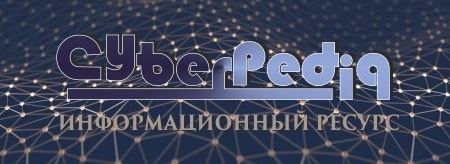
Историки об Елизавете Петровне: Елизавета попала между двумя встречными культурными течениями, воспитывалась среди новых европейских веяний и преданий...
История развития пистолетов-пулеметов: Предпосылкой для возникновения пистолетов-пулеметов послужила давняя тенденция тяготения винтовок...
Топ:
Проблема типологии научных революций: Глобальные научные революции и типы научной рациональности...
Интересное:
Средства для ингаляционного наркоза: Наркоз наступает в результате вдыхания (ингаляции) средств, которое осуществляют или с помощью маски...
Инженерная защита территорий, зданий и сооружений от опасных геологических процессов: Изучение оползневых явлений, оценка устойчивости склонов и проектирование противооползневых сооружений — актуальнейшие задачи, стоящие перед отечественными...
Финансовый рынок и его значение в управлении денежными потоками на современном этапе: любому предприятию для расширения производства и увеличения прибыли нужны...
Дисциплины:
![]() |
![]() |
5.00
из
|
Заказать работу |
|
|
Назначение и классификация магистральных газопроводов
Магистральным газопроводом называется трубопровод, предназначенный для транспорта газа из района добычи или производства в район его потребления, или трубопровод, соединяющий отдельные газовые месторождения.
Ответвлением от магистрального газопровода называется трубопровод, присоединенный непосредственно к магистральному газопроводу и предназначенный для отвода части транспортируемого газа к отдельным населенным пунктам и промышленным предприятиям.
В соответствии со СНиП 2.05.06–85* в зависимости от рабочего давления в трубопроводе магистральные газопроводы подразделяются на два класса: класс I – рабочее давление от 2,5 до 10 МПа включительно; класс II – рабочее давление от 1,2 до 2,5 МПа включительно. Газопроводы, эксплуатируемые при давлениях ниже 1,2 МПа, не относятся к магистральным. Это внутрипромысловые, внутризаводские, подводящие газопроводы, газовые сети в городах и населенных пунктах и другие трубопроводы.
По характеру линейной части различают газопроводы:
– магистральные, которые могут быть однониточными простыми (с одинаковым диаметром от головных сооружений до конечной газораспределительной станции) и телескопическими (с различным диаметром труб по трассе), а также многониточными, когда параллельно основной нитке проложены вторая, третья и последующие нитки;
– кольцевые, сооружаемые вокруг крупных городов для увеличения надежности снабжения газом и равномерной подачи газа, а также для объединения магистральных газопроводов в Единую газотранспортную систему страны.
Магистральные газопроводы и их участки подразделяются на категории, требования к которым в зависимости от условий работы, объема неразрушающего контроля сварных соединений и величин испытательного давления, приведены в таблице 1.
|
Таблица 1 – Категории магистральных трубопроводов и их участков (СН и П 2.05.06–85*, стр. 3, табл. 1)
Категория трубопровода и его участка | Коэффициент условий работы трубопровода при расчете его на прочность, устойчивость и деформативность, m | Количество монтажных сварных соединений, подлежащих контролю физическими методами, % общего количества | Величина давления при испытании и продолжительность испытания трубопровода |
В | 0,60 | ||
I | 0,75 | ||
II | 0,75 | Принимается | по СНиП III-42–80* |
III | 0,9 | ||
IV | 0,9 |
На наиболее сложных (болота, водные преграды и т.д.) и ответственных участках трассы категория магистральных газопроводов повышается. Например, для участков подключения компрессорных станций, узлов пуска и приема очистных устройств, переходов через водные преграды шириной по зеркалу воды в межень 25 м и более СНиП устанавливает категорию I.
К категории В относятся газопроводы, сооружаемые внутри зданий и на территориях компрессорных станций и газораспределительных станций. При проектировании допускается категорию отдельных участков газопроводов повышать на одну категорию, против установленной СНиПом, при соответствующем обосновании.
К категориям магистральных газопроводов и их участкам в зависимости от коэффициента условий работы при расчете на прочность предъявляются определенные требования в части контроля сварных соединений физическими методами и предварительного испытания Рисп.
