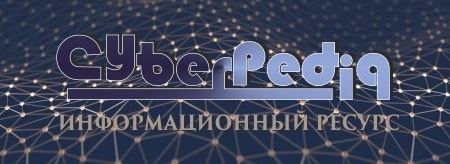
Общие условия выбора системы дренажа: Система дренажа выбирается в зависимости от характера защищаемого...
Типы оградительных сооружений в морском порту: По расположению оградительных сооружений в плане различают волноломы, обе оконечности...
Топ:
Проблема типологии научных революций: Глобальные научные революции и типы научной рациональности...
Определение места расположения распределительного центра: Фирма реализует продукцию на рынках сбыта и имеет постоянных поставщиков в разных регионах. Увеличение объема продаж...
Интересное:
Что нужно делать при лейкемии: Прежде всего, необходимо выяснить, не страдаете ли вы каким-либо душевным недугом...
Средства для ингаляционного наркоза: Наркоз наступает в результате вдыхания (ингаляции) средств, которое осуществляют или с помощью маски...
Как мы говорим и как мы слушаем: общение можно сравнить с огромным зонтиком, под которым скрыто все...
Дисциплины:
![]() |
![]() |
5.00
из
|
Заказать работу |
|
|
Сварные угловые швы в основном рассчитывают на срез по формуле:
где N – расчетная продольная сила, кН; hш – толщина углового шва, см, принимаемая равной катету вписанного равнобедренного треугольника (рис. 25); β – коэффициент, зависящий от вида сварки который должен быть оговорен в проекте; для однопроходной автоматической сварки β = 1; для двух- и трехпроходной автоматической сварки β = 0,9; для однопроходной полуавтоматической сварки β = 0,85; для двух- и трехпроходной полуавтоматической сварки β = 0,8; для ручной сварки, а также для многопроходной (более трех) автоматической и полуавтоматической сварки β = 0,7; lш – расчетная длина шва, равная его полной длине, за вычетом 10 мм, см; R_у^св = расчетное сопротивление углового шва, кН/см2.
Динамика цепной передачи. Сила удара зависит от скорости удара uy= u1-u1¢ и величины приведенных масс. Для роликовых цепей скорость удара тем меньшая, чем меньший шаг цепи р и большее число зубцов z1; для зубчатой цепи uy не зависит от числа зубцов и почти в два раза меньше, чем для роликового. Этим объясняется значительно меньший шум зубчатых цепей сравнительно с роликовыми. Самая большая сила удара действует в момент вхождения шарнира у зацепления с ведущей звездой.
Волновая зубчатая передача[править | править исходный текст]
Детали волновых зубчатых передач
Состоит из жесткого неподвижного элемента — зубчатого колеса с внутренними зубьями, неподвижного относительно корпуса передачи; гибкого элемента — тонкостенного упругого зубчатого колеса с наружными зубьями, соединенного с выходным валом; генератора волн — кулачка, эксцентрика или другого механизма, растягивающего гибкий элемент до образования в двух (или более) точках пар зацепления с неподвижным элементом. Число зубьев гибкого колеса несколько меньше числа зубьев неподвижного элемента. Число волн деформации равно числу выступов на генераторе. В вершинах волн зубья гибкого колеса полностью входят в зацепление с зубьями жёсткого, а во впадинах волн — полностью выходят из зацепления. Линейная скорость волн деформации соответствует скорости вершин выступов на генераторе, то есть в гибком элементе существуют бегущие волны с известной линейной скоростью. Разница чисел зубьев жёсткого и гибкого колёс обычно равна (реже кратна) числу волн деформации.
|
Принцип работы волновой зубчатой передачи
Например, при числе зубьев гибкого колеса 200, неподвижного элемента — 202 и двухволновой передаче (два выступа на генераторе волн) при вращении генератора по часовой стрелке первый зуб гибкого колеса будет входить в первую впадину жёсткого, второй — во вторую и т.д. до двухсотого зуба и двухсотой впадины. На следующем обороте первый зуб гибкого колеса войдёт в двести первую впадину, второй — в двести вторую, а третий — в первую впадину жёсткого колеса. Таким образом, за один полный оборот генератора волн гибкое колесо сместится относительно жёсткого на 2 зуба.
