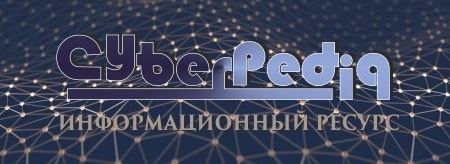
Двойное оплодотворение у цветковых растений: Оплодотворение - это процесс слияния мужской и женской половых клеток с образованием зиготы...
История развития хранилищ для нефти: Первые склады нефти появились в XVII веке. Они представляли собой землянные ямы-амбара глубиной 4…5 м...
Топ:
Когда производится ограждение поезда, остановившегося на перегоне: Во всех случаях немедленно должно быть ограждено место препятствия для движения поездов на смежном пути двухпутного...
Определение места расположения распределительного центра: Фирма реализует продукцию на рынках сбыта и имеет постоянных поставщиков в разных регионах. Увеличение объема продаж...
Теоретическая значимость работы: Описание теоретической значимости (ценности) результатов исследования должно присутствовать во введении...
Интересное:
Средства для ингаляционного наркоза: Наркоз наступает в результате вдыхания (ингаляции) средств, которое осуществляют или с помощью маски...
Аура как энергетическое поле: многослойную ауру человека можно представить себе подобным...
Берегоукрепление оползневых склонов: На прибрежных склонах основной причиной развития оползневых процессов является подмыв водами рек естественных склонов...
Дисциплины:
![]() |
![]() |
5.00
из
|
Заказать работу |
|
|
Термообработка металла является самым частоупоминаемым видом термообработки в ресурсах сети Интернет. Самый увлекательный и обескураживающий факт о термической обработке металла, ставший для абсолютного большинства узнавших о нём неожиданностью, заключается в том, что термически обрабатывают исключительно сталь.
И тогда возникает резонный и абсолютно логичный вопрос: «Но почему именно сталь? Неужели, нет иных металлов, достойных термически обрабатываться?». На самом деле есть, просто сейчас в производстве задействована лишь сталь.
Вообще, назначение термической обработки – получение требуемой твердости, улучшение прочностных характеристик металлов и сплавов. Термическая обработка подразделяется на термическую, термомеханическую и химико-термическую. Термическая обработка - только термическое воздействие, термомеханическая - сочетание термического воздействия и пластической деформации, химико-термическая - сочетание термического и химического воздействия. Термическая обработка, в зависимости от структурного состояния, получаемого в результате ее применения, подразделяется на отжиг (первого и второго рода), закалку и отпуск.
Отжиг - термическая обработка заключающаяся в нагреве металла до определенных температур, выдержка и последующего очень медленного охлаждения вместе с печью. Применяют для улучшения обработки металлов резанием, снижения твердости, получения зернистой структуры, а также для снятия напряжений, устраняет частично (или полностью) всякого рода неоднородности, которые были внесены в металл при предшествующих операциях (механическая обработка, обработка давлением, литье, сварка), улучшает структуру стали.
|
Отжиг первого рода. Это отжиг при котором не происходит фазовых превращений, а если они имеют место, то не оказывают влияния на конечные результаты, предусмотренные его целевым назначением. Различают следующие разновидности отжига первого рода: гомогенизационный и рекристаллизационный.
Гомогенизационный - это отжиг с длительной выдержкой при температуре выше 950єС (обычно 1100-1200єС) с целью выравнивания химического состава.
Рекристаллизационный - это отжиг наклепанной стали при температуре, превышающей температуру начала рекристаллизации, с целью устранения наклепаи получение определенной величины зерна.
Отжиг второго рода. Это отжиг, при котором фазовые превращения определяют его целевое назначение. Различают следующие виды: полный, неполный, диффузионный, изотермический, светлый, нормализованный (нормализация), сфероидизирующий (на зернистый перлит).
Полный отжиг производят путем нагрева стали на 30-50 °С выше критической точки, выдержкой при этой температуре и медленным охлаждением до 400-500 °С со скоростью 200 °С в час углеродистых сталей, 100 °С в час для низколегированных сталей и 50 °С в час для высоколегированных сталей. Структура стали после отжига равновесная, устойчивая.
Неполный отжиг производится путем нагрева стали до одной из температур, находящейся в интервале превращений, выдержкой и медленным охлаждением. Неполный отжиг применяют для снижения внутренних напряжений, понижения твердости и улучшения обрабатываемости резанием
Диффузионный отжиг. Металл нагревают до температур 1100-1200єС, так как при этом более полно протекают диффузионные процессы, необходимые для выравнивания химического состава.
Изотермический отжиг заключается в следующем: сталь нагревают, а затем быстро охлаждают (чаще переносом в другую печь) до температуры, находящейся ниже критической на 50-100єС. В основном применяется для легированных сталей. Экономически выгоден, так как длительность обычного отжига (13 - 15) ч, а изотермического отжига (4 - 6) ч
|
Сфероидизирующий отжиг (на зернистый перлит) заключается в нагреве стали выше критической температуры на 20 - 30 °С, выдержке при этой температуре и медленном охлаждении.
Светлый отжиг осуществляется по режимам полного или неполного отжига с применением защитных атмосфер ил в печах с частичным вакуумом. Применяется с целью защиты поверхности металла от окисления и обезуглероживания.
Закалка - это нагрев до оптимальной температуры, выдержка и последующее быстрое охлаждение с целью получения неравновесной структуры.
В результате закалки повышается прочность и твердость и понжается пластичность стали. Основные параметры при закалке - температура нагрева и скорость охлаждения. Критической скоростью закалки называется скорость охлаждения, обеспечивающая получение структуры - мартенсит или мартенсит и остаточный аустенит.
В зависимости от формы детали, марки стали и требуемого комплекса свойств, применяют различные способы закалки. Ниже упомянуты некоторые основные.
Закалка в одном охладителе. Деталь нагревают до температуры закалки и охлаждают в одном охладителе (вода, масло).
Закалка в двух средах (прерывистая закалка) - это закалка при которой деталь охлаждают последовательно в двух средах: первая среда - охлаждающая жидкость (вода), вторая - воздух или масло.
Ступенчатая закалка. Нагретую до температуры закалки деталь охлаждают в расплавленных солях, после выдержки в течении времени необходимого для выравнивания температуры по всему сечению, деталь охлаждают на воздухе, что способствует снижению закалочных напряжений.
|
|
Адаптации растений и животных к жизни в горах: Большое значение для жизни организмов в горах имеют степень расчленения, крутизна и экспозиционные различия склонов...
Кормораздатчик мобильный электрифицированный: схема и процесс работы устройства...
Типы сооружений для обработки осадков: Септиками называются сооружения, в которых одновременно происходят осветление сточной жидкости...
Организация стока поверхностных вод: Наибольшее количество влаги на земном шаре испаряется с поверхности морей и океанов (88‰)...
© cyberpedia.su 2017-2024 - Не является автором материалов. Исключительное право сохранено за автором текста.
Если вы не хотите, чтобы данный материал был у нас на сайте, перейдите по ссылке: Нарушение авторских прав. Мы поможем в написании вашей работы!