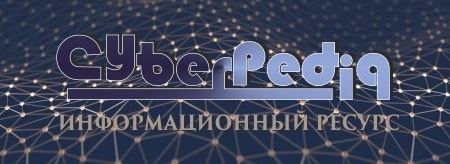
Типы оградительных сооружений в морском порту: По расположению оградительных сооружений в плане различают волноломы, обе оконечности...
Особенности сооружения опор в сложных условиях: Сооружение ВЛ в районах с суровыми климатическими и тяжелыми геологическими условиями...
Топ:
Оснащения врачебно-сестринской бригады.
Марксистская теория происхождения государства: По мнению Маркса и Энгельса, в основе развития общества, происходящих в нем изменений лежит...
Установка замедленного коксования: Чем выше температура и ниже давление, тем место разрыва углеродной цепи всё больше смещается к её концу и значительно возрастает...
Интересное:
Что нужно делать при лейкемии: Прежде всего, необходимо выяснить, не страдаете ли вы каким-либо душевным недугом...
Инженерная защита территорий, зданий и сооружений от опасных геологических процессов: Изучение оползневых явлений, оценка устойчивости склонов и проектирование противооползневых сооружений — актуальнейшие задачи, стоящие перед отечественными...
Подходы к решению темы фильма: Существует три основных типа исторического фильма, имеющих между собой много общего...
Дисциплины:
![]() |
![]() |
5.00
из
|
Заказать работу |
|
|
Техническая норма времени – это время, необходимое для выполнения операций в предусмотренных для нее условиях. Норма времени на обработку одной детали (штучное время) определяется по следующей формуле:Тшт.= to+tв+tобс.+tпер.,где to - основное (технологическое) время;tв- вспомогательное время;tобс. - время обслуживания рабочего места;tпер. - время перерыва на отдых и личные надобности.Основное (технологическое) время – это время, в течение которого достигается цель операции: изменение формы, размеров и состояния поверхностного слоя заготовки (рассчитывается по справочнику технолога) по формуле: гдеLp - расчетная длина в направлении подачи;Sm - минутная подача (при точении; Sm = So×n мм/мин; при фрезеровании Sm = Sz×z×n мм/мин);i - число проходов в переходе;а - число одновременно обрабатываемых деталей.Вспомогательное время (tв) - время на действия рабочего, сопровождающего выполнение основной технологической работы. Это время на:установку, закрепление и снятие детали;управление механизмами станка;перемещение режущего инструмента;промеры.Вспомогательное время определяется суммированием времен перечисленных действий (в каждой отрасли - свои):
Оперативное время tоп. – это сумма основного и вспомогательного времени.Время обслуживания рабочего места (tобс.) – время ухода за станком, отнесенное к одной заготовке, подразделяется на время технического обслуживания (tт.о.) и время организации обслуживания (tо.о):tобс. = tт.о..+ tо.о.Время на техническое обслуживание (tт.о.) – время на смену инструмента, регулирование и подналадку станка, сметание стружки и другие действия, связанные с выполнением основной работы. Рассчитывается в процентах от основного времени:
.Время на организацию обслуживания tо.о. – время на подготовку рабочего места к началу работы, уборку в конце смены, смазку, чистку станка и другие действия, связанные со сменой?.
(для отрасли b=0,6¸0,7).Время tп – время на отдых и личные надобности рабочего, рассчитывается по формуле:
.Норма времени в условиях единичного и мелкосерийного производства (обработка ведется партиями) называется калькуляционной нормой времени и рассчитывается по формуле:
,Где tп.з. – подготовительно-заключительное время;Nп. - размер партии (кол-во заготовок в партии);Подготовительно-заключительное время – время на ознакомление с работой, на подготовку и наладку станка, приспособлений, инструмента (назначается по нормативам).Разряд работы устанавливается по квалификационным справочникам.
|
33.Оформление технологических документов: общие требования и правила оформления
К заполнению граф технологических документов предъявляются следующие требования.
1. Каждая строка мысленно делится по горизонтали пополам. Информацию записывают в нижней ее части, оставляя верхнюю часть свободной для внесения изменений.
2. Графы, выделенные утолщенными линиями, заполняются по одному из трех вариантов:
а) в случае внедрения автоматизированной системы управления производством эти графы заполняются кодами и обозначениями по соответствующим классификаторам и стандартам;
б) информация записывается в раскодированном виде;
в) при курсовом и дипломном проектировании информацию рекомендуется записывать в виде кодов с их расшифровкой.