Основными причинами потери работоспособности волновых Передач являются износ зубьев, усталостные поломки гибкого колеса или выкрашивание поверхностей тел качения и беговых дорожек гибкого подшипника. Проектировочный расчет выполняют в соответствии с условным критерием, обеспечивающим необходимую износостойкость поверхностей зубьев. Геометрический расчет зацеплений (назначение модуля, числа зубьев) сопряжен с подбором наружного, диаметра гибкого подшипника генератора волн. Так как работоспособность гибкого подшипника во многих случаях ограничивает долговечность волновой передачи, необходим проверочный расчет подобранного. К вычерчиванию волновой передачи приступают после проведения расчета на выносливость гибкого колеса и проверки зацеплений на интерференцию головок зубьев гибкого и жесткого колес. [4]
|
Центробежная му́фта — муфта, предназначенная для автоматического сцепления (или расцепления) валов при достижении ведущим валом заданной скорости вращения. Может использоваться как сцепная (цилиндрическая) или предохранительная муфта.
Центробежные муфты могут использоваться:
для облегчения управления (сцепление и расцепление муфты происходит автоматически при достижении определённой частоты вращения);
для разгона механизмов машин, имеющих значительные моменты инерции, двигателями с малыми пусковыми моментами (например, асинхронных с короткозамкнутым ротором);
для повышения плавности пуска;
для предотвращения слишком большого разгона (в этом случае муфта должна быть нормально замкнутой, то есть соединять валы при частоте вращения, не превышающей некоторого граничного значения).
эти муфты способны предохранять двигатель внутреннего сгорания от остановки или резкого снижения оборотов, когда выходной вал резко тормозится.
Однако в некоторых центробежных муфтах используются силы трения, и поэтому в таких муфтах велики потери энергии. Кроме того, такие муфты нежелательно использовать для передачи больших вращающих моментов (из-за возможности проскальзывания).
Паяные соединения
Пайка — технологическая операция, применяемая для получения неразъёмного соединения деталей из различных материалов путём введения между этими деталями расплавленного материала (припоя), имеющего более низкую температуру плавления, чем материал (материалы) соединяемых деталей.
Спаиваемые элементы деталей, а также припой и флюс вводятся в соприкосновение и подвергаются нагреву с тем-пературой выше температуры плавления припоя, но ниже температуры плавления спаиваемых деталей. В результате, припой переходит в жидкое состояние и смачивает поверхности деталей. После этого нагрев прекращается, и припой переходит в твёрдую фазу, образуя соединение.
Прочность соединения во многом зависит от зазора между соединяемыми деталями (от 0,03 до 2 мм), чистоты по-верхности и равномерности нагрева элементов. Для удаления оксидной плёнки и защиты от влияния атмосферы при-меняют флюсы.
|
Паяные соединения подобны сварным; отличие пайки от сварки – отсутствие расплавления или высокотемпера-турного нагрева соединяемых деталей, так как припои имеют более низкую температуру плавления, чем материалы соединяемых деталей.
Основные критерии: прочность, жесткость, износостойкость, теплостойкость, виброустойчивость, надежность и пр.
Прочность — основной критерий работоспособности деталей, ею гарантируется длительная и надежная работа машины. Расчет деталей машин на прочность производят по формулам сопротивления материалов. В предварительных и проектных расчетах наиболее распространенным методом оценки прочности деталей является сравнение расчетных напряжений s и t с допускаемыми [s] и [t]:
Жесткость — способность деталей машин сопротивляться изменению формы под действием нагрузок. Во многих случаях окончательные размеры деталей принимают по условиям жесткости. Различают собственную жесткость детали, обусловленную деформациями всего материала детали, и контактную, которая связана с деформациями только поверхностных слоев в местах контакта.
Оценка жесткости производится сопоставлением расчетных деформаций (прогибов, углов поворота сечений, углов закручивания и пр.) с допускаемыми. Для большинства деталей (валов, штоков, грузовых и ходовых винтов, станин и т. д.) основное значение имеет собственная жесткость. В этом случае проверочный расчет жесткости конструкции выполняют по формулам сопротивления материалов. Расчет на контактную жесткость деталей машин с начальным контактом в точке (шариковые подшипники) или по линии (роликовые подшипники, зубчатые и фрикционные передачи) производят по формулам контактных напряжений и деформаций. Эти расчеты в деталях машин не рассматриваются.
