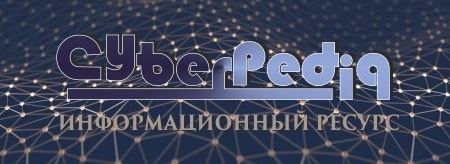
Адаптации растений и животных к жизни в горах: Большое значение для жизни организмов в горах имеют степень расчленения, крутизна и экспозиционные различия склонов...
Наброски и зарисовки растений, плодов, цветов: Освоить конструктивное построение структуры дерева через зарисовки отдельных деревьев, группы деревьев...
Топ:
Техника безопасности при работе на пароконвектомате: К обслуживанию пароконвектомата допускаются лица, прошедшие технический минимум по эксплуатации оборудования...
История развития методов оптимизации: теорема Куна-Таккера, метод Лагранжа, роль выпуклости в оптимизации...
Генеалогическое древо Султанов Османской империи: Османские правители, вначале, будучи еще бейлербеями Анатолии, женились на дочерях византийских императоров...
Интересное:
Отражение на счетах бухгалтерского учета процесса приобретения: Процесс заготовления представляет систему экономических событий, включающих приобретение организацией у поставщиков сырья...
Уполаживание и террасирование склонов: Если глубина оврага более 5 м необходимо устройство берм. Варианты использования оврагов для градостроительных целей...
Лечение прогрессирующих форм рака: Одним из наиболее важных достижений экспериментальной химиотерапии опухолей, начатой в 60-х и реализованной в 70-х годах, является...
Дисциплины:
![]() |
![]() |
5.00
из
|
Заказать работу |
|
|
Основными параметрами, которые оказывают наиболее сильное влияние на конструкцию и технико-экономические характеристики машин и которые необходимы для разработки универсальной и специальной конструкций литьевых машин, являются:
· объем впрыска за цикл (объем отливки),
· объемная скорость впрыска (время впрыска),
· давление литья,
· площадь литья,
· усилия запирания и раскрытия формы,
· ход подвижной плиты,
· максимальное расстояние между плитами,
· жесткость,
· быстроходность,
· пластикационная способность
· диапазон температур инжекционного цилиндра.
1. Усилие запирания формы. Это основной критерий для выбора ТПА. Величина усилия смыкания обычно выносится производителем термопласт автоматов в маркировку каждого конкретного ТПА.
Усилие запирания определяет максимальную площадь литья (площадью литья называют проекцию поверхности детали на плоскость, перпендикулярную оси машины). Это усилие должно быть равным усилию, возникающему в форме при литье, или быть больше него. Несоблюдение этого условия приводит к тому, что форма раскрывается, образуется облой и масса, что недопустимо в свете современных требований к качеству и экономичности процесса литья.
Необходимое усилие запирания формы зависит от технологии литья, технологических свойств полимера, а так же конфигурации получаемого изделия. Так для изготовления более глубокого изделия (при одинаковой площади) требуется большее давление для заполнения формы, поэтому и УЗ потребуется большее.
В целом УЗ должно быть таким, чтобы форма не раскрывалась при впрыске. Поэтому оно выбирается на 10-15 % больше давления литья.
Усилие запирания формы определяет конструкцию механизма смыкания термопластавтомата.
|
Существуют литьевые машины с усилием замыкания от 5 тс до 5000 тс.
2. Объем впрыска ТПА. Объем впрыска (и как следствие масса впрыскиваемого полимерного материала) – также важнейшая техническая характеристика для выбора ТПА и равен площади поршня, умноженной на его рабочий ход. Существуют литьевые машины с объемом впрыска от 1,1 см3 до 49700 см3.
3. Расстояние между плитами и ход подвижной плиты. Ход подвижной плиты - это величина, которая определяет максимальную длину изделия в направлении, параллельном оси машины.
Фактическая максимальная длина изделия, которая может быть получена при данном ходе подвижной плиты, зависит от конструкции литьевой формы, конусности изделия и эластичности термопласта. Так, при получении изделий в форме конуса длина их может быть больше расстояния между оформляющими частями литьевой формы, поскольку можно наклонить изделие при выемке. Детали из эластичного термопласта также могут иметь большую длину. При извлечении из формы детали из такого термопласта возможно временное искривление детали при прохождении ее между концом пуансона и плоскостью матрицы.
Расстояние между плитами можно регулировать в достаточно широких пределах. Как правило, на современных ТПА, максимально возможная величина высоты прессформы больше минимальной высоты примерно в 2,5 раза.
5. Объемная скорость впрыска определяет скорость подачи расплава в полость формы. Скорость впрыска зависит от мощности литьевой машины, величины давления литья и конструкции формы.
Этот параметр влияет также на механодеструкцию полимера, протекающую при заполнении формы.
