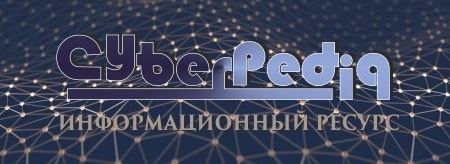
Археология об основании Рима: Новые раскопки проясняют и такой острый дискуссионный вопрос, как дата самого возникновения Рима...
Типы оградительных сооружений в морском порту: По расположению оградительных сооружений в плане различают волноломы, обе оконечности...
Топ:
История развития методов оптимизации: теорема Куна-Таккера, метод Лагранжа, роль выпуклости в оптимизации...
Процедура выполнения команд. Рабочий цикл процессора: Функционирование процессора в основном состоит из повторяющихся рабочих циклов, каждый из которых соответствует...
Интересное:
Лечение прогрессирующих форм рака: Одним из наиболее важных достижений экспериментальной химиотерапии опухолей, начатой в 60-х и реализованной в 70-х годах, является...
Искусственное повышение поверхности территории: Варианты искусственного повышения поверхности территории необходимо выбирать на основе анализа следующих характеристик защищаемой территории...
Берегоукрепление оползневых склонов: На прибрежных склонах основной причиной развития оползневых процессов является подмыв водами рек естественных склонов...
Дисциплины:
![]() |
![]() |
5.00
из
|
Заказать работу |
|
|
Введение
В качестве объекта курсового проектирования по дисциплине "Детали машин и основы конструирования" в высших учебных заведениях, как правило, предлагается механический привод, состоящий из электродвигателя, зубчатого редуктора, исполнительного органа и соединительных муфт. При этом впервые в учебном процессе перед студентом ставится задача конструирования, решение которой позволяет воплотить принципиальную схему привода в реальную работоспособную конструкцию.
Конструирование - сложный творческий процесс, который нельзя представить в виде некоторой последовательности действий, выполнение которых обязательно приведет к успеху. На практике каждый конструктор вырабатывает свои приемы, методы и подходы, определяемые особенностями разрабатываемого изделия, накопленным объемом знаний и психологией самого конструктора. Курсовое проектирование имеет специфику, заключающуюся в лимитированных сроках, дефиците знаний студента и, в конечном итоге, в целевой ориентации проектирования не на создание безупречного по техническим характеристикам изделия, а на расширение технического кругозора, закрепление лекционного материала и овладение основами конструирования.
Цель предлагаемых методических указаний состоит в том, чтобы облегчить студентам процесс вхождения в новую для них сферу деятельности.
Этапы проектирования
Исходным документом для проектирования того или иного изделия является техническое задание. В этом документе четко формулируются назначение создаваемой конструкции, предъявляемые к ней эксплуатационные требования, режимы работы, по возможности, основные её характеристики и другие сведения, подлежащие безусловному выполнению конструктором. Техническое задание конструктору выдает заказчик. Если разработка инициативная, то в роли заказчика может выступать сам конструктор. В учебном процессе техническое задание представлено в виде бланка задания на выполнение курсового проекта.
|
После получения задания конструктор (студент) должен изучить его и все возникшие вопросы, сомнения и предложения проработать с заказчиком (консультантом).
В соответствии со стандартами Единой системы конструкторской документации (ЕСКД, ГОСТ 2.103) в проектировании выделяют 5 этапов: I - разработка технического предложения; 2 - разработка эскизного проекта; 3 - разработка технического проекта; 4 - разработка рабочего проекта; 5 - разработка пояснительной записки. Следовательно ответ на вопрос: "С чего начать проектирование?" звучит однозначно - "С разработки технического предложения".
Техническое предложение представляет собой промежуточный конструкторский документ, в котором на основании анализа технического задания с позиций возможности и целесообразности реализации указанных в нем параметров и характеристик, конструктивных схем и т.п. рассматривают различные существующие и возможные варианты конструктивных решений и обосновывают предлагаемый вариант решения по реализации задания.
