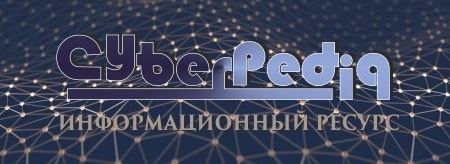
Состав сооружений: решетки и песколовки: Решетки – это первое устройство в схеме очистных сооружений. Они представляют...
Опора деревянной одностоечной и способы укрепление угловых опор: Опоры ВЛ - конструкции, предназначенные для поддерживания проводов на необходимой высоте над землей, водой...
Топ:
Установка замедленного коксования: Чем выше температура и ниже давление, тем место разрыва углеродной цепи всё больше смещается к её концу и значительно возрастает...
Организация стока поверхностных вод: Наибольшее количество влаги на земном шаре испаряется с поверхности морей и океанов...
Интересное:
Подходы к решению темы фильма: Существует три основных типа исторического фильма, имеющих между собой много общего...
Что нужно делать при лейкемии: Прежде всего, необходимо выяснить, не страдаете ли вы каким-либо душевным недугом...
Распространение рака на другие отдаленные от желудка органы: Характерных симптомов рака желудка не существует. Выраженные симптомы появляются, когда опухоль...
Дисциплины:
![]() |
![]() |
5.00
из
|
Заказать работу |
Содержание книги
Поиск на нашем сайте
|
|
Для определения поперечного сечения тупокантного бруса надо его толщину а умножить на ширину b и из полученного произведения вычесть площадь недостающих четырех прямоугольных равнобедренных треугольников, у которых одна сторона l является гипотенузой. Площадь этих треугольников в сумме равна l2. Формула для определения площади поперечного сечения тупокантного бруса следующая:
У = ab – l2
Объем тупокантного бруса будет равен
V = (ab – l2) L
При определении объема тупокантного бруса по этой формуле поперечное сечение берется на середине бруса.
Объем двухкантного бруса (лафета) вычисляется так же как и объем необрезной доски - ширина Х толщина Х длина, причем ширина вычисляется по середине бруса по формуле = ширина узкой пласти + ширина широкой пласти: 2
36) Понятие о колотых, лущеных, строганых лесоматериалах. Измельченная древесина
Путем строгания вырабатывают шпон, штукатурную дрань, стружку (упаковочную и другого назначения).
Строганый шпон представляет собой тонкие листы древесины, отличающиеся красивой текстурой и цветом. Этот облицовочный материал изготовляют из древесины многих отечественных лиственных пород, чаще из дуба, ясеня, бука, а также из экзотических пород (красного, лимонного дерева и др.). Строганый шпон получают из древесины некоторых хвойных пород — лиственницы, сосны.
Для изготовления шпона окоренные кряжи раскраивают на чураки, из которых продольной распиловкой получают брусья, или ванчесы, — части двухкантных брусьев с тремя пропиленными продольными сторонами. После пропаривания брусьев их подвергают строганию на шпонострогальных станках.
В зависимости от плоскости строгания различают шпон радиальный (Р), полурадиальный (ПР), тангенциальный (Т) и тангенциально-торцовый (ТТ). Согласно ГОСТ 2977 — 82 полурадиальным называют шпон, у которого прямые параллельные линии годичных слоев видны не менее чем на 3/4 площади листа. У тангенциально-торцового строганого шпона, получаемого из наростов, годичные слои имеют вид замкнутых кривых линий, а сердцевинные лучи — вид кривых линий или штрихов.
По качеству древесины и чистоте обработки шпон делится на два сорта. В шпоне 1-го сорта не допускаются несросшиеся и частично сросшиеся сучки, червоточина, трещины, внутренняя заболонь, пятнистость, темная прорость, царапины, риски. Некоторые пороки допускаются с ограничениями. Для шпона 2-го сорта требования к качеству древесины снижены. Параметр шероховатости Rm max должен быть не более 200 мкм для дуба, ясеня, ильма, лиственницы, сосны и красного дерева; для древесины остальных пород — не более 100 мкм. Толщина шпона в зависимости от породы и текстуры составляет от 0,4 до 1 мм с градацией 0,1 мм. У шпона Т, ПР, Р 1-го и 2-го сортов длина соответственно 900 и 400 мм и более с градацией 50 мм; ширина 120 и 60 мм и более с градацией 10 мм. У шпона ТТ 1-го сорта длина и ширина 200 мм и более, 2-го сорта — 100 мм и более.
|
Высушенные до влажности (8 ± 2) % листы шпона укладывают в пачки в порядке выхода их при строгании бруса. В пачке должно быть четное количество листов (не менее 10 шт.). Из пачек комплектуют пакеты массой от 80 до 500 кг, включающие шпон одной породы, сорта и толщины. Шпон учитывают в квадратных метрах.