В связи с этим объемная скорость впрыска должна быть такой, чтобы:
1) для заполнения литниковой системы (при наличии такой системы) и полости формы требовались сравнительно небольшое давление литья (для этого скорость впрыска не должна быть, с одной стороны, слишком большой, чтобы при заполнении не возникали большие напряжения сдвига и, следовательно, большие потери давления, и, с другой стороны, слишком малой, чтобы при заполнении не образовался большой охлажденный слой полимера и значительно понизилась температура текущего расплава, так как в противном случае возникают большие потери давления), причем форма должна заполняться с постоянной объемной скоростью течения;
|
2) формировалась структура полимерного материала изделий, обеспечивающая удовлетворительные показатели качества;
3) не произошла существенная механодеструкция полимера.
Регулирование объемной скорости впрыска осуществляется при помощи современных систем автоматики изменением расхода рабочей жидкости в гидросистеме ТПА (при применении гидравлических термопластавтоматов).
6. Давление литья – это д авление литья, необходимое для заполнения полости формы и литниковой системы (при наличии). Его значение определяют в каждом конкретном случае, учитывая конструкцию формы и изделия, свойства перерабатываемого полимерного материала, технологические особенности переработки. На современных машинах давление литья равно 60—200 МПа.
8. Пластикационная способность (производительность). Под пластикационной способностью ТПА понимают массу материала, который может быть переведен в расплав в единицу времени.
В технической документации для термопластавтоматов и каталогах на ТПА обычно приводят пластикационную способность по полистиролу при максимальной частоте вращения шнека и температуре инжекционного цилиндра 190—220 °С. При литье других термопластов пластикационная производительность будет иной. Так, у литьевой машины с червяком диаметром 42 мм пластикационная производительность по полистиролу равна 40 кг/ч, а по другим материалам ниже20: по полиэтилену низкой плотности —35 кг/ч; по полиэтилену высокой плотности — 30 кг/ч; по полиметилметакрилату — 26 кг/ч; по полиамиду 6 и полиформальдегиду — 25 кг/ч; по поликарбонату— 20 кг/ч; по полиамиду 6,6 — 16 кг/ч.
Пластикационная производительность зависит от диаметра шнека, частоты вращения, глубины нарезки и давления пластикации.
Пресс-формы
Литьевые формы предназначены для непосредственного получения изделий из расплава, подготовленного в узле пластикации ТПА. Поэтому их функция состоит в приеме расплава, его распределении по формообразующим объектам, в формовании изделий и затем в их выталкивании.
|
Конструкции литьевых форм весьма разнообразны, что вызвано двумя главными причинами: широчайшим ассортиментом получаемых изделий и разнообразием перерабатываемых полимерных материалов. Кроме того, на конструкцию литьевых форм влияет вид материала (термо- или реактопласт), тип оборудования, характер производства, особые требования к изделиям и пр.
С точки зрения состояния полимерного материала в течение цикла производства изделия литьевые формы для термопластов подразделяются на холодно- и горячеканальные.
В холодноканальных формах во время цикла формования затвердевает весь объем поступившего в форму материала.
Этот тип форм наиболее распространен в литье под давлением. До 90 % изделий, получаемых на ТПА, приходится на холодноканальную технологию.
Достоинства подобных литьевых форм: сравнительно невысокая стоимость, простота изготовления и обслуживания, сравнительно невысокая стоимость ремонтно-восстановительных операций и универсальность по виду перерабатываемых полимеров.
Принципиальное устройство холодноканальной формы следующее.
Формообразующими деталями являются матрица, пуансон и литниковая втулка, выталкиватели. Все эти детали являются технологическими, то есть непосредственно участвующими в технологии процесса.
Конструктивные детали, то есть такие, которые обеспечивают взаимодействие элементов литьевой формы, ее прикрепление к ползуну и стойке узла смыкания, терморегулирование формы и др., — это центрующая шайба, плиты, пластина и направляющие колонки с втулками. В матрице и пуансоне выполнены цилиндрические каналы для охлаждающей жидкости.
Вентиляционные каналы соединяют оформляющую полость с атмосферой. Они служат для удаления воздуха и летучих веществ из объема, заполненного расплавом.
В горячеканальных формах — определенная зона формы, горячая, постоянно заполнена расплавом, часть которого периодически поступает в формующие полости, расположенные в охлаждаемой зоне.
В настоящее время в различных странах, в зависимости от уровня их технического развития, горячеканальными формами перерабатывают от 10 до 30 % термопластов. Горячеканальная технология считается перспективной и ее применение расширяется.
|
Форма состоит из двух частей: холодной матрицы, в которой происходит формообразование изделий, и значительно более сложной горячей части. Обогреваемые горячие каналы формы постоянно заполнены расплавленным полимерным материалом. Горячеканальная часть формы оснащена усовершенствованными предкамерными узлами впрыска с точечным впуском.