На данном этапе конструктору приходится работать со справочной литературой, каталогами, альбомами чертежей, стандартами, проспектами и технической документацией предприятий и фирм, выпускающих аналогичные изделия, описаниями патентов и авторских свидетельств на изобретения. При этом изыскиваются аналоги и прототипы разрабатываемого изделия, оцениваются их достоинства и недостатки, выявляются основные тенденции в совершенствовании конструкций и наиболее перспективные технические решения. Такая работа требует от начинающего конструктора значительных затрат времени и напряженного умственного труда.
|
В курсовом проекте из-за недостатка времени техническое предложение привода устанавливается заданием в виде его кинематической схемы, а студенту предлагается сравнить заданный вариант конструктивной схемы с другими возможными вариантами и сформулировать достоинства и недостатки разрабатываемой схемы привода.
Техническое предложение согласовывается с заказчиком, утверждается им и является основанием для разработки эскизного проекта.
В любом сложном механизме можно выделить отдельные агрегаты и узлы, задача конструирования или выбора которых может рассматриваться как частная. В этом случае первоначально разрабатывается и согласовывается техническое предложение всего механизма, а затем, после выполнения необходимых расчетов и определения требуемых параметров узлов и агрегатов, разрабатываются технические предложения этих узлов и агрегатов.
В состав механического привода входят электродвигатель, зубчатый редуктор, муфты. Требуемые значения их параметров определяются в результате энергетического и кинематического расчетов привода. При проектировании электродвигатель и муфты выбираются из числа серийно выпускаемых, а зубчатый редуктор подлежит детальной конструкторской проработке.
Конструирование валов
Валы могут выполняться гладкими (т.е. с постоянным диаметром по всей длине) и ступенчатыми. Чаще применяет ступенчатые валы. Ступенчатая конструкция позволяет: строго фиксировать детали, устанавливаемые на вал, в осевом направлении; приблизить вал к равнопрочному брусу и снизить расход металла; дифференцировать требования к различным участкам вала по точности и чистоте обработки; обеспечить удобство монтажа и демонтажа деталей. Недостатками ступенчатого вала по сравнению с гладким валом является большая сложность изготовления и значительное число концентраторов напряжений.
Для снижения концентрации напряжений в конструкции вала могут использоваться галтели постоянного или переменного радиуса, разгрузочные канавки и сверления, поднутрение. Разгрузочные канавки не следует путать с канавками для выхода шлифовального круга, которые являются значительными концентраторами напряжений.
Ступенчатость вала обеспечивает фиксацию деталей от перемещения только в одном направлении. Для двухсторонней фиксации дополнительно используют посадку деталей на вал с натягом, закрепление винтами, штифтами, стопорными кольцами различных видов. Поверхности вала под посадку с натягом шлифуют, а под контактные уплотнения полируют.
|
Для облегчения процесса сборки деталей с натягом соответствующие ступени вала не должны иметь лишнюю длину посадочной поверхности. Если посадка с натягом сочетается со шпоночным соединением, то необходимо обеспечивать возможность направить паз ступицы на шпонку до начала участка посадки с натягом. Это достигается удлинением направляющей фаски вала, использованием на части сопряжения посадки с зазором, выходом конца шпонки за пределы ступицы.
Конструирование вала связано с выбором шлицевых или шпоночных соединений. В приводах машин используются напряженные (клиновые, тангенциальные) и ненапряженные (призматические, сегментные, круглые) шпоночные соединения, а также шлицевые соединения с прямоугольным, эвольвентным и треугольным профилем. Шлицевые соединения обладают большей нагрузочной способностью, практически не ослабляют вал, хорошо центрируют соединяемые детали. Однако они сложнее в изготовлении и требуют специального технологического оборудования, что немаловажно в условиях единичного и мелкосерийного производства. Разновидности шпоночных и шлицевых соединений имеют свои достоинства и недостатки, что должно быть учтено при их выборе и отражено в пояснительной записке.
Для обеспечения технологичности изготовления, на одном валу стремятся использовать шпонки одинакового поперечного сечения с размерами, соответствующими меньшему диаметру вала. Это позволяет нарезать все шпоночные пазы с одной установки инструмента и удобно для контроля качества изготовления.