Требования к трубам и материалам
Для строительства магистральных газопроводов должны применяться трубы стальные бесшовные, электросварные прямо шовные, спиральные и другие специальные конструкции, изготовленные из:
– спокойных и полуспокойных углеродистых, реже легированных сталей диаметром 50 миллиметров включительно;
|
– спокойных и полуспокойных низколегированных сталей диаметром до 1020 миллиметров;
– низколегированных сталей в термически или термодинамически упрочнённом состоянии для труб диаметром до 1420 миллиметров;
Трубы бесшовные следует применять по ГОСТ 8731–87, ГОСТ 8732–87, ГОСТ 8734–75, группы В. При соответствующем технико-экономическом обосновании можно использовать по ГОСТ 9567–75. Трубы стальные электросварные диаметром до 800 миллиметров по ГОСТ 20295–85. Для труб диаметром свыше 800 миллиметров по техническим условиям, утверждённым в установленном порядке с выполнением при заказе и приёмке труб требований, перечисленных ниже.
Трубы должны иметь сварное соединение, равнопрочное основному металлу трубы. Сварные швы труб должны быть плотными, непровары и трещины любой протяжённости и глубины не допускаются. Отклонение от номинальных размеров наружных диаметров торцов труб не должны превышать величин, приведённых в ГОСТах, а для труб диаметром свыше 800 миллиметров не должны превышать плюс минус 2 миллиметра.
Овальность концов труб, то есть отношение разности между наибольшими и наименьшими диаметрами в одном сечении к номинальному диаметру, не должна превышать 1%. Овальность труб толщиной 20 миллиметров и более не должна превышать 0,8%.
Кривизна труб не должна превышать 1,5 миллиметров на 1 метр длины, а общая кривизна не более 0,2% длины трубы.
Длина поставляемых заводом труб должна быть в пределах 10,5 – 11,6 метров.
Трубы диаметром 1020 миллиметров и более должны изготавливаться из листовой и рулонной стали, прошедшей 100% контроль физическими неразрушающими методами.
Отношение предела текучести к временному сопротивлению (то есть пределу прочности) и относительное удлинение металла труб должны удовлетворять требования СНиП.
Кольцевые сварные соединения должны выполняться с применением дуговых методов сварки (в том числе ручной, автоматической под флюсом, механизированной в среде защитных газов, механизированной само защитной порошковой проволокой), а также электроконтактной сваркой – оплавлением.
Сталь труб должна хорошо свариваться.
Пластическая деформация металла в процессе производства труб (экспандирование) должно быть не более 102%.
В металле труб не допускается наличие трещин, плён, закатов, а также расслоений длиной более 80 миллиметров в любом направлении. Расслоение любого размера на торцах труб и в зоне шириной 25 миллиметров от торца не допускается.
|
Зачистка внешних дефектов труб (кроме трещин) допускается при условии, что толщины стенки труб после зачистки не выходят за пределы допусков на толщину стенки.
Сварные соединения труб должны иметь плавный переход от основного металла к металлу шва без острых углов, подрезов, непроваров, утяжек, осевой рыхлости и других дефектов в формировании шва. Усиление наружного шва для труб с толщиной стенки до 10 миллиметров должно находиться в пределах 0,5 – 2,5 миллиметров, а более 10 миллиметров 0,5 – 3 миллиметров. Высота усиления внутреннего шва должна быть не менее 0,5 миллиметров.
Смещение наружного и внутреннего слоёв заводского сварного шва не должно превышать 20% толщины стенки при толщине до 16 миллиметров и 15% более 16 миллиметров.
Концы труб должны быть обрезаны под прямым углом и иметь раздел покромок под сварку. Форма разделки покромок определяется техническими условиями.
Косина реза торцов труб должна быть не более 2 миллиметров.
Каждая труба должна проходить на заводах изготовителях испытания гидростатическим давлением.
Все сварные соединения труб должны быть полностью проверены физическими не разрушающимися методами контроля (ультразвуком с последующей расшифровкой дефектных мест расшифровкой просвечиванием).
Подготовка трубопровода к пропуску дефектоскопа
магистральный газопровод дефект строительство
Очистка полости трубопровода выполняется в два этапа.
На первом этапе производится его очистка от грязи, парафиносмолистых отложений и инородных предметов очистным скребком. Необходимость данного этапа обуславливается тем, что металлические предметы и окалина регистрируются измерительной системой дефектоскопа – как дефекты трубы, а отложения смолопарафиновых веществ – как нарушения геометрии сечения.
