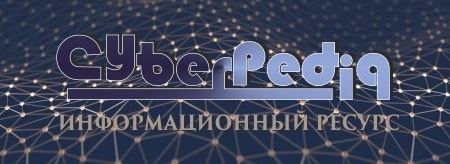
Организация стока поверхностных вод: Наибольшее количество влаги на земном шаре испаряется с поверхности морей и океанов (88‰)...
Биохимия спиртового брожения: Основу технологии получения пива составляет спиртовое брожение, - при котором сахар превращается...
Топ:
Проблема типологии научных революций: Глобальные научные революции и типы научной рациональности...
Характеристика АТП и сварочно-жестяницкого участка: Транспорт в настоящее время является одной из важнейших отраслей народного хозяйства...
Определение места расположения распределительного центра: Фирма реализует продукцию на рынках сбыта и имеет постоянных поставщиков в разных регионах. Увеличение объема продаж...
Интересное:
Уполаживание и террасирование склонов: Если глубина оврага более 5 м необходимо устройство берм. Варианты использования оврагов для градостроительных целей...
Подходы к решению темы фильма: Существует три основных типа исторического фильма, имеющих между собой много общего...
Мероприятия для защиты от морозного пучения грунтов: Инженерная защита от морозного (криогенного) пучения грунтов необходима для легких малоэтажных зданий и других сооружений...
Дисциплины:
![]() |
![]() |
5.00
из
|
Заказать работу |
ВВЕДЕНИЕ
В металлургии и ряде других отраслей техники используют ферросплавы, а также технически чистые металлы для раскисления и легирования стали, получения легированного чугуна и различных сплавов. Улучшение качества и специальные свойства конструкционных, коррозионно- стойких, жаропрочных, жаростойких, прецизионных и электротехнических сталей, специальных литейных чугунов и самых разнообразных сплавов достигается легированием различными элементами.Ферросплавы - это сплавы железа с кремнием, марганцем, хромом, вольфрамом и другими элементами, применяемые в производстве стали для улучшения ее свойств и легирования. Вводить в сталь нужный элемент не в виде чистого металла, а в виде его сплава с железом удобнее вследствие более низкой температуры его плавления и выгоднее, так как стоимость ведущего элемента в сплаве с железом ниже по сравнению со стоимостью технически чистого металла.
В металлургии ферросплавов по объёму производства первое место занимает ферросилиций, так как, кроме применения при получении стали, он используется в качестве восстановителя при получении других ферросплавов. [4]
Ферросилиций – сплав железа с кремнием.
Ферросилиций используют при производстве стали для раскисления и легирования; в ферросплавном производстве в качестве кремний содержащего материала при силикотермическом производстве ферросплавов; в горнорудной промышленности для приготовления тяжелых суспензий при гравитационном обогащении руд; в химических технологиях для получения кремнийорганических соединений¸ взрывчатых веществ и др. [1]
В качестве рудной части шихты при производстве ферросилиция используют кварц, кварцит и халцедон.
Кварц – минерал кристаллического строения белого, серого или красного цвета в зависимости от примесей.
Кварцит – горная порода в виде кристаллов кварца, скрепленных кремнеземсодержащим веществом.
Халцедон – волокнистый минерал с разной окраской и такой же, как у кварца, плотностью. [4]
ТЕХНОЛОГИЯ ПРОЦЕССА ВЫПЛАВКИ ФЕРРОСИЛИЦИЯ
Ферросилиций – сплав железа с кремнием. Химический состав ферросилиция наиболее широко используемых марок приведен в табл. 1. [3]
Таблица 1. Состав ферросилиция по ГОСТ 1415 – 78, масс. % (не более)
Марка сплава | Si | С | S | Р | Al | Mn | Cr | Са |
ФС92 | ≥ 92 | - | 0,02 | 0,03 | 2,0 | 0,2 | 0,2 | 0,5 |
ФС90 | ≥ 89 | - | 0,02 | 0,03 | 3,5 | 0,2 | 0,2 | - |
ФС75 | 74 – 80 | - | 0,02 | 0,05 | - | 0,4 | 0,4 | - |
ФС65 | 63 – 68 | - | 0,02 | 0,05 | 2,5 | 0,4 | 0,4 | - |
ФС45 | 41 – 47 | - | 0,02 | 0,05 | 2,0 | 0,6 | 0,5 | - |
ФС25 | 23 – 27 | 0,8 | 0,02 | 0,06 | 1,0 | 0,9 | 1,0 | - |
ФС20 | 19 – 23 | 1,0 | 0,02 | 0,10 | 1,0 | 1,0 | - | - |
Примечание. Остальное – железо. |
Ферросилиций относится к большой группе ферросплавов. Отечественный стандарт на ферросилиций предусматривает производство сплавов, содержащих в среднем 20, 25, 45, 65, 69, 75, 90 и 92% кремния. Среднее содержание входит в обозначение марки ферросилиция. [2]
Шихтовые материалы
В качестве рудной части шихты при производстве ферросилиция используют кварц, кварцит и халцедон. [3]
Кварц – минерал кристаллического строения (плотность 2,59 – 2,65 г/см3) белого, серого или красного цвета в зависимости от примесей.