2.5. Конструирование корпуса редуктора
Корпус редуктора представляет собой сложную деталь, включающую в себя конструктивно взаимосвязанные корпуса подшипниковых узлов и кожух зубчатой передачи и выполняющую их функции. Корпус редуктора воспринимает нагрузки от подшипников и передает их на фундамент, защищает детали передачи от загрязнений, служит резервуаром для смазки, но главное его назначение - сохранение ориентированного положения деталей редуктора в пространстве. Отсюда следует, что основным критерием работоспособности для корпуса является жесткость.
|
Корпуса редукторов могут выполняться неразъемными и разъемными, состоящими из основания и крышки. Неразъемный корпус имеет большую жесткость, но часто не приемлем по условию возможности сборки редуктора. У разъемного корпуса плоскость разъема может проходить через оси всех валов или часть из них, может быть горизонтальной или наклонной (косой разъем). Крышка и основание разъемного корпуса выполняются с фланцами, размеры которых должны обеспечивать размещение и завинчивание деталей резьбовых соединений. Для повышения жесткости подшипниковых узлов болты (винты, шпильки) крепления крышки к основанию стремятся расположить как можно ближе к подшипникам. Обязательным элементом разъемного корпуса являются штифты, фиксирующие положение крышки относительно основания как при совместной обработке подшипниковых гнезд, так и при последующей сборке. Штифты желательно располагать на возможно большем расстоянии друг от друга.
Форма корпуса определяется типом редуктора, технологическими, эксплуатационными и эстетическими условиями, требованиями прочности и жесткости. В основном корпуса выполняют литыми из чугуна, стали или силумина, реже - сварными. Правила проектирования сварных и литых деталей излагаются в книгах [5,6.7]. Преимущества того или иного способа изготовления зависят от объема производства и могут быть сформулированы студентом на основе знаний, полученных по дисциплине "Технология металлов".
В конструкции литого корпуса конфигурацию мест расположения присоединительных поверхностей следует увязать с необходимостью и возможностью дополнительной механической обработки. При этом желательно, чтобы с одной установки корпуса на технологическом оборудовании обрабатывались возможно большее количество поверхностей, а обрабатываемая площадь была как можно меньше.
Для удобства эксплуатации и технического обслуживания редуктора в корпусе могут быть предусмотрены элементы, позволяющие без снятия крышки производить заливку и замену смазки, осмотр состояния деталей и проведение их контрольных замеров, контроль уровня смазки, а также обеспечивающие строповку редуктора при погрузочно-разгрузочных и транспортных операциях, отвод избыточного давления воздуха, удобство отделения крышки от основания при разборке корпуса и другие элементы. При конструировании перечисленных элементов рекомендуется исходить из соображений необходимости, возможности и эффективности решений тех или иных задач, а не слепо следовать стереотипам, к числу которых относится обязательность элемента, его конструктивное исполнение, размеры, месторасположение. При описании конструкции корпуса требуется обоснование принятого решения как в случае использования элемента, так и в случае отказа от него.
|
С позиции эстетического оформления многообразие конструкций корпусов определяется тенденцией перемещения выступающих частей корпуса с наружных поверхностей на внутренние. При этом улучшается внешний вид, повышается технологичность конструкции, уменьшаются масса и габариты. В учебной литературе [3,5,7] приводятся рекомендации по конструированию корпусов редукторов с обоими вариантами расположения выступающих частей.
Выбор типа и способа смазки
Смазка в машинах выполняет несколько функций. В первую очередь она предназначается для уменьшения коэффициента трения и повышения износостойкости трущихся поверхностей. Дополнительными, функциями смазки являются защита деталей от коррозии, отвод тепла и продуктов износа, демпфирование динамических нагрузок, уменьшение шума и вибрации.
В качестве смазочных материалов используют жидкие масла, пластичные и твердые смазки, а также воду, воздух и различные газы. Смазки классифицируют по способу получения (нефтяные и синтетические), по области применения (общего назначения и специальные), по эксплуатационным свойствам. В редукторах применяют жидкие масла и пластичные смазки.
При подборе смазочных материалов учитывают их вязкость, температуры застывания и вспышки, наличие примесей, способность защищать поверхности трения от заедания, задиров и коррозии, водостойкость или сопротивляемость другим факторам.