Штукатурную дрань (ОСТ 13-2 —73) получают из отходов древесины хвойных и мягких лиственных пород не только путем строгания, но и раскалыванием или пилением. Штукатурная дрань используется при строительстве жилых зданий. Толщина драни 4 мм, ширина 19, 22, 25 и 32 мм, длина от 500 до 1500 мм с градацией 100 мм. Не допускаются гнили и сучки загнившие, гнилые и табачные. Ограничиваются здоровые сучки, трещины, наклон волокон, обзол и покоробленность.
Стружку упаковочную получают строганием, но из-за малости размеров ее относят к измельченной древесине.
Путем лущения получают шпон в виде непрерывной ленты древесины. После выхода из лущильного станка ленту шпона до или после сушки разрезают на форматные листы.
Лущеный шпон вырабатывают в качестве полуфабриката или товарной продукции и используют для изготовления фанеры, слоистых пластиков, для облицовки и других целей. Он предназначен также для изготовления слоистой клееной древесины и облицовки поверхности изделий из древесины. Шпон, применяемый для облицовки, отличается от строганого шпона меньшей декоративностью, но имеет большие размеры листов. В соответствии с ГОСТ 99 — 96 шпон имеет размеры по длине, от 800 до 3750 мм с градацией 100 мм, по ширине — от 150 до 750 мм с градацией 50 мм и от 800 до 3750 мм с градацией 100 мм. Толщина шпона из древесины лиственных пород 0,55; 0,75; 0,95; 1,15 мм и от 1,25 до 4 мм с градацией 0,25 мм, а из древесины хвойных пород — от 1,2 до 4 мм с градацией 0,4 мм и от 4 до 6 мм с градацией 0,5 мм.
|
В зависимости от качества древесины и обработки шпон лиственных пород подразделяют на пять сортов: Е (элита); I, II, III, IV, а шпон хвойных пород — на четыре сорта: Ех, Ix, IIX, IIIX, IVX. К качеству шпона сорта Е предъявляются очень высокие требования: не допускаются булавочные, полностью или частично сросшиеся здоровые сучки, трещины, грибные и химические окраски, ложное ядро, гнили, червоточина, прорость и ряд других пороков, а также дефекты обработки. У остальных сортов требования к качеству древесины соответственно снижаются. Так, у шпона IV сорта допускаются без ограничения сросшиеся здоровые сучки, плотно сомкнутые трещины, прорость, ложное ядро, грибные и химические окраски, гнили, дефекты обработки. С некоторыми ограничениями допускаются другие пороки. Требования к качеству шпона из хвойных пород ниже, чем шпона из лиственных пород.
Шпон изготовляют из древесины. Параметр шероховатости поверхности шпона для наружных слоев из древесины лиственных пород должен быть не более 200 мкм, а из хвойных — 320 мкм. Влажность шпона должна составлять (8 ± 2) %.
Путем раскалывания заготовляют колотые балансы. Удаление ядровой гнили из низкокачественной древесины при раскалывании поленьев позволяет получить полноценное сырье для выработки целлюлозы и древесной массы. Колотые балансы, которые поставляются только в окоренном виде, согласно ГОСТ 9463 — 88 и ГОСТ 9462—88 должны иметь размеры по длине раскола и по периметру внешней окружности не менее 50 мм. Такие же требования для дровяной древесины, идущей на технологические нужды. Древесина толщиной более 60 мм поставляется в расколотом виде, при этом наибольший размер поперечного сечения не должен превышать 40 см. Раскалывание как способ деления круглых лесоматериалов на заготовки в настоящее время применяется довольно редко, оно заменяется пилением. К колотым сортиментам относятся клепка бочарная, колесный обод, санный полоз и др.
