоянным до тех пор, пока не будут проведены определенные мероприятия по предотвращению разрушения пласта. Величина допустимого градиента давления для газоносных пластов с низкой устойчивостью к разрушению устанавливается на скважинах рассматриваемого месторождения в период опытно-промышленной эксплуатации. Изменение технологического режима эксплуатации скважин, установленного исходя из разрушения пласта при превышении допустимой величины градиента, может происходить при укреплении призабойной зоны специальными смолами, внедрении одновременно-раздельной эксплуатации в случае много пластовости, применении механических или гравийных фильтров, проведении ремонтно-профилактических работ скважинного или устьевого оборудования и др.
Основной фактор при установлении технологического режима – наличие в составе газа коррозионно-активных компонентов. Необходимость изменения технологического режима возникает, начиная с момента, когда дальнейшее увеличение диаметра насосно-компрессорных труб невозможно. При этом скорость потока газа не должна превышать приближенно определенную величину в любом сечении ствола скважины. Если в процессе эксплуатации скважины даже в начальный период разработки производится закачка антикоррозионного ингибитора, то изменение технологического режима эксплуатации также становится необходимостью.
Технологический режим эксплуатации скважины при определяющем факторе, связанном с коррозионно-активными компонентами в газе, также подлежит изменению (кроме случаев правильного выбора диаметра насосно-компрессорных труб до их максимально возможной величины и закачки ингибитора коррозии), если необходимо поддержать определенное устьевое давление и увеличение количества влаги в газе приводит к более интенсивной коррозии оборудования.
Изменение технологического режима работы скважины обусловлено накоплением и выносом столба жидкости или песчаной пробки на забое скважины. В том случае, когда дальнейшие изменения в конструкции насосно-компрессорных труб исключены и поступающая из пласта конденсационная, пластовая вода или тяжелые компоненты углеводородов, переходящие в жидкое состояние в призабойной зоне и стволе скважин, полностью не выносятся, процесс накопления жидкостного столба требует изменения технологического режима путем закачки в ствол скважины ПАВ или соответствующих изменений производительности скважин. Аналогичное изменение должно быть произведено при накоплении песчано-жидкостной пробки на забое скважины, приводящей к изоляции части работающего интервала. Если образовалась жидкостная или песчаная пробка, то в процессе их удаления изменением глубины спуска и диаметра насосно-компрессорных труб или применением механических средств по удалению образовавшейся пробки установление нового технологического режима является необходимостью.
Изменение технологического режима эксплуатации обусловлено необходимостью поддержания определенной величины устьевого давления или его изменением. Определяющая величина давления на устье скважин, на входе промыслового пункта осушки и очистки газа или промыслового газосборного коллектора устанавливается исходя из величины дебита скважины, параметров (длина, диаметр и др.) шлейфов, давления сепарации, давления на входе в компрессорную станцию и давления в начале газопровода. По известной заданной величине давления в одном из перечисленных узлов производятся расчеты для определения технологического режима эксплуатации скважин с учетом различных потерь давления от названного узла до пласта.
Таким образом, технологический режим эксплуатации по некоторым определяющим факторам принципиально является переменной величиной, но несоблюдение установленного технологического режима и его изменения в процессе разработки со стороны работников промыслов приводят к преждевременному выходу скважин из строя и бурению дополнительных скважин.
Наиболее часто при проектировании разработки газовых и газоконденсатных месторождений используются режимы постоянного градиента, постоянной депрессии или дебита, а также постоянного забойного давления. Причем, как правило, установленный в начальной стадии технологический режим, например постоянной депрессии или дебита, в период падающей добычи заменяется режимом постоянного устьевого давления по части скважин, устьевые давления которых отличаются от давления основного эксплуатационного фонда. В дальнейшем, с момента ввода компрессорной станции, эти скважины нередко переводятся снова на режим падающего устьевого давления. Увеличение за последние годы числа газовых и газоконденсатных месторождений, переходящих на последний этап разработки, но еще способных обеспечить выдачу значительного количества газа, происходит из-за отсутствия правильно установленного технологического режима эксплуатации скважин и конкретных рекомен-даций по данному вопросу в проектах и анализах разработки месторождений. Существенное снижение пластового давления, производительности скважин, увеличение количества влаги в газе, низкая скорость потока газа в стволе скважины и другие факторы требуют предварительной оценки и выдачи конкретных рекомендаций по режиму эксплуатации скважин в поздней стадии разработки месторождений с учетом возможного применения плунжерных лифтов, применения ПАВ и т.д. для более надежной оценки дебита каждой скважины или группы скважин и месторождения в целом.