Для изложения технологических процессов в маршрутной карте используют способ изложения, при котором информацию вносят построчно несколькими типами строк.
Каждому типу строки соответствует свой служебный символ. В качестве обозначения служебных символов приняты прописные буквы русского алфавита, проставляемые перед номером соответствующей строки. Применение соответствующих служебных символов в графах маршрутной карты следует выполнять в соответствии с табл. 9.1.
|
Сведения, вносимые в графы, расположенные на строке маршрутной карты
Обозначение служебного символа | Содержание информации, вносимой в графы |
А Б К М О Т Р | Номер цеха, рабочего места, где выполняется операция; код и наименование операции Код, наименование оборудования и информация по трудозатратам Информация о комплектации изделия составными частями с указанием наименования деталей, количества на изделие, кода единицы величины, нормы расхода Информация о применяемом основном материале и исходной заготовке, кодах единицы величины, количестве на изделие и нормы расхода Содержание операции (перехода) Информация о применяемой при выполнении операции технологической оснастке Информация о режимах обработки |
При заполнении информации на строках, имеющих служебный символ «Т», следует руководствоваться требованиями соответствующих классификаторов, государственных и отраслевых стандартов на кодирование (обозначение) и наименование технологической оснастки.
Информацию о применяемой на операции технологической оснастке необходимо записывать в следующей последовательности: 1) приспособления; 2) вспомогательный инструмент; 3) режущий инструмент; 4) слесарно-монтажный инструмент; 5) специальный инструмент; 6) средства измерения.
34.Методика- технико-экономического сравнения вариантов технологического процесса.
Экономические критерии оценки вариантов технологических процессов. Различают два показателя экономической эффективности абсолютный и сравнительный.Абсолютный показатель определяют по формуле: ,где Ц - оптовая цена предприятия;С -себестоимость продукции;К - капитальные вложения.Значение Эа сопоставляется с соответствующими значениями отраслевого норматива Еа» 0,14- 0,16. Если Эа> Еа, то капитальные вложения эффективны.Сравнительная экономическая эффективность вариантов технологического процесса определяется по коэффициенту сравнительной экономической эффективности Ер или по расчетному сроку окупаемости Тр дополнительных капитальных вложений.
,Ер > Ен (»0,12).Срок окупаемости Тр определяется по формуле
,Тр < Тп (8,3 года)где С1 и С2 –себестоимость единицы продукции;К1 и К2 - капитальные вложения, отнесенные к единице продукции.Если капитальные вложения не меняются от варианта к варианту, то выбор наиболее эффективного варианта проводится или по величине себестоимости продукции, или только по величине технологической себестоимости, включающей сумму статей себестоимости, изменяющихся при переходе от одного технологического процесса к другому.Расчеты сравнительной экономической эффективности выполняют на стадии разработки технологических процессов при запуске новых изделий и проектировании новых производств.Расчеты абсолютной экономической эффективности выполняют при проектировании новых технологических процессов для существующего конкретного предприятия, цеха, участка.В практике проектирования ТП критерием выбора становится не локальная экономическая эффективность данного усовершенствования, а экономический результат в более широком масштабе.Для экономических расчетов необходимо определить с достаточной точностью и достоверностью слагаемые текущих (С) и капитальных затрат. Определение себестоимости методом прямого калькулирования Экономичность того или иного варианта выполнения операций оценивается по цеховой себестоимости деталей. Цеховая себестоимость рассчитывается по следующей формуле:
,где М – стоимость материала заготовки;Зпр – зарплата производственных рабочих;Н – цеховые накладные расходы.
,где О – расходы, связанные с амортизацией и эксплуатацией универсального оборудования и приспособлений;И – расходы на амортизацию и эксплуатацию специальных станков и специальной оснастки, отнесенные к объему выпуска деталей;Зн – зарплата наладчиков.Затраты, из которых складывается цеховая себестоимость можно разделить на две основные группы: затраты, связанные с выполнением операций – технологическая себестоимость; затраты, не связанные с выполнением операций, а зависящие от общих производственных условий работы цеха:
.Экономические преимущества одного варианта перед другим выявляется путем сравнения технологических себестоимостей.Таким образом, технологическая себестоимость состоит из двух частей:Часть А – это текущие (переменные) расходы, зависящие от объема выпуска деталей А = М + Зпр + ОДругая часть Б – не зависит от объема производства и ее называют единовременными (постоянными) расходами.
