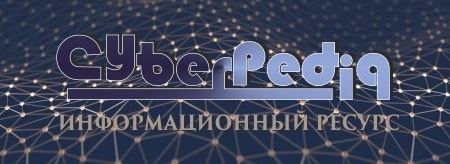
История создания датчика движения: Первый прибор для обнаружения движения был изобретен немецким физиком Генрихом Герцем...
Опора деревянной одностоечной и способы укрепление угловых опор: Опоры ВЛ - конструкции, предназначенные для поддерживания проводов на необходимой высоте над землей, водой...
Топ:
Организация стока поверхностных вод: Наибольшее количество влаги на земном шаре испаряется с поверхности морей и океанов...
Особенности труда и отдыха в условиях низких температур: К работам при низких температурах на открытом воздухе и в не отапливаемых помещениях допускаются лица не моложе 18 лет, прошедшие...
Когда производится ограждение поезда, остановившегося на перегоне: Во всех случаях немедленно должно быть ограждено место препятствия для движения поездов на смежном пути двухпутного...
Интересное:
Отражение на счетах бухгалтерского учета процесса приобретения: Процесс заготовления представляет систему экономических событий, включающих приобретение организацией у поставщиков сырья...
Национальное богатство страны и его составляющие: для оценки элементов национального богатства используются...
Уполаживание и террасирование склонов: Если глубина оврага более 5 м необходимо устройство берм. Варианты использования оврагов для градостроительных целей...
Дисциплины:
![]() |
![]() |
5.00
из
|
Заказать работу |
|
|
При построении оптимальных схем поиска неисправностей применяют методы:
"последовательного приближения (исключения)", "трудозатраты – вероятность", "половинного разбиения", "комбинированный".
Метод последовательного приближения (исключения)
В основу метода положен принцип: от простого к сложному. Сложную систему разбивают на отдельные участки, которые последовательно проверяют (на каждый участок – одна проверка). При каждой проверке непроверяемые участки отключают или заменяют их элементы на заведомо исправные. Затем на участке, где имеется неисправность, проверяют последовательно все элементы.
Описанный метод применяется при отсутствии статистических данных по надежности элементов и трудоемкости проверочных работ. Его нельзя считать оптимальным, так как продолжительность поиска неисправностей с его использованием может быть весьма значительной.
Метод половинного разбиения ("средней точки")
Этот метод определения причин отказов применяется в начальный период эксплуатации новой АТ, когда отсутствуют данные по частоте отказов и неизвестны затраты времени на проведение проверок.
В этом случае предполагается, что любой агрегат с равной вероятностью может быть причиной отказа системы, и затраты времени на осуществление различных поверок одинаковы. Сущность этого метода:
Имеется, например в системе, восемь точек проверки. Первая разбивка в этой системе производится между точками 4 и 5, после чего проверяется исправность агрегатов с 1 по 4. Если они окажутся исправными, то агрегаты с 5 по 8 опять делятся на две группы и осуществляется проверка агрегатов 5 и 6 и т.д.
Метод средней точки для определения причин отказов в начальный период число проверок эксплуатации новых образцов АТ является оптимальным, т.к. при его применении сводится к минимуму число проверок, необходимых для выявления неисправностей.
|
Комбинированный метод.
В тех случаях, когда между элементами системами имеются взаимосвязи, а трудозатраты (время), требуемые для проведения проверок и вероятности отказов известны и не равны между собой, оба рассмотренных выше метода не дают оптимальной последовательности поиска отказавшего элемента. При этом применяется так называемый "комбинированный" построения схемы поиска, в основу которого положен метод "половинного разбиения", но скорректированный с информацией о трудоемкости проверок и вероятности отказов (метод "трудозатраты – вероятность"). Он позволяет учитывать функциональные взаимосвязи между элементами, а также влияние неравенства их надежности в сложной структуре контроля.
Этот метод часто используются для разработки алгоритмов в самолетных бортовых гидравлических, топливных, пневматических, механических и других системах, а также в силовых установках.
Метод "трудозатраты – вероятность" ("время, стоимость – вероятность")
Этот метод поиска неисправностей основан на учете статистических данных о трудозатратах (среднем времени, стоимости) на проведение отдельных проверок и относительных вероятностей появления различных отказов. Пример:
Как и в случае применения метода последовательного исключения устанавливают те агрегаты и узлы исследуемой системы, неисправность которых может вызвать данный отказ. Предположим, что отказ могут вызвать пять агрегатов. С каких агрегатов начинать поиск причин отказа системы. Для ответа на этот вопрос необходимо знать относительные вероятности появления отказов этих 5 элементов W1, W2, W3, W4,W5 и трудоемкости по времени t1, t2, t3, t4, t5 выполнения работ при проверке каждого из них. Вероятность отказа агрегатов определяется по статистическим данным (опыту эксплуатации данного образца АТ).
|
На основании этих данных можно наметить наиболее рациональную последовательность определения причины отказов. Очевидно целесообразно начинать проверку там, где отношение вероятности появления отказов к величине трудозатрат будет наибольшим, т.е. сначала проверяют ненадежные элементы, требующие небольшого времени проверки.
Рассмотренный метод определения причин отказов является наиболее рациональным, однако применение его возможно только при наличии определенного опыта эксплуатации данного образца АТ.
Частными случаями рассмотренного метода могут быть: "метод проверок по возрастающей трудоемкости" (t1< t2< t3< t4< t5 и метод контроля "слабых точек", при котором проверки производятся в порядке уменьшения относительной вероятности отказа компонентов системы (W1> W2 >W3> W4> W5).
|
|
Эмиссия газов от очистных сооружений канализации: В последние годы внимание мирового сообщества сосредоточено на экологических проблемах...
Типы оградительных сооружений в морском порту: По расположению оградительных сооружений в плане различают волноломы, обе оконечности...
Типы сооружений для обработки осадков: Септиками называются сооружения, в которых одновременно происходят осветление сточной жидкости...
Своеобразие русской архитектуры: Основной материал – дерево – быстрота постройки, но недолговечность и необходимость деления...
© cyberpedia.su 2017-2024 - Не является автором материалов. Исключительное право сохранено за автором текста.
Если вы не хотите, чтобы данный материал был у нас на сайте, перейдите по ссылке: Нарушение авторских прав. Мы поможем в написании вашей работы!