Время перехода от одного технологического режима к другому в основном зависит от фактора или сочетания факторов, по которым устанавливался данный технологический режим, от стадии разработки залежи и условий сбора и транспорта газа. Причем первая часть этого вопроса, т. е. выбор технологического режима в зависимости от того или иного фактора, являющегося определяющим для данного месторождения, решается проектирующими организациями на базе имеющихся геолого-промысловых данных. Без выполнения указанного требования правомерность и надежность проектных показателей на месторождениях могут приводить к существенным отклонениям проектных данных от фактической возможности промысла. Указанное выше положение касается временного, или так называемого стадийного (в зависимости от периода разработки залежи), необходимого изменения технологического режима эксплуатации. Если технологический режим установлен по какому-то из перечисленных факторов, то при проведении ряда мероприятий в скважине или неожиданных изменениях по различным причинам необходимо текущее, в отдельных скважинах очень частое, изменение технологического режима эксплуатации. Эта необходимость устанавливается при периодических исследованиях скважин или проведении разных мероприятий в скважинах и корректируется в материалах по анализу разработки.
11. ЭКСПЛУАТАЦИЯ СКВАЖИН В ОСЛОЖНЕННЫХ УСЛОВИЯХ
13.1. Осложнения при эксплуатации фонтанных скважин [7]
Работа фонтанных скважин может быть осложнена в связи с отложениями парафина, солей, накоплением песка на забое, воды, а также с различного рода утечками нефти, газа, нарушением герметичности или поломками запорных устройств.
В процессе эксплуатации ведется тщательный контроль за работой скважины, что позволяет выявить осложнения, например:
– при уменьшении устьевого давления р2и одновременном повышении затрубного давления рзат – отложения парафина и солей в НКТ;
– при уменьшении давлений р2и рзат – образование песчаной пробки на забое;
– при уменьшении давления р2 и увеличении дебита Q – разъедание штуцера;
– при увеличении давлений р2и рзат и уменьшении дебита Q – засорение штуцера или отложение парафина в манифольде и выкидном шлейфе.
По пути движения нефти уменьшаются температура и давление, выделяется газ, поток охлаждается, снижается растворяющая способность нефти, выделяются твердый парафин, мазеобразные асфальтены и смолы. Наиболее интенсивно парафин откладывается в подъемных трубах. Толщина его слоя на внутренней стенке труб увеличивается от нуля на глубине 900 – 300 м до максимума на глубине 200 – 50 м, а затем уменьшается за счет смыва отложений потоком. Отложения приводят к снижению дебита.
Выкристаллизация парафина происходит на механических примесях нефти и на стенках оборудования. При этом парафин, выделившийся внутри объема, практически не принимает участия в формировании отложений. Такие кристаллы откладываются в основном на дне поверхностных резервуаров. Поэтому наиболее целесообразно добиться того, чтобы весь парафин выделялся не на стенках оборудования, а внутри объема.
Процесс отложения парафина имеет адсорбционный характер (поглощение поверхностью твердого тела). Поэтому защитные покрытия труб гидрофильными (смачивающимися водой) материалами оказались весьма эффективными для борьбы с отложениями парафина. Для создания защитных покрытий применяют лакокрасочные материалы (бакелитовый, эпоксидный, бакелитово-эпоксидный лаки), а также стекло, стекло эмаль.
Добавки в поток химических реагентов способствуют гидрофилизации стенок труб, увеличению числа центров кристаллизаций парафина в потоке, повышению дисперсности частиц парафина в нефти. Такими реагентами могут быть водо- и нефтерастворимые поверхностно-активные вещества.
Исследованиями установлено, что использование переменного магнитного поля увеличивает число центров кристаллизации в потоке и предотвращает отложение парафина.
Отложения парафина удаляют тепловыми и механическими способами. При тепловом способе проводят периодическую закачку в затрубное пространство скважины горячей нефти (газоконденсата), перегретого пара или паровоздушной смеси. При этом парафин расплавляется и выносится потоком из скважины по НКТ. Для получения водяного пара используют паропередвижные автомобильные установки типа ППУ, а для нагрева нефти – агрегат депарафинизации передвижной типа 1АДП-4-150.
При механическом способе используют скребки, которыми соскабливают отложения парафина со стенок труб. Их спускают и поднимают на проволоке (тросе) с помощью электродвигателя автоматической депарафинизационной установки типа АДУ-3 или УДС-1. Подъем автоматических летающих скребков происходит под действием напора газонефтяного потока, при этом вверху и внизу труб устанавливают амортизаторы (ограничители).