Зависимость себестоимости от объема производства представлена на рис. 4. Для партии деталей умножив на N получим: С N = Cд× N = А N +Б.Данная зависимость представлена на рис. 5.
|
|
Рис. 4. Зависимость себестоимости от объема производства
Рис. 5. Зависимость себестоимости от объема производства для партии деталей
Рассмотрим пример, когда имеются два варианта (см. рис. 6).
Рис. 6. Зависимость себестоимости от объема производства для партии деталейВ 1-ой зоне предпочтительным оказывается первый вариант. Во 2-ой зоне - второй вариант. Разность между первым и вторым вариантом будет годовой экономией (экономией на партию). Найдем Nкр. : СN1 = CN2 или А1N+b1 = A2N +b2.Отсюда .
35. Обтачивание на токарных станках цилиндрических наружных поверхностей
К токарным относится большая группа станков, предназначенных в основном для обработки поверхностей вращения, соосных оси шпинделя (цилиндрических, конических, винтовых, а также торцовых). Обработку на токарных бесцентровых станках осуществляют вращающимися многорезцовыми головками при продольной подаче заготовок. На этих станках обтачивают трубы, сортовой прокат цилиндрической формы.
Используются след, схемы:базирование детали в токарных патронах(D>l),базирование детали в токарном патроне и заднем центре,установка в центрах(вал)
36. Шлифование наружных цилиндрических поверхностей. Методы шлифования.
На круглошлифовальных станках осуществляют продольное и врезное шлифование.
Метод продольного шлифования более универсальный, чем метод врезного шлифования. Он не требует специальной наладки, одним шлифовальным кругом можно обработать поверхность разной длины. При продольном шлифовании круг изнашивается более равномерно и заметно не влияет на отклонение от цилиндричности шлифуемой поверхности. Метод продольной подачи, метод вырезанием.
При врезном шлифовании одновременно обрабатывается вся шлифуемая поверхность. Этот метод более производительный. Для его осуществления применяют более широкие круги и станки повышенной мощности и жесткости.
37. Обработка цилиндрических отверстий: сверление, зенкерование, развертывание.
На станках сверлильной группы кроме обычных операций обработки отверстий (сверления, снятие фасок, зенкерования) подрезают торцы, растачивают отверстия и канавки, нарезают резьбы. Выбор метода сверления зависит от диаметра отверстия, глубины сверления, точности отверстия и расположения его оси, обрабатываемого материала и др.
|
Глубина резания при сверлении: t=0,5*D, при рассверливании, зенкеровании и развертывании е=0,5(D-d).
Различают сверла: спиральное, полукруглое, пластинчатое, одностороннее, трепанирующее и др.
При сверлении отверстий без ограничивающих факторов максимально допустимую по прочности сверла подачу.
Зенкерование – предварительная обработка литых, штампованных или просверленных отверстий под последующее развертывание, растягивание или протягивание. При точности отверстий 11-13 квалитета и параметре шероховатости поверхности
Ra=5-10 мкм зенкерование м/б окончательной операцией.
Развертывание – чистовая обработка отверстий с точностью 7-11 квалитета, не измеющая положения их осей.
38. Обработка цилиндрических отверстий: шлифование, растачивание, протягивание.
Отверстия в деталях на внутришлифовальных станках обрабатываются напроход и врезанием. Способ врезания используют при обработке коротких, фасонных и глухих отверстий, не имеющих канавок для выхода круга. Во всех остальных случаях применяют шлифование напроход, обеспечивающее более высокую точность и меньший параметр шероховатости поверхности.
Протягивание. Внутреннее протягивание наиболее широко применяют для обработки различных отверстий. Диаметр протягиваемых отверстий 5-400 мм., длина до 10 м. Чаще всего протягивают отверстия диаметром 10-75 мм, с длинной не превышающей 2,5-3 диаметра. Наружное протягивание применяют вместо фрезерования, строгания, шлифования для обработки поверхностей площадью 100-200 кв.см. Чаще всего протягивают плоские и фасонные поверхности, различные пазы, зубчатые колеса. Протяжками обрабатывают все виды металлов и пластических масс, допускающих обработку резанием. Производительность протягивания в 3-12 раз выше производительности других способов механической обработки металла. Одной протяжкой можно изготовить до 1000 деталей.