Кварцит – горная порода в виде кристаллов кварца, скрепленных кремнеземсодержащим веществом.
Халцедон– волокнистый минерал с разной окраской и такой же, как у кварца, плотностью.
Основным требованием к рудному сырью для производства ферросилиция является высокое содержание в нем кремнезема (>96%), минимальное присутствие примесей (Al2O3, MgO, CaO), достаточная прочность при высоких температурах. Наличие в рудном сырье оксидов железа не снижает его ценности, так как при выплавке ферросилиция в шихту вводят некоторое количество железа.
Чем меньше в кремнийсодержащем сырье примесей, тем меньше будет шлака и ниже удельный расход электроэнергии.
Перед загрузкой кварцит дробят на куски размером 20-80 мм, а образующуюся мелочь отсеивают. Промывка кварцитов водой снижает содержание в них глины и других примесей и улучшает показатели электроплавки. В качестве восстановителя применяют кокс, древесный уголь, антрацит. Требования к восстановителю: низкое содержание золы, незначительное содержание летучих, достаточная прочность, стабильный размер кусков, высокое электрическое сопротивление, постоянная, достаточно низкая влажность и большая реакционная поверхность.
По характеристикам к лучшим восстановителям относятся древесный уголь, пековый и нефтяной коксы. Препятствием является их высокая стоимость и дефицитность. По этим причинам древесный уголь применяют только при производстве кристаллического кремния. Каменный уголь и антрацит имеют высокое электрическое сопротивление низкое содержание золы, однако они растрескиваются при нагреве, поэтому их применяют ограниченно и только с добавками других восстановителей.
Наибольшее применение в качестве восстановителя при производстве ферросилиция получила коксовая мелочь – отсев, который образуется при сортировке доменного кокса. Эта мелочь, называемая коксиком, имеет размер кусков 5-25 мм и содержит <13% золы.
Использование кокса как восстановителя имеет свои особенности. Наличие в нем большого количества мелочи затрудняет выход газов и нарушает ход печи. Избыток крупных кусков повышает электропроводность шихты, приводит к уменьшению заглубленности электродов в шихте и снижению производительности печи.
Для поддержания глубокой посадки электродов при выплавке ферросилиция, увеличения реакционной способности и эффективности процесса повышают удельное сопротивление металлургического кокса, для чего добавляют в шихту кокса из газовых углей отходы графитизации с электродных заводов, карборундсодержащие отходы, нефтекокс и другие восстановители.
Наряду с коксиком применяют в значительных количествах полукокс – продукт коксования углей при температуре 7000С, имеющий достаточно стабильный состав, высокое электросопротивление и хорошую реакционную способность. При работе на смеси кокса и полукокса увеличивают глубину посадки электродов и улучшают показатели работы печей.
Большое значение для технологии производства ферросплавов имеет содержание влаги в коксике и полукоксе, которое зависит от условий перевозки и хранения. Поэтому для правильной дозировки восстановителя контролируют их навеску в шихте с учетом влажности. Для повышения однородности материалов целесообразно их сушить теплом отходящих газов.
Требуемое содержание железа в ферросилиции обеспечивается применением стружки углеродистых сталей, чистой от примесей цветных металлов и легирующих элементов, достаточно габаритной и не сильно проржавевшей. Следует иметь в виду, что легирующие элементы и фосфор полностью переходят в ферросилиций, поэтому легированную и чугунную стружку использовать при производстве ферросилиция не разрешается. [3]
Состав шлака
Невосстановленные оксиды сплавляются с кремнеземом и образуют шлак. При нормальном ходе плавки количество шлака составляет 2 – 6% от массы металла, который содержит 30 – 50% SiO2, 10 – 25% Al2O3, 8 – 15% СаО, 2 – 5% MgО, 0,2 – 2,0% FeO. Температура плавления таких шлаков 1500 – 1700оС. Высокая вязкость шлака приводит к затруднениям при удалении его из печи. В результате ванна печи зарастает шлаком, снижается производительность печи, увеличивается удельный расход электроэнергии. Во избежание этого следует использовать для производства чистые материалы, полностью удалять шлак из печи. Последнее достигается глубокой и устойчивой посадкой электродов, оптимальным количеством восстановителей в шихте, вращением ванны печи.