Выбор смазочных материалов в некоторых случаях основывается на расчетах (например, для подшипников скольжения) и чаще на экспериментальных данных и опыте эксплуатации. При проектировании редукторов используется последний вариант. Зубчатые колеса смазывают жидким маслом путем окунания, поливания или комбинированным способом. Способ смазки выбирают в зависимости от окружной скорости. Для смазки окунанием глубина погружения колес в масляную ванну по различным рекомендациям должна находиться в пределах от 0,5 высоты зуба до 0,25 диаметра колеса. При этом верхняя граница устанавливается с учетом окружной скорости колес с тем, чтобы уменьшить потери мощности на перемешивание масла и снизить вспенивание.
Объем масляной ванны принимают из расчета 0,35 - 0,7 л/кВт, чтобы обеспечить отвод выделяемого тепла к стенкам корпуса. Исходя из объема масла и площади днища корпуса, вычисляют высоту масляного слоя, назначают расстояние от днища до зубчатых колес. Минимальное расстояние должно быть достаточным, чтобы продукты износа могли оседать на дне и не попадали на рабочие детали (приблизительно две-три толщины стенки корпуса).
Рекомендации по выбору марки масла для зубчатых колес приведены в книгах [3,5,8, и др.].
Жидкие масла обеспечивают наиболее благоприятные условия для работы подшипников. Их преимущества заключаются в высокой стабильности, меньшем сопротивлении вращению, способности отводить тепло и очищать подшипник от продуктов износа. Пластичные смазки лучше защищают подшипники от коррозии, особенно при длительных перерывах в работе, не требуют сложных уплотнений. При конструировании редуктора и выборе способа смазки подшипников следует иметь в виду, что для подшипников одинаково плохо как избыточное количество смазки, так и её недостаток. При смазке разбрызгиванием для подшипников назначают то же масло, что и для зубчатых колес. При раздельной системе смазки пластичную смазку для подшипников выбирают с учетом рабочей температуры узла и наличия влаги в окружающей среде. Имеющиеся рекомендации [3,7] в качестве критерия для выбора смазки используют частоту вращения подшипника. Размеры внутренней полости подшипникового узла под пластичную смазку должны иметь глубину с каждой стороны подшипника не менее 1/4 его ширины, а объем смазки не должен превышать I/3…I/2 объема свободного пространства полости.
Общие положения
При эскизном проектировании выполняют расчеты и эскизные чертежи, которые позволяют определить габариты и основные параметры узлов и деталей, уточнить и скорректировать предварительно намеченные конструктивные решения.
Различают проектные и проверочные расчеты. Отличительной особенностью проектных расчетов является неполнота информации о величине сил, моментов, размерах и т.д., что приводит к необходимости принятия каких-либо упрощающих допущений, использования приблизительной справочной информации и рекомендаций, введения в расчет повышенных коэффициентов запасов прочности и пониженных допускаемых напряжений. Некоторые размеры предварительно принимаются, исходя из опыта конструирования и эксплуатации аналогичных изделий, технологических или эстетических соображений.
В конструкции любого механизма размеры отдельных деталей так или иначе связаны между собой: размеры корпуса редуктора зависят от размеров зубчатых колес и подшипников, размеры подшипников и уплотнений от размера вала и т.д. Есть детали, для которых такая взаимосвязь отсутствует. Одной из задач конструктора является выбор последовательности расчета и конструирования деталей. В курсовом проекте по деталям машин эта задача легко разрешима путем использования различных методических разработок. Если же таких методик нет (а в практике работы конструктора чаще так и бывает), расчет следует вести от основных рабочих элементов к опорам и корпусным деталям. В нашем случае основными элементами, участвующими в передаче движения, являются валы и зубчатые колеса. В большинстве методик сначала выполняют расчет зубчатых передач. Однако более логично начать с ориентировочного расчета валов, так как размеры валов используются для вычисления некоторых размеров зубчатых колес и влияют на их конструктивное исполнение, а также через размеры подшипников определяют величину минимального межосевого расстояния.
Проектный расчет валов
Вычислительная часть курсового проектирования обычно начинается с кинематического и силового (энергетического) расчетов механического привода. При этом определяют требуемую мощность силового механизма и выбирают электродвигатель, вычисляют передаточное отношение привода и производят его разбивку между передачами, входящими в состав привода, или по ступеням редуктора, рассчитывают частоты вращения валов и вращающие моменты, передаваемые ими. (Здесь и далее не приводятся описания методик расчета и расчетные формулы, так как они излагаются на лекциях и практических занятиях). Затем приступают к проектному (ориентировочному) расчету валов.