Усовершенствование состоит, в частности, в использовании автономно управляемых игольчатых клапанов с индивидуальным пневматическим или иным приводом. В заданный момент игольчатый клапан перекрывает впускное отверстие, что не только прекращает течение расплава, но и позволяет практически исключить образование на поверхности изделия неровностей от литников. При работе инжекционный узел ТПА постоянно сомкнут с формой, действие ее игольчатых клапанов согласовано с движением пластикатора.
Достоинства горячеканальной технологии:
1. Полное отсутствие литниковых отходов.
2. Исключена операция отрыва литника от изделия.
3. Расплав полимера предельно приближен к формообразующей камере, что способствует повышению качества изделий поскольку не возникает линий спая.
4. Это же обстоятельство позволяет получать крупные по размеру изделия (пластмассовая мебель) с минимальной толщиной стенки и, следовательно, более эффективно использовать дорогостоящий полимерный материал.
5. Уменьшается усадка изделия за счет уменьшения остаточных напряжений, поскольку используются более высокие температуры и более низкие давления.
Недостатки горячеканальной технологии:
1. Ассортимент перерабатываемых полимеров ограничен требованиями термостабильности и вязкости.
2. Расплав полимера должен быть маловязким (ПТР > 8 г/10).
3. Инжектирование расплава требует увеличения усилия впрыска в пластикаторе за счет продавливания материала через узкие точечные впуски.
4. Высокая стоимость оборудования.
Конструкция, устройство и обслуживание формы существенно сложнее по сравнению с холодноканальными. Все это является причинами высокой стоимости горячека.нальных форм, применение которых требует тщательного технико-экономического обоснования (тираж изделий, их рыночная стоимость, продолжительность спроса и др.).
Методы литья под давлением
На сегодняшний день существует большое разнообразие разновидностей метода литья под давлением – это и многоцветное и микрослоистое литье и литье вспененных материалов, микролитье, литье с газом.
|
Для осуществления литья под давлением применяют шнековые литьевые машины, на которых устанавливают литьевые формы различной конструкции. Литьевая форма состоит из двух основных частей (пуансон и матрица) и охлаждается, как правило, водой, протекающей по каналам, расположенным в обеих половинах формы.
В матрице имеется конусное отверстие предназначенное для заполнения через него материалом полости формы и называется центральным литниковым каналом. Во время процесса литья сопло инжекционного цилиндра литьевой машины плотно примыкает к лунке.
В форме обычно имеется один или несколько разводящих литниковых каналов в зависимости от количества изделий, отливамых одновременно.
В конце разводящего литникового канала находится впускной литник, который обычно имеет сечение значительно меньших размеров, что обеспечивает легкость отделения литниковой системы от изделия)
Основными режимами, используемыми при пластикации являются инжекционный и интрузионный.
При интрузионном режиме расплав постепенно подается в форму вращающимся шнеком до заполнения ее на 70—80 %, а затем оставшаяся часть дозы впрыскивается в форму за счет поступательного движения шнека.
При инжекционном режиме вращение шнека ведется только в период набора дозы материала и его пластикации в инжекционном цилиндре литьевой машины, а подача расплава в форму осуществляется только за счет поступательного движения шнека.
Режим интрузии используется при изготовлении крупногабаритных толстостенных изделий; инжекционный процесс получил более широкое распространение.
При интрузии заполнение формы происходит при невысоком давлении. После заполнения формы подают некоторое количество расплава для уплотнения и компенсации усадки термопласта.
Цикл интрузии начинается с закрытия литьевой формы. Червяк при этом находится в переднем положении под давлением гидроцилиндра и закрывает отверстие сопла.
Затем червяк начинает вращаться, давление в передней части повышается за счет накопления материала и червяк отодвигается назад, преодолевая давление со стороны гидроцилиндра.
Открывается отверстие сопла и материал непрерывно поступает в форму.
После заполнения формы, давление перед червяком становится большим, чем давление в гидроцилиндре.
При достижении определенного давления в гидроцилиндре, вращение червяка прекращается и он начинает работать как поршень, подавая некоторое количество расплава для компенсации усадки материла в форме.
Во время выдержки под давлением червяк приближается к соплу и запирает его
После охлаждения деталь удаляется из формы.
Цикл повторяется.
По сравнению с инжекционным механизмом, интрузия имеет ряд особенностей:
1. пластикация термопласта, заполнение формы и частичное охлаждение изделия происходят одновременно.
2. литьевая форма заполняется с меньшей скоростью, чем при обычном методе литья под давлением, следовательно ниже сдвиговые деформации и внутренние напряжения.(около 20—25 МПа)
3. литниковые каналы в форме должны иметь большую площадь поперечного сечения, чтобы расплав термопласта в канале не затвердевал до окончания процесса формования изделия, т.к. давление, создаваемое при вращении червяка, ниже, чем давление поршня при обычном методе литья.