Отложения солей могут происходить на всем пути движения воды – в пласте, скважине, трубопроводах и оборудовании установок подготовки нефти. Причинами отложения солей считают химическую несовместимость вод (например, щелочных с жесткими), поступающих в скважины из различных горизонтов (пластов) или пропластков; перенасыщенность водно-солевых систем при изменении термодинамических условий. В основном солеотложения наблюдаются при внутриконтурном заводнении пресными водами, что связывают с обогащением закачиваемых вод сульфатами при контакте с остаточными водами и растворении минералов.
Отложения солей приводят к уменьшению добычи нефти, сокращению межремонтных периодов работы скважин; в некоторых случаях они столь велики, что вообще затрудняют эксплуатацию.
Основными компонентами солей могут быть либо гипс, либо карбонаты кальция и магния. В состав входят также диоксид кремния, оксидные соединения железа, органические вещества (парафин, асфальтены, смолы) и др. Осадки могут быть плотными или рыхлыми, прочность сцепления с металлом возрастает с глубиной залегания пласта. Различный состав и структура отложений требуют индивидуального подхода к выбору метода борьбы с ними на каждом конкретном месторождении.
Все методы борьбы с отложениями солей можно подразделить на две группы: методы предотвращения выпадения солей и методы удаления солевых отложений.
В комплекс работ по подготовке заводнения входит проверка закачиваемых вод на химическую совместимость с другими водами, с которыми они смешиваются в поверхностных или пластовых условиях.
Наиболее приемлемый метод предотвращения выпадения солей в трубах – применение химических реагентов (ингибиторов солеотложений). Их периодически закачивают в пласт или в затрубное пространство добывающих скважин. Ингибиторы с так называемым «пороговым эффектом» покрывают микрокристаллические ядра образующегося осадка, замедляют их рост и удерживают в растворе во взвешенном состоянии. Наиболее эффективными оказались полифосфаты, органические фосфаты, соли сульфокислот, акрилсульфонаты, гексаметафосфат и триполифосфат натрия, аммофос и др.
Менее эффективно применение воздействия на растворы магнитными полями и ультразвуком, а также использование защитных покрытий (стекло, высокомолекулярные соединения). Для борьбы с отложением солей в нефтеводосборных трубопроводах рекомендуется установка у устья специальных гипсосборников.
Отложения солей удаляют с помощью химических реагентов и, в крайнем случае, разбуривают долотом.
При химическом методе удаления осадки гипса преобразовывают в водо-растворимую соль сульфата натрия (калия) и в осадки карбоната (гидроксида) кальция, которые затем растворяют соляно кислотным раствором и промывают водой. В качестве преобразовывающих реагентов эффективными оказались карбонат и бикарбонат натрия (калия), а также гидроксиды щелочных металлов. Реагент вводят в интервал отложений, периодически его прокачивают или даже создают непрерывную циркуляцию. Затем закачивают соляно кислотный раствор и промывают водой.
13.2. Осложнения при газлифтной эксплуатации [8]
Нормальная эксплуатация газлифтных скважин иногда нарушается по ряду причин: 1) образование песчаных пробок на забое и в подъемных трубах; 2) отложение солей или парафина в трубах и выкидных линиях; 3) образование сальников из окалины в кольцевом пространстве при двухрядном лифте и затрубном пространстве при однорядном лифте; 4) засорение выкидных линий; 5) образование стойких нефтяных эмульсий.
Борьба с отложениями песка. При эксплуатации скважин в ряде случаев вместе с жидкостью в скважину поступает песок. Если не будут созданы условия для выноса на поверхность всего песка, попавшего в скважину, он будет оседать на забое, образуя песчаную пробку. Такая пробка закрывает фильтр, в результате чего доступ жидкости из пласта в скважину прекращается. Одни из мер, предпринимаемых на промыслах против образования песчаных пробок, имеют цель не допустить поступления большого количества песка в скважину, другие – создать условия, при которых поступающий в скважину песок выносился бы вместе с жидкостью на поверхность и не оседал в скважине в виде пробки.
Меры против поступления песка в скважину носят режимный характер и сводятся к ограничению депрессии, т. е. к ограничению отбора жидкости.
Регулирование отбора жидкости из компрессорных скважин осуществляется путем изменения глубины погружения подъемных труб, диаметра подъемных труб или количества нагнетаемого рабочего агента.
Образование песчаной пробки в скважине, в трубах первого ряда или в подъемных трубах можно определить по показаниям контрольно-измерительных приборов и по дебиту скважины. Кроме того, образование песчаной пробки можно обнаружить по следующим признакам. Если, например, в процессе эксплуатации скважины подача жидкости прекратилась и из скважины поступает только воздух (газ) при сниженном давлении, это указывает на то, что, на забое скважины или в трубах первого ряда на глубине ниже башмака подъемных труб образовалась песчаная пробка. Это же будет наблюдаться при больших утечках рабочего агента из газлифтной линии, что обнаруживается при проверке линии.