На втором этапе производится очистка участка трубопровода от частиц черных металлов, путем пропуска по нему специального магнитного скребка.
|
Если обследование участка трубопровода с помощью дефектоскопа производится впервые, то прежде, чем пропустить по нему зондовый прибор, необходимо убедиться, что он свободно и беспрепятственно проходит через обследуемый участок трубопровода. С этой целью предусматривается пропуск по нему специального снаряда-шаблона. Снаряд-шаблон представляет собой упрощенную металлоконструкцию без блоков электроники и питания, тех же размеров, что и дефектоскоп.
Перед пропуском инспекционного аппарата по трассе обследуемого участка трубопровода устанавливаются маркеры, которые служат для привязки дефектограмм к местности и предварительной оценки поврежденных участков трубопровода. Маркеры являются генераторами сигналов, воспринимаемых дефектоскопом. Они размещаются на расстоянии 5–20 км друг от друга.
Частота установки маркеров определяется количеством и расположением по длине участка трубопровода естественных «маркеров» (задвижек, отводов, промежуточных насосных станций и т.д.).
При подготовке камер пуска и приема дефектоскопа прежде всего должно быть определено соответствие геометрических размеров камер размерам зонда. При необходимости производится переоборудование камер или установка новых. Камеры должны иметь площадку с твердым покрытием, т. к. для запуска и приема дефектоскопа необходимо использовать специальные приемные и запасовочные лотки, а также применять передвижные краны и другие механизмы.
Сборку, настройку и калибровку дефектоскопа для пропуска по обследуемому участку трубопровода производят в стационарных условиях.
Дефектоскоп доставляют к месту запуска с соблюдением мер предосторожности. Предпусковую функциональную проверку дефектоскопа выполняют непосредственно перед запасовкой в камеру пуска скребка.
Пропуск снаряда-шаблона и дефектоскопа производят при одинаковых режимах перекачки. Во время движения дефектоскопа по трубопроводу его сопровождает специальная бригада на автомобиле, оснащенная устройством слежения за перемещаемым в трубопроводе аппаратом, что позволяет в любой момент времени точно указать его местонахождение.
Извлечение дефектоскопа из камеры приема производится с помощью штатных технических средств. После этого аппарат очищается от перекачиваемой жидкости и подвергается осмотру с целью определения поломок и механических повреждений. Для вскрытия дефектоскоп доставляется в удобное невзрывоопасное место. Здесь отключается электропитание, разъединяются все электрические разъёмы и извлекается из контейнера электронный блок с записанной информацией. Далее производят перенос запоминающего устройства с зафиксированной информацией обследования из электронного блока в считывающее и печатающее устройство в передвижной лаборатории. После предварительного анализа результатов первого пропуска дефектоскопа по обследуемому участку трубопровода отбираются наиболее крупные, характерные дефекты, местоположение которых следует уточнить. Затем выбираются и подготавливаются места установки маркерных устройств, вблизи от выделенных дефектных мест. Второй запуск дефектоскопа в обследуемый трубопровод производят аналогично первому. По результатам сопоставления данных обоих пропусков определяются опасные дефекты.
|
Анализ результатов контроля
После пропуска снаряда-дефектоскопа специалистами инспектирующей организации проводится экспресс-анализ результатов внутритрубного обследования и представляется отчет, в котором должны быть отражены;
– полнота и качество записи информации;
– наличие отметок реперных точек (элементов обустройства, установленных маркеров);
– соответствие скорости снаряда режиму, обеспечивающему получение достоверной информации о техническом состоянии газопровода;
– информация о всех значительных дефектах.
По результатам экспресс-анализа проводятся контрольные обследования (шурфовки) в объеме, определяемом эксплуатирующей организацией. В ходе их проведения:
– измеряют расстояние между смежными реперными точками на участках, где планируется производить шурфовку;
– проверяют соответствие действительного характера обнаруженного повреждения его описанию в отчете об экспресс-анализе;
– погрешности в привязке дефектов по периметру трубы и относительно кольцевых стыков. По результатам контрольных шурфовок составляется соответствующий акт.