Измельчённая древеси́на — древесные частицы различной формы и величины, получаемые в результате механической обработки, а именно: щепа, дроблёнка, стружка, опилки, древесная мука, древесная пыль.
После измельчения древесные частицы проходят сортировку по фракциям, в результате чего отбирается кондиционная фракция, размеры которой соответствуют требованиям, предъявляемым к измельчённой древесине, в зависимости от её дальнейшего назначения. Часто измельчённая древесина является отходами лесозаготовок и деревообработки. Применяется для изготовлениядревесных плит: ДВП, ДСП, ОСП, ЦСП, МДФ; служит сырьём для выработки целлюлозы и используется как топливо для котельных
|
Классификация
Древесные частицы — частицы, полученные в результате измельчения древесного сырья[2].
Щепа́ — измельчённая древесина установленных размеров, получаемая в результате измельчения древесного сырья рубильными машинами и специальными устройствами, используемая в качестве технологического сырья или топлива:
технологическая щепа — щепа для производства целлюлозы, древесных плит и продукции лесохимических и гидролизных производств. Производится из тонкомерного круглого древесного сырья диаметром 2-6 см и длиной 1,0-3,0 м с градацией 0,5 м и предельными отклонениями по длине ±5 см. В сырье не допускаются: гнили (ядровая, заболонная и наружная трухлявая) и обугленность; устанавливаются ограничения на кривизну: простая допускается со стрелой прогиба до 10 %, сложная — до 5 %; остальные пороки древесины допускаются. Высота оставляемых сучков не должна превышать более 1 см. В зависимости от продукции, вырабатывающейся из технологической щепы, устанавливается допустимое содержание в ней разных пород древесины;
зелёная щепа — щепа, содержащая примеси коры, хвои и (или) листьев;
топливная щепа — щепа для производства тепловой энергии.
Дроблёнка — древесные частицы, полученные при измельчении древесины на дробилках и молотковых мельницах.
Древесная стружка — тонкие древесные частицы, образующиеся при резании древесины.
Древесные опилки — мелкие частицы древесины, образующиеся как отходы пиления;
технологические древесные опилки — опилки, пригодные для производства целлюлозы, древесных плит и продукции лесохимических и гидролизных производств.
Древесная мука — древесные частицы заданного гранулометрического состава, полученные путём сухого механического размола древесины;
витаминная мука из древесной зелени — изготовляется из хвои, листьев, неодревесневших побегов (ветвей) и почек.
Древесная пыль — несортированные древесные частицы размером менее 1 мм
37) Модифицированная древесина
Модифицированной называют цельную древесину с направленно измененными физическими или химическими методами и свойствами. Согласно ГОСТ 23944—80 и ГОСТ 24329 — 80 различают пять основных способов модифицирования и соответствующие виды продукции.
Древесину термомеханической модификации называют еще прессованной древесиной (ДП). При прессовании предварительно пропаренной или нагретой древесины обычно в плоскости поперек волокон происходит изменение макроструктуры древесины, увеличение плотности и улучшение показателей связанных с ней свойств. Работы по термомеханической модификации, проведенные Воронежским лесотехническим институтом (ныне ВГЛТА) и другими организациями, позволили предложить различные технологические процессы и приемы получения уплотненной древесины.
|
Прессованную древесину целесообразно получать, используя мягкие лиственные породы, а в ряде случаев хвойные и даже твердые лиственные породы. Требования к сырью для изготовления ДП регламентированы ГОСТ 23551 — 79. Марки, размеры и показатели физико-механических свойств заготовок брускового и доскового типа, а также цилиндров, втулок и т. д. из прессованной древесины установлены ГОСТ 24588 — 81 и ГОСТ 9629 — 81. Плотность ДП 800-1350 кг/м3.
Прессованная древесина имеет в несколько раз большую прочность, твердость и ударную вязкость, чем натуральная, обладает достаточно хорошими антифрикционными свойствами и может быть использована для изготовления подшипников вместо бронзы, баббита и других металлов. Прессованная древесина хорошо гасит вибрации, имеет способность поглощать абразивные частицы, что предохраняет от повреждения валы. В воде прессованная древесина разбухает, и задержанные деформации возвращаются. Однако в некоторых случаях разбухание и распрессовка ДП могут оказаться полезными, например, в уплотнительных устройствах гидравлических машин. Прессованная древесина применяется для изготовления втулок опорных катков, шестерен, паркета и других целей. Прессованную древесину можно дополнительно модифицировать, наполняя ее маслами, металлами, полимерами, главным образом с целью улучшения ее свойств как антифрикционного материала.