При работе вал, как правило, испытывает сложное напряжённое состояние, определяемое действием вращающего и изгибающего моментов, растягивающих или сжимающих сил. При проектном расчете известен только вращающий момент, поэтому минимальный диаметр вала определяют из расчета на кручение по пониженным допускаемым касательным напряжениям. Наличие ступеней на валу и их количество устанавливается при разработке технического предложения. Минимальное значение диаметра вала, как правило, соответствует диаметру его хвостовика, то есть той концевой части вала, которая предназначена для подключения к редуктору других устройств.
В механическом приводе редуктор соединяется с электродвигателем и исполнительным органом посредством стандартных муфт, большинство из которых имеют строго определенные диаметры посадочных поверхностей на вал. Поэтому диаметр хвостовика необходимо согласовать с посадочным размером муфты (следовательно, выбор муфты должен производиться параллельно). Диаметры остальных участков валов назначают, руководствуясь следующими правилами. Если заплечик вала используется для фиксации детали на валу от перемещения в осевом направлении, то разность диаметров должна обеспечивать контакт детали с заплечиком по кольцевой плоской поверхности. Для этого высота эаплечика должна быть больше размера фаски или радиуса закругления детали, а размер галтели вала наоборот - меньше. В учебных пособиях [3, 7] для некоторых деталей даются рекомендуемые соотношения для вычисления высоты заплечика или разности диаметров, обеспечивающие не только требуемый контакт, но и удобство демонтажа деталей с вала. Если заплечик вала не является упорным, разность диаметров следует назначать минимальной с целью уменьшения концентрации напряжений. В некоторых случаях ступенчатость вала достигается путем назначения различных полей допусков при одном и том же номинальном диаметре. Назначаемый диаметр вала должен согласовываться с диаметром отверстия сопрягаемой детали (уплотнения, подшипника, закрепительной гайки), если только размеры сопрягаемой детали не принимают по диаметру вала.
Размеры фасок, скосов, радиусов закруглений, проточек принимаются в зависимости от диаметра вала [3, 7]. Длина различных участков вала определяется конструктивно при выполнении эскизного чертежа редуктора (смотри ниже). Для хвостовика длина может быть принята по стандарту ГОСТ 12080, или ГОСТ 12081, равной длине посадочной поверхности муфты, или из расчета на прочность шпоночных соединений.
Расчет зубчатых передач
Расчет зубчатых передач регламентируется ГОСТ 21354. Для учебного проектирования можно использовать любой учебник [4, 8] или учебное пособие [3, 7], однако, остановившись на одном из них, следует придерживаться излагаемой в нем методики расчета и приводимых справочных данных. Это правило рекомендуется соблюдать и в других случаях. Сравнение методик расчета, излагаемых в разных источниках, может быть весьма полезным для углубления знаний по предмету.
Расчет начинается с выбора материалов и определения допускаемых напряжений. Выбор материалов обычно вызывает значительные затруднения. В реальных условиях конструирования материал выбирают с учетом ограничений по массе и габаритам, условий эксплуатации (температура, динамичность нагрузки), доступной технологии термической, химико-термической и механической обработки, стоимости изготовления, опыта эксплуатации изделия аналогичного типа, результатов исследований. Как правило, при проектировании рассматривается несколько материалов с различными механическими характеристиками, Лучший вариант выявляется в результате технико-экономического сравнения.
При курсовом проектировании упомянутой информацией студент не располагает, т.е. ему представляется свобода выбора, которой как оказывается сложно распорядиться. В этой связи можно руководствоваться следующими соображениями.
1. В качестве габаритного ограничения следует принять размеры чертежного листа формата A1 для изображения двух видов редуктора (вид спереди и вид сверху со снятой крышкой) в масштабе 1:1.
2. Материалы шестерни и колеса должны быть неоднородными по химическому составу или твердости для уменьшения склонности к заеданию. Шестерню выполняют более твердой.
3. Применение различных видов упрочняющих термических обработок обусловлено стремлением повысить механические характеристики стали с целью снижения массы и габаритов зубчатой передачи.