Выпуск и разливка сплава
Выпускают жидкие продукты плавки из печи периодически. Регулярный выпуск ферросилиция из руднотермической печи способствует ее ровному ходу. Задержка в выпуске увеличивает количество металла в печи, уменьшает глубину погружения электродов в шихту и создает неустойчивый электрический режим.
Количество выпусков должно быть оптимальным. При слишком частых выпусках нарушается тепловое состояние нижней части печи из-за больших потерь тепла. Это приводит к затруднениям в выпуске сплава и шлака и потерям сплава при разливке. Слишком редкие выпуски приводят к накоплению больших количеств сплава и шлака в плавильном тигле, что снижает скорость восстановительных процессов, увеличивает потери кремния в улет. Оптимальным считается 6–7 выпусков в смену при выплавке ФС18, 20, 25 и 4–5 выпусков для ФС45, 65, 75, 90. Металл и шлак выпускают через летку, которую затем заделывают конической пробкой из смеси электродной массы и песка или массой из глины и коксика.
Ферросилиций выпускают в ковш с кладкой из шаметного кирпича или с облицовкой графитовой плиткой. Затем ферросилиций разливают в чугунные изложницы для слитков или в чушки на разливочных машинах конвейерного типа.
Исходные данные для расчета
Химические и технические составы исходных материалов приведены в таблице 2.1.
Таблица 2.1 – Химические составы исходных материалов
Материал | SiO2 | Al2O3 | Ғе2О3 | СаО | MgO | P2O5 | S | H2O | Si | C | Fe | ∑ |
Кварцит | 98,2 | 0,83 | 0,28 | 0,17 | 0,09 | 0,03 | 0,03 | 0,37 | 0 | 0 | 0 | 100 |
Зола кокса КНР | 49,5 | 22,8 | 17,9 | 5,38 | 3,48 | 0,94 | 0 | 0 | 0 | 0 | 0 | 100 |
Зола Шубак.уг. | 48,62 | 19,38 | 23,76 | 5,14 | 2,56 | 0,54 | 0 | 0 | 0 | 0 | 0 | 100 |
Fe стружка | 0 | 0 | 0 | 0 | 0 | 0 | 0,02 | 3 | 1,5 | 0,2 | 95,25 | 100 |
Итого, кг | 196,32 | 43,01 | 41,94 | 10,69 | 6,13 | 1,51 | 0,05 | 3,37 | 1,5 | 0,2 | 95,25 | 400 |
Итого, % | 49,080 | 10,753 | 10,485 | 2,673 | 1,533 | 0,378 | 0,013 | 0,843 | 0,375 | 0,050 | 23,813 | 100 |
Исходя из этого, с учетом расходов материалов на выплавку 1 тонны сплава входные данные для расчета состояния фаз для программы «TERRA» следующие, %: (SiO2 – 49,080); (Al2O3 – 10,753); (Ғе2О3– 10,485); (CaO–2,673); (P2O5– 0,378); (H2O– 0,843); (Si– 0,375); (C– 0,050); (S– 0,013); (Fe – 23,813); (MgO – 1,533).
Расчет ведем при давлении равным1 атм. и в интервале температур 1273-2273 К.
ЗАКЛЮЧЕНИЕ
1. Проведен анализ современного состояния выплавки ферросилиция, минералы, оксиды и методы получения ферросилиция, а также проведен анализ существующих способов выплавки ферросилиция.
2. В результате исследований термодинамических расчетов с использованием программного комплекса «ТЕРРА» были установлены основные существующие конденсированные и газовые фазы, характеризующие составы выплавляемых сплавов.
В результате проведенных исследований разработана и опробована в расчетных условиях технология получения ферросилиция с применением зола кокса КНР, а также термодинамические условия для выплавки ферросилиция с применением кварцита.
СПИСОК ЛИТЕРАТУРЫ
1. http://chem100.ru/elem.php?n=24
2. https://metallurgy.zp.ua/vyplavka-sredneuglerodistogo-ferrohroma/
3. Теория и технология производства: Учебник для вузов/Гасик М.И., Лякишев Н.П., Емлин Б.И. М: Металлургия, 1988.784с.
4. Гельд П.В., Баум Б.А., Петуршевский М.С. Расплавы ферросплавного производства. М: Металлургия,1973. 288с.