Растачивание. Растачивание используется для обработки отверстий более 100 мм. Существуют 2 основных способа растачивания:
1. Вращением детали на станках токарной группы;
2. Для обработки деталей больших диаметров (500 мм) вращается инструмент, деталь неподвижна. Используются растачиваемые станки.
Растачивание на станках токарной группы наиболее универсальна. При этом точность, шероховатость поверхности, режим резания такие же как и при обработке наружных поверхностей.
39. Шлифование плоскостей.
Предшествующей обработкой под шлифование служит чистовое обтачивание или фрезерование плоскости. Шлифование осуществляется или торцом круга (в массовом и серийном производстве), или периферией круга (единичное производство). Шлифование торцом круга производительнее, так как в резании одновременно участвует большее число режущих зерен. Однако большой контакт круга с деталью при шлифовании торцом вызывает интенсивное выделение теплоты в процессе шлифования, что нередко приводит к деформациям. При шлифовании периферией круга поверхность контакта и число одновременно режущих зерен значительно уменьшается, поэтому снижается производительность, количество выделяемой теплоты и деформации. Станки работающие периферией круга, более универсальны. Шлифование торцем осуществляется на станках с прямоугольным и круглым столом. Наиболее производительна обработка на круглом вращающемся столе. Обработка может вестись двумя методами – многопроходным и глубинным. При многопроходном шлифовании стол станка вращается (15-20 м/мин). Вертикальная подача осуществляется периодически за один или несколько оборотов стола. При одновременном шлифовании стол вращается стол вращается медленно (0,5-1 м/мин) и за 1 проход снимает весь припуск. Многопроходное шлифование из-за больших затрат времени на установку, снятие и измерение значительно уступает однопроходному. Предварительное шлифование (Ra=125, 9-8 квалитет,z=0.3-1мм)
Чистовое шлифование (Ra=0,32, 7-6 квалитет z=0.2мм)
Тонкое шлифование (Ra=0,025-0,1, 6-5 квалитет z=0.05-0,1мм)
Для тонкого V кр = 50(75)м/с,для предварительного V кр = 30-35м/с s(подача)=0,3-0,8мм/об,
Различают 2 способа- метод продольного шлифования и метод врезания.
Фрезерование плоскостей.
При фрезеровании плоскости необходимо надежное закрепление деталей. Допустимый припуск очень универсален, ограничены лишь надежность закрепления детали и прочность детали.
Цилиндрическое фрезерование (встречное) характеризуется высокой производительностью.
Цилиндрическое фрезерование имеет следующие параметры шероховатости:
Грубое фрезерование (Rz=80-40, 12-14 квалитет)
Черновое фрезерование (Rz=20, 10-11 квалитет)
Чистовое фрезерование (Ra=2,5, 7-9 квалитет)
Торцевое фрезерование более производительно и точно в области применения – широкая.
Торцевое фрезерование имеет следующие параметры шероховатости поверхности:
Грубое фрезерование (Rz=40, 12-14 квалитет)
Черновое фрезерование (Ra=2,5-1,25, 9-11 квалитет)
Чистовое фрезерование (Ra=0,63-0,32, 6-7 квалитет)
Уменьшение параметра шероховатости поверхностей и вибрации достигают работая с фрезами минимально возможного диаметра с малым шагом.
|
|
История развития пистолетов-пулеметов: Предпосылкой для возникновения пистолетов-пулеметов послужила давняя тенденция тяготения винтовок...
Поперечные профили набережных и береговой полосы: На городских территориях берегоукрепление проектируют с учетом технических и экономических требований, но особое значение придают эстетическим...
Общие условия выбора системы дренажа: Система дренажа выбирается в зависимости от характера защищаемого...
Автоматическое растормаживание колес: Тормозные устройства колес предназначены для уменьшения длины пробега и улучшения маневрирования ВС при...
© cyberpedia.su 2017-2024 - Не является автором материалов. Исключительное право сохранено за автором текста.
Если вы не хотите, чтобы данный материал был у нас на сайте, перейдите по ссылке: Нарушение авторских прав. Мы поможем в написании вашей работы!