Отчет обязательно должен включать:
– таблицу используемых реперных точек с описанием вида реперной точки (кран, установленный маркер, отвод и др.), ее обозначением, расстояниями от камеры пуска и до следующей ближайшей реперной точки;
– таблицу особенностей трассы, включающую их описание (патрон, пригрузы, сегментные участки) с координатами начала и конца, с указанием длины;
– таблицу результатов обследования с идентификацией выявленной аномалии (коррозионные и – металлургические дефекты, гофры, вмятины, дефекты сварных соединений, тройники, отводы и др.), угловой ориентацией, размерами (длиной, шириной, глубиной), расстояниями от камеры пуска, ближайших реперных точек, поперечного сварного шва;
– трубный журнал с указанием типа трубы (прямошовная, спиральношовная), координат начала и конца, длины и толщины стенки каждой трубы.
К отчету в качестве приложений прилагаются:
– графики движения снаряда-дефектоскопа по трассе (с указанием скорости и ориентации снаряда);
– подробная информация о наиболее значительных дефектах, с указанием их трассовой привязки и визуальным цветным изображением дефектной зоны;
– масштабная схема обнаруженных элементов газопровода, особенностей и дефектов, в которой трасса газопровода графически представляет собой масштабное изображение уложенных труб по всей длине трассы, с условными обозначениями камер запуска и приема внутритрубных снарядов, линейных кранов, тройников, патронов, пригрузов, сварных стыков, установленных маркеров, выявленных дефектов и аномалий;
– диаграмма общей оценки состояния участка с указанием числа дефектных секций по видам и степени повреждений;
– график распределения дефектов вдоль трассы с координатами «глубина дефекта – длина участка газопровода»;
– угловое распределение дефектов по окружности газопровода с указанием числа дефектов и их угловой ориентации;
– цифровая информация об инспекции на машинных носителях (дискете или компакт-диске), включающая дефектограммы обследованного участка; компьютерную программу, обеспечивающую просмотр этих материалов; и текстовые файлы отчетных документов.
При приемке отчета об инспекции проверяется наличие обязательных разделов и их полнота. Далее все дефекты классифицируются как:
– дефекты потери металла (наружные, внутренние, в теле трубы);
– дефекты геометрии поперечного сечения трубы (овальность, вмятины, гофры и пр.);
– аномалии.
В случае необходимости может быть принято решение о контроле результатов инспекции с помощью щурфовки. При проведении шурфовки необходимо обратить внимание на то, сохранили ли после идентификации обнаруженные дефекты свою прежнюю классификацию на группы, укачанные выше, и укладываются ли выявленные погрешности в измерениях геометрии дефектов в установленные производителем снарядов-дефектоскопов допуски.
В случае получения отрицательного ответа на приведенные выше вопросы инспектирующей организации выставляются претензии, и вопрос решается в рамках действующего договора на выполнение внутритрубного обследования.
Под идентификацией дефектов понимается процедура, в ходе которой визуально и средствами наружной дефектоскопии определяется вид повреждения (коррозия, механическое повреждение, внутренний дефект), характер (геометрические особенности дефекта), местоположение и возможные причины образования дефектов.
Идентификацию дефектов проводит отдельная бригада, состоящая из дефектоскописта, аттестованного на второй уровень в центрах Национального аттестационного комитета по неразрушающему контролю, слесаря и представителя ЛПУ (ЛЭС), в обязанности которого входят:
– проведение вводного инструктажа и оформление наряд-допуска для работы в шурфе;
– контроль безопасности при проведении дефектоскопии обследуемого участка трубопровода.
После получения наряд-допуска дефектоскописты по карте привязки дефекта проверяют правильность выбора дефектной трубы и разметки заявленных дефектов.
Идентификация наружных дефектов имеет некоторые особенности, зависящие от вида дефекта.
Описание локальных дефектов протяженностью до 50 мм (задиры, раковины) обычно ограничивается составлением схемы дефекта на развертке трубы с указанием максимальной глубины и длины дефекта в осевом направлении и фактической толщины стенки в окрестности дефектов.
Рисунок 8 – Описание поверхностных наружных дефектов
Для более протяженных локальных дефектов необходима съемка топографии дефектов на кальке в масштабе 1:1 с измерением глубин по сетке, например, 10x10 мм.
Описание протяженных наружных коррозионных повреждений включает в себя:
– вид коррозии (равномерная, неравномерная; сплошная, пятнами; скопление язв, одиночные язвы; растрескивание);
– местоположение повреждения на развертке трубы с указанием общих размеров повреждения (длина, ширина, фоновая глубина);
– местоположение локальных, наиболее глубоких каверн, входящих в состав основного повреждения с указанием длины, ширины и глубины (таблица 2);
– съемку наиболее опасного участка на кальку в масштабе 1:1 с измерением глубин;
– толщинометрию по периметру основного повреждения с шагом 100–500 мм.