Свойства элементов /Под ред. Дрица М.Б.М: Металлургия 1985.271 с.
5. Хансен М. и Андерко К. Структура двойных сплавов. М., «Металлургиздат», 1962.470с.
6. Мизин В.Г., Серов Г.В. Углеродистые восстановители для ферросплавов. М.: Металлургия, 1976. 272с.
7. Физико-химические основы металлургических процессов/ Жуховицкий А.А., Белащенко Д.К., Бокштейн Б.С., и др. М.: Металлургия, 1973. 392с.
8. Восстановительные процессы в производстве ферросплавов.М.: Мир., 1975.205с.
9. Гасик Л.Н., Игнатьев В.С., Гасик М.И. Структура и качество промышленных ферросплавов и лигатур. Киев: Техника, 1975,142 с.
10. Рысс М.А. Производства ферросплавов. М., «Металлургия», 1975. 336с.
11.Абдуллабеков Е.Э,Каскин К.К.,Нурумгалиев А.Х. Технологические расчеты по производству ферросплавов М., «Металлургия», 2014.224с.
ВВЕДЕНИЕ
В металлургии и ряде других отраслей техники используют ферросплавы, а также технически чистые металлы для раскисления и легирования стали, получения легированного чугуна и различных сплавов. Улучшение качества и специальные свойства конструкционных, коррозионно- стойких, жаропрочных, жаростойких, прецизионных и электротехнических сталей, специальных литейных чугунов и самых разнообразных сплавов достигается легированием различными элементами.Ферросплавы - это сплавы железа с кремнием, марганцем, хромом, вольфрамом и другими элементами, применяемые в производстве стали для улучшения ее свойств и легирования. Вводить в сталь нужный элемент не в виде чистого металла, а в виде его сплава с железом удобнее вследствие более низкой температуры его плавления и выгоднее, так как стоимость ведущего элемента в сплаве с железом ниже по сравнению со стоимостью технически чистого металла.
В металлургии ферросплавов по объёму производства первое место занимает ферросилиций, так как, кроме применения при получении стали, он используется в качестве восстановителя при получении других ферросплавов. [4]
Ферросилиций – сплав железа с кремнием.
Ферросилиций используют при производстве стали для раскисления и легирования; в ферросплавном производстве в качестве кремний содержащего материала при силикотермическом производстве ферросплавов; в горнорудной промышленности для приготовления тяжелых суспензий при гравитационном обогащении руд; в химических технологиях для получения кремнийорганических соединений¸ взрывчатых веществ и др. [1]
В качестве рудной части шихты при производстве ферросилиция используют кварц, кварцит и халцедон.
Кварц – минерал кристаллического строения белого, серого или красного цвета в зависимости от примесей.
Кварцит – горная порода в виде кристаллов кварца, скрепленных кремнеземсодержащим веществом.
Халцедон – волокнистый минерал с разной окраской и такой же, как у кварца, плотностью. [4]
ТЕХНОЛОГИЯ ПРОЦЕССА ВЫПЛАВКИ ФЕРРОСИЛИЦИЯ
Ферросилиций – сплав железа с кремнием. Химический состав ферросилиция наиболее широко используемых марок приведен в табл. 1. [3]
Таблица 1. Состав ферросилиция по ГОСТ 1415 – 78, масс. % (не более)
Марка сплава | Si | С | S | Р | Al | Mn | Cr | Са |
ФС92 | ≥ 92 | - | 0,02 | 0,03 | 2,0 | 0,2 | 0,2 | 0,5 |
ФС90 | ≥ 89 | - | 0,02 | 0,03 | 3,5 | 0,2 | 0,2 | - |
ФС75 | 74 – 80 | - | 0,02 | 0,05 | - | 0,4 | 0,4 | - |
ФС65 | 63 – 68 | - | 0,02 | 0,05 | 2,5 | 0,4 | 0,4 | - |
ФС45 | 41 – 47 | - | 0,02 | 0,05 | 2,0 | 0,6 | 0,5 | - |
ФС25 | 23 – 27 | 0,8 | 0,02 | 0,06 | 1,0 | 0,9 | 1,0 | - |
ФС20 | 19 – 23 | 1,0 | 0,02 | 0,10 | 1,0 | 1,0 | - | - |
Примечание. Остальное – железо. |
Ферросилиций относится к большой группе ферросплавов. Отечественный стандарт на ферросилиций предусматривает производство сплавов, содержащих в среднем 20, 25, 45, 65, 69, 75, 90 и 92% кремния. Среднее содержание входит в обозначение марки ферросилиция. [2]
Шихтовые материалы
В качестве рудной части шихты при производстве ферросилиция используют кварц, кварцит и халцедон. [3]
Кварц – минерал кристаллического строения (плотность 2,59 – 2,65 г/см3) белого, серого или красного цвета в зависимости от примесей.