При химико-механической модификации древесину предварительно (или одновременно) обрабатывают аммиаком, мочевиной или другими веществами, а затем уплотняют. Институтом химии древесины АН Латвии разработана технология получения лигнамона — материала из древесины, подвергнутой обработке аммиаком, прессованию и сушке. Предварительная химическая обработка вызывает изменение свойств клеточных стенок, древесина пластифицируется, ей легко придать новую форму. Пластифицированная аммиаком древесина поглощает воду, разбухает и распрессовывается. Воздействием повышенной температуры можно уменьшить эти недостатки. Показатели физико-механических свойств заготовок из лигнамона приведены в ГОСТ 9629-81.
Из цельной пластифицированной аммиаком прессованной древесины изготовляют детали мебели, паркет, музыкальные инструменты. Модифицированную мочевиной прессованную древесину (дестам) используют для покрытия полов.
Древесина термохимической модификации — это материал, получаемый пропиткой древесины мономерами, олигомерами или смолами и последующей термообработкой для полимеризации или поликонденсации пропитывающего состава.
В некоторых случаях наблюдается химическая прививка модификатора к полимерным компонентам древесины. Древесину пропитывают чаще всего фенолформальдегидными смолами, например, в виде водного раствора фенолоспиртов, смолами фуранового типа, полиэфирными смолами и др. Работы по термохимической модификации проведены в БелТИ, Центральном научно-исследовательском институте строительных конструкций (ЦНИИСК) и других организациях.
|
Модификация древесины синтетическими смолами снижает ее гигроскопичность, водопоглощение и водопроницаемость, уменьшает разбухание, повышает прочность, жесткость и твердость, но часто снижает ударную вязкость. Разработаны рецептуры смол, которые позволяют получить необходимое улучшение свойств без увеличения хрупкости материала; созданы трудногорючие и биостойкие материалы. Модифицированная термохимическим способом древесина используется в строительных конструкциях, мебельном, лыжном производствах.
При модификации древесины радиационно-химическим способом полимеризация введенных в древесину веществ происходит под воздействием ионизирующих излучений. Древесину пропитывают метилметакрилатом, стиролом, винилацетатом, акрилонитрилом и другими мономерами, а также их смесями. Работы, проведенные в филиале Физико-химического института им. В. Л. Карпова, показали, что такой способ модификации улучшает формоустойчивость, механические и эксплуатационные свойства древесины. Модифицированная древесина используется для изготовления паркета, деталей машин и других целей.
При химической модификации древесину подвергают обработке аммиаком, уксусным ангидридом или другими веществами, изменяющими ее тонкую структуру и химический состав. Обработка аммиаком повышает податливость древесины, под его воздействием древесина самоуплотняется при сушке, изменяет цвет. Обработку уксусным ангидридом проводят с целью ацетилирования древесины, т. е. введения ацетильных групп в состав ее химических компонентов. У ацетилированной древесины незначительно изменяются механические свойства, но существенно снижаются водо — и влагопоглощение, разбухание и усушка. Ацетилированную древесину целесообразно использовать для изготовления изделий повышенной формоустойчивости. Работы в области ацетилирования древесины проведены в Латвийской сельскохозяйственной академии
38) Композиционные древесные материалы
|
|
Таксономические единицы (категории) растений: Каждая система классификации состоит из определённых соподчиненных друг другу...
История развития пистолетов-пулеметов: Предпосылкой для возникновения пистолетов-пулеметов послужила давняя тенденция тяготения винтовок...
Наброски и зарисовки растений, плодов, цветов: Освоить конструктивное построение структуры дерева через зарисовки отдельных деревьев, группы деревьев...
Состав сооружений: решетки и песколовки: Решетки – это первое устройство в схеме очистных сооружений. Они представляют...
© cyberpedia.su 2017-2024 - Не является автором материалов. Исключительное право сохранено за автором текста.
Если вы не хотите, чтобы данный материал был у нас на сайте, перейдите по ссылке: Нарушение авторских прав. Мы поможем в написании вашей работы!