Для очистки песчаной пробки, образовавшейся на забое, в пространство между эксплуатационной колонной и трубами первого ряда при двухрядном подъемнике или в пространство между эксплуатационной колонной и подъемными трубами при однорядном подъемнике прокачивают нефть, не прекращая подачи газа. Иногда таким способом удается размыть пробку. Если пробку ликвидировать сразу не удается, производят подземный ремонт скважины.
Однорядный лифт не обеспечивает в достаточной мере выноса песка из скважины. Это объясняется тем, что струя жидкости от забоя до башмака движется по всему сечению скважины, которое в несколько раз больше сечения подъемных труб, и скорость движения струи часто недостаточна для выноса крупных фракций песка, который осаждается на забое и образует песчаную пробку.
Для устранения этого недостатка подъемные трубы следует спускать до фильтра, а рабочий агент нагнетать через рабочие и концевые клапаны, устанавливаемые на подъемных трубах. При двухрядном или полутора рядном лифтах воздушные трубы также следует спускать до фильтра для обеспечения высоких скоростей движения жидкости, поступающей из пласта.
При эксплуатации сильно обводненных скважин иногда в подъемных трубах, а также в арматуре отлагаются соли вследствие изменения температуры и давления в скважине по сравнению с пластовыми. Соли отлагаются в верхней части подъемных труб на протяжении 150 – 300 м от устья, в результате чего давление рабочего агента повышается и одновременно уменьшается дебит скважины вплоть до полного прекращения подачи.
Для предупреждения выпадения карбонатных солей кальция и магния в подъемных трубах, а также в арматуре и выкидных линиях в скважину закачивают различные химические реагенты.
При газлифтной эксплуатации скважин, дающих парафинистую нефть, парафин откладывается на стенках подъемных труб. Способы предупреждения отложений парафина и очистки труб от образовавшихся отложений аналогичны описанным выше, применяемым при фонтанной эксплуатации. Это применение труб, футерованных стеклом, эмалями или лаками; периодическая очистка труб механическими скребками, спускаемыми в скважину на проволоке; тепловой прогрев горячей нефтью или паром.
Кроме того, при этом способе эксплуатации можно применять летающие скребки плунжерного типа. Диаметр скребка выбирают несколько меньше диаметра труб, чтобы скребок мог свободно проходить по всей колонне, не застревая в стыках. При большой корке парафина на трубах, очистку начинают скребками небольшого диаметра, постепенно увеличивая его.
Для очистки труб такими скребками внизу колонны устанавливают нижний ограничитель или амортизатор, в верхней части арматуры – верхний амортизатор.
Устранение металлических сальников. При эрлифтной эксплуатации сжатый воздух проходит довольно значительное расстояние от компрессорной станции до скважин. Движение воздуха по трубам, особенно если в воздухе содержится много влаги, сопровождается коррозией металла. Установлено, что заметная коррозия наступает при 70 – 80 %-ной влажности. Кроме того, на коррозию влияет давление; с увеличением его возрастает скорость образования коррозии.
Иногда коррозию труб вызывает серная кислота, образовавшаяся вследствие взаимодействия сернистых соединений в нефти с кислородом нагнетаемого воздуха. Для уменьшения коррозии проводят следующие мероприятия:
а) покрывают внутренние поверхности труб лаком, стеклом или эмалью;
б) осушают воздух в конденсационных горшках;
в) периодически изменяют направление движения воздуха с кольцевой системы на центральную и наоборот.
Хорошее средство по предупреждению образования сальников – подача в скважину с помощью дозировочных насосов вместе с воздухом поверхностно-активных веществ (ПАВ).
Если указанными в
|
|
Эмиссия газов от очистных сооружений канализации: В последние годы внимание мирового сообщества сосредоточено на экологических проблемах...
Механическое удерживание земляных масс: Механическое удерживание земляных масс на склоне обеспечивают контрфорсными сооружениями различных конструкций...
Индивидуальные и групповые автопоилки: для животных. Схемы и конструкции...
История развития хранилищ для нефти: Первые склады нефти появились в XVII веке. Они представляли собой землянные ямы-амбара глубиной 4…5 м...
© cyberpedia.su 2017-2024 - Не является автором материалов. Исключительное право сохранено за автором текста.
Если вы не хотите, чтобы данный материал был у нас на сайте, перейдите по ссылке: Нарушение авторских прав. Мы поможем в написании вашей работы!