4. Наиболее удобными для изготовления зубчатых колес являются материалы с твердостью до 320 НВ, так как при этом возможно чистовое нарезание зубьев после термической обработки, что обеспечивает высокую точность. Такие зубья хорошо прирабатываются, но обладают относительно невысокими механическими характеристиками.
5. Использование объемной закалки приводит к деформации зубьев в результате термообработки и необходимости их последующего шлифования, что снижает точность зубчатой передачи.
6. Легированные стали обладают большей механической прочностью и вязкостью, лучше поддаются термической термообработке.
7. Химико-термическая обработка характеризуется длительностью процесса и требует специального технологического оборудования, используется для сохранения вязкой сердцевины зубьев при высокой твердости поверхностных слоев.
В некоторых учебниках можно найти рекомендуемые сочетания марок сталей и термообработок материалов шестерни и колеса и принять их, для расчета. Для обоснования выбора материала и термообработки следует пользоваться книгами[1,4,6,8].
Для каждого вида термообработки в справочных пособиях твердость стали указывается в виде диапазона значений, характеризующего разброс параметров в технологическом процессе. При расчете допускаемых напряжений в формулы следует подставлять среднее значение твердости из указанного диапазона.
Проектный расчет зубчатой передачи ведут из условия обеспечения усталостной прочности по контактным напряжениям. В первую очередь производят вычисления для тихоходной ступени. Искомыми параметрами обычно являются межосевое расстояние или делительный диаметр шестерни. Значение принимаемого стандартного межосевого расстояния должно удовлетворять габаритным ограничениям. Верхнее ограничение устанавливается из условия размещения двух проекций редуктора на листе формата A1, нижнее - из условия вписывания в межосевое расстояние полу суммы наружных диаметров подшипников валов шестерни и колеса и обеспечения гарантированного расстояния между их наружными кольцами для размещения болта крепления крышки к основанию корпуса редуктора (можно принять 20 мм). Далее вычисляются все параметры зубчатых колес, и завершается их конструкторская проработка.
В конце расчета уточняются параметры твердости с учетом реально полученных размеров. В случае выявления расхождения фактической и первоначально принятой твердости следует повторить расчет.
Завершает расчет проверка зубчатой передачи на статическую прочность от действия перегрузок.
Затем выполняют расчет быстроходной ступени. Для соосного редуктора и коробки скоростей межосевые расстояния быстроходной и тихоходной ступеней равны между собой. Для этих редукторов с целью достижения равной напряженности зацепления ширину зубчатых колес быстроходной ступени уменьшают.
Параметры обратной ступени реверсивного редуктора можно получить геометрическим вписыванием её зубчатых колес в межосевое расстояние, полученное при расчете прямой ступени. Диаметры шестерни и колеса принимают такими, чтобы минимальное расстояние между вершинами их зубьев было не менее 10 мм при сохранении требуемого передаточного отношения. Размеры паразитной шестерни по возможности выполняют такими же, как размеры основной шестерни. Модуль зацепления целесообразно принять таким же, как и для прямой ступени. Проверку прочности зубьев ведут, используя межосевые расстояния, взятые из чертежа.
Проверочные расчеты
Наличие компоновочного чертежа позволяет составить расчетные схемы валов, определить нагрузки на подшипники (реакции опор), построить эпюры изгибающих и крутящих моментов.
Валы рассчитывает на усталостную прочность по номинальным напряжениям, и на статическую прочность по пиковым напряжениям, возникающим вследствие перегрузок. Распространенным заблуждением среди студентов является утверждение, что опасное сечение вала определяется максимумом изгибающего момента. Это утверждение отчасти справедливо для гладкого вала. У ступенчатого вала до завершения расчетов опасными считаются все участки, на которых изменяется его площадь поперечного сечения. Действительно опасным будет то сечение, для которого коэффициент запаса прочности получится минимальным. У валов редуктора в сумме более десятка опасных сечений. В учебном проектировании по согласованию с консультантом выполняют расчет одного-двух сечений для каждого вала. Однако в пояснительной записке следует перечислить все опасные сечения.