4. В связи с тем, что материал испытывает меньшие сдвиговые деформации, изделие обладает более однородной структурой и меньшей анизотропией свойств.
5. Этим методом можно перерабатывать материалы с высокой вязкостью.
6. Изделия, изготавливаемые этим методом, должны быть симметричны и впрыск должен производится в центре отливки.
7. Интрузия может осуществляться только на машинах, специально предназначенных для этой цели – нет универсальности.
Для литья под давлением используются в основном гранулированные термопласты (реже — порошкообразные) с показателем текучести расплава от 2 до 30 г/10 мин.
При инжекционном литье вращение червяка ведется только в момент набора дозы материала и его пластикации. Подача расплава в форму осуществляется за счет поступательного движения шнека.
В процессе литья полимерный материал загружается в бункер, захватывается червяком и за счет разности коэффициентов трения между м-ц и м-ч, а так же за счет вращения шнека, транспортируется вперед.
Доза расплава накапливается в передней части материального цилиндра, перемещая шнек-поршень вправо. При наборе необходимой дозы, вращение червяка прекращается и происходит впрыск. При этом весь узел пластикации и впрыска подводится к литниковой втулке литьевой формы.
Конструкция литьевых машин определяет процессы пластикации и формования полимеров, возможность реализации различных технологических режимов изготовления изделий, их качество, а также их технико-экономические показатели. Конструкции литьевых машин весьма разнообразны, но каждая из них включает основные узлы:
- узел пластикации и впрыска, состоящий из устройства для дозирования материала, пластикации его в материальном цилиндре, а затем впрыска за счёт гидроцилиндра;
- узел запирания, включающий устройство для перемещения литьевой формы, удержания её в сомкнутом состоянии и выталкивания отливки из полости формы;
- аппаратуру для управления технологическими режимами;
- устройства, обеспечивающие безопасность работы (блокировки механические, электрические).
Назначение механизма пластикации и впрыска состоит в выполнении следующих технологических операций:
- набор и пластикация дозы перерабатываемого материала;
- впрыск расплава и выдержка его под давлением в форме до затвердевания материала в литнике.
Наиболее современной и рациональной является схема червячно-поршневой пластикации в одну линию, обеспечивающая высокую точность дозирования и высокую производительность, простоту конструкции и отсутствие мест застоя материала. Материал в червячных пластикаторах этой конструкции находится в непрерывном движении и поэтому непрерывно гомогенизируется. Прогрев материала осуществляется не только за счёт теплопередачи от нагретых стенок цилиндра, но и за счёт диссипативных тепловыделений при трении материала и его деформировании.
При расположении механизмов пластикации и впрыска в одну линию (рис. 51) червяк выполняет две функции: пластицирует и накапливает необходимую дозу расплава и впрыскивает расплав в форму.
Пластикационный цилиндр 1 укреплён на корпусе 9 механизма впрыска с помощью полуколец 6 и гайки 5. Вращение червяка 3 осуществляется от гидродвигателя 10 через червячную передачу 11, вал 8 и муфту 7. Осевые нагрузки при работе червяка воспринимаются упорным подшипником 14, установленном в поршне 15 гидроцилиндра 13. Расплав нагревается электронагревателями 4; температура расплава контролируется датчиками термопар 2 с терморегуляторами. Шпильки 12 крепят гидроцилиндр 13 к корпусу 9.
Гранулированный материал проходит через загрузочное отверстие А в зону загрузки червячного пластикатора и далее, продвигаясь по червяку при его вращении, превращается в расплав. Доза расплавленного материала скапливается в передней (сопловой) части пластикационного цилиндра 1, а червяк под давлением, возникающим в дозе материала, отходит вправо. При подаче жидкости из гидросистемы машины в поршневую полость гидроцилиндра 13 поршень 15 передвигается влево, сообщая осевое перемещение червяку 3, который впрыскивает дозу расплава в полость формы.
Рис. 51.
|
|
Механическое удерживание земляных масс: Механическое удерживание земляных масс на склоне обеспечивают контрфорсными сооружениями различных конструкций...
Биохимия спиртового брожения: Основу технологии получения пива составляет спиртовое брожение, - при котором сахар превращается...
Организация стока поверхностных вод: Наибольшее количество влаги на земном шаре испаряется с поверхности морей и океанов (88‰)...
Таксономические единицы (категории) растений: Каждая система классификации состоит из определённых соподчиненных друг другу...
© cyberpedia.su 2017-2024 - Не является автором материалов. Исключительное право сохранено за автором текста.
Если вы не хотите, чтобы данный материал был у нас на сайте, перейдите по ссылке: Нарушение авторских прав. Мы поможем в написании вашей работы!