Рисунок 9. – Схема коррозионных повреждений наружной поверхности газопровода (фрагмент)
Таблица 2 – Местоположение дефектов
Обозначение дефекта | Расстояние от шва, м | Ориентация в часах- | Расположение: внешний внутренний | Локальная коррозия | Общая коррозия | Толщина стенки | |||||
глубина, мм | Длина, мм | ширина, мм | глубина, мм | длина, мм | ширина, мм | номин., мм | фактич., мм | ||||
1. | +5,0 | 6 00 | внешний | Отпечаток прилагается | 14,2 | 10,1 | |||||
2. | +2,0 |
5–7 00 | внешний | 2,5 | 30 | 30 |
1,5 |
3000 |
540 | 14.0-
14,2 |
12,5 |
2,0 | 50 | 40 | |||||||||
3. | +4,0 | 5 00 | внешний | 3,5 | 20 | 30 | - | - | - | 14,0- 14,1 | 11,5 |
3,0 | 20 | 20 | |||||||||
4. | -2,8 | 430 | внешний | 10,0 | 350 | 200 | - | - | - | 14,1–14,2 | 14,1 |
5. | -1,3 | 400 | внешний | 3,0 | 200 | 50 | - | - | - | 14,2 | 11,2 |
Границы обнаруженных дефектов на трубе обводятся масляной краской.
Полученные при внутритрубной инспекции данные должны пройти соответствующую обработку. Для этого составляются:
– конструктивная схема трубопровода с указанием отметок запорной арматуры, тройников и врезок, колен и кривых вставок, участков ручной категорийности;
– ситуационный план трассы с указанием отметок переходов трубопровода через препятствия и коммуникации, гидрогеологических особенностей трассы;
– совмещенный план конструктивной схемы и ситуации с отметками выявленных дефектов;
– диаграмма распределения дефектов по трассе в координатах «глубина дефекта – длина трубопровода»;
– то же «положение дефекта (час.) – длина трубопровода»;
– то же «количество дефектов разной степени опасности – длина трубопровода» (по предварительной классификации фирмы-исполнителя).
При наличии подобным образом обработанной информации предыдущих внутритрубных инспекций и электрометрических обследований представляется возможность комплексного анализа технического состояния трубопровода, а именно:
– оценить динамику развития дефектов во времени;
– оценить влияние рельефа и гидрогеологии трассы, состояния изоляции и катодной защиты на зарождение и развитие дефектов трубопроводов;
– откорректировать конструктивную схему трубопровода и трассовые отметки.
На основе комплексного анализа данных разрабатывается перспективная программа внутритрубных, электрометрических и других обследований трубопроводов. Периодичность внутритрубной инспекции действующих магистральных газопроводов не должна превышать 8 лет.
Ранжировка дефектов производится в два этапа. На первом этапе дефекты ранжируются согласно «Рекомендациям по расчету трубопроводов с дефектами» на опасные, потенциально-опасные и неопасные. Балльные оценки приведены в таблице 3.
Таблица 3 – Оценка опасности дефектов по несущей способности
Степень опасности дефекта | Опасные | Потенциально-опасные | Неопасные |
Основной балл | 16 | 8 | 1 |
На втором этапе производится корректировка ранга каждого дефекта в зависимости от его местоположения на трассе трубопровода согласно таблице 4.
Сумма основного и корректирующего балла дает количественную оценку степени опасности (ранг) каждого дефекта, представленного в отчете об инспекции. Согласно установленным рангам весь список дефектов разбивается на группы, характеризующие разную степень опасности или риска эксплуатации поврежденных участков трубопровода.
Все последующие работы, связанные с идентификацией и ремонтом поврежденных участков, осуществляются с учетом установленной приоритетности дефектов.