Подшипники качения проверяют по долговечности. Расчетная долговечность подшипника должна быть не меньше долговечности редуктора. На практике возможна и меньшая долговечность при условиях установления срока замены подшипников в эксплуатации. В курсовом проекте выполнение указанного требования следует безусловно обеспечить изменением параметров или типоразмера подшипников. При определении эквивалентных нагрузок подшипников необходимо учитывать циклограмму нагружения редуктора, осевые силы от радиального нагружения в радиально-упорных подшипниках, способ фиксации опор, направление внешней осевой силы, вариант замыкания осевых сил в раздвоенных ступенях и на промежуточных валах (через вал или через детали, установленные на валу). Неправильная оценка перечисленных факторов является частой ошибкой курсового проектирования.
Для коробки скоростей и реверсивного редуктора выполняется проверочный расчет кулачковой муфты переключения на изгиб и смятие кулачков.
Для реверсивного редуктора размеры оси паразитной шестерни определяют из расчета на статическую прочность. Равнодействующую внешних сил, приложенных к оси, удобно найти графическим сложением их векторов. Принятые размеры оси проверяют на жесткость. Затем подбирают подшипники паразитной шестерни и оценивают их пригодность. В пояснительной записке следует привести эскиз узла паразитной шестерни.
ХХХХ. ХХХХХХ. ХХХ
1 2 3
где: 1 - код организации разработчика; 2 - код классификационной характеристики изделия по классификатору ЕСКД; 3 - порядковый регистрационный номер в пределах от 001 до 999. Для курсового проекта по деталям машин рекомендуется следующий вариант обозначения спецификации
СТ. КПДМ7.015,
где: СТ означает, что разработчиком является студент механического факультета, КПДМ7 - аббревиатура курсового проекта по деталям машин и номер задания на проектирование, 015 - условный регистрационный номер. Для обозначения не основного конструкторского документа в приведенной записи справа указывают код документа:
СВ - сборочный чертеж, ПЗ - пояснительная записка.
Обозначения чертежей деталей будут отличаться регистрационными номерами, которые рекомендуется самостоятельно назначать, начиная с номера 010.
Пример обозначения рабочего чертежа детали: СТ.КПДМ7.055
(Не требуется совпадение номера позиции на сборочном чертеже с регистрационным номером).
Рабочие чертежи деталей
В составе графической части курсового проекта по деталям машин разрабатываются рабочие чертежи 4-6 деталей. Перечень деталей согласовывается с консультантом.
Оформление чертежей должно соответствовать требованиям ЕСКД, предъявляемым к рабочим чертежам. На рабочем чертеже детали указывают размеры, предельные отклонения, шероховатость поверхности, допуски формы и расположения и другие данные, которым она должна соответствовать перед сборкой. Для некоторых деталей (например, зубчатых колес) ЕСКД устанавливает стандартные изображения, которые должны соблюдаться.
В случае, когда отдельные данные, указания, разъяснения невозможно или нецелесообразно выразить графически или условными обозначениями, в чертеж включают текстовую часть, которую располагают над основной надписью. Применительно к рабочим чертежам деталей редуктора, текстовая часть обычно состоит из таблицы параметров для зубчатых колес, состав и положение которой на чертеже определяется соответствующими стандартами, и технических требований.
Пункты технических требований последовательно нумеруют арабскими цифрами и по возможности располагают в следующем порядке:
а) требования, предъявляемые к материалу, заготовке, термообработке и к свойствам материала готовой детали (твердость, прочность, магнитные, электрические и другие свойства);
б) размеры, предельные отклонения размеров, допуски формы, расположения поверхностей
в) требования к качеству поверхностей, указания об их отделке, покрытии.
Заголовок "Технические требования" не пишут.
Пояснительная записка
Пояснительная записка является документом, содержащим описание устройства и принципа действия разрабатываемого изделия, а также обоснование принятых при его разработке технических и технико-экономических решений. Требования к содержанию и оформлению пояснительной записки устанавливают стандарты ЕСКД (см. [9]).
Написание пояснительной записки является заключительным этапом проектирования, к моменту выполнения которого все решения касающиеся конструкции, материалов, способов изготовления, критериев работоспособности, методов расчета и так далее приняты и реализованы. Поэтому недопустимо при изложении текста пояснительной записки использовать слова и словосочетания типа «целесообразно», «предварительно намечаем», «ориентировочно принимаем», «рассматриваем возможность использования» и тому подобные, вносящие в изложение элементы неопределенности.