Износостойкость — это способность материала оказывать сопротивление стиранию. В результате износа изменяются размеры деталей, увеличиваются зазоры, возникают дополнительные динамические нагрузки. Большой износ может привести даже к поломке детали. Износ деталей снижается с повышением твердости и понижением шероховатости трущихся поверхностей. Для повышения износостойкости деталей применяют смазку, термическую и химико-термическую обработку рабочих поверхностей, для изготовления деталей применяют антифрикционные материалы и т. п.
|
Расчет деталей на износ заключается в определении для трущихся поверхностей соответствующих допускаемых давлений.
Теплостойкость. При нагреве стальных деталей до температуры 300—400° С, а деталей из цветных сплавов и пластмасс — до температуры 100—150° С значительно снижаются механические свойства их и возникает явление ползучести. При чрезмерном нагреве значительно ухудшаются свойства смазочных масел, увеличивается износ, изменяются зазоры, появляются дополнительные динамические нагрузки. Для определения влияния нагрева машины на ее работу выполняют тепловые расчеты.
Виброустойчивост ь — это способность конструкции работать в заданном диапазоне режимов без недопустимых колебаний. Вибрация чаще всего появляется в результате недостаточной жесткости деталей машин, неуравновешенности вращающихся масс, повышения рабочих скоростей и т. д. Вибрация вызывает дополнительные переменные напряжения, создает шум, ухудшает качество работы машины, а в случае резонанса может вызвать усталостные разрушения деталей и машины.
Надежность ( общая) — свойство изделий выполнять в течение заданного времени или заданной наработки свои функции, сохраняя в заданных пределах эксплуатационные показатели. Надежность изделия обусловливается долговечностью, безотказностью, ремонтопригодностью и сохраняемостью их. Надежность деталей машин в значительной степени зависит от запасов по основным критериям работоспособности и определяется качеством их изготовления.
Долговечность — свойство изделия сохранять работоспособность до определенного состояния с необходимыми перерывами для технического обслуживания и ремонта.
Основным критерием работоспособности клепанных соединений является прочность, причем при расчетах предполагается, что напряжения в сечениях распределены равномерно.
Основным критерием работоспособности сварных соединений является прочность, причем предполагается, что напряжения в опасных сечениях распределены равномерно.
Основным критерием работоспособности крепежных резьбовых соединений является прочность.
Основными критериями работоспособности ненапряженных шпоночных соединений являются прочность шпонки на срез и прочность соединения на смятие.Расчеты на срез и смятие основаны на предположении, что соответствующие напряжения распределены по сечениям равномерно.
Итак, критерием работоспособности зубчатых передач является износостойкость активных поверхностей зубьев и их изгибная прочность.
Основными критериями работоспособности червячных передач являются износостойкость активных поверхностей и изгибная прочность зубьев червячного колеса.
Основными критериями работоспособности подшипников качения являются износостойкость рабочих поверхностей и долговечность подшипника, а также сопротивление пластическим деформациям.
|
|
История развития пистолетов-пулеметов: Предпосылкой для возникновения пистолетов-пулеметов послужила давняя тенденция тяготения винтовок...
Поперечные профили набережных и береговой полосы: На городских территориях берегоукрепление проектируют с учетом технических и экономических требований, но особое значение придают эстетическим...
Двойное оплодотворение у цветковых растений: Оплодотворение - это процесс слияния мужской и женской половых клеток с образованием зиготы...
История развития хранилищ для нефти: Первые склады нефти появились в XVII веке. Они представляли собой землянные ямы-амбара глубиной 4…5 м...
© cyberpedia.su 2017-2024 - Не является автором материалов. Исключительное право сохранено за автором текста.
Если вы не хотите, чтобы данный материал был у нас на сайте, перейдите по ссылке: Нарушение авторских прав. Мы поможем в написании вашей работы!