Таблица 4 – Оценка опасности дефектов в зависимости от трассовых условий
Особенности трассы | Корректирующий балл |
Переходы: – через реки, авто- и железные дороги – то же на расстоянии 500 – 1000 м – то же на расстоянии > 1000 м | 2 |
1 | |
0 | |
Пересечения с другими трубопроводами: – есть – нет | 2 |
0 | |
Близость населенных пунктов: – в радиусе 1000 м – в радиусе 1000–2000 м – в радиусе > 2000 м | 2 |
1 | |
0 | |
Состояние наружной изоляции: – плохое – удовлетворительное – хорошее | 2 |
1 | |
0 | |
Агрессивность грунтов: – высокая – средняя – низкая | 2 |
1 | |
0 | |
Электрохимзащита: – нет – есть | 1 |
0 | |
Участок трубопровода: – начальный (до первого крана) – средний – отдаленный от КС | 2 |
1 | |
0 |
Размещено на Allbest.ru
Назначение и классификация магистральных газопроводов
Магистральным газопроводом называется трубопровод, предназначенный для транспорта газа из района добычи или производства в район его потребления, или трубопровод, соединяющий отдельные газовые месторождения.
Ответвлением от магистрального газопровода называется трубопровод, присоединенный непосредственно к магистральному газопроводу и предназначенный для отвода части транспортируемого газа к отдельным населенным пунктам и промышленным предприятиям.
В соответствии со СНиП 2.05.06–85* в зависимости от рабочего давления в трубопроводе магистральные газопроводы подразделяются на два класса: класс I – рабочее давление от 2,5 до 10 МПа включительно; класс II – рабочее давление от 1,2 до 2,5 МПа включительно. Газопроводы, эксплуатируемые при давлениях ниже 1,2 МПа, не относятся к магистральным. Это внутрипромысловые, внутризаводские, подводящие газопроводы, газовые сети в городах и населенных пунктах и другие трубопроводы.
По характеру линейной части различают газопроводы:
– магистральные, которые могут быть однониточными простыми (с одинаковым диаметром от головных сооружений до конечной газораспределительной станции) и телескопическими (с различным диаметром труб по трассе), а также многониточными, когда параллельно основной нитке проложены вторая, третья и последующие нитки;
– кольцевые, сооружаемые вокруг крупных городов для увеличения надежности снабжения газом и равномерной подачи газа, а также для объединения магистральных газопроводов в Единую газотранспортную систему страны.
Магистральные газопроводы и их участки подразделяются на категории, требования к которым в зависимости от условий работы, объема неразрушающего контроля сварных соединений и величин испытательного давления, приведены в таблице 1.
Таблица 1 – Категории магистральных трубопроводов и их участков (СН и П 2.05.06–85*, стр. 3, табл. 1)
Категория трубопровода и его участка | Коэффициент условий работы трубопровода при расчете его на прочность, устойчивость и деформативность, m | Количество монтажных сварных соединений, подлежащих контролю физическими методами, % общего количества | Величина давления при испытании и продолжительность испытания трубопровода |
В | 0,60 | ||
I | 0,75 | ||
II | 0,75 | Принимается | по СНиП III-42–80* |
III | 0,9 | ||
IV | 0,9 |
На наиболее сложных (болота, водные преграды и т.д.) и ответственных участках трассы категория магистральных газопроводов повышается. Например, для участков подключения компрессорных станций, узлов пуска и приема очистных устройств, переходов через водные преграды шириной по зеркалу воды в межень 25 м и более СНиП устанавливает категорию I.
К категории В относятся газопроводы, сооружаемые внутри зданий и на территориях компрессорных станций и газораспределительных станций. При проектировании допускается категорию отдельных участков газопроводов повышать на одну категорию, против установленной СНиПом, при соответствующем обосновании.
К категориям магистральных газопроводов и их участкам в зависимости от коэффициента условий работы при расчете на прочность предъявляются определенные требования в части контроля сварных соединений физическими методами и предварительного испытания Рисп.
|
|
Археология об основании Рима: Новые раскопки проясняют и такой острый дискуссионный вопрос, как дата самого возникновения Рима...
История развития пистолетов-пулеметов: Предпосылкой для возникновения пистолетов-пулеметов послужила давняя тенденция тяготения винтовок...
Типы сооружений для обработки осадков: Септиками называются сооружения, в которых одновременно происходят осветление сточной жидкости...
Индивидуальные очистные сооружения: К классу индивидуальных очистных сооружений относят сооружения, пропускная способность которых...
© cyberpedia.su 2017-2024 - Не является автором материалов. Исключительное право сохранено за автором текста.
Если вы не хотите, чтобы данный материал был у нас на сайте, перейдите по ссылке: Нарушение авторских прав. Мы поможем в написании вашей работы!