Содержание пояснительной записки
Применительно к разрабатываемому приводу рекомендуется следующий состав разделов пояснительной записки:
Введение
1. Техническая характеристика привода.
2. Кинематический и силовой расчеты привода.
3. Выбор муфт.
4. Описание конструкции редуктора.
5. Конструирование и проектный расчет валов.
6. Расчет зубчатых передач.
6.1. Выбор материалов и определение допускаемых напряжений для тихоходной ступени.
6.2. Расчет тихоходной ступени.
6.3. Выбор материалов и определение допускаемых напряжений для быстроходной ступени.
6.4. Расчет быстроходной ступени.
7. Конструирование и расчет размеров зубчатых колес.
8. Конструирование и расчет размеров корпуса редуктора.
9. Конструирование подшипниковых узлов.
10. Конструирование системы смазки.
11. Определение нагрузок, действующих на валы и опоры.
12. Расчет подшипников качения.
13. Расчет валов на усталостную прочность.
14. Расчет шпоночных соединений.
Список литературы.
В зависимости от особенностей задания на проектирование состав разделов может быть изменен как в сторону увеличения, так и в сторону уменьшения.
Главные требования к пояснительной записке – ясность изложения и удобство чтения, обеспечивающие понимание написанного без привлечения автора. В этой связи ниже излагаются требования к построению разделов пояснительной записки.
Во введении следует указать на основании каких документов разрабатывается проект, привести схему и описать устройство и принцип действия разрабатываемого привода, назначение и конструктивные особенности механизмов, входящих в его состав; сформулировать достоинства и недостатки заданной схемы; привести исходные данные для проектирования. Здесь же, не выделяя в самостоятельный раздел, можно отметить назначение и область применения привода.
Техническую характеристику привода составляют на основании окончательных результатов проектирования. В ней указывают параметры, характеризующие привод в целом (мощность, КПД, передаточное отношение, номинальный и максимальный вращающие моменты на тихоходном валу или отношение максимального момента к номинальному), а также обозначения и параметры основных узлов и агрегатов (электродвигателя, редуктора, муфт, цепной и ременной передачи и т.д.).
Кинематический и силовой расчеты привода предполагают определение рабочих параметров и выбор электродвигателя, разбивку передаточного отношения редуктора по ступеням, вычисление частот вращения валов и вращающих моментов, передаваемых ими. Следует принять во внимание, что стандартные передаточные отношения обязательны только для редукторов общего применения.
Выбор муфт производится исходя из значений вращающих моментов, передаваемых ими, коэффициента, учитывающего условия эксплуатации и диаметров соединяемых валов. Для предохранительных муфт расчетное значение момента приравнивается значению пускового момента электродвигателя, умноженному на коэффициент 1,1…1,2. При изложении раздела рекомендуется указать условные обозначения муфт и привести мотивы, по которым были выбраны муфты определенного типа.
Следующим разделом является описание и обоснование конструкции редуктора. Для этого следует привести эскиз редуктора (вид спереди и сверху со снятой крышкой), описать устройство редуктора и назначение узлов и деталей, входящих в его состав.
Описание конструкции отдельных деталей может быть изложено коротко с учетом содержания последующих разделов, посвященных конструированию этих деталей.
Раздел, посвященный конструированию валов, можно разбить на подразделы в соответствии с количеством валов. Раздел рекомендуется начать с обоснования принятого конструктивного исполнения валов, которые следует показать н<
|
|
Двойное оплодотворение у цветковых растений: Оплодотворение - это процесс слияния мужской и женской половых клеток с образованием зиготы...
Индивидуальные очистные сооружения: К классу индивидуальных очистных сооружений относят сооружения, пропускная способность которых...
История создания датчика движения: Первый прибор для обнаружения движения был изобретен немецким физиком Генрихом Герцем...
Своеобразие русской архитектуры: Основной материал – дерево – быстрота постройки, но недолговечность и необходимость деления...
© cyberpedia.su 2017-2024 - Не является автором материалов. Исключительное право сохранено за автором текста.
Если вы не хотите, чтобы данный материал был у нас на сайте, перейдите по ссылке: Нарушение авторских прав. Мы поможем в написании вашей работы!