Кварцит – горная порода в виде кристаллов кварца, скрепленных кремнеземсодержащим веществом.
Халцедон– волокнистый минерал с разной окраской и такой же, как у кварца, плотностью.
Основным требованием к рудному сырью для производства ферросилиция является высокое содержание в нем кремнезема (>96%), минимальное присутствие примесей (Al2O3, MgO, CaO), достаточная прочность при высоких температурах. Наличие в рудном сырье оксидов железа не снижает его ценности, так как при выплавке ферросилиция в шихту вводят некоторое количество железа.
Чем меньше в кремнийсодержащем сырье примесей, тем меньше будет шлака и ниже удельный расход электроэнергии.
Перед загрузкой кварцит дробят на куски размером 20-80 мм, а образующуюся мелочь отсеивают. Промывка кварцитов водой снижает содержание в них глины и других примесей и улучшает показатели электроплавки. В качестве восстановителя применяют кокс, древесный уголь, антрацит. Требования к восстановителю: низкое содержание золы, незначительное содержание летучих, достаточная прочность, стабильный размер кусков, высокое электрическое сопротивление, постоянная, достаточно низкая влажность и большая реакционная поверхность.
По характеристикам к лучшим восстановителям относятся древесный уголь, пековый и нефтяной коксы. Препятствием является их высокая стоимость и дефицитность. По этим причинам древесный уголь применяют только при производстве кристаллического кремния. Каменный уголь и антрацит имеют высокое электрическое сопротивление низкое содержание золы, однако они растрескиваются при нагреве, поэтому их применяют ограниченно и только с добавками других восстановителей.
Наибольшее применение в качестве восстановителя при производстве ферросилиция получила коксовая мелочь – отсев, который образуется при сортировке доменного кокса. Эта мелочь, называемая коксиком, имеет размер кусков 5-25 мм и содержит <13% золы.
Использование кокса как восстановителя имеет свои особенности. Наличие в нем большого количества мелочи затрудняет выход газов и нарушает ход печи. Избыток крупных кусков повышает электропроводность шихты, приводит к уменьшению заглубленности электродов в шихте и снижению производительности печи.
Для поддержания глубокой посадки электродов при выплавке ферросилиция, увеличения реакционной способности и эффективности процесса повышают удельное сопротивление металлургического кокса, для чего добавляют в шихту кокса из газовых углей отходы графитизации с электродных заводов, карборундсодержащие отходы, нефтекокс и другие восстановители.
Наряду с коксиком применяют в значительных количествах полукокс – продукт коксования углей при температуре 7000С, имеющий достаточно стабильный состав, высокое электросопротивление и хорошую реакционную способность. При работе на смеси кокса и полукокса увеличивают глубину посадки электродов и улучшают показатели работы печей.
Большое значение для технологии производства ферросплавов имеет содержание влаги в коксике и полукоксе, которое зависит от условий перевозки и хранения. Поэтому для правильной дозировки восстановителя контролируют их навеску в шихте с учетом влажности. Для повышения однородности материалов целесообразно их сушить теплом отходящих газов.
Требуемое содержание железа в ферросилиции обеспечивается применением стружки углеродистых сталей, чистой от примесей цветных металлов и легирующих элементов, достаточно габаритной и не сильно проржавевшей. Следует иметь в виду, что легирующие элементы и фосфор полностью переходят в ферросилиций, поэтому легированную и чугунную стружку использовать при производстве ферросилиция не разрешается. [3]
Папиллярные узоры пальцев рук - маркер спортивных способностей: дерматоглифические признаки формируются на 3-5 месяце беременности, не изменяются в течение жизни...
Двойное оплодотворение у цветковых растений: Оплодотворение - это процесс слияния мужской и женской половых клеток с образованием зиготы...
Поперечные профили набережных и береговой полосы: На городских территориях берегоукрепление проектируют с учетом технических и экономических требований, но особое значение придают эстетическим...
Кормораздатчик мобильный электрифицированный: схема и процесс работы устройства...
© cyberpedia.su 2017-2024 - Не является автором материалов. Исключительное право сохранено за автором текста.
Если вы не хотите, чтобы данный материал был у нас на сайте, перейдите по ссылке: Нарушение авторских прав. Мы поможем в написании вашей работы!